The content is published under a Creative Commons Attribution Non-Commercial 4.0 License.
Reviewed Article:
The Production of Roman Metal Screw Threads
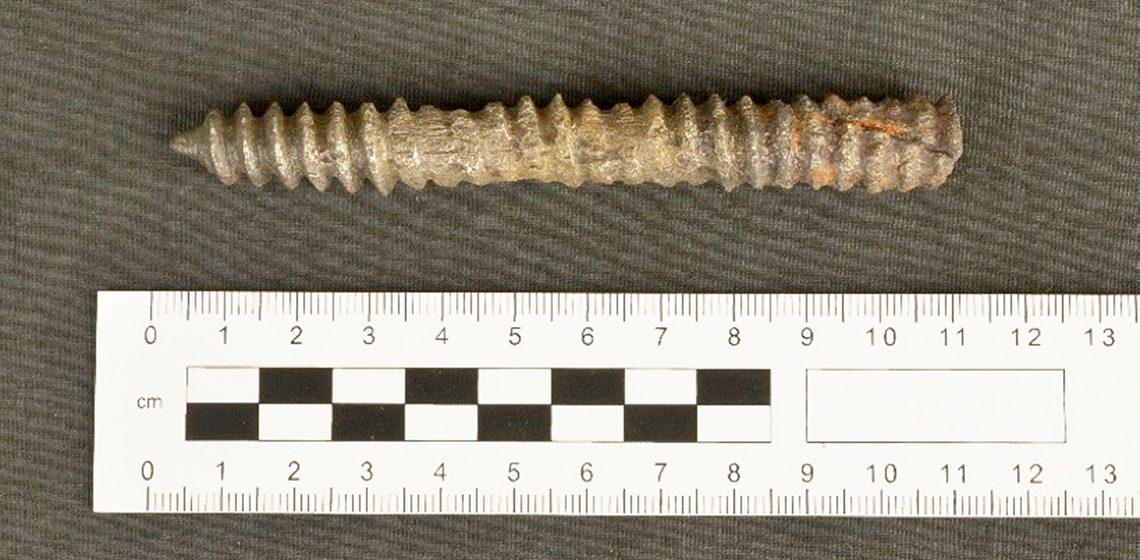
The production of Roman screws and screw threads is a topic that is largely absent in the archaeological literature. During the Roman period, small metal screw threads were used both as fastenings and to impart motion. This paper will show that it is possible to produce small metal screw threads using very simple technology that was well within the skill set of any competent metal worker. Using experimental techniques showed that small metal screw threads can be produced by semi- and unskilled labour in a timeframe that makes their production economically viable. Low visibility in the archaeological record has led to the erroneous assumption that the Romans did not use small metal screw threads.
Metal Screw Threads In Antiquity
During the Roman period, small metal screw threads were used both as fastenings and to impart motion (Burstall, 1970, p.77; Singer, et al., 1972, pp.631–632). Screw threads as fastenings can be seen in some jewellery and screw threads to impart motion can be seen in olive presses. These screw threads could have either a square or V-shaped profile. In the Roman period screw threads were made of wood, iron, bronze, gold and silver, however this paper focuses on the production of metal screw threads, with experiments utilising both brass and copper.
Screw threads can be classified into two distinct types: motion screws and fastening screws. Motion screws are used for the transmission of mechanical power.1 In contrast, fastening screws are designed to unite two or more components.
Motion Screw Threads
In the Roman period, motion screws were used for a variety of purposes, including presses. These include direct vertical screw-operated presses, where a screw thread is incorporated into the screw and lever press. Another application of the screw thread is for raising water with an Archimedean screw.2 However, there are examples of small metal threads being used to impart motion; these can be found on Roman surgical instruments, such as the vaginal speculum (See Figure 1).
Fastening Screw Threads
Fastening threads come in two forms: male (bolt) and female (nut) threads. These threads can be left or right-handed. A right-handed thread is tightened by turning clockwise, and a left-handed thread anti-clockwise.
In construction made from metal and wood, there are two kinds of fastenings, permanent and semi-permanent. Nails and rivets are permanent fastenings that are not designed to be undone, whereas screw threads are semi-permanent joints, in that they can be removed.
Thread Forms In The Roman Period
In the Roman period, there were two principal thread forms: square and v-thread.
