The content is published under a Creative Commons Attribution Non-Commercial 4.0 License.
Reviewed Article:
“Look at the Bones!” - Adding Bone in a Bloomery Iron Smelt
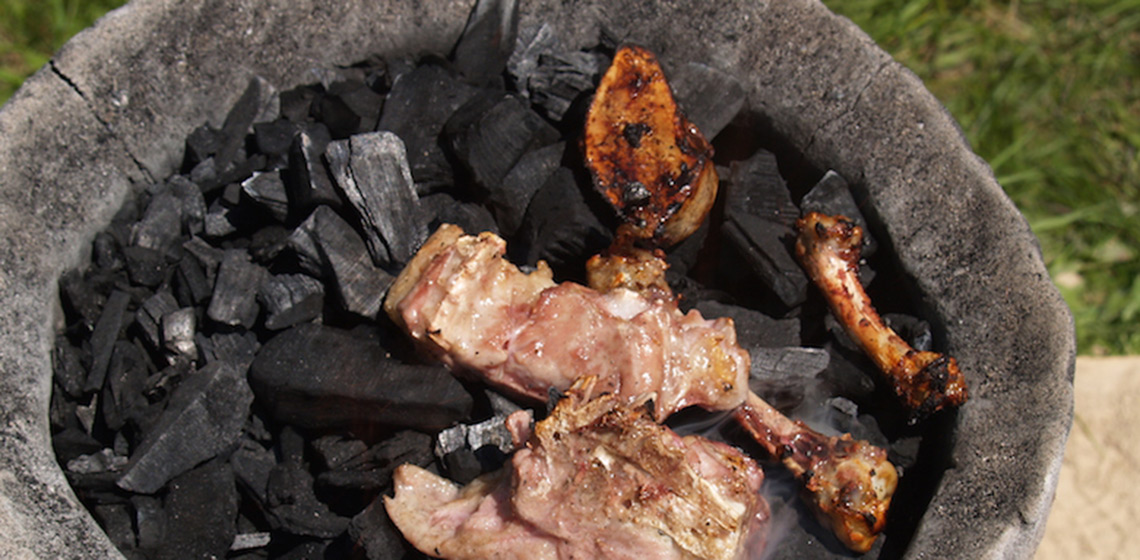
A case study of a practical experimental test. Through 2019, much was made in the popular press suggesting that during the Viking Age, exhumed human bone had been used in the chain of production from iron ore through to finished swords. Contradicting this, considerable experience with small scale direct reduction process bloomery iron smelting furnaces indicated that at least while creating the iron itself, the effect of adding bone would be minimal, if any. To establish what kind of physical traces that might remain if quantities of bone were added during smelting, in June 2020 a full furnace build and firing was undertaken, with a range of animal bones added, then the resulting debris field recorded. The concept, design and implementation of this experiment is discussed, and how limits on methods, instrumentation and analysing results shaped the final conclusions. This discussion suggests how even a simple experiment, if carefully recorded, can add to the body of available knowledge, and may prove insightful to both educators and other investigators.
...
He’s got huge, sharp… er… He can leap about. Look at the bones!”
Tim (an Enchanter) / John Clease (Monty Python and the Holy Grail, 1975)
Introduction
“Vikings unwittingly made their swords stronger by trying to imbue them with spirits.
Iron Age Scandinavians only had access to poor quality iron, which put them at a tactical disadvantage against their neighbors.
To strengthen their swords, smiths used the bones of their dead ancestors and animals, hoping to transfer the spirit into their blades.
They couldn't have known that in so doing, they were forging a rudimentary form of steel.“
Matt Davis (2019)
Stories like this one were published in the popular press, distributed via web sites, pumped on social media, over early 2019. Anyone even loosely familiar with the Norse of the Viking Age would question the statement ‘tactical disadvantage’, which most certainly is not borne out by historical events. Stating ‘poor quality iron’ is also not an accurate reflection of the high level of workmanship observed in Norse objects, most particularly as seen in weapons.
Background – Iron plus Carbon
All iron materials used in the Viking Age1 are the product of the direct reduction, bloomery furnace method. The spongy iron created is then hand hammered to collapse internal voids and expel contained glassy slag, a process that will involve repeated folding and forge welding to refine into a working bar. This produces an iron material that will still contain minimal to microscopic inclusions of slag, and a distinctive linear texture.
‘Steel’ is a loose term for an alloy primarily of iron, with very small amounts of carbon included.2 As carbon increases, although the metal can become harder, it is at the cost of increasing brittleness. To retain the ability to be effectively hand / hot forged, the carbon content cannot exceed much over 1%. In practical experience, this means for long, high impact cutting tools i.e., swords, the overall carbon content should be about 0.5%, while for fine detailed cutting tools i.e., carving, the content may approach that 1%. A continuing problem in the literature is the use of ‘iron’ and ‘steel’ as interchangeable terms, compounded using ‘iron’ when writers are referring to modern industrial mild steel, which has different physical properties and use techniques.
Early bloomery furnaces are fired with charcoal which, when burned, provides not only the high temperatures required, but also carbon, both loose and converted to carbon monoxide gas, which reduces the iron oxide ore. This process continues for many hours to create the desired iron bloom. There is never any problem with having enough carbon inside a working bloomery furnace. What is clearly not understood by those unfamiliar with the operation of bloomery iron smelting furnaces, is that any attempt may result in metal with considerable variations in carbon content, not only between individual firing cycles but even within the same bloom itself. For the ancients, restricted using human power for bellows operations and thus lower furnace temperatures3 , the desired result would be a low carbon iron, softer and easy to forge. For the Norse smith wanting a harder metal, the appropriate parts of a bloom when rendered into a bar could be utilized for objects needing different final performance characteristics, qualities chosen based on experience with the metal.4
It is worth considering the comparison between temperatures developed inside a functioning bloomery iron smelting furnace and those utilized in modern crematoriums, fired using propane or natural gas, which are typically in the range of 1400 – 1600°F / 760 – 870°C (Cremation Association of North America, 2023)
It needs to be remembered that in a cremator, the fully fleshed body, with average 60% water, is being consumed, not just the bones at 20 – 25% water. (Sissons, 2020). In comparison, temperatures inside the lower part of a working bloomery iron furnace range from 1100 – 1200°C, with temperatures in the shaft as high as 1350°C expected.5 Time at temperature is also a factor. Temperatures at the top of a typical short shaft furnace as described later, are at the range of 500 – 600°C, and although the time for any given particle to fall to the level of the bloom is variable, 30 to 45 minutes is a very rough average.
A second overall problem is that these stories, and too often academic papers, push iron smelting and blacksmithing together as if these were combined into a single progression of ore into object in the hands of a single individual. Examined critically, the articles referred to above are also written without any real understanding of the technical aspects of metalworking that are involved. Methods which may be possibly useful for making small knives are unrealistically extended to the highly specialized skills of sword making.6
Iron as a solid, when heated to forging temperatures, will absorb carbon from its surroundings, but only extremely slowly. In a technique known as case hardening the soft iron is sealed away from the effects of oxygen, within an environment rich in powdered carbon, where it is held at temperatures well above ‘critical’ at about 900°C (Andrews, 1994, p.100-101). For any significant penetration of carbon, this process takes many hours, or even days. It will only be truly effective for previously forged, ground and polished blades, as the higher carbon layer will extend at best a few millimetres into the iron; otherwise losses during the forging process, and importantly the required surface grinding stages, can well exceed any beneficial effects.7 Traditionally, carbon for case hardening could be most easily and effectively supplied as powdered charcoal, from pieces of the forge fuel of the Viking Age, but also burned leather or burned bone are suggested in various historic writings as other organic alternatives.8
Powdered charcoal is primarily composed of carbon, for example + 80% for Oak (FAO UN, 1983). Any raw bone in comparison contains 67% inorganic materials, with only about 33% for the total organic components, of which carbon is only one (Anwar, 2013, p.19). Modern industrial bone char, as an indicator, contains only 8 - 11% carbon (Rede Advanced Materials, 2023). Even if the bone was ‘burned’ and pulverized before use as a case hardening medium, clearly the on hand simple wood charcoal would contain significantly more carbon.
