The content is published under a Creative Commons Attribution Non-Commercial 4.0 License.
Reviewed Article:
Peat Burns: The Methods and Implications of Peat Charcoaling
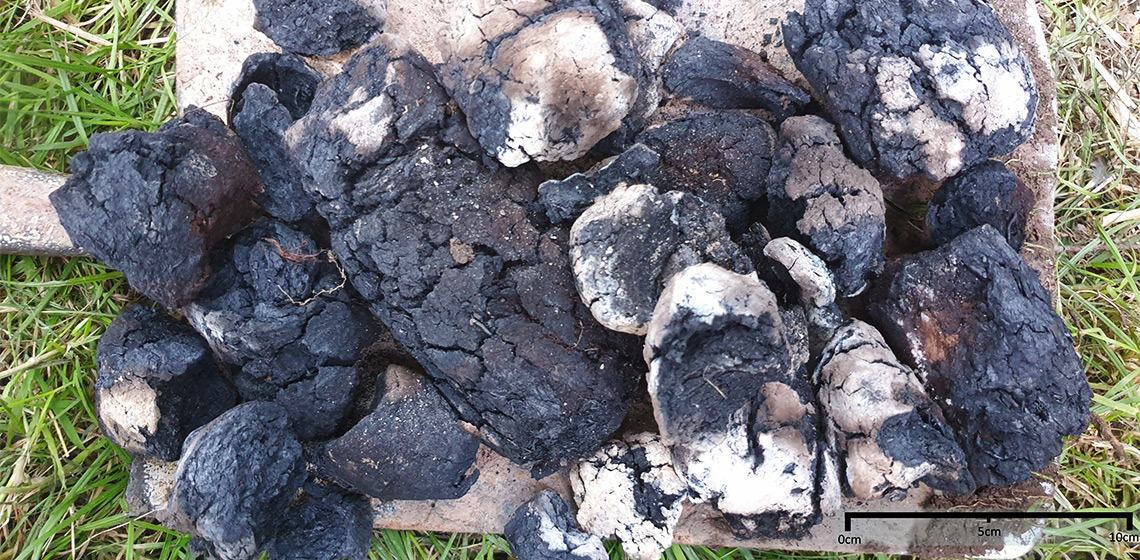
The Northern Isles of Scotland offer a fascinating case study for understanding past economies and resource management due to the comparative lack of trees found elsewhere in the British Isles. Archaeological evidence proves that this environment did not prevent the development of industrial pursuits in this region during the Iron Age and local accounts dating to the 19th -20th centuries detail how blacksmiths were charcoaling peat in pursuit of metalworking endeavours. Little, however, is known about this peat charcoaling process. By following the peat charcoaling steps identified in ethnographic and historic accounts from the Northern and Western Isles of Scotland it was possible to create this fuel with relative success. This paper describes the way in which 155.6kg of peat was charcoaled across 10 attempts which produced an average yield higher than would be expected from charcoaling wood via similar methods. Small fluctuations in the moisture content of the peat and differences in fanning style had no statistical relationship with the yields produced. The experience of the charcoaler appears key as an even temperature profile was challenging to attain with possible repercussions for the quality of the fuel for the iron smelter and smith.
Introduction
Peatlands are an important facet of the modern economy of the Northern Isles with, for example, 13.5% of those living in Shetland harvesting peat for household fuel (Citizens Advice Bureau, 2013, p.14). This importance is thought to extend into prehistory with blanket peatland forming in parts of the Northern Isles by 1500 B.C. (Dickson, 1994, p.133 & p.126). At the Iron Age site of Wiltrow, Shetland, Curle goes as far as to hypothesise that peat must have been an important fuel for industrial activities, such as iron smelting (1936, p.153 & p.165). The fact that just c.5-10% (Farrell, 2015, p.473; Timpany et al., 2020, p.10) and c. 15% (Edwards et al., 2005, pp.1745) of pollen recovered from Iron Age Orkney and Shetland respectively are from arboreal sources suggests that Curle’s theory may be correct. Positing the idea of peat as an iron smelting fuel is further justified when considering that 1kg of iron may require over 140kg of wood to produce when assuming a wood:charcoal ratio of 8:1 (Oaks, 2018, p.48) and a charcoal:iron ratio of 10-18:1 (Pleiner 2000, p.126). Tylecote (1990, p.140) claims that peat must be charcoaled if it is to be used for iron production due to the detrimental impact of peat’s sulphur content. This paper will provide a brief overview of the possible relationship between peat and metalworking in the archaeological record before exploring the ethnographic and historic record. The results of experimental peat charcoaling attempts based on these accounts are then detailed to better understand the influences of the process, and implications for understanding the past economy of the Northern Isles are discussed.
