The content is published under a Creative Commons Attribution Non-Commercial 4.0 License.
Reviewed Article:
The Production of Roman Metal Screw Threads - Extended Version
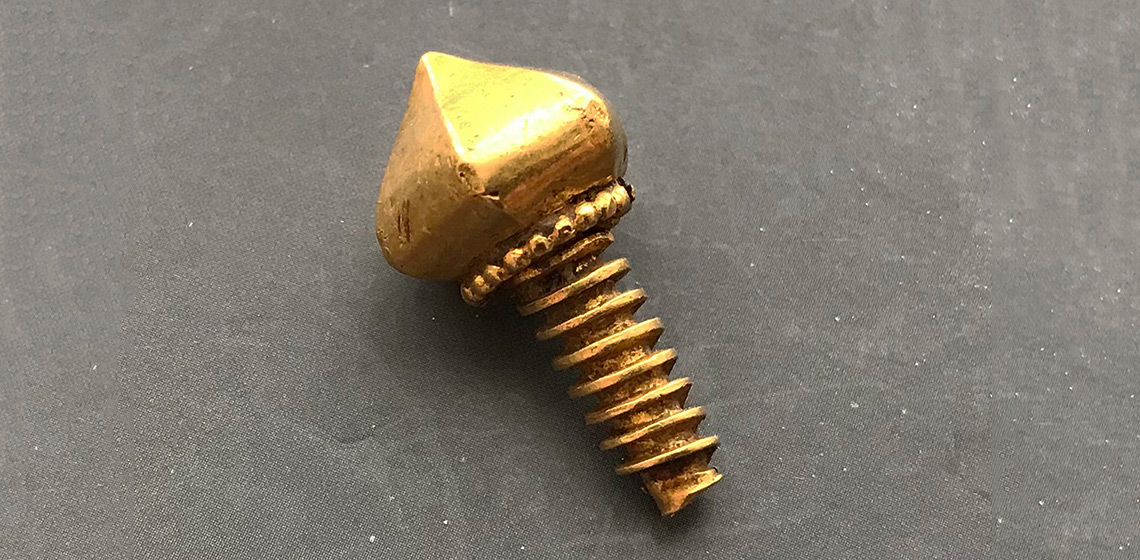
During the Roman period, small metal screw threads were used both as fastenings and to impart motion. This paper, which is an extended version of my previous article, will show that it is possible to produce metal screw threads using very simple technology. The tools and expertise to carry out this work is well within the skills of any competent metal worker. Small metal screw threads can be produced by semi- and unskilled labour, in a time frame that makes their production economically viable.
Introduction
History
The invention of the screw thread is traditionally attributed to Archytas of Tarentum (c 400 BC). However, the first definite information on it concerns Archimedes (c. 287 - c. 212 BC) but this may be a false attribution (Singer et al., 1957; Paipetis and Ceccarelli, 2010). The Archimedes screw was used to raise water. Both Diodorus Siculus (1st century BC) and Vitruvius recorded that water-screws or water-helices were used in Egypt for water supply in cities and military camps near the River Nile. Archimedean screws and large screw threads are well attested from the Roman period. Archimedes was able to launch such an enormous ship by means of a device involving a screw; possibly he was the first to invent devices employing the force of the screw.
Screw threads made from metal were made both in Greece and Rome (Burstall, 1970, p.77; Singer et al., 1972, pp.631-632). There are classical references to the use of screw threads. Pliny describes their use (as noted above). There are examples of metal screw threads in existence from the Roman period. "the screws used in ancient worm gears were usually bronze.
Classification of screw threads
Screw threads can be classified into two distinct types: motion screws and fastening screws. Motion screws are used for the transmission of mechanical power. In contrast, the fastening screws are designed to unite two or more components.
Motion screw threads
In the Roman period, motion screws were used for wine and olive presses or raising water with an Archimedean screw (See Figure 3). These threads were generally made of wood. However, there are examples of small metal threads being used to impart motion; these can be found on Roman surgical instruments, such as the vaginal speculum (See Figure 11). (Square threads and V-threads can both be used to impart motion.)
Fastening Screw Threads
In contrast, the fastening screws are designed to unite two or more components. Fastening threads come in two forms: male and female threads. These threads can be left or right-handed. A right-handed thread is tightened by turning clockwise and a left-handed thread is tightened by turning anti-clockwise.
