The content is published under a Creative Commons Attribution Non-Commercial 4.0 License.
Reviewed Article:
Wooden Matrices in Bracteate Production: An Experimental Approach
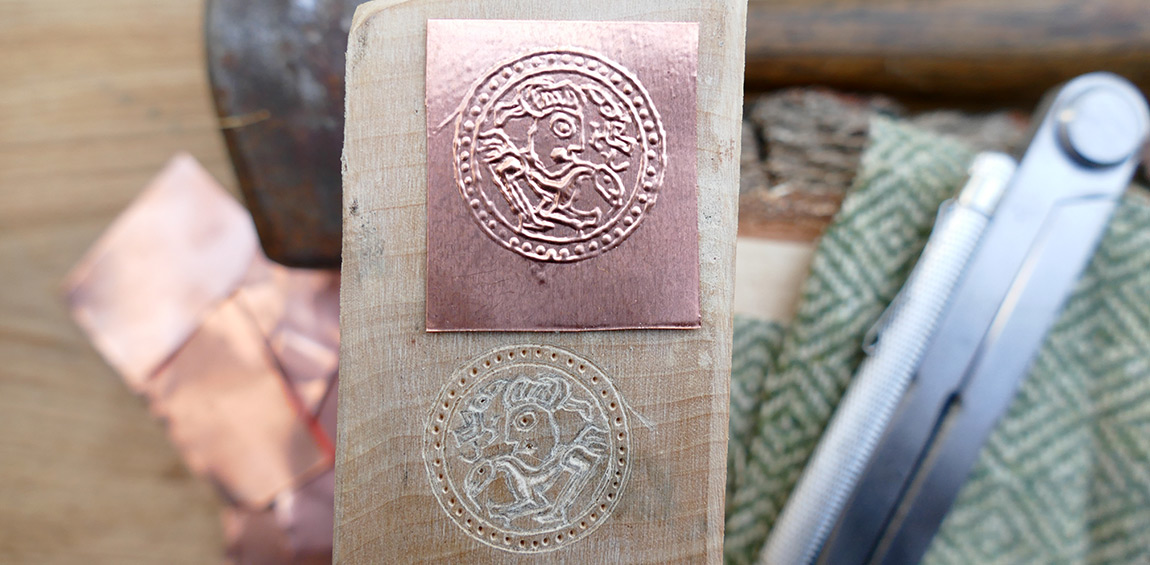
The literature on the production of Migration Period (c.400-550 AD) gold bracteates has suggested wood as a possible material to be used for the matrix on which bracteates are made, but only in the production of a single or very few bracteates. This study experiments with how such a matrix could have been made and what part of the wood could have been used. Additionally, it examines the quality changes in serial production.
Introduction
Gold bracteates are a type of jewelry, most likely worn around the neck as a pendant, which occurred in northern Europe during the migration period. They are made of a thin gold sheet which has been embossed with a motif, and usually but not always strengthened and adorned with a rim of gold wire thicker than the sheet itself. A gold loop is fastened on top of the bracteate to allow it to be worn in a necklace, or similar application. Most of the research on the field is devoted to the study of typology (for example Axboe, 1981 or Pesch, 2007), iconography (such as Pedersen, 2021 or Pesch, 2018) or chronology (see Axboe 2004; 2007; 2011). The method by which migration age gold bracteates were produced, while not as commonly the object of academic research, has still been greatly discussed. In 1895, Salin (1895) considered the possibility that both metals and organic material were used in the production of bracteates. He suggested that metal matrices were used to produce bracteates with a low relief, while organic material had been used for the bracteates with a bolder relief. The very first experiments were not conducted until half a century later when Mackprang (1952) showed how production could be done with bronze matrices. The conclusion of their experiment was that bracteates were struck with the gold plate placed on top of a matrix of negative relief and with lead or wood placed between the hammer and plate, thus creating the image or pattern in the relief. This method, known as pressblech (Coatsworth and Pindler, 2002), would then distribute the force of the hammer's blow to ensure a more consistent push of the gold into the shapes of the matrix. This was evident, according to the authors, due to the visible traces on the backside of the bracteate which were interpreted as the year-rings of the wood placed between the hammer and the gold plate. The argument has been made, however, that these traces are not from wood, but from cloth (Axboe, 2004). Indeed, it has been argued that the irregularities and patterns found in the visible traces are consistent with cloth but not with wood (Axboe, 2004). Axboe (2004) suggests that organic material is likely to have been used in bracteate construction, suggesting possibilities such as wood, walrus ivory, bone, and clay. In some instances, marks that are best explained by organic materials have been found on the surfaces of bracteates. According to Axboe (2004), wood would likely have been used as the matrix in cases where only a single, or few, bracteates were requested, but for a longer series of 10 or more bracteates, he points to Bohlin's (1981) suggestion of using other softer material, which could also include wood, as an intermediary medium before casting the final die in bronze. An experiment by Arrhenius (1975) using clay matrices to make bracteates has been criticized by Axboe (1982) who questions the validity of this theory. He points to the major decline in quality when making several bracteates from the same matrix, making serial production of even a few bracteates an impossibility at the required quality.
