Podcast:
Stuck in the Past
Next Episode
Previous Episode
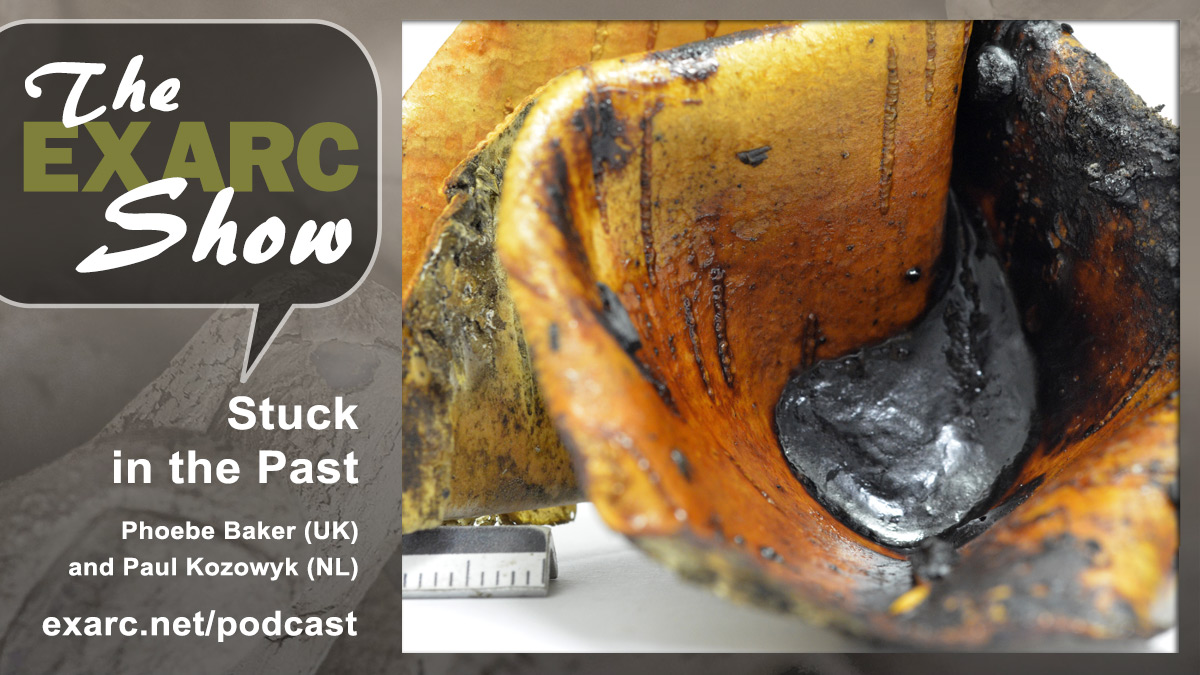
This month #FinallyFriday travels all the way back into the deep past, as we discuss the trials and joys of experimenting with Neanderthal glue. We discuss how to overcome the limitations of working without specialised laboratory equipment, how to deal with a lack of archaeological evidence, and why glue is such a sticky subject! Dr Paul Kozowyk is a post-doctoral researcher at the Delft University of Technology in the Netherlands. His work focuses on the investigation of ancient adhesives from Neanderthal and early human archaeological contexts, specifically looking at the material properties of different glue recipes. Phoebe Baker is currently working as a Terrestrial Geophysics Technician for Wessex Archaeology in the UK, but she is also an experimental archaeologist whose research focuses on ancient sewing technologies.
EXARC Member: Phoebe Baker (UK) Phoebe Baker is currently working as a Terrestrial Geophysics Technician for Wessex Archaeology in the UK, but she is also an experimental archaeologist whose research focuses on ancient sewing technologies. Her research looked at the potential use of glue in Neanderthal clothing manufacture, and she has recently been awarded the EXARC grant for her new research project investigating shoemaking technology... Read More |
![]() |
Paul Kozowyk (NL) Dr Paul Kozowyk is a post-doctoral researcher at the Delft University of Technology in the Netherlands. His work focusses on the investigation of ancient adhesives from Neanderthal and early human archaeological contexts, specifically looking at the material properties of different glue recipes. He is also a talented woodworker, and brings his love and knowledge of crafting to his experimental work. |
It's the first Friday of the month, which means that it's time for the next episode of #FinallyFriday, bringing you insights and discussions from around the world focussing on experimental archaeology, ancient technology, archaeological open-air museums and interpretation.