Where did this concept of adding bone, much less grave sourced human bone, as a modifier to iron come from?
The inspiration for these media tales appears to be the 2004 paper Roll the Bones – from Iron to Steel by Terje Gansum (2004). A general reading of excavation reports of metalworking, particularly iron smelting at Norse sites, does sometimes include mention of small bone fragments being recovered. These are rarely, if ever, identified by species, most certainly not as being of human origin.
It is beyond the scope of this paper to critique how a single paper can construct an edifice where cultural theories overshadow practical realities. Although the original Gansum paper is primarily written more from the approach of cultural anthropology, it does include elements of experimental archaeology in support of its concepts. It bears remembering however that one of the guiding principles of any experimental archaeology is: ‘All that can be illustrated is A way, not THE way’. Just because a method can be demonstrated to be possible considering modern knowledge, it does not mean that it represents actual historic practice.
Experimental Design
The concentration here is on the technical and physical aspects of producing iron, so also there will be no attempt to delve into the murky depths of what might have constituted ancient, so often secret, Ritual. The stress of the following experiments is on the smelting and consolidation phases, ore to bar, not the smithing phase, bar to object.
Working as an Independent Researcher, and so personally funded, there was no laboratory analysis possible, and very limited instrumentation available. Although an attempt to proceed in a systematic manner was made, the observations are largely quantitative and observational rather than qualitative and providing detailed analysis. Under the leadership of the author over the last two decades, the working team from the Dark Ages Re-Creation Company has developed considerable experience with small scale bloomery iron furnaces (see Markewitz, 2023a). The working design is primarily based on archaeological samples from Northern Europe over the Late Iron Age (here post Roman, through the Viking Age specifically). As important details such as furnace heights and air delivery methods cannot be determined from archaeologically recovered historical prototypes, details of furnace design and operation have been refined through practical testing. Some modern elements have been included, primarily due to material availability and labour requirements. The experiment described was undertaken at Wareham, Grey County, Ontario Canada, a location about 130 km northwest of Toronto. The weather on smelt day June 20, 2020, was sunny, hot at 29°C, with humidity at 67%.
- The standard type is described as a ‘Short Shaft’ / slag tapping, furnace, with an inserted style tuyere for air input, and may either use a top or bottom extraction. Generally, the size is 25 – 28 cm internal diameter (ID) and 60 – 70 cm total (shaft) height (See Figure 1).
- Furnaces are primarily constructed of clay and may be free standing or partially earth banked. Some designs place the clay shaft on top of a base plinth constructed of concrete blocks or natural stone, then filled with charcoal fines. Over time several different clay types and additive mixtures have been tested. The standard mix is equal amounts by volume judged by eye, of a dry powdered high firing clay, typically ‘EPK'9 coarse sand locally gathered, primarily granite based, and ‘seasoned’, dry, hand shredded, horse manure, with enough water added to form a suitable plastic consistency.
- Various materials have been tested for tuyeres: steel pipe / pre-fired ceramic / heavy forged copper, all most typically with 2 cm ID. Placement of the tuyere is normally set 15 – 20 cm above the furnace base so creating a minimum of 40 cm from tuyere to the top of the furnace (stack height). The internal tip is positioned 5 cm beyond the inside wall, angled downwards to roughly 20 – 25 degrees.
- An attempt is made for as little modification of natural slag bowl formation as possible, generally only intervention via tuyere clearing or liquid slag tapping made when levels begin to interfere with air flow.
- Although past experiments have utilized several human powered bellows systems, the considerable physical effort, so number of workers required, has limited this use. Standard is air provided by an electric compression style blower, capable of dependably delivering up to 1400 litres per minute (LpM).10 Delivered air is estimated using a sliding plate blast gate, roughly marked at 100 LpM amounts placed downstream of the blower output. This use of modern electrically powered blowers is well understood to be the largest distortion of possible historic methods.
- Many types and sources of ore have been processed over the years. The ideal would be to use a primary bog iron ore in these experiments, but none is available within any reasonable travel distance of the working location. For this reason, the team developed a bog ore analogue, comprised of red iron oxide powder at 81% FE2O3, mixed with 10% whole wheat flour into a paste and then dried, which results in roughly 55% Fe content.11 This has proved a dependable substitute to primary bog iron ore, allowing for consistency over repeated tests.
- Charcoal is the fuel used, commercially purchased as either oak or maple. This is broken and screened to particle size between 25 to 5 mm.
- Although sometimes internal temperatures are measured via thermocouples to a digital thermometer, the operation of the furnace is primary gauged by measuring the time taken to burn a fixed quantity of charcoal, determined by volume, calculated later to record weight per fixed volume.
- A standard sequence is undertaken (Markewitz, 2012):
- first drying and pre-heating the furnace using wood splints
- adding charcoal and raising the furnace to operating temperature
- adding ore as smaller amounts distributed through each charcoal charge, not thick slabs of ore as suggested by some academics.
- ore additions increasing as the reduction reactions proceed, typically by 500 gm amounts over time
- once total ore is involved, covering with several additional charges of charcoal to start a burning down process, to ensure all ore is reduced and added to the bloom.
- final extraction, including initial compaction via hand hammers to break off any remaining slag materials.
The iron oxide used is supplied in a standard packaging that creates roughly 25 kg of prepared analog, so most test smelts by this team utilize this amount, with the consumption of about 50 kg prepared charcoal expected. Normal projected yields are bloom weights averaging +/- 5 kg, so into the range of 20 – 25% return yields from this ore type.
Experiments
Initial Experiment
In 2014, Emma Harrison from the University of Aberdeen added a component incorporating bone into the end of a working bloomery iron smelt, within the ongoing experimental series undertaken for the ‘Turf to Tools’ project at the Scottish Sculpture Workshop, Lumsden, Aberdeenshire, Scotland (Markewitz, 2023b). The furnace was based on the archaeology of the Pictish site of Culduthel, Scotland, dated to roughly 200 – 400 AD (Preece, 2011). It was a short shaft, slag tapping furnace, set on a stone plinth, with bottom extraction. At the last stages of an otherwise typical smelting sequence, a total of 5.2 kg beef bone pieces, oven dried and broken to average 2.5 cm, was added as two equal charges, in addition to the normal charcoal amounts, and above the last ore charge. The finished 11.5 kg bloom was subjected to further testing by Harrison (Harrison, 2015) (See Figure 2).
