The content is published under a Creative Commons Attribution Non-Commercial 4.0 License.
Reviewed Article:
Hard Fun: Further Discussions on an Undergraduate Project to (Re)Construct and Fire a Medieval Tile Kiln
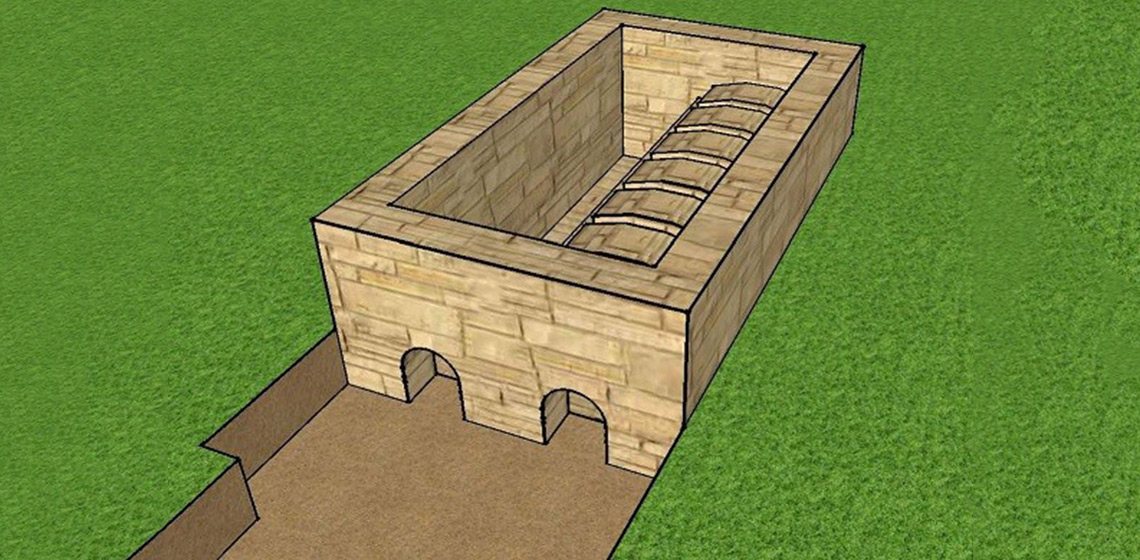
This experiment, undertaken over a 12-month period in 2015 at Norton Priory Museum in Cheshire, formed part of a pedagogic case study and an experimental archaeology project. Here eight Archaeology and 12 Ceramics students from the University of Central Lancashire (UCLAN) researched, built, and fired a tile kiln using evidence from previous experimental archaeology projects on the site and other firing projects. The students undertook this activity because of their own interest in wood-firing kiln technology and in experimental archaeology. The kiln was fired as a public exhibition, and approximately one hundred hand-decorated tiles were fired on the site (Wood, 2013, 2021).
Context
Norton Priory Museum, Cheshire displays the remains of an important Augustinian Priory. A series of excavations revealed the story of the Priory, its growth and development from 1134 to its suppression in 1536 and the subsequent amalgamation into the family home of the Brooke family. From 1970 to 1987 archaeologists worked on the site as a community excavation, hoping to engender a sense of a communal past with the older inhabitants of the town and the newer ones from Liverpool rehoused in the new town development. The project was called âRoots for Runcornâ (Cheshire Life, 1975) and initiated and funded by Runcorn Development Corporation.
Norton Priory has a large and important collection of plain, encaustic, and mosaic tiles from the fourteenth century, which have been excavated from the monastic church and its surroundings, but it was only during the 1972 season of excavations that an associated floor tile kiln was discovered in the north-eastern area of the complex (Greene, 1989). The flues and the lower portions of the kilnâs walls were extremely well preserved and after conservation exhibited in the museumâs galleries.
During the 1977 excavation season, archaeologists worked with students from the University of Liverpoolâs Institute of Extension Studies to design an experimental archaeology project to reconstruct the tile kin. Through a series of successful kiln firings in 1977 and 1978, they explored questions of kiln design and the tile production process (Greene and Johnson, 1978).