Square Form Threads
Roman Square Form Fastening Threads
Small square threads are widely used in jewellery. Examples include a filed thread of the screw bolt of a crossbow fibula found at Richborough, Kent (British Museum; Bushe-Fox, 1928). Also in the British Museum, there is a gold screw belonging to a crossbow fibula from the Moray Firth, Scotland (Accession number 1962.12-15.1). A square thread, with a length of 25.4 mm with a diameter of 3 mm from the Eastern part of the Empire, is held at the J. Paul Getty Museum, Malibu, USA (Accession number E1)
Roman Square Form Motion Threads
Square form motion threads are seen in medical instruments such as the speculum in Figure 1.
The Archimedean screw is an application of the screw thread for raising water. This usually utilises a square-form thread.3
V-Form Threads
Roman V-Form Fastening Threads
Fastening threads with a ‘V’ form were known in the Roman period, as seen in the travelling lamp holder in Figure 2. This was found during excavations in Herculaneum, giving a terminus ante quem of AD 79. The shaft comprises four cylinders joined together with male V-form screw threads. When the shaft was assembled, it was held in place by a fifth screw joining the shaft to the base (Roberts, 2013, p.120).
Further examples of portable lampstands with V-threads can be found at the British Museum. For instance, lampstand Q3929 has V-threads on each end. The top thread screws into a female thread on the top section of the lamp. The bottom thread screws into a female thread on the three-legged base (Bailey, 1996, plate 139). This indicates that the lamp was meant to be disassembled, possibly for transportation. Another similar example from the British Museum (Q3928) has a length of 45 mm and a diameter of 3 mm.
Trieste Museum (inv. 619) holds another example with a top cylinder comprising a right-handed cylindrical screw that engages with a female threaded screw in the dip tray. The lower screw seems to have passed through the base and was attached, possibly by some form of nut that is now missing (Bravar, 1974, Figure 2).
Roman V-Form Motion Threads
V-form threads are most seen in direct vertical screw-operated presses such as those for wine4 and oil. (Drachmann, 1932; Gichon, 1979). A screw thread is incorporated in the screw and lever press (Pliny, Natural History 18: lxxiv. 317; Patton and Myres, 1898). These threads were generally made of wood.
Experiments
Replicating A Roman V-Form Wood Screw
Figure 3 shows an incomplete Roman iron wood screw thread found at Silchester, Hampshire, measuring 157 mm and weighing 64 g; the thread lacks the head. The average outside diameter of the complete thread is 13 mm (See Table 1). It retains 23 convolutions and a cone-shaped tip (1.5 convolutions [threads] per cm; the average thread angle is 68º). The cone-shaped geometry, in conjunction with the discovery of the thread in wood, indicates that this was a wood screw. The nature of the missing fragment is a matter of conjecture, but it is suggested that a head was used to turn the screw into the wood. It is, therefore, unclear how long the screw was originally and how it was screwed into the wood.
Average diameter | Variation from mean diameter | Range | ||
Outside diameter | 13.04 | +0.04 | -2.04 | 2.08 |
Core diameter | 9.46 | +2.54 | -1.46 | 4.00 |
Thread pitch5 | 4.18 | +1.22 | -0.68 | 1.90 |
Table 1: Measurements of the Silchester wood screw (in mm).
The pitch of a thread is the distance from a point on a screw thread to a corresponding point on the next thread.
The thread remains intact on both ends of the screw fragment; however, the centre section shows considerable wear. The centre section of 44 mm shows considerable mechanical abrasion along one part of the circumference (see Figure 4).
The unusual wear pattern suggests a reciprocating motion rather than a rotary one. This wear pattern could be the result of repeated lifting and falling, such as could be found on a latch. If this were the case, it would mean that such threads were not considered expensive items and were there for easily available. To test this proposition, it was decided to make a replica to determine the time taken to produce this type of thread (See Figure 5)
A. The bar is roughly forged into a cylinder.
B. The bar is forged into an accurate cylinder between swages.
C. A taper is forged on one end of the bar.
D. The thread is cut using a file.
Results
Stages of manufacture | Time (minutes) |
Forging time [stages A + B + C] | 9 |
Production time to cut 24 threads | 96 |
Total production time | 105 |
Table 2: Production times for one person working alone.
The timings shown in Table 2 can be reduced. The forging time can be reduced to four minutes if several bars are worked in rotation. Furthermore, it is possible to reduce the time taken by training semi-skilled labour to perform the task of thread making.
An unskilled person was trained to cut threads by hand in under three hours. At the end of that time, they could work unsupervised and, within a day, could produce a screw thread of the same dimensions as the Silchester thread in one hour. A workforce devoted exclusively to forging and cutting threads can therefore be made up of semi-skilled labour.
