The content is published under a Creative Commons Attribution Non-Commercial 4.0 License.
Reviewed Article:
Copper Smelting Could Have Been Discovered in Connection with the Massive Production of Lime Plaster in the Near East During the Pre-Pottery Neolithic B, which is Much Earlier than Previously Believed
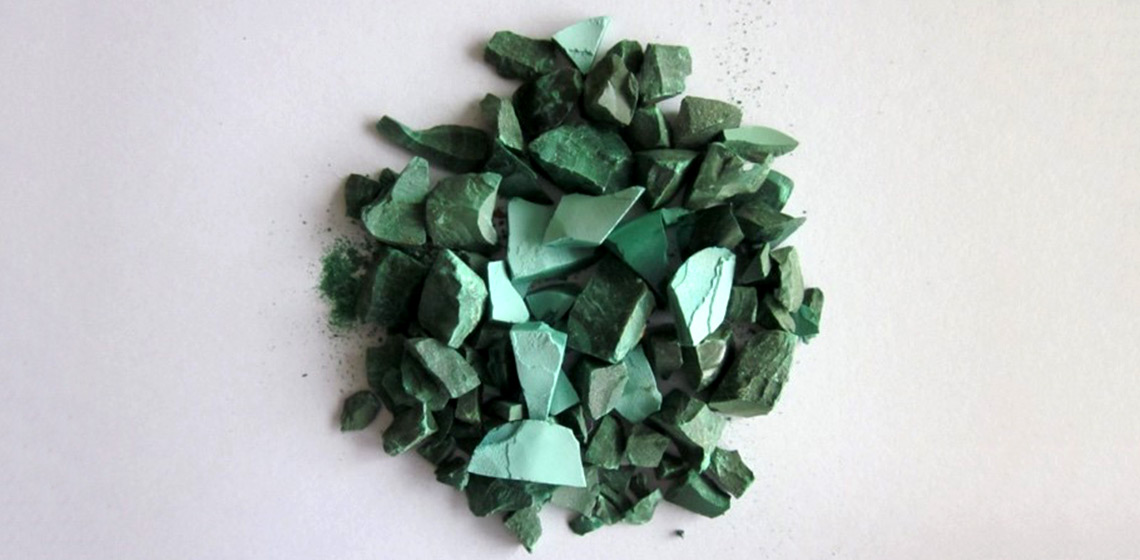
A common theory is that copper smelting first appeared in the Near East in close connection with the early pottery industry. However, copper smelting may well have been discovered many times in history and at many places. Our hypothesis is that copper smelting could have been discovered when the copper-bearing mineral malachite, accidentally or intentionally, was present in lime-burning kilns. To test our hypotheses, a series of test burnings during which malachite, limestone and solid carbon fuel were present in the same furnace have been carried out. The weight and copper content before and after burning was measured. The weight loss was the result of the evaporation of carbon-dioxide in the limestone and the evaporation of carbon-dioxide as well as water in the malachite. The weight loss and final copper content give a clear picture of the effectiveness of the burning procedure. The mechanism behind the successful smelting was most probably the reaction between the carbon in the solid fuel and the carbon-dioxide released from malachite and limestone when they were heated up. This reaction created the carbon oxide necessary for the reduction of “copper-oxides” to copper. The best conditions for discovering this conversion are likely to have existed in areas with an extensive production of lime plaster in combination with an abundance of native copper as well as malachite. The Anatolian mountains was one of the areas where these conditions were at hand. Massive lime production first began in this region in the PPNB around 10,800 BP. We, therefore, propose that copper smelting could have been discovered at this time in Anatolia.
Introduction and methods
Converting malachite to copper may have been the earliest example of copper smelting in a solid-state process. This process requires a reducing atmosphere (Henderson, 2000, p.220) and a temperature of at least 700‑800ºC (Hauptmann, 2007, p.219). The first technology to match these requirements was lime burning, which was carried out on a large scale, in the Near East, during the Pre-Pottery Neolithic B (Ivanova, 2013, p.39). The PPNB began about 10400 cal BP in the Levant and Pottery Neolithic (PN) about 8300 cal BP in the same area. These are average ages based on data from Borell, Junno and Barcelo(2015, pp.1-2). Smelting is the process when an ore is converted to metal in a liquid or a solid state, whereas melting simply means heating up the material until it reaches the liquid state.