Examples of Tile Kilns
John Musty (1974) classified tile kilns, such as the example at Norton Priory, as Type 4b kilns; parallel flue kilns in which âthe whole length of the flue would have been used as a fireplace, the kiln load (floor tiles, roof tiles or bricks) being supported above the flues by arches sprung from the side walls which enclose the fluesâ (1974, p.04). He identified three examples of 4b kilns:
- Meaux Abbey, Yorkshire. In 1925 - 1935 Beaulah and Foote, excavating at the North Grange moated site at Meaux Abbey, found the remains of a tile kiln dated from 1190 -1200. (Eames, 1961). Underneath and around this structure the discovery of mosaic tile wasters suggested that the mosaic tile kiln had been built on the same site and was later demolished to build the larger roof tile kiln.
- Clarendon, Wiltshire. Further excavations in 1937 by Eames (1963) discovered a tile kiln dated 1200. Removed from the site in 1967, it is now on display in the British Museum (Van Geersdaele and Davison, 1975).
- Boston, Lincolnshire. Excavated in 1965, the remains of a coal-fired kiln dated from 1400- 1450 were found with an associated workshop and yard. (Mayes, 1965).
Since the publication of Mustyâs work in 1974, other tile kiln sites have been discovered through various field surveys, watching briefs, and excavation. For example, Denbigh, South Wales (Lewis, 1999), Naish Hill, Wiltshire (McCarthy, 1971) and the Tythings site, Worcester (Lindford, 2003). The discovery and, in some cases, excavation of tile kilns has occurred on other sites of religious houses. Fawcett mentions a very early kiln dated around the 1200âs and discovered in the Cistercian convent at North Berwick by workmen in 1908 (2007). Other examples associated with religious houses include:
- Chertsey Abbey, Surrey. A late 1200 â early 1300âs kiln site was discovered near the south transept of the church. The tiles produced by this kiln formed part of the decorated floor in the Abbey church (Gardner and Eames, 1954).
- Bordesley Abbey, Worcester. Work undertaken during 30 years of excavation and an associated research project indicated that there was a possible industrial area with waster tiles near the Abbey complex (Rahtz and Hurst, 1976).
- Byland Abbey, Yorkshire. In 2011, the remains of a post 1147 AD tile kiln or a dump of kiln wasters were discovered at the Tile House, a former monastic grange associated with the Abbey (Heritage Gateway, 2012).
- Repton Priory. A drawing from the 1866 excavations shows the substantial remains of a kiln built from brick and tile wasters (Lemmen, 2004).
- Tyler Hill, Canterbury. The discovery and excavation of several tile kiln sites dated 1300 â 1400, occurred in 1949, 1961, and 1971. The finds were tentatively associated with the royal abbey at Faversham, but the tiles and their products need further research (Fawcett, 2007).
There are also kilns found within a medieval industrial complex. For example, the Danbury Tile Factory, Essex where excavations from 1972 to 1974 revealed a complex consisting of workshops, drying sheds, possible accommodation for workers, and two well-preserved tile kilns. The production of ridge tiles and plain or decorated floor tiles from this complex occurred from 1275 â 1335 (Dury and Pratt, 1975).
Kiln (Re)Constructions
The Bickley Project is an example of a long-term experimental programme which ran from 1981 to 2010 (Dawson, Kent, Dawson and Kent, 2012). The project explored many aspects of ceramic technology, experimenting with fire boxes, kiln floors, ware chambers and the upper parts of the kiln superstructure. After several years the project moved onto reconstructing different types of kilns using the archaeological evidence from excavations and then onto excavating and recording their archaeology of their own reconstructed kilns.
In 1988 the York Archaeological Trust was restoring the medieval building Barley Hall in York and contacted local potter John Hudson to make tiles for the roof construction (Hudson, 1989). He built and fired a very large wood-fired kiln off-site to produce ceramic roof tiles and roof louvres for the building. Hudson, an ex-ceramics teacher and member of the Medieval Pottery Research Group, also intended to use this as a training exercise for archaeology students and volunteers to understand the process of the technology involved. Whilst the kiln did not fire successfully, due in part to the appalling weather conditions in the wettest summer for many years; the project produced one thousand two hundred tiles of the six thousand needed.
