The content is published under a Creative Commons Attribution Non-Commercial 4.0 License.
Reviewed Article:
Different Vessel Surface Polishing Methods and Mutual Effects of their Applications
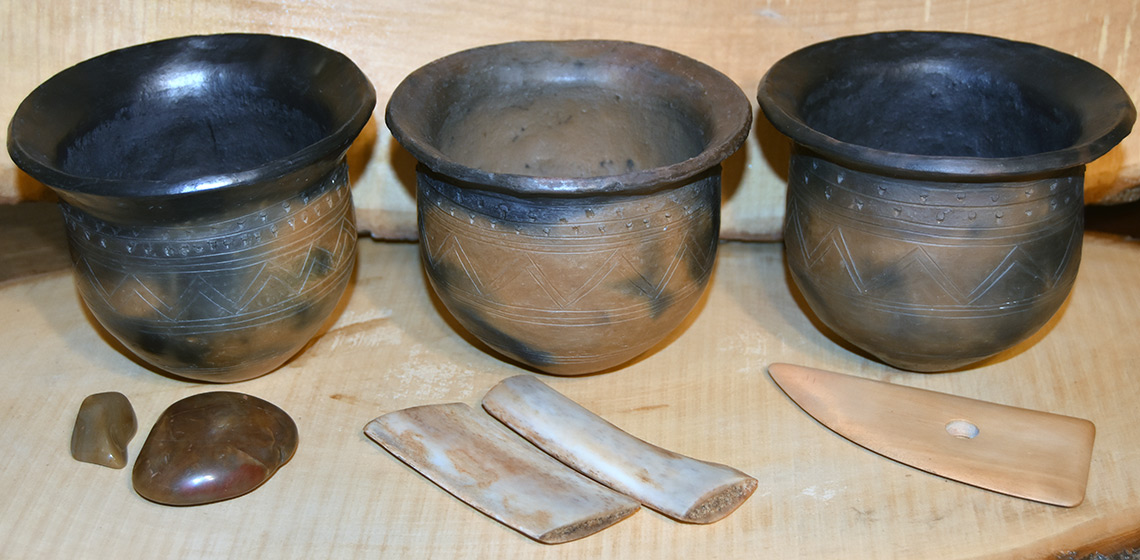
The discovery of an excavated cup with a glossy surface prompted reflection on the polishing of vessel surfaces and their mutual significance. We present the results of the application of three different polishing methods along with a reflection on their function and on the skills and ability of the potter.
Introduction
Petroarchaeological studies carried out in 2015 on selected fragments of pottery from sites in north-eastern Poland associated with Late Neolithic communities (Manasterski, 2009; Wawrusiewicz, et al., 2015; Krajcarz and Manasterski, 2015), revealed the presence of an interesting surface polishing process. This finish has stood the test of time despite the impact of post-depositional processes leading to the weathering of other pottery fragments from one of the sites.
It was identified on a fragment of a Bell Beaker cup (454/01) dated ca. to 2500-2000 BC, which had been made with coiling and had both surfaces of a "copper" colour (See Figure 1). Its inner surface was roughly finished, having not only horizontal traces of rubbing but also gravel grains of different granulation and imprints of plant fragments (grasses?). The external surface, on the other hand, was very carefully smoothened (rather polished than burnished; acc. Rice, 2015) and decorated with engraved and punctured ornamentation in a zonal arrangement, but here, too, single grains of crushed white stone can be seen.
Research has shown that careful treatment of the surface, especially polishing, is a very functional method of sealing the walls of dishes and helps with their cleaning (La Torre, et al., 2020). But was this method applied to a cup with the same goal in mind? While looking for an answer to this question, we became interested in the surface polishing method itself. In this article, we present the results of applying three different methods using readily available materials commonly mentioned in the literature (e.g., Van Gijn and Lammers-Keijsers, 2010; Rice, 2015): polished stone, a fragment of beef rib, a flat wooden tool.
The aim of the research was to find out which tool is most suitable for polishing and which gives the best appearance; at what stage of production the vessel's surface had to be polished in order to be as shiny as possible; whether this was done in one go or had to be repeated at different stages of the vessel's manufacture; and, finally, whether the use of aids such as animal fat is more effective than just smoothing and, if so, at what stage of the vessel's manufacture should the aid be applied? We are also trying to answer the question of whether the polishing was purely functional (sealing the vessel) or aesthetic (shining); (acc. La Torre, et al., 2020). Additionally, a seepage experiment was conducted to verify the functional properties of polished and unpolished vessels. In the article, we mainly focused on polishing as such, rather than burnishing. The reason for this approach was that during the classical macroscopic analysis of the fragment, no visible linear traces, typical of the latter method, were seen (acc. Rice, 2015).
