The content is published under a Creative Commons Attribution Non-Commercial 4.0 License.
Reviewed Article:
Testing Roman Glass in the Flame
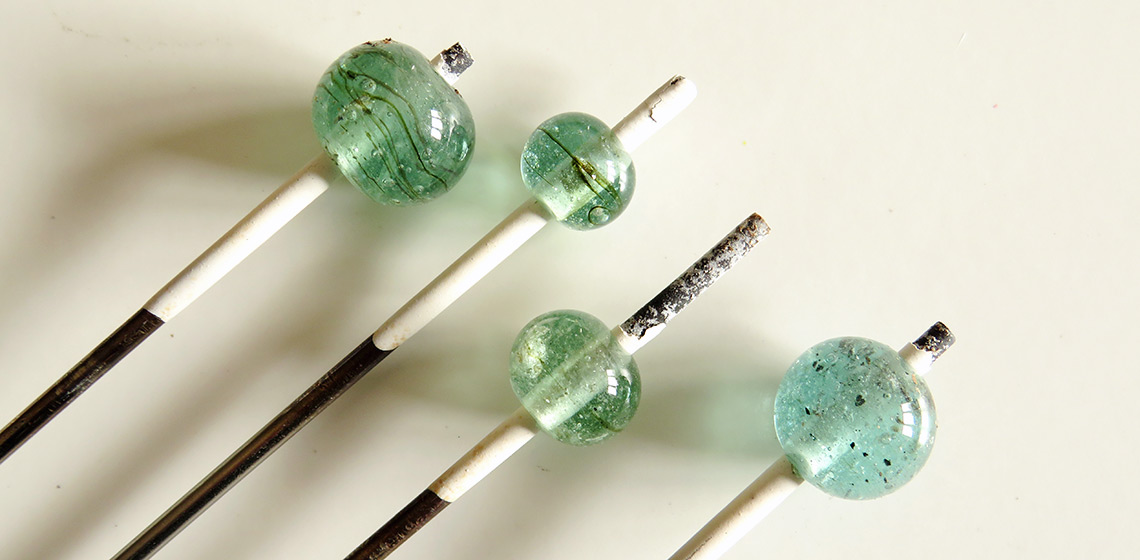
- The working properties of glass used in Early Medieval England -
Glass made during the Romano British period was recycled throughout the Late Roman and Early Medieval periods. Studies have shown that British beadmakers of the fifth and early sixth centuries AD made a large proportion of their beads using Roman period glass (Peake, 2013). To study fully the techniques of glass workers in early Anglo-Saxon times, it is important to be sure the modern glass used to recreate ancient beads and other glass objects is similar in properties to the ancient glass used to make the originals. Glass with very different working properties could affect the techniques used. This study explains the importance of glass properties such as viscosity, temperature working range and softening point when studying ancient techniques of glass working. A quantity of Roman glass cullet, supplied by the Museum of London Archaeology, has been put to a range of tests, including beadmaking, to investigate the behaviour of the glass in the flame. The results show that the thermal expansion and viscosity of the ancient glass samples place them well within the range of modern artisan glasses used for beadmaking and glass fusing. The tests also revealed a wide variety of working properties in the samples, but the glass was all easily workable with more favourable properties than some modern glasses (See Figure 1).
Introduction
Experiments on glass bead techniques used in antiquity have produced many insights into how early medieval beadmakers made their beads (Heaser, 2018). The studies mainly focused on early medieval beads found in cemeteries of the fifth and sixth centuries AD in England. Replica tools and a simple modern blow torch were used to simulate the conditions of the ancient beadmakers (See Appendix 1).
The one missing factor, however, has been the ability to use a similar type of glass to the ancient glasses used by the early medieval beadmakers. The closest glasses available for these experiments are soda-lime glasses that are used today by lampwork beadmakers such as Effetre glass manufactured in Murano, Venice. The question is, do these behave in the flame in the same way as ancient glass?
For this study, 250g of Roman cullet from Basinghall Street in London was kindly provided by the Museum of London Archaeology (MOLA). Cullet is waste glass collected for recycling, and large quantities were found at this site, which excavation showed was a Roman glass works. This is the type of base glass that has been identified in analyses of early medieval glass beads in Britain and was widely used at that time (Peake, 2013). The following study analyses this glass both chemically and physically. The results show that while there are differences in chemical content and glass handling in the flame compared to modern soda lime glass, they are small enough to require only a small amount of adaptation by the beadmaker (See Figure 2).
While the practical experiments were conducted using beadmaking, the results throw light on the general working properties of Roman glass. Considerably larger quantities of glass would be needed to test the glass for glass blowing.
Glass Ingredients
Soda lime glass is made from three main ingredients:
- Silica or sand
- Soda, which acts as a flux and lowers the temperature required to melt the silica.
- Lime, which prevents the glass from becoming water soluble
The levels of soda and lime in the mixture impact the properties of the resulting glass, such as its durability and behaviour at different temperatures. There are many other additives that alter glass. Oxides of elements such as iron, copper, lead, antimony and manganese are used for clarifying the glass, adding colour, and changing the viscosity of the glass. Ancient glassmakers appear to have had a wide knowledge of these additives, which were available in the form of slag from metalworking or were naturally occurring in the environment. Some were in the main ingredients already. It has been shown recently that beadmakers at Ribe coloured their own glass using melted cullet and metal oxides (Barfod, et al., 2022), so this activity was not limited to major glass-making workshops.
The full chemistry of glass is a vast subject and mostly beyond the scope of this study, which concentrates on the physical properties of glass in the flame. Basic glass chemistry is referred to when needed to explain the experiments and findings. (Corning Museum of Glass 2011). A good overview of the subject is found in Kervin (1999, pp.67-77).
Measuring glass coe and viscosity
Most analytical studies of ancient glass focus on elemental analysis, and the terms “COE” (Coefficient of Expansion) and “Viscosity” are rarely mentioned. This should be addressed because while the elemental analysis shows the glass recipe and suggests its provenance, it gives no indication as to the performance of the glass when it is used to create objects. This means that a large store of information has largely been ignored. Glass that is too stiff, or has a very narrow thermal working range, will be difficult to use for creating fine blown vessels or other objects. Different glass colours that are incompatible because of a large difference in COE will cause untenable stresses within an object if used together. The result will be fractures in the glass that can shatter or spoil the piece. Glass that is too soft will be impossible to use for finely decorated beads, thin stringers of glass will melt in the slightest touch of the flame.
