The content is published under a Creative Commons Attribution Non-Commercial 4.0 License.
Reviewed Article:
The Mother of All Bead Furnaces: Testing a Hypothesis about a Natural Draft Bead Furnace
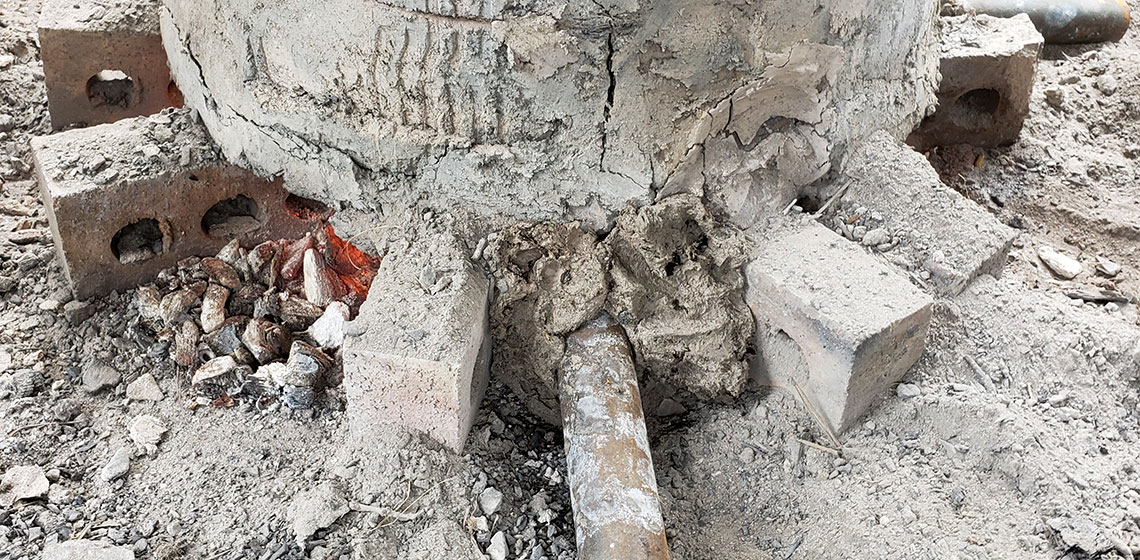
As a part of the ongoing exploration of Viking Era glass bead production, the Dark Ages Re-creation Company (DARC) team perform new pilot experiments on a regular basis. These experiments provide a preliminary understanding of a specific construct or research question, allowing us to judge the validity of further experiments, as well as what equipment or additional questions may be necessary as a part of a related experiment sequence. For a more complete understanding of the archaeological and cultural background to this series of experiments please refer to Peterson, 2017 and Peterson, et al., 2014.
For 2018 experiment the DARC team consisted of Darrell Markewitz, Richard Schweitzer, Sarah Backa, the author, and two guests.
The specific goal of this pilot experiment was to gather a preliminary understanding of a rather radical interpretation of hearth QA from Ribe. Ribe sits at the southwestern side of Jutland in Esbjerg municipality. On the north side of the Ribe river across from the medieval town of Ribe is the Viking era marketplace of the same name. Archaeology dates the location to the first decade of the 8th century (Jensen, 1991, p.5). This site was a seasonal market town divided into plots which remained in service for annual or semi-annual craft markets for over one hundred years (Jensen, 1991, p.7). At least one bead maker worked on this site as documented by a rich debris field including raw glass, tesserae, clipped glass threads (stringers), incomplete and damaged beads and fire marked hearths. Hearth QA is unusual due to its larger size (50 cm diameter) and lenticular cross-section. The cross-section and the radial cracking strongly suggest the hearth is in situ. The burn pattern implies a thick-walled structure, unfortunately, no specific remains of the structure survive beyond this hearth (Bencard and Jørgensen, 1990, p.99).
One suggested interpretation is that hearth QA represents a natural draft bead furnace. Natural draft iron smelters are known from earlier time periods such as the Roman Iron Age, so the knowledge could have existed in Viking Era Scandinavia. Since the comfortable working temperatures for glass (800-1000°C) are slightly lower than the 1200-1300°C required to smelt iron, the idea appears functional at a basic level.
