The content is published under a Creative Commons Attribution Non-Commercial 4.0 License.
Reviewed Article:
Approaching Pottery Burnishing through Experimental Firings
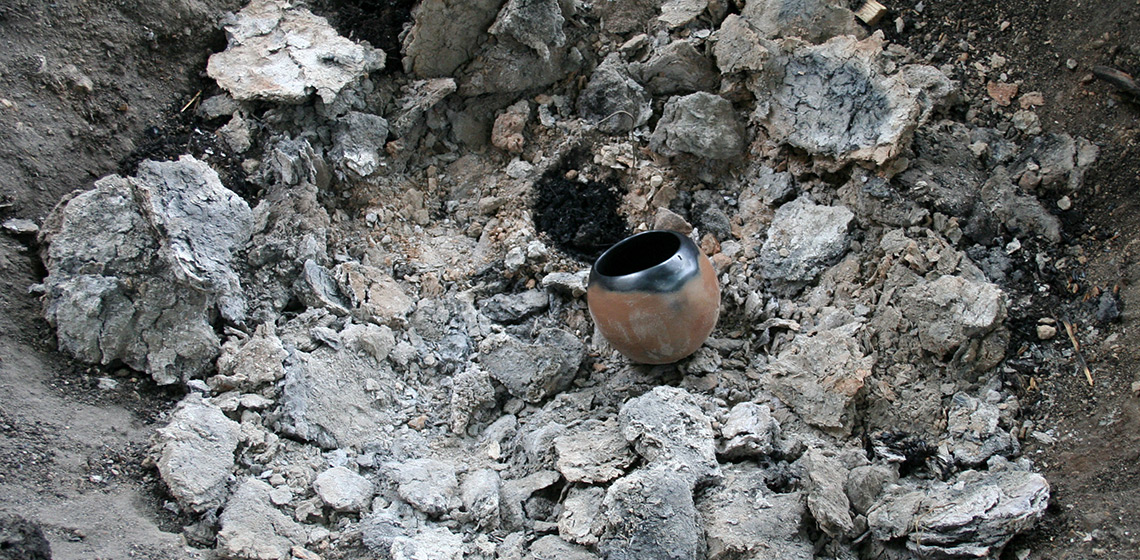
This study assesses the impact of firing on burnished ceramic surfaces. For this task, two main factors related to burnishing were examined and evaluated, the reflection of the ceramics and pottery surface sheen. Macroscopic observations on the burnished surface were made with the naked eye. A series of experiments was conducted to explore the ways in which traditional firing conditions affect pottery surfaces. Data was gathered from four different firings, including three open-air dung firings and one wood-firing in an updraft kiln. Additional testing was carried out under controlled conditions in the laboratory. The aim was to further investigate and determine the specific thermal characteristics that influenced the burnished pottery and use the feedback to approach burnishing disturbance in traditional conditions. The data showed that certain thermal profiles and characteristics cause a reduction in burnishing on ceramic surfaces, with the rise in temperature, among others, being a significant one. The type of clay also proved to be an important factor regarding the way in which the reduction in burnishing progresses. The present inquiry constitutes the first part of an ongoing research project that will be completed with Scanning Electron Microscopy (SEM) analysis of the microstructure and surface micromorphology of the ceramics.
Introduction
Burnishing is a long-term and broadly applied pre-firing practice for processing the surfaces of ceramics. Burnished pottery refers to a common type of ware that was used in antiquity over a long period of time across Europe (for example, Vagalinski, 2002; Gâţă and Dragoman, 2012; Osório, 2016; Forte, 2019) and beyond (for example, Daviau and Graham, 2009; Fragnoli, 2018). Ethnographic parallels all over the world demonstrate that contemporary potters using traditional techniques continue to produce this type of pottery ware (for example, von Dassow, 2009).
In the case of prehistoric Greece, burnished pottery has been widely attested from the Neolithic to the end of the Bronze Age, circa 6500-1050 BC (Holmberg, 1964; Zerner, 1978; Rutter, 1983; Zerner, 1986; Rutter, 1990; Lis, 2009; Hale, 2014, pp.68-80). It has been documented in the archaeological record in a range of shapes, including tableware, transport containers, and vessels for food preparation and storage (Zerner, 2008; Lis, 2009; Romanos, 2011). Furthermore, it is observed with different clays of variable coarseness, from fine to rather coarse (for example, Rutter, 1995, pp.13, 19-20, 23-27).
While some scholars have emphasized the social value embodied in the consumption of burnished pots (for example, Faust, 2002), others have stressed the importance of burnishing in reducing pottery permeability and providing waterproofing, or highlighted the correlation between impermeable burnished cooking pots and heating effectiveness (Schiffer, 1990; Skibo, Butts and Schiffer, 1997).
Burnishing is produced by rubbing against the leather-hard surface of the pottery with a smooth medium - for example, a pebble or piece of bone. As a result, the sunlight is reflected on the surface, producing, at its maximum, specular reflection and a very bright sheen (See Figure 1). The shiny appearance seems to result from the rearrangement and orientation of the surface clay particles and their following compression (Shepard, 1956, pp.67, 191; Rice, 1987, p.138). Through rubbing, a mechanical coat, a so-called “self-slip”, is created, which is visible to the naked eye alongside the fresh break of the pots.