The Glass Analysis Data
Glass | Na2O | MgO | Al2O3 | SiO2 | P2O5 | SO3 | Cl | K2O | CaO | TiO2 | MnO | Fe2O3 | Sb2O3 |
Basinghall St. Vessel cullet – clear1 | 19.0 | 0.4 | 1.9 | 69.0 | 0 | 0.4 | 1.2 | 0.5 | 6.1 | 0.1 | 0.2 | 0.5 | 0.6 |
Basinghall St. Vessel cullet – natural1 | 15.5 | 0.6 | 2.4 | 70.8 | 0 | 0.3 | 1.1 | 0.6 | 7.6 | 0.1 | 0.5 | 0.5 | <0.3 |
Lakenheath Roman2 | 17.6 | 0.6 | 2.3 | 68.4 | 0.2 | 0.4 | 1.1 | 0.7 | 6.6 | 0.1 | 0.6 | 0.9 | 0.5 |
Lakenheath EMed I2 | 18.9 | 0.9 | 2.3 | 65.5 | 0.1 | 0.5 | 1.0 | 0.7 | 7.6 | 0.2 | 1.0 | 1.3 | 0 |
Lakenheath HIMT2 | 18.4 | 0.9 | 2.4 | 66.4 | 0.1 | 0.4 | 1.0 | 0.6 | 6.1 | 0.3 | 1.9 | 1.5 | 0 |
Table 1. Typical glass compositional analysis from XRF and SEM-EDS in weight percent.
1 Wardle et al, 2015; 2 Peake, J. 2013. Figures rounded to 1 decimal place
Table 1 shows a typical compositional analysis table. It includes different types of glass from two excavations in Britain: Roman cullet from Basinghall Street, London, (c. 140 – 180 AD), and glass beads from Lakenheath Anglo-Saxon cemetery, Suffolk, (5th to 7th centuries AD) A large proportion of the Lakenheath beads were identified by analysis to have been made using Roman glass of the type found at Basinghall Street. This is the data used in this study to calculate both COE and viscosity.
Glass properties
Before presenting the findings of this study, it is necessary to explain the way glass behaves when it is heated and how its different chemical constituents affect that behaviour.
Viscosity
Glass is unlike water which has a specific temperature point where it changes from a liquid to a solid or vice versa. When glass, as a solid, is heated, it goes through a range of different states as it reaches different temperatures. These are summarised in Table 2.
Viscosity (P) | Description |
1014.5 | Strain point (Above this point, the glass will develop internal stress) |
1013.0 | Annealing point (At this temperature, stress will be relieved inside the glass.) |
107.6 | Softening point (Glass deforms under its own weight.) |
104.0 | Working point (Glass can be shaped and worked and beads can be wound) |
102.0 | Melting point (the glass flows like a liquid – control is lost in flamework) |
Table 2. Glass Viscosity Points (From Vogel, 1994, p.30). Temperature increases from top to bottom]
Viscosity is the measurement of a liquid’s resistance to flow. Therefore, the higher the viscosity, the thicker, stickier, and less fluid the liquid becomes. Heating lowers viscosity and the liquid becomes more fluid, while cooling raises the viscosity.
Poise is the most common unit of measurement of viscosity for glass scientists and uses the centimetre-gram-second scale. Several different instruments are needed to measure the entire viscosity range.
Traditionally, glass scientists have described the viscous behaviour of different glasses using the temperatures corresponding to five ‘fixed’ points. At these ‘points’, flow rates and conditions of measurement are precisely defined by widely agreed protocols. Table 2 indicates these different behaviours without recourse to the full definition. Between these temperatures, viscosity changes gradually and bead-making operations simply become faster or slower.
Viscosity is best shown in graph form. Figure 3 shows the calculated temperatures of the different points of transition for Roman vessel glass cullet - a typical soda lime glass.
Viscosity is shown on the vertical axis in Poise and is a logarithmic scale to express the enormous viscosity changes which occur. Temperature is shown on the horizontal axis in degrees centigrade. The black dotted lines correspond to specific ‘fixed points’ used to describe specific points in viscous behaviour but do not correspond to a step change in behaviour such as occurs for example, when ice becomes water.
Working range: This is the most important factor from the point of view of working the glass and is the range between the softening point and the working point. It is between these two temperature points that glass objects can be made: beads can be wound and decorated, and glass vessels can be blown. Below this temperature, the glass is too stiff to work. Above the working point, the glass will become increasingly less viscous and more difficult to control.
Annealing range: This is the range between the strain point and the annealing point. The strain point is the point where the glass starts to change from solid to liquid when heated. Temperature differences across an object, as it cools through this range, will result in stresses in the final object when it is cold. So, glass must be cooled slowly through this range. Equally, well annealed glass heated too rapidly up to this range will become highly stressed. Above this range, stresses relax increasingly quickly through viscous flow.
These transition points for glass will be at different temperatures for different types of glass. Typical viscosity for different glasses is shown in Figure 4.
Calculating Viscosity
There are various calculators available that can be used to calculate the viscosity of glass at different temperatures and the Fluegel calculator from the website http://glassproperties.com/ was used for this research (Fluegel, 2007a,b).
The weight (by percentage) of different elements in the glass are entered into the calculator which applies a factor depending on how much the presence of each element affects viscosity. The models have warnings that they are crude tools and can only be estimates but are sufficient for this study which only requires the basic properties of the glass to compare types in the practical experiments.
Figure 4 shows a range of different glasses and their viscosities at different temperatures. Silica glass needs the highest temperatures to reach the different points, and modern lead glass the lowest. A long shallow curve shows a long working range, and a more vertical curve shows a short working range, representing a relatively rapid change from the annealing point to the maximum working point. This is shown by the Effetre glass (turquoise line) in the early stages of heating. The Roman glasses (light blue and purple lines) are in the mid-range, along with modern soda lime glass (yellow), suggesting they are very similar.