Matilda: Hello and welcome to #FinallyFriday. My name is Matilda Siebrecht and today I am joined by two specialists from our EXARC community and abroad focussing on ancient glue. Dr. Paul Kozowyk is a post-doctoral researcher at the Delft University of Technology in the Netherlands. His work focusses on the investigation of ancient adhesives from Neanderthal and early human archaeological contexts, specifically looking at the material properties of different glue recipes. He's also a talented woodworker and brings his love and knowledge of crafting to his experimental work. Phoebe Baker is currently working as a terrestrial geophysics technician for Wessex Archaeology in the UK, but she is also an experimental archaeologist whose research focusses on ancient sewing technologies. Her research looked at the potential use of glue in Neanderthal clothing manufacture, and she's recently been awarded the EXARC Grant for her new research project investigating shoemaking technology. So welcome both. Thank you so much for joining me on this podcast. I have a quick question to start you off. So, glue is, at least in my opinion, still quite a specialised research area. It's not kind of one that is standardly offered, shall we say, at undergraduate courses or general archaeology degrees. So how did you both get into this field? Perhaps Phoebe, you could start us off?
Phoebe: Yeah, sure and first off, I wanna say thank you for having me on. It's really cool to be on this side of it.
Matilda: Yes, some of you might recognize Phoebe's voice...
Phoebe: It was kind of accidental that I came into studying glue. Looking at research projects as part of my degree, I really wanted to combine something with my interest outside of archaeology and archaeology. I'm quite a keen seamstress outside of archaeology and throughout the pandemic, I was doing quite a lot of DIY work involved in this. And quite a lot of the DIY videos on YouTube, which show you how to do things say if you don't have a sewing machine, an alternative way of sewing might be to glue your stuff together. And I thought that this was a really intriguing idea and it's not really something that I've ever really seen explored anywhere in an archaeological context at all. So I knew from my undergraduate research tar and pitch from Neanderthals had been touched on, but as you said, it's never been hugely explained. But I was wondering whether there was a precedent for exploring whether pitches and tars could be used in this kind of more clothing-related way, rather than just for its production value.
Matilda: That's very interesting and indeed very specialised. Paul, how about you?
Paul: Thank you for inviting me on here, this is really fun. In terms of Phoebe's using research looking at glue and clothing, I think that that's really cool and fascinating because obviously I've spent a lot of time looking at glue and studying glue and reading about glue and I know that it's used in clothing all of the time and I often use it as like it's used in clothes, shoes and jackets and all kinds of things for seams. But it never really occurred to me about using it a long time ago. So I'm interested to hear more about that today. In terms of how I got started, it was also not really by accident but lucky I guess. One of the first master’s classes that I took in Leiden was, I can't remember the name, but it's something like Introduction to Human Origins, maybe, by Professor Wil Roebroeks. One of the first slides, he showed this picture of Neanderthal birch bark tar, and talked about it in terms of the use of fire to produce it, and we don't know how it was made, that kind of thing. That immediately captured my attention and I was lucky that Geeske Langejans at the time was doing a Veni project, I think called What's in a Plant. So it was looking at archaeological plant use and of course, resins and adhesives, a lot of them come from plants. So I was able to kind of squeeze in a master's thesis under that umbrella of looking at plant material archaeologically, and then from there it just snowballed to a PhD and then a Postdoc in a bigger project also run by Geeske.
Matilda: Which must give you some optimism, Phoebe, that there is indeed a future in this career choice…
Phoebe: No, it's really cool hearing that from you, Paul, definitely.
Paul: I was very lucky. It was super nice to be able to find that position for my master's alone, be able to do the topic I wanted. And then, you know how it is, every time you answer one question or you do one experiment, five more pop up. So that's basically been what happened at each stage. After I finished my master's, there were way more bigger questions. Then after I finished my PhD, again, more big questions.
Matilda: Both of you indeed mentioned that your focus is on early human or Neanderthal glue use. What sort of sparked the interest in this earlier period? Paul, you mentioned that it was sort of a course on human origins that got you started. Phoebe, where did you go from watching YouTube videos on sewing technology in the modern day to Neanderthal glue?
