The content is published under a Creative Commons Attribution Non-Commercial 4.0 License.
Reviewed Article:
Experimental Roman Minting: Casting Silver-Copper Alloys into a Bronze Mould
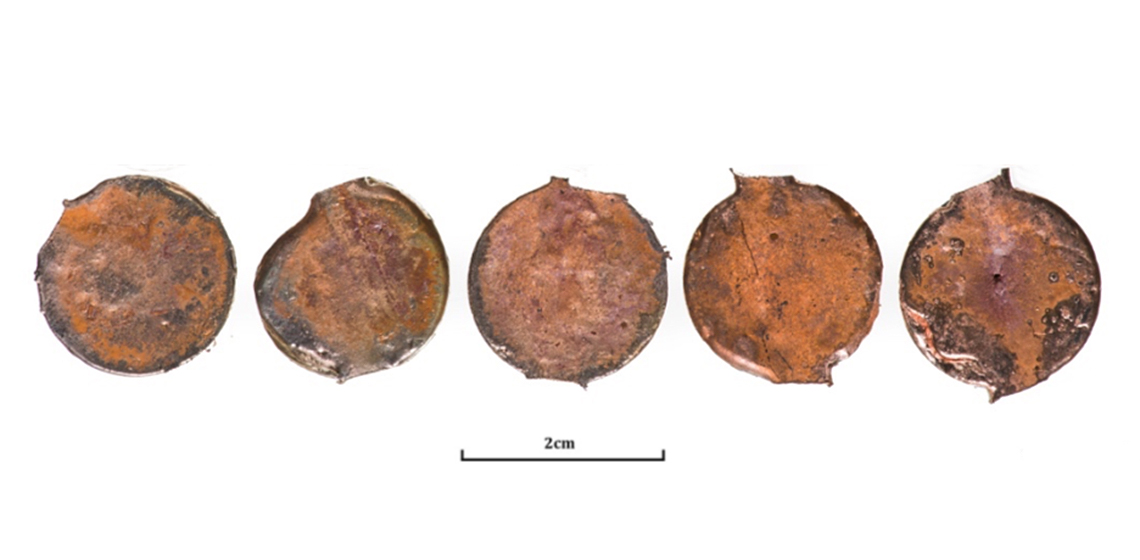
This paper provides the details of a Roman minting experiment, which used a bronze mould to cast debased silver blanks typical of the third century A.D. The investigation follows the paper ''Experiments reproducing Roman debased alloys" (George, 2020) which studied the manufacturing methods used in the production of Roman silver coinage. The purpose of those experiments was to both recreate the casting process used by ancient moneyers and test the suitability of different mould materials, including clay, limestone and bronze. Although the experimental moulds offered new insights into minting technologies, the initial bronze mould experiments failed to produce blanks with a silver content lower than 70 %. Upon reflection, this was caused by decisions made in the design process, such as the choice of coating agent, which negatively affected the success of the castings. The current investigation revisits the bronze mould experiments using a different release agent. and results of the second bronze mould experiment are presented here.
Flan Technology
Determining the ancient processes used in the production of Roman silver coinage is challenging due to a lack of archaeological finds associated with their manufacture. Despite the lack of archaeological evidence for Roman minting practices, two crucial stages of production were necessary for the creation of Roman silver coinage; firstly, the fabrication of a blank or flan and secondly the impression of the obverse and reverse design. This paper will be examining the former.
The completion of a preliminary visual inspection of 37 Roman silver coins from the third century AD identified the remnants of casting channels called sprues on some of the coins. This indicated that the flans were cast with a mould (George, 2020: 79). The presence of casting sprues also indicates the mould typology; individual depressions, connected by channels that distribute the molten metal.
Although only two of the 37 coins investigated (Elagabalus, RIC131 and Severus Alexander RIC178d) retained this feature, similar protuberances have been identified by Bernhard Woytek (2020: 132). The author recognised that some imperial denarii showed signs of casting sprues which had been neatly clipped from the blank. One coin in particular minted in Rome under Hadrian (RIC Augustus 208) had been clipped on both sides indicating that the blank had been in the middle of a string of cast flans (Woytek and Blet-Lemarquand, 2017 no’5).