A natural draft furnace replaces the forced air system (such as the bellows normally employed in our experiments) with the application of the chimney principle. By building the furnace tall (in excess of 140 cm) the temperature difference between the lower and upper portions of the furnace cause a draft to draw fresh air in through inlets at the bottom of the furnace as heated air is expelled out the top of the chimney. As one would expect the complexities of such a system mean the details are important, so a pilot experiment to explore the different conditions is a good solution.
21 July 2018 - The Build
DARCâs intention had been to reuse a bloomery iron smelting furnace for this burn by extending the height. Unfortunately, that furnace was vandalized in the days leading up to the effort.
Instead, a clean build from start to finish was initiated. The entire construction was cobb (clay, sand, and horse manure mix in equal volumes). The plan was for a furnace with a 50 cm outside diameter at the base thinning as it got taller, 30 cm internal diameter, and a height of at least 1.4 m. Given that our past bead furnaces have a contained volume of 14 l, while this furnace would result in a contained volume of 131 l, the build was named the Mother Of All Furnaces (MOAF).
A ring of bricks was placed in a circle with their inner sides forming a 30 cm circle. In this way, the walls could be built on top of the bricks. Individual bricks could be removed later to provide air-ports. Each brick is 6x9 cm in cross section, making each port 54 cm2. The walls were built around a standard 20 lb propane tank to provide a stable 30 cm internal diameter (See Figure 1).
As the construction got near the top of the tank, it was pulled out, and the inside surface was patched. Working only from the outside, it is difficult to ensure a solid construction - by taking the time to ensure a solid blending on the inside of the clay, cracking can be reduced. The interior was then filled with a 50-50 mix of dry wood ash and coarse sand, however when the mix ran out and we used charcoal fines in lieu. The packing serves both as a sponge to draw water out of the cobb, and as a support for the structure as it grows. The tank is then placed on top of the filling and the process is repeated (See Figure 2 and 3).
When the furnace was fully formed two ports were cut into it, on opposite sides. These were set at heights that would allow testing of "seated" and "standing" working positions, then we left the furnace to dry (See Figure 4).
The final "wet" height ranged from 151 to 154 cm of which 9 cm came from the bricks at the base. The outside width at the top was 40.6 cm, with an internal diameter of 31 cm and thus an interior cross-sectional area of 755 cm2. The circumference at the top and bottom were measured to provide counter checks on the diameter: 135.9 and 177.8 cm respectively. Those measurements produce average diameters of 43.3 and 56.6 cm and show that single measurements of diameter have problems in the real world. The discrepancy between measured and calculated diameters is due to variations in both wall thickness and maintaining an even diameter (perfect circle) during the hand building and drying processes. The lower port was cut in at 94 - 95 cm (not quite horizontal) and was 12.7 x 5 cm. The upper port was at 117 cm and was 14.6 x 7 - 8 cm.
Unfortunately, the original plan had been to perform a burn that same day, but the build process took longer than estimated, and the burn needed to be postponed. As a result, a month passed before the furnace could be checked and a small mistake was identified. Usually, the packing is left in for a couple of days, then removed allowing the structure to finish drying. That step was omitted here. The problem (which should have been anticipated) with failing to empty the furnace is that the interior mix acts as a solid form. As the clay dries from "wet" through "leather hard" to dry it shrinks - typically 10-15%. Since the furnace could not contract against the packing materials, the walls cracked. In this case, it was a spiral crack through the weakest points, passing from just above the base, running diagonally through the lower working port, and extending beyond it.
The widest part of the cracking was about 2 cm and extended fully through to the inside of the furnace. The crack was patched on Aug 25, allowing the newly applied clay time to dry and shrink before the planned firing (See Figure 5).
1 Sept 2018 - The Burn
Burn day began with drilling out a series of "light brights". Four bricks were removed from the base to act as air-ports. The total area of those ports was 195 cm2. This area gives a ratio of inlet to the interior cross-section of the chimney of 195:755 or 1:3.8.
