The content is published under a Creative Commons Attribution Non-Commercial 4.0 License.
Reviewed Article:
Experiments with Lime Mortars containing Charcoal and Ashes
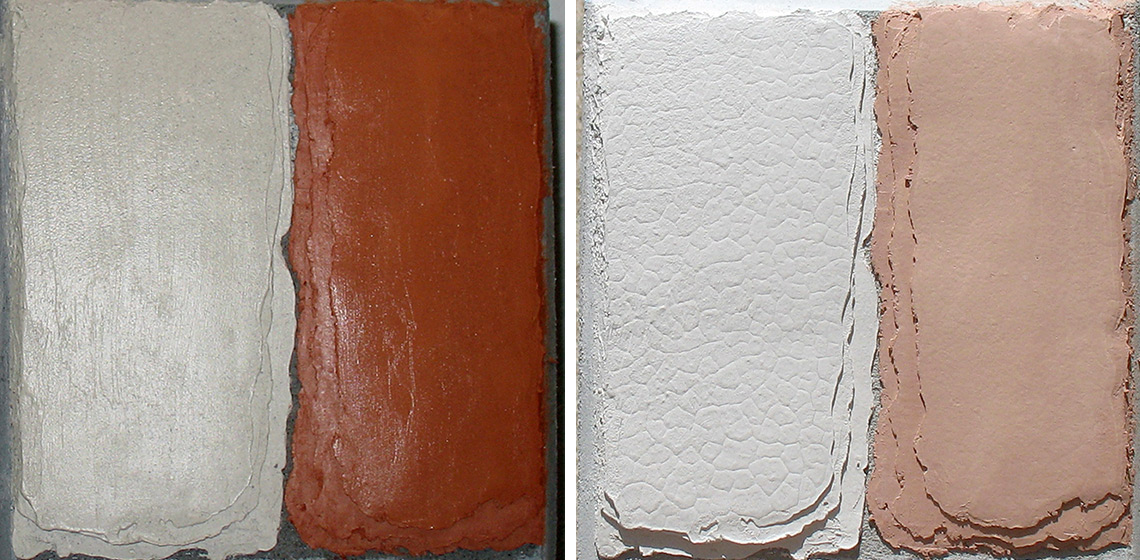
We encountered a number of cases in the published archaeological studies where ashes and charcoal were used as aggregates in ancient lime mixtures. These mixtures were tested in a small number of experiments, and this paper presents the results. Our tests confirmed that charcoal retains moisture and can be used to help mortars retain water. It does not, however, increase a mortar's ability to retain moisture to the same degree that crushed ceramic does. Charcoal should be an additive to a mortar and not its sole aggregate, as it is brittle and the mortar produced would be weak. Mixtures of ash with lime seem to work best when spread on a single layer. When the ash is a small part of a mortar, it does not affect its behaviour significantly. The addition of ash does not increase the ability of lime mortars to retain water. Powdered ceramics also limit the effect of ash on lime. The paper concludes with suggestions for future research into these materials and mixtures.
Introduction
While researching ancient lime mortar technology, we encountered a number of cases in published archaeological studies that refer to the use of ashes and charcoal as aggregates in mixtures. These mixtures were tested in a small number of experiments, and this paper presents the results.1
The purpose of these experiments was: 1. To understand the technology of mortars containing ashes and charcoal. Included here is the behaviour of these materials in mixtures. 2. To study the difference in the behaviour of these unusual mixtures in relation to normal lime mortars. 3. To study a specific variation of a form of technology.
It is hoped that the experiments presented in this paper will contribute to the understanding of lime mortar technology.
Materials under investigation
Charcoal
In ancient mortars, charcoal (presumably ground) appears either as an impurity from the burning of limestone to make plaster or as a pigment that was added to colour the mortar (Elsen, 2006, p.1419). Charcoal has been used in Greece as an additive in mortars during different periods. In mortars of the Hellenistic period, the charcoal used was round in shape and was usually less than 1% of the mixture (Stefanidou, Papayianni and Pachta, 2012, p.741). Kyriakou reports that the final mortar layer used for the floors of tricliniums was a mixture of lime, charcoal, ash, and sand, which was spread as a thick layer (Kyriakou, 1997, p.403). The most frequent use of charcoal in mortars in Greece was during the Ottoman period (Stefanidou, Papayianni and Pachta, 2012, p.747). Historically, charcoal has also been used in other applications. For example, in the frescoes of the 12th century in England there are cases where the top mortar contained crushed charcoal, but only in the areas of the composition that were meant to be painted blue (Howard, 1995, p.93). Charcoal is added to mortars to make them lighter in weight, to allow them to breathe and to influence their colour. For Stefanidou, Papayianni and Pachta, however, these properties cannot be supported because the amount of carbon in the mixtures is usually low (0.5-1%) (2012, p.747).