As the intention of the bone addition was to determine what effects might occur to the upper surface of the bloom, no impact to carbon content was expected. Even on careful analysis this bloom showed no significant changes in either carbon content or visible calcium deposits that could be attributed back to the bone additions. (Harrison, 2016) The primary impact to the smelting process was seen in a modification of the very last slag produced in the furnace. Rather than the black, iron rich, and fluid, material normal to an effectively operating furnace, a quantity of thick and viscus, yellowish white slag was produced as the bone charges settled to tuyere level. The creation of a considerable volume of this viscus slag would have been a major problem, likely to produce blockage to input air flow, if this had happened at any point in the iron making process other than the final furnace burn down towards extraction of the bloom. Several small fragments of burned bone were recovered in the post smelt debris, but the great majority of the bone was totally consumed (Harrison, 2015, p.35) (See Figure 3).
Experimental Smelt # 85 – June 20, 2020
The intent of this experiment was to add bones of differing species and states (from raw through previously cooked and cleaned) at two different points within a working smelt. After extraction, the final debris field would be graded and carefully screened by hand, with the expectation of being able to recover any remaining fragments down to about 5mm in size. The site preparation and furnace build was undertaken in the days leading up to the smelt itself.
The Furnace
In preparation for the later debris field evaluation, a new clean working surface was established. First, a solid base was laid over the existing grass lawn, consisting of a total of eight concrete paving slabs, each 60 x 60 cm. A frame, 180 cm to a side composed of standard ‘2 x 2’ lumber (so 4 x 4 cm) was placed on top of these and then filled with a layer of coarse sand to the top level of the wood.
As the operation of the furnace itself was not under investigation, the standard short shaft on a plinth build was used.
The base plinth was formed from several irregular sized pieces of natural granite blocks that were on hand. The advantage of a plinth base is to provide for more room for slag collection and increased ease during a bottom extraction. The furnace was placed to the centre rear of the prepared pad, knowing that additional room should be provided for the frontal debris field. The blocks created a height of about 12 cm at the front, a second course to the rear adding another 9 cm. The plinth interior was then filled with charcoal fines.
A clay mixture was prepared as described above, with grapefruit sized pieces formed into bricks, which were blended as added against a metal form that had been wrapped in newsprint paper to prevent wet clay from sticking to the surface. This 28 cm diameter form would ensure a consistent internal diameter to the furnace. After the first course of clay had been added and blended, the upper surface was scored to create a ‘Beardsley Break’ and coated with charcoal dust.12 As the build progressed, the metal form was removed, and the interior filled with a mix of dry wood stove ash and sand, which provides both stability and initial drying. The form is then replaced, mounted higher, the build process continuing until the furnace reached a total of 66 cm above the top of the plinth base. After the clay had been given a day to partially dry and stabilize, a generous extraction arch at 20 x 20 cm, and a smaller tapping arch at 7 x 7 cm, were cut above the plinth level. Last, a heavy forged copper tuyere with a 2 cm ID was mounted. It was inserted 5 cm beyond the interior wall, angled at 22.5 degrees downward, at a height that created 48 cm total stack height (tuyere tip centre to top of furnace).
After the drying fire, some of the charcoal fines in the base were burned away, and then covered with a layer of thin powdery wood ash. The result lowered the effective base depth to 22 cm below tuyere level (See Figure 4).
The Smelt
The smelt itself was deliberately carried out employing a standard sequence, so that any variations in normal progression could be at least potentially attributed to the bone additions – not differences in method. Air input increased over the smelt, from 800 LpM at the beginning to 1000 LpM at the end, both estimates. This increase was to maintain a consistent burn rate of roughly 12 – 14 minutes per 1.8 kg charcoal charge. During the main sequence, the time from first to last ore additions, a total of 21 kg of graded charcoal was consumed over 166 minutes, and a total of 24.7 kg of ore analogue added. Initially, a total of 4 kg of recovered iron rich tap slag was added as separate 1 kg charges. Individual ore charges would increase from 1 kg to 3 kg as the smelt progressed. The average burn rate for charcoal was 6.7 minutes per kg, average addition rate of ore was 7.9 minutes per kg.
For the details of the smelting sequence, see Appendix 1 - Smelt Data
Into the later stages of the smelt, it became clear that the slag bowl had formed higher than ideal, related to the position of the tuyere. Generally, this will result in two problems: first, fluid slag can rise high enough to interfere with the air blast, and second, there is less room for the bloom to accumulate. On the final extraction of the bloom, it was found to be a flat disc shape, rather than the oval hemisphere normally expected. The end yield was less than expected, a 2.6 kg bloom, only a 10.5% return from the ore.
The Bones
The bones to be added were all smaller pieces ranging from 1.5 - 15 cm long, partially due to availability but also to ensure they would easily fit inside the 28 cm diameter of the furnace. Bones from contemporary Canadian domestic food animals were collected, both from remains of earlier meals and by acquiring waste cuts from a local butcher. These would include uncooked with meat on, cooked with viable meat pulled free, cooked and completely cleaned. None of the bones were further dried or baked to remove moisture. There was no special attempt made to match the species used to historically likely ones, due to simple cost and availability, the inclusion of turkey the most obvious example. The turkey was available and was considered a reasonable substitute for a large fowl like goose. Pork and beef were the remaining two types included, considered to be at least from animal types available to the Norse, even if the physical animal sizes and butchering methods were the result of modern farming to butchery practices.
The initial concept was to make two additions of bone, one on the base before the addition of charcoal, one part way through the smelting sequence. The available material was divided into two roughly equal groupings, attempting to ensure there was as much as possible a representative sample of each bone type in each group. It should be noted that although scaled photographs were made, no detailed measurements of sizes beyond this, and most especially no individual starting weights were recorded, an error in process (See Figure 5).
- Poultry (Turkey) - breastbone, raw with meat remaining
- Poultry (Turkey) - thigh bone, cooked (roasted) with majority of meat removed
- Pork - cut rib sections, cooked (slow cooker) all meat and marrow removed
- Pork - cut rib sections, raw with meat remaining
- Beef - cut (lower?) leg section, cooked (boiled) all meat and marrow removed
- Beef - cut rib (steak) section, cooked (fried) with majority of meat removed
The final drying and pre-heat, using small wood splints, lasted approximately two hours. With the interior of the furnace still hot, and some small coals remaining, the first group of bones were carefully laid inside through the tap arch. This placement was considered consistent with a purely imagined concept of bones as a ritual deposit at the beginning of a smelt, with the following used (See Figure 6):
- Turkey thigh / Pork ribs (meat) / Turkey breast (meat)
- Beef leg section / Turkey thigh / Beef rib / Pork rib sections.
The extraction arch block was replaced and one by one larger pieces of charcoal dropped in from the top, as the air blast was slowly increased. This process was to ensure that the starting charcoal would correctly ignite in the lower base part of the furnace. Once enveloped, the furnace was filled first with larger pieces of rough charcoal, followed by graded fuel as the interior came up to working temperatures leading to the normal sequence of ore additions.
Discussions during the initial additions of iron rich tap slag13 led to a change in plan for the bone additions. It was decided to make three separate additions, at least conceptually relating to three possible intentions for adding bone. As mentioned, the first at the base at the start of the smelting process itself, could be likened to an ‘offering’ as the smelt began. The second, part way into the usual sequence, could be considered to be a ‘functional’ addition, where bone might affect the developing bloom. It was decided to separate that original grouping to allow for a third and final addition to be placed at the end of the smelting sequence, representing ‘discarding lunch’ remains. To that end, several of the remaining large pieces were cut in half to provide materials for this last deposit.