Experimental framework
For the experiment, six copies of a Bell Beaker cup found at site II in Szestno (Masurian Lake District, Poland) were made. Two types of clay were used in their production: two cups were made of red clay, two more with a combination of light beige and red clay and two additional only with light beige clay. The use of different clays was intended to reproduce precisely the vessel's exterior, also with regard to the "copper" colour of the original cup. The red clay was sourced from the south of Poland (Lower Silesia). The light beige clay was gathered from the site vicinity as it naturally occurs in this region. This choice was prompted by potentially foreign provenance of the studied materials (Manasterski, et al., 2022). Mineral admixture coming from granite stone and river sand was added to the clay according to results of previous petrographic studies (Krajcarz and Manasterski, 2015).
In total, admixture constituted 16% of the paste used for vessel’s production, while thickness of the grains varied from dust fraction to 1.5 mm. The vessels were made using the coiling, then they were burnished with wooden tool to get more smoothened surfaces, beaten with wooden tool (acc. Derenne, et al., 2020) and subjected to drying (See Figure 2a). When the cup was slightly dried decorations analogous to the original cup were made with a wooden spatula, a flat-tip stylus and a bird feather (See Figure 2b). Subsequently, polishing was carried out after the clay had hardened, but before it had dried and again after it had dried. After this, the vessels were fired. Three of them were fired in a home-made open hearth with stone setting with a maximum temperature of 800 °C in the middle of December 2022 in Silesia (south-western Poland) [Experiment 1].
For comparative purposes and in order to ensure that the vessels would not be affected by the traditional firing, three more were fired in a pottery kiln (Cromartie Kilns LTD. Model cer 40 No12/1299) with the temperature set at 800°C [Experiment 2]. In order to achieve the greatest shine, some vessels were greased with pork lard at room temperature [Experiment 3]. To verify the functionality of the polishing, a seepage experiment was conducted on all of the vessels [Experiment 4]. It aimed to study cups made with different chaîne opératoire – each of them had differently treated surfaces (unpolished, polished, greased with animal fat, ungreased with animal fat) and were fired under various conditions (electric kiln, open hearth). As the experiment aimed to check how much water had seeped through the vessel, 300 millilitres of water was poured into each vessel and the water level marked with a marker. The condition was observed over a period of two hours.
Proceeding
The cups (See Table 1) were formed using the same technique – coiling, but the red clay behaved slightly differently during drying. Due to the higher fat content felt in touch and thus shrinkage, it was necessary to beat the dishes with a wooden spatula more carefully and for longer periods of time during the forming process. This prevented the surface of the cups from deforming during drying. A higher surface gloss was also achieved when smoothing, so that it was not necessary to polish a second time as it was done in the first version of the experiment. After firing in the open hearth, the dishes showed a higher gloss, probably due to the greasiness of the soot formed during wood burning. It also resulted in reductive atmosphere of the firing, which caused various colouration of the surface of the vessels as beige-orange-black spots. This was probably due to the low temperature achieved in the firing chamber and the high quantity of generated ash.
The polishing of the vessels was carried out once in the case of red clay cups and twice in the case of cups made with mixed clays. Polishing was started just before the clay was completely dry; this moment can be observed when the surface of the clay stops spreading and "pulling", but still retains some plasticity.