Sources: Modern commercial glass producers are reluctant to publish their precise recipes, so it has not been possible to find a complete list of the chemical content of the Effetre glass which was used for the bead technique experiments. There is, however, information on the viscosity measurements of a variety of glasses available on websites such as Chatter Glass and the Corning Museum of Glass (see References). Figures from a variety of sources were used to compile the comparison graphs, and these give a reasonable idea of glass properties.
Glass log viscosity | Strain Pt 14.5 | Annealing Pt 13 | Softening Pt 7.6 | Working Pt 4 | Melting Pt 2 | Reference |
Fused silica | 910 | 1050 | 1590 | 1820 | 1723 | Musgraves et al. 2019 |
Borosilicate glass | 500 | 550 | 810 | 1200 | 1650 | Callister and Rethwisch 2009 |
Float Glass COE 83 | 511 | 548 | 715 | 910 | 1400 | Pilkington Tech bulletin ATS-129 |
Effetre COE 104 | 450 | 520 | 670 | 1120 | 1400 | Effetre Glass, Murano, Venice: https://www.effetremurano.com/en/ |
Fusing glass COE 90 | 480 | 520 | 680 | 944 | - | https://chatterglass.wordpress.com /2014/03/23/the-mystery-of-softening-annealing-and-strain-points/ |
Soda Lime | 450 | 480 | 700 | 1000 | 1400 | Glassproperties.com |
Roman Window cullet | 511 | 539 | 715 | 1013 | 1423 | Basinghall St. - SH calcs |
Roman Vessel cullet | 510 | 538 | 715 | 1016 | 1430 | Basinghall St. - SH calcs |
Lead Glass | 400 | 432 | 620 | 910 | 1500 | Glassproperties.com |
Schott 28% lead glass | - | 435 | 630 | 982 | - | Schott glass MDS 8095 |
Levantine I - Peake | 515 | 543 | 718 | 1017 | 1432 | Peake 2012 - SH calcs |
Table 3. Viscosity of Selected Glasses. The figures in Table 3 are guides only and are found to vary slightly depending on the source. The grey shaded area indicates the “Working Range” of the glass or the range of temperatures between which the glass is workable for beadmaking or glass blowing.
Working Range
Glass Type | Working range °C |
Borosilicate glass | 390 |
Float Glass COE 83 | 195 |
Effetre | 450 |
Fusing glass COE 90 | 264 |
Soda Lime | 300 |
Roman Window cullet | 298 |
Roman Vessel cullet | 300 |
Lead Glass | 290 |
Levantine I - Peake | 299 |
EMed I - Peake | 274 |
Table 4. Working Ranges.
This is the most important factor when working with glass, and as described above, it is the difference in temperature between the softening point and the working point of the glass (See Table 4). Glassblowers categorise glasses as “Long Glass” and “Short Glass”. Long Glass can be worked over a wide range of temperatures and is ideal for glassblowing or intricate beadmaking when lots of small adjustments are needed over a period. However, the Effetre glass becomes viscous rapidly, and this can make it difficult to control. Short Glass has a short working range and is most useful for moulding bottles or making sheet glass, where it is desirable to have the glass set relatively quickly. Figure 5 shows the working ranges calculated for different types of glass.
Note how the borosilicate glass has the second longest working range. This modern glass is used for Pyrex ovenware, and its low COE means that it can be heated and cooled without shattering. It is also used for beadmaking but needs a very hot flame. The modern float glass which is made in sheets for window glass and is similar to that used for bottles, is a “short glass” and would be more difficult to use for beadmaking.
Effetre glass has a long working range and a low softening point. But within this range, the viscosity drops rapidly at first, which makes it very fluid quickly. The Roman glass is again in the middle range. This is noticeable when using Roman glass to make beads – it feels stiffer and takes longer to soften in the flame. However, it also stiffens more slowly as it cools, making it an easy glass to work with.
Coefficient Of Expansion
This is a second measurement of glass behaviour and is a measure of how much the glass expands and contracts when it is heated and cooled. It is important to the compatibility of different glasses and gives further indication of the behaviour of glass in the flame. A high COE is usually a soft glass that becomes soft at lower temperatures. A low COE glass is stiffer and needs a hotter flame to melt. The low COE glass is also better for fine added detail because it is relatively stiff and easier to control. This shows how a compromise is needed when making glass objects so that the glass melts reasonably quickly but does not become too soft for adding fine threads of different colours to decorate the objects being made.
COE is measured in ten-thousandths of an inch expansion between the heat range of 20°C and 300°C. For example, a 96 COE glass is one that expands or contracts 0.0096 of an inch (0.24384mm) as it heats up or cools down between 20°C and 300°C. Modern glasses are all given a COE number so that glass workers can be sure to only combine glasses of similar expansion ratings in their work. If different glasses are used, the finished object will be liable to crack on cooling, however carefully it is annealed. This is because different shrinkage rates will cause adjacent pieces of glass to pull away from each other.
An example of this is seen in a group of Early medieval beads found in several sites across Eastern England (See Figure 6). The white beads were decorated with translucent blue trails and red dots, but because the blue and white glasses are of different COE, the blue trails have dropped out. The red dots remain, which suggests that there was compatibility between the white and red. Calculations from the XRF analysis of the white glass show a COE of up to 106 – indicating a very soft glass which would contract a lot on cooling. The red and blue glass was unfortunately not analysed in the study.
Calculating Coe
The COE of glass can be measured using a dilatometer. This will measure the linear expansion of glass at different temperatures. It is also possible to calculate the COE of glass theoretically using the elemental content of the glass in the same way that viscosity is calculated. Glassworking manuals give the necessary tables for beadmakers to calculate the COE of the glass they are using. Each oxide is given a factor that must be multiplied by its weight percent in the glass. Oxides that raise the COE will have higher factors than those that lower it. For example, in the widely used English and Turner tables (Halem, 1996, p.24), silica is given a factor of 0,05 while soda is 4,32. The only way to be certain that two glasses are compatible is if they came from the same furnace batch, although physical tests can be used as well (see below).
