The content is published under a Creative Commons Attribution Non-Commercial 4.0 License.
Reviewed Article:
(Re)constructing an Early Medieval Irish Ard
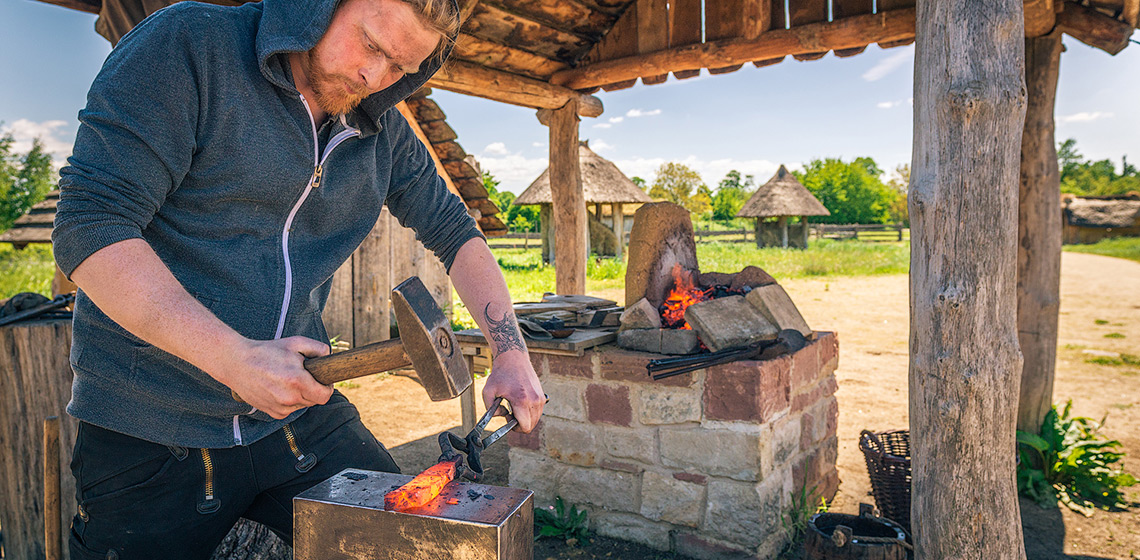
This article outlines the results of an EXARC funded 2019 Twinning project exploring the production and use of an Irish early medieval ard. In this, the project partners researched the evidence for early ploughs and ards, made bloomery iron, produced an ard share, and worked wood to form the frame of the ard. This paper also includes the results of scientific analysis and reflections on ploughing using specially trained draft animals. Ultimately, this provided details about this crucial agricultural technology and its place within early medieval society. This project is also a case-study, showcasing collaborative, practical research strengths between leading centers for experimental archaeology.
Introduction
The early medieval period in Ireland (AD 400-1100) was a time of far-reaching social, religious, and technological developments across the island (O’Sullivan and McCormick, 2017). The people were mainly pastoralists, devoted to raising cattle, but were also increasingly engaged in arable farming. Somewhat unusually, there is excellent and abundant evidence for the kinds of crops people were growing and how they were processing these to make bread, pottages, biscuits, etc. (McCormick et al. 2011). What is less well documented are the details of plough making and ploughing, archaeologically enigmatic yet crucial technologies during the early medieval period. This Twinning Project sought to investigate this by bringing the strengths of The Lauresham Open-Air Laboratory in Germany (Lauresham) and the Centre for Experimental Archaeology and Material Culture in University College Dublin, Ireland (CEAMC) together in the reconstruction of an early medieval Irish ard; a light plough with a symmetrical ploughshare.
Lauresham, at the UNESCO World Heritage Site Lorsch Abbey, and CEAMC at University College Dublin (UCD) are two complementary institutions. The first is a high-quality Archaeological Open-Air Museum (AOAM) dedicated to communicating daily life and work at an early medieval monastic manor associated with Lorsch Abbey while conducting scientific research on agricultural livestock management and technologies. CEAMC is an officially designated UCD Research Centre dedicated to researching and teaching material culture using a wide range of methodologies found in experimental archaeology. Its staff, students, and facilities are also committed to public outreach and engagement to showcase past material culture, ancient technologies, and the strengths of interdisciplinary research.
