The content is published under a Creative Commons Attribution Non-Commercial 4.0 License.
Reviewed Article:
Scored Basins from Late Minoan Crete: an Experimental Interpretation from Construction to Functionality
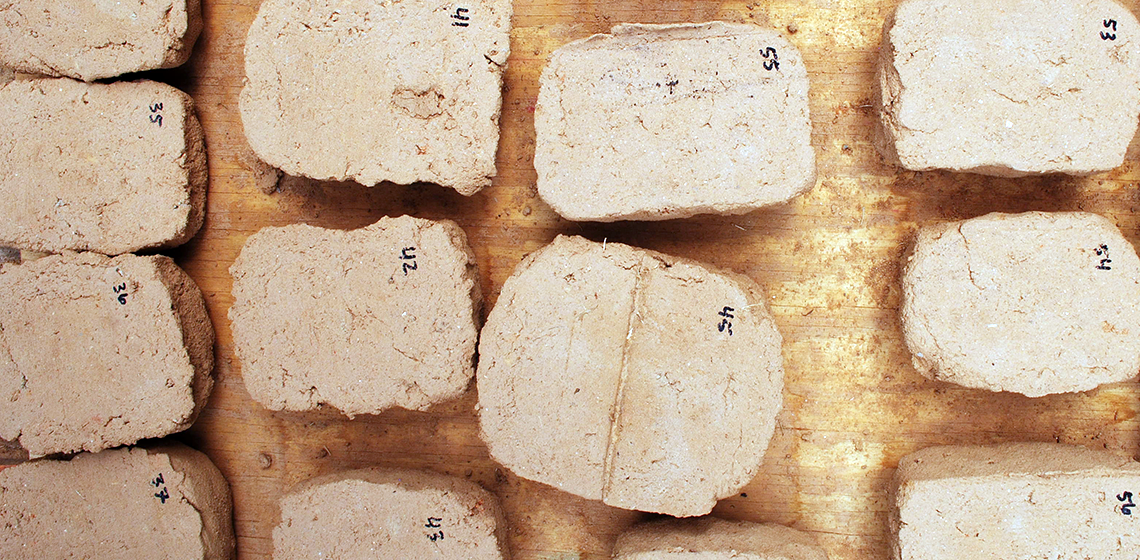
During the Bronze Age in Crete, agriculture, pottery production, metallurgy, textiles, architectural feats, trade, and other specializations flourished. Throughout habitation on Crete, pottery production was an area of craftsmanship and practicality from the end of the Neolithic to Mycenean and Iron Age. This experiment, however, relates to the Late Minoan I period in the geographical region of Mochlos.
The Artisan’s Quarter is a building that contains various rooms that have been tied to craftsmanship and workshops. Once connected by a land bridge to the ancient site of Mochlos, this particular building would have been the place of vast amounts of pottery production. Activities would have ranged from the clay preparation to forming the vessels by hand or wheel to the decoration choices to the firing, and then finally to the exportation. For this experiment, the construction of the kiln was based on the research of two kilns of differing sizes and characteristics in this area, combined with other Late Minoan sites on Crete, to understand firing techniques and building aspects.
Chalinomouri was another place of specialization. It was a small habitation that seemed to concentrate on agriculture. The pottery collected from this site varies in date and function, which is similar to that of the Artisan’s Quarter. As seen in the excavations at Mochlos, the scored basins were discovered fragmented within various rooms of different activities, suggesting their fabrication and possible function.
Experiment Objectives
The objective of the experiment was to identify the various functions of scored basins found in Late Minoan Crete. This paper describes the experimental steps taken to evaluate the process which may have produced these Bronze Age vessels. It also evaluates the skills and techniques of the ancient potter in producing the large body vessels and establishes a correlation between their functions.
Context
Mochlos was a major settlement on Crete during the Neolithic period, which evolved into a well-established civilization (Moorey, 2019). The main concern of this study focuses on the Late Minoan period, often known as the Neopalatial period (Soles, et al., 2003).