Ash
According to Forbes (1965, p.188), in ancient times, the potash that was used to make soap came from beech or seaweed ashes. Lye was made from the ashes of wood or other plants and was extracted with water. The material is a potassium carbonate solution (K2CO3) (Burnell, 1865, p.63; Kirby, 1977, p.37; Stodulski, Farrell and Newman, 1984, p.148; Hemelrijk, 1991, p.239; Sciuti, et al., 2001, p.139; Seymour 2003, p.94; Kirby, Spring and Higgitt, 2005, pp.71, 78-79; 2007, p.69).
An ash solution that is left to cure over lime plaster produces potassium hydroxide (KOH) or sodium hydroxide (NaOH) (Kirby, Spring and Higgitt, 2005, pp.78-79). Different types of ash produce different types of lye, depending on the plants burned. Ashes from the burning of plant materials give pozzolanic properties2 to mortars and can be added to lime to create hydraulic mortars (Hauptmann and Yalcin, 2000, pp.61, 66-67). However, a) they must be added in the correct proportion in relation to the other materials of the mixture, and b) water must be added to the mixture because ash absorbs the moisture of the lime (Burnell, 1865, p.63). According to Burnell (1865, p.63), wood ash must be washed before it can be used for a mortar. A floor mortar of 8700-7000 BC that was made of lime with ash particles from volcanic tuffs is preserved in Aşıklı Höyük in Anatolia (Hauptmann and Yalcin, 2000, pp.61, 66-67). Forbes (1965, p.243) reported that in Mesopotamia, craftsmen used a mortar made out of lime plaster and ashes, which was spread in 4 mm thick layers. In later periods, pieces of coarsely-ground brick were also added to the mixture.
Experiments
In all of the samples, we used lime plaster that is free from both magnesium and gypsum. We used lime plaster from a producer in Crete, Greece, that creates lime plaster by calcining a local dark marble. Before being used for the samples, the lime plaster was sieved, without dilution, with a thin net to remove any impurities.
The ash we used came from a household fireplace that had burnt pieces of olive and oak wood. Before using it in the mixtures, we sifted it with a very fine net to clean it. Sifting resulted in a thin, almost like powder substance. The charcoal came from the same fireplace as the ash. We tried to pick fully burned pieces of wood from the fireplace. These pieces were washed with water to remove the ash that was on them. After they were dried, they were crushed to different sizes.
All of the aggregate materials that were used in the mixtures were measured by volume using the same shovel. A masons spatula was used to remove excess material from each shovelful while measuring. To make each mixture, the aggregates were measured first, and then the lime was measured and added. Before mixing the different aggregates with the lime, we mixed them dry together to distribute them more evenly in the mortar. The sizes of the aggregates mentioned in this paper are based on the following categorisation:
Thick | Ø 5 mm – 1.1 cm |
Medium to thick | Ø 4-5 mm |
Medium | Ø 4 mm |
Thin to medium | Ø 1-3 mm |
Thin | Ø up to 0.5 to 0.75 mm |
The materials we used in the experiments were also used to make mortars in each of the studied time periods. We used trowels, paint brushes, and other equipment versions of which existed in antiquity. Painting brushes ( Winsor & Newton Cotman Series 111 round synthetic hair No 6, Art & Hobby 2600 round long synthetic hair No 8, and two Da Vinci Series ARTE VII 5408 round synthetic hair brushes (No 5 and 8)) were only used to paint the samples. All of the mixtures were spread and levelled with a simple triangle-shaped steel trowel. Lime washes were spread with a household painting brush with hog hair (Morris Pure Bristle 1,5 inch). The only material that did not exist was extruded polystyrene (XPS), an insulation material that was used as a base for the samples. Extruded polystyrene is lightweight, easy to cut and shape. It was used because it does not react with lime (for example, as cement does) and as a replacement for wood (that would be damaged by the wetting and the alkalinity of the mixtures). The surface of the polystyrene was scored to improve its mechanical cohesion with the lime mixtures. As a material, polystyrene does not absorb water, so the mixtures placed over it are essentially spread over a dry surface. In most cases, we used a mixture that acted as a base for those placed over it. Some of the samples do not have a base coat (21213 Demeter, 15513 Ash, 1914 Aineia Box).