These sites are ideal Twinning partners, as together they encapsulate the ethos and pillars of EXARC; AOAMs, Experimental Archaeology, Ancient Technologies, Interpretation and Living History. They also share an interest in creating and communicating archaeological knowledge as well as a number of common research themes: early medieval architecture; agricultural technologies; crafts and production, including ironworking and non-ferrous metalworking. Importantly, both bring different strengths to a project of this kind. Lauresham has established knowledge in raising, training, and working with a range of domesticated animals, allowing investigation of past lifeways and living conditions. CEAMC has a longstanding research history investigating early medieval “hot technologies”, such as metal work. Based within a university campus CEAMC also has access to a broad range of analytical possibilities. Together, this partnership provided the skillsets to create early medieval iron, forge a ploughshare, and ultimately assemble a suitable plough with the view to testing it under ‘actualistic’ conditions (Hurcombe, 2008, 85; Molloy, 2008, 119).
Reconstructing the evidence
Plough technologies and their development are key indicators of the character and productivity of early medieval agriculture, particularly from the 7th/8th century AD onwards, when cereal production intensified across Europe to support growing populations. They were a vital means of preparing soils for growing cereals such as wheat, barley, and oats, which were important food staples and a means of acquiring surplus goods for markets and exchange. However, there is still much that is not fully understood about the effectiveness of ploughs and their typological development (See Figure 1). Consequently, the aim of this project was to create new insights into evolving agricultural practice in early medieval Ireland and Germany (and more broadly throughout Europe) by undertaking the complete reconstruction of a particular example. Additionally, it sought to understand the detail of this agricultural practice, how ploughing was actually undertaken, and what components it involved.
There is quite a lot of archaeological evidence from Ireland for 8th/9th century ploughshares (the arrow-or sock-shaped iron object that lifted and sometimes inverted the soil) and iron coulters (the heavy iron blade that hung down from the wooden plough and cut the sod) (See Figure 2). In contrast, these iron implements are almost completely missing in the south-western part of Germany where the Lauresham Laboratory is situated. As such, the starting point of this project was a symmetrical ploughshare, excavated at Rathtinaun, Co. Sligo (See Figure 3) and dated c.500 AD (Brady 2016, p.146). Although only one component, this implies important information about other aspects of the wooden frame it was attached to and how it may have been used. According to Bentzien’s typology (1990, 25 and 33), it can be categorised as an early medieval ‘spear-shaped’ share, which had ‘elongated, tubular’ spouts. Šach (1968, p.19) and Fries (1995, p.47) also held the opinion that such shares were mounted almost vertically on the ard, resulting most likely in a sole-less construction of the implement (Bentzien, 1990, p.25). The vertical position is important for a possible reconstruction as it is known that ards with shares in this position do not require coulters (Leser, 1931, cited by Fries, 1995, p.58; Brady, 1993, pp. 34 and 37). Accordingly, the plough types a, b, c, or e in Figure 1 can be considered as suitable for the chosen share. Of elementary importance for said types is the so-called Tegneby plough (Type 2), derived primarily from Bronze Age rock paintings (Fries, 1995, p.29).
The starting materials for the Tegneby plough might have been either a forked branch (in the form of a type 1 plough of Figure 1), to which an additional piece was added as a stilt, or two separate pieces were used for the beam and stilt with an ‘ard-head’ (Fries, 1995, p.30). Fries (1995, p.30) claims that the stilt wore out faster than the beam and therefore the connection of the two parts would most likely have created a hole in the beam. Also, in the replica of Hansen (1969, p.68), the ard head was passed through the beam. However, results of experiments with earlier models at the Open-Air Laboratory show that the beam broke just as often and was therefore at least equally prone to wear (cf. Töngi, 2019, p.15).
A bipartite beam is the normal case in most ards (Lerche, 1994, p.12). This has been proven, among other things, by the discovery of the ard from Dabergotz, which was dated to the 8th century AD by means of radiocarbon dating and analysis (Bentzien, 1968, p.53). Its beam was located only a very short distance above the sole, making it impossible to attach it to the yoke. Therefore, the presence of a beam extension was concluded, which could be up to 2 metres long. Further research confirmed this (Bentzien, 1968, pp.50 - 53). A 2m long beam was also found on a plough find in Drumlee, Co. Down (Earwood and Beattie, 2008, pp.118). Possibly the extension was attached to the actual beam by means of bands of willow and wooden pegs (Bentzien, 1968, pp.50 – 53). A handle at the upper end of the stilt may also be archaeologically attested in a find from Hendriksmose. In this case, the stilt has a perforation just below the upper end, likely indicating the original presence of a handle (Coles, 1973, p.26).
