The content is published under a Creative Commons Attribution Non-Commercial 4.0 License.
Reviewed Article:
Socketed Axes of the Irish Late Bronze Age: Understanding the Internal Rib Phenomenon
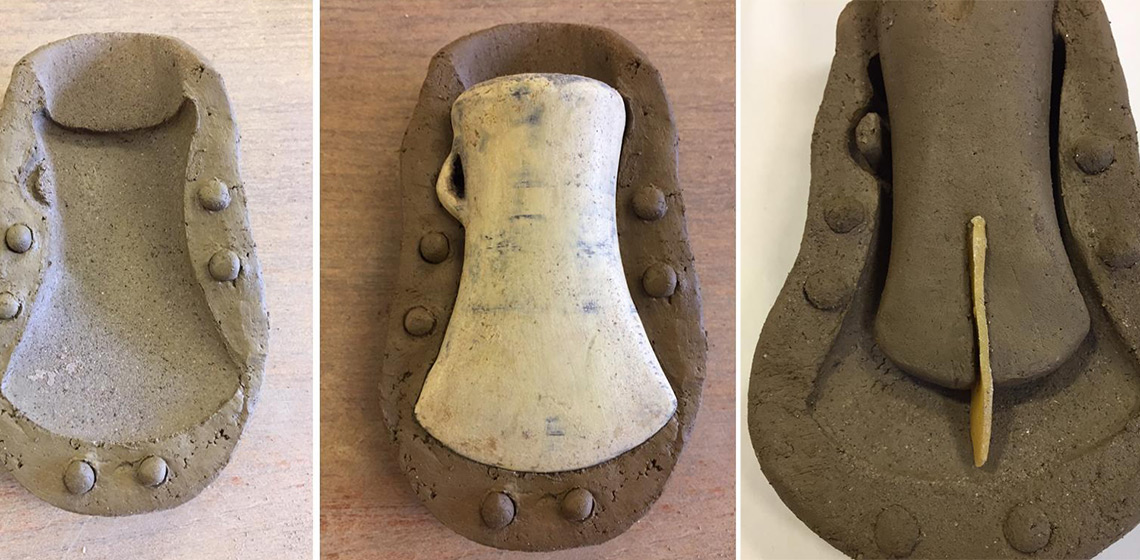
This study explores the possibility that the internal rib commonly recognised inside bronze socketed axes may suggest an entirely different step in the casting process than previously thought. The internal rib, more commonly referred to as a ‘hafting rib’, has always been regarded as a functional addition to help tighten the grip of the haft once fitted into the socket. However, many of the internal ribs inside bronze socketed axes produced in Ireland do not appear to optimize this function and in some cases contradict this implied intention all together. This study demonstrates that there are recognizable trends in their form that indicate a replicated step in the casting process and further suggests that the rib may be the signature focus for a procedure closely related to a casting technique.
Introduction
The bronze socketed axe is perhaps one of the most ubiquitous tool forms of the Late Bronze Age respectively (See Harding, 2000 for a more comprehensive breakdown of the European Bronze Age). These axes have been found across Western Europe, with typologies stretching to the island seascapes of Ireland from as far away as the Carpathian Basin of Central Europe (Dietrich, 2015). Socketed axes have been produced in many different shapes and sizes, which suggests their broad versatility as a tool. While the variation in form and size can tell us the story of their practical and perhaps social use, one such feature, the internal rib, often seen in forms from Ireland, stands out to tell us a story of their creation. My 2018 master’s thesis explores the possibility that the internal rib indicates a step in the casting process of bronze socketed axes in Ireland during the 12th through seventh century BC.
In brief, an internal rib is a raised ridge cast into the bottom of the socket of bronze socketed axes (See Figure 1). While not present in all forms, internal ribs have been recognized in socketed axes throughout Scotland, England, Wales (Evans, 1881, p. 110; Burgess and Miket 1976, p. 5), and in northern Europe beginning in the Montelius Phase IV becoming inherent during Phase VI (Baudou, 1960, p. 17). Internal ribs have a strong presence in Irish examples showing a high frequency in the ‘bag-shaped’ trend of the Dowris Phase (900-500 BC). In most cases bronze socketed axes contain a single vertical rib, while others contain as many as five consecutive vertical ribs (See Figure 2). For the most part, the vertical orientation of the ribs is their defining attribute, beginning from the bottom of the socket and reaching to various lengths toward the rim. However, some less common forms have a single vertical rib with two divergent ribs that appear to angle toward it (Ehrnberg, 1981, p.215 Fig.1, 3b).