Over the past decade, the author has produced and fired dozens of handmade burnished vessels inspired by known examples from Greek prehistory, specifically in terms of shape repertoire, building methods, surface treatment, and firing technology (see: https://www.facebook.com/JasperHandmadeCeramics). Εarlier observations made in collaboration with M. Zavadil on the reduction of the sheen of several heavily burnished pots in these firings prompted the design and implementation of the current experiment. The decline in the quality of burnishing was initially assumed by the author and M. Zavadil to be the result of the prevailing thermal conditions in specific sections of the wood-firing updraft kiln that was used (Kordatzaki and Zavadil, 2020). The lateral internal parts of that kiln, between the side walls and the perforated floor, were open to the firebox (See Figure 2). Consequently, the margins of the upper surface of the floor were immediately subjected to the intense heat, hot gases, and combustion products (for example, suspended ash) that were released from the lower to the upper chamber. Due to this, specific sides of the burnished pots (for example, side B of the pot in Figure 3a) that were set next to the lateral gap in the kiln (See Figure 3b) were heavily disturbed and, in places, became noticeably rough. On the contrary, those sides of the pots that were facing towards the centre of the upper chamber (for example, side A of the pot in Figure 3a), appeared very bright and highly lustrous.
A decline in the sheen of several pots was also observed in open-air firings carried out in the past (See Figure 4). The author ascribed that decline to the direct contact of the glowing coals with the burnished pottery, which likely produced some dullness.
Methodology
The present study explores in greater depth those parameters which disturb burnishing and affect the sheen of the pottery during firing. For the purposes of this research, well-documented traditional firings were conducted, followed by a series of controlled firings in the laboratory. The laboratory testing was carried out to better understand all those variables that contribute to the decline in sheen in controlled thermal conditions. The data from these experimental firings provided the necessary information for reassessing this topic from the perspective of traditional firing contexts. For the needs of the experiment, a number of heavily burnished pots and test sherds were produced and fired.
Burnishing the experimental pots and test sherds
All burnished experimental pots and test sherds in this study displayed the same specular reflection and the maximum sheen before firing. It was important to produce equally well-burnished unfired pottery so that each pot and test sherd could be directly comparable with the others after firing. For this reason, the author adopted the following process:
Before burnishing, the experimental, moist pottery (pots and test sherds) was smoothed so that irregularities would not appear on the surface. Burnishing started when the ceramics were in the soft leather-hard dry stage. When they became quite hard and transitioned to the so-called stiff leather-hard stage, extreme burnishing took place (for more on burnishing and other finishing techniques, see Shepard, 1956, pp.67, 123-124, 186-193; Rye, 1981, p.89; Rice, 1987, p.138; Cuomo di Caprio, 2017, pp.124-125. For an experimental approach on the burnishing marks, see Forte, 2019).
Previous experiments undertaken by the author in the context of a study on the prehistoric pottery from the archaeological site of Pheneos, Corinthia, in Greece (Burke, Zavadil and Kordatzaki, 2021) have demonstrated that the softer the burnishing medium, the less shiny the pottery surface and the more diffused the reflection (see Lepère, 2014; Forte, 2019; Dymańska, Cetwińska and Manasterski, 2022). Specifically, burnishing became more intense when pebbles and bones were used in the process instead of leather and wood (See Figure 5abc). As a result, in order to achieve the maximum brightness and a specular reflection in the current experiment, the same smooth limestone pebble was used for burnishing. Rubbing was carried out mostly with the broad surface of the pebble and, less frequently, with its narrow face. A vigorous forward-backward rubbing motion was applied on the unfired ceramics, leaving linear marks with clear margins that were often arranged in clusters (See Figure 6ab).
Burnishing striations on the pottery surface appeared mostly horizontal, following the dominant movement of the pebble. Nevertheless, striations in other directions were also detected due to additional random rubbing (for a systematic study of such striations, see Lepère, 2014). Careful examination under an RS PRO USB digital, handheld microscope revealed a combination of striations on each pot and test sherd, including those with shallow, straight, and sharp margins and others that were deeper and wider with diffused margins and pointed edges (See Figure 7ab). In sum, the surfaces of all experimental pots and test sherds appeared extremely shiny, providing specular reflection. Generally speaking, the reflected light rays on a rough surface scatter in all directions and are diffused (for the interaction between the light and the surface of the ceramics, see Shepard, 1956, pp.122-123).
It is clear that not all types of clays are suitable for burnishing. In some cases, clays proved to be quite sticky, making burnishing practically impossible. For comparison, pottery from two different Greek commercial clays were used in the experiment for both the traditional and the laboratory firings. The first type was a semi-fine, plastic clay from Euboea, brown when unfired (See Figure 6a). Petrographic analysis revealed that it contained mostly minerals, such as monocrystalline quartz, mica, and feldspars, and, less frequently, rock fragments, including carbonates (mostly micritic limestone). The second type was a Cretan clay that appeared fatty, grey when unfired, of medium coarseness (See Figure 6b). It was dominated by monocrystalline quartz, mica, and feldspars, as well as rock fragments, including quartz-mica schist, strained quartz, and carbonates (micritic and holocrystalline limestone).
The reflection of the pottery surface and the sheen of the ceramics were thoroughly documented to assess the effects of the firing on burnishing. The examination of the burnished surfaces of the experimental pots and test sherds was done with the naked eye and always under the same lighting conditions. The main subdivision for the reflection comprised specular and diffused reflection. For evaluating sheen, from the shiniest to the least shiny surface, very bright, bright, velvety, soft, and dull lusters were recorded.