Table 5 shows the stated COE of examples of different types of modern glass. Modern art glass manufacturers always give the COE of their glasses so that glass artisans can avoid incompatibility problems, but most beadmakers use the glass from a single manufacturer to be on the safe side. It also gives beadmakers an indication of the behaviour of the glass. The reported COEs for modern glasses are a guide to their viscous behaviour, which is not reported. Typically, glasses with a high COE are also softer, having a lower glass transition temperature. Both properties are linked to weaker bonding of the structure.
The most common COE glass used for lampwork beads is 104 COE. This gives a good compromise of glass that melts easily in the flame but is stiff enough for detail. Satake glass from Japan, at 125 COE, is described by modern beadmakers as very soft, melts at a very low temperature and remains soft until it is almost cool. Adding fine detail with this glass is difficult. Borosilicate glass is used widely for beadmaking, but it needs a very hot flame.
How much was known in antiquity about this is hard to assess, and practical tests for stress in Roman glass for this study have shown stress in the glass cullet (See Test 2 below). Nonetheless, glassworkers must have been aware of the problem when the glass shattered more easily on cooling and fractures appeared where handles joined vessels or bead trails and dots fell out. They would also have been sensitive to the working properties; if a glass is too soft, it is difficult to control; if it is too hard, it takes longer to work and needs a hotter flame.
COE is useful to identify similar types of glass but needs to be used alongside measurements of viscosity when assessing glass behaviour in the flame. Glass with higher COE is more likely to be fragile on cooling; lower COE glass is normally stronger.
Glass | COE |
Satake Glass rods (Japanese) - Lampwork | 125 |
Effetre / Moretti sheets and rods (Italian); CIM rods (USA) - Lampwork and fusing | 104 |
Spectrum System 96; Uroboros 96 (USA) - Fusing | 96 |
Bullseye; Uroboros 90 (USA) - Fusing and lampwork | 90 |
Float glass (used for windows and most bottles). | 82 to 87 |
Borosilicate (Pyrex) | 32.5 |
Table 5. Modern glass types with stated COE
Glass | COE |
Roman vessel cullet from Basinghall St - naturally coloured fragments1 | 87 |
Roman vessel cullet from Basinghall St – clear1 | 99 |
Lakenheath Beads Roman base glass average2 | 96 |
Lakenheath Beads E Med I base glass average2 | 103 |
Lakenheath Beads E Med II base glass average2 | 102 |
Lakenheath Beads E Med III base glass average2 | 102 |
Lakenheath Beads HIMT base glass average2 | 100 |
Lakenheath Beads Levantine 1 base glass average2 | 88 |
Table 6. COE calculated by the author from published chemical analyses of selected ancient glasses. 1Wardle et al 2015; 2Peake 2013
Table 6 shows the COE calculated for a range of ancient glasses from elemental data. It is remarkable how close the COEs are to modern glass and each other. This suggests that ancient glassmakers were adjusting the ingredients in the glass melt to create glass that was easy to use in the flame or furnace. This can be done by adding ingredients that lower the melting point of the glass, such as extra soda (flux) or lead. More silica in the mix will make the glass harder.
It is interesting that some of the later glasses sampled from beads at Lakenheath have a higher COE than the Roman base glasses. These are EMed I (c. 450 to 580 AD), EMed II (6th and 7th centuries), and HIMT (4th and 5th centuries). Could this be a deliberate attempt to make glass that was easier to work in the flame to make the colourful polychrome beads? Levantine I (4th to 7th centuries) has a much lower COE but was only used for a small number of beads at Lakenheath, mostly imported types (Peake, 2013)1 .
Modern Artisan Glassworking
There are three main types of hot glass craftsmanship today:
- Lampworking - making beads over an open flame.
- Fusing - making vessels and other objects by forming glass in a kiln.
- Glassblowing - making vessels and sculptures using a larger furnace.
Today, beadmakers usually use glass rods to make beads. Figure 7 shows rods supplied by Effetre or Moretti glass made in Italy. Their COE is 104, so they are a relatively soft glass that works well in the flame. Different colours may be slightly softer or harder due to the different oxides used to colour the glass.
Fused glass artists use sheet glass in a large variety of finishes and colours. Glassblowing glass comes from manufacturers who specialise in that type of glass.
Practical Experiments
Viscosity and COE calculations have shown that the Roman glass cullet is comfortably within the property range of modern artisan glass. This means that a modern glassworker should be able to handle the Roman glass in almost the same way as modern glass.
Practical experiments were carried out on the Roman glass to confirm this. Both fusing and lampwork techniques were used.
The Roman Cullet
The glass used for the experiments is a naturally-coloured translucent blue/green glass cullet from Basinghall Street, London. The glass is very varied, with some of it partially melted (See Figure 8). Many pieces have soil or stone inclusions. Most is in relatively small pieces, from 1-2 g to about 7 g. Two large pieces of c. 35 g and 44 g were also provided. The colour varies from translucent pale turquoise blue to slightly more greenish.
Much of the glass that is identifiable is cullet from vessels, with some pieces showing the occasional section of the rim or foot. The thickness of the vessels varies a lot, with some pieces very fine, one millimetre thick, up to about 5mm thick.
A. Fused Glass Experiments
The properties of glass mean that a fragment heated above its softening point on a flat surface will naturally assume a height of approximately 6mm. This means that glass pieces that are thicker than 6mm will spread and flatten while thinner glass pieces will bead up to 6 mm, drawing their sides inwards. All glass will eventually assume a symmetrical circular outline – in effect, a cabochon. This behaviour of glass is useful when observing how glass of different viscosity behaves when heated. Softer glass will ball up quicker.
TEST 1
This experiment was to observe the behaviour of Roman glass when melted in a small kiln and to visually compare its viscosity to modern glass of known COE and viscosity.
Roman glass: Numbered one to five. Five pieces of 3 g each +/- 0.2 g. All pieces are at least 10mm thick.
Modern glass: prepared samples as follows. All 3g +/- 0.2 g:
90 COE fusing glass - 2 mm thick - 2 layers
Modern bottle glass - unknown COE but normally c. 82. (B) - 2 mm thick. Curved.
96 COE fusing glass - 3 mm thick.
DV = Dalle de verre or architectural billet glass – translucent light blue. Unknown COE. Chunk 5 - 10 mm thick.