Currently, the Guédelon Castle, France project aims to construct a castle from 1201- 1300 using only original building techniques and materials (Guédelon Castle, 2023). Their tile kiln consists of a brick-built single flue construction whose firings seek to answer technological questions such as the elimination of cold spots, whilst allowing volunteers the experience of making and firing tiles. Guédelon has a very strong educational focus to its work, offering school projects, living history tours, master building courses, and work placements for students over the summer.
Case Study
In choosing Norton Priory Museum as a base for the experiment, it was possible to utilise an extremely large space to construct the tile kiln and its associated working area. Building a large kiln needs storage space for the building materials, tiles, woodpile, and clay pits, plus camping and living spaces for the volunteers. This was not available on campus, and it was fortunate that Norton Priory recognised the experimental and pedagogic aspects of the project and welcomed the students onto the site.
Deciding to repeat the experiments also offered the students the very rare opportunity to re-examine the archaeological evidence available on the same site. This allowed them to develop two research questions based on their interpretation of the physical evidence preserved in the museum, and the available reports on the original firings by Green and Johnson (1978). Their chosen questions related to the physical aspects of the build and thermal properties of their chosen building material:
- Would they be able to design and build a kiln that was based on archaeological evidence and research from other projects such as the Bickley Experiment?
- Would their structure, created from only water, sand, straw and clay, function reliably enough to stand firing to 1000 degrees Centigrade?
As well as the important research aspects, the pedagogic benefits were enormous. This group of ceramicists and archaeologists shared a common interest in ceramics and the technology of wood firing. The ceramicists had practical experience of making pots and firing them in a gas kiln, whilst the archaeologists had no ceramics experience, but they did have skills in interpreting archaeological evidence and good field-work techniques. Experimental archaeology has a considerable aptitude for encouraging multi-disciplinary working within student groups as different groups of people share their different skills and knowledge. This is a key employability skill, along with communication, problem solving, and critical thinking.
Data gathering
The students volunteered purely for the experience of doing this experiment as all the work happened outside the formal university curriculum. Instead of a formal assessment to record their learning, an open, shared, and optional diary was available in which the students could comment on the day-to-day running of the project and reflect on their personal experiences. Everyone was told that their comments may appear in a publication or article in an anonymous form and that copies of the diary would be made available to anyone who asked to see them.
Kiln Design
The major discussions centred on designs for the kiln. The floor plan for the kiln was evident from the actual kiln preserved in the museum, and the students produced a scale drawing of the kiln to give a guideline about the dimensions of the kiln. However, there were no parts of the structure existing above the initial 0.5 metres, which had been preserved, so there were three major problems that were evident for the experimental (re)construction. Firstly, the possible design of the roof or the chimney for the kiln , secondly, the internal design of the floor for the firing chamber and thirdly the possibility of having to build a more complex firing chamber firing but this proved erroneous, and they were advised by John Hudson that this was unnecessary.
The initial designs for the kiln included a two-story (re)construction as suggested by excavators at Meaux (See Figure 1). The students thought there should be an additional firing chamber as there would be huge amounts of ash produced during a wood -fuelled burn and the regular removal of this ash would ensure that the airflow through the kiln was clear. Further examination of photographs from the early stages of the Norton Priory firings also showed an initial two-story (re)construction of a beehive shape, which the experimenters felt was necessary to draw more air into the firing chamber and to aid the circulation of the hot gases stopping cold spots developing in the firing chamber.
A search of relevant literature suggested that the kilns were roofed, and there was some discussion about using a domed construction. However, work at Bickley ( Dawson and Kent, 1984) showed that this is not necessary, and indeed Green and Johnson (1978) did not use a roof on their second experiment, merely a layer of waster tiles laid directly onto the tiles stacked in the firing chamber. After further consultation, the students chose to use a thin and temporary layer of waster tiles (in this case, old roofing tiles), sufficient to allow hot gases to escape and to allow for the flow of oxygen. They decided that this would be beneficial when loading and unloading the firing chambers as the structure would remain undamaged. Rebuilding a roof after each firing would have slowed down the commercial production of tiles by the original tile makers.