Two frequently-quoted hypotheses suggest that the discovery of copper smelting was closely linked to the early pottery industry in the Near East (Lamber,t 1997, p.173; Tylecote, 2002, p.7). In essence, the hypotheses are: (1) clay pots that were painted with ground malachite were fired in kilns with reducing atmospheres. The change of colours from green to a colour similar to native copper could then have been observed, and (2) when native copper, which contained high amounts of oxidized copper, was melted in ceramic pots, the output of copper appeared to have exceeded the input. Someone could then have understood that the material looking quite different from copper must have contained that metal. The focus of this article is to demonstrate experimentally that copper could have been extracted from malachite when, accidentally or intentionally, placed in kilns designed and operated for lime burning. This, in turn, raises the possibility that copper smelting could have been discovered in the Near East, already during the PPNB, which is earlier than the advent of pottery production.
Lime manufacturing
The manufacturing of lime starts with heating limestone in a kiln. The purpose is to decompose the calcium carbonate (CaCO3), which is the main component of limestone, and to produce quicklime (calcium oxide, CaO). The next step is the slaking of quicklime, by adding water, in order to produce slaked lime (calcium hydroxide, Ca (OH)2), which is the binding component in lime. Finally, tempers such as sand, ground limestone, or other inert material are mixed with the slaked lime. Adding temper has two major advantages, namely that it reduces the amount of work required to produce lime plasters and lime mortars by increasing the volume and that it makes them stronger and more durable (Boynton, 1980, pp.159-89; Lambert, 1997, pp.30-1; Goren et al., 1991, p.137; Kingery et al., 1988, p.221). The material hardens when the slaked lime and the carbon dioxide in the atmosphere react to form calcite (Boynton, 1980; Lamber,t 1997, p.30).
The chemical reactions for the three steps are as follows (Lambert, 1997, p.30):
Burning/calcination: CaCO3 + Heat = CaO + CO2
Slaking: CaO + H2O = Ca (OH)2 + Heat
Hardening: Ca (OH)2 + CO2 = CaCO3 + H2O
Lime burning requires a temperature of about 800-900° C (Gourdin and Kingery, 1975, p.134; Weiner, 2010, p.186; Frierman, 1971, p.213) depending on the size and characteristics of the raw materials and the concentration of carbon dioxide in the kiln (Boynton, 1980, pp.159-91). The first equation indicates that a high concentration of carbon dioxide in a kiln could suppress the conversion rate. Therefore, some ventilation should be useful, not only for boosting the temperature but also to facilitate the disintegration of the calcium carbonate (Boynton, 1980, p.162). A temperature of about 750° C is attainable in a small campfire ventilated by a moderate breeze (Frierman, 1971, p.213) but attaining 900° C requires lots of fuel, a kiln and some ventilation.
An important aspect of ventilation is that it can boost the temperature as well as cool the fire (like blowing out a candle). Therefore, it is not possible to identify an ideal wind speed suitable for all lime-burning kilns. A fire can, to some extent, create its own winds, as the exhaust gases that leave the kiln are replaced with fresh air being sucked into the kiln. The cooling of the fires is caused by the high amount of inert nitrogen gas in the atmosphere. Diluting carbon dioxide, with an airflow in terms of wind, is obviously more effective on the outside of a stone than inside of it. A temperature of about 750° C could be sufficient to heat a thin layer on the outside of a stone, whereas heating it right through requires temperatures in the order of 900° C. The larger and denser the stone is, the higher is the required temperature, and the longer is the necessary burning time for complete calcination (Boynton, 1980, pp.161 and 166). The most efficient way to produce quicklime with the technology available during the Neolithic would, therefore, have been heating small pieces (a couple of centimeters) of porous limestone in a kiln or a hearth. With suitable raw materials and sufficiently good heating conditions, the calcination could have been completed in one day, but with less favorable conditions (such as low temperature or insufficient airflow for removing the carbon-dioxide), it could have required several days (Kingery et al., 1988, p.221; Weiner, 2010, p.186).