The transitional phase of the Middle Minoan period to the Late Minoan period resulted from different dynamics of ceramic production. The concentration of the Late Minoan period for this study resides around the Late Minoan IB period which is estimated as 1500-1450 B.C. (Popham, 1970, p.227).
Experimental Context
The experiment has three aspects: the construction of mudbrick, the construction of a Minoan kiln, and the construction of a scored basin prototype. Minoan architecture usually consists of mudbrick and other raw materials available during that time. Luce and Bolton (1976, p.10) described mudbrick as being “a contemporary surface material, mixed with freshly dug clay if not already sticky enough, and with straw or other organic fibrous matter often added”.
Oftentimes sand can be added (Emery, 2009, p.2), which can make the product grittier. Once the clay mixture and the organic materials were kneaded and mixed together, they would be left to dry in the sun with a continuous rotation for approximately eight days (Emery, 2009, pp.3-4). This provided evidence for the length of time required to sunbake the mudbrick made for this experiment.
Once this was established, research revolved around the construction of the kilns that were excavated in the rear yard of Building B of the Artisan’s Quarter on Mochlos (See Figure 1). Firing in kilns is an important stage in creating ceramic vessels in Minoan culture. There are various styles of kilns present in the archaeological record around Crete. The most common shape is circular or horseshoe-shaped with an opening at the front (Betancourt, 1987, p.118). Inside the bottom are a number of channels covered with a perforated ceramic slab that allowed for the heat to travel up and to provide a surface for the pottery during the firing process (Betancourt, 1987, p.118). The dome of the kilns can either be temporary or permanent depending on the size of the ceramic vessels (Bryant, 1997; Hasaki and Raptis, 2016). The size of the kilns can vary as well, such as the one from Kommos that has four preserved channels which have been presented as being approximately 0.25m wide, which would allow space for the heat from the firepit to rise through the pottery vessels (Shaw, et al., 2001, pp.8-18). Further reviews of the firing process had been conducted by a researcher that resulted in a reconstructed Late Minoan kiln (Day and Kobik, 2019) and therefore their techniques were used as an interpretation when constructing the Mochlos kiln. As for the construction of the ceramic vessel known as the scored basin, heavy emphasis was placed on the Neopalatial catalogue in the Mochlos IB volume (Barnard, et al., 2003) (See Figure 2). The coiling technique was used to produce the ceramic vessel (Casson, 1977, p.13) which simply involves creating the same size coils and building up from the base into a shape that is desired by the potter. Examination of the ceramic vessel through the evaluation of its typology, function, and raw materials had been made within this experiment (Rice, 1987; Blackman, 1992; Orton, et al., 1993).
Experiment Method
The methodology for this experiment relies heavily on the archaeological record and the chaîne opératoire concept. According to Jeffra (2015), the chaîne opératoire method within experimental archaeology concentrates on the manufacturing processes rather than focusing on the political and social aspects of ceramics. Throughout this experiment, processes were made in order to complete one goal of completing a pottery vessel in order to determine its functionality.
The following sections involve pilot tests, raw material collection and preparation, construction of both the kiln and the ceramic vessel, data collection, and finally a discussion on several aspects attributed to the experiment itself. The results portion of this experiment has been added within each part, rather than a separate section so that the information and data provided could be read fluidly while still connecting the subject to the resulting data.
Recording techniques involved creating tables that would display measurements, temperatures, and analysis made through notetaking and photographs.
Part 1: The Mudbrick
Fragmentary evidence from archaeological research of the Artisan’s Quarter indicated mudbrick construction (Nodarou, et al., 2008, p.3006), so this was selected for this experiment.