The patched crack could easily lead to a "barrel fracture" (Pulling the crack further and further open) due to a couple of different forces - the first force is applied by the clay contracting as heat removes the last traces of moisture, with a second force applied by the expansion of the dry clay as it approaches high sintering temperatures. The pre-existing crack provides a weak area in the structure where these forces can produce a failure. To avoid such a failure, a few wire wraps around the furnace were installed to add additional support (roughly every 20 cm). The working ports and crack were then sealed to maximize the draw through the bottom air-ports.
The furnace was loaded with several small branches and paper, then ignited. The goal was to burn a slow fire to drive out any residual moisture in the cobb and heat the furnace body. This pre-heat ran for 69 minutes and during this phase we experienced the first surprise. The air draft in the chimney was quite impressive and highly variable. The feedstock was small branches (smaller than a thumb diameter) about 30 cm long. A bundle of branches about 20 cm across would cause a massive shift in temperature and draft over a very short period - less than 2 minutes. One such cycle resulted in an increase of over 370°C in that short a period.
At the 69-minute mark, charcoal was added. In doing iron smelts DARC had gotten into the habit of using a standard âbucketâ of charcoal as a measurement. This bucket holds approximately 5 l / 1.8 kg of charcoal, although the exact weight can vary depending on the humidity â and hence the moisture content of the charcoal. Charcoal mass will also change based on species. DARC normally uses commercially produced lump charcoal of either maple (Acer sp.) or oak (Quercus sp.) for experiments requiring charcoal. Both are readily available in Canada and represent species known from Viking Era Scandinavia. This experiment sequence used oak. Following a recommendation in Rehder (2000), a larger size of charcoal than normal was used. In previous experiments, the charcoal was between 0.6 and 2.5 cm in diameter. To ensure this consistent sizing the charcoal is hammered through a metal grid with 2.5 cm openings, and then sifted on a 6 mm screen. Using a consistently smaller size was a lesson from the iron smelts. The 6 mm screen removes the dust, avoiding clogging the air flow in the column and allowing for uniform movement of the charcoal into and through the burn area. The lack of larger pieces helped to avoid bridges forming in the charcoal and creating cooler void areas. For this experiment, the charcoal was not broken up, instead, it was used directly as provided, providing a larger average chunk size (closer to 3-5 cm). A larger chunk size allows for easier air flow between and around the charcoal allowing air to move more effectively through the tall stack of the furnace.
The first goal was to find out how tall the "heat-zone" of ignited charcoal could be built. This was done by looking down from the top (with face shields on) looking for the time when all of the charcoal was burning. The hope was that the ignited column would build up to just under one or the other of the working ports. Sadly, that wasn't the case.
Each bucket of charcoal added approximately 10 cm of charcoal height. Buckets were slowly added while checking the burn level. At approximately 2 hours into the experiment and at 50 cm of depth, the ignited charcoal was burning away before the surface charcoal was engaged. This is one place where the âlight brightsâ aid in observation. It is possible to look through them and see the colour of the charcoal. Orange is burning charcoal clearly showing the charcoal ignited at that height. Black is charcoal that has not ignited. Temperatures just below the lower working port reached a general peak at this time at 700°C just below a good working temperature for glass.
Since a stable point had not been reached, a change of method was proposed. We rapidly added three buckets of charcoal to test the impact of a larger fuel column. The ignited column remained at 50 cm, although it was possible to have the system run for a long time without additional charges of charcoal.
The next significant observation, at the 2 hour 30-minute mark, was that there were flames being drawn inwards from the exterior through the light brights. In forced air systems, DARC has become used to seeing flames coming out of these small openings. The colour and length of the flames can be used to approximate conditions inside the furnace at that height. In this case, the flames being drawn in show that air was being pulled into the stack through the light bright. Air being drawn in above the level of the charcoal would decrease the amount of air entering through the inlets at the bottom, and thus reduce the oxygen available to provide combustion within the charcoal. This is a good reminder that natural draft systems are easily disrupted by such cracks and holes. All visible cracks were re-patched and the light brights not in use for a thermocouple were plugged to reduce this unwanted airflow (See Figure 6).