(Re)constructing the ploughshare
Raw materials
The ore from which the iron (iarainn in old Irish) for this project was made was Irish ‘bog ore’ (Carlin et al. 2008, 91), formally known as goethite, collected from a raised bog in Co. Offaly. Bogs and other wetlands are ideal environments for the formation of this ore, as minerals, particularly iron, are leached from peat, stone, vegetation, and underlying geology by a weak reaction with humic acid (Feehan and O’Donovan, 1996, p.99; O’Neill et al., 2014). The exact location of this mineral just below the surface of many bogs (Dungworth, 2015) can be easily identified by following iridescent discolouration of ground water to its source and digging down, typically revealing varying quantities of nodular, “rusty” rocks.
Despite some initial scepticism surrounding the ‘usually vague’ (Scott, 1991, p.152) references to bog ore in excavation reports, more recently our understanding has been greatly advanced through a combination of increased archaeological excavations in Ireland and applied archaeological sciences. Finds of iron ores from early medieval Ireland are understandably few as the process of smelting does not lend itself to their preservation. While a small number of excavations have reported “haematite”, these tend to be only tiny pieces found close to well-known sources, such as at Cahircalla More, Co. Clare (Keys, 2006; Taylor, 2006). Aside from these, the vast majority of ore finds are either bog ore, siderite, or limonite, each forming under similar wetland conditions.
Another source for determining the ores used in the production of iron is slag, a waste product of the smelting process. Importantly, the elemental composition of this substance is directly related to the parent ore and so may infer type (Paynter, 2006). Specifically, the presence of trace manganese (more correctly manganese oxide) has been cited as diagnostic of bog iron ore (Scott, 1991, p.153; Hall and Photos-Jones, 1998). This has also been borne out by analysis of archaeological slags (Photos-Jones, 2008, p.186; Wallace and Anguilano, 2010, p.70; O’Neill, 2017), corroborating bog ore as the primary ore used in early medieval Ireland. Indeed, similar evidence has been discovered from a range of near contemporary Viking sites where iron was also produced from this ore (Stenvik, 2003, p.123; Wallace, 2003, p.15; Smith, 2004, p.189), perhaps demonstrating a preference for its use during this time.
Smelting
Iron was made in early medieval Ireland in non-tapping, slag-pit, shaft ‘bloomery furnaces’ (Killick and Gordon, 1988, p.120). These features create specific conditions (thermal and atmospheric) that facilitate complex thermo-chemical reactions to make metal. For this twinning project the iron was made at the Centre for Experimental Archaeology and Material Culture (CEAMC), University College Dublin. Over two individual smelts (c.7 hours each) almost 10.5kg of iron was made by 9 participants from 45kg of ore and c.200kg of oak charcoal. These were only roughly consolidated to remove the bulk of the slag, after which the metal was analysed and delivered to Lauresham Open-Air Laboratory to be forged into ploughshares.
As smelting bloomery iron is a complicated and organic process (with no two smelts identical), only a generalised procedure is outlined here, reflecting years of research and testing at CEAMC. Before smelting, the ore was heated to temperatures of c.600-800°C, a process that is typically known as “roasting” (See Figure 4). Although the informal nature of this process leaves little archaeological traces, technologically it has two main advantages. Firstly, it allows the ore to be more easily crushed as it microfractures through heating. Although not strictly necessary, this makes smelting more efficient by providing a greater surface area of ore to react with the heat and atmosphere of the furnace. Additionally, in the case of bog ore, it converts the already quite reactive goethite into even more reactive magnetite.
A furnace was constructed as a 1m high tapering clay shaft over a cut basal pit (See Figure 5). On one side at ground level an arched opening was cut into the shaft that was resealed with a thin ‘false door’ of clay. This provided an opening allowing air to enter the furnace, and a means of retrieving the bloom once formed. Archaeological evidence for the use of similar non-tapping, slag-pit, shaft furnaces can be found throughout early medieval Ireland showing access to bloomery iron at all levels of this society.