Some researchers studying and classifying bronze socketed axes have accepted the early interpretation that the internal rib is a functional addition related to the hafting of the axe head to the handle, sometimes referred to as “hafting ribs” (Pitt-Rivers, 1906, p. 184; Maryon, 1938, p. 214; Baudou, 1960, p. 17). This interpretation suggests that the internal rib acts as a wedge to split the haft once fitted into the socket to expand the wood to create a more robust connection. Some researchers (Ehrnberg, 1981; Rynne, 1983) interested in the internal rib feature would reject this interpretation first on the basis that if this were to be the primary intention of the rib, all of the iterations of internal ribs would optimize this intention, and secondarily, none of the previously suggested explanations for the creation the internal ribs (i.e. two part core, air vents) seemed practical during a live casting.
Considering internal ribs within the casting system, Ehrnberg (1981, p. 215) contends that while internal ribs may be the result of cut channels to improve the flow of metal, they may also be markers for centring the core within the mould. Rynne (1983, p. 48) alternatively argues that the internal rib may be the outcome of wax strips set in place to centre the core (often referred to as a chaplet or pin) while metal is poured into the mould. Evidence of chaplets has been discovered only in context with socketed spears (Grimes, 1931, p. 358) and horns (Holmes, 1979, p. 180), which provides supporting evidence to suggest their use in clay moulds. Evidence for chaplets in socketed axe casting has yet to be distinguished, though it may be argued that both socketed spear and horn moulds have difficult-to-manage cores requiring the use of further support. The absence of these features in context with socketed axe casting suggests a reasonably good method for centring and stabilizing the core or perhaps that the method in practice is archaeologically invisible.
The use of wax suggested by Rynne (1983, p. 49) as a chaplet is seemingly viable considering that beeswax is a natural resource with evidence of its use in prehistory. Wax in an archaeological context has been analysed in ancient Roman (Kimpe, Jacobs and Waelkens, 2002) and Greek (Evershed and Dudd, 2003) contexts revealing itself in pottery and as well in early Egyptian embalming practices (Ménager et al., 2014) among others. In prehistoric European regions however, wax has been somewhat rare and even more so in metallurgical contexts. Interestingly, a recent study in Poland has revealed traces of beeswax on the interior of a bronze mould valve for the casting of a socketed axe (Baron, Miazga and Nowak., 2014). At the very least, this presents reasonable evidence for the use of wax in the bivalve casting process outside of the common cire perdue [lost wax] method that had undoubtedly been employed to create more complex bronze forms (see Auenmüller, Verly and Rademakers, 2019, 142). While the possible use of wax strips suggested by Rynne (Rynne, 1983, p. 49) was confirmed upon testing, the mould materials involved in Late Bronze Age socketed axe casting were never considered, which thereby omitted the critical technical parameters necessary to cast bronze. Altering the mould system in which the internal rib becomes relevant would significantly change the possible reason for internal ribs making any interpretation archaeologically irrelevant.
Therefore, the objective of my project was to rebuild the Late Bronze Age socketed axe casting system as understood through archaeological evidence in Ireland, but with the view to recompose the wax strip in a different part of the chaine opératoire of socketed axe casting and to compare the morphology of internal ribs made from cut channels. This reconstruction experiment allows for morphological comparisons between the impression of a wax strip and cut channels, as well as for additional observations on how the wax strip—acting as a chaplet or pin to hold the core in place—assists the alignment of the central core in the context of clay moulds. The information from the experiment is then cross-compared with a reference collection of sample internal rib traits collected during this study. This paper describes the morphological trends among common examples, relates bronze socketed axe casting evidence found in Ireland, and then discusses the results and findings of the experiment.
The internal rib morphology
Although bronze socketed axes are of considerable age, their composition (usually copper, tin, and lead being the main body) is not subject to the same corrosive pattern as iron (Turner-Walker, 2008 p. 48). The advantage of studying bronze artefacts is that tool marks and other indications of the manufacturing process are more likely to survive. For socketed axes another protective condition is the socket itself because the interior is sheltered not only from post-depositional wear, but also from the post-casting process, which leaves the interior relatively intact. Micro abrasion from the use of the tool in contact with the wooden haft could alter the shape and form of the rib, but presumably in distinguishable patterns if at all. These factors contribute to an opportunity to observe patterns of the mould system directly in confluence with the core and internal rib.