Mudbrick usually consists of a combination of clay, water, sand, and organic materials (straw, grass, and microscopic elements of quartz, chert and phyllite) (Nodarou, et.al., 2008, p.3004). At the beginning of the mudbrick preparation, a pilot test was conducted to analyse what clay source would be the best. The location of the first clay source came from the back yard of the author’s home. The clay was a light grey colour and had a gritty texture without the addition of sand. Once sand and water were added to the clay source, four test bricks were made with the largest measuring approximately .03m by .38m (See Figure 3). Their measurements are smaller compared to the archaeological record from Mochlos (Nodarou, et al., 2008, p.3000) because the goal of these test tiles was to determine the proportions of clay, sand, and water, not their size. This consideration of just proportion resulted in the tiles being of different shapes, thicknesses, and consistency. For instance, the pilot tiles broke after two days of sun baking and could have also presented another problem being that this clay source was either not properly retrieved or processed thoroughly. Another clay source had to be located and a different technique adopted if these bricks were to be used in the Minoan kiln.
Part 1a: Final Mudbricks
Red clay was sourced for the mudbricks (See Figure 4a). Sand was added to the mixture of the clay and water, which in total weighed 48.57kg (See Figure 4b). The mixture itself consisted of 50% dry powdered clay with 25% sand and 25% water added together. This resulted in six production periods (which were conducted over eighteen days). It took approximately ten minutes to collect the clay from the source and from approximately forty minutes to an hour to mix the raw materials. The distinction for the production periods was made as a recording technique due to the limitations of time and materials made available.
The consistency of the materials was a gritty, yet sticky smooth texture. After a total of three days for each production period, the mudbricks went from a dark brownish-red color to a light brownish-red. Overall there were 48 small bricks weighing approximately 450g, measuring 7cm by 12cm; 4 medium bricks weighing approximately 910g measuring 12cm by 15cm; and 7 large bricks weighing approximately 2.27kg measuring 17cm by 20cm. Once the 59 mudbricks were sun baked, they were all photographed, weighed, measured, and set aside for the construction of the Minoan kiln providing the floor, walls, and possible shelving unit (See Figures 5a and b). Due to the time taken on production brick production ceased after the sixth production period and the bricks were stored outside, with protection from the weather.
Part II: The Scored Basin
An aim of the experiment was to manufacture a scored basin. A published scored basin was chosen from the Mochlos IB volume to fabricate (See Figure 6). In order to understand the construction of the large-scale version of the basin chosen for research, the author had to practice their techniques by completing two pilot tests. One was made from stoneware (that can withstand high temperatures if needed; Rice, 1987, p.63) which had to be purchased, while another was modelled out of the same red clay that was used during the mudbrick process. The stoneware clay was made into a small version of the basin, this was intentional because the only desire up to this point was to practice the coiling method. Along with the technique, there was also another element of practice and that was the scoring on the interior. Inside this particular example was the “X” shaped version of the scoring, which would later determine the outcome of the interior on the large-scale version (See Figure 7).
The second small-scale pilot scored basin, however, was made from the red clay that was retrieved and processed only with water. A base was first created and then 22 coils were attached to the base and one another to form a small-scale version of the scored basin from Mochlos IB. Handles were applied to the vessel after it had dried for over a day. Once this was complete, the vessel was left to sun dry for another day and left until the firing of the kiln. Production of each test basin required two days due to the reduced size.
Part 2a: Mochlos Scored Basin
A scale version of a Mochlos scored basin, IB.270, was recreated (See Figure 8). Commercial clay was used in the hopes that fewer impurities in the mix would provide more reproducible building and firing. The clay purchased had an earthenware base and would withstand a wood firing and reach a Cone 6 or higher (Cone 6 is a form of temperature range of approximately 2200°F, used for firing ceramic).