During smelting of this kind, the hottest area inside the furnace is at ground level where oxygen is being bellowed into the feature (adding additional combustible ‘fuel’ and pressure). This creates something like a conveyor belt, allowing charcoal above to slip downwards into this “hot zone”. If all works well, this will create space at the top of the shaft where new charcoal and ore can be added throughout the smelt (See Figure 6). To create the right atmosphere (a reducing atmosphere) within the furnace, a high proportion of carbon (a reducing gas) is needed, which we estimate to be roughly 2:1 (charcoal:ore). Being non-tapping furnaces, the slag accumulates within the basal pits of these features throughout the smelt, providing an effective limit when it is filled with slag, blocking the air hole and stopping the smelt (Pleiner, 2000, p.141).
At this point, the bloom, a ‘spongy mass of reduced iron particles’ (Scott, 1991, p.156) and slag, must be retrieved while still hot to allow the malleable iron to be consolidated and the more liquid slag to be expelled. To do this, the “false door” where the bellows entered the feature is broken through and the ferrous mass removed using tongs (See Figure 7). In this instance, the bloom was placed on a wooden stump for repeated hammering and splitting until it was too cold to be worked.
Refining and Forging
On the first day of the refining process in the Lauresham Open-Air Laboratory, the material was fire-welded, forged, split and fire-welded again in several repetitions (See Figure 8). During this work process, it was noticed that only the layers in the core connected, while hardly any connected at the edge. Another problem was encountered during splitting, where the material often became brittle and broke.
Analysis of samples of ore, slag, blooms, and iron (cut, polished, and etched) was conducted at UCD to better understand if these issues were material in nature. Bulk chemical analysis of iron samples using SEM-EDS (Hitachi TM3030Plus) showed a consistent progression of elements from ore to the resulting iron (See Figure 9). Importantly, trace elements such as phosphorus (P) and sulphur (S), which might account for brittleness in the metal, are only in extremely low concentrations. There was, however, a somewhat elevated detection for carbon (C) specifically in the iron samples. Subsequent quantitative analysis of the original blooms using an Optical Emission Spectrometer (OES) confirmed only trace amounts of phosphorus and sulphur as well as elevated amounts of carbon, albeit in varying quantities across the samples (See Figure 10). Indeed, this variable carbon content can also be seen in the differing, uneven distributions of pearlite across micrographs of these samples.
One explanation for the incomplete connection of the partially flaky iron pieces in the edge areas may be insufficient heat during the welding process. This may be due to the design of the forge used at Lauresham, which seems to have produced inadequate heat for this size of iron stock (Holdermann and Trommer, 2017, 14f.). It should be noted at this point that the external forge located at Lauresham is normally operated by two bellows and used for smaller work pieces such as nails, brackets, or smaller tools. An initially used portable forge (usually used for damask manufacturing) failed and the Lauresham forge had to be used. In order to create a better air supply for all sides of the workpiece during the refining process, the forge was equipped with a second nozzle stone and finally operated with four bellows simultaneously on the second day of the process (See Figure 11). Nevertheless, the heating process remained rather long. Indeed, another part of this bloom was refined in the regular forge at Trommer Archäotechnik in Blaubeuren (Germany) using a forge with a larger heating area and modern machinery. After repeated working, the result was a thoroughly coherent bar.
In a final step, the actual ploughshare was forged from the bar that had been produced (See Figure 12). After the tip was forged out, the two flaps (as a spout) were worked out in a second step. The finalised ploughshare had an overall length of 17 cm and was 8 cm at its widest point (See Figure 13).
(Re)construction of the plough-body
The naturally curved branch of an oak (Quercus petraea) was selected as the stilt. The diameter of this piece was 20 cm. Another piece of oak with a diameter of 24 cm served as the main part of the beam. Willow (Salix sp.) with different curvatures was selected for the beam extension. A round log, also made of willow, was used as the material for the sheath. The tools used were a drawknife, beard axes, and splitting axes of various sizes. Furthermore, a hand saw, various chisels, and in connection with them a wooden hammer (german Klüpfel), as well as a manual hand drill were used (See Figure 14).