Fastenings
There are two kinds of fastenings, permanent and semi-permanent. Nails and rivets are permanent fastenings, in that they are not designed to be undone, whereas screw threads are semi-permanent joints, in that they can be removed.
Fastening threads come in two forms: male threads [bolts] and female threads [nuts] (See Figure 13).
Left and right hand threads
There are two different types of thread, left hand and right hand. Turning it clockwise tightens a right-hand thread, a left hand thread is tightened by turning it anti-clockwise (See Figure 14).
Thread forms in the Roman period
In the Roman period there were two principal thread forms: square threads and V-threads. (See Figures 2, 32 and 34). These were probably the only two, although there are many different thread forms in use today.
V-form threads
V-form threads are known from were used in the Roman period as both fastening devices and as a means to transmit power and motion.
V-form threads to impart motion
V-form threads used to impart motion are mentioned by the following in the following sources:
- Upright screw-operated presses (Gichon, 1979).
- Screw and lever press (Pliny, Natural History 18,: lxxiv, p.. 317; Patton and Myres, 1898).
- An example of another use is ancient oil presses (Drachmann, 1932).
Motion threads are most commonly evidenced in devices such as wine presses (Schürmann, 1995, pp.64-67; Vitruvius, 1998, 6.6.1) and Archimedean screws (Vitruvius, 1998, 10.6.1; Landels 1978, pp.58-64; Schürmann, 1995, pp.56-61).
The Archimedes screw thread was known as a means of raising water during the Roman period, although it is known to have existed long before the Roman period. (Tuplin and Rihil, 2002)
V-form fastening threads
Threads with a V-form were known in the Roman period, as can be seen in the travelling lamp holder seen in Figure 3 This was found during excavations in Herculaneum, giving a terminus ante quem of AD 79. The shaft comprises four cylinders, joined together with male V-form screw threads. When the whole shaft has been assembled it is held in place by a fifth screw that holds the base and the shaft in place. 136.3 cm (See Figures 4 and 5).
From this example it is clear, that at a date sometime before AD79 the Romans were producing V-form threads and were using them as a method of joining components together.
Roman V-form wood screw
Figure 5 shows an example of an incomplete Roman iron screw thread that measures 157mm and weighs 64g. This example was originally found embedded in wood at Silchester, however the wood has since been lost.
This screw thread type was typically, for used in wood, found at Silchester, measuring 157mm and weighing 64g; the thread lacks the head. The as indicated by the pointed end, and would have had an average outside diameter of the complete threads is 13mm (See Table 1) when complete. . It retains 23 convolutions and a cone shaped tip (1.5 convolutions [threads] per cm; the average thread angle is 68º). Because it has a point at one end, this indicates that it is a wood screw. When it was discovered, it was embedded in wood; the wood has since been lost.
This screw would have had a head on it, which would have allowed it to be screwed in, However, as the head of this example is missing The nature of the missing fragment is a matter of conjecture. It is therefore unclear how long the screw originally was, and how it was screwed into the wood.
Average diameter | Variation from mean diameter | Range | ||
Outside diameter | 13.04 | +0.04 | -2.04 | 2.08 |
Core diameter | 9.46 | +2.54 | -1.46 | 4.00 |
Thread pitch | 4.18 | +1.22 | -0.68 | 1.90 |
Table 1. Measurements of the Silchester wood screw (in mm).
Figure 7 shows that the thread remains intact on both ends of the screw fragment; however, the centre section shows considerable wear. The centre section of 44mm shows considerable mechanical abrasion along one part of the circumference (See Figure 8).
The unusual wear pattern is suggestive of a reciprocating motion rather than a rotary motion. This could be the result of repeated lifting and falling such as could be found on a latch (See Figure 9).
If this was how this kind of thread was used, it would mean that they were not considered expensive items and were therefore easily available. To test this proposition/hypothesis, it was decided to make a replica to determine the time taken to produce this type of thread.
Production sequence
- The bar is rough forged into a cylinder
- The bar is forged between swages into an accurate cylinder
- A taper is forged on one end of the bar
- The thread is cut using a file.
Results of experiment
Stages of manufacture | Time (minutes) |
Forging time [stages A + B + C] | 9 |
Production time to cut 24 threads | 96 |
Total production time | 105 |
Table 2. Production times for one man working alone.
The timings shown in Table 2 can be reduced. The forging time can be reduced to 4 minutes if several bars are worked in rotation. Furthermore, it is possible to reduce the time taken by training semi-skilled labour to perform the task of thread making.