At approximately the same time it was noted that the internal temperature had gone down and not returned to the desired level. By 2 hour 36 minutes, the temperature was down to 546°C. An investigation showed that the furnace faced a second problem. When building iron smelters and other bead furnaces, the tuyeres were always placed above ground level and pointed down. Placing them above ground level is necessary because as the burn progresses the charcoal will leave behind ash. The design of the MOAF had the air-ports on the ground which was a mistake that could have been avoided. By this point in the burn, about 50% of the air-port cross-sectional area was obscured by ash buildup. The ash was preventing air from getting into the furnace body and was one likely contributor to the reduced temperature. This blockage was addressed by rogering out the openings with a trowel and a longer rod, emptying the ash into the area around the furnace. An immediate increase in temperature was observed (See Figure 7).
The second problem visible at this time was that the size of the charcoal pieces visible in the air-ports was much smaller than the desired 3 â 4 cm diameters. This is a result of the larger pieces burning away while they dropped, leaving only smaller pieces at the bottom. Unlike earlier in the firing process where there would have been a mix of sizes at the bottom, the time had allowed the accumulation of these smaller pieces. The obvious problem is that the smaller pieces form a tighter packed body making it more difficult for the air to be drawn in. With less air coming in, less charcoal can burn, thus reducing the overall temperature.
Both problems could have been easily addressed by mounting the air-ports/tuyeres 10 - 20 cm above the base of the furnace. Given that the experiment in progress is a bad time to try drilling holes in the furnace it was decided to try removing an additional brick, increasing the total inlet area by 54 cm2. This action changed the ratio of inlet to outlet cross-sectional areas to 249:755 or 1:2.9. At an observational level the flames at the top of the furnace which had been blue indicating a reduction atmosphere, changed to orange (an oxidizing atmosphere) showing that more air was entering the overall system. Over time as the ash/charcoal built up again and again the flames would change from orange to blue and back to orange as ash was pulled out and more air was allowed in.
At 3 hour 6 minutes into the experiment, the sound of the furnace changed. Previous smelt and bead furnace experiments have shown that sound is important. When the sound changes something has happened inside the reactive area, possibly where it canât be seen. In this case, a popping sound was noted. Tracing the sound and adding a visual search revealed that intermittent draws of air around the lower working port were occurring. These were injecting oxygen into the column where there were combustible gasses but insufficient oxygen for them to burn â causing a small explosion as the gasses ignited. Our supposition was that the explosion would push outwards, blocking the airflow and choking off the oxygen. When this expansion stopped due to lack of oxygen, more air could come in around the port, setting off a new pop of ignited gas. Additional patching around the working port was added and the system settled down.
From 2hr 30m to 3hr 30 minutes the sequence was to add charcoal, watch the temperature rise then fall, roger out the inlets, watch the temperature rise and fall, never getting hot enough to work glass, and discuss options. One of the fun ideas with a pilot experiment is that since there isnât a specific question being asked/answered the experimenters can change the system on the fly to explore working conditions or improvements. This process, as one by-product, generates questions for future experiments. In this case, the options being debated were opening more bricks or adding tuyeres (pipes). Removing more bricks would allow more air in (but at a lower pressure) while inserted tuyeres would aid the air in getting to the center of the stack. Eventually, it was decided to explore both alternatives.
At 3 hour 30 minutes three additional bricks were removed adding 162 cm2 of air-port and increasing the inlet to outlet ratio to 411:755 or 1:1.8. This increased the temperature but still only to a point below the desired level. At 3 hour 42 minutes four pipe tuyeres were added to route the input air deeper into the body of the furnace. The internal ends of the pipes were set approximately 25% of the way in and as high as possible to avoid the ash. The openings around the pipes were sealed with clay. Three pipes were 3.5 cm interior diameter, the other was 2.5 cm internal diameter. This meant 208 cm2 of inlet were replaced with pipes totalling 34 cm2. Input area was thus 228 cm2 giving a ratio of 1:3.3. This caused a temperature drop; likely as not enough air was getting through the ash and small charcoal. Without the pipes, the air could at least get in and move along the inside edges of the walls (See Figure 8).