Despite the longstanding academic interest in and discussion surrounding the techniques used to produce Migration Period gold bracteates, few actual experiments have been made, and none have tested the suitability of using wood, despite it being explicitly suggested, based on the inspection of the bracteate surfaces done by Axboe. An experiment by Ernzt Foltz (1975) who attempted to press gold foil crosses by using wooden matrices is the closest known experiment for the materials used in this study. He found that while much wood was too soft to leave an impression of the required quality, it was possible using box wood. Still, while box wood is known for its density and excellent qualities for wood cutting of fine details, such as chess pieces or pipes, it may not be representative of the wood available to artisans of the Migration Period northern Europe.
A short note on terminology. The words anvil dial, matrix, model, and mould have all been used to describe the object used to press the metal sheet to create the bracteate. In this paper I have chosen to go with the term matrix for simplicity, but know that in other literature on the topic all of these may be encountered.
Research goals and scope
The goal of this study is to evaluate the suitability of wood being used as a matrix-material to produce migration period gold bracteates. It is not the goal of this study to exactly reproduce any given bracteate, nor to be procedurally authentic, beyond what is necessary to achieve a reliable and valid result that is relevant to the academic discourse. Thus, machine tools have been used for cutting and sanding the wood, while only simple metal tools have been used for the shaping of the surfaces themselves.
The research questions that this experiment will attempt to answer are:
- How would one work the surface of the wood to achieve a result of acceptable quality?
- Is there a difference in using the end wood versus the side wood for the matrix?
- Is it possible to achieve the production of bracteates with acceptable quality using a wooden matrix?
- Is a wooden matrix capable of producing multiple bracteates, or does it suffer a drop in quality that makes it unsuitable for serial production?
Research design
To start out the experiment, several pieces of birch approximately 15x15x4cm were cut and sanded gradually to 600 in grit to provide a smooth surface to work on. The choice of wood was based on availability and some initial testing. Other woods, such as oak, may possibly be better suited, but a study on the suitability of different types of wood (except grain direction) is outside the scope of this paper. Different tools were tested to find a workflow that would allow for the possibility of creating the relief in the matrix. A learning period was conducted in which several trial matrices (ca 15) were made and a number (40-50) of test bracteates struck. This was done to minimize the impact of variance in the process of pressing the metal into the wood to transfer the motif onto the sheet, as this is important to achieve reliable and valid results when examining the development of quality during serial production.
Due to gold being an expensive metal, not suited for repeated experimental research, a substitute had to be considered. Bracteates vary somewhat in thickness, usually between 0.2- 0.4mm (Axboe, 2004). To emulate the gold bracteates, copper-sheets of 0.1mm (99,9% annealed copper from efco creative, product number 9955014) in thickness were used. Gold has a hardness of 2.5 on Mohs scale, while copper has a hardness of 3. A thinner sheet of copper, 0.1mm instead of 0.2-0.4mm, was used to have a somewhat more pliable material despite its hardness.