22.68kg of clay were purchased and divided into two separate bags weighing 11.33kg. One bag was used to create a pottery vessel based on the observations made by the measurements within the published Mochlos IB Catalogue. The preserved scored basin that was used as a guide had measurements of approximately .41m in height, .55m in rim diameter, and finally the base diameter was .34m (Barnard, et al., 2003, p.57). Two types of handles were presented in the photograph as well as the description in the publication, so they were translated to this prototype scored basin. The inside scoring was described as either being “X” shaped or simply diagonal lines going across each other. The latter was chosen in order to give a different perception of the scoring pattern than the red clay and stoneware test pilots. The depth of scoring was not mentioned in great detail within Soles, et al. (2003), but the example made for the experiment stayed at a shallow depth of approximately .010m.
Construction of the scored basin consisted of the coiling technique which can be seen archaeologically (Knappett, 1999, p.113) as well as in today’s ceramic industry. Tools used during this process were some basic pottery tools and by hand. Throughout the construction a total of 55 coils were made, they were approximately 38-40cm long and approximately 2cm thick. The entire process was completed in three days with a total of 10-11 hours of work. After the third day, the vessel was left to slowly dry for a couple of days and then the handles were attached. Four handles were attached to the vessel, two of them were designed to look like knobs and the other two are described as being irregular lug shaped. After this, the vessel was left covered and through slight touch-ups, the scored basin was then left completely uncovered for five days to be bone dry upon firing.
Part 2b: Results of the Unfired Scored Basins
Regarding the pilot test versions of the ceramic vessel, the stoneware clay seemed to have consumed the least time in this portion of the experiment. Stoneware was purchased through a local pottery shop. The clay itself was a light grey that turned completely white after the drying phase. The scoring inside as stated above was only designed as an example for the large-scale version. “X”-scoring the inside of the vessel was done using the slightly sharp end of a pottery tool.
However, when the visual analysis was made upon the red clay pilot test it seemed to replicate a similar color and style of the IB.270 scored basin. The scoring was made the same way as the stoneware clay pilot test, the same pottery was used as well. A difference between the two pilot tests was that this version had a wider mouth and body as well as the application of the handles. Although the hand-building technique went smoothly, the base of the red clay vessel within the interior suffered some cracking upon the firing process. This may have been due to how the clay may not have been fully processed even though it took a total of two hours to mix the water and dry clay by hand. The moisture and small particles within the matrix of the clay may not have benefitted the vessel in the long run.
In the end, the large-scale version of the scored basin suffered various complications during construction. The process of drying seemed to go too quickly, and this resulted in various cracks on the exterior as well as the interior of the vessel. In order to fix these flaws, at first, the initial instinct was to try to get the entire vessel wet again, by using a spray bottle to liberally allow for water to seep into the pores of the clay. After this, scoring occurred in order to allow for the attachment of small pieces of the clay. However, none of this seemed to work, so another technique was used and that was the creation of slip. This technique is used amongst modern-day potters in order to restore their ceramic vessels and help prevent further cracking upon the firing process (Casson, 1977). This alternative technique seemed to work, and the ceramic vessel was then documented through photographs and put into a safe place to prevent any other damages. All three vessels that were created through this portion of the project were set aside for the kiln firing that took place a couple of days later.
Part 3: The Minoan Kiln
The construction of the kiln took place in the same location as the mudbrick productions and clay preparations were. Materials used were the same as before with the bricks, but the addition of reclaimed industrial bricks and firebricks were also needed. Firebricks and industrial bricks would not have been available during the Late Minoan IB period but it is presumed from Soles, et al. (2003) that mudbricks or fragmentary sherds would have been used in the construction of a kiln. These additional types of bricks were added due to the constraint on time, limitations on the quantity of materials and the labor provided to the author. Kiln A from the Artisan’s Quarter was used as a model, therefore, a blueprint was created on the bare ground that was picked because of its stability and protection from rain and other disturbances.