The construction of the plough was completed by a couple of people within 5 days (07/27 - 07/31/2020). In the beginning, the stilt main piece was constructed. The first step consisted of debarking the wood with the drawknife and a bearded axe. The tool was also used to smooth out the surface. To reduce the diameter of the wood, successive notches were cut into the wood with a splitting axe. The area between each notch could eventually be chipped out with the axe. The lower end of the stilt (ard-head) was also axed with a bearded axe, and then its width and depth were adjusted to the size of the share with a chisel. A drawknife (Zieheisen) was useful to work the surface of the head into a flat shape (See Figure 15).
To model the beam, the selected wood had to be debarked and shortened again. The beam piece, which was to be passed through the stilt, was additionally worked down to 9x5 cm edge length. For the sheath, a round piece of willow was found in Lauresham, which only had to be sawn to the correct length. The sawn-off remainder was to serve as a handle in the stilt. The willow for the beam extension also had to be shortened and debarked. The branch attachments were cut off with an axe. A wooden nail was integrated at the front end of the beam extension, which would then be attached to the yoke. Furthermore, a support surface for the yoke was created, as well as notches for attaching the ropes.
After all the individual parts were made, they were joined together by plug-in connections. For this purpose, three mortises were cut in the stilt. A small mortise just before the upper end served as a holder for the handle. Below this, a mortised tenon joint was used to connect the beam to the stilt (See See Figure 16). The two-sided tenons of the beam were secured at the exit point with a wooden nail. A mortised tenon hole in the stilt served as a contact surface for the sheath, which was guided through a hole in the beam and was held in position by another wooden nail. Various chisels and a mallet were used as tools for all holes. The nails were created by means of a bearded axe and driven into the hole pre-drilled with a hand drill. For the connection of the beam and its extension, an overlap was chosen as the joint. For this purpose, the wooden parts joining each other were sawn to the same length up to the centre point and then flattened from the end of the wood to that point. To secure the overlap, two additional wooden nails were made. Finally, the share was fixed on the ard-head of the stilt after it was heated in the forge.
Experimental archaeological testing of the (re)construction
After completion of the reconstruction (See Figure 17), a detailed practical test was carried out in the Lauresham Open-Air Laboratory, including the associated draft measurements. A small field of slightly loamy sand served as the test area. During a total of three test measurements, a furrow depth of 7 cm was achieved. If force was applied to push the ard into the soil, a furrow depth of 13 cm could be produced (See Figure 18). The furrow width was around 11 cm. Depending on the ploughing depth, the average draft force varied from 24.2 kg to 67.4 kg. The maximum load at 13 cm ploughing depth was 133.8 kg. The plough generated V-shaped furrows, which fits well with corresponding archaeological plough marks (Lerche and Steensberg 1980, 60-63).
The present results allow the conclusion that light ard types, like the one reconstructed in the present report, may have been of great importance within early medieval Irish agriculture. This is because compared to heavier plough types (cf. Kropp, 2022 forthcoming) they could be pulled by 1-2 draught cows. This conclusion can be drawn from the fact that on average, draught cattle can pull between 10 and 15 percent of their live weight over a long period of time without major issues (Minhorst, 2015, p.154). Although the maximum pulling capacity over short distances is significantly higher, the average pulling capacity must always be used as the basis for calculation for the ploughing process. The cows of the Rhaetian Grey cattle breed used in the Lauresham open-air laboratory have a bodyweight of 400-450 kg and were considered as the basis for comparison. Due to the low height at the withers of female animals, usually less than 110 cm, this breed also falls within the general size range of the medieval comparative finds (Kropp, 2017, p.27).
The low furrow depth was compensated by the generally lower tractive force needed. Efficiency and feasibility were therefore in a special tension with one another. Finally, the time factor must not be disregarded. For example, a light ard may have required less tractive force than a heavy mouldboard plough, but the necessary crisscross ploughing pattern also required a considerably bigger time investment.
Discussion
If taken in isolation, the iron components that represent most of our archaeological evidence of early ploughs and ards provide limited understandings of what they actually represented for the people that depended on them. Not only are they just one small part of the physical structure of ploughs but they also suffer terribly from corrosion, creating a conceptual distance between the artefact and what it might have originally looked like. Aside from a very small number of fragmentary archaeological finds and a few iconographic depictions, the wooden components of these ploughs are even more poorly represented. This project demonstrates the complexity, not only in their production (including the choice of materials) but also in their specific engineering. This Twinning project successfully bridged this distance, bringing early medieval ploughs back to life.