All of the samples mentioned in this paper are presented in Table 1. The number and name of each sample refers to the date of its creation and the subject painted on it, respectively. The name ash was given to samples that were created specifically to study mixtures of ash and lime. Some of the samples presented here were painted in a fresco technique. By that we mean, that they were painted while the lime mortar was fresh (within 30 minutes from spreading or levelling the surface).
In the description of the samples, we differentiate between layers and doses. When we mention a layer, this means that it was produced by a single spreading of one lime mixture. When we mention doses, this means that a single mixture was spread at intervals. The application in doses allows the spreading of a thin mixture in a thicker layer than what it would normally withstand.
It must be pointed here that all the observations presented in this paper were made using observations (human senses) and not with specialised laboratory equipment. A more detailed analysis of such samples would be useful in the future to study the characteristics of these mixtures. All photographs were taken by the author of this article.
Samples
21213 Demeter
The first (base) layer of the sample was a mixture composed of a ratio of 1 lime : 1 thin river sand : 1/4 ash. A single layer of 3.5 mm thickness was placed on a polystyrene surface. The mortar was as easily mixed as a simple mixture of lime and thin sand. It was easily spread and levelled. We believe that the small amount of ash contributed to these properties. Three days later, the surface of the mixture was incised with a toothpick (See Figure 1). The surface appeared tight and lighter in colour but was relatively soft and cold to the touch. This indicated that the mortar was still wet on the inside. The layer retained its softness for a few more days, something which we attributed to the reaction of ash with the lime. Eight days after spreading the mixture, it was wetted with water, covered by a layer of lime emulsion (1 lime : 4 water) and was painted almost immediately. The colour it was painted with was a 1 : 1 mixture of ash and lime emulsion (1 lime : 1 water). The two materials were mixed by stirring with the brush (without grinding). The “paint” worked well on the first layers in which it was diluted with water. In the last layer, it was used undiluted, making the brushstrokes thicker and more embossed. The colour was a creamy yellow and became a matte yellowish grey when it dried. When the sample is viewed at an angle, the colour appears to be whiter in colour and to have a more satin texture than the surface. The ash we used in the paint was not sifted, and this resulted in the creation of lumps. When the sample dried, it had a glossy surface texture (See Figure 2). A notable difference to a normal mixture was that it felt softer to the touch. The mixture would have behaved differently if it contained more ash.
15513 Ash
In sample 15513 Ash we tried a mixture composed of 1 lime : 1.5 ash. It was spread on a single 4 mm-thick layer on a polystyrene surface. The mortar was very difficult to mix because the ash absorbed moisture from the lime. It took a lot of effort to break the lumps that were constantly created. After a while, the mortar began to appear dry. When it was finally mixed, it had a clay-like texture. Even after the prolonged mixing, the light grey mortar was uneven in its consistency, which made it very difficult to spread. A few minutes after levelling the surface, blisters started to appear at various points. These were punctured with a toothpick to prevent cracking in the mortar. After an extra 30 minutes, blisters were observed and were also punctured. When we checked the sample after 24 hours, we did not observe any new blisters.
When completely dried (the process takes 20 to 30 days depending on each case), the mixture had a lighter grey colour than when it was wet (See Figure 3). We also observed that the sample was very light in weight. The mortar had an appearance and texture closer to dried paper pulp than a mixture of lime. Its surface had a matte texture and was covered with cracks. Despite the cracks, the mortar did not detach from the polystyrene. The cracks do not follow or originate in the holes we had made with the toothpick. As such, we attribute them to the composition of the mortar. The ash reacted with the moisture of the lime, which caused the blisters and affected the texture of the mortar. We think a ratio of 1 lime : 1 ash would be more correct. We cannot exclude the possibility that the quantity of lime in the mixture should have been higher (for example 1.5 lime : 1 ash). The mortar would also probably behave better if it was spread as a thinner layer.