After a visual plan was made, the work was put in over two months with the total of 197 bricks (including industrialized bricks, mudbricks, and firebricks) that resulted in weighing approximately 310.7kg with approximately 181.44kg in the clay mortar (using the same formula as the mudbricks). The total length of the kiln was 290cm with the flue being 160cm and the combustion chamber being 115cm long by 79cm wide. Inside the kiln, mudbricks were laid down with the hopes of retaining heat upon firing. A perforated ceramic slab was added to act as a shelving unit for the large scored basin. On each side of this slab were small mudbricks that were attached to the kiln walls and the industrial brick to act as small shelves for the pilot test versions of the scored basin. Once the kiln construction was underway, plans were made to close the top (See Figures 9a and b). This proved to be a very difficult aspect and resulted in two pilot tests of the dome and one final temporary dome that had been decided on after the firing pilot test. Below are the different firings that occurred sparsely throughout a two-week time span and their results.
Part 3a: Firing Pilot Test
The pilot test firing was conducted to test out the strength of the kiln as well as to see if the dome that was built out of two triangular mudbricks and clay coils could hold up on its own (See Figures 10a and b). Also, cones were not added inside because the first initial goal was to just dry the dome. The dome was supported by a wooden frame just in preparation for the clay dome (See Figure 11). There was some speculation that this dome may not work due to the nature of the triangular mudbricks and the clay having different moisture content.
The recording of this pilot test firing did not rely heavily on data collection but rather on an observatory perspective. Meaning that there was not a detailed collection of data; no temperatures were taken, no records were kept of the fuel intake. This test was simply to determine if the kiln could withstand a firing as well as to test the process of building a dome lid (See Figure 12a).
The fire began in the evening. and within an hour the kiln was visually observed as retaining a considerable amount of heat as a result of which the wood frame that was made out of plywood for the support system in the dome had started to burn away. The burning of local hydrangea wood lasted three hours, in which fuel was added to the fire periodically during that time. The reasoning behind using a three-hour time frame was due to an observation made halfway through the burning process. The dome was changing from a light brownish red colour to a dark brownish red indicating that the clay itself was drying and losing moisture.
Unfortunately, the dome did not survive the firing. It is likely to have failed because no fuel was added after the three-hour mark. This meant the cooling of the kiln could start and the slow
fire had reduced to embers which may have caused the dome to cool too quickly, resulting in cracking from the uneven firing and instability of the dome (See Figure 12b). At 10:50 p.m. the kiln was left unattended because there were no visual flames or smoke indicating any danger to the surrounding environment. The decision to recreate a dome was reflected upon and this activity consumed the next couple days.
Part 3b: First Firing
After the pilot test firing that was described above, a new dome was created. This dome was made out of stoneware that was purchased at a local pottery shop and was the same quality as the small version of the scored basin. The idea was that by creating this temporary dome out of clay that was already processed and wedged, then it may work. The construction of this took approximately four and a half hours using the coil and slab technique. This temporary dome was left to slowly dry over the duration of several days until the first firing took place. However, the dome did not survive the drying process due to the uneven hardening of the clay which resulted in cracking.
So the final lid was to use one from an electric kiln, the temperatures required could be withstood but the drawback was it was no longer a dome top. This may, therefore, have altered certain aspects of this Minoan kiln, but in order for it to fire the pots, a lid had to be put on the kiln. The ceramic vessels were then put inside the kiln before the lid went on and the preheating began (See Figure 13).
The firing process took place on a day of warm weather, so that there would be no chance of rain affecting the kiln. For a total of twelve hours, the kiln went through various temperatures and used a total of 33.11kg of fuel. The fuel type ranged from small to large pieces of birch, pear, oak, pine, and hydrangea wood. Similar wood types were indicated at another Minoan site, Prinatikos Pyrgos, with the addition of olive and juniper (Day and Kobik, 2019, p.70). According to Soles, et al. (2003, p.83), a temperature of 600°C/1200°F was required. The kiln was successful in reaching this temperature and while recording it had actually reached 1500°F which was maintained for the last hours of the firing.