PPNB was a period of intense production of lime plaster in the Near East, by far exceeding both the earlier and following periods. According to Dr. Joanne Clarke at the University of East Anglia (pers comm), the reason can be found in the rapid population increase in the villages. The reason for this was, in turn, that many more children survived when people had settled down than during the Hunter-Gatherer periods. And, also according to Clarke, when villages grew, common myths and rituals probably helped to ease tensions among the villagers and increased their feeling of community. In order to make the myths less abstract, some kinds of pictures were needed. Therefore suitable surfaces for paintings were also needed. Lime plaster seems to be the obvious choice since it is white, can be spread on the floors and walls, and be smoothed.
Metallurgical and geological aspects
Copper was one of the first metals to be utilized by mankind. One possible reason is that it can occur as a pure metal, known as native copper, as seen in Figure 1. This metal can, when it is hot, be pounded and stretched without manipulating its chemistry. Native copper was mainly used for producing small objects, like needles and sheets. (Craddock, 2001, p.153). The formation of native copper is the result of different kinds of weathering processes in copper-bearing deposits (Goody 2012, p.8; Golding and Golding 2017, pp.21-24). This is also the case with, for instance: cuprite (Cu2O), melaconite (CuO), and malachite (Cu2(OH)2CO3). Copper could easily have been smelted, in a solid state, from these ores (frequently referred to as “oxide-ores”) in simple hearths or furnaces with reducing (oxygen-starved) atmospheres.
The extraction of copper, from the minerals mentioned above, can be illustrated by the following equations (4 ) – ( 6 ):
Cu2(OH)2CO3 + Heat = 2 CuO + H2O + CO2 ( 4 )
4 CuO + C + Heat = 2 Cu2O + CO2 ( 5 )
2 Cu2O + C + Heat = 4 Cu +CO2 ( 6 )
As long as “oxide-ores” were ubiquitous in the Near East, copper smelting was probably a fairly simple enterprise. A small pit in the ground, filled with charcoal and malachite and covered with a turf lid could have been sufficient to produce copper. The combustion air, necessary for attaining sufficiently high temperatures, as well as for creating a reducing CO-rich atmosphere, could have been supplied by means of blowpipes, ventilated by human breath, or bellows (Hauptmann, 2007: 219-220; Weeks, 2012: 300).
However, when “oxide-ores” became scarce, the metallurgists had to rely upon sulphide-ores, which are more abundant but also much more difficult to smelt. Common sulphide minerals are chalcocite (Cu2S), covellite (CuS), chalcopyrite (CuFeS2), and bornite (Cu5FeS4) (O'Brian, 2015: 2). Chalcopyrite is the most important copper-bearing mineral today (Allaby and Allaby, 1999, p.93). The reason is that the mineable resources of that mineral are, by far, the most abundant.
Figure 2 is a schematic representation of a copper deposit, in which weathering and alteration of minerals are taking place. The chemical conditions above the water table are oxidizing and acidic, whereas the conditions below the water table are reducing and often slightly alkaline. The acidity is most pronounced in the uppermost part of the oxidizing zone and least just above the water table. These differences have a profound influence on the formation of minerals. They control which minerals will be formed and where each mineral will form. Let us imagine an ore body, mainly consisting of chalcopyrite (CuFeS2), with access to the open air. Chalcopyrite is usually accompanied by pyrite (FeS2). When rainwater is seeping down, it can bring oxygen, carbon dioxide, and carbonic acid to the ore body. The two last compounds partially derive from decomposing plants above the ore body. Pyrite can, together with oxygen and water, produce sulphuric acid, which, in combination with the carbonic acid, can make the water sufficiently acidic to destabilize the chalcopyrite, thereby liberating copper-, iron-, and sulphate ions (Robb, 2005, pp.238-239; Golding and Golding, 2017, pp.21-24). The disintegration of chalcopyrite can be represented by the equation below (Loberg, 1993, p.277):
CuFeS2 + 4 O2 = Cu2+ + Fe2+ + 2 SO42-
The iron-ions can, together with oxygen and water, form the mineral goethite (FeO (OH)), which is virtually insoluble and therefore remains in the upper part of the ore body. There the goethite can, together with other minerals, form a durable “cap” usually referred to as “gossan”. Unlike the iron-ions, the copper ions, the carbonate ions and the sulphate ions can percolate and form copper-rich minerals above the water table (“oxide-ores”) as well as below it (“sulphide ores”). Malachite (See Figure 3) has the chemical formula Cu2(OH)2CO3, and its building blocks are: Cu2+, OH- and CO32- (Robb, 2005, p.41): The hydroxide ions (OH-) derive from the water and the carbonate ions (CO32-) from carbonic acid and calcium carbonate (CaCO3) in neighbouring limestone rocks. In acidic environments, these ions cannot react to form malachite. In alkaline environments, e.g. in the vicinity of limestone rocks, malachite can be formed. Therefore, malachite is often found together with limestone. The area with the best conditions for the formation of malachite is the oxidized zone, just above the water table where the lowest acidic level in that zone can be found. This is also the case when it comes to the formation of native copper, which can be illustrated by the equation below (Killick, 2014: 19):
2Cu2S + 8Fe3+ + 12SO42- = 2Cu + Cu2O + 8Fe2+12 H+ + 14SO42-
The close chemical connection between malachite and limestone makes it likely that chunks containing malachite occasionally, or even frequently, were present in lime-burning kilns.