11613 Pluto Arm
The first layer of the sample was a mixture of 1 lime : 1/3 ash : 1/3 brick powder : 1 medium marble chips. A single layer, 5 mm thick, was spread on a polystyrene surface. The mortar was easily mixed, which we attributed to the small amount of ash. The fresh mixture had a dark orange colour. When it dried, it became pinkish-white in hue and a glossy texture. It had several stretch marks on its surface but no cracks. Before placing the next layer one month later, we wetted the surface with water. The mixture retained a lot of moisture, which was expected from the quantity of the brick powder it contained. When the quantity of ash in a mortar occurs in low quantities in relation to the other materials, it does not affect its behaviour significantly. The surface of the ash mixture was covered by a single 2 mm-thick layer of a mixture of 2 lime : 1 marble powder : 1 brick powder : 1/20 water (See Figure 4). This layer was painted in fresco, and it dried without problems. The pigment used to paint the sample was a soot-black (made by us) that was mixed with lime and with lime emulsion (1 lime : 1 water). When the sample dried, the colours had a matte texture and had adhered well to the surface.
14613-13913 Ash
The base layer of the sample was a mixture composed of 1 lime : 1.5 fine river sand : 0.25 ash : 0.5 oak charcoal crushed into thin sand-sized pieces. It was spread in one layer, 7.5 mm thick, on a polystyrene surface. It took a lot of effort to make the mortar because the materials did not seem to mix with each other. The mortar was also difficult to mix because it was lumpy. It was, however, easier to mix than the base mixture of sample 15513 Ash. The mixed mortar felt quite dry and had a texture similar to clay (See Figure 5). The dark grey mixture was easily spread because it was stiff. The next day we observed five blisters on the surface of the layer. They were punctured with a pin so as not to cause cracks. Charcoal absorbs and retains moisture, which helps the mortar stay moist. The ashes reacted with the moisture of the lime, a reaction that caused the blisters. No new blisters were discovered after 24 hours. The surface of the layer was tight, but touching it revealed that there was plenty of moisture on the inside. The mortar was still cold to the touch three days later, which indicated that it retained moisture within. The surface of the mortar had a satin gloss when it dried. Its colour was a shade of grey with a hue towards blue. The sand allowed the mixture to be spread as a thick layer, made it more stable, and more compact than that of sample 15513 Ash. The holes from the blisters reached down to the polystyrene and were 1 mm in diameter. The blisters did not lead to cracks or stretch marks. Before placing the next layers three months later, the surface of the base layer was scraped with fine sandpaper, wetted with water, and left for 5 minutes (See Figure 6). When we spread the next layers over it, we observed that this mixture could hold moisture. Charcoal as a material retains moisture, which helped the mixtures that followed to behave better.
The mortar that was placed on the left side of the surface (henceforth 2A) was a mixture of 1 lime : 0.5 ash. It was placed on the wet surface of the base layer in three doses that were spread 30 minutes apart from each other (See Figures 7 and 8). All of the layers were 1 mm thick. The mortar was relatively easy to mix. Its texture was similar to that of a mixture of 1 lime : 1 marble dust. When the last dose was placed, the mixture had a texture that was similar to soft butter. In all three doses, the mixture was easily spread. After 48 hours, we observed stretch marks across the surface of the doses but no cracks (See Figure 9). The surface was hard, but from a tactile perception, it appeared to have moisture within. When it dried, the mixture had a pale grey colour and appeared to adhere well to the surface of the base layer. Similar to sample 15513 Ash, it resembled dried paper pulp.
Each dose exhibited a different texture (See Figure 10). The first dose had a matte texture and exhibited very light stretch marks. The second dose had a matte to satin texture, slight stretch marks, and very shallow craquelure. The last dose had the same texture as the second dose and thin shallow stretch marks. The thin cracks, which existed only in the lower part of the first dose, followed the shape of the craquelure.3 The stretch marks that appeared in the previous dose were also at the same point. This means that the damage either originated in the second dose or continued from the first dose. It is likely that this particular mortar works best spread in one, or at most, two doses. We also believe that the amount of ash was very small. A ratio of 1 : 1 would probably produce a more solid mortar. Ash works well as a mortar but should be applied in thinner layers. If it had been placed in only two doses it would have probably worked better. It seems that the nature of the mixture does not allow it to be placed in thick layers.