By the 4 hour 35 minute mark the team was confident that no amount of adjustments or clearing of the inlets would raise the temperature to the desired level. A second variable which impacts the efficiency of a natural draft furnace is the total stack height. A metal collar was added to the top of the furnace to increase the total stack height from 150 cm to 185 cm. This change in the stack height caused the temperature to increase by nearly 100°C quite rapidly. The system was monitored for an additional half hour, but no additional temperature increases were observed (See Figure 9).
At 5 hours into the experiment, most potential new observations from this pilot run were complete. There was, however, at least one additional question worth examining. What would happen if a working port was opened? This question was of particular interest for the bead makers who had been patiently waiting all day for a high enough temperature to make beads.
A thermocouple was mounted immediately below the working port to be opened, and initially showed a temperature of 560°C. When the port was opened it was noted the level of the charcoal was just above the lower edge of the port. This charcoal was not burning at the time. Within one minute the temperature had jumped from 560°C to 1013°C and continued to climb to 1093°C over the next minute. This change came from feeding a lot of air right into the charcoal around the probe. The air was being drawn in through the working port. It had been expected that the temperature would drop sharply when the port was opened due to the inrush of cold air. The difference between the expectation and observation was both the height, and the effect on the charcoal bed in the furnace. In this case, the bed was high enough that the probe was inside the charcoal but in the area where the extra oxygen caused increased combustion. As the level of the charcoal dropped the temperature rapidly started to drop (see the measurements at 5 hour 6 minutes and 5 hour 7 minutes). It is also worth recording that the radiant heat at the working port was impressive and would take an adjustment to get used to bead working in that area.
This point also marked the end of the planned activities. Because bead making equipment was handy it was decided to see what impact a simple addition of a bellows might have. This was done with an eye to raising the temperature just enough in the port to allow bead making for those who had been patiently waiting for many hours to try. An electric blower was also added later to try and allow some bead making. Neither was particularly effective although some beads were produced.
Time | Notes | Charcoal (buckets) | Total Charcoal (buckets) | °C @ top | °C @ 140 cm | °C @ 120 cm | °C @ 90 cm | °C @ 40 cm |
0h 0m | Start heat with small wood | |||||||
0h 6m | 429°C | |||||||
0h 25m | Temperatures highly variable | 209°C | 306°C | 214°C | 246°C | |||
0h 40m | External temps 55°C at base, 65°C @ 30 cm and above | |||||||
1h 9m | First charcoal addition | 1 | 1 | |||||
1h 15m | 350°C | |||||||
1h 18m | First bucket fully red | 1 | 2 | |||||
1h 22m | 97°C on the outside at the top | 1 | 3 | |||||
1h 34m | 1 | 4 | 604°C | 580°C | 675°C | 800°C | ||
1h 39m | 1 | 5 | ||||||
1h 50m | 639°C | 634°C | 700°C | 560° C | ||||
1h 52m | 1 | 6 | ||||||
1h 58m | 1 | 7 | 604°C | |||||
2h 8m | 3 | 10 | ||||||
2h 12m | 555°C | 500°C | 450°C | 755°C | ||||
2h 30m | 630°C | 581°C | 546°C | 916°C | ||||
2h 45m | 3 | 13 | ||||||
2h 53m | Extra Temps: 1010°C @ 30 cm; 800°C @ 50 cm, 655°C @ 60 cm | 487°C | 435°C | 475°C | 810°C | |||
3h 6m | Charcoal at 50 cm | 1 | 14 | 505°C | ||||
3h 15m | 440°C | |||||||
3h 30m | Still burning at 50-60 cm | 550°C | 550°C | 940°C | ||||
3h 42m | 1 | 15 | ||||||
3h 51m | 3 | 18 | 490°C | 434°C | ||||
4h 6m | 240°C | |||||||
4h 10m | Rogered air-ports | 179°C | ||||||
4h 20m | 2 | 20 | ||||||
4h 25m | 260°C | |||||||
4h 26m | Rogered air-ports | 290°C | ||||||
4h 30m | 356°C | |||||||
4h 35m | Added metal collar | 463°C | ||||||
4h 38m | 500°C | |||||||
4h 45m | 1 | 21 | 390°C | |||||
5h 0m | 540°C | |||||||
5h 2m | 560°C | |||||||