Assuming a working day of 12 hours, each worker can produce 12 screws of the Silchester type in a day. Assuming a working week of six days, a single worker could produce a maximum of 72 threads per week. A workforce of twenty could produce 1440 a week.
If the labour force is trained to perform this task alone, the cost will be low, compared to the cost if carried out by skilled craftsmen, making it a viable option.
These experiments have shown that screw threads such as the one found at Silchester could potentially be produced in large quantities by unskilled labour, thereby making their use economical.
Accuracy of male thread
As seen in Figure 1, the male thread engages with a pin set in a housing; as the screw is turned, it causes the jaws of the speculum to open.
As long as the jaws open smoothly, any small inaccuracies in the pitch of the thread will have little consequence. The manufacturing methods used to make square threads are covered later in this article.
Other devices that incorporate screw threads can be found in Hero’s Dioptra6 (Coulton, 2002).
Manufacturing methods to produce screw threads
The following experiments were conducted to consider methods of manufacture that could have been used to make screw threads of Roman type. These experiments will consider the production of two different types of screw thread – square threads and V-threads. In antiquity, screw threads were probably made by one of the following methods.
- Metal removal. Cutting the thread into the outside of a bar and cutting the female thread into a hole in a piece of metal that will become the nut.
- Fabrication. Threads can also be made by making the thread separately from the core and then soldering it in place.
- Lost wax casting. This is a well-established method of producing accurate castings (Craddock and Hockey, 1986). However, this avenue has not been explored in this paper as the recreation of the lost wax methods employed in the Roman period is prohibitively expensive.
Experiments to reproduce screw threads
In this set of experiments, only tools and equipment known to have existed in the Roman period were used. They were an anvil, tongs, hammer, files, abrasive fine sand, silver solder and borax, and charcoal as fuel (See Figure 6).
Producing A Thread Free Hand
Cutting a V-thread freehand
Total time to produce a 60 mm long, 10 mm diameter V-thread with an average pitch of 8.28 mm + 0.40 -0.19 was: 1 hour 45 minutes. It can be seen from Figure 7 that visually, there is very little difference between a handmade thread, and one produced with a modern die. Therefore, it is conceivable, that threads from the Roman period likely have been misidentified as modern manufacture.
Fabrication Method
Fabricated square thread
Small screw threads like those found on jewellery can be made by fabrication. This involves making wire, wrapping it around a cylindrical shaft, and then soldering it in place with hard solder.
Experiment No.1 Solder square wire onto a bar
A single piece of wire 1.62 mm was wound around the copper bar to form a coil (See Figure 8). A piece of copper wire was drawn through a draw plate with square holes in it (see Sim, 1997).
The coil was pried open with a small tapered copper lever. Copper was used so as not to damage the coil, they being made from the same metal. The pitch of the coil was gauged using a spare piece of wire the same thickness as the coil wire. The coil was then hard-soldered to the copper rod (See Figure 8, 9, 10 and 11).
Making brass square threads
The next set of experiments were used to determine the times taken to make the threads and the two alternatives to producing the wire.
Measurements
A | B | C | D | E | F | Maximum variation | |
Pitch (mm) | 4.02 | 3.90 | 4.05 | 4.42 | 3.89 | 4.00 | 0.13 |
Table 3: Variations in pitch
This set of experiments were conducted on copper wire as the use of gold or silver in experiments is prohibitively expensive.
This is because copper has similar working properties to gold which was commonly used in Roman Jewellery. The next set of experiments was to determine how easy it is to make square threads from brass.
Experiment No.2 Fabricating square threads from brass
To ensure the threads have a consistent pitch, a jig was made, as can be seen in Figures 12-14.
There is a much more straightforward method of ensuring that the pitch of the coil is even. A wood rod has a nail driven into it that is the same diameter as the pitch required, and the coil is twisted on the rod and pushed past the nail. This is a very simple and cheap method of ensuring even and equal pitches on the coil.
A length of brass wire was drawn down into a cross-section of 1.62 mm, the same as in previous experiments. It was wrapped around a mandrill to form a coil. This was twisted over the jig producing a coil with even spaces. As can be seen in Figure 14.
The total production time for this thread was 14 minutes 11 seconds.
Conclusions
The use of screw threads for imparting motion and fastening was known and used in the Roman period. Roman screw threads could have square and V-shaped profiles. Such threads can be made using various techniques, including metal removal, fabrication, and casting.