Test burnings
Lime burning in Neolithic pit-kilns was experimentally modelled by using a vertical tubular reactor of stainless steel with an inner diameter of 2.5 cm placed in a tubular electric furnace with a heated length of 60 cm. The samples were placed in separated layers on a fine metallic grid. The facility is a reasonable representation of a kiln as it allows the thermal treatment of materials at controlled temperatures and a gaseous atmosphere. The experimental facility is illustrated in Figure 4. Figures 5-7 show the crushed raw materials utilised for the experiments: Figure 5 shows limestone, Figure 6 shows carbonaceous fuel, and Figure 7 shows malachite.
The numbers represent the positioning of limestone (1), carbonaceous fuel (2), and malachite (3). Figure 8 shows a small lump of newly produced copper.
Three different materials were used for the malachite transformation: limestone, solid carbon fuel and malachite. The malachite used had a copper content of 57.7%. All materials were prepared and sieved to a particle size of 3-5 mm. In each experiment, the furnace was loaded with 45 g of limestone (position 1), 10 g of charcoal (position 2), and 9.5 g of malachite (position 3). The samples used in the experiment were pre-dried at 105Âş C in a drying chamber. After loading the steel pipe in the furnace, it was heated to the final temperatures: 800 and 850Âş C, followed by heat treatment at constant temperature for 2 hours. Thereafter, the furnace was allowed to cool in room temperature surrounding until reaching 40Âş C. The same experimental procedure was applied for both temperatures. A nitrogen gas flow rate of 25 ml/min was applied during the time of the experiments in order to transport the formed CO2 from limestone and malachite through the beds of charcoal and malachite in order to simulate the gas circulation from ventilation in the pit kiln. The experiments were designed in order to expose malachite to a reducing CO atmosphere formed when CO2 from limestone reacted with solid carbon in the charcoal according to the Boudouard reaction:
CO2 + C = 2CO
After the experiments, the samples were separated and scaled. Furthermore, the product from malachite was analysed for its copper content using ICP/MS.
The results from the experiment were analysed based on weight and sample compositions. For malachite transformation, the weight and Cu-content of the samples before and after treatment were compared on a molar basis to study the conversion reaction at different temperatures.
The conversion of limestone (CaCO3) into burnt lime (CaO) and thereby the amount of available CO2 for the Boudouard reaction was calculated on a molar basis using the mass of limestone before and after heat treatment. The molar weights used for the conversion of malachite and limestone are presented in Table 1.
Cu2(OH)2CO3 | 221.12 | H2O | 18.1 |
CuO | 79.54 | CO2 | 44.01 |
CaCO3 | 100.09 | O2 | 32.00 |
CaO | 56.08 |
Table 1. Relevant chemical compounds and their molecular weight (g/mol). Cu2(OH)2CO3 corresponds to malachite.
Malachite transformation
Figure 8 is a photograph of the product of malachite transformation in the kiln. The ICP/MS analytical results of malachite transformation during heat treatment are presented in Figure 9. Figure 9 and Table 2 present the mass of copper in the product over the mass of copper in the malachite (in white in the figure), as well as the concentration of copper in the product (in grey). The results show that malachite was transformed into copper at both temperatures without significant difference in the temperature range investigated. Based on the amount of copper in the malachite feed (mass basis), about 96-99 % was found in the derived products. The concentration of copper increased from 57.7 % (presented in the previous section) in malachite to almost pure copper in all cases. The results clearly show that the malachite can be reduced into copper when exposed to a reducing CO atmosphere. The temperatures investigated are in the same range as the temperatures in traditional lime production. Also, the gas atmosphere is similar. Therefore, these results indicate that this phenomenon could have occurred during lime production.