After those last hours, the kiln was completely closed after a final stoking. Covering up the kiln took approximately fifty minutes and involved the application of slip from the local clay and newspaper. This was a very important step that was needed in order to cover all the holes and any cracks that developed throughout the long firing process. The kiln was left to cool down very slowly so that none of the ceramic vessels would be damaged.
Part 3c: Second Firing
The first firing indicated that the vessels did not properly reach the temperature needed that would change the clay into a non-porous vessel. A second firing was, therefore, necessary, the difference being that this firing began during the night and went for a longer period. The recordings were more focused on the temperatures coming from inside the kiln, the quantity of wood and the time it took to reach certain temperatures. There were shorter stoking times (beginning with 10 minute intervals and then changed to 5 minute intervals in order to get the temperature higher ), so that the fire would be continuously fed but this may have affected the temperatures rising due to the doorway opening all the time causing the fuel to cool and fluctuate. The second firing lasted a total of fifteen hours, with approximately 36.27kg of fuel (the same type of wood as before) and the ending temperature was around 1500 °F (See Graphs 1 and 2).
Part 3d: The Results of the Firing
Overall the kiln was used for three firings. The pilot test was successful in the sense that it did dry the dome that was created specifically for it, but ultimately it was not successful. (See Figures 14a and b). The first firing was unsuccessful in reaching the temperature that the large-scale version of the scored basin needed. This commercial clay was supposed to be fired at Cone 6 (2200°F) and this temperature was not reached in the kiln. The third firing was unsuccessful in that one ceramic vessel that did get fired in both processes was the red clay version of the scored basin, but sadly it broke somewhere during the firing. This may have been due to the vessel not being entirely dry and luckily it did not damage the other vessels or the kiln itself. The large-scale version did not reach the 2200°F, and this changed the outcomes of performing the portion of the function of this experiment. The success of the experiment, however, was that the kiln did withstand the temperatures that were found to be evident on Mochlos.
Discussion/Conclusion
In the end, the experiment was not a successful one in the aspect of interpreting the functions of the scored basin. This was due to the firing of the kiln being unsuccessful in changing the clay into a workable ceramic vessel. Data and work put into all the experiments can lead one to suspect some functions. These vessels were large and required a lot of work, so their use would need to have a purpose and may have been stationary. Although when researching this vessel, many of them had spouts and handles (Barnard, et al., 2003, p.57) which would possibly suggest that they were only moved slightly and may have been involved with pouring activities.
Another element to consider is the effort it would have taken to construct a kiln big enough to fire these vessels successfully. With regards to the construction of the kiln, upon the experimentation, the dome presented a challenge. For the Late Minoan period, there is little to no evidence of the dome left when excavated, so suggestions are always made by researchers based on the architecture that is preserved (Betancourt, 1987, pp.117-119). Although this experiment did not go as planned, there is still useful data on time frames and necessary steps required to achieve success.
Justifications and Limitations
A tremendous setback in this experiment was the pandemic which limited the schedule and location, and the experimentat was only executed after quarantine. The sand and the clay used for the pilot tests of the scored basins were purchased and the options were severely limited by having to choose local shops that were open during the pandemic.
Timing was a huge limitation throughout this entire experiment with the construction of the kiln having the biggest impact. Unfortunately, due to the basin not reaching temperature, this prevented the experiment from completing the functions portion. The context of the function remains in this paper so that the reader can get some insight into what the plausible function may have been for these large vessels.
Future Research
This experiment provided some interesting views; however, the goal was not met so therefore there are some experiments that will be continued in the near future. For example, the scored basin function experiment was not able to be completed so there is still hope of running this experiment. In order to do this, the large-scale version of the Mochlos IB scored basin will have to be fired once again.
Through the progression and results of this experiment, certain perspectives were brought to light and have led to various ideas on future experimental avenues. Therefore, presented below are some additional ideas for future experiments that may be evaluated in due time.