In considering the morphological attributes within the scope of this study, I first outlined how they are represented amongst known socketed axes, primarily through referencing George Eogan’s The Socketed Bronze Axes of Ireland (2000), which catalogues all examples known to have originated in Ireland. Descriptions of each socketed axe (length, weight, and cutting edge) were recorded along with the heights and numbers of the internal ribs that appear inside the sockets. Many of the bronze socketed axes recorded for Eogan’s catalogue were dispersed upon recovery during the 19th century or recorded more recently at auction, so effectively Eogan’s catalogue could have either incorporated a wider range of examples or been even shorter, given the luck of timing. None the less, Eogan’s corpus of work comprises 2100 bronze socketed axe examples and is the most current collective survey on Irish bronze socketed axes. Since the time of this publication, some 500 new examples have made their way to the collections of the National Museum of Ireland (S. Weadick, Personal communication, 13 June 2018).
To narrow the focus for the scope of this study, I began by quantifying the frequency at which ribs appear (in other words, how often single or multiple ribs appear) within the most common class of socketed axe. Internal ribs most frequently appear within the Class 11 (1700) set otherwise known as the ‘bag shape’ trend, with a further prolific style classified as the Class 11A subset (509). From this category, I further narrowed the focus to 10 representative samples based on internal rib frequency, length, and the relative size range of socketed axes they are represented in. The most common frequency of internal rib was found to be represented by a single short rib.
The ten bronze socketed axes examined for this study retain novel characteristics and shared features. In nearly all examples, the internal rib feature in profile form is either a U- or V-shape, likely depending on the acute angle of the core that forms the socket tapering in toward the bottom or blade. The height of the internal rib from the bottom to the rim, although categorized as ‘short’ varies considerably (sometimes barely present to nearly half the depth of the socket). In practice, these features may not have needed to be uniform in height, but simply present. The difference between the U- and V-shaped rib profile is likely a replicated practice subject to the arbitrary relationship between the composite materials and the maker. Another interesting feature of the axes is that some internal ribs seem to ‘twist’ along their length and strikingly realign at the bottom. This feature suggests that the tool responsible for making the impressions in the core is a single piece and thus negates the possibility of a two-part core off-set during registration. Alternatively, the twist and realignment could mean that the rib was created with a single cut from one side of the core to the other. Yet another novel feature of the samples is the appearance of ribs at a slight ‘tilt’, as if the impression making the internal rib in the core was either not correctly aligned or had shifted upon placing the core in the mould. My current interpretation of this feature is that a channel is created with a single tool and perhaps the ‘tilt’ and the ‘twist’ occur upon closing the mould system around the core, which suggests that the tool used to make the internal rib remained in place upon closing the mould. Whether or not this could have been the case can best be demonstrated in an actualising experiment in a recreated socketed axe mould. The current evidence for bronze socketed axe casting in Ireland, particularly in relation to socketed axes of the ‘bag shaped’ trend, is explored in the next section.
Bronze socketed axe casting technology in Ireland
At present only four stone moulds containing the matrices for socketed axes are known in Ireland (See Ó Faoláin, 2004, Fig 35A, 35B, 36A and Eogan, 2000 Appendix D). Though little contextual evidence associated with these moulds remains, the matrices would produce socketed axes that fall within Eogan’s class 14 and 17 types, in parallel with the Sompting Type axes of Brittan, which places their dates approximately within the late Dowris Phase (900-500 BC) (Burgess, 1969, p. 267). However, the first socketed axes appeared within the Bishopsland Phase (1350-1000 BC), particularly in the Bishopsland Hoard (See Eogan, 2000, Class 1., No. 3) and along with them came a new approach to casting technology – the clay mould. Ó Faoláin (2004, p. 9) suggests that the first evidence for clay moulds come from the Bishopsland hoard, as seen in the form of a complex ‘rope’ matrix around the neck of a socketed axe and the hammer. During the Late Bronze Age, clay moulds dominated the manufacturing process and subsequently became a common find amongst Late Bronze Age casting assemblages.
Internal ribs produced in the context of clay moulds are somewhat difficult to determine. A study exploring stone, bronze, and clay mould materials has shown that both stone and bronze moulds produced very little flashing, whereas in moulds made of clay, flashing was quite common (Heeb and Ottoway, 2015, p. 181). Nearly all of the bronze socketed axe examples examined for this study show signs of misregistration and flashing, which makes a suitable argument that internal ribs were likely produced within the context of a clay mould.