Despite evidence that Roman moneyers were casting their silver flans in moulds, no flan moulds associated with official mints have been found in the archaeological record. However, the lack of moulds is accompanied by the absence of other related minting apparatus such as coin dies (George, 2020: 77).
The last complete compilation of coin die finds was composed by Malkmus in his paper ‘Addenda to Vermeule’s Catalog of Ancient Coin Dies: Part 1.’ (1989). Only three dies have been found dated to the third century A.D used for striking silver denominations (Table 1). When taking into account the most modest of estimations for dies, there is an unquestionable lack of material from the Roman era. The small number of die finds in the archaeological record indicate that coin dies were kept secure (Malkmus, 1989: 80).
Issue | Date | Face | Denomination | Material | Find Location/Date |
Septimius Severus | AD209 | Reverse | Denarii | Unknown | Budapest 1941 |
Maximinus | AD234 | Reverse | Aureas or Denarius | Bronze | France, 1953, Musee Monetaire, Quai de Conti, Paris |
Maximinus | AD235-238 | Obverse | Aureas or Denarius | Bronze | Angouleme, 1934, Musee Monetaire, Paris |
Table 1: Roman coin die finds used for striking silver coins between AD193 and AD260 Malkmus (1989)
The scarcity of archaeological evidence for Roman minting practices suggests that materials used for the production of silver coinage were destroyed after use. It seems likely that once official dies reached the end of their life, they were destroyed by mint workers to prevent them falling into the wrong hands. The correct disposal of these dies being imperative to security. It is also reasonable to suggest that official Roman flan moulds were disposed of in a similar manner.
The vast majority of Roman dies currently on record are of the high tin bronze variety. This alloy is robust enough to withstand the impact of continuous striking and malleable enough to engrave. In addition, exhausted dies made of hardened bronze could be melted down and re-used, leaving no trace in the archaeological record.
Bronze Mould Use in Antiquity
Moulds made of bronze and iron were regularly used for the manufacture of metal objects in antiquity. Piece moulds, fabricated from bronze are common from the Middle and Late Bronze Ages (Tylecote, 1986: 84-93). The method of production for creating bronze moulds is uncertain. It is likely that bronze moulds were cast using a clay or limestone mould, however no such master moulds have been unearthed (Webley and Adams, 2016: 325).
Chemical analyses of late Bronze Age moulds revealed them to be made of tin-bronze, containing around 11% lead (Webley and Adams, 2016: 325). However, the low thermal resistance of bronze has often led scholars to theorise that these Bronze Age moulds were not used for direct casting, but for creating patterns made of wax or lead (Tylecote, 1986: 93-94). This idea has been the topic of some debate, with authors highlighting the practical difficulties with the proposed lost-lead castings method (Foltz, 1980).
An original bronze axe mould from France (Voce, 1951) has confirmed their suitability for direct casting. The comparison of moulds and corresponding bronze implements also show that the final castings often fit perfectly into the moulds. This would not be the case for the last wax or lead method, where one would expect the final cast pieces to be smaller than the mould (Howard, 1983: 492). Moulds found in the archaeological record show evidence of use, with cracks visible along the edges, however these can also present as a result of casting flaws. In addition, the discovery of later Bronze Age axes displaying casting flash, indicates that they were cast directly into a mould (Webley and Adams, 2016: 332).
Numerous casting experiments and replications of bronze axes have demonstrated the suitability of bronze moulds for casting metal objects directly (Voce, 1951; Drescher 1958; Stansby 1984; Jochum Zimmerman et al. 2003; Wirth 2003; Ottaway and Wang 2004; Fregni 2014; Heeb and Ottaway 2014).
The durability of bronze is the perceived advantage of using this metal for flan moulds. However, the amount of castings a bronze mould can withstand remains unknown. Experiments with bronze moulds offered differing use life estimates. The bronze mould used by Ottoway and Wang (2004) survived nine castings, finally failing on the tenth. Drescher (1958) completed 15 castings with no signs of failure. Similarly, Fregni (2014) cast into a mould multiple times without issue. Estimates of a 50-casting limit proposed by Tylecote (1986) and Coghlan (1975) seem arbitrary without any physical investigations backing this number up. The use life of a bronze mould will likely vary depending on the elemental composition, quality of fabrication, preheating parameters and coating agents. In addition, the size and shape of the object to be cast may impact the amount of castings a mould can withstand.