Fabric | Shaping | Surface treatment / Polishing tool | Decoration | Tools | Drying stage | Firing | Brightness | Traces identified | Greasing / Rows | |
C1 | Beige + red clay | Coiling, beating, | Burnishing, Polished / Stone | engraved and punctured ornamentation in a zonal arrangement | Wooden spatula, bird feather | Plastic | Electric kiln | Shiny | Shiny polished markless surface | Pork fat / Three times rubbed with a pork fat. |
C2 | Red clay | Coiling, burnishing, beating, | Burnishing, Polished / Bone | engraved and punctured ornamentation in a zonal arrangement | Wooden spatula, bird feather | Plastic | Open hearth | Very shiny | Striations | No / - |
C3 | Beige + red clay | Coiling, burnishing, beating, | Burnishing, Polished / Wood | engraved and punctured ornamentation in a zonal arrangement | Wooden spatula, bird feather | Plastic | Electric kiln | Shiny | Fluting | No / - |
C4 | Red clay | Coiling, burnishing, beating, | Burnishing, Polished / Stone | engraved and punctured ornamentation in a zonal arrangement | Wooden spatula, bird feather | Plastic | Open hearth | Extremely shiny | Shiny polished markless surface | Pork fat / Three times rubbed with a pork fat. |
C5 | Beige + red clay | Coiling, burnishing, beating | Burnishing, Polished / Bone | engraved and punctured ornamentation in a zonal arrangement | Wooden spatula, bird feather | Plastic | Electric kiln | Shiny | Striations | No / - |
C6 | Red | Coiling, burnishing, beating, | Burnishing, Polished / Wood | engraved and punctured ornamentation in a zonal arrangement | Wooden spatula, bird feather | Plastic | Open hearth | Shiny | Fluting | No / - |
C7 | Beige clay | Coiling, beating, | No / - | engraved and punctured ornamentation in a zonal arrangement | Wooden spatula, bird feather | Plastic | Open hearth | Mat | Mat markless surface | No / - |
C8 | Beige clay | Coiling, beating, | No / - | engraved and punctured ornamentation in a zonal arrangement | Wooden spatula, bird feather | Plastic | Open hearth | Mat | Mat markless surface | Pork fat / Three times rubbed with a pork fat. |
Table 1. Different chaine opératoires of the produced vessels.
Using the stone (See Figure 3) gave by far the best result when polishing. It was the tool with the hardest and most stable surface, resistant to scratching by grains of admixture. The clay yielded easily to the stone, making it possible to level out surface irregularities and indent protruding admixture grains. After using the stone, the surface of the vessel was completely smooth and “glassy", with a high gloss. The polishing time was approximately 20 minutes. In Experiment 2, after the cup had dried completely (after a few hours – 1 night in this case), the obtained gloss decreased and the surface became dull during drying, so polishing was performed a second time. This was done in the same way, except that the surface could no longer be corrected and smoothed, only polished, as the clay had hardened completely. The second polishing took about 15 minutes and restored the previous gloss. In Experiment 1, the vessel made with red clay retained its gloss after it had dried completely, so re-polishing was not necessary.
The bone tool (a fragment of a polished beef rib polished on sand stone for surface treatment) proved to be a softer material and to have less impact on the desiccated clay (See Figure 4). The levelling of irregularities was not as effective as in the case of stone, the admixture grains were also less susceptible to polishing and left traces on the surface and a lower degree of gloss was obtained. The polishing process was carried out in a similar way as with the stone described above – the first polishing before the cup was completely dry, lasting about 20 minutes, followed by the second (next day) polishing on the completely dry cup, lasting about 15 minutes. In Experiment 1, also the first polishing gave a satisfactory result, the surface did not tarnish during drying, so this procedure was not repeated. The bone itself initially became shiny, but with sharper grains of admixture its texture became duller and small scratches appeared.
The wooden smoother – the softest one – was the least effective tool (See Figure 5). It also gave a shine, but less than stone or bone. The surface of the cup did not become as smooth and slippery as when stone was used, because the smoother itself was scratched and tarnished in contact with the grains of admixture contained in the clay. The levelling of irregularities was visible but limited. The polishing process was carried out in the same way as described above for Experiment 1 and Experiment 2 and took a similar amount of time.
All the vessels were then fired, some of them under controlled conditions (kiln) at 800°C., the others in uncontrolled conditions in an open hearth with a stone setting (See Figure 6). In the first case, a red clay cups fired in an oxidising atmosphere acquired a brick and the mixed ones an orange colour. In the second case, changing weather conditions (strong wind), and most likely the use of mixed kinds of wood, caused partial reduction and partial blackening of the vessels (see Buko, 1990, pp.152-155). Nevertheless, smooth copper-coloured walls were achieved.
Experiment 3
Half of some of the vessels (C3, C4, C8) were greased using 200g of a pork lard, which was rubbed into the walls of the vessels several times to achieve the greatest possible shine.
Experiment 4 was carried out after the vessels had been made, fired and polished. 300 ml of water was poured into each vessel at 4 p.m. and reached 8,5 cm of height (See Figure 6). The water level was marked with a marker. After 1 hour (at 5 p.m.) the distance of the water surface from the marked level was measured for each of the dishes tested. After another hour the distance of the water surface was measured again, this time from the level marked in point 2. The water from each of the test vessels was poured successively into a measuring cup and its volume in milliliters was measured. All results are recorded in Table 2.