The very nature of clay mould casting, along with the friability of the materials, leaves a very fragmented picture of the casting process. I supplemented the evidence I reviewed with the National Museum of Ireland catalogue entries of socketed axe valves, pouring cup fragments, potential cores, and even some items described as both pouring cups and gates. I also considered casting debris (bronze removed from the intended form) and especially objects identified as casting jets (that is, the remnant potion of bronze that would fill the pouring cup), which could provide information on the interface between the gate, core, and the intended object.
In Ireland remnants of clay moulds are rare. Fortunately, at sites such as Dún Aonghasa, County Galway, Rathgall, County, Wicklow and Dalkey Island, County Dublin fragments of clay moulds have survived (Liversage et al., 1967-68; Cotter & Barklie 2012; Becker, Personal communication, 25 July 2018). These clay fragments provide information on mould materials and the mould building process, while casting jets from Tullowbeg, County Carlow and Money Lower, County Wicklow indicate the pouring cup and runner configuration (See Figure 3). Although it is not certain whether these casting jets result from casting socketed axes, their width would indicate a system meant to cast an object around the average rim width of socketed axes to make the double gate system consistent with flashing (remnants of the sprue) seen in some socketed axe examples.
The body of clay moulds from Dún Aonghasa were consistently layered with finer clay on the interior to a courser exterior wrap. Two of the valves were thin sectioned and subjected to a petrological examination (Unitt, 2012, p. 33). The report determined that there were three fabric groups for all ‘ceramic’ fragments found and revealed that the innermost layers of the socketed axe moulds were made up of a well-crushed temper comprised primarily of quartz (up to 1 mm). The third fabric group consisted of only one example containing much larger inclusions (up to 2 mm) at a higher volume. Mould valves from Dalkey Island (Liversage et al., 1967-68, p. 148) and Rathgall (Becker, Personal communication, 25 July 2018) were also reported to have an inner layer consisting of finer quartz temper with a coarse outer wrap.
An elusive feature of socketed tool manufacturing is evidence for cores. The core is the central part of the mould that blocks out the space making the socket. Some early interpretations for the core have been put forward (Pitt-Rivers, 1906, p. 185; Maryon, 1937, p. 213; Hodges, 1954, p. 133) that informed later descriptions of the manufacturing process (Tylecote, 1962, p. 123; Eogan, 2000, p. 5) asserting a system that combines the gate and the core as a single unit. Evidence for this system, otherwise known as a ‘gate-core unit’, has been interpreted from finds at Haag, Jutland (Neergaard, 1910, p.151 fig. 29), and may well have been used in the Bulford-Helsbury stone moulds found in Southern Britain (Needham, 1981, p. 27). However, the evidence for the gate and core at Dalkey Island (Liversage, 1967-68, p. 149), Dún Aonghasa (Cotter & Barklie, 2012, p. 41) and from my own observations of core fragments from Rathgall suggest a system where the ‘pouring cup’ is an extension of the outer wrap and the core is clamped at an extension of the valve above the axe, referred to by Coghlan (1962, pp. 57-58) as ‘core-prints’. An example of this can be seen in the Late Bronze Age mould finds at Jarlshof, Shetland, where a nearly intact valve was discovered (Hamilton, 1956, fig 14, p. 4). The provisions for a core-print can also be seen in a wooden socketed axe model found in Tobermore, County Derry (Hodges, 1954, p. 64, fig. 3).
The materials that make the core have been an engineering challenge because after the cast is complete, the core must be removed. When bronze is poured into a mould, the core becomes encased. As the bronze cools, it shrinks, gripping the core. The ‘bag shape’ trend of the Late Bronze age adds a further technical complication because many of the sockets are ‘waisted’ (Tylecote, 1962, p. 123), such that the flanges of the socket flare with the blade making it impossible for the core to be taken out as a single piece. The archaeological evidence for core technology during the Late Bronze Age suggests that the material of choice was clay (Ó Faoláin, 2004, p. 38). Evidence for cores at Dún Aonghasa are fragmentary, abraded and, retain very little distinctive core-like qualities, while core fragments found at Rathgall are much more distinct. One fragment from Rathgall (E84: 1462) may be the top portion of a core with a double-gate configuration that would produce a casting jet such as those from Tullowbeg, County Carlow and Money Lower, County Laois.