To adequately examine the ability of using wood to achieve bracteates of sufficient quality for such production, it is necessary to create matrices that have realistic attributes when it comes to size and complexity. Thus, despite reproduction not being a goal of this study, an original has been chosen to be emulated. This will ensure realism in the experiment as well as providing a benchmarking tool against which to evaluate and discuss the results. Arbitrarily, IK 21, object C3325 in (Unimusportalen) has been chosen for this study. The bracteate, which can be seen in figure 1, was found at Berge in Lyngdal, Norway. The bracteate, which shows a head over a quadruped, with a bird next to the head, is of the C-type according to the typology (Pesch, 2007), of which at least 290 bracteates have been found (Pesch, 2018). It thus represents a suitable benchmark with regard to size and complexity. The Berge bracteate is 0.2-0.3mm thick with an outer max diameter of 24.5mm, however the area of the motif that is being recreated has a diameter of approximately 22.1mm.
The experiment(s)
The initial phase of the experiment was conducted as exploratory experimentation in which many matrices were being made to test different methods of achieving a relief in the wood, as well as transferring it to the metal sheet. This part of the process was not intended to be a part of the scientific study, but a period of experience gathering, enabling the formal experiment to be conducted with as high a reliability as possible, minimizing problems and uncertainty from the process itself. The aim was to establish a workflow-moving from creating the matrix to transferring the relief-that could be reproduced repeatedly and minimizes the impact on quality from variance in the author`s ability to both create the matrix as well as the process of striking the bracteate.
The second phase of the experiment was to create a matrix capable of creating a relief of close resemblance to the Berge bracteate. Additionally, and more importantly, this phase would allow for the evaluation of the characteristics of a bracteate struck on wood.
The third part of the experiment was to strike the bracteates on the matrices of end wood and side wood to examine if there were noticeable differences in quality.
The fourth part included the selection of the most suitable wood type, the creation of a matrix and a series of bracteates with this method, and finally evaluate whether this method is suitable only for a single or a few bracteates as assumed in the literature, or whether a longer series could be produced.
Results
Experiment Part 1 - Initial experiences
The initial experience of producing bracteate matrices from wood, was that the minute details are limiting the types of tools that can effectively be used, at least in the production of this specific bracteate. After attempting to use small scalpels, V-irons, and scrapers it was concluded that the best result would be gained by simply using a tool with a sharp tip to gradually scrape the lines on the surface. Even small errors will cause a distortion in the surface of the bracteate; thus, it is important to be patient and take uttermost care to achieve a crisp and clear motif. A characteristic of working on wood is that it moves, which means that after making some line or dot, it will change in form when you make another line or dot next to it. This makes spacing between details and going back over old details to redo them important, as they would otherwise deform and not show up clearly on the bracteate. When transferring the motif onto the copper sheet, the wooden matrix was placed on top of an anvil, the sheet was place over the matrix and 8 layers of diamond cubic woolen cloth were placed on top, then struck repeatedly with a hammer to press the sheet down into the matrix and transfer the motif. In Figure 2 an image of the tools used can be seen. The compass was used both to make the initial circles as well as a scraper. While using the sharp points of the compass worked to achieve the results in this study, more suitable tools would be needed for higher quality bracteates. The round punch-tool was used to stamp the dots between the outer circles.
Experiment Part 2 - End wood versus Side wood
End wood is harder than side wood. This, it turned out, had major impact on the results, which can be seen in Figure 3. Initially it appeared better to work the side wood as it was easier to form and make a deeper relief. However, this softness also makes the wood yield under the hammering, making for a poor transfer of the motif. In addition, as the grains going along the side of the wood is of uneven hardness, it makes for a strong wavy pattern on the surface of the bracteate when struck. With these two factors combined, the poor transfer and the creation of noise makes using birch side wood unsuitable as matrix anvil matrices in the production of gold bracteates. The end wood however, due to its hardness and unity, was more difficult to work initially as it required more effort to achieve sufficient depth in the relief on the surface. The transfer, however, was vastly superior to that of side wood. Due to its hardness the end wood produces much improved quality with sharper and crisper details, and virtually no artifacts from the structure of the wood itself.