Traditional experimental firings
Four traditional experimental firings were carried out to investigate the impact of past conditions on burnished pottery. Specifically, two major types of structure were used (See Table 1), including a depression, where three open-air firings took place, and a two-chamber, wood-firing updraft kiln, for the fourth firing (for more on firing structures, see Gosselain, 1992, p.246 fig.1; Gosselain and Livingstone Smith, 1995, p.153 fig.4; Livingstone Smith, 2001). The open-air dung firings were conducted at Hallstatt in the context of the 1st pottery workshop organised in 2022 by H. Reschreiter of the Naturhistorisches Museum in Vienna. The kiln firing took place at Asparn an der Zaya at the MAMUZ Museum in 2020. The open-air dung firings were executed by L. and V. Albustin, S. Gütter, H. Reschreiter, and M. Zavadil together with the author. The kiln firing was carried out by F. Ugrinovits.
Firing | Firing structure | Main fuel type | Supplementary fuel type | Dung arrangement |
1st | Depression with heavy insulation (sod) | Admixture of cow pats & straw | - | 2 to 3 layers of dung |
2nd | Depression | Admixture of goat dung & straw | Cow & sheep dung | 2 layers of dung |
3rd | Depression | Admixture of goat dung & straw | Horse manure | 4 layers of dung |
4th | Updraft kiln | Beech & spruce wood | - | - |
Table 1. Firing structure in association with fuel type and dung arrangement.
In order to effectively reduce additional parameters that may hinder the comparison of the different open-air firings, the subsequent process was followed:
A depression (shallow pit) 1.10 x 1.40 m in size and 0.30 m deep was dug in the ground and used for all three open-air firings. Although not precisely the same, the total volume of the pile of the pottery in each firing was similar, with a maximum size of 0.40 x 0.35 m, and a maximum height of 0.17 m.
Dried dung was the main combustion agent for all three open-air firings (See Table 1), although the specific type of manure differed. For the first open-air firing structure, cow pats were used in an arrangement of two to three layers in places (See Figure 8a). An additional layer of moist sod, about 10 cm in thickness, covered the top of this arrangement to facilitate a slow heating rate (SHR) (See Figure 8b). For the second and third open-air firing structures, large slabs of goat dung, broken into pieces, were used. In the former, the pottery was covered with two layers of dung (See Figure 9), while in the latter, four superimposed dung layers were arranged (See Figure 10). In all cases, the dung was naturally mixed with some straw. In addition, a small amount of a cow-sheep dung admixture in the form of powder was used for the second firing, and horse manure for the third. A layer of broken pieces of manure was put at the bottom of each dung structure, which served as a thermal insulating material. Dung in the form of powder was also spread over this layer to prevent oxygen from circulating among the pots. The pots were put in contact with the dung.
In regard to the updraft kiln (See Figure 11, Table 1) and as opposed to the open-air firings, the pottery load was set in the upper chamber and not in direct contact with the fuel. The latter was a combination of dried chopped beech and spruce wood and logs.
Α probe connected with a pico-technology data logger (TC08-USB) was placed at the bottom of the depression and kept in the same position for all three open-air firings. Temperature readings were recorded every minute. Apart from the Cretan pot in the first firing, which was lying a bit further away and covered with a large pot to achieve reduction, all experimental vases were in contact with the probe. For monitoring the kiln temperature, an analogue pyrometer with a thermocouple was attached to the upper chamber where the pottery was loaded. However, the thermocouple was not in direct contact with the burnished pots. The temperature was measured every ten minutes.
The experimental pottery produced by the author, together with ceramics manufactured by other colleagues, was set in common firings. However, the data from the traditional firings and their evaluation was only gathered from observations made on the author’s experimental vessels. In each of the open-air firings, two small, experimental handmade closed pots were placed, one made of the Euboean clay and the other with the Cretan clay. The pots were set from the beginning in the fire without preheating and put upside down in the depression. Two small, burnished bowls, one made of the Euboean clay, the other from the Cretan clay, were put in the kiln. In addition, one burnished goblet (See Figure 11), a type of stemmed open pot, often medium-large in size, that display a polished or burnished surface and constitute a characteristic ceramic type of the Middle Bronze Age (circa 2000-1700 BC) pottery in Greece (Balitsari and Papadopoulos, 2018, pp.234-238), made from the Cretan clay was also fired.
In general, open-air firings have been traditionally associated with uncontrolled conditions (Livingstone Smith, 2001), whereas the conditions in the kilns, a priori, have long been assumed to be better controlled. Nevertheless, available data has demonstrated extreme thermal variation in both open-air firings and kiln firings (Gosselain, 1992, p.244; Livingstone Smith 2001; Hein, Müller and Kilikoglou, 2017). In addition, a series of past experimental open-air firings carried out by the author and other colleagues revealed a thermal variation of up to 230° C between different parts of the same medium-large sized pots. Ethnographic and experimental studies have sufficiently documented that the attribution of certain thermal characteristics to specific structures is overly simplistic (for example, Gosselain, 1992, p.244; Livingstone Smith, 2001; Hein, Müller and Kilikoglou, 2017; Kordatzaki and Zavadil, 2020), and future research should consider each firing structure separately.
Given the above, full documentation of every single traditional firing was carried out (See Table 2) with the main focus on the following thermal characteristics: maximum temperature, heating rate (average temperature per minute to reach the maximum temperature), soaking time (namely, time the pottery was subjected to above specific temperature thresholds, for example, above 700° C, 800° C or 900° C, and/or at its maximum).