The mixture that was spread on the right side of the base layer (henceforth 2B) was made of 1 lime : 0.5 ash : 0.5 brick powder. It was placed in three doses 30 minutes apart See (Figures 7 and 11). All of the doses were 1 mm thick. The mixture was smoother than that of 2A and was slightly dryer than a mixture of lime and thin sand. All of the doses were spread very easily. They remained supple and without any change in the texture of the mortar. When inspected after 48 hours, the surface was very cold, which indicated that there was moisture inside the mortar. When it dried, the first two doses had a matte texture, without cracks or stretch marks. In contrast, the last dose had a satin to glossy texture without cracks (See Figure 12). The surface looked smooth, but when viewed with light coming at an angle some stretch marks were visible. The dark orange colour of the fresh mixture took a lighter orange hue when it dried. Upon touch, the mortar appeared to be more solid than that of 2A. The mixture also appeared to be more compact and durable. It would have probably worked better if it had been spread in two instead of three doses. The mortar adhered well to the surface of the base layer. The ash : brick powder ratio appeared to be correct. Brick powder is a more solid material that seems to limit the effect of ash on lime. The placement of three doses of the same mortar at 30 minutes apart worked well. But we believe that they should have been more distant. When mortars were spread in doses, these did not necessarily have the same texture (See Figure 13). This relates to the fact that the mixture is left to rest for quite some time, The ingredients are mixed once, then the mortar is left undisturbed until the next dose. Letting it sit for a while allows it to settle , so each dose has a slightly different behaviour. The mixture of 2B did not appear to require boiled ashes, but we think that it would also help improve its behaviour and qualities. Based on findings from 2B we believe that the mixture of 2A would behave better if the ash was boiled. Boiled ash is a drier material that does not react with lime.
281113 Ash
The base layer of the sample was made of 1 lime : 1 thin river sand : 1 medium to thick quarry sand. It was spread in a single 7.5 mm-thick layer on a polystyrene surface. Before placing the next mortars 3 months later, the surface of the layer was scraped with fine sandpaper, wetted with water, and left for 15 minutes. The second mixture of the sample was composed of 1 lime : 1. 5 boiled ash (See Figure 14). It was placed in three doses, placed 30 minutes apart on the wet surface of the base layer. The first dose was 1 mm thick, while the second and the third were each 0.5 mm thick.
Before using the ash, four tablespoons of ash were boiled slowly in 300 ml of water to produce the boiled ash used in the mixture. Afterwards, we let it cool down and then removed most of the liquid, added clean water and stirred again (See Figure 15). When it settled, we removed the water and let the yellowish-grey ash dry. When it was dry, we observed that it was a harder material than plain ash and with a more yellowish hue (See Figure 16). The mortar produced with the boiled ash was a little tighter than that of sample 15513 Ash. It was also harder to handle, and it took a lot of effort to spread it. But when we levelled the surface of the first dose, the mixture had become a bit more pliable. The last two doses were spread and levelled more easily. After 48 hours, we observed very shallow stretch marks on all three doses (See Figure 17). These were more prominent in the second and third doses. The third dose also had developed cracks. A re-examination after a further 48 hours did not reveal new cracks. Those of the final dose had not expanded. The surface of all of the doses had a satin texture when the sample dried (See Figure 18). Based on the previous experiments, we believe that the texture is justified by the use of boiled ash. The first two doses had shallow cracks. The last dose also had cracks, the deepest of which were up to 0.5 mm deep. We cannot exclude the possibility that this mixture cannot support placement in many layers or that the ratio of its materials cannot support placement in layers that are thicker than 0.5 mm. Since boiled ash seems easier to use than plain ash, we could have used a ratio of 1 lime : 1 boiled ash.
30714 Lily
The base layer was composed of 1 lime : 1 thin river sand : 1 thick quarry sand : 1 medium quarry sand and was spread on one 9 mm thick layer on a polystyrene surface. Three months later it was covered by the next layer. Before spreading it, the surface was wetted with water and left for 10 minutes. The second layer of the sample (0.5 mm thick) was made of 1 lime : 1 thin marble : 1/10 powdered charcoal from oak wood. The charcoal was added to the mixture after the marble was mixed with the lime (See Figure 19). The resulting mortar was grey, with a slightly darker hue than a mixture of lime with thin river sand. It was left to rest for 10 minutes before spreading on the surface. After levelling, the layer was left for 15 minutes before being painted. The pigments (red ochre and a synthetic blue) were mixed with water by stirring without grinding. We did not observe anything different in the behaviour of the mixture when we were painting it. The surface texture was matte when the mortar dried, as the addition of charcoal made the mortar less glossy (See Figure 20). Cracks appeared at the bottom part of the surface. We believe that the surface layer is partly to blame for the cracks. It should have been levelled better. If it had been levelled better, the surface would be even, and the second layer would not “sink” in the crevices. The colour of the mortar was pale grey with a hue towards blue-grey. It was darker than a mixture of river sand. A very small amount of charcoal powder proved enough to colour a mortar. We did not observe any alteration of the colours that could be attributed to the charcoal of the mixture. Both colours dried a little darker, but the result was not bad aesthetically. The colour of the mortar can be used creatively, but one needs to know what the final shade of mortar will be, in order to take advantage of it in the choice of colours.