While Tylecote (1962, p. 123) suggests that an important feature of the core is its permeability, socketed axe cores of solid bronze have been found near Saint-Germain-sur-Vienne, France (Cordier, 2012, p. 37) suggesting that it may not technically be necessary for cores to be made from clay, although it is uncertain whether a mould using this core produced a suitable bronze socketed axe. However, a 3D simulation of a stone socketed axe mould and core (See Garbacz-Klempka et al., 2017) revealed that while a double-channel runner is more efficient, the potential for porosity in the metal around the core remains. This suggests that porosity of the core body could alleviate air from being trapped around the core. To ensure that the cores and valves used in the experimental moulds for the present project were sufficiently tempered, a higher mixture of 1 and 2 mm quartz was used (up to 60% by volume).
Reconstructing the clay mould system for socketed axes
Given the available archaeological evidence outlining a profile of the clay moulding process in making bronze socketed axes, two theoretical possibilities for creating the internal rib formed the basis for my experiment. A total of 12 clay moulds were created using a 3D printed model of sample socketed axe No. UCD 2498. This socketed axe retains the classic ‘waisted’ shape of the Class 11A category measuring 68.3 mm in length. Its exterior shows signs of porosity, though its overall form is well defined. Its socket measures 53 mm in depth with a uniform ‘oval’ shape to its dimensions, which flares to the curvature of the blade. The internal rib appears to be sheared in the middle and bent slightly as a result of post-cast processing (See Figure 1, Right). These characteristics, along with the artifact availability in the UCD School of Archaeology Teaching Collection, made axe No. 2498 a prime candidate for replication. The axe was 3D scanned using a NextEngine Laser scanner, and 3D printed on a Flashforge 3D printer. The print was coated in a thin layer of epoxy and fitted with a wooden extension making up the ‘core print’ as suggested by the Tobermore models (See Figure 4).
The model was impressed into the valves to halve its thickness and ensure that the clay registers tightly around its form. The area around the matrix on the valve face was indented and fitted with balls of clay acting as registration keys to align both valves (See Figure 5). A number of clay mould fragments used to make socketed axes found at Dalkey Island (Liversage et al., 1967-68) as well as at Jarlshof, Shetland (Hamilton, 1956) and Traprain Law, East Lothian (Coles, 1959-60, p. 89) show similar methods termed ‘lug and socket’ (Ó Faoláin, 2004, p. 39). Because the model had to be removed, a release agent was applied before either valve was imprinted with the model. Evidence for a release agent in this process would be virtually invisible archaeologically, but it is inherent to the valve moulding process to prevent the clay from bonding to the model. Although ground charcoal or soot would have worked as a release agent during an experimental practice in bronze sword casting, fine ash was the most effective (Ó Faoláin and Northover, 1998, p. 71). Once the first valve was impressed and the keys set in place, the mould was left to dry leather hard before informing the second valve of the mould.
The third part of this mould, the core, was created next. Although Tylecote (1986, p. 123) speculated that the creation of clay cores would require a template referred to as a ‘core-box’ it was found during the experimental phase of this project that the core could be modelled freehand easily in a matter of minutes. Fitting the core into the mould took careful matching to the valve, given that the core of socketed axe No. 2498 curves slightly outward at the rim while also flaring at the bottom of the socket toward the blade. Gates and runners were cut and shaped on both sides of the core as suggested by the morphology of the Tullowbeg and Money Lower casting jets. The runners were matched to the shape of the Money Lower casting jet, which appears to be wide and rather shallow.
Some observations of the chaine opératoire in casting the ‘bag shaped’ socketed axe were made when considering how the core is placed between the valves. Because the flared end of the core is wider than the waist of the axe body, the core cannot be introduced into the mould after the valves have been put together. For the core to be placed into the mould, the valves must be open, such that the core can be placed into one valve while the second valve closes the system. The difficulty of leaving the valves open is that the core simply slumps to the lower valve. However, the slumping core problem was managed by allowing both the valves and core to stiffen to a leather-hard consistency before closing the mould. Even so, once the valves were closed, ensuring that the core remained equidistance from the valve walls remained an issue.
The next step was to cut the impressions that form the ribs. To do this I fitted the first six moulds with a wax strip formed into a V-shape and cut channels in another six in the same orientation (See Figure 6). Although centring the core became more manageable with the introduction of the wax strip acting as a chaplet, the system was difficult to close without the wax being pressed into the mould valves, a feature not observed in any of the archaeological examples (See Figure 7). The solution lay in ensuring that the strip had a wider base to displace the pressure against the walls. Furthermore, I placed the core between the valves by standing the core upright inside one valve and then closed the mould with the second valve. The stability of the core at this point depended on the fit of the core-print clamping the core in place.