Phoebe: Well, I've always been really interested in human origins. I particularly like the mystery of it, I guess. I like how little we have and that allows us to use a little bit of imagination and I just love how we are able to piece together an idea of what was going on with such little evidence. The glue usage just really humanises that period for me. I'm not quite sure why. Maybe it's because there's an example with a fingerprint in, which to me is incredible. I can't believe that we have a fingerprint from that long ago, but I really just love how we're starting to get these really humanising aspects of very early humans coming through in the archaeological record. What about you Paul?
Paul: Well, pretty much the same, that was a good answer. I was always fascinated with human origins, I guess, because of the mystery behind it. There's not so much... like there's no written history, obviously, you're looking at species that are very much, not human, but at the same time, well, like you said, with glue and like finding this fingerprint and stuff, very much human as well. So that just makes me more interested in it than the more recent times, even mesolithic and neolithic and of course historic times, just don't seem to have as much intrigue to me.
Phoebe: Yeah, I agree with you on that.
Paul: You did a good job explaining why, because of the mystery and that there's not so much material remains and glue as well, even less leftover of that than stone tools, for example. So then you do have to use, like you said, your imagination. That's why the experimental archaeology in my research is so heavy, because there's so much missing. We have to fill in the gaps, somehow. We’ve spent a lot of time looking for archaeological residues, and there's currently a PhD in our project right now who's almost entirely focussing on archaeological residues. He's doing usewear as well. It's a lot of work usually for very little reward. Of course, when something does come to light, it's incredible. But you can look for a long time without finding anything because it's so rare and so difficult to identify.
Matilda: At least you have then that evidence for resin use. Is this being used for hafting or..., what kind of uses do you see in your research, Paul?
Paul: Yeah, for hafting.
Matilda: Okay, yeah, that's the predominant one. Because I can imagine, Phoebe, it's very different for you because you don't have Neanderthal clothing, do we?
Phoebe: No, not yet. It would be amazing to find some concrete evidence of clothing, but at the moment we are really reliant on things like usewear analysis of stone tools or the chance find of a bone tool that possibly, maybe could be used for sewing. We are really reliant on kind of ephemeral evidence for clothing and there's no direct clothing at the moment.
Paul: Can I ask you a question, Phoebe, about the glue in Neanderthal clothing? If you were to find, from an ice patch or exceptional preservation from a waterlogged site or something, what would you expect, which material and what would you expect it used for, like in shoes or something else? Waterproofing?
Phoebe: That's a really good question and it's something I've been looking at a little bit with the research project that I'm doing at the moment, which is more based on shoes, which is a more specialised item of clothing than just general clothing. But I've been looking particularly at the moment for leathers and hide processing. These are things that we are able to see at the moment from stone tool usewear. I started collecting a database for my master's research project and there's way more evidence of hide processing with stone tools than I thought there was, which of course is not necessarily directly clothing as you could use hides for a variety of things, including shelter and things like that. But I think that the results from my experiments with the tar show that it's not necessarily the strongest material. I found this amazing paper that basically used the exact same methodology as me, but for testing stitch strength. So they used an overcast stitch and I think a running stitch, although I could be wrong. They definitely used an overcast stitch and my tar experiments, they were not as strong as the stitching. So I think that birch bark tar, if it was used in clothing, would be most likely to be used for its waterproofing properties. It could be used in combination with sewing because some Inuit sewing methods have very, very complicated ways of only piercing through a certain portion of the leather so you don't pierce the whole way through so you keep a fully waterproof stitch the whole way. But if you were to use birch bark tar as well as the stitching, you wouldn't necessarily have to do such a complicated way of stitching. So I think that it's kind of in these aspects that it might be used rather than just by itself.
Paul: That's really interesting cause it's how you use adhesives in clothing or leather working today as well. You glue the seams and then stitch through it, or you glue it or seal it after to waterproof the stitching.
Matilda: And the materials that you're using. You mentioned birch bark, but are there other recipes that are used or that you have used in your experiments?