Start | After 1 hour (in mm) | After 2 hours (in mm) | Final | |
C1 | 300 ml | 6 mm | 2 mm | 250 ml |
C2 | 300 ml | 5 mm | 1 mm | 260 ml |
C3 | 300 ml | 4 mm | 1 mm | 257 ml |
C4 | 300 ml | 3,5 mm | 0 mm | 265 ml |
C5 | 300 ml | 4 mm | 1 mm | 259 ml |
C6 | 300 ml | 5 mm | 1 mm | 258 ml |
C7 | 300 ml | 4 mm | 3 mm | 240 ml |
C8 | 300 ml | 4 mm | 1 mm | 235 ml |
Table 2. Results of the seepage experiment.
After 1 hour: under the polished and unpolished ungreased vessels, a slight dampening of the surface on which they stood appeared in the form of a circle of small drops under the bottom. In the case of the greased vessels this did not occur, the surface under the bottom remained dry. The result of the experiment with C8 may not be entirely reliable, because a small amount of water seeped out (from 300 ml to 235 ml) through a small crack that appeared during firing and after 2 hours there was oozing condensation where no animal fat had entered.
Results
A high degree of surface gloss was achieved during both experiments related to the polishing process (See Figures 7-9). The vessels made with mixed clay were even polished twice to achieve the highest possible shine. After firing in controlled conditions, the surface in both experiments became slightly duller. Therefore, following a suggestion in the literature (e.g., Mogielnicka-Urban, 1984, pp.122-127), animal fat was applied to half of one of the vessels (See Figure 10) to darken the surface, enhance the colour and improve the gloss. Interestingly, the vessels fired in the hearth had a much better lustre. However, this observation is hampered by the dominant black on the vessel. The red clay produced a higher gloss and a darker colour than the mixed red and beige clay, because the red one was oilier. It also caused slight deformation of the cup during drying and firing. When it comes to observing the polishing process and its effects, stone gave the best result – the best smoothing and the greatest shine. In second place was bone, in third place was wood, because it is the softest and has a matte texture. The greasing at the final stage brought out the depth of colour of the vessels and gave an extra shine.
The vessels polished and greased showed the lowest seepage. Also, the open hearth firing (probably due to the presence of oily soot, even if it is not visible on the surface of the vessels), and the higher content of oily red clay had an impact on the reduction of seepage. The vessel without the addition of red clay, without polishing and without fat absorbed the most water into itself. Experience shows that the best water tightness of vessels can be obtained after all three treatments: polishing the walls, firing in a wood-fired hearth, and rubbing the walls with fat after firing. Red clay also absorbs less water due to its fattiness. The technique of rubbing the walls with fat before firing is still worth testing.
Discussion
As already mentioned, polishing the surface of vessels is a very important process that has the real benefits of preventing liquids from leaking and making the pottery easier to clean (La Torre, et al., 2020). Given its qualities, it should be noted that it also has its own decorative value, which is often forgotten considering the numerous decorations of various natures on pottery (i.e., incisions, applications). Achieving the effect of polished walls requires a careful eye and applying the exact technique to achieve the best possible result. Sometimes it even requires additional polishing attempts, as well as the use of "enhancers" for the effect. This experiment showed that the best technique for polishing is the one using a stone, but only when highly polished. In this case it is also worth to further verify the impact of beating and burnishing.
Polishing can be done before the vessel completely dries, even several times for a better effect. However, much about this method of surface treatment depends on the skill of the potter themselves. Of course, polishing itself is not difficult, but requires knowledge, familiarity with the "know how", which is, after all, generated by the "know why". Here we return to the purpose of polishing vessels.
Regarding the vessel, which was the starting point of the presented experiment, the decorative layer had already been provided by wooden tools and a bird feather. Polishing the surface here could therefore be an expression of technological care for the vessel. However, the technical approach to other parts of it, e.g., the poorly performed smoothing and no visible polishing inside the vessel (in contrast as in Gawron-Szymczak, et al., 2020), as well as the composition of the ceramic paste itself, which included large grains of mineral temper, lead us to conclude that the maker of the vessel was not an eminent specialist in this field, but rather was very keen to achieve this kind of outer surface. For sure, it had some functional benefits. There was certainly less leakage from the vessel, but probably the maker was more concerned with accomplishing a visual effect. Various "boosters" may have helped him/her do this. The literature indicates that animal fat used by us may have been applied also in the past (Mogielnicka-Urban, 1984, pp.122-127). Its application gave not only a visual effect and enhanced colour and shine, but also reinforced the walls against leakage. The results of the experiment showed that the best leak-tightness of vessels can be obtained after applying the following treatments: using "fatty" clay, burnishing and beating of the surface, polishing the walls with stone, firing in a wood-fired hearth, and greasing the walls after firing with pork fat (8% of improvement). While we do not have the lipid data to support greasing vessels’ surfaces with fat in the past, we would like to point out that such technological behaviour may have occurred and lipid results that indicate the presence of such fats in vessel walls would need to be reconsidered.