1914 Aineia Box
The single layer of the sample was a mixture of 1 lime : 2 charcoal from oak and olive wood (ground into pieces the size of thin and medium sand) : less than 1/10 water. A 3 mm thick layer was placed on a polystyrene surface (See Figure 21). The mortar looked dry, but it was very easy to mix. It was spread on the surface and left for 15 minutes before levelling it with a dry spatula. It was then left to set for 40 minutes. When that time passed, we observed a few blisters on the surface, which we punctured with a needle (See Figure 22). The layered mixture was too wet, for which the added water is not necessarily to blame. Charcoal retains moisture, which prevents the mixture from setting. That is why we decided to leave it for 2 hours before attempting to paint. This proved to be a good choice, as the surface accepted the colours without being disturbed by the brush. We did not observe new blisters on the surface during that time. The colours used to paint the sample were three synthetic blue pigments (cerulean, electric, and cement blue4 ) and Cennini’s white (made by us) that were mixed with water with and without grinding (For Cennini’s white see Cennini, n.d., p.34; Thompson, 1956, p.97; Gettens and Stout, 1966, p.104; Seymour, 2003, pp.449, 451). Two days after painting the surface of the layer, it had become grey (See Figure 23). In some areas,, it had glossy yellowish stains. These appeared on both the painted and the unpainted parts of the mortar. We also noticed that the blue colour had become very intense.
Both the mortar and the colours became matte when they dried. The mortar took on a medium tone of grey that had a blueish hue (See Figure 24). It had become quite light in weight. It was heavier than that of 15513 Ash, but lighter than a mixture of lime with thin sand. The holes from the pierced bubbles were still visible. We observed only one small crack in front of the date of the sample (See Figure 25). The mortar generally worked well. The proportion of lime and charcoal also appeared to be correct. We believe, however, that charcoal should not be the only aggregate in the mixture. It would be more appropriate and more durable if the mixture contained some sand. A mixture such as that of the base mixture of sample 14613-13913 Ash is more appropriate because the dominant aggregate is sand, and charcoal is only an additive in a small amount.
All the colours behaved well and had adhered well to the surface. The intensity of the white colour was enhanced by the contrast with the colour of the mortar. The glossy stains in the centre of the sample remained yellowish. Those that were on the unpainted surface of the mortar were easily visible, with light coming from the side. The stains in the parts painted with the blue colours did not appear as intense. When viewing the sample with light at an angle, we saw that some dots and stains were glossier than the surface. We believe that these stains in the mortar were due to some impurity that was present in the charcoal. It is possible that some of the charcoal we crushed was not completely burnt. Charcoal can be used to help the mortar retain water. It is, however, more fragile than crushed ceramic, and the resulting mortar is weak. The addition of water, which makes the lime weaker (Dionysius of Fourna, 173?, p.12; Nordmark, 1947, p.17), also contributed to the weakness of the sample. The charcoal mixture would work better if it was spread over a base layer instead of directly on the polystyrene. Spread on a base layer, this mortar would have set faster, and it would not need the addition of water when mixing.