Paul: Birch bark tar is certainly the main adhesive. But that's mostly because the first Neanderthal adhesive found was birch bark tar and it's also the oldest known adhesive. I think from Neanderthals there's more birch bark tar finds than any others. There's a couple that may be resin or gum, but it's also not very clear. But the birch bark tar finds are completely unambiguous. It's definitely birch bark tar, it's definitely made by Neanderthals. That is the focus of most of the discussion. But also, I would expect that Neanderthals would be using pine resin before birch bark tar, just because you can find it from a tree. It’s widely used as an adhesive in more recent times, but it's something that, if you've ever climbed a spruce tree or something like that, and you get it on your hands, it's incredibly sticky and it's impossible to get off. I'm sure at some point, probably before they figured out how to make birch bark tar using specific fire techniques, they probably found this sticky pine resin and were using it. Maybe not on its own, but also like with stitching, maybe to waterproof a binding material or to wrap in combination with binding probably, using some other adhesives. On top of birch bark tar, rather than resins from pine trees, you can also have gums from deciduous trees. Like cherry is a native European tree that produces gum. But also, in Africa there's Acacia and a number of other trees that produce gums and they're water soluble. That's the big problem for Paleolithic archaeology. They're not gonna survive as well as birch bark tar or pine resin. So they're much harder to find.
Matilda: And I guess wouldn't be as waterproof or...
Paul: No, they wouldn't be waterproof either, so they wouldn't suit that purpose.
Matilda: And do you find similar, or did you conduct with similar materials, Phoebe, in your experiments?
Phoebe: In my experiments, I only looked at birch bark tar. But I did experiment, and I think Paul has as well, with adding different things to birch bark tar, because it can change the adhesive properties quite a lot, as I actually found with mine. So I tried adding things like beeswax and rosin and my favourite, which was holly ash. I also tried some beech ash. They actually can have really dramatic impacts on how strong your birch bark tar is. And I think it's the same for pine tar as well. I really found that the holly ash, which we did some chemical analysis on and found that it has a really, really high potassium percentage, which then, when it's exposed to oxygen, it forms a really strong alkaline, made the birch bark tar way stronger than any of the other ones, which I really wasn't expecting. I think that this is something that Paul has also touched on, in your research?
Paul: We have, but not looking at something as detailed as ash from different trees. For our experiments we found that birch bark tar on its own is usually the best hafting adhesive, so we don't need to add things to it to improve birch bark tar. Pine resin, for example, is not very good compared to birch bark tar. And for that it was really important to add other ingredients and the easiest way of improving it is adding beeswax, at least for the materials we tested. So far we've primarily done beeswax and red ochre, hematite and clay and a few other mineral fillers because those are what's found in Southern Africa. We're sort of doing a comparison between middle Stone Age African adhesives versus European middle Paleolithic adhesives.
Phoebe: That's really interesting. I'd love to experiment with things like ochre.
Paul: The potassium content is, I guess, something you can figure out from just the ash content of trees. You can probably look up which species have a high potassium content anyway. Now that you know that it has that effect you could potentially see what other trees have high potassium.
Matilda: Which leads me to another question because, indeed you mentioned a few times now this potassium and obviously recipes are involved. You have to mix a lot of things. You have to understand the relative - I'm not sure what your official terminology is - I'm just gonna call it strength, I guess, of the glue. How much of a chemistry background did you have before entering into this field or how much have you had to learn?
Phoebe: That's quite an easy answer for me in that I had no chemistry background beforehand, but I was really lucky that the people in the department at the university that I was doing it at which was the University of Liverpool, had quite a lot of experience in applying chemistry and applying science to archaeology. So they were really helpful and they really were able to support that kind of aspect of my research.