Experiment Part 3 - Quality assessment
The aim of this study was not to create an exact copy of the original, a goal which would have required assembling an array of customized tools which would be able to more accurately depict the exact characteristics of lines and dots in the original. The comparison between original and recreated bracteate in Figure 4, therefore, is just to provide a baseline and context for the discussion. The bracteate struck on wood in this experiment is clearly capable of producing crisp and readable details, with higher skill (the author is no migration period gold smith) and with more specialized tools it seems likely that a result close to the quality of the original would be achievable. The minor vertical lines that can be seen as noise in the background are visible on the unstruck copper sheets (Figure 5) and do not represent grains or other artifacts from the matrix. High resolution images of the recreated bracteates were analyzed, and nothing was found that would disqualify the possibility of wood being used as a matrix in the production of bracteates. This indicates that wood, at least end wood from birch, is a suitable material to use as matrices in the production of bracteates.
Experiment 4 - Serial Production
To test the assumption that wooden matrices, if used, could only have been involved in the production of a single or very few bracteates, a series of 15 bracteates were struck in rapid succession on the same wooden matrix. To assess how quality is impacted by the number of bracteates produced on the matrix, two different methods to assess quality were used.
First, an examination of the occurrence of artifacts in the bracteates surface which could indicate damage to the matrix were made using high resolution image analysis. Secondly six volunteers were asked to study the 15 bracteates closely and rank them in order of quality. This was done as a measure of perceived quality. This was done to evaluate when and if visible changes in quality occurs, as this is arguably the most relevant measure to evaluate the suitability for serial production during the Migration Period.
Surface analysis
The investigation of the 15 bracteates that was made during this study, in which a high-resolution surface photographs were analyzed using computer enhancement, did not reveal any artifact, lines or otherwise that were persistent in nature and thus indicative of damage such as cracking of the matrix. In Figure 6, bracteate nr 1, 5, 10, and 15 can be seen, with no discernible damage occurring throughout. This shows that, while damage or cracking of a wooden matrix will occur in some cases, it is by no means an absolute necessity. Even under the stress of producing 15 bracteates, which exceeds any known series of bracteates, the matrix was able to endure without any major damage.
Perceived quality
While studying the surface of a bracteate on a large monitor based on high resolution images is possible today and makes us able to discover even the slightest of irregularities, such would not have been the case for the actual makers, buyers or users of these objects. Thus, to properly evaluate the feasibility of producing a series of bracteates using a wooden matrix, a survey of perceived quality was undertaken. The bracteates were given a random ID between 1 and 100 so that their striking order would not be known, and five volunteers ranked the bracteates according to their evaluation of their quality. This was done independently of each other not knowing any previous evaluations.
Estimate | Std.Error | Sign. | |
Intercept | 3.54 | 1.3 | 0.03* |
Serial Number | 1.58 | 0.48 | 0.001** |
Serial Number ^2 | -0.1 | 0.03 | 0.001*** |
Table 1. Regression results. Signif codes: 0 "***", 0.001 "**", 0.01 "*", 0.05 "." | Adjusted R-squared: 0.12 | p-value: 0.003778.
When analyzing the perceived quality, no linear correlation was found, with the correlation being only -0.001. However, the boxplot in Figure 7 shows a clear non-linear trend between serial number and perceived quality. A quadratic regression shows that there is in fact a significant parabolic relationship between the serial number and the perceived quality, as can be seen in Figure 8 and Table 1. This is a surprising result which indicates that the quality of the first few bracteates is relatively poor before gradually increasing to a peak, and then starting to deteriorate again. As this could potentially be due to random variance in the experiment, a second matrix was made, and another 15 bracteates were struck. The results, which can be seen in figure 9, support the finds of a non-linear relationship in which the first bracteates are of lower quality followed by bracteates of a higher quality. These finds directly contradict the assumption made by Axboe (Axboe, 1982) where he states that "It would seem likely that a goldsmith, asked for a single bracteate only, would strike it directly on a wooden or ivory die, while a series of 10 identical pieces would require, and justify, the casting of a bronze die". As demonstrated by this experiment, a longer series of up to at least 15 bracteates can all be struck directly on the wooden matrix.
The explanation for the parabolic relationship in quality, may be found when combining this result with the experience gained in the exploratory Part 1 of the experiment, as well as Part 2 where both end wood and side wood were tested. The experience and results showed that when the wood is softer it has a lower ability to transfer the motif onto the metal sheet. Thus, it seems that the process of repeatedly striking the surface of the wood with the hammer when making the first few bracteates is "priming" the surface by making it more compact and denser. This in turn increases its ability to transfer the motif to the metal sheet. This operation does however come at the risk of potentially damaging the matrix, even if that did not occur in this experiment, and there are indications that the quality will drop somewhat after a peak at approximately 8 bracteates. Where this peak occurs would be expected to vary based on the characteristics of the wood used and should not be generalized, but the concept of increased quality through hardening the surface should and could.