An unskilled person was trained to cut threads by hand in just under three hours. At the end of that time, they were capable of working unsupervised and within a day could produce a screw thread in one hour of the same dimensions as the Silchester thread. A workforce devoted exclusively to forging and cutting threads could therefore have been made up of unskilled labour.
Assuming a working day of 12 hours, each worker would produce 12 screws of the Silchester type in a day. Assuming a working week of six days, a single worker could produce a up to 72 threads per week and workforce of twenty around 1440 a week. If the labour force was trained to perform this task alone, the cost will be low, making it a viable option.
Summary
These experiments have shown that screw threads such as the one found at Silchester could potentially be produced in large quantities by unskilled labour, thereby making their use economical.
Square form threads
Square form fastening thread
There are also small square threads that were widely used in jewelry in antiquity.
- For example, the British museum, London has a thread of the screw bolt from a fibula1 (catalogue number A7).
- There is also a gold screw thread belonging to a crossbow fibula, found at Richborough England - now in the British Museum.
- There is another crossbow fibula from the Mory Firth Scotland. Catalogue number 1962.12-15.1
- In the Louvre Museum, France there is a square thread on a bracelet.
- In the Metropolitan Museum of Art, New York there is a square thread on a bracelet.
- In the Staatliche Museum Berlin there is a square thread1.
- In the Paul Getty Museum USA there is a square thread.
These small screw threads demonstrate that in the Roman period their use as motion screws and fastening screws was clearly understood.
Square form motion threads
The examples of jewellery and the speculum show that the concept of using square threads to impart motion was clearly understood in the Roman period
As can be seen in Figure 12 the male thread engages with a pin, set in a housing.
As the screw is turned, it causes the jaws of the speculum to open. The thread can have variation in its pitch. However, because the thread is only engaged at a single point, any such errors are not detrimental to the operation of the instrument. As long as the jaws open with a smooth motion, any small inaccuracies will be of little consequence. The manufacturing methods used to make square threads are covered later in this article. Another device that incorporates several screw threads is Hero's book 'Dioptra'. The dioptra is a levelling instrument, combining a theodolite and water level.
Manufacturing methods to produce screw threads
The following experiments were conducted to consider methods of manufacture that could have been used to make screw threads in the Roman period. These experiments will consider the production of two different types of screw thread. Square threads and v-threads, the difference between the two is shown in Figure 2.
In antiquity screw threads were probably made by one of two methods.
- Metal removal
Male threads are cut into a bar; this removes metal. The female thread is cut into a hole, in a piece of metal, this will become the nut. - Fabrication
Threads can also be made by making the thread separately from the core and then soldering them together.
Experiments to reproduce screw threads
Square male threads (bolts) (See Figures 10 and 16)
In this set of experiments only tools known to have existed in the Roman period were used.
There are formulae to determine the ratio of the sizes of modern screw threads; however, these have not been consulted in these experiments. They were made using a much less scientific principle, namely, 'if it looks right, it probably is right'. This is a principle that engineers have used since time immemorial and has generally proved to be correct. (The lead author has no doubt Roman makers of threads made use of this principle.)
In antiquity some threads were produced as one offs. Such threads can be seen as the large threads used on wine presses (See Figure 3). It seems likely that small fastening threads may have been made in small quantities (batch production).
Batch production
In batch production similar items are produced together. One person does one component then passes on to another person for the next task to be performed. For example; in nail making, one man will put the point on a bar, then cut it to length. It is then passed it on for someone else to put the head on.
Mass production
In mass production, a large number of components are produced to high tolerances. This means parts are interchangeable. For example: the crank shaft of a particular model of Jaguar car, will fit into the engine of any other car of that make and model.
Proof of concept
In order to establish proof of concept, the initial experiments were conducted on wood.
Experiment
The first experiment was to reproduce, in wood, a copy of a square thread as use on the speculum shown in Figure 11. From Figure 16 it can clearly be seen that a square thread can be produced on wood using a miter block.
Producing a metal square thread using a miter block.
There are examples of square threads surviving from antiquity (such as the speculum shown in Figure 11). On some surgical instruments the threads are clearly square threads, that have been produced by filing (See Figure 18)
The hook had been exposed to the elements for three years and it is still capable of supporting the same weight as it did when first tested (see Figure 19).