In keeping with the overall concept of a bone addition as functional, a second grouping was now placed just on top of the first addition of ore (250 gms), at 70 minutes into the main sequence (See Figure 7):
- Pork rib sections
- Pork ribs (meat)
- Turkey breast (meat)
- Turkey thigh
For this addition, pieces were placed to the side of the furnace away from the tuyere, which is also the normal location when new ore charges are made.14 The atmosphere directly at the top of the furnace is oxygen reduced to absent. Despite the extremely high temperatures (500 – 600°C), the meat quickly flash cooked, but did not show much surface burning. As with ore additions, as soon as the top charcoal level dropped enough to allow a further addition of fuel (normally about 5 cm), the layer with the bone was covered by fresh charcoal.
A final addition of bone was now placed at the very end of the smelting sequence. Normal practice is to add at least one final charge of charcoal, to completely cover the remaining ore and ensure all of it has reduced and dropped to bloom level. In this case, the bone constituted a final addition, which in turn was covered by an additional measure of charcoal and allowed to burn down inside the furnace (See Figure 8):
- Turkey breast (meat)
- 2 Turkey thigh.
- Beef leg section
- Pork rib sections
- Pork rib sections (meat)
- Beef rib section
Of note is the difference between the last two images. Figure 8 shows several bright streaks, visible as spark trails above the furnace. These are normally associated with the iron surface of the bloom being directly exposed to the air blast, effectively burning away (oxidizing and cutting) the bloom mass. This almost always indicates the slag bowl and the bloom within both sitting too high in the base of the furnace, and a loss of accumulated mass is expected (See Figure 9).
The Survey
For safety, it can be expected that both tap slag during a smelt and hot materials removed from the furnace during extraction will be all removed quickly from the working area close around the furnace front. This will include still burning charcoal, congealed liquid slag, pieces broken free from the slag bowl, and possibly fragments of the clay furnace walls. With a bottom extraction, exposing and grabbing clear the bloom will require a worker to be on their knees to accomplish this task, so clearly careful clearing of the working area is required.
As might be expected, the next day the interior of the furnace was still hot enough that it was not possible to explore here. Some images of the overall working area were made. Although the weather was clear and sunny, a tarp overhead was placed above the sand pad, to protect the debris until a detailed examination could be made.
In Figure 10 several larger aspects of the remains that might be expected around a bloomery iron furnace are apparent:
- As the tuyere is located above ground base level, some means of support is required, as it is likely to require slag obstructions cleared from its interior during a smelt. Although it is possible to supply this via a few forked sticks driven into the ground, to provide stability (thus preventing damage to the furnace wall) ideally these supports should be substantial, suggesting use of stones or timber stumps, in this case standard concrete blocks. These are just surface placed, so the only evidence would be voids in the pattern of ash and fine charcoal, or an edge line in furnace debris as was seen here.
- Any large bloom will necessitate the creation of an even larger slag bowl in the base of the furnace. The slag bowl will adhere to the inner clay walls and, as in this case, any supporting plinth structure. Although there would be potentially care given to not breaking the lower furnace walls against any possible re-use, differing amounts of damage often result. Normally these large pieces of hot material are grabbed and tossed to either side of the working area out of the way. This may not be the case if these pieces are broken away as the bloom itself is pulled clear of the encasing slag bowl in the furnace. Speed is essential during the extraction process, to retain as much internal heat as possible within the bloom as it is moved to the initial cleaning and consolidation hammering area.15 In Figure 10, several stones from the base plinth, and some larger pieces of broken lower furnace wall, can be seen pushed to either side of the extraction pathway
- Two piles of broken tap slag can be seen, one to the far left, one to the rear right. As it was generated, this material would likely have been collected from against the walls of the furnace as soon as it solidified and removed well out of the working area around the furnace. As this team uses this black iron rich slag at the start of other smelts, the bulk of this material is recovered later.
- One quite large (centre left foreground) and several smaller pieces of broken slag bowl can be seen, again pushed aside from the extraction space
- The largest spray of ash and charcoal debris is seen as a fan leading away from the extraction arch portion of the furnace.
Several days later, on June 25, a detailed examination of the smelting area was undertaken.
A simple grid system was created, using 6 mm (1/4 inch) diameter steel rods to mark off 30 cm squares. Positional numbering started from the lower left corner, as one looked to the front / extraction arch of the furnace (the northwest corner), recorded as cm S / cm E. The first task was to take a series of photographs of each of the individual grid squares, plus additional ones down into the furnace itself. During this process, the concrete blocks used to support the air supply system were left in place A small colour chart scale was included at the edge of each of these photographs. Most of the images were in shadow from the early morning sun via the solid tarp overhead, but the row of images to the lower / west edge were sun lit (See Figure 11).
During the initial photography, only one piece of clearly recognizable bone was seen on the surface This was a section of poultry thigh, split in half lengthwise, located at grid 60 S / 50 E. (When the images were processed for constituents later, the position of each recovered bone fragment was marked as seen in Figure 12).
Once this photography was completed, each individual square was cleared by hand. Material was first examined visually, then the fine ash and powdered charcoal strained through the fingers. This allowed the discovery of any fragments down to about 5 mm. There was no attempt to use a fine screen to sort even smaller solids from the fines. This being done as more detailed examination, at the hands of non-biologists, was considered overly tedious and of no practical value. Some attempt was made to remove material in descending layers, but even the thickest deposit of debris was only about 5 cm deep. The large pieces of stone, furnace wall, and slag bowl were left in place, the finer debris cleared around them first. When down to the sand level, these larger pieces were lifted, and then any material under them examined. The location of any fragments of bone was recorded as they were exposed. Each individual piece or collection of pieces was bagged separately.
Taken together, this simple method represented a macroscopic recovery of any bone fragments that survived the overall smelting process. There was no obvious visual difference to the slag / slag bowl pieces examined than that seen in numerous previous smelting events. With no access to any form of laboratory analysis, there was no useful purpose to finer examination or gathering samples of ash or slag.
A total of 15 bone fragments were recovered:
60 S / 50 E | 1 longer piece, porous tube, broken lengthwise (poultry thigh) | 25 x 10 x 5 mm | 1 |
50 S / 60 E | 4 small pieces, hollow porous tubes (poultry thigh) found near top of loose charcoal materials pulled out during extraction | 20 x 13 mm (triangular) | 2 |
20 x 8 mm | 3 | ||
32 x 8 mm | 4 | ||
7 x 6 mm | 5 | ||
50 S / 80 E | 1 small piece, slightly cylindrical, likely poultry thigh, but heavily carbonized | 5 x 20 mm | 6 |
85 S / 80 E | 1 piece of flat porous bone (turkey breast bone?) | 42 x 26 x 6 mm | 7 |
3 pieces of flat very solid bone (beef leg section) found on top of fines layer raked out | 45 x 26 x 12 mm | 8 | |
30 x 15 x 5 mm (broken after recovery) | 9 | ||
40 x 20 x 15 mm | 10 | ||
100 S / 70 E | 1 large piece, with slag attached to one side (clearly a piece of turkey breast bone) found in same orientation as originally placed (‘keel’ side up) | 90 x 50 x 40 mm | 11 |
90 S / 45 – 40 E | 4 smaller fragments of porous bone (may be fragments of above?) | 25 x 12 x 7 mm | 12 |
22 x 12 mm | 13 | ||
15 x 7 mm | 14 | ||
15 x 5 mm | 15 |
Table 1. Recovered Bone Fragments
In so much as the observed fragments were clearly distributed due to the emptying of the furnace during extraction (See Figures 13, 14 and 15), it is hard to assign specific bones to their initial placement within the furnace:
- The collection of fragments recovered at grid 85 S / 80 E were contained within a mass of charcoal fines, obviously material that had formed the initial base of the furnace. These fines would have been raked clear out of the furnace at the beginning of the extraction process to create more working space. The most obvious origin of these pieces would have been the bones placed on top of the fines and fine ash layer before the addition of charcoal. From previous experience, it is known that the air blast does not allow for much actual combustion in this lower area. Heat is generated from the slag bowl, which over the course of the smelt will sag down, usually coming to rest on the top of the fines layer.