Although screw threads appear complicated, they are comparatively easy to produce and, through the use of simple jigs, can be produced by unskilled labour. This reduces time and costs. They can be made in large quantities enabling them to be cost-effective.
Roman V-shaped screw threads are almost identical to modern threads.
It is highly likely that many Roman screw threads have been found on archaeological excavations, but because of their appearance they have been mistaken for modern threads and have been discarded.
- 1
The invention of the screw thread is traditionally attributed to Archytas of Tarentum (c 400 BC).
- 2For Archimedean screws see Vitruvius, The ten books on architecture, 10.6.1; Landels, 1978, pp.58–64; Schürmann, 1995, pp.56–61. Although Archimedes’ (c. 287–c. 212 BC) name is indelibly associated with the device he may have simply described a long-established device (Singer, et al., 1957, pp.676–7; Paipetis and Ceccarelli, 2010). It is possible that Archimedes saw water-screws in use when The travelled in Egypt.
- 3For Archimedean screws see Vitruvius, The ten books on architecture, 10.6.1; Landels, 1978, pp.58–64; Schürmann, 1995, pp.56–61. Although Archimedes’ (c. 287–c. 212 BC) name is indelibly associated with the device he may have simply described a long-established device (Singer, et al., 1957, pp.676–7; Paipetis and Ceccarelli, 2010). It is possible that Archimedes saw water-screws in use when he travelled in Egypt.
- 4For wine presses see Schürmann, 1995, pp.64–7; Vitruvius, The ten books on architecture, 6.6.1.
- 5Pitch is the distance from the crest of one there to the crest of the next thread.
- 6A Dioptra is a surveying instrument used by the Romans in road building and other applications.
Country
- Italy
Bibliography
Bailey, D. M., 1996. A catalogue of lamps in the British Museum. London: British Museum Press.
Bravar, G., 1974. Un candelabro bronzo nelle raccolte civiche di Trieste. In: Atti del III Congresso Nazionale di Archaeologia Cristiana. Antichita Altoadriatiches VI. Trieste, LINT, pp.255–65.
Burstall, A. F., 1970. A history of mechanical engineering. London: Faber and Faber.
Bushe-Fox, J. P., 1928. Second report on the excavation of the Roman fort at Richborough, Kent, London: Society of Antiquaries.
Coulton, J. J., 2002. The Dioptra of Hero of Alexandria. In: C. J. Tuplin and T. E. Rihll, eds. Science and Mathematics in Ancient Greek Culture. Oxford: Oxford University Press.
Craddock, P. T. and Hockey, M. I., 1986, Technical examination and analysis. In: J. Swaddling, ed. Italian Iron Age artefacts in the British Museum. London, British Museum Press, pp.88–98
Craddock, P. T., 2019. The screw threads of antiquity: To raise, to adjust, to measure, to press, and hold, Mouseion 16:2, pp.177–190.
Drachmann, A. G., 1932. Ancient oil mills and presses. Copenhagen: Levin: Munksgaard.
Gichon, M., 1979. The upright screw-operated pillar press in Israel, Scripta Classica Israelica 5, pp.206–244.
Landels, J. G., 1978. Engineering in the ancient world. London: Chato & Windus.
Paipetis, S. A. and Ceccarelli, M., 2010. The Genius of Archimedes – 23 centuries of influence on mathematics, science and engineering; Proceedings of an Internal Conference held at Syracuse, Italy, June 8-10, 2010; Dordrecht: Springer.
Patton, W. R. and Myres, J. L., 1898. On some Karian and Hellenic oil-presses, Journal of Hellenic Studies 18, pp.207–17.
Pliny, 2000. Natural History. Translated by W.H.S. Jones. London: Harvard University Press.
Schürmann, A., 1995. Die überlieferung antiker autoren. In: D. Planck, ed. Die schraube zwischen macht und pracht: Das gewinde in der antike, Jan Thorbecke: Sigmaringen, pp.55–76.
Sim, D. N.,1997. Roman chain-mail: Experiments to reproduce the techniques of manufacture. Britannia 28, pp.359–371.
Singer, C., Holmyard, E. J., Hall, A. R. and Williams, T. I.,1972. A history of technology: The Mediterranean civilisations and the Middle Ages. Volume 2. Oxford: Clarendon Press.
Vitruvius,, 1998. The Ten books on Architecture. Translated by M.H. Morgan. Dover publications Inc