However, after further research the group changed their design to a simple one-storey structure which would be easier to build, load and fire. This structure measured approximately 1.90 metres long by approximately 1.70 meters wide with the height at the front of the kiln 1.50 metres from the stoking pit. The other three walls were raised to a height of 1 metre above the ground. The walls were between 30 â 40 centimetres thick. The design is shown in Figure 2.
Firing chambers
Greene and Johnson (1978) had written that during the excavations of the original kiln at Norton Priory that there was some possible indication on the original structure that clay fire bars had been used to create a perforated floor for the firing chamber. In their (re)construction, he and Johnson had built the clay fire bars initially supported on arched, wooden forms that would burn out during an initial firing in the unloaded kiln. However, in their experiment it might have been easier to create these arches as their kiln seemed to be smaller than our reconstructed kiln.
Ultimately, the students did not have the wood working skills to make these wooden forms and were concerned that any poor construction of these frames would run the risk of blocking the airflow if they failed to burn out completely. Other ceramicists at UCLAN suggested that we could use metal firing bars or a metal grate, but this had been discounted by Dawson and Kent, âany transference of this technology to ceramics before any post-medieval period has not been possible to demonstrate â(1984, p.13).
Instead, the students chose to use cut hazel withies then twisted them into thick rods ( average diameter 20 centimetres) and inserted these rods into the soft cob of the inner walls of the stoking chambers and the central spine. These bundles were covered in a very thick layer of cob to protect them for the heat of the firing. This formed twelve small, arched fire bars, six covering each of the two flues, with the spaces between each bar ranging from approximately 15 centimetres to approximately 20 centimetres which allowed hot gases to circulate into the firing chambers. However, although having tried to resolve a skills issue with ingenuity, they created an issue with stacking the kiln as the fire bars were quite uneven therefore, the tiles could only be stacked on one layer.
(Re)Construction of the kiln from cob
The kiln was built up slowly over a period of two hot and dry weeks in May using the same floor plan as that of the original kiln. This procedure was hard work, as three tonnes of West Yorkshire extruded clay needed to be softened by mixing with cold water, straw, and yellow sand. Then it was rigorously puddled (trodden with bare feet) until it was pliable and soft enough for use in the (re)construction. This material produces cob, an ancient building material that is both cheap and extremely durable. Originally, it would have been puddled by animals rather than humans to produce the large amounts needed for the kilns. The original kiln was built of the cob mixture, with additional stones and waster tiles added, but subsequent experiments had used a mostly clay mixture provided from the medieval clay pits (now buried under the museumâs car parks).
Prepared cob, when dry, is very hard, but it cannot be soaked and needs protection from rain and frost. Modern houses today with cob walls need to have overhanging eaves to channel rainwater away, and it is likely that a kiln made from cob also had a temporary roof to do this. This is perhaps another indicator that tile production was summer activity as suggested by La Patourel (1968) and Stopford (1993). It would be easier to build the kilns and to harden off wet tiles in the sun or in nearby sheds or shelters near the kilns.
The students experimented with the cob, such as soaking the clay for longer, varying the sand and straw mixtures, and even for a short while, using a cement mixer (which proved to be messy and clogged up with clay very easily) so that they could understand the properties of the material itself. After building, the kiln required a period of two months to dry out and during this time, it was covered with a temporary tarpaulin roof.
Making tiles
The students had made two hundred tiles in the universityâs ceramic laboratory where they decorated them with slip and then biscuit fired them in a modern kiln at the university. This ensured that the tiles were less fragile and were hard enough for transportation to the museum site.
Firing the kiln
As part of the Health and Safety arrangements between the museum and the university, a person who had extensive experience of the process would fire the kiln. John Hudson, a potter and experimental ceramicist, came to dry out the kiln and fire the kiln. Initially he lit four small fires before the main firing, to warm the cob and dry it out and then fired the kiln with its full load of tiles later that weekend.
His own (re)constructed kiln at York (Hudson, 1989) was made entirely of modern bricks. John had some concern that our large kiln, built entirely of cob, would not be able to withstand the heat of the firing over such a long period, and he suggested that the kiln would either collapse or explode. At hearing this, the students were not despondent but rather thrilled at the potential drama.