Paul: It's also an easy answer for me... basically no chemistry knowledge before starting. And it's still one of my major shortcomings, I guess, in my research right now. It takes me quite a lot of effort to get a clear understanding of what's going on at a chemical level. But I'm lucky that a lot of my experimental work has been able to kind of avoid - so far - what's going on at a chemical level and just understand the material property. It would be saying that potassium improves the strength or makes it weaker, but not saying why it is that that happens. So the red ochre clearly improves the adhesive properties, but it's not a hundred percent clear what is actually causing the improvement, whether it's just physical change because of like a concrete aggregate that it's just these hard particles intermixed that help lock everything together, or whether there's actually some chemical change taking place. We still need to do some more work on that. But adhesion and adhesives are also something that is kind of mystical to a lot of people as well. Even in modern adhesion theory, the modes of adhesion is not always completely agreed upon and different adhesives bond in different ways. So you can have interlocking and mechanical bonds. You can also have interaction from Van der Waals forces and sometimes it's not known which one of those is the predominant force in a certain adhesive. So the important thing for us was not necessarily explaining why it changes, but just knowing that it does. Knowing that birch bark tar does perform better as a hafting adhesive or does have a higher impact resistance than pine resin. That's the practical result from my experiments that's useful for looking at these uses from a Paleolithic point of view. Understanding the chemistry would certainly, I think, help in the future because then you can, like when you find something, an ash with a high potassium content, you can make predictions about how that would've affected the adhesive. But we're not there yet.
Matilda: I guess that makes sense because also I assume that Neanderthals weren't considering the potassium content of the ingredients that they were using while they were mixing the glues up, right? So it's more about observations and the sort of qualitative aspect, in terms of how well it adheses. You were just talking about relative strength and the different modes of adhesion and stuff, but I guess glue also… as we've spoken about today, can be used for stuff like waterproofing. Have there been experiments that have looked at the different levels of waterproofness? We've already talked about the fact that gum is water-soluble. Phoebe, is this something you are planning to do further?
Phoebe: This is something that I am really hoping to do as part of this EXARC research Grant that I've been given to look at footwear is to start to have some actual analysis on how waterproof these things are and how much water they can withstand before they start failing.
Paul: I know from more recent times which materials have been used, like spruce resin, in Canada was used to waterproof birch bark canoes and of course pine tar was used to waterproof ships, for hundreds and hundreds of years and huge, Spanish Armada-type ships for a long time. So I think that it's pretty clear that pine tar and pine or spruce resins definitely have really good waterproofing capabilities. For me, the big waterproofing thing would be the binding that you would use to tie a stone tool to a wooden handle, for example, would probably be either some plant fibre or animal fibre like sinew. Both of those things are very susceptible to moisture. The plant fibre will expand and get soft when it's wet. And the sinew will also expand a lot and the natural adhesive that's in it will completely come loose. So if you use those and want them to be successful for using in the environment without having to worry about rain or dropping it on wet grass or anything like that, then putting a coat or at least, using an adhesive like resin or tar that you can kind of smear around it as well definitely helps, but that's not as extreme as waterproofing a canoe. So I think that there's not a lot of difficulty in waterproofing a binding on a stone tool. I could imagine that clothing is something that needs certain properties because it kind of soaks the waterproofing material. Whether it was tar or resin would soak into the leather a little bit and disperse a bit and water can still kind of penetrate that. I think it would be impractical to have a few millimetre thick layer of tar over your leather clothing. So I could imagine there could be some nice experiments in there to test the waterproofing capabilities of tar or resin on leather.
Phoebe: Am I also right in thinking, Paul, that tar and pitches often have insecticide properties?
Paul: Definitely. And you hear it a lot with tar and with birch bark tar and sometimes it's even still made and sold today in Scandinavia and Eastern Europe as an insecticide, also for garden use, like to keep out slugs and to protect wooden posts from insects and things like that. I could imagine that in the past you could also use it on your body to keep mosquitoes away.
Matilda: We talked a little bit about the fact that the sort of chemical aspect of things and that side, shall we say, of the methodology was something that you've learnt or you work in a very multidisciplinary team, which is a great thing with this kind of research it seems. But in terms of the other kind of methodologies that you used I'm just curious to talk a little bit about it because I think some people listening to this podcast, I mean Paul, the amount of experiments that you're able to do and the kind of facilities that you have access to are incredible, especially at the moment. But then for example, Phoebe, your project was like you say, in a much smaller scale and the lab equipment that you had was maybe a little more restricted. So for our listeners to hear, you know, people who are saying ‘but I don't have access to a fancy uni or a fancy lab’. How did you compensate for the kind of physical limitations on the methodology that were imposed?