Sample | Base coat ratio of materials | Base coat date and method of placement | Base coat dimensions | Top coat ratio of materials | Top coat date and method of placement | Top coat dimensions |
21213 Demeter | 1 lime : 1 thin sand : 1/4 ash | 13/2/13, 1 layer placed on a polystyrene surface | 17.6 cm × 12.8 cm × 3.5 mm | Lime emulsion (1 lime : 4 water) | 21/2/13, 1 layer placed over the wetted base coat | 16 cm × 12.8 cm |
15513 Ash | 1 lime : 1.5 ash | 15/5/13. 1 layer placed on a polystyrene surface | 19.5 cm × 12 cm × 4 mm | |||
11613 Pluto Arm | 1 lime : 1/3 ash : 1/3 brick powder : 1 medium marble chips | 10/5/13,1 layer placed on a polystyrene surface | 14.3 cm × 22.5 cm × 5 mm | 2 lime : 1 marble powder : 1 brick powder : 1/20 water | 11/6/13.1 layer placed over the wetted base coat | 13 cm × 20 cm × 2 mm |
14613-13913 Ash | 1 lime : 1,5 fine river sand : 0.25 ash : 0.25 charcoal (thin sand size) | 14/6/13,1 layer placed on a polystyrene surface | 18.7 cm × 17.1 cm × 7.5 mm (top surface 18 x 15.7 cm) | 2A: 1 lime : 0.5 ash | 13/9/13, spread in 3 doses, 30 minutes apart, over the wetted base coat | 1st dose 14.5 cm × 8 cm × 1 mm, 2nd dose 13.9 cm × 7.4 cm × 1 mm, 3rd dose 13.5 cm × 7 cm × 1 mm. |
2B: 1 lime : 0.5 ash : 0.5 brick powder | 13/9/13, spread in 3 doses, 30 minutes apart, over the wetted base coat | 1st dose 14.5 cm × 7.5 cm × 1 mm, 2nd dose 14 cm × 6.8 cm × 1 mm, 3rd dose 13.5 cm × 6 cm × 1 mm | ||||
281113 Ash | 1 lime : 1 thin river sand : 1 medium to thick sand | 20/7/13, 1 layer placed on a polystyrene surface | 10.5 cm × 19.2 cm × 7.5 mm (top surface 10 × 18.5 cm) | 1 lime : 1.5 boiled ash | 28/11/13, spread in 3 doses 30 minutes apart, over the wetted base coat | 1st dose 9.5 cm × 16.5 cm × 1 mm, 2nd dose 8 cm × 12.2 cm × 0.5 mm, 3rd dose 6.7 cm × 9.3 cm × 0.5 mm |
1914 Aineia Box | 1 lime : 2 charcoal (thin and medium sand-sized pieces) : less than 1/10 water | 1/9/14, 1 layer placed on a polystyrene surface | 16.8 cm × 11 cm × 3 mm (top surface 16.1 × 10.8 cm) |
Table 1. All of the samples mentioned in this paper. The number and name of each sample refers to the date of its creation and the subject painted on it, respectively.
Experimental findings and future applications
Charcoal
Charcoal powder is very strong as a pigment and can colour a mortar even when it is used in a small amount. The extent that this occurs depends on the amount of charcoal in relation to the composition of the mortar that is coloured. This is well-known in painting. Pigments such as vine black and carbon black are all forms of charcoal powder and were confirmed in relation to mortars. From our experiments, we deduced that charcoal as an aggregate makes the mortar lighter in weight and should be used in small quantities. The shade of the mortar is most affected when the charcoal is crushed into very small pieces and especially if it is ground into powder. A mixture containing small pieces of powdered charcoal dries grey with a light blue hue. Its colour is a darker grey than that of a mixture of lime plaster and thin river sand. A painter that is experienced with the change of the hue in mortars can take advantage of the colour of the mortar creatively.
If used, charcoal should be an additive to a mortar and not its sole aggregate, as it is brittle, and the mortar produced would be weak. A mixture such as that used in the base layer of sample 14613-13913 Ash is more appropriate because the dominant aggregate is sand, and charcoal is only a small part of the mixture. Our tests confirmed that charcoal retains moisture and, similarly to crushed ceramic, can be used to help mortars retain water. However, it does not increase a mortar's ability to retain moisture to the same degree that crushed ceramic does. The charcoal that is used in a mortar must be clean and well-burned because any impurities it contains will pass into the mortar. It is also expected that stains like those of sample 1914 Aineia Box will invite microorganisms in the future.
Ash
Based on the above experiments, in mixtures that are composed only of lime with ash the correct material ratio appears to be 1 lime : 1 ash, with the best layer thickness being 1 mm. Such mixtures should be applied in thin layers and in very few doses, as they cannot support placement in thick layers. A mixture that only contains ash, plain or boiled, cannot have a ratio of materials that is higher than 1 : 1. Similarly, mixtures with boiled ash cannot support placement in many layers or layers thicker than 0.5-1 mm.
It was observed in mixtures that contained unwashed ash that it reacted with the moisture of the lime plaster. This affected the texture of the mortar and, in some cases, caused blisters. In the samples that had mixtures of ash with lime, we observed that ash absorbed moisture from the lime. The mixture became lumpy, and after a while, it became dry. When the layers dried, they displayed a texture and a feel to the touch that was closer to dried paper pulp than a mixture of lime. Boiled ash is a harder material than plain ash and has a more yellowish hue. It is easier to handle because it does not seem to react with lime.
Mixtures of ash with lime appeared to work best when spread on a single layer. When the ash is a small part of a mortar, it does not affect its behaviour significantly. The addition of ash does not increase the ability of lime mortars to retain water. Powdered ceramics also limit the effect of ash on lime.