The firing used approximately three tons of dry and seasoned wood taken from the Priory grounds over several years. The wood was from a range of deciduous trees such as birch, beech and sycamore, cut into very long lengths, approximately three metres to four metres in length and from a variety of diameters, approximately 10 to 40 centimetres. The wood burned efficiently to a very fine ash, and at no point did the stoking chamber need clearing of the accumulated ash (See Figure 3).
A single layer of 100 tiles was packed: some edge to edge, others stacked vertically against them, forming a hollow cube. This haphazard arrangement was due to the uneven floor of the kilnâs firing chamber but allowed for the maximum possible air movement between them. Laid on top of these tiles was a single layer of modern, clay roof tiles which formed a roof over the firing chamber.
In each of the quadrants A, B, C and D four pyrometers were placed diagonally under the roof tile layer that formed a temporary roof, protruding at least 30 centimetres into the firing chamber (See Figure 4). The students took readings at 11.35 and then at thirty-minute intervals until 22.00 ( see figure 5).
This firing took place at 11.35 on a warm, dry, and windless morning in July. This lasted for eleven hours until one of the four pyrometers had established that the temperature was at 954 degrees Centigrade at 21.30. However, it was not possible to increase the temperature beyond this point because the design of the firing chamber floor impeded the flow of gases around the kiln interior. At 21.30, stoking stopped, the entrance was blocked with old modern roof tiles, and the kiln fires were allowed to burn out.
Unloading the kiln
At 10.00 the following day, the kiln had cooled enough to be unloaded. After removing the layer of modern roof tiles, the fired tiles were unstacked from each quadrant. The tiles were still hot enough that protective gloves were needed in order to remove them from the kiln safely (See Figure 5).
Results
Opening the kiln revealed a collection of partially fired tiles, but from the glaze and the body of the tiles, the students and Mr Hudson decided that we had failed to reach the correct temperature of 1000 degrees Centigrade. The tiles were brittle with much blistering of the glazed surfaces.
The kiln structure had survived the firing very well, with only one design fault that had impeded it in maintaining the anticipated temperature of 1000 degrees Centigrade. Overall, the fire bars had survived surprisingly well; the thick coating of cob had fired and protected their woody interior. However, in quadrant B the fire bars with their uneven widths and irregular shapes, had collapsed and dumped their load of tiles into the flues. Ironically, these tiles had fired very well.
The interior of the kiln showed minor cracks in the walls, but these did not threaten the solidity of the structure and they could easily have been repaired with fresh cob before the next firing. After unloading quadrant C of the kiln, blackening was evident on the internal walls. During the firing the students had observed black smoke and yellow flames being emitted from this quadrant. This blackening showed that reduction had occurred during the firing, as the design of the fire bars had impeded the circulation of hot gases.
Through this experiment, the students planned to repair the kiln, make changes to the initial design, especially in the manufacture of the fire bars, and fire it again, hoping to reach and maintain the magical temperature of 1000 degrees Centigrade. However, due to the constraints of the studentsâ timetables and the damage by vandals that the kiln sustained over the winter months, it was not practical to attempt a second firing, and the kiln was eventually demolished by the Priory.
Discussions
This experiment was not all about teaching archaeology but rather about teaching through the medium of archaeology as students, through their own experiences, actively discovered new knowledge and formulated new ideas. They learned from each other by sharing, discussing, challenging and then reflecting upon this new understanding. Some comments from the groupâs diary comment on this metacognitive process,
âI think we did well. We overcame problems and learned a lot. If the learning is left unfinished without a firing...then a lot of answers will be left if the kiln cannot be used. You maybe need to have a build that doesnât work so you know what not to do.â (Anon., 2015).
A key factor was the development of understanding and skills through practical experience in the real world. An experimental archaeological project should âtest out hypotheses using potentially authentic materials and conditionsâ (Outram, 2008, p. 02). It was much more fun and valuable to do this experiment in real-life conditions within the constraints of the technology available or even with the factors imposed by working in the outside environment. Outram calls these experiments âactualisticâ experiments allowing the researchers to develop their skills by coping with these non-laboratory experiences.