The archaeological context
There is a range of Iron Age sites from the Scottish Northern Isles that have produced evidence for iron smelting and smithing in association with peat. In Shetland this can be seen in, for example, the layer of peat ash over the smelting area at Underhoull (Small, 1964, p.230) and Scalloway (Campbell, 1998, p.123), which also appears to have used a more humified peat than the contemporary, but non-smelting, sites of Kebister and East Shore (Campbell, 1998, p.123; Holden and Boardman, 1998, p.105). Orkney too shows an association between peat and iron working with peat ash being contained within a furnace dump with slag at The Howe (Dickson, 1994, pp.131-4) and carbonised peat being associated with furnace deposits, hearth rakes, and iron slags (pers. comm. Nick Card). It therefore appears reasonable to posit that peat may have been involved in the ironworking process at these sites.
The ethnographic and historic evidence for peat charcoaling
There are historic and ethnographic accounts of peat charcoaling from the Highlands and Islands throughout the 19th and early 20th centuries, for example, in Orkney, the island of Harray was known for having peat that would burn like coal once it had been charred by blacksmiths to work iron (Fenton, 1997, pp.206-210 & p.238). In North Uist, in the Outer Hebrides, a blacksmith states that the production of peat charcoal continued as late as 1909/10 (MacDonald, 1962) and on the Isle of Jura, Inner Hebrides, this fuel was so ubiquitous with blacksmiths that it earned the name ‘smiddy coal’ (MacLeod and Maclean, 1972). Details on how to successfully conduct this peat charcoaling process, however, are sparse but by looking at accounts from across the Northern and Western Isles a broad picture can be formed.
The principles of peat charcoaling are generally similar across the Northern and Western Isles with peat being carefully loaded into pits and lit from the centre before adding more fuel and eventually smothering the pit with turf (Fenton, 1997, p.237; MacDonald, 1962). However, the size and shape of these charcoaling pits do vary. Bell shaped pits with a diameter of ~180cm and a depth of ~36cm were most common in Shetland in the Northern Isles (Fenton, 1997, p.237), and rectangular pits ~244cm long, ~91cm wide and ~91cm deep appear to have been in the standard in North Uist in the Western Isles (MacDonald, 1962). It should be noted that ‘mòine dhubh’, Scots Gaelic for ‘black peat’, was specifically targeted for the production of charcoal in North Uist (MacDonald, 1962). This matches the type of peat used in Orkney (Fenton, 1978, p.213) and refers to a more humified type of peat, possibly correlating with the type of peat found archaeologically at the iron working site of Scalloway (Campbell, 1998, p.123).
Aims and objectives
The aims of this research were to assess the yields and the influences on the outputs of peat charcoaling. To do this, a series of 10 experimental charcoal attempts were conducted following these ethnographic and historic accounts. Field observations including the quantity of peat put into each charcoaling attempt, the moisture of the peat, the amount of artificial fanning carried out, the types and quantities of material recovered from each charcoal attempting, and the temperature profile of the charcoaling pit were recorded.