What we now know is that even a light ard, like the one reconstructed for this project, represents a huge number of skills. Iron must be made by a community of people, transforming ores, charcoal, and clay into ingots of hard metal. The expertise of blacksmiths is needed to forge, weld, and shape reliable and robust shares (and coulters). In-depth knowledge of woods, individual wood characteristics, woodworking, no doubt common to most people in the early medieval period, was essential to making a frame that could withstand the forces exerted by draught animals pulling them through hard soil. Yet, these components brought together would be meaningless without the ability to read the land, control the animals, and work the plough. All of this is not to mention the bewildering number of associated tools and people intersecting with the extended biography of any plough during the early medieval period.
With this in mind, it is not surprising that early medieval sources not only attribute enormous importance to the process of ploughing (lat. arare), but also the plough (lat. aratro) itself. Perhaps similar to the possible sharing of draft animals between groups of farmers (as known from Charlemagne's decree concerning a complaint by vassals about the use of ploughing and manual labour from the year 800), ploughs might have been owned and/or used by groups rather than individuals. If true, this would fit well into the understandings of the production and use of these ploughs derived through this project.
Nevertheless, it can be assumed that at least the ploughshares must have been regularly in use over a quite long period of time. The long-term experiments carried out in the Open-Air Laboratory using different plough- and ard(re)constructions show significant signs of wear on the shares already over the course of a few years, but without any major functional constraints (See Figure 19). This even applies to collisions with stones on the arable land. If the effort in the production of such elementary farming implements was very high, they were also very durable. This finally adds even more value to them.
Conclusion
This EXARC Twinning project between Lauresham Open-Air Laboratory and UCD CEAMC provided a framework of collaboration and support for our two institutes. By making an early medieval ard, visiting each other, and writing up our results together we have established networks for future work together and already encouraged colleagues, students, as well as visitors to once more focus on the practical micro-level of medieval agriculture. Only in this way will it be possible to explore more about the functional interrelationships of work processes at that time.
Acknowledgements
We would like to recognise the generosity and support of EXARC and thank them for providing seed funding for this project.
To achieve such a multifaceted project, we are indebted to a number of people and groups. CEAMC would like to specifically thank Paul Bright from UCD School of Mechanical and Materials Engineering for preparing samples and operating coordinating the OES analysis and the School of Earth Science for the use of their SEM-EDX. We would also like to thank the two classes of students that participated in both iron smelts; MSc in Experimental Archaoelogy and Material Culture class of 2019 and DSCY10070 class of 2019. The Lauresham Open-Air Laboratory would like to specifically thank Kim Liebscher and Pierre Stoll from Trommer Archäotechnik for their expertise and support in the refining and forging process as well as Sebastian Diehl as staff member of Lauresham for his fine skills when it comes to wood-working. A special thanks also goes to both Niall Brady and Janine Fries-Knoblach for providing the permission to use their graphs and illustrations in this paper.
Country
- Germany
- Ireland
Bibliography
Bentzien, U., 1968. Der Haken von Dabergotz. In: A. Steensberg, A. Fenton, G. Lerche Eds. Tools and Tillage. Vol. 1: 1 1968, pp. 50 – 55.
Bentzien, U. 1990. Bauernarbeit im Feudalismus: Landwirtschaftliche Arbeitsgeräte und -verfahren in Deutschland von der Mitte des ersten Jahrtausend u. Z. bis um 1800, Berlin, Akademie-Verlag.
Brady, N. 1993. Reconstructing a Medieval Irish Plough. In: Museo Nacional del Pueblo Español Eds. I Journadas Internacionales sobre Tecnologia Agraria Tradicional. Madrid, pp. 31-44.
Brady, N. 2016. What the Plough can reveal about the role of agrarian technology in the changing nature of early medieval Ireland. In: Agrarian Technology in the Medieval Landscape: Agrartechnik in mittelalterlichen Landschaften. Technologie agraire dans le paysage médiéval Smolenice, Slovakia: Turnhout, 9th - 15th September 2013. pp 143-155.
Carlin, N., Ginn, V. and Kinsella, J. 2008. Iron working and Production In: N. Carlin, L. Clarke L. and F. Walsh Eds. The Archaeology of Life and Death in the Boyne Floodplain: The Linear Landscape of the M4 Kinnegad-Enfield-Kilcock Motorway. NRA Scheme Monographs 2, pp. 87-112.