Forging and filing
The next experiment was to twist a bar hot (700℃) and then file the thread sharp. A length of 8 mm square bar was twisted hot, at a temperature of 700℃ over a length of 75 mm. A length of 30mm was filed to produce sharp threads. The filing took 41 minutes.
Cutting a male V-thread freehand
Results
Total time to produce a V-thread of 10 mm diameter by 60 mm long with an average pitch of 8.28 mm + 0.40 -0.19 was; 1 hour 45 minutes (See Figure 20).
It can be seen from Figure 21 that, visually there is very little difference between a handmade thread and one produced with a modern die. Given that there are so similar it is likely that threads from the Roman period found in the archaeological record have been miss-identified as modern manufacture and, sadly discarded.
Making internal V-thread [nut]
Methods to produce nuts
Hero's thread cutting machine (See Figure 22) is an effective way to produce internal screw threads, (nuts) however, it is a slow method.
Several methods were examined for the production on small diameter V-nut threads. In the production of nuts today the thickness of the nut is the same dimension as the diameter of the male thread.
There are many possibilities as to how a nut can be produced, and what materials it can be made from. One possibility is that metal male threads could have been used with nuts made of wood, probably a hard wood such as oak.
The thread used in this experiment was 10mm diameter and the core diameter 7.62mm. The amount of thread engaging with the nut was 1.19mm on each side (See Figure 23). Working on the assumption that the nut height [thickness] is equivalent to the diameter of the screw, and then, if the bolt and nut are made of metal, only five threads inside the nut is enough to support the weight.
Wooden Nuts
In the first experiment it was decided make nuts from wood. The first nut was made from a block of oak, thick enough to have eight threads in the thickness of the nut.
To make the thread a hole of 8.0 mm in diameter was drilled into a block of oak.
The metal thread was then screwed into the block. This was accomplished by turning the screw one revolution clock-wise, then three quarters of a revolution anti-clock wise. The anti-clockwise rotation is to break off the wood that is trapped in the thread. When the thread was cut to its full depth, it was unscrewed and all the wood trapped in the threads was brushed off. The rest of the thread was then completed. When it was in place it was tested, by two men pulling on it with a rope. It did not move. The block was then cut in half to show the thread (See Figure 24).
Nuts made from wood reinforced with metal
In the second experiment the wood was reinforced with an iron plate on each side, as can be seen in Figure 25.
In the next experiment two pieces of brass 2.80 mm thick were tapped using the tapered tap. The tap did not show any wear after use. This is to be expected as iron is harder than brass. The plates were riveted to the wood and then the wood was tapped. As can be seen in Figure 26.
Nuts made from several sheets of iron
The tap was used to try to cut a thread in a 2mm thick sheet of iron. It was not possible. However, experiments have shown that a thread can be cut into a piece of iron 1 mm thick. Using a male thread as a tap would not work on iron greater that 1 mm thick but it can be done on brass up to 3 mm thick (See Figure 27 and 28).
Testing the thread
Tests on the nuts
To test if the screw and nut assembly is to an acceptable standard, the nut must travel the length of the thread without sticking. All screw and nut assemblies passed the test. All three nuts were tested and all supported a weight of 158.76 KG (25 stones) (See Figure 29).
Tests on the male threads
The bar with the hand cut V-thread had the opposite end of the bar threaded using a modern die. A ring bolt was attached to it, as can be seen in Figure 30 The hand cut threaded section was screwed into an oak post.
Results
This thread was tested in the same manner as before and supported a weigh of 25 stones (159 KG) with no sign of giving way.
Summary
It can be seen from Figure 21 that there is very little difference between the two threads when viewed by eye. The two threads were shown to professional engineers, who was unable to tell the difference between them.
Making male and female threads by fabrication
Threads can be produced by fabrication. The thread is made separately, and then fixed to the core, usually by soldering. It was decided to make threads in brass. To establish that these methods are viable they were first tried out using copper because it is malleable and ductile and has similar working properties to the brass that will be used in later experiments.
The coil was prized open with a small tapered copper lever. Since they are made from the same metal, copper was used so as not to damage the coil, The pitch of the coil was gauged using a spare piece of wire the same thickness as the coil wire. The coil was then hard-soldered to the copper rod (See Figure 31).
A brass nut was bored out to the same diameter as the outside diameter of the coil. The coil was then soldered into place. It was found that the screw and nut fitted together with very little slack. These first experiments showed that this method can be used to produce a male and female thread.
