The content is published under a Creative Commons Attribution Non-Commercial 4.0 License.
Reviewed Article:
The Little Bowl That Could! Experimental Iron Smelting in a Bowl Furnace
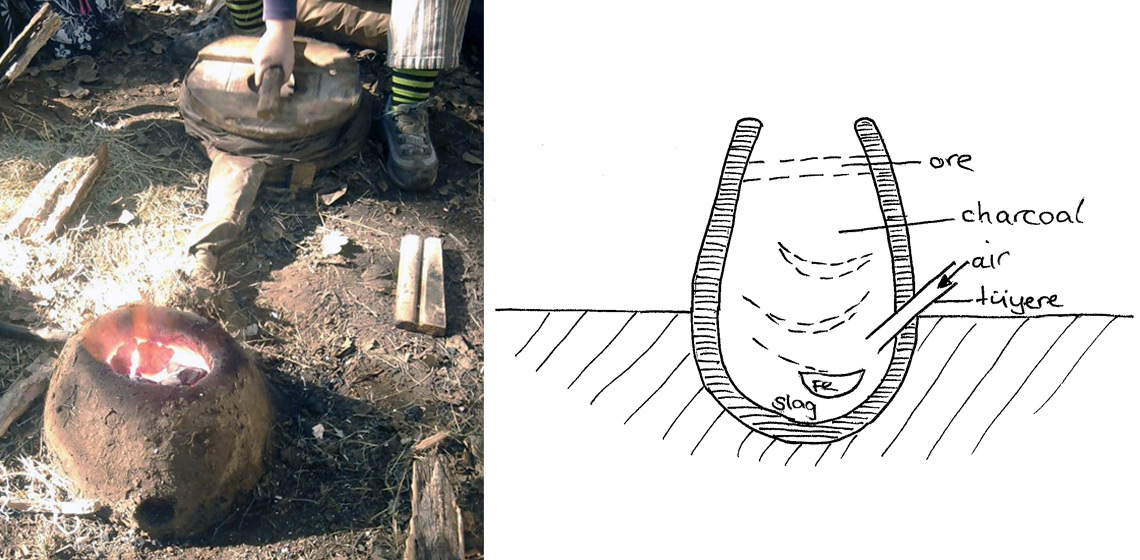
The bowl furnace has been a somewhat neglected topic in the early history of iron making, often overshadowed in experimental work by the shaft furnace. This assessment attempts to re-evaluate the position of the bowl furnace in early iron-making - firstly by looking at how it is regarded in scholarly literature, and secondly, through an experimental reconstruction programme.
Introduction
The bowl furnace is a somewhat enigmatic feature within the early history of iron-making. Site formation processes and preservation can mean that the material evidence found for shaft furnaces sometimes reflects a truncated design, and therefore may resemble what is thought to be a bowl furnace. The bowl furnace design was rejected by many in the 1970/80’s (Cleere, 1972; 1981; Coughlan, 1977), most likely due to the design not fitting within the expected framework of how furnace technology was thought to evolve through the Bronze age and into the Iron Age. Work by Dungworth has sought to revive the idea of the bowl furnace (Dungworth, 2011; 2013) and has supported this with a series of ongoing experimental reconstructions coupled with archaeometallurgical characterisation of the materials produced. The work reported here seeks to add further experimental data to the ongoing debate concerning the use and identification of bowl furnaces in the archaeological record.
Principles of early iron smelting – bloomery process
The fundamental principle of iron smelting is the reduction of the metal oxide with carbon dioxide, which is provided by partial combustion of the fuel, in this case charcoal, with air from the tuyère (Tylecote, 1986). It is necessary for the air from the tuyère to pass through a sufficient amount of charcoal before there is enough carbon monoxide to reduce the ore (Tylecote, 1986). Reduction of the ore needs to be as controlled as possible to provide the most efficient operation. The ore must be maintained in a reduced environment long enough, to enable the iron ore to reduce and enable the slag to separate and metallic iron to form (Markewitz, 2012). The area of the furnace where this takes place, is often referred to as a combustion zone and is achieved by heating the charcoal and iron ore together. Carbon monoxide is produced as the charcoal is heated and then the enables the iron ore to react and then reduce with the carbon monoxide, converting the ore into metallic iron (Friede and Steel, 1977). In a shaft furnace, different zones are considered to be present, as the material passes through the furnace and different temperatures are achieved (Mihok, 1993, p. 230), however in a bowl furnace, there is less space and less movement of the material, which could result in less regions of variation. It is considered that reduction starts at c.750°C and at 900°C the carbon becomes a solution. The ‘purer’ iron produced will form as a spongy bloom. The impurities from the ore are separated from the iron and becomes liquid and runs to the bottom of the furnace (Markewitz, 2012). As a bowl hearth is smaller than a bloomer furnace, the smaller space can be problematic, as if the ore is subjected to oxygen before it has turned to metallic iron, it can stop the process from finishing. If the pure iron is able to settle into a space within the bowl hearth where it is protected from the oxygen, it will be able to form into a bloom. However, the lack of space can see the bloom and slag combine, which is problematic.