Conclusions
A conscious approach to surface polishing has a significant effect on the appearance of the vessel after firing. The tools used for polishing of the vessels’ surfaces used in the present study can be ranked according to the quality of the resulting effect, from the best: stone, bone, wood. Each tool produced a smoothing and shining of the surface of the vessels, but to varying degrees. Each of these tools may have been available and used in the past. Research has shown that the most effective polishing should be done when the vessel become plastic – while it is reasonably dry, but not devoid of water. Experimentation has shown that the amount of polishing depends largely on the fattiness of the clay – the fattier, the less polishing needs to be done. The experiment showed that although firing the vessels somewhat quenches the shine of the vessels, it can be improved by greasing the walls with fat. Previous research (La Torre, et al., 2020) has shown that polishing the walls is also a functional process. This was also demonstrated in the present study - polished vessels, as well as those covered with animal fat, are much less permeable to liquids placed in them. Therefore, in order to assess the aesthetic value of polishing treatment, other factors related to the 'know-how' and 'know-why' used in vessel manufacturing must be taken into account.
Acknowledgments
The experiment is a part of a broader project on the reconstruction of Bell Beaker vessels from north-eastern Poland conducted by the Faculty of Archaeology University of Warsaw.
Keywords
Country
- Poland
Bibliography
Buko, A., 1990. Ceramika wczesnopolska. Wrocław: Wprowadzenie do badań..
Derenne, E., Ard, V. and Besse, M., 2020. Pottery technology as a revealer of cultural and symbolic shifts: Funerary and ritual practices in the Sion ‘Petit-Chasseur’ megalithic necropolis (3100- 1600 BC, Western Switzerland). Journal of Anthropological Archaeology, 58, https://doi.org/10.1016/j.jaa.2020.101170.
Gawron-Szymczak, A., Łaciak, D. and Baron, J., 2020. To smooth or not to smooth? A traceological and experimental approach to surface of Bronze and Iron Age ceramics. Sprawozdania Archeologiczne, 72(2), pp.67-86. DOI: 10.23858/SA/72.2020.2.2275.
Krajcarz, M.T. and Manasterski, D., 2015. Ceramika Pucharów Dzwonowatych z północno-wschodniej Polski w świetle analiz petrograficznych. Studia i Materiały do Badań nad Neolitem i Wczesną Epoką Brązu na Mazowszu i Podlasiu 5, pp.49-85.
La Torre, A., Mannino, G. and Zurzolo, A., 2020. Fine Pottery Chaîne Opératoire from the Bronze Age site of Via Ordiere, Solarolo (RA, IT): Experiments on the Relationship between Surface Treatments and Function. EXARC Journal, 2020(1), https://exarc.net/ark:/88735/10483.
Manasterski, D., 2009. Pojezierze Mazurskie u schyłku neolitu i na początku epoki brązu w świetle zespołów typu Ząbie-Szestno. Warszawa: Instytut Archeologii, Uniwersytetu Warszawskiego.
Manasterski, D., Januszek, K., Wawrusiewicz A. and Klecha, A., 2020. Bell Beaker Cultural Package in the East European Periphery of the Phenomenon. Documenta Praehistorica 47, pp.374-389. https://doi.org/10.4312/dp.47.20
Manasterski, D., Januszek, K. and Cetwińska, A., 2022. Bell Beakers in the Masurian Lake District in north-eastern Poland – relics and identification issues. Praehistorische Zeitschrift, app, https://doi.org/10.1515/pz-2022-2032.
Mogielnicka-Urban M., 1984. Warsztat ceramiczny w kulturze łużyckiej. Wrocław.
Rice, P., 2015. Pottery Analysis, Second Edition. A sourcebook. Chicago.
Wawrusiewicz, A., Januszek, K., Manasterski, D., 2015. Obiekty obrzędowe pucharów dzwonowatych z Supraśla. Złożenie darów – przejęcie terenu czy integracja kulturowa? Ritual Features of Bell Beaker in Supraśl. The Offering – Taking Possesion of the Land or Cultural Integration? Białystok.
Van Gijn A. and Lammers-Keijsers Y., 2010. Toolkits for ceramic production: informal tools and the importance of high power use-wear analysis. Bulletin de la Société Préhistorique Française, 107 (4), pp.755-762.