- The large turkey breastbone recovered at 100 S / 70 E is most likely the meat covered piece placed at the top of the furnace at the end of the smelt sequence. It had been placed initially with the central ‘fin’ (keel) upwards. If it stayed in this orientation as it dropped, it would have presented the bottom side to the fluid slag bowl, which could have resulted in the same encrusting slag as found. This last set of added pieces had been exposed to the internal heat of the furnace for the shortest time, suggesting the water contained in the encasing meat had helped to protect this specific piece during the descent. That no other fragments (especially of the larger circular beef bone) were found suggests that without this protective meat covering, the internal heat was enough to consume the other pieces from this layer.
- The small fragments of chicken leg bone recovered from 60 S / 50 E are more uncertain as to their initial placement. They are furthest from the extraction arch, suggesting they were pulled clear early in the emptying of the furnace. They show no surface burning / carbon marks, which suggests they were exposed to heat, but in an oxygen reduced area. As the bones placed in the bottom of the furnace were also deposited on an ash layer (about 2 cm thick) this suggests that these, quite thin and fragile bones, were initially placed at that location.
- There was only a single, very small fragment that was recovered that showed extensive carbonization, the piece of chicken thigh bone at 50 S / 80 E. The exact conditions that this bone was exposed to are uncertain. Considering the small size, its found location like the group at A, may suggest a similar origin?
Additional – Bloom to Bar
Working with the dozens of iron blooms from previous experimental smelts has certainly illustrated that the resulting carbon contents can vary considerably, not only between processing of different ore types, but even between individual repetitions using similar ores, furnaces and smelting sequences. Beyond differences in ore, the next largest influence certainly appears to be the air volumes applied (Sauder and Williams, 2002). There can certainly be differences in the carbon content within a single bloom itself, often seen as lower carbon iron (so softer to forge) to the bottom and higher carbon to the upper surface. A simple qualitative test for carbon content can be made by ‘spark testing’ in experienced hands.16
The bloom produced in experiment # 85 had been compressed to a plate shape under a hydraulic press and then divided into five sections as radial cuts, after the initial compaction by hand hammering. Three of these sections have been since refined to solid working bars through a series of compactions including folding and repeated forge welding. This process was undertaken using a ‘traditional’ bituminous coal forge working both by hand and under a mechanical hammer. One piece (later progressing to object) was worked by the author, the two detailed here by Neil Peterson, who should be considered at a ‘hobbyist’ level of skill. Both finished bars were spark tested, as well as the irregular surfaces of the two remaining un-processed sections of bloom. The rectangular bars were tested on both ends and in the wider middle section. Raw blooms are harder to get consistent results from, but both the original top and bottom surfaces were tested:
Section | Starts weight | Finished / return | Carbon via spark test |
bar B | 403 g | 240 g / 60% | end - ‘mild’ / 1020 middle - ‘low’ / 1005 end - ‘spring’ / 1045 |
bar C | 732 g | 585 g / 80% | end - ‘low’ / 1005 middle - ‘tool’ / 1095 end - ‘spring’ / 1045 |
raw bloom 4 | 343 g | n/a | top - ‘spring’ / 1045 bottom - ‘mild’ / 1020 |
raw bloom 5 | 512 g | n/a | top - ‘tool’ / 1095 bottom - ‘iron’ / 1000 |
Table 2. Bloom to Bar – estimated carbon contents / comparison*
* The comparison is to modern steel (iron + carbon) alloy bars with known contents, expressed in the last two numbers as 1/100% carbon.
As discussed in the Background section above, there would be expected to be variations between different sections of even the same bloom.17 The carbon contents indicated here are certainly within the normal expected range, as observed over the course of over 90 earlier bloomery iron smelts / blooms created.
Discussion
On Methods
This experiment benefited from having a very experienced working team, in terms of managing the smelt itself. The mounting of an effective bloomery iron smelt is a technical exercise, where the creation of a large and good quality bloom requires specialized skills and considerable experience. The overall process itself however is relatively simple, if viewed as an experiential undertaking. Locally dug clay and sand can be used to build the furnace. Finding suitable ore can be problematic, but the red oxide developed by this team is not overly expensive and industrial taconite also serves very well. The primary expense involved is the charcoal. Standard steel pipe will survive a single firing as the tuyere. Although often demeaned by academics, a simple vacuum cleaner can effectively serve as a blower.
The key to providing useful data lies in complete and effective record keeping. At the simplest level, measuring volume of containers, weights of added components, and careful noting of time of events; all will provide useful, sometimes critical, information. Photography is of incredible utility, especially as a means of detailing what can often be quite frantic activities during a smelt, such as slag management of extraction. In contrast to this, expensive instrumentation is needed to make measurements of precise temperature and air volumes, but burn rate of charcoal consumed over time is directly influenced by both, and is a simple, if comparative, measure.
One failure of this experiment was in not recording the weight of the individual bone pieces, even though a simple digital scale, accurate to + / - one gram, was on hand. Scaled photographs, if only set against a normal tape measure, allowing for later recovery of sizes, also were not made during the experiment itself.
The survey of the final debris was undertaken using the simplest of tools, the human hand and eye, resulting in a detection down to roughly 5 mm pieces. The location of the individual bone fragments was estimated against the grid used, so at best were only + / - 5 cm but deemed appropriate for the purposes of the experiment. Passing the debris through a screen would have allowed for the recovery of finer bone fragments, but given the considerable additional time and labour required, especially considering the volume of charcoal pieces included, this was not considered useful.
There might have been some related information available if it was possible to provide chemical analysis of both slag and the metal itself. Beyond potentially small amounts from the charcoal, the only phosphorus available had to come from the bone, so tracing the movement of that element might provide some insight. Without institutional support however, such testing was not available.
On Concepts
As above, the slag bowl developed in a higher than ideal position. The reason for this is not entirely clear, as the furnace layout and general operation sequence had followed those used over a large number of previous experiments where such a level was not the result. Without any other simple explanation, it might be assumed that the meat covered bone placed at the very base of the furnace, because of its water content, had caused this. In reflection, this seems unlikely, both as the amount of bone containing meat was small, so also the amount of applied moisture even smaller. This considered against the time taken to fully ignite the interior charcoal which should have long baked out any moisture well before the accumulation of any slag.
Addition | Location | Total time | Temperature |
One | base below charcoal evenly placed | 340 minutes | starts at lower temperature |
Two | away from tuyere | 215 minutes | 1300°C + |
Three | evenly placed | 45 minutes | 1300°C +, decreases slightly to end |
Table 3. Times at combustion / placement
Taking note of Harrison’s earlier work, and comparing it to the results recovered during this experiment, several elements become clear:
- The normal 1300°C plus temperatures within an iron smelting furnace, coupled with the expected duration at temperature for any given particle, can be expected to totally consume any small, i.e. 5 cm +, piece of bone.