No flan moulds associated with official Roman mints have been uncovered, however Roman moulds used for the creation of other objects have been found. Although not directly related to the manufacture of coinage, these moulds can provide information about the available materials and technologies being used by Roman metallurgists.
Excavations in 1993 at Old Buckenham, Norfolk unearthed a Roman-British mould made of bronze (Bayley et. al, 2001). The mould was used for casting bronze brooches and was discovered with a casting in situ. Found alongside the mould was another as-cast brooch blank with the same design and the lower parts of three unfinished cast brooches of the same type. The bronze mould comprised two pieces or valves, which when placed face to face created a stand made up of three feet. The top of the mould had an in-gate corresponding to the foot of the brooch (Bayley et.al, 2001: 100). Elemental analysis of the mould was carried out using x-ray fluorescence and found it to be made of bronze, containing trace amounts of lead and zinc.
A close inspection of the moulds led to a few important observations. Firstly, the authors found that the inner surface of the mould was dressed with a coating agent such as tallow or oil (Bayley et. al, 2001: 112). Dressing the mould would minimise the potential for mould failure or adhesion to the mould by providing a lubricated barrier between casting and mould.
The authors observed two pairs of holes in the front part of the mould. They determined that hoops of iron wire would be threaded through the mould, to fasten the parts together (Bayley et.al, 2001: 113). When the two sides of the mould were placed face to face they would have aligned with a perforation on the back, and the wires could be held together with a peg or pair of wedges. This would be easy to remove when the mould was hot, and the casting could be taken out quickly.
The authors also observed that the craftspeople appeared to have encountered some difficulty with the metal solidifying before it had completely filled the mould. This was evident by a number of incomplete castings found alongside the moulds. The authors suggest a solution to this would be superheating the metal to be cast and pouring at a higher temperature or to heat the mould prior to casting (Bayley et. al, 2001: 113).
The evidence from the Old Buckenham clearly demonstrates that Roman metallurgists were using bronze moulds to cast small objects. Roman moneyers may also have adopted bronze in the creation of their flan moulds, following a similar process.
Bronze Mould Experiments
In George, 2020 the casting process was recreated using three different mould materials (clay, limestone and bronze). However, this paper will look specifically at the results gained using the bronze mould. The main question being addressed in this paper is whether small silver-copper-alloy objects such as flans can be cast directly into a bronze mould.
The bronze mould (See Figure 1), which was created by the Engineering Department at the University of Liverpool was designed to reflect the denarius and Antoninianus coinages (George, 2020: 83). Measurements taken from the 37 coins investigated determined their diameters varied between 18.5 mm and 23 mm. The average diameter of Roman coins being 20.5 mm, with an average thickness of 1 mm. The bronze mould should be capable of producing blanks of a standard weight with a significant degree of accuracy. The ingress channels should enable the flow of molten metal to reach each depression. Pins fastened the bronze mould tightly together to stop any flashing upon casting. The bronze mould was a copper-tin alloy containing 12% tin.
The casting of silver-copper alloy blanks with varying compositions (80 %, 50 %, 30 %, 20 % and 5 % silver) was attempted in the bronze mould. Pure silver granules, copper pipe, lead and tin were weighed individually to produce blanks of an accurate composition. The metal to be cast was placed in a clay-bonded graphite crucible and heated in an electric furnace until the furnace reached 1250 ℃. The silver, copper (and tin) were placed into the crucible first. Charcoal was added to the crucible to prevent oxidation. For the creation of blanks containing lead, the crucible was briefly removed from the furnace and the lead added after 18 minutes. Lead has a low melting point of 327.5 ℃ and requires much less time in the furnace to melt. The silver-copper alloys took approximately 20 minutes to become molten and liquid enough to pour.