The final stage in building the mould was to ensure that both valves and the core remained secure by applying an outer wrap. Mould fragments from all three sites reviewed above showed evidence for the application of an outer wrap encompassing the entire mould. A key function of the outer wrap is its ability to allow air through the mould fabric while locking the system together. This means that the outer wrap must be somewhat thick and at the same time porous enough to allow air to escape and water to evaporate. I achieved this effect by adding a concentration of 2 mm quartz inclusion without thoroughly smoothing the surface.
After the moulds had been completed, they were left to dry for several days where they were then force-dried at 200°C in an oven for six hours. The moulds were then introduced to an open fire for approximately three hours at temperatures in excess of 800°C and left to cool (See Figure 8). The following section describes the performance of the moulds during a live cast with the results of the reconstructed internal ribs.
Experiment and results
Once the casting process was complete and the moulds broken open, I learned that something had gone wrong. An expulsion of gas causing major defects had occurred consistently throughout all 12 of the moulds rendering them the equivalent of what I can describe only as bronze ‘Swiss cheese’ (See Figure 9). This unintended result did not mean, however, that no useful information came from the project. The result of these trial casts, while insufficiently producing a usable bronze socketed axe, did produce discernible differences in the performance of the methods used to produce the internal rib and gave additional information on the performance of the clay mould in the current approach.
For example, a comparison of the methods used to create the internal ribs shows that cutting a channel to create the internal rib (See Figure 10) produces a relatively thin profile compared to those created using the wax strip method (See Figure 11). The difference may be due to the thickness of the instrument used to cut the channel (a wooden knife) compared to the modelled wax strip, or alternatively, to the wax being displaced while being pressed into the clay. With so few samples under the extraneous conditions related to air entrainment, I cannot yet determine which factor was most responsible. Further observation of relatable attributes reveals no discernible tilt or twist as noted in the archaeological examples. All ribs produced seemed relatively straight as they were applied. I expected the impression from the remaining wax strip would be distorted while either being impressed or that perhaps it would be shifted upon closing the mould, but this did not occur. In the strip’s use as a chaplet or pin to hold the core in place, the wax strip did seem to prevent the core from shifting while drying. In contrast, the six examples with only the cut channels had shifted, regardless of the grip from the core prints. The wax strips were shaped relative to the contours of the mould valves, but the strips were not uniform and consistent throughout. Because the strips were too wide, the strips would press into the valves when the mould was closed, and were thus no longer aligned with the core in the centre of the mould.
It could be argued that the morphology of the internal rib is best observed by narrowing the focus to the internal ribs themselves, removing the complications of the clay mould system and pouring metal into a more predictable mould material. This approach would not, however, overcome the problem with previous interpretations seeking to understand this feature outside of the clay mould system in which the internal rib manifests. The morphology of the internal rib is not its defining feature, but a signature to support potential methods. Produced in any other context outside of the scenario in which they were created, the morphology of these features may be drastically different.
While the primary research intent was to explore the morphological features of the internal rib phenomenon, the larger picture of clay mould casting during the Irish Late Bronze Age and its current interpretation was an important ancillary component revealing some behaviours comparable to archaeological finds. Although removing the core from the socket is seemingly difficult after being baked hard, the core could, in fact, be removed in a matter of minutes by simply digging through the clay with a sharp tool. Additionally, soaking the core in water before attempting its removal loosens the clay, making removal easier. Removing the core in this way may explain why very little definitive evidence for cores appears archaeologically, while still producing some comparative materials for the core above the socket. Perhaps the most indicative evidence for the position of not only the mould itself but for the configuration of the double-gate is the outcome of the casting jet from nearly all the experimental moulds (See Figure 12, Right). As for the core itself, the portion that remained relatively intact is the extension above the matrix, which in part forms the gate that resembles fragment E84: 1462 found at Rathgall (See Figure 12, Left). This portion of the core would have likely been cut off before it was removed from the socket.