Coles, J. 1973. Erlebte Steinzeit – Experimentelle Archäologie. München, Gütersloh, C. Bertelsmann Verlag.
Earwood, C. and Beattie, K. 2008. A Medieval Plough from Drumlee, County Antrim. Ulster Journal of Archaeology, Third Series, Vol. 67, p. 118.
Feehan, J. and O’Donovan, G. 1996. The Bogs of Ireland. University College Dublin, The Environment Institute.
Fries, J., C. 1995. Vor- und frühgeschichtliche Agrartechnik auf den Britischen Inseln und dem Kontinent: Eine vergleichende Studie. In: C. Dobiat, K. Leidorf Eds. 1995: Internationale Archäologie. Band 26, Espelkamp, Verlag Marie Leidorf GmbH.
Hall, A. and Photos-Jones, E. 1998. The bloomery mounds of the Scottish Highlands: Part II – a review of iron mineralization in relation to the Scottish Highlands bloomeries, Journal of the Historical Metallurgy Society, 32 (2), pp. 54–66.
Hansen, H.O. 1969. Experimental Ploughing with a døstrup ard replica: a report to Imitative ploughing experiments with replicas of a prehistoric ard type carried out in 1962-1968. In: A. Steensberg, A. Fenton, G. Lerche Eds. Tools and Tillage. Vol. 1: 1 1968, p. 68.
Holdermann, C. and S., Trommer, F. 2017. Zum karolingerzeitlichen Metallhandwerk – Eine Skizze zu Ausstattung, interner Organisaion und Funktion der rekonstruierten Schmiede von Lauresham, In: C. Kropp together with Verwaltung Staatlicher Schlösser und Gärten Hessen Eds. Laureshamensia – Forschungsberichte des Experimentalarchäologischen Freilichtlabors Karolingischer Herrenhof Lauresham No. 1. Bad Homburg v.d.H., pp. 6-23.
Hurcombe, L. 2008. Organics from inorganics: using experimental archaeology as a research tool for studying perishable material culture, World Archaeology, Vol. 40, No. 1, Experimental Archaeology, pp. 83–115.
Dungworth, D. (Ed) 2015. Centre for Archaeological Guidelines, Archaeometallurgy: Guidelines of Best Practice, available at: < https://historicengland.org.uk/images-books/publications/archaeometallu… > [Accessed date: 26/03/22]
Keys, L. 2006. Metalworking Remains. In: K. Taylor, N18 Ennis Bypass and N85 Western Relief Road Site AR128. Cahircalla More, Co. Clare Final Archaeological Excavation Report for Clare County Council, Unpublished Report, TVAS Ireland Ltd, pp. 15-18.
Killick, D. J. and Gordon, R. B. 1988. The mechanism of iron production in the bloomery furnace. In: R.M. Farquhar, R.G.V. Hancock and L.A. Pavlish (eds.) Proceedings of the 26th International Archaeology Symposium, Toronto, Archaeometry Lab, University of Toronto, pp. 120-23.
Kropp, C. 2017. Tierische Anspannung im Experiment. Potentiale und Grenzen. In: C. Kropp together with Verwaltung Staatlicher Schlösser und Gärten Hessen Eds. Laureshamensia – Forschungsberichte des Experimentalarchäologischen Freilichtlabors Karolingischer Herrenhof Lauresham No. 1. Bad Homburg v.d.H., pp. 24-31.
Kropp, C. (forthcoming 2022). Cattle and tillage in early medieval Europe: first results from the Lauresham Laboratory for Experimental Archaeology, Germany. In: M. McKerracher and H. Hamerow (eds). New Perspectives on the Medieval ‘Agricultural Revolution’: Crop, Stock and Furrow. Liverpool: Liverpool University Press.
Lerche, G. and Steensberg, A. 1980. Agricultural Tools and Field Shapes. International Secretariat for research on the history of agricultural implements. No. 3, Copenhagen.
Lerche, G. 1994. Ploughing Implements and Tillage Practices in Denmark from the Viking Period to About 1800. Kopenhagen, Herning.