Methods and Materials
169.3kg of peat was donated by the Aberdeenshire based PeatHeat, which had been extracted using a screw typed auger creating, small, very slightly compacted and cylindrical pieces of peat. This peat was determined to generally be between H6 and H9 on the Von Post scale based on the visual appearance of plant remains (SEPA, 2017, pp.11-12) and thus could be considered ‘black peat’. The peat was tested using a moisture meter to ascertain the average water content of the peat before being added to one of three charcoaling pits. These charcoaling pits were circular and steep sided following Fenton’s (1997, p.237) account from Shetland while measuring 76x76cm, 73x78cm, and 78x75cm, with depths of 25cm, 25cm and 26cm, respectively (Figure 1). These pits were intentionally smaller than those attested ethnographically as it was believed that these would be better suited to the lack of experience of the author and volunteers. Mahler and Jouttijärvi (2005) had also proven that, within a Faroese context, that these smaller pits would still function for charcoaling peat. A fire was lit in the centre, as per MacDonald (1962), using straw wrapped in a light stock cardboard tube, surrounded by ~5 pieces of wood kindling and ~2.5kg of peat (Figure 2a). This fire was gradually fed peat until ~33-50% of the total peat that was intended to be charcoaled had been added (Figure 2b). Time was allowed to pass until all the peat had lit and the fire had spread across the base of the pit before the remainder of the fuel was added (Figure 2c). The pits were then smothered with damp turfs as according to (MacDonald, 1962) and Mahler (pers. comms.) (Figure 2d). The resulting charcoal was then collected between 24 and 30 hours later. Three Type K thermocouples were inserted into the charcoaling pit of attempt no.10 to record temperatures from the left, centre, and right-hand side of a charcoaling pit for the entire duration of the process. There was no comment in any of the aforementioned historic and ethnographic accounts on whether the pit was at any point fanned. Therefore, four different fanning styles were attempted with cardboard sheets: no fanning, occasional fanning, intermittent fanning, and constant fanning, which also employed the additional aid of double-lung accordion bellows. The impact of these variables was tested statistically using IBM’s SPSS (v.25). All experiments were conducted in Abbeydale, South Yorkshire.
Results
155.6kg of peat produced 26.8kg of charcoal and 32.1kg of partially charcoaled peat from 10 charcoaling attempts (Figure 3). The yields of this process averaged at 5.8:1 (17.2%) when excluding the unburned peat but including the partially charcoaled peat as peat lost. The best attempt managed to reach a yield of 3.1:1 (27%) (See Table 1) which is in line with the yield figures quoted by Mahler and Jouttijärvi’s experiments, (25-30%) (2005:94). This yield was also attained by a volunteer manipulating the pile of burning peat by knocking it over to assist the spread of the fire. An average of 37.1% of the peat was not charred and so could be reused in subsequent charcoaling attempts. See Figure 1 for typical distribution of the different charcoaling products within the pits.
Char. 1 | Char. 2 | Char. 3 | Char. 4 | Char. 5 | Char. 6 | Char. 7 | Char. 8* | Char. 9 | Char. 10* | Average | |
Average moisture content | 22% | 23% | 27% | 33% | 23% | 34% | 33% | 33% | 33% | 33% | 29% |
Fanning Style | Const. | Const. | Const. | Inter. | Inter. | Inter. | Occas. | Occas. | None | Occas. | Inter. |
Quantity of peat used | 32.0 kg | 40.0 kg | 43.6 kg | 25.9 kg | 23.6 kg | 25.4 kg | 22.6 kg | 24.3 kg | 24.4 kg | 24.6 kg | 28.6 kg |
Peat charcoaled | 2.1 kg | 2.8 kg | 4.8 kg | 1.4 kg | 2.2 kg | 2.6 kg | 2.3 kg | 2.2 kg | 1.6 kg | 4.8 kg | 2.7 kg |
Peat partially charcoaled | 2.6 kg | 1.4 kg | 3.8 kg | 2.0 kg | 3.5 kg | 3.9 kg | 4.8 kg | 3.1 kg | 3.5 kg | 3.5 kg | 3.3 kg |
Peat lost | 7.1 kg | 21.4 kg | 29.1 kg | 6.7 kg | 7.1 kg | 10.1 kg | 10.6 kg | 5 kg | 8.7 kg | 16.3 kg | 12.2 kg |
Peat uncharred | 20.2 kg | 14.4 kg | 5.9 kg | 15.8 kg | 10.8 kg | 8.8 kg | 5.2 kg | 14.0 kg | 10.6 kg | 0.0 kg | 10.6 kg |
Peat consumed:Charcoal produced | 4.6:1 | 8.1:1 | 6.9:1 | 6.2:1 | 4.8:1 | 5.4:1 | 6.7:1 | 3.7:1 | 7.6:1 | 4.1:1 | 5.8:1 |
Table 1. Summary of peat charcoaling attempts. (Const.=Constant, Inter.=Intermittent, Occas.=Occasional) *Charcoaling attempts in which the stack of burning peat was toppled
As seen in Figure 4, the temperatures within the charcoaling pit typically ranged between 400 and 600°C with fanning greatly assisting temperature increases, with the post-fanning temperature decline being steady. However, an even temperature throughout the pits was challenging to achieve, with one side dropping below the point at which sulphur would have been removed (444.6°C Encyclopaedia Britannica n.d.).