- There may be some possibility of a fully meat covered bone retaining some integrity, at least for a limited time, inside the furnace.
- It is unclear if meat covered bones, interjecting water mass into the furnace column, might affect the regular progress of the smelt. Such cooling effects, if significant, are most likely to have an overall * negative * effect on the progress of the smelt.
- Bones placed at the base of the furnace will be subjected to the least amount of direct heat effects from burning charcoal itself.
- Hot slag will envelop the base area of the furnace over the sequence of the smelt, however. The slag bowl itself will sag downwards as it collects. Slag tapping events, both as direct interventions and as ‘incontinence’, can allow even hotter liquid slag to run down into this area.
It is being presumed that if historically bones had been added into a smelt, these would most likely have had to consist of smaller pieces, cut or broken, if for no other reason than the confined space available inside the furnace itself. Long bones could of course be added ‘end down’, but if placed during the main charging sequence, this placement might well interfere with normal smelting processes. It is worth remembering that any human ‘bones of ancestors’, especially if exhumed from long standing burials, certainly include little or no meat, just because of the process of natural decay. There might be some difference in consumption rate with a whole bone against a piece with its marrow interior exposed, but unlikely significant against the combustion times and temperatures involved. It remains unknown how placing whole long bones inside the base of the furnace at the very start, before any addition of charcoal, might affect the overall internal dynamics inside the furnace. Some impact on the initial ignition of charcoal would be likely here, as these long bones would interfere with the filling and settling of the furnace, most likely extending this phase of the smelt.
It is known through modern chemistry that small amounts of phosphorus will impact the quality of iron, making the metal harder, but also more brittle and at higher concentrations prone to cracking at lower functional use temperatures, what is called ‘cold short’.18 Phosphorus is an element naturally occurring in some primary bog iron ores, which were widely used throughout Northern Europe. Bone converted to ash will contain a good amount of phosphorus, in the range of 16% (Gallemagne and Richelle, 1973 in Turner-Walker, 1994, figure 4) A whole separate question is if bone added to the smelting process causes the resulting iron to pick up any phosphorus at all. Secondary to this would be how large a quantity of bone would need to be added to generate any useful effect. As the ancients lacked any understanding of elemental chemistry, it certainly cannot be assumed that adding bone was done functionally to mimic some unknown property within some local ores and absent in others. That phosphorus containing iron was used during the Viking Age has been certainly demonstrated by metallurgical analysis of artifact blades, certainly within pattern welding, where this metal is a brighter white colour, and so better contrasts against the dark colours of etched carbon alloy, the ropy textures of plain iron (Föll, n.d.) (See Figure 16).
Conclusions
The consistent destruction of any bones added during the main charcoal charging sequences of a bloomery iron smelt does suggest that it is unlikely to recover archaeologically more than the smallest traces of any added bones. The only likely situations where bone has much chance of leaving fragments after being added to a functioning bloomery iron furnace are
- Meat containing bone, but only if added at the very end of the smelting sequence.
- Bones placed on the base layer of the furnace before the smelt starts.
With a lack of any detailed laboratory analysis within this experiment, it cannot be stated with certainty that an addition of bone might not have affected the composition of the resulting iron itself. At least from a qualitative standpoint, this does not appear to be the case.
It is worth noting that in Harrison’s 2014 experiment, the addition of large amounts of bone did have a noticeable effect on the operation of the furnace, being the creation of noticeable amounts of a green, viscous slag. If this had happened earlier during the main smelting sequence, this slag would have most likely caused problems through potentially blocking air flow, with its thick consistency making it more difficult to clear or drain. This makes addition of any volume of bone a negative impact to a successful iron smelt.
Bone added into the furnace during the very long operation cycle may be least likely to survive. From first pre-heat to final extraction, even when creating blooms smaller than the known artifact samples, the total elapsed time can easily range from 4 - 8 hours. During the bulk of this, the furnace needs additions every 2 – 4 minutes so some of the working team needs to be constantly in attendance. With the use of human powered air, a Viking Age reality, individual workers are rotated in and out on a roughly 5-minute-long cycle. It has certainly been this team’s experience that any food needs to be grabbed quickly between tasks, eaten at the furnace itself. This suggests that some bone fragments that have been recovered archaeologically may be simply from an end of smelt ‘cleaning up lunch’.
As the best preservation of the bone added in this experiment appears to have been from pieces placed on the base ash layer, before the addition of any charcoal at all, this would tend to support a supposition that bone fragments recovered in archaeological examination, especially if discovered within a body of other furnace debris (ash, charcoal) may point to a more ‘Ritual’, over functional, purpose.
It is important to remember that this experiment makes no attempts to suggest why Norse smelt masters may have chosen to, or even if they ever did, add bone pieces into a working bloomery furnace. Extreme care must be taken in any attempt to apply ritual practice from other cultures, remote in time, geography, working methods, and especially radically differing world views, to the practices of the Viking Age Norse. It is suggested that the only potential functional reason for adding bone may possibly be to promote an intake of phosphorus, but it was well beyond the scope of this experiment to provide any data related to this.
Acknowledgements
Working Team - Neil Peterson, Rey Cogswell
Dundalk Foodland - for providing many of the bone pieces used.
Andrew Welton – for supplying an image of his work (See Figure 17 for Contemporary pattern welded blade by Andrew Welton, showing contrast between low P bloomery iron and high P antique wrought iron).
Emma Harrison – for her early work and contributions, use of her image.
Neil Peterson – For his constant support and input during discussions leading up to and during this experiment. For the last two years, he has participated (and greatly encouraged) a series of working sessions to convert many of the past blooms on hand into working bars. Neil also undertook a review of the draft of this paper, helping considerably with the final version.
Kelly Probyn-Smith – for undertaking the conversion of the Power Point presentation prepared for the EAC13 conference summarizing this paper into a movie format (and enduring several days of frustrated muttering during my own attempts).
A note about the Author
Darrell Markewitz has been a professional artisan blacksmith since the later 1980’s and has made a lifelong study of Early Medieval / Viking Age material culture. Since 2001 he has specifically investigated the physical techniques of bloomery iron smelting, undertaking over 90 individual furnace firings to date of writing. Many of the opinions and observations stated in this paper are a result of this accumulated experience.
A less academic report of this experiment is available on the ‘Experimental Iron Smelting’ web site (2020).
‘Look at the Bones - Build and Smelt’
http://www.warehamforge.ca/ironsmelting/iron2020/6-20-smelt/smelt.html
‘Look at the Bones – Exploration’
http://www.warehamforge.ca/ironsmelting/iron2020/6-20-smelt/explore.html
An overview of this material was presented at the EAC-13 conference (2023).
- 1Not precisely true, as there may be some evidence of ferrous metal ingots imported from Asia via Middle East. (Williams, 2007) Correctly called ‘wootz’, this higher carbon alloy is created using a crucible process, where carefully selected ingredients are contained in a sealed clay cup, heated to the melting point of iron, then slowly cooled. (Föll, n.d., chapter 10.4)
- 2The primary problem arises as modern steels, starting 1855 AD, are made using a quite different mechanical process, and so have a very different physical structure than historic metals. The precise term for Viking Age iron plus carbon alloys is suggested as ‘bloomery steel’ by this author.