The bronze mould was positioned upright in a tray of sand, allowing the molten metal to be poured carefully into the gate. This created a safe working space, as any overspill from the mould would settle on the sand. The Pouring of the molten metal was executed with caution to avoid imperfections that can frequently occur at this stage. The bronze mould was covered in powdered charcoal, which was expected to act as a release agent to aid the removal of the flans following casting. Preheating the bronze mould to 300 ℃ was necessary to prevent an explosive reaction when the molten metal contacts the mould surface.
The experiment found that blanks with 80 % silver were easily cast in the bronze mould, however the metal became securely fixed to the surface. Further casting attempts revealed the bronze mould to be largely unsuccessful for casting blanks with a silver content below 70 %. When the molten metal was poured into the bronze mould, it cooled quickly in the gate and became stuck. Several attempts were made to improve the fluidity of the molten metal cast into the bronze mould by increasing the temperature, with no success.
As a result of these failed attempts, an additional set of castings were carried out, this time adding small amounts of tin and lead to the alloy, in an attempt to improve the fluidity of the castings. If successful this would have have offered a good explanation for the increasing amounts of these metals observed in third-century Roman silver coinage (Ponting, per comm.). However, even with the addition of small amounts of tin and lead, the blanks cast in the bronze mould failed.
Despite the failure of the bronze mould to produce silver-copper alloy flans for the full-range of intended compositions, the conclusions drawn from the experiment were that the use of a bronze mould for casting Roman silver flans remained a possibility. Upon reflection the choice of charcoal as a coating agent may have negatively affected the castings.
Experiments Revisited
The decision was made to repeat the bronze mould experiments with minor modifications. The previous castings had all failed because the molten metal did not flow into the mould. Since altering the alloy composition of the blanks made little difference to the castings, the decision was taken to change the coating agent in favour of a substance that provided better lubrication. Upon reflection, the use of an alternative coating agent could improve the flow of metal and also aid the removal of the solidified flans.
Coating Agents in Antiquity
Modern castings in metal moulds often use coating agents. All materials, including bronze, exhibit some degree of porosity and the level of porosity in a mould material has a noticeable effect on release performance. A coating agent applied to the surface of a mould will create a thermal barrier between the metal and mould resulting in reduction of thermal shock, casting defects and adhesion of the cast metal to the mould.
Since no official Roman flan moulds made of bronze have been found in the archaeological record, it is not possible to determine if a coating agent was used. However, evidence from a limestone mould found at a Roman forger’s mint at Châteaubleau, Seine-at-Marne in France indicated that a release agent had been applied (Pilon, 2003: 8). The use of a coating agent may be necessary for bronze moulds to prevent the cast from adhering to the mould surface. The chosen coating agent should adhere to the surface of a mould and provide adequate protection against metal penetration. Alternatively, a coating agent such as greasy tallow could have been used to seal the surfaces of porous types of limestone. A sealant would prevent the metal from seeping into the mould material upon casting.
Carbon based substances make effective release agents, however the powdered charcoal used in the previous experiment did not have the required consistency to stick to the bronze mould. For the second round of bronze mould experiments liquid graphite was used to dress the mould. Graphite was readily available in antiquity with ancient artisans commonly using graphite to create highly reflective surfaces on decorative pottery (Gardner, 1979: 23). Large deposits of graphite exist across central Europe, but there is no evidence that the Romans ever exploited them (Richardson, 1990: 6). Liquid graphite uses natural graphite powder dispersed in an acrylic polymer emulsion. The decision to use a modern coating agent was largely due to time constraints. However, more authentic coating agents readily available in antiquity have been used in previous experiments. Northover added beef dripping or tallow to carbon which allowed the coating agent to be painted onto the mould (Peter Northover, per comm.). Bayley et. al suggested that either tallow or oil would make a sufficient dressing (Bayley et. al, 2001: 112). Other suitable release agents include soot and lamp black mixed with lard oil (David Tokar, per comm.)