Firing | Firing structure | Minutes up to max temp. | Max temp. (° C) | Average heating rate (° C/min) | Soaking time at max temp. (min) | Soaking time >700° C (min) | Soaking time >800° C (min) | Soaking time >900° C (min) |
1st | Depression with heavy insulation (sod) | 283 | 544 | 1.91 | 1 | - | - | - |
2nd | Depression | 177 | 846 | 4.77 | 1 | 24 | 3 | - |
3rd | Depression | 165 | 929 | 5.63 | 1 | 21 | 11 | 1 |
4th | Updraft kiln | 360 | 925 | 2.56 | 20 | 70 | 36 | 20 |
Table 2. Detailed thermal characteristics of the traditional firings (max temp.: maximum temperature).
Controlled experimental firings
To thoroughly evaluate how certain thermal features affected the sheen and the reflection of sunlight off the burnished surface of the pottery, as was the case following the traditional firings, a series of experimental firings were conducted in the laboratory.
Twenty-four heavily burnished test sherds of the same thickness were prepared. All sherds were pinched and finally beaten on a mould. They were then fired under controlled, oxidising conditions in a Nabertherm L-151K2TNL 15/12/C450 muffle furnace (for the controlled testing, the equipment of the Fitch laboratory, British School at Athens was used). Four main series of controlled firings were performed (for example, for the 1000° C, see Graph 1) with the following thermal characteristics (See Table 3): 1. Fast heating rate (FHR) and 3 minutes soaking time (at maximum temperature; see Graph 2); 2. FHR, 1 hour soaking time (at maximum temperature); 3. FHR, 3 hours soaking time (at maximum temperature); 4. Very slow heating rate (VSHR), 3 minutes soaking time (at maximum temperature). Four different maximum temperatures/temperature thresholds were consistently regulated (700° C, 800° C, 900° C, and 1000° C) in each of the main series of firings. The exception to the above were the test sherds that were kept for three hours at the maximum temperature and, due to general funding limitations, fired only at 1000° C. Moreover, the test of 900° C, VSHR/3 min was not conducted.
Test sherds | ||||||||
CRETAN | ||||||||
FHR/3 min | FHR/1 h | FHR/3 hrs | VSHR/3 min | |||||
700° C | Reflection | Sheen | Reflection | Sheen | Reflection | Sheen | Reflection | Sheen |
Specular | Very bright | Specular | Very bright | - | - | Specular | Very bright | |
800° C | Specular | Bright | Specular | Bright | - | - | Specular | Bright |
900° C | Diffused | Soft | Diffused | Soft | - | - | - | - |
1000° C | Diffused | Soft | Diffused | Soft | Diffused | Soft | Diffused | Dull & rough |
EUBOEAN | ||||||||
FHR/3 min | FHR/1 h | FHR/3 hrs | VSHR/3 min | |||||
700° C | Reflection | Sheen | Reflection | Sheen | Reflection | Sheen | Reflection | Sheen |
Specular | Very bright | Specular | Very bright | - | - | Specular | Bright | |
800° C | Specular | Velvety | Specular | Velvety | - | - | Specular | Velvety |
900° C | Diffused | Soft | Diffused | Soft | - | - | - | - |
1000° C | Diffused | Soft | Diffused | Soft | Diffused | Dull | Diffused | Dull |
Table 3. Main thermal characteristics of the controlled firings in the laboratory in correlation to the reflection and sheen of the test sherds (FHR: fast heating rate; VSHR: very slow heating rate).
In the FHR controlled firings, the average rate to reach the maximum temperature of each firing ranged between 8.41-9.85° C/min (for the detailed characteristics of the controlled firings, see Table 4). However, regardless of the maximum temperature, the actual heating rate to reach the previous temperature thresholds was consistently the same (See Graph 2). For all VSHR firings in the laboratory, the maximum temperature was reached in five hours, and the average heating rate was below 3.33° C/min.
FHR | VSHR | |||
Max temp. | Minutes to reach max temp. | Average heating rate to max temp. (° C/min) | Minutes to reach max temp. | Average heating rate to max temp. (° C/min) |
700° C | 71 | 9.85 | 300 | 2.33 |
800° C | 85 | 9.41 | 300 | 2.66 |
900° C | 107 | 8.41 | - | - |
1000° C | 116 | 8.62 | 300 | 3.33 |
Table 4. Detailed thermal characteristics of the controlled firing conditions in the laboratory (max temp.: maximum temperature; FHR: fast heating rate; VSHR: very slow heating rate).
Discussion
Thermal characteristics of the traditional firings
Similar high temperatures were achieved in the fourth kiln firing (925° C) and the third open-air firing (929° C) (See Table 2, Graph 3). A marginally lower temperature (846° C) was attained in the second open-air firing, while by far the lowest temperature (544° C) was recorded in the first open-air firing (See Graph 4). A closer comparison (See Table 2, Graph 3) between the fourth and third firings indicates that they significantly vary in terms of soaking time and heating rate. On the one hand, a VSHR (2.56° C/min) and long soaking time above 800° C and 900° C, respectively, were revealed in the kiln firing. The soaking time of the kiln firing above 700° C was more than three times longer than that of the third open-air firing. Conversely, the third firing showed a SHR (5.63° C/min), approximately twice as fast as that of the kiln firing. Regarding the soaking time above 900° C, a considerable difference was also observed, with the kiln firing taking twenty times longer. Regarding the first open-air firing, it seems that the sod facilitated an extremely slow heating rate. The temperature for about 100 minutes was between 480° C and 540° C, with brief intervals of falling temperature.