Figure 9 presents the results of the malachite conversion into copper and is presented as the weight of solid product over the copper content in malachite (in white) as well as the Cu content in the solid product (in grey, wt %). Absolute numbers of results are presented in Table 2.
Temperature (°C) | Repetition | Weight sample (g) | Weight solid product (g) | Cu in product (wt%) |
800 | 1 | 9.6 | 5.4 | 98.5 |
800 | 2 | 9.7 | 5.4 | 95.5 |
850 | 1 | 9.5 | 5.3 | 96.6 |
850 | 2 | 9.3 | 5.3 | 99.6 |
Table 2: Results of malachite treatment in terms of temperature, the weight of feed and solid product, as well as Cu content in the solid product.
Limestone transformation
The results of limestone conversion at the temperatures investigated are presented below in Figure 10 (mass basis on the conversion of CaCO3 into CaO). The results show that limestone conversion occurred in the experiments when heated to 800 or 850Âş C. The results show that the extent of conversion of CaCO3 to CaO increased when treating the material at 850Âş C compared to 800Âş C. CO2 was produced from the thermal treatment in the experiments, which further indicates the role of the Boudouard equation to generate a reducing atmosphere for the formation of pure copper.
Discussion
We have experimentally demonstrated that copper can be produced in kilns operating under conditions that can decompose limestone to form lime. This raises the intriguing possibility that the earliest produced copper occurred when malachite was deliberately or inadvertently heated in a lime burning kiln. For this to have occurred, lime would need to have been produced in a region where malachite is also present. Lime was first produced in the Southern Levant in the Natufian Period starting about 15,000 BP. However, it was only in the pre-pottery Neolithic (PPNB), starting about 10,800 BP, that lime was produced on a large scale both in the Levant and Anatolia. The sites where the remains of lime from the PPNB have been found are shown in Table 3 and Figure 11.
Native copper was probably fairly common in the Neolithic Near East (Tylecote, 200, p.1) and apparently more widespread in Anatolia than in the Levant, which is clearly demonstrated in Table 4. Hence it is likely that native copper was better known in Anatolia than in the Levant. One reason is that the Anatolian mountains host many more copper ore deposits than the Levant. The abundance of copper in that area is due (at least partially) to the collision between the African and Eurasian plates, which have pushed up huge amounts of minerals to the Anatolian surface (Yalçin, 2017, p.116). The four sites surrounded with red circles in Figure 11 are sites where traces of burnt lime as well as native copper have been found. In our opinion, they could all have potentially been the birthplace of metallurgy. Cayonu Tepesi appears to be the best candidate since it is the biggest and oldest lime-burning site discovered in Anatolia, dated to the 11th millennium cal BP (Yalçin, 2016, p.124). The site has also yielded lots of malachite as well as native copper (Craddock 2001, p.153; Demand 2011, p.23; Hauptmann, 2007, p.255; Weeks, 2012, pp.296-297). Finally, it is the only PPNB-site in which all these kinds of artefacts have been found.