82 COE float glass - 2.5 mm thick.
104 COE fusing glass - 3 mm thick.
The glass was arranged on a ceramic kiln shelf that had been covered with kiln shelf paper. At least 10mm of space was allowed between each sample (See Figure 9). The 90 COE glass was only 2 mm thick, so two layers were superimposed to reduce the time needed to reach equilibrium.
The shelf was put on kiln props to raise it above the kiln floor. The shelf was placed so that the Roman glass ran from front to back. Kiln chambers can be slightly cooler near the door, so this was to ensure that the Roman glass was exposed to the full temperature range (See Figure 10).
The kiln was heated at full speed up to 840°C. This took 40 minutes from room temperature. The start of slumping of some of the glass was observed at 830°C - after 35 minutes.
At 40 minutes, the kiln was held at 840°C, and the door opened every 2 minutes to observe the progress of the slumping.
After 7 minutes, all of the glass was observed to have either changed shape or the edges had rounded. The kiln door was propped open, and the kiln crash-cooled to 670°C. This ensures that the glass does not melt any further. The kiln door was then closed, and the glass was allowed to cool slowly to room temperature over 2 hours to anneal it.
This is a standard glass-fusing kiln program that is widely published in glass fusing manuals.
TEST 1 RESULTS
(See Figure 11)
Roman Glass The samples slumped and rounded in line with the modern glasses with COE between 90 and 104. All the Roman samples became rounded and flattened towards 6mm.
Modern Glass The modern glass samples fused mainly in line with the COE ratings:
90 COE Fusing glass: 5.5 mm thickness. Pulled thicker than the 96 COE but was a double layer of glass before fusing. Well rounded.
Bottle glass: This glass appeared to be the hardest (most viscous). It slumped slightly but changed the least, retaining relatively sharp corners and remaining thin (2.5 mm). COE unknown but probably similar to float glass.
96 COE glass: 5 mm thick; rounded more than the 82 but less than the 90 and 104.
DV glass: 6mm thickness but was much thicker to start with. Well rounded. Probable COE = 104.
Float glass COE 82: The second hardest glass. This reached 3.5mm thick, and the corners rounded slightly. It discoloured with a yellowish tinge, which can happen with float glass, which is not intended for remelting.
104 COE fusing glass: 6mm thickness and well-rounded.
Conclusions The Roman glass is of a similar COE and viscosity to the modern samples. It shows the most similarity to 90, 96 and 104 COE glass when fused to a temperature of 840°C, which is the centre of the Working Range of these modern glasses.
TEST 2
This experiment set out to test for compatibility of the Roman glass compared to modern glass of several different COEs using a polarising filter.
This test is a standard one used by glass workers today when a type of glass is unknown, and they wish to check if it will be compatible with glasses of known thermal expansion. Combining incompatible glass in the same object will cause stresses to form even if the piece has been carefully annealed. These stresses can be shown by using polarising filters. Glass is laid on a polarising film with a light behind it. A second polarising film is laid on top and rotated until haloes are seen in the glass. The change in light within the glass shows where the stresses are. Alternatively, an iPad can be used instead because the glass screen emits polarised light. In this case, the glass is laid on an iPad screen that is showing a plain white background. A single polarising film is then held over the glass and turned until the haloes begin to show (See Figure 12).
An initial test on the Roman glass cullet showed that most had stresses within the glass. The glass appears to be broken pieces of vessels.
Figure 13 shows the glass laid on the iPad screen. Figure 14 shows the glass viewed through the polarising filter which was rotated until the haloes of light showed strongest. All four pieces show areas of stress (marked with arrows). This suggests that the Roman glassblowers may not have annealed their vessels properly. They would have been quite fragile as a result. Alternatively, the glass cullet may have been partially melted or allowed to get above 500°C (Annealing temperature) in the storage area if it was near the furnaces. Rapid cooling would have caused the build-up of stress in the pieces.
It was important to use several samples from a single piece of Roman glass to compare like for like, so larger pieces of glass cullet were selected, and each was cut into 1g samples.
A sheet of modern glass of each of the four COE ratings was prepared. Each piece is approximately 20mm wide and 70mm long. These were arranged on the kiln shelf, and a piece of each of the four Roman glass types was placed on each, keeping the same order (See Figure 15).
The fusing was carried out in the same way as before. The fused glass is shown in Figure 16, and the polarised film photograph is shown in Figure 17.
TEST 2 RESULTS
Base Glass | Float Glass 82 COE | 90 COE | 96 COE | 104 COE |
SAMPLE 1 | Cracked = large difference in COE; Fusing minimal = Roman glass has higher working temperature. | Edges fused into the base glass; stress visible. | Fused well into the base glass; less stress than 90 COE. | Fused entirely into the base glass. Very slight stress. Similar COE and working temperature. |
SAMPLE 2 | As above. | No stress; no cracking; not fused into the base layer = similar COE but higher temperature. | Slight stress; glass has fused well into the base. | More stress than for 96 COE; fused well into the base with only a slight dome = different COE and similar working temperature. |
SAMPLE 3 | As above. | Definite stress; edges have fused slightly into the base = Different COE; higher working temperature. | Stress; similar fusing to 96 COE. | Still showing stress but slightly better fused. COE likely higher. Working temperature higher. |
SAMPLE 4 | As above. | Cracked. | No stress; only slightly fused to base. Similar COE, higher working temperature. | Stress but fused well = similar working temp. |
Table 7. Test 2 Results.
The sheet glass is slightly less fused at the bottom of the photograph because that was the side nearest the kiln door. This is impossible to avoid in small kilns but has been considered subjectively when assessing the results: more rounding of the edges at the front of the kiln was likened to slightly less rounding at the back. The float glass again shows yellow discolouration, which is probably from the oxidation of iron impurities in the glass.
The results are shown in Table 7. The grey tint shows the closest for compatibility. When glass cracks, stress is released, so no halo is visible.
TEST 2 CONCLUSIONS
The 82 COE glass produced cracking in all the Roman samples, showing that this was the least compatible glass.
The only Roman glass sample to show full compatibility with modern glass was sample 4 with 96 COE glass. All the other Roman samples showed either cracking or at least some stress in the polarised filter.