Results
The application of a liquid graphite coating agent to the bronze mould produced much better results compared to the earlier attempts. With this small alteration to the casting process it was possible to produce blanks with all the intended compositions (see Table 2). Once a suitable dressing was applied the molten metal flowed into the mould and once cooled the blanks were easily extracted. This evidence demonstrates that the selection of a suitable coating agent is pivotal to the success of castings.
The tin-bronze mould (12 % tin) offered excellent strength and wear resistance. Molten metal was repeatedly cast into the mould with no indication of stress or failure of the mould. The mould was used a total of 15 times for the experiments that formed part of a PhD thesis (George, 2019). It was later used for subsequent student projects and remains fully operational. This evidence confirms that metal moulds are capable of multiple castings. Therefore, ancient bronze moulds could be reused repeatedly without failure. The creation of a reusable mould would significantly reduce fabrication times and is more suitable for the mass production of Roman silver coinage than expendable moulds made of clay. Tin-bronze is also relatively easy to cast, making this a desirable material for the creation of flan moulds in antiquity.
One interesting feature of the flans cast into the bronze mould is the uniformity of the weights achieved, with the standardization being quite striking. After trimming any channels from the blanks, the weights ranged between 7.0 g and 7.9 g. Very little effort was required to produce this consistency and if more time had been taken to trim the blanks then even greater conformity could have achieved.
Ascertaining the degree of accuracy available to official mint workers is important because weight fluctuations in Roman Imperial coinage are common and it is necessary to determine the cause of these fluctuations. If Roman moneyers were capable of casting coins to a desired weight, then the changing standards could suggest manipulation of the weights over time as a form of debasement, alternatively they may indicate extensive weight losses through post depositional corrosion.
With a suitable coating agent, the bronze mould was capable of producing cast blanks of a consistent weight and size. Blanks cast in the metal mould were of a uniform size. However, any additional striking would introduce slight size differences due to the inevitable randomness of the force applied by each hammer blow (See Figure 2).
Compositions |
50% Ag/50% Cu |
40 % Ag/60% Cu |
30% Ag/70% Cu |
20% Ag/80% Cu |
15% Ag/ 85% Cu |
70% Cu/ 10% Ag/ 10% Pb/ 10% Sn |
85% Cu/ 5% Ag/ 5% Pb/ 5% Sn |
Table 2: Compositions of silver-copper alloy blanks cast in the bronze mould
Microstructural Analysis of Blanks
The blanks cast in the bronze mould (See Figures 3-7) all have a relatively fine-grained microstructure which is indicative of fast cooling within the mould. The grain size is much smaller than those observed in ancient examples. However, the grain size of the blanks cast in both clay and limestone were also much smaller (George, 2020:91). This indicates that casting within a mould may have taken place in an enclosed furnace structure that allowed for slow cooling.
Discussion and Conclusion
Channels found on Roman silver coinage confirm they were cast in moulds, despite the absence of these in the archaeological record. The limited archaeological evidence for Roman minting practices shows that Roman mint workers used bronze dies for striking coins, raising the possibility that they also used bronze for their flan moulds. The process of creating a bronze mould is more time consuming than making clay or stone moulds. The experimental bronze mould was hard-wearing and even after numerous castings showed no signs of failure. A mould fabricated from bronze would be capable of producing many castings and would only be discarded after excessive wear and tear. Therefore, a reusable bronze mould would be much less labour intensive for the production of Roman silver coinage than the alternatives.
The use of bronze flan moulds would also explain the absence of official Roman moulds in the archaeological record, because any exhausted moulds would be melted down for the raw materials. Recycled bronze moulds would leave no trace, effectively making it an invisible form of flan technology.
Further Research
At present these conclusions rest on findings from casting with a small mould and it would be interesting to see if this success could be replicated when the size of the mould is scaled up for mass production. The grain sizes observed within all blanks produced during the experimental investigation (figures 3-7) are much smaller than those found in the ancient examples. All of the experimental blanks were left to cool slowly within their individual moulds but despite this the grain-size is much finer. This evidence indicates that the ancient blanks were left to cool over longer periods. If the moulds were considerably larger, then the mass of cast metal would allow for slower cooling. Another potential explanation for this could be that ancient moneyers were casting into moulds that were contained within a furnace structure and allowed the entire furnace to cool after casting. Alternatively, the moulds could have been left to cool close to an open furnace, rather than in a cool air-conditioned laboratory. If many moulds were used for a large production cycle then they may have been left to cool for longer, whilst the other moulds were filled.