Determining typologies: what is a bowl furnace?
Variously, throughout the 1950’s to the 1980’s, many different classifications of early furnaces were attempted. In these, the bowl furnace appears in a range of different forms, from rudimentary holes in the ground, to what are essentially small shaft furnaces. The size and covering of these furnaces are varied, but the basic form is of hollow in the ground, with some form of superstructure or covering to aid the smelting process (see examples in Figure 1) (Coughlan, 1956; Wynne and Tylecote, 1958; O’Kelly, 1961; Cleere, 1972; Coughlan, 1977; Cleere, 1981; Tylecote and Merkel, 1985; Tylecote, 1986; 1987; 1992; Bayley et al., 2001). The bowl furnace contrasts with the relatively developed and more sophisticated shaft furnace which provides a larger internal volume for the different zones and for the smelt to take place and enables easier separation between the slag and the bloom (Wynne and Tylecote, 1958; Tylecote and Merkel, 1985; 2013; Crew, 2013; Smith, 2013; Doonan and Dungworth, 2013).
Within the literature on early iron smelting, the bowl furnace is typically regarded as the earliest and simplest of ancient furnaces, used by ‘primitive’ people, until the Romans spread the infinitely superior technology of the shaft furnace (Cleere, 1972; Coughlan, 1977; Cleere, 1981). The typologies tend on the whole to be both limiting and vague, implying gradual transition from the technologically stunted bowl furnace to the efficiency of the shaft furnace, without really making provision for the many anomalous archaeological remains that do not fit into any strict classifications (Cleere, 1971; 1972; Coughlan, 1977; Tylecote, 1986; 1992; Marks, et. al., 2020). A knock-on effect of this confusion of the different types, and the difficulty in identifying the remains of bowl furnaces (as distinct from other furnaces which may have had larger superstructures), is that the actual operation of the bowl furnace is poorly understood (See Figure 1).
There has been some previous experimental work carried out on the functioning of the bowl furnace for iron smelting, although the quantity is limited. Further experiments can help illuminate our understanding of the possible methods and working parameters of the bowl furnace. Experiments carried out by Wynne and Tylecote (1958) and O’Kelly (1961), have shown that it is difficult to produce iron in a bowl furnace. Wynne and Tylecote (1958) found that it needed to be worked either by the ‘Catalan method’ (see Figure 1 (A) ) or else ‘manipulated’ in the bowl to prevent the reduced ore being re-oxidised by the air from the tuyère. Overall, the bowl furnace was not very successful, and a more productive alternative was found by converting it into a low shaft furnace. Experiments by O’Kelly (1961) around the same time, managed to produce iron, though it was full of slag and pieces of charcoal, resulting in the product needing excessive refinement in order for it to be rendered useable. Based on experiment and archaeological remains, he concluded that the typical bowl furnace was 30cm in diameter, dug around 20-30cm deep into the ground, and coated with a clay lining. These were covered with a clay dome, and air was provided by a bellows (O’Kelly, 1961). However, it should be noted that the report is brief, and full details of the methods of charging and results were not given. While O’Kelly claims to have been successful, the results have not been fully published. However, the difficulty of the technique is noted, and it is stated that it is more suitable to soft bog ores or limonites than haematites (O’Kelly, 1961).
Tylecote and Merkel (1985) defined a bowl furnace as having a height/width ratio of ~1.0, and described work seen by anthropologists of use of bowl furnaces where the ore is manipulated in the bowl during firing to achieve the desired bloom. One of these examples comes from Burundi in East Africa, where it was used up to the 1930’s. The furnace has two opposed tuyères directed downwards, thus creating an upwards flow of carbon monoxide to the ore above. When the ore drops too low and is in danger of being oxidized, it is moved aside, and a further charge of ore and charcoal is added (See Figure 1. (C)). This process is repeated until a bloom forms (Tylecote and Merkel, 1985).