- 3As a liquid, iron will absorb carbon almost instantaneously. The introduction of water powered machinery is highly significant, allowing for higher air volumes, so not only larger furnaces, but also higher operating temperatures. Into the Late Medieval period, one method would be to make a high carbon cast iron via blast furnace, and then carefully burn out excess carbon via the finery process.
- 4There are several ways an experienced blacksmith can judge qualitatively the hardness / carbon content of a bar. The simplest is impact resistance, a higher carbon metal does not deform as much under the same hammer stroke as soft iron. This also changes the sound on impact, although this a subtle effect. A piece of bar, heated to orange and quenched, becomes significantly harder and brittle with the presence of carbon. When forced to breaking, both the colour of the exposed surface and the crystal structure revealed are indicative of the relative carbon content.
- 5Measurements taken in past experimental smelts by this team have regularly recorded temperatures up to and exceeding 1300 °C, the failure limit of the thermocouples employed. See also: Pleiner, 2000, pp. 132-136.
- 6Knives, or single flat bars intended to be forged into knives, are small enough, in the range of 50 – 100 gm, to allow for the encasement and long duration heat soaking method involved in case hardening. It should be possible with detailed, if destructive, metallurgical sampling to distinguish if this method was utilized, as there should be a variation in carbon content with the highest amount on the surface, fading away over a relatively short distance towards an unaffected centre. Sword blades are simply too long to be encased and effectively heated and have finished weights an order of magnitude larger, into the range of 1000 – 1500 gm. A potential solution would be to create several small plates, each case hardened, then forge welding those into larger billets, a simple version of the much later blister steel process. This would result in a ‘piled’ structure, again potentially visible in metallurgical cross sectioning. It also needs to be remembered that there will be considerable losses in mass during the required multiple forge welds leading to the preparation of the starting sword billet, 25 % or more could be expected, based on past experience.
- 7Without going into detail of the mechanics of blacksmithing / blade smithing, it is important to remember that at effective forging temperatures, iron in the presence of oxygen will form a surface layer of iron oxide scale, notably being thicker at higher working temperatures. With every hammering cycle, this scale is knocked off, a loss which can become significant, on the order of millimetres, within elaborate forgings. At forge welding temperatures, as high as 1350 °C for ‘pure’ iron, carbon will burn off metal surfaces. This is a well-known problem for those creating billets of ‘layered’ steels, where individual pieces of differing carbon content are welded into blocks for blade making, for example in North European pattern welded swords.
- 8Modern readers are reminded of the significant observer bias contained in all historic descriptions. The writers are almost never actual practitioners of the crafts they describe. There is also the likelihood that the actual workers, especially within technical specialties, may not have been correctly divulging ‘trade secrets’ to outside observers, still a phenomenon seen today. Ancient workers, without scientific understanding, will be following a pattern of ‘it worked last time’ as much as the modern concept of ‘innovation leading to a best possible method’.
- 9Edger Plastic Kaolin (EPK) is high firing clay body, (1325 – 1345 °C) See Hansen (2023)
- 10The manufacturer’s description: “AMETEK #116246-04 / 50CFM BLOWER Motor is rated 115 VAC 1.9 amps, 60Hz / 3450 rpm. Ball bearing. Continuous duty. Thermally protected. Five-stage centrifugal design. The blower will move 50 cfm (1415 LpM) of air at 0" of water-static pressure.”
- 11This analogue was originally developed to mimic the primary bog iron ore from L’Anse aux Meadows NHSC / Vinland, as used by the Norse c. 1000 AD. See: Markewitz, 2008
- 12Named after George Beardsley, who demonstrated its effectiveness at Turf to Tools 1 in 2014 (Markewitz, 2023b). Clay adhering to an irregular stone base is prone to cracking as the clay dries and shrinks. A depression scored into the top surface of a line of soft clay, then dusted with charcoal, both keeps the upper furnace wall in place, and creates an effective barrier to keep hot reactive gases from escaping. At the same time, the break keeps cracks from the base from propagating upwards.
- 13A method demonstrated by Michael Nissen of the Ribe Viking Centre, Denmark has proved very effective and has been adopted as standard. First charges of broken iron rich tap slag, gathered from a previous smelt, are added, typically in 250 gm amounts, spread as 1 kg total per 1.8 kg charcoal charge, over several charges to a total of 2 – 5 kg. This material has been found to quickly form a functional slag bowl system, allowing better final yields, as reduced ore will start collecting into a bloom mass earlier in the smelting process.
- 14This is because the hottest part of the furnace is directly above the tuyere and typically charcoal is consumed faster on that side. This offside position allows for the descending ore to travel on a diagonal path through the furnace, allowing for the longest time available for the reduction process.
- 15This location may also reveal distinctive debris patterns, centred around marks indicating a wooden stump (or less functional large stone block). It most likely to be found very close by the furnace and needs to have enough clear area around it to provide space for several workers with sledgehammers plus one holding the bloom via oversized tongs. (Markewitz, 2022)
- 16Applying the surface of an iron alloy bar to a high-speed grinder will create sparks. The colour and nature of these sparks gives an approximation of carbon content, especially when compared to samples of known alloy content bars. A skilled eye can make estimations within about 0.10 % of carbon content. Sparks from known alloy content bars were compared to tested samples, applying 45 years of blacksmithing experience.
- 17In past work, this team has created blooms in spark tested carbon content ranging from virtually carbon free iron through to ‘bloomery steel’ amounts similar to modern spring steel at 0.5 %, to tool steel at roughly 1 %, even on several occasions cast iron at plus 1.8 % (Markewitz, 2023a).
- 18Again, a pronounced difference in the handling characteristics between knives and swords. Phosphorus at 0.6 % will result in a metal that is noticeably harder, so cutting edges will stay sharp longer over carbon free soft iron (Sauder & Williams, in preparation). However, the increase in brittleness with high additions of phosphorus becomes significant as environmental temperatures drop from 20 °C down to 0 °C (or below). Consider this range against daily temperatures in Northern Europe during the Viking Age! A knife is unlikely to be subjected to the kind of impact shock where brittleness unbalances the increase in edge holding. A large, high impact blade, i.e., a sword, becomes prone to catastrophic failure, especially in the winter (Föll, n.d., chapter 3.2.2).
