The content is published under a Creative Commons Attribution Non-Commercial 4.0 License.
Unreviewed Mixed Matters Article:
Broken Rocks, Fired Clay and Soured Milk – A Summer of Experiments with the Bamburgh Research Project at the Bradford Kaims Site
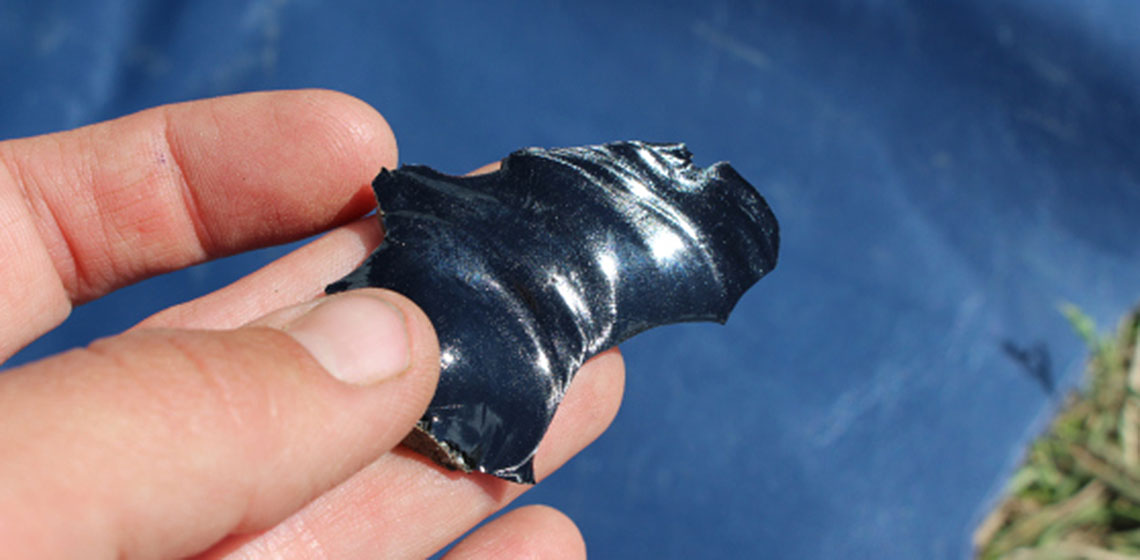
The Bamburgh Research Project operates an archaeological field school every summer in Northumberland, England. We have two sites: one located at seaside Bamburgh Castle and the other a few miles away inland at the Bradford Kaims. The Bradford Kaims is located on the edge of a wetland and has shown evidence for prehistoric seasonal human occupation. Features and artefacts found on site include burnt mounds, post holes, worked wood, and lithics/debitage (Gardner et al 2015). Over the summer of 2016, we conducted an Experimental Archaeology Programme at the Bradford Kaims in an attempt to better understand the processes involved behind the features and artefacts found at the site. We focussed on processes we could acquire materials for, which included flint knapping, prehistoric pottery, and prehistoric glue.
Knapping
The first experimental archaeology process attempted was knapping. Knapping is the process of lithic core reduction with the intention of producing a tool. Flint, obsidian, and quartz can all be used as cores to knap tools. First, the core is struck by a denser tool, known as a hard hammer. The impact creates a force which ripples through the stone, known as conchoidal fracturing. The location of the strike on the core is crucial to whether or not a flake is created. If struck on the edge of the platform, a flake will usually break off. Sometimes the pressure will continue through the stone, hit a naturally occurring impurity within the stone and break away which creates a blunt edge (Andrefsky 2005: 11-30).
Students, staff, and local volunteers learned the basics of knapping and attempted to create usable pieces of worked stone. We had two types of stone materials to use: flint and obsidian. Due to its harder nature, we began our experiments using flint and we learned how to properly hold the stone and how to strike. After everyone got the feel for the tools and how the process worked, we began using the obsidian which was easier to flake off, but very sharp. A benefit to using obsidian is that the ripples created from striking were easier to see, facilitating a better understanding for the mechanics behind knapping. We saved the usable flakes to test out later in the season during out woodworking project and we tried using the scrapers and awls on some leather hide, with some success!