Statistic | Std. Error | |||
Skewness | Kurtosis | Skewness | Kurtosis | |
Charcoaled | 1.254 | .516 | .687 | 1.334 |
Peat Lost | 1.156 | .905 | .687 | 1.334 |
Fanning Style | -.610 | -.157 | .687 | 1.334 |
Average Moisture | -.691 | -1.704 | .687 | 1.334 |
Table 2. Skewness and Kurtosis of data collected
Shapiro-Wilk | |||
Statistic | df | Sig. | |
Charcoaled | .806 | 10 | .017 |
Peat Lost | .900 | 10 | .220 |
Average Moisture | .737 | 10 | .003 |
Fanning Style | .886 | 10 | .152 |
Table 3. Shapiro-Wilk test of normality results
The non-parametric correlation test Spearman’s Rho was conducted to assess whether there was a relationship between fanning style and charcoal produced or peat lost. This test was chosen due to the non-standard distribution of the data, as indicated by the high skewness and kurtosis values as well as the insignificant Shaprio-Wilk values (See Table 2 and Table 3) and the lack of clear monotonicity between the variables and the charcoal outputs. This revealed that there was no significant correlation between the variation in moisture content and the outputs of the charcoaling attempts (See Table 4). Insignificant results were also returned when testing if the fanning style correlated with the outputs of the charcoaling attempts (See Table 4). This suggests that other factors were more significant.
Spearman's rho | |||
Peat Charcoaled | Peat Lost | ||
Average Moisture | Correlation Coefficient | .033 | .110 |
Sig. (2-tailed) | .929 | .762 | |
N | 10 | 10 | |
Fanning Style | Correlation Coefficient | .400 | .261 |
Sig. (2-tailed) | .252 | .467 | |
N | 10 | 10 |
Table 4: Spearman’s Rho correlation test results
Discussion
This research was unable to identify a quantifiable influence on peat charcoaling yields. This is due to the lack of correlation between the moisture content of the peat used and the fanning styles with the outputs of peat charcoaling attempts. This suggests that other variables, unaccounted for here, may be significant instead. Variation in skill is likely to be one such variable, although not easily quantifiable. The initial lack of experience in charcoaling is visible in the substantial quantities of uncharred peat remaining after each attempt and the difficulties in attaining consistent temperatures throughout the pit. The impact of differing skill levels on yields can be seen in charcoal attempts no. 8 and no. 10 which produced the best yields, possibly due to a volunteer deciding to knock over the stack of burning peats to assist the spread of the fire. The lack of experience meant that these experiments were typified by what Townend (2005, p.206-7) coins ‘presence-at-hand’ due to the limited ability to employ skilled coping. This means that the nature of these charcoaling attempts would have been substantially different to charcoaling attempts conducted by skilled blacksmiths and as such the emphasis of testing these variables may be misguided.
As stated, the lack of experience had a noticeable impact to attaining an even temperature within the charcoaling pits, with the thermocouples identifying differences of up to 250°C between one edge of the charcoaling pit and its centre. Within the context of metalworking this appears to put the fuel at risk of being high in sulphur which would worsen the mechanical properties of any iron that was smelted or smithed with it. Certainly, pXRF analysis suggests that sulphur was found to have been significantly elevated in the smelt products and furnace material after the use of peat charcoal (Jack, forthcoming). The notable increases in temperature associated with fanning the charcoaling pit suggests that this problem may be prevented by a more effective fanning technique or by the wind encountered in the unsheltered Northern Isles. A natural draught, which was not encountered during these charcoaling experiments in South Yorkshire, combined with a more effective charcoaling procedure, is thought to be capable of reducing the sulphur content substantially. Practised placement of the charcoaled peat during smithing would also allow the fuel to burn off additional sulphur before encountering the metal, as would the avoidance of blockages during the smelting process. Therefore, although not ideal, the possible sulphur content that the iron might encounter can, theoretically, be reduced during both smelting and smithing stages.