Keywords
Country
- Canada
Appendix 1
CLOCK | ELAPSED | EVENT | AIR | CHARCOAL | ORE | |||
June 20, 2020 | UNIT | COUNT | TOTAL | Unit | TOTAL | |||
Bones' concept test | LpM | bucket | kg | kg | kg | |||
1.8 ? | ||||||||
PREHEAT | ||||||||
920 | start wood splints pre-heat | |||||||
1100 | 1-40 | start fill charcoal (error, removed) | ||||||
gap to place lower bone | ||||||||
IGNITION | ||||||||
1125 | fill with rough charcoal | 800 | 5.5 | 9.90 | ||||
1134 | finish last part bucket rough | 0.5 | 6 | 10.80 | ||||
1148 | 14 | rough charcoal | 1 | 7 | 12.60 | |||
1151 | probed to settle | |||||||
1153 | 5 | switch to graded, top ignites | 1 | 8 | 14.40 | |||
1207 | 14 | 1 | 9 | 16.20 | ||||
1224 | 15 | 1 | 10 | 18.00 | ||||
1229 | increase air | 900 | ||||||
MAIN SEQUENCE | ||||||||
1231 | start first slag addition | |||||||
1240 | 16 | 1 | 11 | 19.80 | 1 S | 1 S | ||
1252 | 12 | 1 | 12 | 21.60 | 1 S | 2 S | ||
1307 | 15 | 1 | 13 | 23.40 | 1 S | 3 S | ||
1322 | 15 | 1 | 14 | 25.20 | 1 S | 4 S | ||
slag tap / start analog addition | ||||||||
1333 | 11 | 1 | 15 | 27.00 | 1 | 1 | ||
1340 | bone addition | |||||||
1345 | 12 | 1 | 16 | 28.80 | 1 | 2 | ||
1401 | 16 | ore increase | 1 | 17 | 30.60 | 1,5 | 3,5 | |
1418 | 17 | 1 | 18 | 32.40 | 1,5 | 5 | ||
1422 | air increase | 1000 | ||||||
1441 | 23 | tuyere 25% blocked, even ring | 1 | 19 | 34.20 | 2 | 7 | |
1452 | 11 | 1 | 20 | 36.00 | 2 | 9 | ||
1504 | 12 | 1 | 21 | 37.80 | 2 | 11 | ||
1517 | 13 | 1 | 22 | 39.60 | 2 | 13 | ||
1531 | 14 | 1 | 23 | 41.40 | 3 | 16 | ||
1540 | 9 | 1 | 24 | 43.20 | 2 | 18 | ||
1556 | 16 | 1 | 25 | 45.00 | 3 | 21 | ||
1608 | 12 | 1 | 26 | 46.80 | 2 | 23 | ||
last ore addition | 1 | 27 | 48.60 | 1.75 | 24.75 | |||
add gromps | 1 | 28 | 50.40 | 1 G | 1 G | |||
1430 | add bone, charcoal to cover | |||||||
1646 | 10 | last charcoal added | 1 | 29 | 52.20 | |||
BURN DOWN | ||||||||
start burn down | ||||||||
1715? | X 3 ? | (no record of extraction time) | ||||||
TOTALS | ||||||||
Charcoal - all Maple | 52 | kg | ||||||
Ore | 24.8 | kg | ||||||
Ore total with gromps | 25.8 | |||||||
Bloom | 2.6 | kg | ||||||
Yield | 10.5 | % | ||||||
flat disk, crumbly texture |
TEAM: Neil Peterson / Rey Cogswell
Bibliography
Andrews, J., 1994, The New Edge of the Anvil. Skipjack Press.
Anwar, J., 2013, General Osteology [e-slide show] Available at: < https://www.slideshare.net/jamilanwar/general-osteology > [Accessed 17 February 2023].
Cremation Association of North America, 2023. Cremation Process. [online] Available at: < https://www.cremationassociation.org/page/CremationProcess > [Accessed 20 September 2023]
Davis, M., 2019, Vikings unwittingly made their swords stronger by trying to imbue them with spirits. Big Think, March 22, 2019. [online] Available at < https://bigthink.com/hard-science/norse-rituals/ > [Accessed 13 February 2023].
FAO UN, 1983, 10.1.5 Typical Charcoal Analyses. In: Simple Technologies for Charcoal Making. [online publication] Available at: < https://www.fao.org/3/x5328e/x5328e0b.htm#10.1.5 typical charcoal analyses > [Accessed 20 September 2023].
Föll, H., n.d. Iron, Steel and Swords. [online] Available at: < https://www.tf.uni-kiel.de/matwis/amat/iss/index.html > [Accessed 19 March 2023].
Gansum, T., 2004. Roll the Bones – from Iron to Steel. Norwegian Archaeological Review 37(1)’, pp. 41-57 [online] Available at: < https://www.researchgate.net/publication/248980640_Role_the_Bones_-_from_Iron_to_Steel > [Accessed 14 February 2023].
Hansen, T., 2023. Digitalfire. [online] Available at: < https://digitalfire.com/material/291 > [Accessed 20 November 2023].
Harrison, E., 2015. Iron, Turf and Bone: An explorative study into Viking Age Icelandic bloomery smelting and the effect of bone in iron smelting. Honours Undergraduate thesis, University of Aberdeen.
Harrison, E., 2016, Smelting the Ancestors? An experimental investigation into the effect of bone on slag systems and extractive metallurgy. Master Thesis, University of Sheffield. Available at: < https://www.academia.edu/51894130/... > [Accessed 20 November 2023].
Markewitz, D., 2008. Error Correction – Ore Analog Composition. Hammered Out Bits. [blog] 25 June Available at: < https://warehamforgeblog.blogspot.com/2008/06/error-correction-ore-analog-composition.html > [Accessed 4 March 2023].
Markewitz, D., 2012. “But if you don’t get any IRON…” Towards an Effective Method for Small Iron Smelting Furnaces, EXARC Journal 2012/1 [online] Available at: <https://exarc.net/ark:/88735/10041> [Accessed 6 March 2023].
Markewitz, D., 2022. 'That Which Remains’: Signs from Bloomery Iron Smelting - Initial Compaction’. [pdf] Available at: <http://www.warehamforge.ca/ironsmelting/iron2022/2-compacting.pdf> [ Accessed 5 March 2023].
Markewitz, D., 2023a. Experimental Iron Smelting’. [online publication] Available at: < http://www.warehamforge.ca/ironsmelting/index.html > [Accessed 13 November 2023].
Markewitz, D., 2023b. Experiment, Archaeology & Art - The Turf to Tools Project. Presentation, EAA conference, Belfast, Ireland, 30 August to 2 September 2023.
Monty Python and the Holy Grail, 1975 [film] UK: Python (Monty) Pictures.
Pleiner, R., 2000. Iron in Archaeology: The European Bloomery Smelters. Prague: Archeologický Ústav ČR.
Preece, R., 2011. The Archæological Finds at Culduthel, Inverness. Inverness: Inverness Royal Academy.
Rede Advanced Materials, 2023. Bone Char (Granular) / Bone Black, Physical Properties. [online] Available at: < https://www.reade.com/products/bone-char-granular-bone-black > [Accessed 20 September 2023].
Sauder, L. and Williams, S., 2002, A Practical Treatise on the Smelting and Smithing of Bloomery Iron, Historical Metallurgy 36 (2). [online] Available at: < https://s3.amazonaws.com/images.icompendium.com/sites/eliz2406/sup/3694971-A-practical-treatise-on-the-smelting-and-smithing-of-bloomery-iron.pdf > [Accessed 5 March 2023].
Sauder, L. and Williams, S., in preparation, The Management and Exploitation of Phosphorus in Bloomery Iron: A Practitioner's's Observations.
Sissons, C., 2020. What is the average percentage of water in the human body? Medical News Today [e-newsletter] 27 May. Available at: < https://www.medicalnewstoday.com/articles/what-percentage-of-the-human-body-is-water > [Accessed 16 February 2023].
Turner-Walker, G., 1994, The Characterisation of Fossil Bone. PhD thesis, National Yunlin University of Science and Technology. Available at: < https://www.researchgate.net/figure/4-shows-the-composition-of-the-mineral-phase-of-bone-first-published-in-1894-by_tbl1_258239992 > [Accessed 20 September 2023].
Williams, A., 2007. Crucible Steel in medieval swords. In: S. La Nice, D. Hook and P. Craddock, eds. Metals and Mines: Studies in Archaeometallurgy’. London: Archetype Publications Ltd., pp.233-241.