Phoebe: You are right Matilda. I have had quite a lot of limitations on what I'm able to do and indeed when I was actually doing the project, I’ve had very strong time restraints as well because we had restrictions on what labs we could use because of covid. And then I had deadlines that were quite close to when I was actually allowed into labs. So there was also time restraints as well as material restraints, which I think actually made the project better, because it was relatively simple the methodology that I used. So it was taking this idea of lap shear tests, which Paul has done, I think, in some experiments to test strength, which is where you use two different substrates, which are glued together in the middle and you basically pull them apart. So I used a clamp, which had a piece of leather in, and then the leather had a strip of glue on with another piece of leather glued onto it. This had a grommet in it that I put in myself, and that was then attached to a mechanical weight gauge that I think we bought off Amazon. It was really useful. This was then attached to a lever pole, which was put against the wall, and you kind of pulled the lever pole back until the glue failed. Similarly, I think, to how they're actually made in a lap and shear machine. But then I also filmed this so you could see how high the weight gauge got without you having to check it at all times, which made it much easier to see what kind of strength each thing got to. Basically I just repeated that for the main methodology. The tar itself was produced in an as simple way as possible, because for my experiments it wasn't necessarily important that I made it in a period-authentic way, because Neanderthals don't have things like ceramics, they don't have things like tins. So I used quite a simple method, which is called the double-pop method, where you put a load of birch bark into a tin with a hole in the bottom. This then drains into another tin that's underneath it, kind of slightly into the ground. You put a fire on top of it and you just burn it until you start to get oil and the fire dies down. You can then sieve the oil and get rid of some of the excess volatile compounds and water and make it into a bit of a thicker thing. But all of this was done with very simple materials that would be accessible to most people, I think. The only thing that was fancy was that we did analyse the holly ash that we put in. But as Paul mentioned earlier, you probably could look this up on the internet and not necessarily have to do that particular analysis.
Matilda: Is that familiar, Paul?
Paul: I was thinking as you were talking, Phoebe, about the amazing things that you can do with a smartphone and a smartphone camera as well. And then when you said you recorded it also with the video of the tests, with the cheap force gauge and you're basically doing what the lap shear machine does. Especially if you can measure with the camera the displacement, the amount that it moves or stretches before it fails. Probably the big thing that a dedicated lap shear tensile bench tester does, is that it tells you very fine or very high precision, of course, the load and the load rate but also the amount that the adhesive stretches or is displaced before it fails. Those things are kind of difficult to do with just a camera because you can't distinguish such fine changes. And with leather it would be even harder because it would stretch as well, so you don't know how much it's the leather stretching and how much is the glue stretching. But those kinds of details are also not necessarily the most important things. When we did our first lap shear tests, really we were interested in the maximum load that it was able to withstand. You could have done that with a force gauge and a lever or, talking about having lab restrictions because of covid. At the start of the middle of the first year of covid, we did a bachelor's course in Delft with testing adhesives, testing archaeological adhesives or -inspired adhesives. But we couldn't go in the lab, so we also had a hanging weight scale, and we made our lap shear specimens and we filled up - this is very archaeology - beer crates, until the lap shear broke. Then we weighed the crate afterwards and could figure out what the maximum weight that it was able to withstand. These kinds of simple tests work really well for getting that key information. And I could imagine, for example, if you had like a grid or a scale behind your sample and you recorded it with a good camera, then you could also measure how much it's moving and possibly stretching before it fails and put those things together manually.
Phoebe: That's a really good idea.
Matilda: That's really promising. You just need a couple of beer crates, two bits of leather and some glue, and you could do full, proper scientific archaeological experiments, which is lovely to hear!
Paul: Yeah, the impact tests are also ones that you could do fairly makeshift, especially with a good quality camera. Because you have your adhesive sample and you basically have a pendulum hammer that swings down and hits your adhesive and breaks through it. And then the machine records the height that the hammer swings to on the other side. And then you calculate how much energy was lost during the impact and that tells you the impact resistance. If you had a good camera with a good grid background recording and a known mass of your hammer swinging on a ball bearing or something with very little resistance, you can record something similar. You wouldn't be able to compare it with other tests because there would be differences in the machine and that's one thing that this lab equipment is really good for. Different laboratories can do the same test and you can compare the results. If you're doing your own tests with a force gauge and a camera and things, that's harder to do that, but you can still get good information for comparing your own materials.
Phoebe: That sounds really cool.