Three of the four samples (1, 2 and 4) proved to be reasonably compatible with at least one type of modern glass (see the green shaded cells). Sample 3 showed the least stress with COE 104 glass, which suggests it may have an even higher COE.
This shows that this base Roman glass cullet is very variable for COE. Unlike modern glass that is made to exact recipes in controlled conditions, Roman glass cullet may have had a long history before being broken up for cullet. It would probably have come from different glass-making furnaces across the Roman world and been recycled numerous times before being excavated at Basinghall Street.
Therefore, the Roman glass is of a similar range of COE to modern artisan glass and mostly between COE 90 and COE 104.
B. Lampwork Experiments
TEST 3
This test was an exploration to test the viscosity of both the Roman and modern glasses.
Viscosity is the most important property when working with glass. While COE gives indications of similar and compatible glasses that will combine without stress, viscosity is the property that most affects working with hot glass. Glasses with similar COE can have different viscosity and working ranges. It was therefore important to test the viscosity of the Roman glass and compare it with the calculated viscosity.
The following is a simple test using lampwork techniques to compare how much different glasses moved when melted into the working range.
Step 1: Small pieces of glass, each approximately 1gm, are cut. The pale blue is the Roman glass from a single piece; the black is COE 90 fusing glass. Black glass is used to show the contrast (See Figure 18).
Step 2: The pieces are pre-heated on a tin lid over a candle flame. This prevents the glass from cracking or spitting in the next step (See Figure 19).
Step 3: A pontil (an iron rod similar to a blunt mandrel used to gather and manipulate gobs of glass) is heated, and a piece of black glass is picked up on the end and heated to softening point. A piece of Roman glass is then picked up next to it (See Figure 20).
Step 4: This is repeated to build up alternating layers of black modern and Roman glass (See Figure 21).
Step 5: A clear rod of glass is attached to the free end of the stack to make a handle. The stacked glass is heated until it is uniformly softened, and then the pontil and the glass rod are pulled slowly apart (See Figure 22).
Step 6: The cooled glass, still attached to the clear rod, shows that the Roman glass was more viscous in the flame than the modern glass. Glass with a low viscosity will move further and become thinner; high viscosity will remain thick and resist being pulled (See Figure 23).
The test was repeated with clear Float glass COE 82 using samples from the same Roman glass piece. The viscosity of the Roman glass and the Float glass is shown to be almost the same. The stack pulled evenly and remained the same thickness (See Figure 24). Figure 25 shows the viscosities of calculated examples of glasses that are the same types as the three glasses tested. The working ranges of each are marked with arrows. Float glass has a much narrower working range, but it fits within the working range of the Roman vessel glass. COE 90 glass has lower softening and working temperatures than the Roman glass, which shows why it was less viscous in the test. The Roman glass working range extends to a higher temperature than the other two. However, all three glasses are easily within the comfortable working range of a simple heat source with 715°C to 910°C a shared working range.
TEST 4
This experiment was formulated to test the glass for making beads. This practical test was conducted with several different types of glass to compare and contrast the behaviour of different types of glass when making wound beads over a simple flame.
1. Float glass COE 83 - 3 samples from the same sheet of glass
2. Fusing glass COE 96 - 5 samples from the same sheet of glass
3. Effetre beadmaking glass COE 104 - 5 samples from the same sheet of glass
4. Roman glass - 18 samples. Each sample was taken from a different piece of glass
TEST 4 PREPARATION
Samples of glass of approximately 2g were prepared and pre-heated to 500°C in a kiln to prevent shattering when first held in the blow torch flame. A stopwatch was used to measure the time to reach each stage. The time to wind the bead was not measured as this can vary for mechanical reasons, and the glass is held at the same temperature during the process.
The stages measured were as follows:
1. Time to softening (Figures 26 and 27) A glass piece was removed from the kiln with tongs, held in the flame and pressed onto a heated pontil. The stopwatch was then started, and the time taken for the sample to reach the point where it was soft enough to sag under its own weight and to wind onto a mandrel. This would be 670°C for the Effetre glass and 715°C for the other glasses.
2. Time to round (Figures 28 and 29) The glass was then wound onto a prepared mandrel from the pontil until all was used up. The bead at this point was irregular in shape, with obvious winding lines in the glass. It was then held in the hot part of the flame and rotated. The time was measured from the beginning of this process until the point when the bead became entirely rounded and smooth. Bubbles and inclusions of debris from the Roman glass are visible in the beads.
3. Time to cool: The bead was removed from the hot part of the flame and held at a point where the flame almost ends and is at its coolest point. The bead was rotated to prevent sagging while it was allowed to cool down in the soft flame until all traces of red glow had gone. This is called flame annealing and is a common beadmaking practice to prevent the bead from shocking and cracking as it cools. The time measured was from first holding it in the cooler part of the flame until the red glow had gone. The glow disappearance will be at the same temperature for all types of glass. Therefore, variations will depend on the temperature of the glass at the starting point, indicating a higher or lower working temperature.
TEST 4 RESULTS
The measured times are given in Table 8. It is difficult to identify a particular point when a gob of glass is soft, fully rounded, or has entirely lost its colour, and the results show inevitable variations even between pieces cut from the same glass sheet. However, the data shows at least some indication of the working properties of the glass. Laboratory equipment for measuring temperature would make this a more accurate experiment. All the modern samples of each kind are cut from a single sheet of glass.