5h 3m | 1013°C | |||||||
5h 4m | 1093°C | |||||||
5h 5m | See extended note below | 978°C | ||||||
5h 6m | Added bellows to one tuyere | 946°C | ||||||
5h 7m | Put the large plug back into the port. Keep pumping bellows. | 811°C | ||||||
5h 9m | 727°C | |||||||
5h 11m | Temp @ 30 cm = 956°C | |||||||
5h 14m | Temp @ 30 cm = 987°C | |||||||
5h 15m | Add blower, stop bellows, open working port | |||||||
5h 20m | Simple beads were made | 720°C |
Table 1. Results of the experiment
Results
Several conclusions were drawn from this pilot experiment which can feed into future experiments and considerations about the design and possible explanation of hearth QA.
Mounting the inlets right at the furnace base was a mistake. The accumulating ash needs some place to go. Also, as individual charcoal pieces are consumed, they get smaller, reducing the gaps between them that allow air into the system. In retrospect, this should have been obvious based on DARCâs previous smelting work. A shallow pit, extending below the inlet level, would have provided a space for ash to collect into without blocking these air intakes.
A ring of tuyeres, sticking in approximately 6 â 7 cm, on slight down angles, would have moved the location of input air further into the interior of the furnace. Ideally, this should create a more even burning of the interior volume.
Air flow is a complex equation, needing to balance the draw both in terms of enough air to support the combustion, and enough pressure to move through the charcoal mass. Rehderâs Mastery and Uses of Fire (2000) is the primary reference source here. This furnace was fired with ungraded charcoal (to match the diameters suggested in the book) as the normal graded charcoal size would be a tighter mass, making air penetration more difficult.
One related observation will affect the planned iron smelting experiment sequence intended for the Fall season. It was originally hoped this âtall stackâ furnace would effectively generate the required 1200°C temperatures through a passive air draw. This temperature range is clearly not available with this specific furnace design. The team felt that it should prove possible to modify the existing structure as defined above to generate the required temperatures (potentially by modifying the air input system).
13 Oct 2018 - A Day of Redemption
An opportunity arose on 13 Oct to revisit the MOAF for an experiment to run a full bloomery iron smelting sequence, based on Roman era examples. The furnace was still in excellent shape and some basic modifications were possible. Openings for the tuyeres were drilled 20 cm above the ground at the normal 22° down angle. The tuyeres were inserted 7 â 8 cm into the body of the smelter. This represents 25% of the diameter and was chosen to get an overlapping hot spot in the center of the furnace. A careful reading of Rehder (2000) implied that 4 pipes of schedule 40 mild steel with 3.5 cm inside diameter should provide adequate input air flow (See Figure 10).
The charcoal was sized differently than the initial pilot experiment as well. This time the charcoal was screened on a 2.5 cm grid removing all material that fell through the grid, increasing the average particle size closer to 4 â 5 cm. Unlike the first pilot experiment, the furnace was equipped with three thermocouples that were monitored continuously. One of the thermocouples was damaged part way into the experiment throwing its later values in question but the other two seemed consistent.
The process followed was a simple one, beginning with a basic wood preheat for 44 minutes. Then getting charcoal added/ignited. At that point, the furnace was filled with charcoal, and more as added whenever the level dropped low enough (See Figure 11).
The output graph for the thermocouples clearly shows that these changes were sufficient to generate temperature levels well above those required for working glass (See Figure 12).
A final experiment step is required at some point in the future to figure the best location for glass working and the impact that port has on the draft.Can ports in the side work or is a different placement required?