It is stressed that no particular documentation and mention of the cooling rate is taken into account in the current series of firings (both traditional and controlled), since the author considers that burnishing is only affected during temperature rise, when changes in the composition and structure (related for example to the vitrification process; for the vitrification development, in general, see Maniatis and Tite, 1981) of the pottery is happening. However, it is noted that in the second and third firings, a rapid cooling rate followed (for example, 11.35° C/min for the third firing). On the contrary, the kiln firing displayed a very slow cooling rate (2.06° C/min): the initial sharp drop in temperature to 600° C, followed by a gradual decrease to 100° C, when temperature recording stopped.
In the second and third open-air firings, as soon as the temperature reached its maximum, it immediately dropped sharply (See Table 2, Graph 4). This was not the case for the kiln firing, which maintained its maximum temperature for a longer period (See Table 2). The first firing constitutes a special example since the fire suddenly went out when the maximum temperature was still quite low.
Regarding the atmospheric conditions, in the first open-air firing, the pots were covered with cereal husk and a small amount of soil and, finally, changed into silver black (Euboean) and black (Cretan pot) (See Figure 12ab). Oxidation prevailed in the second and third open-air dung firings so that the body of the vases became light in colour (See Figures 13abcd and 14abcd). However, the upper sections of the pots that were lying upside down and partly covered by the burned dung layer at the bottom of the depression were reduced and finally changed to black or produced a silvery black tint. In general terms, different colours were to be expected in these experiments. Due to an unsuccessful reduction, mixed conditions prevailed in the kiln firing (See Figure 15ab). It should be stressed that the Cretan pot showed advanced lime spalling approximately one month after its firing, when the photos were taken.
To sum up, although there was a slight variation in the maximum temperatures, the second and third firings displayed a similar thermal profile. It is worth mentioning that dung is generally considered to be a slow-burning fuel (for example, Livingstone Smith, 2001, p.993). In comparison to the second firing, a longer soaking time above 800° C was documented in the third firing. The first and fourth firings differed substantially from the previous two and between each other. The highest, almost similar, temperature was achieved in both the third open-air dung firing and the fourth kiln firing; the lowest temperature was demonstrated in the first dung firing with the sod covering. Although all four are characterized by a SHR (below 5.63° C/min), the first and fourth firings exhibited considerable VSHR. The longest soaking time, above the threshold of 900° C, was attested in the kiln firing. This was also the case where the longest exposure to such a high maximum temperature was attested.
Traditional firing and burnishing
The original reflection and sheen of the unfired, burnished experimental pots were variably affected by the fire, which depended on the specific thermal characteristics of each single firing (See Table 5). After the first open-air firing (very low maximum temperature and VSHR), the specular reflection of the pots was maintained regardless of the type of clay (See Figure 12ab). Interestingly, both pots looked slightly brighter than before. The black or silvery black surface of the ceramics probably created the illusion that the vessels were shinier.
Firing | Main thermal features | EUBOEAN | CRETAN | |||||||
Max temp. (° C) | Heating rate | Soaking time (min) | Reflection | Sheen | Reflection | Sheen | ||||
>700° C | >800° C | >900° C | At max temp. | |||||||
1st | 544 | VSHR | - | - | - | 1 | Specular | Very bright | Specular | Very bright |
2nd | 846 | SHR | Long | Very short | - | 1 | Specular | Velvety body Bright top | Specular | Bright body Very bright top |
3rd | 929 | SHR | Long | Short | Very short | 1 | Diffused | Soft body Very bright top | Diffused | Soft body Very bright top |
4th | 925 | VSHR | Very long | Long | Long | 20 | Diffused | Dull | Diffused | Dull & rough |
Table 5. Main thermal characteristics of the traditional firings in relation to the reflection and sheen of the experimental pots (max temp: maximum temperature; VSHR: very slow heating rate; SHR: slow heating rate; Very short: 1-9 min; Short: 10-19 min; Long: 20-39 min; Very long: >40 min).
The Euboean pot in the second firing (relatively high temperature, very short soaking time above 800° C and SHR; for the accurate soaking time, see Table 2) kept its specular reflection (See Table 5), but its sheen sharply diminished from very bright to a velvety appearance (See Figure 13ab). In contrast, the sheen of the Cretan vase (See Figure 13cd) was reduced to bright under the same conditions. The reflection on both pots (See Figure 14abcd) dramatically changed from specular to diffused in the third open-air firing (high maximum temperature, SHR, short soaking time above 800° C and very short above 900° C). In addition, the sheen of the two pots further decreased and appeared soft. Several dullish, brownish-red blotches were noted on the surface of the Euboean pot (See Figure 14b), possibly the result of some kind of melting of the combustion products on the pottery surface (for example, glowing coals). It should be noted that the black and black silver upper part of the pots of the second and third open-air firings from both types of clay appeared brighter than the body.
A major change in the sheen of the pots from the two clays took place for the first time in the kiln firing (maximum temperature 925° C, VSHR, long soaking time above 800° C and 900° C, and very long above 700° C). This was the only time when the pots of both clays totally lost their sheen and turned dull (See Figure 15). In addition, a significant deterioration was observed in the texture of the Cretan pot, notably dull, rough patches in certain places (See Figures 11 and 15ab).