Conclusions
This study has demonstrated, using the methodology of experimental archeology, that by utilizing the end-wood of birch, it is possible to make matrices capable of producing high quality bracteates. This confirms the suggestion by Axboe (2004) that wood is a candidate to have been used for matrices in the production of migration age gold bracteates. The experimental results of serial production do however contradict the assumptions set forth by Axboe (1982) that wood could only produce a single or a few bracteates. The results from this experiment demonstrate that not only is a wooden matrix perfectly capable of producing a long series of bracteates, up to at least 15, but the quality does in fact improve after the first few bracteates and remains at a higher level throughout the series despite dropping somewhat after peaking around the 8th bracteate. This find has a big impact on our understanding of the production of bracteates and the debate on which bracteates could have been produced and using which materials. This study shows that a much larger quantity of bracteates may have been produced using wooden matrices than hitherto believed possible.
Keywords
Bibliography
Arrhenius, B., 1975. Die technischen Voraussetzungen für die Entwicklung der germanischen Tierornamentik. Frühmittelalterliche Studien.
Axboe, M., 1981. The Scandinavian Gold Bracteates. Studies in their manufacture and regional variations. With a supplement to the catalogue of Mogens. B Mackeprang. Acta Archeologica, 1981(52), pp. 1-100.
Axboe, M., 1982. On the Manufacture of the Gold Bracteates. In: K. Hauck, ed. Band 16. Berlin: De Gruyter, pp. 302-318.
Axboe, M., 2004. Die Goldbrakteaten der Völkwanderungzeit - Herstellungsprobleme und Chronologie. Berlin: Walter de Gruyter.
Axboe, M., 2007. Brakteatstudier (Studies in Gold Bracteates). Series: Nordiske fortidsminder, Ser. B, Vol 25, pp. 141-200.
Axboe, M., 2011. Die Chronologie der Inschriften-Brakteaten. In: Heizmann/Axboe, ed. Die Goldbracteaten der Völkwanderungzeit - Auswertung und Neufunde. Berlin, Boston: RGA Ergbd. 40, pp. 279-298.
Bohlin, P.-O., 1981. Brakteat-Teknik. C-Uppsats i Arkeoligi, särskilt Nordeuropeisk, Uppsala Universitet.
Coatsworth, E. and Pindler, M., 2002. The Art of the Anglo-Saxon Goldsmith: Fine Metalwork in Anglo-Saxon England: Its Practice and Practitioners. NED-New edition. Woodbridge: Boydell & Brewer.
Foltz, E., 1975. Technische Beobachtungen an Goldblattkreuzen. In: W. Hübner, ed. Die Goldblattkreuze des frühen Mittelalters. s.l.:Konkordia.
Mackeprang, M. B., 1952. De Nordiske Guldbrakteater. Jysk Arkæologisk Selskabs Skrifter 2.
Pedersen, T. Ø., 2021. Eigi Einhamr: Jernalderens GEullbrakteater Og Den Åbne Krop Som Form. Aarhus: Aarhus University Press.
Pesch, A., 2007. Die Goldbrakteaten der Völkerwanderungszeit - Thema und Variation: Die Formularfamilien der Bilddarstellungen. Berlin, New York: De Gruyter.
Pesch, A., 2018. Confiding birds: some short remarks on the "head-with-bird-on-top-of-horse-motif" on Migration Period gold bracteates. In: ZBSA, ed. Advanced studies on the archaeology and history of hunting, Raptor and human - falconry and bird symbolism throughout the milennia on a global scale . s.l.:Wachholz Murmann publishers, pp. 431-448.
Salin, B., 1895. De nordiska guldbrakteaterna. s.l.:Antiquarisk Tidskrift för Sverige.
Unimusportalen, 2024. https://www.unimus.no/portal/#/things/99a31cdc-c4bc-4364-a37a-22003e163…, s.l.: s.n.