Measurements of copper square thread
Position | A | B | C | D | E | F | Maximum variation |
Pitch (mm) | 4.02 | 3.90 | 4.05 | 4.42 | 3.89 | 4.00 | 0.13 |
Table 3. Pitches of square threads shown in Figure 33.
Maximum variation 0.5mm
A modern credit card is 0.75mm in thickness. A variation of 0.5mm means the pitches are to a high level of accuracy (See Figure 33).
Making square threads from brass
The next sets of experiments were used to determine the times taken to make the threads and the two alternatives to producing the wire. To establish proof of concept, this set of experiments was again conducted on copper wire. The next set of experiments was to determine how easy it was to make square threads from brass.
Fabricating square threads from brass (See Figure 36 and 37)
To ensure that the gaps between the coils are equal, a jig was made. It has a wooden shaft with a pin at 90° to the long axis. The spiral is engaged with the pin and rotated along the long axis (See Figure 35).
This is a very simple jig. However, if a large number of coils were required, making this design of jig from metal would be a simple task. This jig was used to produce all the coils used in these experiments and shows no sign of wear.
A length of brass wire was drawn down into a cross section of 1.62mm, the same as in previous experiments. It was wrapped round a mandrel to form a coil. This was twisted over the pitch jig producing a coil with even spaces (See Figure 39)
Testing threads
Screw threads are used as fixing devices and must be able to withstand a level of force that will enable them to fulfil this function.
To determine the force required to bring about failure the threads produced for this paper were subjected to testing.
A torque wrench was used to find the breaking strain on the fabricated thread. It failed at 1.38kgm. The internal thread was intact but the male thread failed due to the solder failing (See figure 38).
Fabricated v-threads
(See Figure 40)
Fabrication Method
This v-thread was made from brass wire in the form of an equilateral triangle. The included angle of the thread will be 60°. The angle of a Whitworth thread is 55° therefore it is possible they may have similar characteristics in their tensile strength. The former for the v-groove was made by filing a groove in the shape of an equilateral triangle into a piece of mild steel 12mm square. The v-cross-section wire was formed, by hammering round brass wire into the v-groove in a swage block (See Figure 42). The surface appeared flat, but by running a finger over the surface of the wire undulations were detected. These undulations were removed using a file and finishing off with a piece of sandstone. Only two surfaces were cleaned up this way the third was cleaned using a rough file. This was to provide a key for the silver solder when attaching the coil to the core. The wire was wrapped around the core which was made of 6mm diameter copper rod. The coils were then cleaned using vinegar and boiled in clean water. The same was done to the copper core. This was done to remove the oxide film from the coil and the core to make a cleaner soldered joint. The coil was then soldered to the core using silver solder with borax as the flux. 1 It was then boiled in water for 20 minutes to remove excess material.
The coil for the nut
The coil that will make the female thread was formed by drawing the wire to make a triangular cross section wire, then wrapping it around the male thread. The outside diameter of this coil was 10mm. A piece of brass was bored out to a diameter of 10mm then small amounts of metal were removed with a file until the coil slid into the hole with no slack. The coil was prepared as before then silver soldered into place. The screw threads fitted together with very little slack.
Timings
Process | Time |
Hammering into shape | 14 minutes 59 seconds |
Filing clean | 16 minutes 23 seconds |
Winding coil | 3 minutes 19 seconds |
Soldering wire to coil | 3 minutes 58 seconds |
TOTAL 38 minutes 39 seconds |
Table 4. Timings to make a male thread.
Process | Time |
Hammering into shape | 16 minutes 0 seconds |
Filing clean | 16 minutes 23 seconds |
Making nut | 9 minutes 00 seconds |
Winding coil | 4 minutes 58 seconds |
Soldering wire to coil | 3 minutes 28 seconds |
TOTAL 48 minutes 49 seconds |
Table 5. Timings to make a female thread.
Results
Total time to make male and female threads 1 hour 26 minutes
Making the coil using the draw plate
Process | Time |
Drawing wire | 6 minutes |
Winding coil | 5 minutes |
Soldering coil to core | 4 minutes |
Total 15 minutes |
Table 6. Timings for making the coil using a draw plate (male thread).
Process | Time |
Drawing wire | 3 minutes |
Winding coil | 5 minutes |
Making nut | 9 minutes |
Soldering coil to core | 4 minutes |
Total 21 minutes |
Table 7. Timings for making the coil using a draw plate (female thread).
Results
A nut and bolt could be made in 36 minutes.