Final remarks
Demonstrated here is the use and advantage of an actualised engagement with archaeologically relevant materials to investigate how internal ribs become relevant within the sequence of bronze socketed axe casting. The methodology employed an experimental approach by presenting the implied placement and morphologies of wax chaplets and cut channels. This approach has provided some comparable results while demonstrating that the processes of Bronze Age metal casting, although widely described and generally accepted, have yet to consider in total the minutiae of artefacts fully and their implications for manufacturing processes in the past. This modest examination of the internal ribs inside socketed axes presents the gravity of an experimental engagement in archaeological science, and presents grounds for further research into the craftsmanship behind the casting of bronze socketed axes. Complementary to the field of archaeology is the potential to highlight connectivity and continuity between spatially separated communities connected through the intimacy of craft as demonstrated by Ehrenberg (1981). Although basic forms and style can be observed and imitated, the internal rib implies a closer level of interaction requiring cooperation, engagement, and agreement on the manufacturing of tools between communities and potentially even cultures. Further study into this simple nuance may indicate a more socially complex range of connectivity between Bronze Age people of Ireland and continental Europe.
Too often experimental projects go unpublished due to problematic or unforeseen occurrences that hinder the intended path toward data. While the circumstances can be very different, the dynamics of this project fortunately revealed some problematic symptoms under the current interpretations, while simultaneously verifying some speculations surrounding the clay mould fragments and casting debris. For experimental archaeology, these types of minor mistakes are necessary to reveal archaeologically invisible steps in a process or to encounter some otherwise unknown experience. In the end, the difficulties occurred during this project may simply be related to inexperience with the process of casting bronze. Following the archaeological trail may lead us to an understanding of the archaeological materials, but not guide us to the approach. The problems related to air entrainment may be as simple as not having enough ventilation, or that the clay body was too thick and not permeable enough. With continued experience, the answer to these problems may become clearer.
Future research inside socketed axes should begin inside the mould system as demonstrated here. The internal ribs are a feature defined within the mould and may become transparent in light of further research and developing discovery. Any meaningful interpretation of the formative processes of metal objects should consider the experiential mode of analysis as a viable contribution to archaeology. Furthermore, the expertise and experience from active bronze casters should be viewed as complementary to experimental research questions providing cooperative dialogue on technical matters. Any further research on either the internal ribs or the process of mould making should consider the benefits of time and experience in the outcome of data.
Country
- Ireland
Bibliography
Auenmüller, J., Verly, G., and Rademakers, W. F. 2019. Bronze Casting Artefacts from the Qubbet El-Hawa – Moulds, Materials, and Experimental Methods, In: G. Verly, W. Frederik, T. Rademakers and T. Florian, eds. Monographies Instrumentum, Studies in Experimental Archaeometallurgy, Methodological approaches From Non-Ferrous Metallurgies. pp. 141-163
Baron, J., Miazga, B., and Nowak, K. 2014. Functions and contexts of Bronze Age metal casting moulds from Poland, In: Bulletin De La Société Préhistorique Française, 111(2), pp. 325-338 [online] Available at < http://www.jstor.org/stable/24364547 >Accessed 05/06/2018
Baudou, E. 1960. Die regionale und chronologische Einteilung der jungeren Bronzezeit in Nordischen Kreis, Stockholm.
Becker, K., 2018. Notes on the Bronze Age Clay Mould Assemblage from Rathgall, Co. Wicklow. [Draft/Illustrations] (Personal Communication, 25 July 2018).
Burgess, C. and Miket, R. 1976. Three socketed axes from North-East England with notes on faceted and ribbed axes, Archaeology Aeliana, 5s(4), pp. 1-9.
Coghlan, H. 1962. Notes on the Prehistoric Metallurgy of Copper and Bronze in the Old World, Pitt Rivers Occasional Papers on Technology 4. Oxford.
Coles, J. M. 1959-60. Scottish Late Bronze Age metalwork: Typology, distributions and chronology, Proceedings of the Society of Antiquaries of Scotland, 93, pp. 16-134.
Cordier, G. 2012. Le Dépôt de L’âge du Bronze Final de L’étang, Commune de Saint-Germain-Sur-Vienne, Archaologisches Korrespondenzblatt, 42(1) 31-39.
Cotter, C. and Barklie, R. 2012. The Western Stone Forts Project: Excavations at Dún Aonghasa and Dún Eoghanachta. Dublin, Wordwell
Dietrich, O. 2015. The Earliest Socketed Axes in Southeastern Europe: Tracking the Spread of a Bronze Age Technological Innovation. In: Paulina Suchowska-Ducke, Samantha Scott Reiter, Helle Vandkilde. (eds) Forging Identities. The Mobility of Culture in Bronze Age Europe: Volume 2. pp. 39-46. BAR International Series 2772
Eogan, G., 2000. The socketed bronze axes in Ireland, Prähistorische Bronzefunde, Abteilung IX, 22.