Controlled firing and burnishing
Table 3 summarizes the correlation between controlled thermal characteristics, burnishing (in terms of reflection and sheen), and type of clay. It reveals that a major change in the reflection took place at 900° C. The reflection of the burnished surface appears specular for the lower maximum temperatures (700° C and 800° C) and diffused for the higher ones (900° C and 1000° C), regardless of the specific thermal profile (FHR/3 min, FHR/1 h, VSHR/3 min) and the clay. This also applied to the FHR/3 hrs test at 1000° C.
In comparison to the unfired sherds, no reduction in sheen was noted in the test sherds that were fired at the lowest temperature of 700° C. This was the case regardless of the heating rate and soaking time. The exception was the Euboean sherd, which was subjected to a VSHR firing (See Table 3; for more, see below). In general terms, as the temperature increased 100° C, from 700° C to 1000° C, the sheen progressively diminished (See Figures 16 to 21; it is noted that certain test sherds, such as those displayed in Figures 17c and d, 19c and d, and 21c, showed lime spalling approximately one month after their firing, when the photos were taken). This concerns both types of clay and is linked to variable heating rates and soaking times. However, no further reduction in the soft sheen of the test sherds of both clays was documented between 900° C and 1000° C when they underwent a FHR firing (See Figures 16 to 19). However, this was not the case with the Euboean sherd, which was subjected to three hours at 1000° C. In this instance, its sheen changed to dull.
The way the loss of sheen progresses from 700° C to 1000° C is directly related to the type of clay. The sheen disturbance is either gradual and smooth, or abrupt and sharp. The crucial temperature threshold, where a sharp decline takes place, depends on the type of clay. For the Cretan sherd, a marked reduction from bright to soft was attested at 900° C, FHR, independent of the soaking time (See Figures 17 and 19). For the Euboean sherd, a sharp drop from very bright to velvety was documented at 800° C, FHR, irrespective of the soaking time (See Figures 16 and 18). Sherds of the same clay, when subjected to FHR at the same temperatures, similarly lost their brightness, whether or not the soaking time was three minutes or one hour.
The exact conditions under which dullness appeared depended on the type of clay and the heating rate. Dullness was produced only when the sherds of both clays were subjected to 1000° C, in association with certain firings. Specifically, the Euboean sherds totally lost their gloss and changed to dull when subjected to:
- three hours at 1000° C, in a FHR firing (two hours to reach maximum temperature, see Figure 22a);
- three minutes at 1000° C, in a VSHR firing (five hours to reach maximum temperature, see Figure 22b).
Contrary to the Euboean samples, the Cretan sherds never changed to dull in the FHR firings. VSHR appears to be an important thermal attribute that has a significant impact on the deterioration of the sheen. The only time the Cretan pottery became dull was when it was soaked at 1000° C in a VSHR firing (See Figure 21abc). Furthermore, this was when the dull Cretan example displayed a rough texture in places.
The VSHR firings seemed to accelerate the reduction in sheen in the case of the Euboean sherds from quite low temperatures (See Figures 20abc). Specifically, the sheen of the Euboean sherd reduced from very bright as early as 700° C (See Figure 20c). On the contrary, the Cretan sherds appeared very bright and bright at 700° C and 800° C respectively, following the gradual drop of the FHR firings (See Figure 21ab).
Integrating the laboratory feedback to understand the impact of traditional firing on burnishing
Variation in the decline of burnishing on the surfaces of the experimental pots set in different traditional firings must be attributed primarily to the varying maximum temperatures reached in each firing. Further variability in the sheen and reflection between the pots of the same firing is due to the different clay. The two extreme examples of burnishing (specular reflection and very bright sheen vs diffused reflection and dull sheen or dull sheen and rough texture) have been correlated with the two extreme thermal profiles of the traditional firings (first open-air dung firing: very low maximum temperature, VSHR vs fourth kiln firing: high temperature, VSHR, long soaking time above 900° C respectively) (See Figures 11, 12 and 15). Obviously, due to the very low maximum temperature of the first open-air firing, the reflection and the sheen of the pottery were not affected.
Differences in the sheen of the pots made of the same clay between the third open-air firing (See Figure 14abcd) and the fourth kiln firing (See Figures 11 and 15), where similar maximum high temperatures were recorded, could be assigned to the variable heating rate (SHR vs VSHR respectively) and soaking time (very short vs long above 900° C) (See Graph 3; Table 5).
The diffused reflection and the dull sheen or dull sheen and rough surface of the pots fired in the updraft kiln at 925° C (See Figures 11 and 15) resemble features observed in the laboratory at 1000° C. Specifically, similar burnishing characteristics were achieved in the laboratory at conditions equivalent to:
- for the Euboean pot, FHR, 1000° C/3 hrs or VSHR, 1000° C/3 min (See Figure 22ab);
- for the Cretan pot, VSHR, 1000° C/3 min (See Figure 21c).
Based on the above, one could state that there was considerable thermal variation in the upper chamber of the wood-firing updraft kiln, where the actual maximum temperature reached in certain parts was close to 1000° C. Moreover, it is possible that the indirect subjection of the pots to the combustion products (for example, suspended ash) produced at lower temperatures changes in the pottery, in comparison to similar changes that occurred at higher temperatures in the electric furnace. The scenario that similar changes might have occurred in the electric furnace in temperatures slightly lower than 1000° C cannot be excluded.