The unsuccessful results from initial campaigns of experimental work can be seen to have acted as a deterrent and contributed to the lack of further studies in relation to iron smelting in bowl furnaces. However, more recent research (Brown, 1995; Dungworth, 2013), has inspired fresh experimental work. Experimental work carried out by Girbal (2013) initially looked to be unsuccessful, however during analysis iron was found within the furnace conglomerate. When the process that occurs in a shaft furnace is considered in comparison to the bowl furnace, it is unsurprising that there has been so little enthusiasm for experimenting with bowl furnaces. In a shaft furnace, ore and fuel travel down the shaft together, allowing different stages of decomposition and reactions to occur in a controlled manner (see the discussion of the bloomery process above). In particular, the shaft furnace is thought to be adept at hosting the ore in a reducing atmosphere for a sustained period of time, before reaching the hottest part of the furnace occurs (Tylecote, 1986; Mihok, 1993). For a bloom to be formed, the individual particles of iron need to become hot enough, that they are able to come together and form a bloom mass. If they particles become too hot, they will become liquid and will not form a bloom, but would become entrapped within the slag. Therefore, temperature control is critical, as if it is too cold, solid iron absorbs carbon too slowly, and if it is too hot, the product will be a high carbon cast iron, which was not usable to the ancient metallurgists (Qian and Huang, 2021). Temperature control is easier to gain in a larger furnace, therefore we can see why it is considered so difficult to successfully smelt an iron bloom in a bowl furnace.
Experimental reconstruction
Owing to the somewhat limited research and literature on the use of the bowl furnace to make iron, an experimental project was designed to add more data to this field of research and to evaluate the success of the bowl furnace at producing iron. The experimental campaign consisted of comparing two different methods of loading the ore into the furnace. Using a refined, high content iron ore with constant bellowing and regular charging, it was hoped that it would prove possible to produce a furnace product with some iron content.
Methodology
The furnace was reconstructed to represent a general model of a bowl furnace, rather than aiming to reconstruct a specific example from the archaeological record. The design (See Figure 2) was most similar to Tylecote’s (1986) Type (B). The pit for the furnace was dug into the ground, to provide a slag pit, which is the area below the tuyere. The depth of the interior of this area, known as the Base Depth (not including the wall thickness) was 15cm. The thickness of the clay wall was 5 cm. The Total Height of the furnace (from the ground to the top of the furnace, not including the clay walls) was 40 cm and the Interior Diameter (at the point of the tuyere) was 45 cm. The Stack Height (from centre of tuyere to top of furnace) was 25 cm, the charcoal level was kept consistent throughout the smelt, only being allowed to burn down 2 cm, before being topped up. No Tap Arch or Extraction Arch was built into the furnace. The Tuyere Interior Diameter was 3 cm and the Tuyere Insert Angle was 0o as it was laid flat on the ground. The definitions for the measurements of the reconstructed furnace, are those suggested in Markewitz (2021). The upper part of the superstructure tapered in, resulting in the opening on top being a smaller diameter than the lower part of the furnace. The superstructure was built of clay ‘bricks’ tempered with straw and moulded into shape, then baked with a wood fire in the interior before being used to smelt in. The tuyère was made of fine clay, which was pre-fired in a kiln and entered the furnace wall on the horizontal just above ground level. The air was supplied through a bag bellows, which were made from cloth treated with linseed oil, with a circular wooden disc at the top and bottom. The bellows were pumped every 3 second, with a 2 second air blast. A refined iron ore pellet was used (67% iron content hematite), it was crushed finely (c.0.5 cm) by hand using a stone platform and stone hand hammer, prior to being added to the furnace. Temperature and reducing conditions were judged by the colour of the flame; when it was mostly colourless with some purple/blue flame (indicating that carbon monoxide was being burnt at the top of the furnace), the ore was added.