Matilda: Also related to replicability, Phoebe, for example, you mentioned that you created your tar by doing it with the classic - I can't remember what the method was that you mentioned - but in a tin with a hole in and I assume that was done then outside with a fire lit, or was it done in a lab environment?
Phoebe: The first stage with the pots and the fire was done outside and actually the second stage was as well. The second stage where you then take the oil that you've got from your fire and refine it, that was done on a camping stove just outside the lab, because I wasn't using a lab that had a fume hood. It's very smelly and quite flammable, so that was not something we wanted to risk doing inside.
Matilda: What I was just curious about was, it seems to me at least, that it would be difficult to create the tar in sort of an authentic way inside a lab. I don't know, Paul, you probably have more experience with this. How can it be done? Is it replicable in that way?
Paul: Yeah, it's really difficult to create it in an authentic way inside the lab. Unless you had somewhere inside that you could dig a hole and light a campfire, like a big sandbox..., that would be really cool and you could do that in the lab. But what we do is when we want to make birch bark tar that we know exactly the temperature that it was produced at and stuff, we have what's called a tube furnace. It's basically an electric oven, but it heats up a vertical tube and then you put - it is exactly the same as this double-pot method that Phoebe described - but you have one pot inside the tube furnace and then a funnel and another part below the tube furnace and then you can program the furnace to specific temperatures. What we did the first time was make it in the field like a campfire, basically outside, but with the thermocouples, temperature probes, at four different locations around, and recorded the maximum temperatures that the birch bark reached during the production. And then we just set the tube furnace to the same temperature. It still is a little different because when you do it in a tube furnace or in a metal container, you collect a lot more material. But when you do it using Paleolithic techniques your containers are not so airtight, so you get a lot of those volatiles that you have to boil off afterwards are gone already. And you end up with something that's already more thick and viscous without having to reduce it afterwards.
Matilda: But I can imagine potentially less for the amount you're putting in because there's a lot more loss, or is the difference not so big?
Paul: It depends a little bit on how good you are at setting it up or how lucky you get. But in general, you get a little bit less and usually more contaminated with charcoal and sand or dirt or whatever is around. In the lab it's really pristine. There's nothing else contaminating it.
Phoebe: Am I right in thinking that these contaminants... I think the piece of tar from Zandmotor, does that have some sand in it?
Paul: Yeah, and charcoal as well. There's definitely nothing wrong with having contaminants in it. It's probably beneficial, like what you found with adding ash that having some other mineral fillers or charcoal, whether it was added on purpose or not is still unclear, but it could be beneficial. You don't need to spend a lot of time really trying to make it as clean as possible if you were doing it in the field. It's just harder to control because if we were to do that, maybe one batch would have more charcoal or more sand than another, and then you would have to measure that somehow. Otherwise your results might be actually measuring how much contaminants built into the tar and not something else. Whereas when you do it in the lab and you have no contaminants in it, it's just more clear, one more variable removed. But it's not necessary. And the two-pot… like with two metal paint tins is basically the same thing as we did. The temperature fluctuation would be a little higher, because it's got a natural campfire around, but otherwise, the process is exactly the same.
Matilda: It certainly sounds like there's enough future experiments for both of you to keep you occupied for the rest of your archaeological careers. We talked a little bit already about how there's limited material evidence for the background research, the chemistry knowledge is something that you have to overcome, the methodologies you use, the equipment you use is also something limiting. But one thing that you both had a lot of, before getting into this project, was crafting experience. Phoebe, you mentioned already you were a very experienced seamstress even before you started and Paul, obviously you're a fantastic woodworker and creating all kinds of tools, like knives and bows and things. So how big an influence did that experience have in your experimental work, and do you think that it is necessary for people to have that kind of crafting understanding in order to get into this topic specifically? Perhaps Phoebe, you could go first?
Phoebe: Yes and no I think. It's important for keeping you interested, definitely. For me, things like putting the grommets in the metal, I wouldn't have thought to have done unless I had done sewing before. If I hadn't been sewing before, I would've just thought putting a hole in the leather would have been enough. But the grommet helps to lessen the risk of the leather just ripping beforehand. What I'm actually doing in my experiments isn't very similar to the kind of sewing that I've done before, so it's not necessarily something you have to have, although as I said, it does help keep your interest.