Bibliography
Bayley, J., Mackreth, D.F. and Wallis, H. Evidence for Romano-Bristish Brooch Production at Old Buckenham, Norfolk. The society for the promotion of Roman studies. 2001.
Coghlan, H.H. 1975. Notes on the prehistoric metallurgy of copper and bronze in the old world. Pitt Rivers Museum Occasional Paper on Technology 4, Oxford, 112-15.
Drescher, H. 1958 Der Überfangguss, Mainz.
Fregni, E. 2014 The complete metalsmith: craft and technology in the British Bronze Age, PhD thesis, University of Sheffield.
Foltz, E. 1980. Guss in verlorener Form mit Bleimodellen? Archäologisches Korrespondenzblatt 10, 345-9.
Gardner, E. 1979. Graphite painted pottery. Archaeology (July/August): 8–23
George, N., 2019. The Manufacture of Official Roman Silver Coinage and Blanks Between AD193 and AD270. Unpublished PhD thesis. University of Liverpool.
George, N., 2020. Experiments reproducing Roman debased alloys. In Butcher, K. Debasement: manipulation of coin standards in pre-modern monetary systems. Oxbow Books. Oxford.
Heeb, J. and Ottaway, B. 2014 Experimental archaeometallurgy, in B. Roberts and C. Thornton (eds), Archaeometallurgy in Global Perceptive, New York: 161–92.
Howard, H. 1983. The bronze casting industry in later prehistoric southern Britain: a study based on refractory debris. PhD thesis, University of Southampton.
Jochum Zimmermann, E., Künzler Wagner, N. and Kunnert, U. 2003 Zurück zur gussform! Einfluss des gussformmaterials auf die mikrostruktur eines geogossenen bronzeobjekts, Experimental Archaeology in Europe, Bilanz 2002: 79–91.
Malkmus, W. 1989. Addenda to Vermeule's catalog of ancient coin dies. Part 1. SAN, 17(4), 80-85.
Ottaway, B. and Wang, Q. 2004 Casting Experiments and Microstructure of Archaeologically Relevant Bronzes (British Archaeological Reports S1331), Oxford.
Pilon, F., 2003, Experimental evidence of direct silver surface on silver-copper alloys. Application to the analysis of ancient silver coins. Archaemetallurgy, Milan.
Richardson, W. F. ‘Some modern elements in an ancient setting’. In Prudentia 18.1 May 1986.
Stansby A. 1984. The Production and Finishing of Wrought Bronze Tools and Other Objects. PhD thesis, Faculty of Physical Sciences, University of Oxford.
Tylecote, R.F. 1986 The Prehistory of Metallurgy in the British Isles. Institute of Metals.
Voce, 1951. Bronze castings in ancient moulds. In Coghlan, H.H. Notes on the prehistoric metallurgy of copper and bronze in the old world. Pitt Rivers Museum Occasional Paper on Technology 4, Oxford, 112-15.
Webley, L. and Adams, S. 2016. Material genealogies: bronze moulds and their castings in later Bronze Age Britain, Proceedings of the Prehistoric Society 82: 323–40.
Wirth, M. 2003 Rekonstruktion bronzezeitlicher Gießereitechniken mittels numerischer Simulation, gießtechnologischer Experimente und werkstofftechnischer Untersuchungen an Nachguss und Original, Aachen
Woytek, B.E. and Blet-Lemarquand, M., The C. L. CAESARES denarii RIC I² Augustus 208. A pseudo-Augustan unsigned restoration issue. Corpus, die study, metallurgical analyses. Revue Numisamtique. 2017: 174. Pp. 183-248.
Woytek, B.E. 2020 Metal and system in Roman imperial mints. Flan production, quality control and internal organisation of minting establishments during principate. In Butcher, K. Debasement: manipulation of coin standards in pre-modern monetary systems. Oxbow Books. Oxford.