Concluding remarks
Based on the above data, the following statements can be made:
Temperature constitutes the most important thermal characteristic that affects burnishing. Additionally, temperature increases cause sunlight diffusion and reduce brightness. As the temperature increases, the way in which the reduction in burnishing develops is associated with the type of clay. It seems that there are specific temperature thresholds, directly related to the type of clay, where major changes are happening on the burnished surface. In the context of the present study, such significant thresholds proved to be at 800° C for the Euboean clay, and 900° C for the Cretan one. At these temperatures, an important change from specular to diffused reflection was reported that highly affected the quality of burnishing. At lower temperatures, such as 700° C and below, sheen and reflection were not affected. The exception was the Euboean test sherd, which showed a decline in burnishing even at low temperatures (for example, 700° C), when subjected to VSHR firings.
Heating rate and soaking time can also accelerate a decline in sheen, and again, the type of clay plays a key role. On the one hand, in the laboratory-controlled FHR firings, soaking time did not seem to have any important effect on the decline of the sheen; the exception was when sherds of the Euboean clay were subjected to a long period of time at 1000° C. On the other hand, it has been demonstrated that VSHR firings can facilitate dullness, at temperatures as high as, for example, 1000° C, regardless of the type of clay. As far as the Cretan pottery was concerned, at such high temperatures in relation to VSHR, extreme burnishing decline produced roughness. Firings of a VSHR can also speed up the reduction in sheen as low as 700° C, but this is directly linked with the type of clay (for example, this refers to the Euboean ceramics of this study).
The vessels fired in the wood-firing updraft kiln appeared dull or dull and rough, and displayed the maximum decline in burnishing among those fired in the traditional firings. Pottery fired in the open-air dung firings never appeared dull and, in general terms, displayed the least reduction in burnishing. The VSHR and the long soaking time in association with the high temperature proved to be decisive for this big reduction in the kiln firing. In short, thermal profiles of lower maximum temperatures, faster heating rates, and shorter soaking times could prevent a significant decline in the sheen. Temperatures above 900° C did not work properly for producing extremely shiny pottery, at least in the context of the current research. However, to a certain extent, this relates to the type of clay used in the manufacture of the pottery.
The possibility that the decline in burnishing is directly related to the vitrification progress is high. It is also very likely that certain types of clay, rich in fluxes (for example, a high content of feldspars), could enhance the vitrification and thus disturb the sheen at lower temperatures than others (the author is thankful to J.H. Sterba for his interesting ideas on this topic). Additional laboratory analysis could shed more light on this issue. For this reason, further investigation of the burnished pottery and the microstructure of the ceramics will be implemented using Scanning Electron Microscopy (SEM) and the data will be presented in a future publication.
Acknowledgements
The author gratefully acknowledges the contribution of L. and V. Albustin, S. Gütter, H. Reschreiter, and M. Zavadil, who advised and assisted the author with the open-air dung firings. Their experience and support also proved invaluable for the open-air firings. Special thanks to H. Reschreiter (Naturhistorisches Museum in Vienna) for organising in 2022 the 1st pottery workshop at Hallstatt (Austria), where the open-air dung firings took place. Many thanks go to F. Ugrinovits who carried out the kiln firing at the MAMUZ Museum (Asparn an der Zaya, Austria). The author is thankful to E. Marzec and C. Gardner for adjusting the settings of the furnace at the Fitch laboratory, British School at Athens, as well as E. Kiriatzi for permission to use the facilities of the laboratory. Much appreciation to J.H. Sterba for his insightful comments and remarks, which proved to be important for the formation of the laboratory experiments. I also extend my thanks to N. Gerakakis for his excellent photos and photo editing, and D. Howitt-Marshall for the English proofreading. This research could not have been accomplished without the contribution of M. Zavadil at various stages of the study.
Keywords
Country
- Greece
Bibliography
Balitsari, A. and Papadopoulos, J.K., 2018. A cist tomb on the south bank of the Eridanos in the Athenian Agora and the Middle Bronze Age in Athens. Hesperia, 87(2), pp.215-277.
Burke, C., Zavadil, M. and Kordatzaki, G., 2021. The chaîne opératoire of pottery traditions at Pheneos, Peloponnese, mainland Greece. Journal of Archaeological Science: Reports, 35, article number: 102660.
Cuomo di Caprio, N., 2017. Ceramics in archaeology. From Prehistoric to Medieval times in Europe and the Mediterranean. Ancient craftsmanship and modern laboratory techniques I. Rome: L'ERMA di Bretschneider.
von Dassow, S., 2009. Low-firing and burnishing. London: A & C Black Publishers.
Daviau, P.M.M. and Graham, A.J., 2009. Black-slipped and burnished pottery: a special 7th-century technology in Jordan and Syria. Levant, 41(1), pp.41-58.
Dymańska, J., Cetwińska, A. and Manasterski, D., 2022. Different vessel surface polishing methods and mutual effects of their applications. EXARC Journal, 2022(3). Available at: < https://exarc.net/ark:/88735/10647 > [Accessed 05 January 2024].
Faust, A., 2002. Burnished pottery and gender hierarchy in Iron Age Israelite society. Journal of Mediterranean Archaeology, 15(1), pp.53-73.
Forte, V., 2019. Skilled people or specialists? Knowledge and expertise in copper age vessels from central Italy. Journal of Anthropological Archaeology, 55, article number: 101072.
Fragnoli, P., 2018. Pottery production in pastoral communities: archaeometric analysis on the LC3-EBA1 Handmade Burnished ware from Arslantepe (in the Anatolian Upper Eyphrates). Journal of Archaeological Science: Reports, 18, pp.318-332.