Site | Period | Nr | Source |
Abu Gosh | PPNB | 1 | Kingery et al. 1988, 224-37 |
Ain Ghazal | PPNB | 2 | As above |
Asikli Huyuk | PPNB | 3 | As above |
Beidha | PPNB | 4 | As above |
Beisamun | PPNB | 5 | Goren and Goldberg 1991, 133-5 |
Byblos | PPNB | 6 | Kingery et al 1988, 224-37 |
Catal Huyuk | PPNB | 7 | As above |
Cayonu Tepesi | PPNB | 8 | As above |
Farah | PPNB | 9 | As above |
Hacilar | PPNB | 10 | Kingery et al 1988, 224-37 |
Hama | PPNB | 11 | Thuesen and Gwozdz 1982, 99 |
Hurbat Galil | PPNB | 12 | Goren and Goldberg 1991, 133-5 |
Jericho | PPNB | 13 | Kingery et al 1988, 224-37 |
Kfar HaHoresh | PPNB | 14 | Goring-Morris 2000, 109 |
Laboueh | PPNB | 15 | Kingery et al 1988, 224-37 |
Motza | PPNB | 16 | Khalaily et al 2007, 5 |
Munhata | PPNB | 17 | Wright 1985, 369 |
Musular | PPNB | 18 | Yalçin 2017, 124 |
Nahal Hemar | PPNB | 19 | Kingery et al 1988, 224-37 |
Nahal Oren | PPNB | 20 | As above |
Nesher- Ramla | PPNB | 21 | Toffolo et al 2017, 353 |
Ras Shamra | PPNB | 22 | Kingery et al 1988, 224–37 |
Shaqart Mazyad | PPNB | 23 | As above |
Suberde | PPNB | 24 | Yalçin 2017, 124 |
Tell Assouad | PPNB | 25 | Kingery et al 1988, 224-37 |
Tell Eli | PPNB | 26 | Yalçin 2017, 124 |
Tell Ramad | PPNB | 27 | Kingery et al 1988, 224-37 |
Tel Teo | PPNB | 28 | Goren and Goldberg 1991, 133-5 |
Yiftahel | PPNB | 29 | As above |
Table 3: Traces of lime plaster or burnt lime are reported to have been found in these PPNB sites.
Anatolia: 4 sites out of 6 | Levant: 1 site out of 23 |
Asikli Huyuk | Tell Ramad |
Catal Huyuk | |
Cayonu Tepesi | |
Hacilar |
Table 4: Lime burning sites in Anatolia and the Levant where native copper has also been found.
The best evidence for showing that copper was produced from malachite in simple lime kilns would be the presence of copper in such a kiln. However, despite the massive and widespread remains of lime plaster in many PPNB-settlements, only one lime kiln from the PPNB has, so far, been confirmed and thoroughly investigated. It was found in the Israeli site of Nesher Ramla and was located in a sinkhole. This could explain why it was not destroyed after such a long time. If a pit-kiln or another simple kiln, was located in the open air, the remains would probably have been destroyed or scattered by winds, floods, or strolling animals. A pit-kiln is just a hollow dug out in the ground and loaded with fuel and, e.g. limestone. Despite its simplicity lime burning in pit-kilns was common practice in the Near East as late as the end of the 19th century (Ronen, Bentur and Soroka 1991, pp.152-154).
Lime burning requires a temperature in the order of 800-900° C. As can be seen from Figure 12, high temperatures are conducive to high concentrations of carbon monoxide in the kilns. A temperature of that order would have created an atmosphere sufficiently reducing for the final transformation of malachite to copper in a Neolithic lime burning kiln.
Malachite and other green minerals were highly prized in the Near East, particularly in farming communities, during the Neolithic era. The similarities in colours between the minerals and the growing crops could be one reason for their attraction. Malachite stones could have been kept as amulets for good harvest etc. (Bar-Yosef Mayer and Porat, 2008, pp.8548-8550; Hauptmann, 2007, pp.255-256). Therefore, this mineral and other green stones were collected and traded over a vast area in the Near East. Hence it is likely that malachite was a well-known mineral there. Native copper and malachite were formed at about the same level in the ore deposits. When erosion reached that level, both minerals could have been unearthed, and people collecting malachite, could have collected native copper as well (Craddock, 2001, p.153). Knowledge of the character of both minerals could have helped the lime burners and potters to recognise the transformation of malachite to copper.
Conclusions and summary
- Lime burning was the first technology regularly operating at temperatures sufficient for converting malachite to copper.
- Lime burning was taking place on a large scale, in the Levant and Anatolia, during the PPNB.
- Malachite and limestone are frequently found in the same rock.
- Malachite and Native Copper appear to have been well known in the Near East during the Neolithic, particularly in Anatolia.
- Our experiments show that malachite could have been converted to copper and limestone to lime in the same kiln.
- Southern Anatolia appears to have been the area with the best conditions for discovering the conversion of malachite to copper.