- Scored basins are rarely an interest of study for pottery specialists. Therefore, research should be dedicated to a variety of different fragmentary scored basins with regards to residue analysis. Permission and funding would have to be available for the researcher in order for this to be completed. Unfortunately going through the research for the scored basins, there has not been any residue analysis done for the Mochlos project. So, it would be excellent to work with the director in order to achieve this goal.
- A re-evaluation in the kiln construction would be another avenue to go down. Instead of using the industrialized version of bricks, it would be ideal to dedicate more time to the production of more mudbricks and processing of more clay. This would probably alter the dimensions of the kiln that was originally used for this experiment. Another idea would be to have the kiln made completely out of local red clay using the coiling method. This would definitely take more than a two-month time-span and more than likely will result in more pounds of clay than the previous experiment.
- More evaluation should be made on the time periods of the Bronze Age on Crete. It would be interesting to look into various scored basins from different time periods to see if there were any changes in construction. The evolution of pottery on Crete is very complex and involves a lot of analysis. Therefore, by involving the Mochlos project with this idea, further examinations can be made of these simplistic ceramic vessels. However, this needs to be completed under supervision and with permission by the director as well as the government of Greece. The only way to analyze these ceramic vessels is to examine the published as well as the unpublished material.
Acknowledgments
I would like to start by thanking Dr. Linda Hurcombe, who inspired me to apply to the university. Thank you for your guidance, advice, discussions, dedication, and unbelievable faith in me. I appreciate your patience with my writing skills. My family has been a huge part of this degree. A special dedication goes to my mother, “The Firemaster”, without her wisdom and advice, there would never be an interest in pottery as much as I have now. All of this work, however, would have not been possible if I did not become a part of a team for the Mochlos Project. Dr. Jeffrey Soles took a chance on me five years ago to join the team as a volunteer and I have not stopped since. Through the guidance of Mr. Luke Kaiser, Ms. Angela Ratigan, and Dr. Giorgos Doudalis, I was able to learn so much about Archaeology and kickstart my passion for Minoan pottery. I sincerely thank each of you for allowing me to continue working for the project.
Keywords
Country
- Greece
Bibliography
Barnard, K., Brogan, T., Day, P., Joyner, L., Nicgorski, A., Nodarou, E., Relaki, M., Soles, M.E., Soles, J. and Davaras, C., 2003. Mochlos IB: Period III. Neopalatial Settlement on the Coast: TheArtisans' Quarter and the Farmhouse at Chalinomouri. The Neopalatial Pottery. INSTAP Academic Press, [Online] Available at: < http://www.jstor.org/stable/j.ctt3fgwd4 > [Accessed 16 June, 2020].
Betancourt, P. P., 1987. The History of Minoan Pottery. William Street, Princeton, New Jersey: Princeton University Press.
Blackman, M.J., 1992. The effect of human size sorting on the mineralogy and chemistry of ceramic clays. In: H. Neff, ed. Chemical Characterization of Ceramic Paste (Monographs in World Archaeology, no. 7). Madison: Prehistory Press. pp.113-124.
Bryant, G.F., 1977. Experimental Kiln Firings at Barton-on-Humber, S. Humberside 1971. Medieval Archaeology, 21(1), pp.106-123.
Casson, M., 1977. The Craft of the Potter: A Practical Guide to Making Pottery. British Broadcasting Corp.
Day, J. and Kobik, M., 2019. Reconstructing a Bronze Age Kiln from Priniatikos Pyrgos,Crete. In: C. Souyoudzoglou-Haywood and A. O’Sullivan, eds. Experimental Archaeology: Making, Understanding, Story-Telling. Summertown, Oxford: Archaeopress, pp.63–72. [Online] Available at: < www.jstor.org/stable/j.ctvpmw4g8.11 > [Accessed 15 February, 2020].