Two firings were carried out, the first using the layered technique (See Figure 3), which comprises of the charge being administered in between loads of charcoal, in layers. Each charge consisted of 200 g ore, which was then covered by c.300 g charcoal. The ore was crushed to c.0.5 cm pieces and the charcoal was crushed so the pieces were consistent, averaging 3 cm in size. Once all the ore was administered, charcoal was continued to be added in layers, to keep a reducing environment whilst the ore reacted in the furnace, until a total of 115 kg of charcoal has been added. Then the fuel was burnt down and left to cool before extracting the metallurgical material. When each load of fuel/charcoal was administered, was determined by the fuel burning down in the furnace, once the fuel line was 4 cm below the rim of the furnace, the next charge of ore and fuel or fuel was added. 1690 g of charcoal was added to the furnace as part of the pre-heating phase, then batches of c.300 g were added each time the furnace was charged, resulting in a total of 5507 g being added during the whole smelting process. The smelt ran for a total of 3 hours and charges were added on average every 20 mins (but this was determined by how quick the fuel burned down, to be able to compare consumption rate, rather than a set time interval). The second method consisted of the full charge of ore being added in one load (1500 g), as per the Catalan method (See Figure 4), this was added into the fuel in the furnace, once the furnace was up to temperature, then covered with charcoal. The charcoal was topped up during this smelt, not allowing it to burn down more than 4 cm below the rim. A total of 4259 g of charcoal was added to the furnace over a total smelt time of 3 hours (including the fuel used to fill and heat the furnace up). The smelt time was 3 hours as well, to enable comparison between the smelts. The charcoal loads were added when the charcoal has burnt down 4 cm below the rim as with smelt one, however this ended up being in intervals which averaged 20 minutes also, showing there was a comparable consumption rate between the two methods. The same quantity of ore was administered for both smelts (1500 g) (See Figure 5).
Results
Smelt One
The first smelt produced a friable conglomerate which can be seen in Figure 7 Small foils of malleable iron were noted on the surface of the conglomerate although these were too small to constitute ‘useful’ amounts of iron. This does however suggest that the reducing conditions required had been achieved. The disassembly of the furnace shows the high temperature effects on the clay, with voids left from the burnt out fired organic material and the colour of the interior of the clay being heat altered (See Figure 6).
The conglomerate was sectioned (cut with a saw) which revealed that the central portion of the conglomerate contained greater amounts of metallic iron than either the region nearer the tuyère or the area furthest from the tuyère. This suggests that optimal smelting conditions occurred in this region (approximately 15-20 cm from the tuyère).
Smelt Two
The second smelt did not produce any conglomerate, only burnt ore was found in the bottom of the furnace mixed in with ashes and un-burnt charcoal. It was obvious that this method was unsuccessful in producing iron, and the firing did not achieve much more than roasting the ore. When the ore was added, a significant drop in temperature and change in atmosphere in the furnace was noted. Though the overall temperature of the furnace was brought back up and maintained after this, it was obvious that the area in which the ore was situated did not reach the kind of temperature necessary to have any significant effect on the ore.
Microscopic analysis of materials and results
Samples were taken from the three different areas of the conglomerate formed in the first test firing (See Figure 7) and examined using reflective light microscopy. The samples were mounted in epoxy resin, then ground using an automatic Buehler Metaserv machine using 120 to 4000 grit papers. The samples were then polished using an automatic Buehler Metaserv with diamond paste from 6, 3 and 1 µm. Then cleaned to remove the residue of the process with an ultrasonic bath. The samples were then characterised and photographed using a Leica DM 2700P polarization microscope with magnifications up to 100x.
Sample one: tuyère end of conglomerate
This sample shows poorly developed structure; it is clear that while the furnace was hot enough to break down the ore and begin the early stages of iron formation, the sample was never fully molten and was formed in a semi-solid state. The major phase consists of disseminated iron oxides interspersed with glassy regions, and some rare inclusions of metallic iron. These metallic iron inclusions are found predominantly on the outer edge of the conglomerate.
Sample two: middle section of conglomerate
Microscopy showed (See Figures 8) that the pores in the middle section are much more rounded and vesicular, suggesting that they were produced by escape of gas from a fluid or semi-fluid substrate, and the slag was fluid enough to flow. This suggests that the middle section was approaching the temperatures required for the production of a liquid slag, this is supported by the high proportion of iron silicates (probably fayalite) and developed fayalite lathes. That the matrix was fluid or semi-fluid at some stage is evident by the fact that the metallic iron has begun to coalesce into a single mass of iron along the edges of the conglomerate.
Sample three: section furthest from tuyère
The region of the conglomerate formed furthest from the tuyère showed a similar structure to the central region but with significantly less metallic iron present. This area was characterised by iron oxides, mostly in the form of wustite over fine fayalite crystals. Wustite is an iron oxide phase, which is formed before turning to metallic iron and fayalite crystals show the environment was reducing. The lower proportion of metallic iron present and the fact that it has not coalesced into a single mass is indicative of cooler temperatures (See Figure 9).