The close geological connection between malachite and limestone makes it likely that limestone chunks containing malachite occasionally were present in lime kilns. This is particularly true in malachite rich areas like Anatolia. The massive production of lime during the PPNB makes it far from unlikely that it happened many times. The early lime burners apparently tried to avoid strong winds, making it likely that the CO-concentration in the kiln was not seriously diluted, and therefore sufficient for the final reduction to copper. Anatolia could have hosted the cradle of metallurgy (Yalçin 2016, pp.116-119). But what was its impetus? Discovering the conversion of malachite to copper in lime-burning pit-kilns during the PPNB could have been the spark that ignited the metallurgical fire.
Acknowledgements
The authors would like to thank the following persons for their help, inspiration and encouragement during our search for the advent of copper smelting: Dr. Claude Björk, Archaeologist, Stockholm Sweden, Prof Elisabetta Boaretto, The Weizmann Institute of Science Rehovot Israel. Prof Voicu Brabie, The Royal Institute of Technology Stockholm Sweden. Mr. Lars Bentell, metallurgist, formerly the Swedish Steele Producers' Association Stockholm Sweden. Dr. Joanne Clarke, archaeologist, University of East Anglia UK. Prof Hans-Peter Hermansson, formerly Technical University of Luleå Sweden. Mr Lars Jacobsson, Storfors Sweden. Mr. Rahul Puthucode, The Royal Institute of Technology, Stockholm, Sweden, Prof Pär Jönsson, The Royal Institute of Technology Stockholm Sweden. Prof Dag Noréus, Stockholm University Sweden. Prof Steve Weiner, The Weizmann Institute of Science Rehovot Israel.
Abbreviations
PPNB = Pre-Pottery Neolithic B
PN = Pottery Neolithic
cal = Calibrated age based on dendrological studies
BP = Before present=Before 1950
About Authors and their contribution:
Dr Henry Hammarström, formerly the Royal Institute of Technology Stockholm Sweden (KTH), Hammarström has been responsible for the descriptions of the experiments, and Ulf Fornhammar for the rest. The experiments were carried out by the two authors, in cooperation with KTH.
Keywords
Country
- Israel
- Lebanon
- Syria
- Turkey
Bibliography
Allaby, A. and Allaby, M., (Eds.). 1999. A dictionary of Earth Sciences. Oxford. Oxford University Press.
Bar-Yosef Mayer., D.E. and Porat, N., 2008. Green stone beads at the dawn of agriculture. Proceedings of the National Academy of Science PNAS, June 24, vol. 105, no. 25, p. 8548-8551 [online] available at < https://doi.org/10.1073/pnas.0709931105 >
Borell, F., Junno, A., & Barcelo, J.A., 2015. Synchronous Environmental and Cultural Change in the Emergence of Agricultural Economies 10000 Years Ago in the Levant, PloS One, vol. 10(2015), No. 8, p. 1-19 [online] available at < https://journals.plos.org/plosone/article?id=10.1371/journal.pone.0134810 > [Accessed 04 February 2022]
Boynton, R.S., 1980. Chemistry and Technology of Lime and Limestone. Second ed. New York Chichester Brisbane Toronto. John Wiley & Sons Inc.
Craddock, P. T., 2001. From hearth to furnace: Evidence for earliest metal smelting technologies in the eastern Mediterranean. Paléorient, vol 26/2. p. 151-165 [online] available at < https://www.jstor.org/stable/41496588 > [Accessed 04 February 2022]
Demand, N.H., 2011. The Mediterranean context of early Greek history. Chichester, West Sussex. Wiley-Blackwell.
Frierman, J.D., 1971. Lime burning as the precursor of fired ceramics. Israel Exploration Journal vol 21, 212-216 [online] available at < https://www.jstor.org/stable/27925291 > [Accessed 04 Febr 2022]
Golding, B., Golding, S. D., 2017. Metals, Energy and Sustainability-The Story of Doctor Copper and King Coal. Cham, Switzerland. Springer.
Goody, J., 2012. Metals, Culture and Capitalism: An Essay on the Origins of the Modern World. Cambridge, Cambridge University Press.
Goren, Y., & Goldberg, P., 1991. Petrographic thin sections and the development of Neolithic plaster production in northern Israel. Journal of Field Archaeoogly. Vol 18, No (1), p. 131-140 [online] available at < https://doi.org/10.1179/009346991791548735 >
Goring-Morris, N., 2000. The quick and the dead. The social context of Aceramic Neolithic mortuary practices as seen from Kfar HaHoresh, in I. Kuijt (ed), Life in Neolithic Farming Communities. Social Organization, Identity, ad Differentiation. New York. Kluwer Academic/Plenum Publishers, p. 103-136.