Despite the lack of experience, the yields achieved here are favourable to those that might be expected from charcoaling wood. Using the 8:1 figure provided by Oaks (2018, p.48) the least efficient peat charcoal attempt (Char. no. 2) matched the efficiency of the wood charcoaling process. Combined with the average yield being 1/3 more efficient than wood charcoaling, and the twice as efficient yield of Char. no.8 (See Table 1), it might be thought that peat is a better fuel to charcoal than wood. While already impressive, these yields may be improved upon further by the skill and experience held by peat charcoalers in the past. These yields would have been greatly beneficial to communities who may have been worried about the fuel consumption of activities such as metalworking. Additionally, when considering the similarity of the process to charcoaling wood and the presence of blanket peat since 1500B.C. (Dickson, 1994, p.133 & p.126) it would seem likely that charcoaling peat would have occurred substantially prior to the historic and ethnographic accounts used here. It may even be legitimate to propose that the charred peat recovered from archaeological sites may be from the intentional creation of peat charcoal as opposed to accidental charring, particularly when found in association with metalworking debris.
It should be remembered, however, that, in the same way that woodlands can be over exploited, so too can peatlands. The over-cutting of peatlands has historically had disastrous effects on local communities with, for example, the islands of Uist and Papa Stour, Shetland, witnessing significant population decline due to the lack of fuel (Fenton, 1978, p.223). Sanday and North Ronaldsay, Orkney, were able to resort to cow dung for fuel when peat reserves were running low, but this led to extensive mockery by other Orcadian communities (Ibid, p.209). The use of peat, therefore, cannot be considered a perfect solution to marginal woodland resources but rather a vital part of a larger resource management regime.
Conclusion
This experimental campaign has suggested that intentionally charcoaled peat may be a legitimate interpretation for the charred peat found within archaeological contexts. This is because the general principles outlined in historic and ethnographic accounts from the Western and Northern Isles of Scotland successfully produced a charcoaled peat despite the inexperience of the author and volunteers. Considering the availability of peat to past communities in the Northern Isles as well as the length of contact these communities had with peat, even in the Iron Age, it seems reasonable to assume that peat charcoaling would have been attempted due to the relative simplicity of the process and its similarity to wood charcoaling. Once realised, the greater efficiency of the peat charcoaling process compared to what is expected from charcoaling wood may have encouraged the use of peat charcoal and alleviated economic strains and pressures on the marginal woodland resource in the Northern Isles. This interpretation opens a new avenue to understand the role of peatlands in past landscape management strategies.
A correlation between fanning type or slight moisture variation could not be ascertained statistically here, perhaps owing to the significant contribution of individual skill and technique. A skill gap exists between those conducting the charcoaling attempts and those who conducted it historically, and possibly in prehistory. This contributed to an inability to attain an even burn throughout the pit, leaving sulphur within the fuel. This would create a challenge for smiths and smelters, however, one that would likely be reduced via more skilful charcoaling and negated via careful placement of the fuel.
Acknowledgements
I must acknowledge the extensive support and assistance offered by Charlotte Cooper in conducting these peat charcoaling experiments as well as the assistance of Thomas Dunn. Additionally, the insightful conversations had with Dr Julie Gibson, Dr Ian Tait, Dr Stephen Carter, Dr Ditlev Mahler and Brian Smith with regard to all aspects of peat, Northern Isles archaeology and history must not go unrecognised. Without the generosity and interest shown by PeatHeat and Highland Park this campaign would not have been possible. The support of the Department of Archaeology and the Scottish Association of Metals has also been tremendously appreciated and helped me fund my studies in Sheffield and thus carry out this passion project. Finally, the continued support of my supervisor Professor Caroline M Jackson has been hugely appreciated.
Keywords
Country
- United Kingdom
Bibliography
Campbell, E., 1998. Metalworking. In N. Sharples, Scalloway: A Broch, Late Iron Age Settlement and Medieval Cemetery in Shetland. Oxford: Oxbow, pp.123-4.
Citizens Advice Bureau, 2013. Fuel Bills Survey Report Shetland Islands. [pdf] Available at < https://www.cas.org.uk/system/files/Fuel%20Bills%20Survey%20Report.pdf > [Accessed 21 November 2020].