Production methods for making wire
Making wire of square cross-section
Wire with a square cross-section can be produced by either hammering to shape or drawing it though a draw plate with square holes in it (Sim, 1997).
Hammering wire to shape
Process | Time |
Hammering into shape | 8 minutes 38 seconds |
Filing clean | 10 minutes 32 seconds |
Winding coil | 2 minutes 55 seconds |
Soldering wire to coil | 2 minutes 32 seconds |
Total 26 minutes 00 seconds |
Table 8. Timings for making and attaching a coil to a shaft (male thread).
Results
A piece of wire 170 mm long can be produced by hammering in 26 minutes
Process | Time |
Hammering into shape | 9 minutes 0 seconds |
Filing clean | 10 minutes 23 seconds |
Making nut | 9 minutes 0 seconds |
Winding coil | 2 minutes 55 seconds |
Soldering wire to coil | 4 minutes 0 seconds |
Total 35 minutes 18 seconds |
Table 9. Hammering wire to shape (female thread).
Results
Male and female threads can be produced by hammering wire in 1 hour 10 minutes
Drawing wire
Process | Time |
Drawing wire | 7 minutes 13 seconds |
Winding coil | 1 minutes 0 seconds |
Soldering wire to bar | 3 minutes 58 seconds |
Total 11 minutes 11 seconds |
Table 10. Drawing wire to shape (male thread).
Process | Time |
Hammering into shape | 6 minutes 0 seconds |
Making nut | 9 minutes 0 seconds |
Winding coil | 0 minutes 58 seconds |
Soldering wire to bar | 3 minutes 28 seconds |
Total 19 minutes 26 seconds |
Table 11. Hammering wire to shape (female thread).
Results
A male and female thread can be made by hammering in 70 minutes.
A male and female thread can be produced by use of a draw plate in 38 minutes (See Figure 41).
Discussion
The use of a draw plate reduces the time to produce the wire from 31 minutes to 9 minutes. The use of a draw plate removes the need to file the faces of the wire coil smooth because they are already smooth. This reduces the production time by a further 32 minutes 42 seconds. The total time to produce a male and female thread by hammering the wire to shape is 1 hour 26 minutes 3 seconds. The total time to produce a male and female thread by drawing the wire to shape is 36 minutes.
Fabricated threads made by drawing the wire can be produced at a much faster rate than those made by hammering the wire to shape.
V-Threads
Wire with a triangular cross section, can be produced by either hammering it to shape using a form, or drawing it though a draw plate with triangular holes in it.
The objective of this set of experiments is to determine if a workable v-thread can be made by wrapping triangular cross section wire, round a core and soldering it in place. It is also to determine if a nut can be made by soldering the same triangular cross section wire into the inside of an existing brass nut.
Making triangular wire by drawing through a draw plate
The thread was made by drawing brass wire through a triangular draw plate to make wire. Enough was made to make the male and female threads. The wire was then wrapped round a brass rod that would form the core of the thread. The wire was soldered into place using silver solder.
A commercially produced brass nut was drilled to the outside diameter of the triangular wire and the wire soldered in place. The test for the thread was that it could be screwed by hand down the whole length of the male thread.
The nut stuck on the thread in places. To remove the tight spots, a lapping paste was made of silver sand combined with lamb dripping. This was mixed into paste. It was applied to the threads and the nut was run up and down the thread till it could turn freely when turned by hand.
The whole experiment was conducted again.
Thread 28.03 .2014 took 4 minutes 4 seconds
Thread 28.03 .2014 A took 6 minutes 4 seconds
Measurements of V-Thread
Pitch (mm) | Core Diameter (mm) | Outside diameter (mm) |
2.90 | 8.20 | 10.30 |
2.78 | 8.23 | 10.32 |
2.71 | 8.20 | 10.29 |
2.79 | 8.00 | 10.16 |
3.01 | 7.91 | 9.92 |
3.02 | 7.92 | 10.19 |
Average 2.87 Variation 0.31 - 0.24 + 0.23 | Average 8.08 Variation 0.29 - 0.15 + 0.17 | Average 10.20 Variation 0. 40 - 0.12 + 0.28 |
Table 12. Copper V-thread.