Glass | Time to soft mm:ss | Time to round mm:ss | Time to cool mm:ss | g | Comments |
Float 1 | 01:30 | 01:11 | 00:32 | 2 | All samples from the same glass sheet. The stiffest glass. Slow to soften. I had to really push to get it to wrap round the mandrel. Lost red glow more quickly than other glasses. |
Float 2 | 01:24 | 00:59 | 00:37 | 2 | |
Float 3 | 01:23 | 01:01 | 00:26 | 2 | |
Fusing 96/1 | 00:41 | 00:36 | 00:37 | 2 | All samples from the same glass sheet. Felt slightly stiffer than 104 COE glass. All times are longer to reach the different points. Overlaps with the properties of some of the Roman glasses. |
Fusing 96/2 | 00:40 | 00:22 | 00:28 | 2 | |
Fusing 96/3 | 00:45 | 00:20 | 00:39 | 2 | |
Fusing 96/4 | 00:41 | 00:31 | 00:34 | 2 | |
Fusing 96/5 | 00:38 | 00:24 | 00:31 | 2 | |
Effetre 104/1 | 00:31 | 00:23 | 00:21 | 2 | All samples from the same glass sheet. Much softer. Very much quicker to work. Heated up quicker, and cooled quicker compared to the other glasses in the study which is because it can be worked at a lower temperature than the other glasses. No stiffness when winding. Delicate work more difficult with a basic torch. Modern torches provide the control required for this type of glass. |
Effetre 104/2 | 00:45 | 00:27 | 00:21 | 2 | |
Effetre 104/3 | 00:32 | 00:23 | 00:22 | 2 | |
Effetre 104/4 | 00:37 | 00:27 | 00:20 | 2 | |
Effetre 104/5 | 00:35 | 00:26 | 00:23 | 2 | |
Roman A1 | 00:59 | 01:23 | 00:51 | 2.7 | All samples from different pieces of cullet. All these samples felt stiff in the flame and took time to soften. Cooling time was long as well. These are all from different pieces of cullet and show much variation in timing. However, the working properties of the samples were similar in the flame, even if it took different times to reach softening point etc. A few felt stiffer when being wound: B4, B7 and B8. |
Roman A2 | 00:51 | 00:47 | 00:51 | 2.3 | |
Roman A3 | 01:03 | 01:24 | 01:02 | 2.6 | |
Roman A4 | 00:55 | 00:47 | 00:59 | 2.4 | |
Roman A5 | 01:32 | 01:21 | 01:05 | 2.8 | |
Roman A6 | 01:04 | 01:04 | 01:03 | 2 | |
Roman A7 | 01:05 | 01:10 | 01:10 | 2.4 | |
Roman A8 | 00:58 | 01:04 | 00:59 | 2.7 | |
Roman A9 | 00:42 | 00:38 | 00:55 | 2.3 | |
Roman B1 | 01:13 | 00:42 | 01:04 | 2.1 | |
Roman B2 | 00:52 | 00:50 | 00:48 | 2.3 | |
Roman B3 | 01:04 | 00:49 | 01:02 | 2.1 | |
Roman B4 | 00:54 | 01:15 | 00:49 | 2.5 | |
Roman B5 | 00:46 | 00:56 | 00:45 | 2 | |
Roman B6 | 01:01 | 01:04 | 00:47 | 1.9 | |
Roman B7 | 01:00 | 01:28 | 00:49 | 2.1 | |
Roman B8 | 01:34 | 00:55 | 00:41 | 2 | |
Roman B9 | 01:47 | 01:03 | 01:17 | 2.8 |
Table 8. Time Comparisons of Beadmaking stages of different glasses in the study. Times are mm:ss.
(See Figure 30)
Float glass 83 COE: 2 g samples cut from a single sheet. Softening time is the longest, then rounding time, then cooling time. The profile of the graph for float glass samples was similar to Roman glasses A5 and B8.
96 COE: 2 g samples cut from a single sheet. Rounding time was the shortest in all 5 samples. Softening time was the longest, then cooling time. Profiles similar to Roman glasses A2, B1, B3, B9.
104 COE: 2 g samples cut from a single sheet. Same profile as float glass, but times were much shorter throughout. Similar timings to 96 COE glass.
Roman glass: 2 g samples from different pieces. Highly varied throughout and times recorded were longer than for the 96 and 104 COE glasses. Many of the samples showed very different profiles to the modern glass. This suggests that the broken vessels that made up the cullet came from many different batches of glass.
How Different Is the Roman Glass?
Despite the differences between the samples of the Roman glass, the author found all the Roman glass samples were easy to work for beadmaking. It took a longer time to achieve each stage compared to the modern glass, but the glass was controllable and a pleasure to work with. The differences in the profiles shown above did not appear to affect the feel of the glass in the flame; some glasses just took slightly longer to reach different stages than others. The times involved are only in the region of 30-40 seconds, which are barely noticeable when working on a bead.
After experiencing the Roman glass, the modern 104 COE glass, in particular, felt difficult to control in comparison. This is remarkable because this type of glass is specifically made for beadmaking and is widely used by lampworkers worldwide but the torch used in the study was basic and not adjustable in order to simulate ancient beadmakers’ heat sources. Modern sophisticated torches can be used at lower temperatures and give control of the flame to prevent glass with a low softening point and shorter working range becoming too hot and fluid.
Did the Roman glassmakers adjust their base glass to make it more suitable for crafting? The suggestion from these results is that they did. It could have been done in a relatively unscientific way by simply adding materials to the base glass that were known from experience to make the glass more easily workable. For example, the melting temperatures of glass can be lowered by adding more soda during primary glass-making or raised by adding more silica. Beadmakers colouring their glass by melting in metal oxides could alter the glass properties depending on which oxides they used.
Conclusions
This experiment began as an investigation to see if the modern lampworkers’ glass used for replicating ancient beadmakers’ techniques has similar working properties to ancient glass. The experiments produced a range of results that showed that the Roman glass was broadly similar in working properties to modern glass. In the practical beadmaking tests, the Roman glass cullet proved to consist of many different types of glass that showed a variety of small differences when worked in the flame, both between the samples and when compared to modern glass. These working properties were still within a comfortable range for beadmaking.
A series of tests was devised in order to quantify the differences between modern glass and the Roman cullet used for the tests. The tests were in the following sequence:
- The glasses were compared theoretically using published elemental analysis tables for ancient glass and published figures for modern glass. The COE and viscosity of the samples were calculated using calculation tables from glass technology literature.
- The glasses were next put through a series of fusing tests to see how they reacted in the controlled heat of a kiln.
- Polarising film was used to show stresses in the glass to identify different COE ratings between the Roman glass and modern glasses.
- Finally, dozens of beads were made using different samples of Roman glass. Time was measured for the glass to reach different stages of viscosity. The beadmaker’s comments on the behaviour of each sample in the flame were also recorded.