Curle, A. O., 1936. Account of the excavation of an iron smeltery, and of an associated dwelling and tumuli at wiltrow in the parish of Dunrossness, Shetland, The Society of the Antiquaries of Scotland, 70, pp.153-69.
Dickson, C., 1994. ‘Plant remains’. In B. B. Smith, Howe: four millennia of Orkney prehistory: 1978-82. Edinburgh: Society of Antiquaries of Scotland, pp.125-39.
Edwards, K, J., Whittington, G., Robinson, M., and Richter, D., 2005. Palaeoenvironments, the archaeological record and cereal pollen detection at Clickimin, Shetland, Scotland, Journal of Archaeological Science, 32, pp.1741-56.
Encyclopaedia Britannica, n.d. Sulphur [online]. Available at < https://www.britannica.com/science/sulfur > [Accessed 10 September 2021].
Farrell, M., 2015. Later prehistoric vegetation dynamics and Bronze Age agriculture at Hobbister, Orkney, Scotland, Vegetation History and Archaeobotany, 24(4), pp.467-86.
Fenton, A., 1978. The Northern Isles: Orkney and Shetland. 1st ed. Edinburgh: John Donald Publishers.
Fenton, A., 1997. The Northern Isles: Orkney and Shetland. 2nd ed. East Linton: Tuckwell Press.
Holden, T., and Boardman, S., 1998. ‘Crops’. In N. Sharples. Scalloway: A Broch, Late Iron Age Settlement and Medieval Cemetery in Shetland. Oxford: Oxbow, pp. 99-106.
Jack, P. M., forthcoming. Feeling the Peat: An investigation into an alternative metalworking fuel for the Scottish Iron Age. (Submitted March 2021)
MacDonald, D, A., 1962. A' dèanamh gual Gà idhealach nuair a bha gual gann. 37403. MacLean, D., Blacksmith and crofter in North Uist [online]. Available at < https://www.tobarandualchais.co.uk/track/37403?l=en > [Accessed 19 September 2020].
MacLeod, M., and Maclean, J., 1971. Smithy and hen-farm in Jura. 101105. MacDougall, C. Unknown (female), Blacksmith, farrier and hen-farmer in Jura [online]. Available at <https://www.tobarandualchais.co.uk/track/101105?l=en> [Accessed 19 September 2020].
Mahler, D. L., and Jouttijärvi, A., 2005. Experiments with peat charcoal and iron production in the Faeroe Islands. In A. Mortensen and S.V. Arge, eds. Viking and Norse in the North Atlantic: select papers from the fourteenth Viking Congress. Tórshavn: Foroya, pp.92-8.
Oaks, R., 2018. Making Charcoal and Biochar: A Comprehensive Guide. Wiltshire: The Crowdwood Press.
Pleiner, R., 2000. Iron in Archaeology: The European Bloomery Smelters. Praha: Archeologický ústav AV ČR.
SEPA, 2017. Peatland Survey. Guidance on Developments on Peatland. [pdf] Available at < https://www.gov.scot/binaries/content/documents/govscot/publications/advice-and-guidance/2018/12/peatland-survey-guidance/documents/peatland-survey-guidance-2017/peatland-survey-guidance-2017/govscot%3Adocument/Guidance%2Bon%2Bdevelopments%2Bon%2Bpeatland%2B-%2Bpeatland%2Bsurvey%2B-%2B2017.pdf > [Accessed 07 September 2022].
Small, A., 1964. Excavations at Underhoull, Unst, Shetland, Proceedings of the Society of Antiquaries of Scotland, 98 (1), pp.225-48.
Timpany, S., Mighall, T., Foster, I., Martinez Cortizas, A., Owen, O., Krus, A., and Kamerling, I., 2020. Later Prehistoric and Norse Communities in the Northern Isles: multi-proxy environmental investigations on Orkney, Environmental Archaeology, 27(2), pp.1-22.
Townend, S. D., 2005. The Development and Application of a Heideggerian Phenomenological Methodology for the Analysis of Human Engagement in Field-based Experimental Archaeology: a case study from the reconstruction of an Iron Age roundhouse in Wales. PhD. University College London. Available at: < https://discovery.ucl.ac.uk/id/eprint/1446621 > [Accessed 7th October 2021]
Tylecote, R. F., 1990. The Prehistory of Metallurgy in the British Isles. London: The Institute of Metals.