Leser, P. 1931. Entstehung und Verbreitung des Pfluges, Ethnol. Anthropas-Bibliothek 3, Vol. 3, Münster.
McCormick, F., Kerr, T. McClatchie, M. and O’Sullivan, A. 2011. The archaeology of Livestock and cereal production in early medieval Ireland, AD 400-1100, Early Medieval Archaeological Project (EMAP) report 5.1 to the Heritage Council INSTAR Programme, Dublin and Belfast, University College Dublin and Queen’s University, Belfast.
Minhorst, R. 2015. Zugkraft. In: A., Masson Ed. Handbuch Rinderanspannung. Praktischer Ratgeber zu Verhalten, Ausbildung, Beschirrung und Anspannung von Zugrindern, Berlin, p. 154.
Molloy, B. 2008. Martial arts and materiality: a combat archaeology perspective on Aegean swords of the fifteenth and fourteenth centuries BC, World Archaeology, Vol. 40, No. 1, Experimental Archaeology, pp. 116-134.
O'Neill, B., Gilhooly, B. and Cooney, G. 2014. Stone Tools of Shetland: Experimental Felsite Project, EXARC Journal, available at: < https://exarc.net/ark:/88735/10163 > [Accessed date: 3 July, 2022]
O’Neill, B. 2017. Analysis of a Partial Slag Assemblage from Inis Cealtra. Co. Clare, Unpublished Report for Seaver, M. and O' Sullivan, A. (UCD), funded by the Royal Irish Academy (RIA).
O'Sullivan, A. and McCormick, F. 2017. Early medieval Ireland: Investigating social, economic and settlement change, AD 400-1100, In: M. Stanley, R. Swan and A. O'Sullivan (eds). Stories of Ireland's Past: knowledge gained from NRA roads archaeology, Dublin: Transport Infrastructure Ireland, pp.101-132.
Paynter, S. 2006. Regional variation in bloomery smelting slag of the Iron Age and Romano-British periods. Archaeometallurgy 48 (2), pp. 271-292.
Photos-Jones, E. 2008. Analysis of metallurgical waste from Johnstown 1. In: N. Carlin, L. Clarke and F. Walsh, The Archaeology of Life and Death on the Boyne Floodplain: The linear Landscape of the M4, NRA Scheme Monograph 2, Dublin. National Roads Authority, Appendix 6: Part I, CD Excavation Reports.
Pleiner, R. 2000. Iron in Archaeology: The European Bloomery Smelters, Praha: Archeologický ústav AVČR.
Šach, F. 1968. Proposal for the classificaion of pre-industrial tilling implements. In: A. Steensberg, A. Fenton, G. Lerche (Eds.). Tools and Tillage. Vol. I: 1, Gad Publishers Copenhagen, p. 3-27.
Scott, B.G. 1991. Early Irish Ironworking. Belfast: Ulster Museum.
Smith, K.P. 2004. Ore, Fire, Hammer, Sickle: Iron Production in Viking Age and Early Medieval Iceland. In: R. Bork (eds.), De Re Metallica: The Uses of Metal in the Middle Ages, AVISTA Studies in the History of Medieval Technology, Science and Art 4, Ashgate, pp. 183-206.
Stenvik, L.F. 2003. Iron Production in Scandinavian Archaeology. Norwegian Archaeological Review. Vol. 36, No. 2, pp. 119-134.
Taylor, K. 2006. N18 Ennis Bypass and N85 Western Relief Road Site AR128. Cahircalla More, Co. Clare Final Archaeological Excavation Report for Clare County council, Unpublished Report, TVAS Ireland Ltd.
Töngi, V. 2019. Anmerkungen zur (Re)Konstruktion eines mittelalterlichen Hakenpfluges im Freilichtlabor Lauresham. Universität Kassel, Witzenhausen (unpublished).
Wallace, B. 2003. The Norse in Newfoundland: L’Anse aux Meadows and Vinland. Newfoundland Studies, 19(1), pp.5-43.
Wallace, A. and Anguilano, L. 2010. 9.1 Metallurgical report, In P. Stevens and M. O’Droma, M8/N8 Cullahill to Cashel Road Improvements Scheme, Archaeological Resolution, Final Report E2376 Site AR 33, Borris Co, Tipperary, Unpublished report by Valerie J. Keeley Ltd Submitted to Tipperary County Council.