Gourdin, W.H., & Kingery, W.D., 1975. The beginnings of pyrotechnology: Neolithic and Egyptian lime plaster. Journal of Field Archaeology. 2, 133-150 [online] available at < https://doi.org/10.1179/009346975791491277 >
Hauptmann, A., 2007. The archaeometallurgy of copper. Evidence from Faynan, Jordan. Berlin Heidelberg. Springer.
Henderson, J., 2000. The science and archaeology of materials: An investigation of inorganic materials. Abingdon, Oxon. Routledge.
Ivanova, M., 2013. The Black Sea and the early civilizations of Europe, the Near East and Asia. Cambridge, Cambridge University Press.
Khalaily, H., Bar-Yosef, O., Barzilai, O., Boaretto, E., Bocquentin, F., Eirikh-Rose, A., Greenhut, Z., Goring-Morris, A.N., Le Dosseur, G., Marder, O., Sapir-Hen, L., and Yisaq, H ., 2007. Excavation at Motza in the Judean Hills and the Early Pre-Pottery Neolithic B in the Southern Levant, Paléorient, vol. 33, No. 2 [online] available at < https://www.jstor.org/stable/41496809 > [Accessed 04 February 2022]
Kingery, W.D., Vandiver, P.B. and Pricket, M., 1988. The beginnings of pyrotechnology, part II: production and use of lime and gypsum plaster in the pre-pottery Neolithic near east. Journal of Field Archaeology. 15, 219-244. Taylor & Frances, Ltd. [online] available at < https://doi.org/10.1179/009346988791974501 >
Killick, D., 2014. From Ores to Metals. Chapter 2 in: B.W. Roberts and C.P. Thornton (eds.) Archaeometallurgy in Global Perspective. Methods and Synthesis. New York. Springer.
Lambert, J.B., 1997. Traces of the Past. Unravelling the Secrets of Archaeology Through Chemistry. Cambridge, Massachusetts. Perseus Publishing.
Loberg, B., 1993. Geologi Material, processer och Sveriges berggrund (bedrock) 5th edition. BorĂĄs. Norstedts.
O'Brien, W., 2015. Prehistoric Copper Mining in Europe 5500-500 BC. Oxford, Oxford University Press.
Robb, L., 2005. Introduction to ore-forming processes. Oxford. Blackwell Publishing.
Ronen, A., Bentur, A., & Soroka., I., 1991. A plastered floor from the Neolithic Village, Yiftahel (Israel). Paléorient 17 (2), 149-155 . [online] available at < https://www.jstor.org/stable/41492462 > [Accessed 04 February 2022]
Theusen, L. A., Gwozdz, R., 1982. Lime plaster in Neolithic Hama, Syria. A preliminary report. Paléorient, vol. 8, No. 2, p. 99-103.
Toffolo, M. B., Ullman, M., Caracuta, V., Weiner, S., & Boaretto., E., 2017. A 10,400-year-old sunken lime kiln from the Early Pre-Pottery Neolithic B at the Nesher-Ramla quarry (el Khirbe), Israel. Journal of Archaeological Science: Reports 14, 353-364 [online] available at < https://doi.org/10.1016/j.jasrep.2017.06.014 >
Tylecote, R. F., 2002. A History of Metallurgy. 2nd Edition. London. Maney for the institute of materials.
Weeks, L., 2012. Metallurgy. Chapter 16 in: Potts, D.T. (ed.) A companion to the archaeology of the ancient near east, volume I. Chichester, West Sussex. Wiley-Blackwell.
Weiner, S., 2010. Microarchaeology. Beyond the Visible Archaeological Record. Cambridge, Cambridge University Press.
Wright, G.R.H., 1985. Ancient Building in South Syria and Palestine I. Brill Archive.
Yalçin, Ü., 2016. The beginnings of metal use in West Asia. Chapter 8 in: A. Tsuneki, S. Yamada, and K. Hisada, 2017 (eds) Ancient West Asian civilization. Geoenvironment and society in the pre-islamic Middle East. Singapore. Springer.