Discussion
The results of the experimental campaign demonstrates that the furnace conditions within a bowl furnace of this size and shape, are capable of being sufficiently reducing to produce an iron bloom and to reduce iron oxide to iron metal. This campaign was successful in producing very small amounts of iron. Further experiments to investigate the efficiency of producing large amount of iron in a bowl furnace, would require longer smelting periods with larger amounts of ore being added during the smelting process. The type of device and method used for air input and the amount and pressure of the air, also needs to be investigated, as this can significantly affect temperatures and the reducing environment. This investigation has highlighted that primary challenge of the bowl furnace appears not to be in producing and maintaining a reducing atmosphere but in reaching the temperatures required to produce a molten slag to allow bloom consolidation. With the use of one tuyere and one bellow, it was difficult to maintain elevated temperatures across even half the diameter suggesting that even simple hearths probably required the coordinated labour of several people. More investigations into how much air flow is required, for different size furnaces, primarily dependant on the furnace diameter has been conducted by Sauder (2000a; 2000b) and Markewitz (2012), highlighting how the furnace volume effects many aspects of smelting bloomery iron. Therefore, more work is needed testing different variables of air input within bowl furnaces to understand their capabilities, to fully understand this technology.
A limiting factor of the bowl furnace appears to be the restricted residence time the charge spends in the fusion zone. As the furnace is shorter, there is less space for ore to move within, before reaching the top of the furnace. This furnace took used 5.5kg of charcoal for a 3-hour smelt, whereas an 80 cm high shaft furnace with a diameter of 40 cm used 23.6 kg of charcoal for a 2 hour smelt (Marks, 2020). This highlights the difference in volume between a shaft furnace and a bowl furnace. As this bowl furnace only took 1175 g to fill, according to the burn rate (the speed and amounts of charcoal added) the ore would have reached the bottom of the furnace after 48 minutes of being administered. Whereas in an 80 cm high shaft furnace which would take at least double the amount of charcoal to fill, the ore would take longer to move down through the shaft. However, burn rates can be altered in both styles of furnace (bowl and shaft) dependant on the air input and resulting temperatures achieved. Therefore, the volume of a furnace is important to record and consider too, as well as burn rate. The layering technique worked better than the pre-charge technique as the ore tended to move towards the fusion zone as charcoal was consumed. We therefore suggest that the reducing atmospheres afforded by the volume provided by a shaft furnace have been overstated and a key advantage is the extended time that charges can dwell at elevated temperatures.
It should be pointed out that it has been observed during this project that successful use of the bowl furnace technique requires intricate knowledge of the different zones within the furnace, and a skill at manipulating the contents without having a detrimental effect on the process. While the experiments here did not produce significant quantities of iron, it is believed that this was down to poor technique, using one air source and using a small amount of ore, rather than the inability of a bowl furnace to produce iron. Further experimentation focusing on different air sources, as well as these loading methods, could serve to illuminate better this poorly understood process.
Conclusion
This consideration of the bowl furnace for iron smelting – combining analysis of previous experiments conducted with the experimental campaign presented in this paper, has demonstrated that there is still more to be understood about the functioning of a bowl furnace for iron smelting.
We believe that we have shown the value in further experimental campaigns to explore the use and function of bowl furnaces to smelt iron. Particularly, more in-depth studies of the internal environment of such furnaces, as well as considering different loading methods, will help us gain a better understanding of how bowl furnaces may have been used to smelt iron. Additionally, there is value in such studies to inform consideration of the emergence and functioning of shaft furnaces.
Keywords
Country
- United Kingdom
Bibliography
Bayley, J. D., Dungworth and Paynter, S. 2001. Centre for archaeology guidelines: archaeometallurgy. London: English Heritage.
Brown, J. and Sassoon, J.B., 1995. Traditional metalworking in Kenya (No. 38). Oxbow Books Limited.
Cleere, H., 1971. Iron smelting experiments in a reconstructed Roman furnace. Britannia 2, pp.203-217 [online] Available at: < https://www.jstor.org/stable/525810 >
Cleere, H. F., 1972. The classification of early iron-smelting furnaces. The Antiquaries Journal, 52(1), pp. 8-23.
Cleere, H., 1981. The Iron Industry of Roman Britain, University of London.
Coughlan, H., 1956. Notes on Prehistoric and Early Iron in the Old World Including a Metallographic and Metallurgical Examination of Specimens Selected by the Pitt Rivers Museum. 1st ed. Oxford: Oxford University Press.