The conclusions were as follows:
- Calculations from elemental analyses of Roman glass show that it shares a middle range of COE with modern artisan glasses and is mostly in the range of 90 to 105 COE.
- Viscosity calculations in the same way show that the Roman glass is similar to modern artisan glasses with a working range of temperature that would be comfortable to most modern beadmakers.
- Beadmaking using the Roman glass was surprising because it showed that while the glass was largely more viscous in the flame than modern lampworkers’ glass, it was extremely pleasing to work with. The beadmaker felt that overall, the samples tested gave more control over beadmaking than modern glass when used with a basic torch.
This experiment has demonstrated that there is far more to look for in ancient glass than purely elemental analysis. Testing ancient glass in the flame is a successful way to analyse the techniques of the ancient beadmakers. This could be applied to all types of glass working.
Future Work: The Working Properties and Colourants
Glass viscosity and COE are affected by the addition of colourants to the base glass. The Roman glass tested for this paper was naturally coloured vessel cullet and not the highly coloured opaque glass used for polychrome beads. The next stage in these experiments will be to look at the calculated viscosity of different colours of glass to see how much the metallic oxides such as lead and copper affect the handling of the glass. The working properties of modern glass vary between colours; for example, white glass is less viscous in the flame compared to other colours in the Effetre range. It is possible that the addition of lead to make red glass would affect the handling of the glass, but ancient red beads do not show a lessening of control in their making, so it is expected that the differences would be noticeable but not a hindrance to an experienced beadmaker.
The addition of metallic oxides to the remaining samples of Roman glass to compare behaviour in the flame will be part of the continuation of this project.
Acknowledgments
I am very grateful to the following: The Museum of London Archaeology for providing me with the Roman glass from Basinghall Street for this project. John Parker, Emeritus Professor, Dept of Materials Science and Engineering, University of Sheffield, who kindly checked the glass science and made many helpful suggestions. Professor John Hines and Dr Robert Anderson for technical advice and encouragement on this project. Dr Hajnalka Herold, University of Exeter, for all her help and advice.
- 1Peake’s 2013 thesis calls EMed I and EMed II glasses by their old names Saxon I and II.
Country
- United Kingdom
Appendix 1
Replica Tools used in the Experiments
As well as a heat source, few tools are needed to make and decorate beads of the kinds made in early medieval Britain.
Mandrels for winding the glass onto to make the beads; a knife for smoothing (called marvering); tweezers to pull thin threads of glass for decoration; tongs for shaping beads. Spare mandrels can be used as pontils which are tools used as handles for melting glass pieces onto. The soft glass is then wound onto the mandrel (See Figure 31)
The Blow Torch used in the Experiments
The Hothead Blowtorch is widely used by lampworkers. It is a single fuel burning torch and uses propane gas. The estimated maximum temperature of a torch of this type is 1100°C to 1250°C while an dual gas torch can be up to 2550°C. For this most modern lampworkers will use a dual gas torch that combines oxygen with propane and reaches much hotter temperatures (See Figure 32).
Softening glass in the flame to make beads is a combination of heat and the time in the flame. A lower temperature torch such as a Hothead can melt harder glass such as borosilicate (softening point 810°C) but it will take some time for the glass to reach softening point and the working range of temperature. Soft glass such as Effetre 104 (softening point 670°C) which has a much lower softening temperature can be melted quickly.
The Hothead torch was used for these experiments because it was considered to have a more similar temperature range to the small volcano furnaces that were probably used for early medieval beadmaking. (Heaser, 2022).
Bibliography
Barfod, G.H., Feveile, C. and Sindbæk, S.M., 2022. Splinters to splendours: from upcycled glass to Viking beads at Ribe, Denmark. Archaeological and Anthropological Sciences [e-journal] 14, 180. < https://doi.org/10.1007/s12520-022-01646-8 >.
Chatter Glass, 2014. The Mystery of Softening, Annealing and Strain Points. [online] Available at: < https://chatterglass.wordpress.com/2014/03/23/the-mystery-of-softening-annealing-and-strain-points/ > [Accessed 25th October 2023].
Corning Museum of Glass, 2011. Chemistry of Glass. [online] Available at: < https://www.cmog.org/article/chemistry-glass > [Accessed 25th October 2023].
Fluegel, A., 2007a. Glass Viscosity Calculation Based on a Global Statistical Modeling Approach. Glass Technology - European Journal of Glass Science and Technology Part A, 48(1), pp.13-30. [online] Available at: < http://glassproperties.com/viscosity/Viscosity_2006_AFluegel.pdf > [Accessed 25th October 2023].
Fluegel, A. 2007b. Statistical Calculation and Development of Glass Properties. [online] Available at: < http://glassproperties.com/ > [Accessed 25th October 2023].
Fluegel, A. 2007c. Glass Viscosity Calculation. [online] Available at: < http://glassproperties.com/viscosity/ > [Accessed 25th October 2023].
Halem, H., 1996. Glass notes – A reference for the glass artist. Kent: Franklin Mills Press.
Heaser, S., 2018. Anglo-Saxon Glass Beadmakers: A New Look at the Tools, Materials and Techniques. [online] Available at: < https://www.researchgate.net/publication/339178110 > [Accessed 25th October 2023].
Heaser, S., 2022. Bead Furnaces in Anglo-Saxon Britain: An investigation into the likely sources of heat used by beadmakers in the 5th to 7th centuries CE. [online] Available at: < https://www.researchgate.net/publication/354986153 > [Accessed 25th October 2023].
Kervin, J., 1999. More Than You Ever Wanted to Know About Glass Beadmaking. GlassWear Studios, Livermore, CA, USA.Peake, J.R.N., 2013. Early Anglo-Saxon glass beads: Composition and origins based on the finds from RAF Lakenheath, Suffolk. PhD Thesis, Cardiff University.
Vogel, W., 1994. Glass Chemistry. Springer-Verlag Berlin and Heidelberg GmbH & Co. K. 2nd revised edition.
Wardle, A., Freestone, I., McKenzie, M. and Shepherd, J., 2015. Glass Working on the Margins of Roman London – Excavations at 35 Basinghall Street, City of London, 2005. MOLA Monograph 70. London: Museum of London Archaeology.