Evans, J. 1881. The ancient bronze implements, weapons and ornaments of Great Britain and Ireland. London.
Ehrenberg, M. 1981. Inside socketed axes, Antiquity 55, pp. 214-18.
Evershed, R. P. and Dudd, S. N. 2003. New chemical evidence for the use of combed ware pottery vessels as beehives in ancient Greece, Journal of Archaeological Science, 30, pp. 1-12.
Garbacz-Klempka, A., Kwak, Z. Żak, P.L., Scuzki, M., Ścibior, D., Stolyarczyk, T., and Nowak, K. 2017. Reconstruction of the Casting Technology in the Bronze Age on the Basis of Investigations and Visualisation of Casting Moulds, Archive for Foundry Engineering, 17(3), pp. 184-190.
Grimes, W. F. 1931. A bronze casting in the Guilsfield, Montgomery, hoard, Cambridge Archaeological Journal, 86, p. 358.
Hamilton, J.R.C. 1956. Excavations at Jarlshof, Shetland, Ministry of Works Archaeological Report, (1), Edinburgh.
Harding, A. F. 2000. European Societies in the Bronze Age, Cambridge World Archaeology, Cambridge, Cambridge University Press.
Heeb, J. and B. Ottaway 2015. Experimental archaeometallurgy. In B. Roberts and C. Thornton, eds. Archaeometallurgy in global perspective, pp. 161-192.
Hodges, H.W.M. 1954. Stone and clay moulds, and wooden models for the bronze implements, Ulster Journal of Archaeology, 17, pp. 62-80.
Holmes, P. 1979. The manufacturing Technology of Irish Bronze Age Horns, In M. Ryan, ed. The origins of Metallurgy in Atlantic Europe, pp. 165-88.
Kimpe, K, Jacobs, P.A., and Waelkens, M. 2002. Mass spectrometric methods prove the use of beeswax and ruminant fat in late Roman cooking pots, Journal of Chromatography. A. 968, pp. 151-160.
Liversage, G. D., Hattington, T., Dooley, R. H. M., Hodges, and H. M. W., Morganite. 1967-68. Excavations at Dalkey Island, Co. Dublin 1956-1959. Proceedings of the Royal Irish Academy: Archaeology, Culture, History, Literature, 66, pp. 53-233.
Maryon, H. 1937-8. The Technical Methods of Irish Smiths in the Bronze and Early Iron Ages, Proceedings of the Royal Irish Academy, 44, pp. 181-221.
Ménager, M., Azémard, C., and Vieillescazes, C. 2014. Study of Egyptian Mummification balms by FT-IR spectroscopy and GC-MS, Microchemistry Journal, 114, pp. 32-41.
Needham, S. 1981. The Bulsford-Helsbury Manufacturing Tradition: The production of Stogursey socketed axes during the later Bronze Age in Southern Brittan, British Museum Occasional Papers, (13), pp. 1-72.
Neergaard, C. 1910. Un amas de débris provenant d’une fonderie du recent âge du bronze, Trouvaille de Haag, Mémoire de la sociologe Royale des antiquaries du Norde, pp. 134-224.
Pitt-Rivers, A. L. F. 1906. The evolution of Culture and other essays. Oxford.
Rynne, E. 1983. Why the ribs inside socketed axeheads? Antiquity 57(119), pp. 48–49.
Turner-Walker, G. 2008. A Practical Guide to the Care and Conservation of Metals. [Online] Available at < https://www.researchgate.net/publication/... > Accessed 02/22/2020
Tylecote, R.F. 1962. Metallurgy in Archaeology. London: Edward Arnold.
Weadick, S. (2018) Discussion of bronze socketed axes in the National Museum of Ireland (Personal communication 13th June 2018)
Ó Faoláin, S. and Northover, J.P. 1998. The technology of Late Bronze Age Sword Production in Ireland. The Journal of Irish Archaeology, (9), pp. 69-88.
Ó Faoláin, S. 2004. Bronze age artefact production in Late Bronze Age Ireland. BAR British Series 382. Oxford: B.A.R.
Unitt, R. 2012. Petrological analysis of the ceramic objects in C. Cotter and R. Barklie, eds. The Western Stone Forts Project: Excavations at Dún Aonghasa and Dún Eoghanachta. Vol. 2. Dublin pp. 26-27.