Pitch (mm) | Core Diameter (mm) | Outside diameter (mm) |
2.49 | 8.38 | 11.00 |
2.36 | 7.68 | 10.68 |
2.16 | 7.57 | 10.80 |
2.28 | 8.27 | 10.79 |
2.10 | 7.94 | 10.65 |
2.14 | 7.88 | 10.62 |
2.26 | 7.90 | 10.64 |
2.10 | 7.88 | 11.01 |
2.30 | 8.27 | 10.88 |
2.00 | 8.23 | 10.80 |
Average 2.22 Variation 0. 49 - 0.27+ 0.22 | Average 8.0 Variation 0.38 - 0.27 + 0.38 | Average 10.79 Variation 0.35 - 0.17 + 0.0.22 |
Table 13. Measurements of Brass V-Thread
Pitch (mm) | Core Diameter (mm) | Outside diameter (mm) |
2.00 | 7.90 | 10.05 |
1.87 | 7.76 | 10.64 |
1.82 | 7.91 | 10.66 |
2.10 | 7.76 | 10.62 |
2.00 | 7.74 | 10.64 |
2.12 | 7.04 | 10.67 |
2.24 | 7.75 | 10.63 |
2.0 | 7.96 | 10.67 |
2.0 | 8.01 | 10.72 |
Average 2.02 Variation 0.42 - 0.20 + 0.22 | Average 7.76 Variation 0.97 -0.72 + 0.25 | Average 10.59 Variation 0.67 -0.54 + 0.13 |
Table 14. Measurements of brass V-thread 28/02/2014 A
Brass V-thread 28/02/2014A
Testing
Comparison between a modern brass thread and a brass thread made by fabrication
A modern v-threaded brass screw 10 mm diameter was tested against a 10 mm diameter brass v-thread made by fabrication.
A torque wrench was used to determine the breaking strain of the modern bolt. It fractured at 3.50 kgm. The same technique was used to test the fabricated thread. It fractured at 1.38 kgm. This was repeated on a second thread with the same results. On the fabricated thread, it was the solder used to attach the triangular wire to the shaft that failed.
Conclusions
Small screw threads made of metal were known and used during the Roman period. They have been found on jewellery, as fastenings, and on a campaign lamp to join sections together.
Both square and v-threads have been found. These were used to join metal items together. In addition, a v-thread has been found that was used to join two pieces of wood.
Experiments have shown that threads can be made by hand using a file by unskilled labour in an amount of time that would make their use as fastenings economical.
There is a strong possibility that Roman screw threads have been misidentified and discarded on excavations due to their similarity to modern examples.
Country
- Italy
Bibliography
Burstall, A. F., 1970. A history of mechanical engineering. London: Faber and Faber.
Drachmann, A. G., 1932. Ancient oil mills and presses. Copenhagen: Levin: Munksgaard.
Gichon, M., 1979. The upright screw-operated pillar press in Israel, Scripta Classica Israelica 5, pp.206-244.
Landels, J. G., 1978. Engineering in the ancient world. London: Chato & Windus.
Paipetis, S. A. and Ceccarelli, M. eds., 2010. The Genius of Archimedes - 23 Centuries of Influence on Mathematics, Science and Engineering; Proceedings of an Internal Conference held at Syracuse, Italy, June 8-10, 2010; Dordrecht: Springer.
Patton, W. R. and Myres, J. L., 1898. On some Karian and Hellenic oil-presses, Journal of Hellenic Studies 18, pp.207-17.
Pliny, 2000. Natural History. Translated by W.H.S. Jones. London: Harvard University Press.
Schürmann, A., 1995. Die überlieferung antiker autoren. In: D. Planck, ed. Die schraube zwischen macht und pracht: Das gewinde in der antike, Jan Thorbecke: Sigmaringen, pp.55-76.
Singer, C., Holmyard, E.J., Hall, A.R, and Williams, T.J., 1957. A History of Technology. Volume II Oxford University Press. London.
Singer, C., Holmyard, E. J., Hall, A. R. and Williams T. J., 1972.
A History of Technology. Volume II. Oxford University press. London. P. 632.
Sim, D. N., 1997. Roman Chain-mail: Experiments to reproduce the techniques of manufacture. Britannia 28, pp.359-371.
Sim, D. N. and Legg, C., 2023. The Production of Roman Metal Screw Threads. EXARC Journal 2023/02. available online < https://exarc.net/ark:/88735/10688 >
Tuplin, C.J. and Rihil, T.E., eds., 2002. Science and Mathematics in Ancient Greek Culture. Oxford University Press.
Vitruvius,, 1998. The Ten books on Architecture. Translated by M.H. Morgan. Dover publications Inc