Next, we tried pressure flaking which proved to require more finesse. This involves abrading the surface (crushing/sanding down the inconsistent edges to create a stable edge for sharpening) and then applying pressure directly onto the flake edge with a softhammer, pulling down with an antler tine to flake off tiny pieces. This process, though difficult, is necessary as it strengthens and sharpens the flake edge creating a blade. This technique was more difficult to grasp, but everyone was still able to attempt it and gain an appreciation for the skills required to manufacture stone tools. At the end of the day, we saved the flakes which we thought could be hafted and students were able to take a souvenir piece home with them.
Prehistoric Pottery
Our next experimental archaeology project was an effort to make a variety of pottery vessels using only raw clay sourced from our prehistoric site here at the Bradford Kaims Wetland Project. ”Prior to the Roman invasion, almost all native pottery in Britain was hand-made and open fired” either on the ground surface or in a pit (Gibson 1997:26). Prehistoric ceramics ”were made primarily for domestic use, as storage, cooking or serving containers, or to receive or accompany the bones or bodies of the recent dead” (Woodward 2008: 85-86). Since wheel-throwing and kiln firing produce finer ceramics, prehistoric pottery was comparatively rough and weak compared to the later Roman varieties, but it evidently served its various purposes well enough. Archaeological evidence suggests that the early production of pottery was non-specialised, and that it was being produced ”as and when needed, regardless of the time of year” (Gibson 1997:48).
We knew from previous seasons that the trenches and test pits often turn up natural clay deposits of varying colours and quality. Excavations here at the Kaims have also produced a few examples of possible Late Bronze Age or Early Iron Age potsherds. So, given the pottery record on site and the abundance of raw material, this summer’s experimental archaeology program seemed like a perfect opportunity to test out our prehistoric potting skills! Altogether the process of preparing the clay, forming the pots, and the subsequent firing turned out to be a messy, fun and educational experiment for all involved.
Upon examining the cooled pottery the next day I was pleased to confirm that none of the vessels had cracked or exploded during firing. Additionally, the pieces had fired, if not completely through, then most of the way through despite the shortened firing time. The fired pots are noticeably brittle and not completely water tight, but with a little more practice we could probably produce vessels that would be more serviceable. Since we accomplished our goal of using only raw materials from site and an open fire to create prehistory-inspired pottery—and we had fun doing it—we called this experiment a success!
Prehistoric Glue
Once we knew that woodworking and flint knapping were in our schedule, we thought we should see if we could combine the two products from these activities to make a tool. In order to do this, we decided to try making glue with resources that would have been available to the prehistoric people at the Bradford Kaims. An article by Lyn Wadley (2005) focusses on residue studies from lithics found in South Africa, and suggests that ochre was part of the adhesive and not simply decoration on the surface of the tool; when we saw red ochre coming out of the ground in Trench 6, we decided to include it in our recipe in order to take advantage of as many natural resources as possible.
Keywords
Country
- United Kingdom
Bibliography
ANDREFSKY, W. (2005). Lithics: Macroscopic Approaches to Analysis, Second Edition Cambridge University Press, pp 11-30.
GARDNER, T., GETHING, P.A., LALLY, T., BLACK, S. & RUTHEFORD (Brummet), R (2016)
http://bamburghresearchproject.co.uk/wp-content/uploads/2013/07/Bradfor… - last viewed 16/04/17.
GIBSON, A. and WOODS, A. (1997). Prehistoric Pottery for the Archaeologist. London. Leicester University Press, pp 26-53.
WADLEY, L. (2005). Putting ochre to the test: replication studies of adhesives that may have been used for hafting tools in the Middle Stone Age. Journal of Human Evolution 49: pp 587-601.
WOODWARD, A. (2008). Bronze Age pottery and settlements and in southern England. Bronze Age Review. The British Museum, Vol. 1, pp. 79-92
http://hubpages.com/art/woodworking-how-to-make-your-own-strong-wood-gl…; - last viewed 19/01/17.