Coughlan, H., 1977. Notes on Prehistoric and Early Iron in the Old World Including a Metallographic and Metallurgical Examination of Specimens Selected by the Pitt Rivers Museum. 2nd ed. Oxford: Oxford University Press.
Crew, P.,2013. Twenty-five years of bloomer experiments: perspectives and prospects, in: D. Dungworth and R.C.P. Doonan (eds.). Accidental and Experimental Archaeometallurgy. London: Historical Metallurgy Society, pp. 25-50.
Doonan, R. C. P. and Dungworth, D., 2013. Experimental archaeometallurgy in perspective, in: D. Dungworth and R.C.P. Doonan (eds.). Accidental and Experimental Archaeometallurgy. London: Historical Metallurgy Society. pp. 1-10.
Dungworth D., 2011. Examination of metalworking debris from the 1939 excavations at Trevelgue Head, in: J. Nowakowski and H. Quinnell (ed.) Trevelgue Head, Cornwall – an Iron Age cliff-castle: the story of the 1939 excavations by the late C K Croft Andrew (Truro), pp. 220-224.
Dungworth, D., 2013. Experimental archaeometallurgy: hypothesis testing, happy accidents and theatrical performances, in: D. Dungworth and R.C.P. Doonan (eds.). Accidental and Experimental Archaeometallurgy. London: Historical Metallurgy Society. pp.11-16.
Friede, H. M. and Steel, R. H., 1977, An experimental study of iron-smelting techniques used in the South African Iron Age, Journal of the South African Institute of Mining and Metallurgy, 77(11), pp. 233-242.
Girbal, B., 2013. Experimenting with the bowl furnace’, in: D. Dungworth and R.C.P. Doonan (eds.). Accidental and Experimental Archaeometallurgy. London: Historical Metallurgy Society. pp. 83-92.
Markewitz, D., 2012. But if you don't get any IRON... Towards an Effective Method for Small Iron Smelting Furnaces, EXARC1. Available at: < https://exarc.net/ark:/88735/10041 >
Markewitz, D., 2021. Standardized Reporting of Experimental Iron Smelting - A modest (?) Proposal, EXARC 1. Available at: < https://exarc.net/ark:/88735/10559 >
Marks, Y., Groat, N, Lortie, L. O., Hughes, M., Thompson, H. F., Woodland, C. J., Adams, T. M.S., Thorpe, T., Tang, B., Kenyon, R., Langhorne, B. and Fraser-Darling, J., 2020. Smelting Conditions and Smelting Products: Experimental Insights into the Development of Iron Bloomery Furnaces, EXARC 2. Available at: < https://exarc.net/ark:/88735/10504 >
Mihok, L., 1993. Metallographic examination of pattern-welded swords from the Hark Roman period in Eastern Slovakia, Archaeomaterials, 7. pp. 41-51.
O’Kelly, M., 1961. The Ancient Irish Method of Smelting Iron, in: G. Bersuand and W. Dehn (eds.) Bericht über den V. Internationalen Kongress für Vor- und Frühgeschichte, Hamburg vom 24. bis 30. August 1958. 1st ed. Berlin: Mann, pp. 459-461.
Qian, W. and Huang, X., 2021. Invention of cast iron smelting in early China: Archaeological survey and numerical simulation, Advances in Archaeomaterials, 2(1), pp. 4-14.
Sauder, L., 2000a. The Basics of Bloomery Iron Smelting, in: The Anvil’s Ring. Artist Blacksmith Association of North America.
Sauder, L., 2000b. Smelt Diary for Smelts 21- 27. [online] Available at: < http://iron.wlu.edu/smelttables/21-27.html >
Smith, T., 2013. A report on the Wealden Iron Research Group smelt, in: D. Dungworth and R.C.P. Doonan (eds.). Accidental and Experimental Archaeometallurgy. London: Historical Metallurgy Society, pp. 99-106.
Tylecote, R., 1986. The Prehistory of Metallurgy in the British Isles. London: Institute of Metals.
Tylecote, R., 1987. The early history of metallurgy in Europe. London: Longman.
Tylecote, R., 1992. A History of Metallurgy. 2nd ed. London: Institute of Materials.
Tylecote, R. and Merkel, J., 1985. Experimental smelting techniques: achievements and future, in: P. Craddockand M. Hughes (eds.) Furnaces and Smelting Technology. 1st ed. London: British Museum Press, pp. 3-20.
Wynne, E.J. and Tylecote, R., 1958. An experimental investigation into primitive iron smelting technique, Journal of the Iron and Steel Institute, 190, pp. 339-48.