Gâţă, R. and Dragoman, R-A., 2012. A comparative technological study of the Neolithic burnished pottery from Vădastra and Cruşovu (Romania). Acta Musei Napocensis, 47-48/I, pp.27-45.
Gosselain, O.P., 1992. Bonfire of the enquiries. Pottery firing temperatures in archaeology: what for?. Journal of Archaeological Science, 19(3), pp.243-259.
Gosselain, O.P. and Livingstone Smith, A., 1995. The ceramics and society project: an ethnographic and experimental approach to technological choices. In: A. Lindahl and O, Stilborg, eds. The aim of laboratory analyses of ceramics in archaeology. April 7-9 1995, Lund, Sweden, in honour of Birgitta Hulthén. KVHAA Konferenser 34. Stockholm: Almqvist & Wiksell. pp.147-160.
Hale, Ch., 2014. The Middle Helladic ceramic sequence at Mitrou, east Lokris: A diachronic quantitative analysis and its implications for inter- and intra-regional interaction in central Greece during the Middle Bronze Age. PhD. The University of Melbourne.
Hein, A., Müller, N.S. and Kilikoglou, V., 2017. In and out: CFD modelling of the temperature distribution inside an ancient updraft pottery kiln. In: G. Vavouranakis, M. Katsianis, Y. Papadatos, M. Mouliou and P. Petridis, eds. Digital pasts for the present. Proceedings of the 2nd conference on computer applications and quantitative methods in archaeology. Greek Chapter (CAA-GR), Athens, 20-21 December 2016. Athens: Department of History and Archaeology, National and Kapodistrian University of Athens. pp.99-104.
Holmberg, E.J., 1964. The appearance of Neolithic black burnished ware in mainland Greece. American Journal of Archaeology, 68(4), pp.343-348.
Kordatzaki, G. and Zavadil, M., 2020. Wood-firing experiments: testing the efficiency of an updraft kiln. Forum Archaeologiae, 96/IX/2020. Available at: < https://www.alpinehiking.eu/forum/forum0920/96brand.htm > [Accessed 05 January 2024].
Lepère, C., 2014. Experimental and traceological approach for a technical interpretation of ceramic polished surfaces. Journal of Archaeological Science, 46, pp.144-155.
Lis, B., 2009. Handmade and burnished pottery in the eastern Mediterranean at the end of the Bronze Age: towards an explanation for its diversity and geographical distribution. In: C. Bachhuber and R.G. Roberts, eds. Forces of transformation. The end of the Bronze Age in the Mediterranean. Proceedings of an international symposium held at St. John's College, University of Oxford 25-26 March 2006. BANEA Monograph 1. Oxford: Oxbow Books. pp.152-163.
Livingstone Smith, A., 2001. Bonfire II: the return of pottery firing temperatures. Journal of Archaeological Science, 28(9), pp.991-1003.
Maniatis, Y. and Tite, M.S., 1981. Technological examination of Neolithic-Bronze Age pottery from central and southeast Europe and from Near East. Journal of Archaeological Science, 8(1), pp.59-76.
Osório, A.B., 2016. Variability within Late Bronze/Early Iron Age handmade pattern-burnished pottery from the Iberian peninsula. Monografias AAP 4. Lisbon: Associação dos Arqueólogos Portugueses.
Rice, P., 1987. Pottery analysis: a sourcebook. Chicago: University of Chicago Press.
Romanos, C.L., 2011. Handmade burnished ware in Late Bronze Age Greece and its makers. PhD. The University of Birmingham.
Rutter, J.B., 1983. Fine gray-burnished pottery of the Early Helladic III period the ancestry of Gray Minyan. Hesperia, 52(4), pp.327-355.
Rutter, J.B., 1990. Some comments on interpreting the dark-surfaced handmade burnished pottery of the 13th and 12th century BC Aegean. Journal of Mediterranean Archaeology, 3(1), pp.29-49.
Rutter, J.B., 1995. Lerna. A preclassical site in the Argolid. Volume III. The pottery of Lerna IV. Princeton, New Jersey: The American School of Classical Studies at Athens.
Rye, O., 1981. Pottery technology: principles and reconstruction. Washington, D.C.: Taraxacum Press.
Schiffer, M.B., 1990. The influence of surface treatment on heating effectiveness of ceramic vessels. Journal of Archaeological Science, 17(4), pp.373-381.
Shepard, A.O., 1956. Ceramics for the archaeologist. Carnegie Institution of Washington Publication 609. Washington, D.C.: Carnegie Institution of Washington.
Skibo, J.M., Butts, T.C. and Schiffer, M.B., 1997. Ceramic surface treatment and abrasion resistance: an experimental study. Journal of Archaeological Science, 24(4), pp.311-317.
Vagalinski, L.F., 2002. Burnished pottery from the first century to the beginning of the seventh century AD from the region south of the lower Danube (Bulgaria). Sofia: NOUS Publishers.
Zerner, C., 1978. The beginning of MH period at Lerna. PhD. University of Cincinnati.
Zerner, C., 1986,. Middle Helladic and Late Helladic I pottery from Lerna. Hydra, 2, pp.58-73.
Zerner, C., 2008. The Middle Helladic pottery, with the Middle Helladic wares from Late Helladic deposits and the potters' marks. In: W.D. Taylour† and R. Janko, eds. Ayios Stephanos. Excavations at a Bronze Age and Medieval settlement in Southern Laconia. British School at Athens Supplementary Volume 44. London: The British School at Athens. pp.177-298.