Emery, V., 2009. Mud-brick. UCLA Encyclopedia of Egyptology, 1 (1), [Online] Available at: < https://escholarship.org/uc/item/7v84d6rh > [Accessed 16 March, 2020].
Hasaki, E. and Raptis, K. T., 2016. Roman and Byzantine Ceramic Kilns in Greece (1st-15th c. CE): Continuities and Changes in Kiln Typology and Spatial Organization of Production. In: N. Cucuzza, B.M. Giannattasio and S. Pallecchi, eds. Archeologia delle produzioni ceramiche nel mondo anticoSpazi, prodotti, strumenti e tecniche Atti del convegno(Genova, 1-2 dicembre 2014). Ariccia: Aracne editrice. pp.213-233.
Hemingway, S., 2012. Art of the Aegean Bronze Age. The Metropolitan Museum of Art Bulletin, 69(4), pp.4-48, [Online] Available at: < http://www.jstor.org/stable/23223028 > [Accessed 10 July, 2020].
Jeffra, C.D., 2015. Experimental approaches to archaeological ceramics: unifying disparate methodologies with the chaîne opératoire. Archaeological and Anthropological Sciences, 7(1), pp.141-149. doi: 10.1007/s12520-014-0177-4
Knappett, C., 1999. Tradition and Innovation in Pottery Forming Technology: Wheel-Throwing at Middle Minoan Knossos. The Annual of the British School at Athens, (94), pp.101-129. [Online] Available at: < http://www.jstor.org/stable/30103454 > [Accessed 1 June 1, 2020].
Knappett, C. and Cunningham, T., 2003. Three Neopalatial Deposits from Palaikastro, East Crete. The Annual of the British School at Athens, (98), pp.107-187, [Online] Available at: < http://www.jstor.org/stable/30073205 > [Accessed 18 June, 2020].
Luce, J.V. and Bolton, K., 1976. Thera and the Devastation of Minoan Crete: A New interpretation of the Evidence. American Journal of Archaeology [e-journal] 80(1), pp.9-18. doi:10.2307/502934.
Moorey, C., 2019. A History of Crete. London: Haus Publishing, [Online] Available at: < www.jstor.org/stable/j.ctvjdzcsx.8 > [Accessed 10 January, 2020].
Nodarou, E., Frederick, C. and Hein, A., 2008. Another (mud)brick in the wall: scientific analysis of Bronze Age earthen construction materials from East Crete. Journal of Archaeological Science 35, pp.2997–3015. doi: 10.1016/j.jas.2008.06.014
Orton, C., Tylers, P. and Vince, A., 1993. Pottery in Archaeology. Cambridge: Press Syndicate of the University of Cambridge.
Popham, M., 1970. Late Minoan Chronology. American Journal of Archaeology, [e-journal] 74(3), pp.226-228. doi:10.2307/503097.
Rice, P.M., 1987. Pottery Analysis. Chicago: The University of Chicago Press.
Richter, G.M.A., 1912. Cretan Pottery. The Metropolitan Museum of Art Bulletin, [e-journal] 7(2), pp.28-35. doi:10.2307/3252760 [Accessed 17 March, 2020].
Shaw, J.W., Day, P.M., Van de Moortel, A. and Kilikoglou, V., 2001. A LM IA ceramic kiln in south-central Crete: function and pottery production, Hesperia, 30. Lisse: American School of Classical Studies at Athenes.
Soles, J., Brogan, T., Davaras, C., Frederick, C., Mylona, D., Nicgorski, A., Reese, D., Sarpaki, A., Schoch, W., Smith,R.A. and Walker, C., 2003. Mochlos IA: Period III. Neopalatial Settlement on the Coast: The Artisans' Quarter and the Farmhouse at Chalinomouri. The Sites. INSTAP Academic Press. [Online] Available at: < http://www.jstor.org/stable/j.ctt3fgwcn > [Accessed 16 June, 2020].