In this project each group, the ceramicists and the archaeologists brought different skills, understanding and knowledge to the project. The ceramicists knew about pottery manufacture and different firing techniques, but they had no opportunities to work with wood-burning kilns. This project enabled them to experience and understand the techniques involved, such as loading the structure and the skilful art of firing it to reach a temperature of 1000 degrees Centigrade. For the archaeologists their main contact with pottery was with the sherds that they find on excavations. Here was a chance to try making pots, learn about kiln technology and recognise the processes of reduction and oxygenation.
The following comments from the group diary show the studentsâ increasing confidence in their own practical skills and other skills such as working together, negotiating ideas, problem-solving and efficacy,
âDay Three and the group work really well together. So far lots of excellent problem-solving ideas to combat many of the problems that have arisen from every aspect of this build. We have limited knowledge of how medieval people built their kilns...so we have to be very creative in our approach to cob making.â (Anon., 2015).
There was an appreciation of the sheer manual labour that was required in the process of making cob and building a structure from it, and the actual discovery of the joy in doing this. In her reflections one student commented,
âlooking back, I canât believe that I have the energy to do that much stamping and lifting for a week... Itâs all down to the team mentality and our determination to get it finished.â
Research was a key factor in the project as all the students undertook some aspect of researching the design and build of the kiln. Students usually start on their dissertations in their third years of study as it felt that it is only then that they have the skills to undertake research. In this experiment they were developing the research skills that they would need: those of observation, finding and analysing information, and critical thinking,
âI went into this project wanting to do a full archaeological (re)construction and to do experimental archaeology with a wood firing being a bonus, I would like to finish the experiment and draw some conclusions.â (Anon., 2015).
Two students used this research on the kiln and the details of the experiment within their academic work; one as a credit-bearing module assessment and one who wanted to continue onto a competitive post-graduate course. She recognised the importance of having an article referenced on her CV and published a short article in UCLANâs student journal, Diffusion (Tyrer, 2009). Two other students also went along to a Lancashire Archaeological Society (a charitable group) which had generously given some funding for the experiment and gave an illustrated talk to the Societyâs members.
Conclusions
This experimental archaeology project offered an opportunity to link teaching and research effectively through an actualistic, non-laboratory experiment that was designed and undertaken by the students. My pedagogic objective was the enhancement of their employability skills in fieldwork practice and their understanding of their own disciplines.
The students developed their cognitive, and metacognitive skills and their personal self- efficacy by working with the constraints of the technology available and with the factors imposed by working in the outside environment. Yet this project also impacted on the affective domain of emotional attitudes with friendships made, having fun, and being challenged in a supportive learning environment.
This was also a reconstruction of an industrial setting which needed space to build the structure, the pits to soak and prepare the clay , shelters in which to make and dry the tiles and storage of all the material required. This project helped the students to appreciate not only the physical efforts of the original kiln builders and tile makers and the different skillsets required, but the efficient organisation and management of processes and working areas.
Projects such as these can be time-consuming and need to be carefully introduced to the students and supported by scaffolding techniques such as encouraging open discussions and tapping into the studentsâ prior knowledge. It should also be noted that not all students may wish to be involved to such a depth in a project and alternative assignments should be available for those who do not wish to participate. However, as this type of experiment shows, they can be impactful, challenging, and encourage a degree of personal reflection from all the participants.
Acknowledgements
Thanks are due to UCLAN for the funding awarded from the Harris Bursary Awards, the support and advice of the staff at Norton Priory Museum, the UCLAN students who took part, Mr John Hudson, Mr Brent Platt and Lancashire Archaeological Society for their generous donation.
Keywords
Country
- United Kingdom
Bibliography
Anonymised Norton Priory Kiln Project Diary, 2015. Studentsâ Comments on the Project. Unpublished.
Cheshire County Life. 1975. Roots for Runcorn, Cheshire County Life, May, pp. 54- 56.
Dawson, D., & Kent, O. 1984 . Kiln Superstructures. In: A. Woods, Ed. , Bulletin of the Experimental Firing Group, 2, 13. Leicester. Leicester University.
Dawson, D., Kent, O., Dawson, V. & Kent, H. 2012 . The Bickley Book. The Bickley Ceramics Project 1981 â 200. Bristol: The Bickley Ceramics Project.