Ash levels were very high during the warmup burn with wood, but overall, they appeared lower when burning charcoal. This is a visual observation only as there was no data collection on ash during this pilot. Obviously, as more experiments are run this will be a useful measurement to gather. Possibly the reduced ash level observed is due either to the increased height or to the reduced airflow. How this would relate to ash in the working ports is also an interesting question.
Conclusions
This test of the basic hypothesis of a natural draft furnace capable of bead-working temperatures built to scale for hearth QA must be considered plausible. The temperatures generated match the required profiles. Within experimental archaeology we may produce more than one reconstruction which matches all required parameters. When this occurs it is important to judge on different criteria whether all successful reconstructions are equally as likely to represent what was actually used at the time.
Many of DARCâs previous experiments involved reproductions based on a different hearth at Ribe - hearth ĂZ, a 30x60 cm oval hearth (see Peterson, et al., 2014 for additional details). Enclosed furnaces 25 â 40 cm in height built to these dimensions also provide stable bead production platforms.These furnaces can run 30 - 45 minutes at an appropriate temperature between reloads of charcoal. They use about 12 kg of clay, about the same of sand, 10 l of horse manure and around 3 person-hours to build. A total of 8 kg of charcoal can run such a furnace for a full day, requiring a bellows operator and a bead maker.
In contrast MOAF required over 136 kg each of clay and sand with proportional amounts of horse manure and 4 person-days to build.The five-hour burn used over 40 kg of charcoal, and 3 more person-days to run.Both in capital investment and in operating costs MOAF is significantly less cost-effective than the smaller forced air bead furnaces.
The natural draft system proved extremely sensitive to variations in air flow. The system as built needs a person constantly clearing the air-ports. Granted this is a lower skill/effort job than operating a bellows but is the difference enough to matter? If the operators are clearing ports why not just put them on a bellows with a smaller furnace that is easier to build and uses less raw material?
Burn rates on a charcoal bucket were close to those normally obtained with iron smelters (See http://www.darc.ca/iron for comparative times), estimating 10 minutes per bucket. It should be possible to configure this system to accept large cycle additions (3-4 buckets) while maintaining a working temperature the whole time (estimated 30 minutes). Of course, one of the smaller bead furnaces can run at working temperatures for the same length of time using less than one bucket of charcoal (and less construction material/labour) - so again why do the big build? Nothing in the natural draft experiment series, however, mitigates the excessive costs (both capital and operational) of this class of furnace.These facts force the team to conclude that hearth QA could plausibly be used as the base for a natural draft bead furnace, but that due to construction and usage costs it was unlikely to have been used in that fashion.
Keywords
Country
- Canada
Bibliography
Bencard, M. and Jørgensen, L.B., 1990. Excavation and Stratigraphy. In: M. Bencard, L.B. Jørgensen, and H.B. Madsen, eds. Ribe Excavations 1970-76, Text Volume 4. Esbjerg: Sydjysk Universitetsforlag. pp.15-168.
Jensen, S., 1991. The Vikings of Ribe. Den antikvariske Samiling, Ribe.
Peterson, N., 2017. Kicking Ash, Viking Glass Bead Making. EXARC Journal 2017/4 [e-journal]. Available at: https://exarc.net/issue-2017-4/ea/kicking-ash.
Peterson, N., Backa, S., Ross, J. and Schweitzer, R., 2014. Glass on Fire: Temperatures in reconstructed Viking Era bead furnaces. In: M.A. Cramer, ed. If these Bones Could Talk Vol II. Wheaton, IL: Freelance Academy Press. pp.27-44
Rehder, J.E., 2000. The Mastery and Uses of Fire in Antiquity. McGill-Queen's Press.
Further Reading on Natural Draft Furnaces
Asmus, B., 2009. A Natural Draught Furnace for Bronze Casting. In: J. Mei and Th. Rehren, eds. Metallurgy and Civilisation: Eurasia and Beyond. Archetype: London. Available at: https://www.researchgate.net/publication/299536984_A_natural_draft_furnace_for_bronze_casting.