Paul: I think going way back that it did have a big influence, because talking about woodworking and things like that, the summer before I started my masters, I had just built a mandolin. And on a mandolin - it's a small stringed instrument with eight strings, tuned like a violin - the steel strings exert about 70 kilograms of force on the neck, just constantly. It's just a glued joint, so it needs to have a really good glue. And I remember that summer before getting lost in discussions online about glue performance and testing. And modern glues tend to creep a lot under constant load and what's the best alternative and all kinds of things like that. And then when I started, I immediately was using some of that knowledge and ways of testing adhesives to get started with my master's thesis. In terms of getting started, it was definitely a huge influence. In terms of being a requirement or necessary or anything like that, I would say that having crafting experience maybe gives you a head start, but it's definitely not necessary. You can learn these things from once you start the experiments or start the research. You shouldn't go into an experiment, say testing adhesive hafting performance, if you've never hafted a stone tool before. But you can find people that have the expertise or you can learn it before you start the experiment. It takes you longer then to get there, and you might run into more hiccups along the way, like not using a grommet in the leather. Maybe it would tear first and then you'd have to rack your brains to try to come up with a way to make that joint stronger. Eventually, I'm sure you would get there, but not as quickly and easily as if you already have that experience. So it helps, but it's not necessary.
Matilda: From the discussion we've had today, I think it's a very positive view on anyone who wants to do glue, but has thought that it's an overly specialised subject. You can do it with beer crates, not having any crafting experience. It's easy, everyone should be doing it. Obviously much more complicated than that and we haven't really got into the full details of the research. But I thought it would be interesting to discuss the practicalities, shall we say, and the sort of details around this subject because it's such a rare one and it's such a fascinating one. So thank you very much both for that very interesting discussion. Just as a final question before we wrap up, what are your plans for the near future and how do you think the EXARC community or those listening in to this podcast can help to make a difference or to do their own research in regards to the points that we discussed today? Phoebe, you wanna go first?
Phoebe: My direct plans for the future are to work with this EXARC Grant that I've very kindly been given to explore Neanderthal footwear use, which is kind of an extension of my master's project, which I've just been doing. And I'm really, really excited to start getting some results from this, which hopefully will involve actually making some shoes, although we'll have to see!
Matilda: And walking in little puddles apparently to test the waterproofness...
Phoebe: Yes, I'm hoping so! And then the second part of that was how can the EXARC community help to make a difference. I think just being interested in it would be really cool. EXARC is quite big on social media. I think it could be a really interesting thing to start having a discussion through these kind of mediums. I'm just always keen to talk to people about this kind of thing, which is why this has been so nice.
Paul: Yeah, it's definitely good to just talk to people about it and especially with the EXARC community, there are a lot of skilled craftspeople that you can really get new insights into all kinds of different things, from knowledgeable people in different fields. Things that you can't learn about or experience from reading a book or sitting in front of a computer that you really need to have this hands-on experience with. That definitely is a really nice way to help the research go forward. In terms of my personal plans for the near future, well, I still have a year and a few months left in the current project that's called Ancient Adhesives at the TU Delft and it's going to be a busy year. We have a lot of data that we are gonna be writing up, everything to finish in the last part of the project. Hopefully I can find some time, while we're doing that to also apply for some new grants and hopefully can keep doing sort of the same stuff. Maybe branching out a little bit from just adhesives, but who knows?
Matilda: Well, it certainly sounds like there's enough to do. Thank you very, very much to both of you, Paul and Phoebe, for joining us today and sharing your experience and your expertise. I definitely learned a lot, and hopefully our listeners did as well. It's been very inspiring and I think an optimistic view of a relatively understudied research topic. And thank you to everyone else for listening in to this episode of #FinallyFriday by EXARC. If you would like to become more involved with EXARC - after all, our members do really interesting research on things like glue so it's really cool - you can become a member. Alternatively, you can also make a small PayPal donation through the website to help support EXARC in its endeavors through, for example, funding projects such as that which Phoebe will be doing with the EXARC Grant.
Join us next month for another episode of #FinallyFriday and learn more all about the world of experimental archaeology, ancient technology, archaeological open-air museums and interpretation. Don't forget to follow the show through exarc.net and our associated social media channels. See you soon.