Dury, P. J. and Pratt, G.D. 1975 . A Later 13th Century and Early 14th Century Tile Factory at Danbury, Essex, Medieval Archaeology, pp.92 - 164.
Eames, E.S. 1961 . âA Thirteenth-century Tile Kiln Site at North Grange, Meaux, Beverley, Yorkshireâ, Medieval Archaeology, pp.137-168.
Eames, E. S. 1963 . âA 13th Century Tiled Pavement from the Kingsâ Chapel, Clarendon Palace.â Journal of British Archaeological Associations, 26 1963 , pp. 40 â 50.
Fawcett, J., 2007 . Historic Floors: Their Care and Conservation. Oxford: Butterworth and Heinemann.
Gardner, J.S. and Eames. E. 1954 . âA Tile Kiln at Chertsey Abbey.â Journal of British Archaeology, xvii, pp.24 -42.
Greene, J.P. 1989 . Norton Priory. The Archaeology of a Medieval Religious House. Cambridge: Cambridge Press.
Greene, J.P. and Johnson, B. 1978 . âAn Experimental Kiln at Norton Priory,â Medieval Ceramics, pp. 30 â 42.
Guédelon Castle 2023 . Visiting with Family or Friends: The 21st Century Medieval Adventure. Available at: < https://archaeology-travel.com/france/guedelon > [Accessed 23 February 2023].
Heritage Gateway 2012 . Historic England Research Records â Byland. Available at < https://www.heritagegateway.org.uk/Gateway/Results_Single.aspx?uid=f65e⊠> [Accessed 23 February 2023].
Hudson, J. 1989 . âThe York Medieval Tile-Making Experiment â A Potter's Tale'. Medieval Ceramics 13, pp. 43 â 51.
Le Patourel, E.J. 1968 . Documentary Evidence and the Medieval Pottery Industry. Medieval Archaeology, 12, pp.16 â21.
Lemmen, H. 2004 . Medieval Tiles. Buckinghamshire: Shire Publications.
Lewis, J.M. 1999 . Denbigh Kins. The Medieval Tiles of Wales. Cardiff. National Museum of Wales.
Lindford, P. 2003 . 9-10 The Tythings Kiln: Worcester, Archaeomagnetic Dating Report. Available at < https://ArchaeomagneticDatingReport2003%20 1 .pdf >
Musty, J. 1974 . Medieval Pottery Kilns. In Evison, V.I., Hodges, H. and Hurst, J.G. Eds. , Medieval Pottery from Excavations. Studies Presented to Gerald Clough Dunning, pp.41 â 65. John Baker: London.
McCarthy, M. R. 1971 . âThe Naish Hill Kilns: An Interim Report.â Wiltshire Archaeology and Natural History Magazine, LXVI, pp.179 - 181.
Mayes, P. A. 1965 . A Medieval Tile Kiln at Boston. Journal of the Archaeological Association, 28.1, pp. 86-106.
Outram, A. K. 2008 . Introduction to Experimental Archaeology. World Archaeology, 40 1 , 1-6. Doi: 10.1080/00438240801889456
Rahtz, P. A. and Hirst. S.M, 1976 . Bordesley Abbey, Redditch, Hereford-Worcestershire. First report on excavations 1969â1973, Oxford: British Archaeological Reports 23, 19.
Stopforth, J., 2000 . Monastic Industry at Wethercote, Bilsdale West Side. Yorkshire Archaeological Journal, 72, pp.41- 53.
Tyrer, S., 2009 .âThe Norton Priory Medieval Tile Kiln Projectâ. Diffusion, 1, pp. 101 -104.
Van Geersdaele, P. C. and Davison, S. 1975 . The Thirteenth-Century Tile-Kiln from Clarendon Place: Itâs Removal and Reconstruction for Exhibition. Studies in Conservation, 20:3, pp.158-168.
Wood, G. 2013 . Letâs Build a Medieval Tile Kiln. Introducing Experimental Archaeology into the Archaeological Curriculum. EXARC Journal. < https://exarc.net/ark:/88735/10108 > [Accessed 23 February 2023].
Wood, G. 2021. From Outside to Inside. Evaluating Employability and Enterprise Through Experimental Archaeology. Ph.D. University of Central Lancashire.