Suggestions for future research
This paper intended to act as a stimulus for future research into unusual ancient lime mortars. It is a feasibility study of a form of ancient technology. These experiments should be repeated. Future studies need to be more extensive and include different parameters and materials. These can include:
a) Using different types of lime. Such as lime that is made locally in the areas that belonged to Mesopotamia, aged lime, lime from calcining materials such as seashells or sandstone, or hot mortar-type techniques.
b) Mixtures made with different types of ash, for example, from burning seaweed and other plants.
c) Ideally, these trials should be made on surfaces that are like those of the ancient mortars or at least on natural surfaces, such as slabs of limestone. These samples will need to be left outside to study their resistance to environmental weathering. That will allow a better examination of the behaviour of these mortars in real-life conditions. There also needs to be an analysis of the mechanical and chemical properties of the mixtures using specialized equipment.
- 1The experiments, samples and research findings presented here are described and illustrated in more detail in Vlavogilakis, 2020. They are part of a PhD research that was conducted at the Department of Mediterranean Studies, University of the Aegean, Rhodes, under the supervision of Professor M.I. Stefanakis.
- 2Pozzolanas are natural and artificial aggregate materials that are added to mortars to affect their behaviour and properties. They create mortars that dry slowly and become stronger and with a greater compressive strength than mixtures that only contain lime and sand. (Vitruvius, De architectura, 2.6.1; Gettens and Stout, 1966, p.255; Stefanidou and Papayianni, 2005, p.915, table 1). The addition of pozzolanas creates hydraulic mortars, meaning they can harden under water and become water resistant. That is why these mixtures have been used for constructions that are exposed to moisture both in antiquity (by the Greeks, Etruscans, and Romans), and in later periods up to the present. (Vitruvius, De architectura, 2.6.1; Nordmark, 1947, pp.13, 15-17, 35; Elsen, 2006, p.1419; Papayanni, 2006, p.686; Connor, 2009, pp.91-92; Papayianni, Stefanidou and Christodoulou, 2010; Salavessa, Fernandes and Duarte, 2012, p.438; Vlavogilakis, 2020, p.240-254). Natural pozzolanas are different forms of volcanic ash deposits such as pumice, scoria and tuff. Artificial pozzolans are crushed ceramics (roof tiles, bricks, firebricks, tiles) and baked clays (Burnell, 1865, p.59; Gettens and Stout, 1966, pp.254-255; Ling, 1991, p.xii; Elsen, 2006, p.1419; Michoinová and Rovnaníková, 2008, p.26; Torgal, Gomes and Said, 2008; Connor, 2009, pp.73, 91).
- 3Craquelure is a pattern of cracks that develops on the surface of materials (paintings, ceramics, etc.). The term is usually used for panel paintings, but these crack formations can also appear in wall paintings due to various factors affecting the mortar. The cracks in craquelure formations can be very thin and shallow or reach down to the substrate (Bucklow, 1997; Brysbaert, 2008, p.117; Vlavogilakis, 2020, pp.319-321).
- 4The cerulean blue is Sennelier Cerulean Blue pigment SEP145305. Both Electric and Cement Blue pigments were bought in the past from Abio and are now discontinued.
Country
- Greece
Bibliography
Brysbaert, A., 2008. The power of technology in the Bronze Age eastern Mediterranean: The case of the painted plaster. Monographs in Mediterranean Archaeology, 12. London: Equinox.
Bucklow, S., 1997. The description of craquelure patterns. Studies in Conservation, 42(3), pp.129-140.
Burnell, G.R., 1865. Rudimentary treatise on limes, cements, mortars, concretes, mastics, plastering, etc.: Fifth edition, with appendices. London: Virtue Brothers & Co.
Cennini, C., n.d. The craftsman's handbook. The Italian "Il Libro dell' Arte". Translated by D.V. Thompson, Jr., 1933. New York: Dover Publications, Inc. and Yale University Press.
Connor, J.A., 2009. The Last Judgement: Michelangelo and the death of the Renaissance. New York: Palgrave Macmillan.
Dionysius of Fourna, 173?. The painter's manual of Dionysius of Fourna. Translated from Greek by P. Hetherington, 1989. London: Sagittarius Press.
Elsen, J., 2006. Microscopy of historic mortars—a review. Cement and Concrete Research, 36(8), pp.1416-1424.
Forbes, R.J., 1965. Studies in ancient technology III. 2nd ed. Leiden: E.J. Brill.
Gettens, R.J. and Stout, G.L., 1966. Painting materials: A short encyclopedia. New York: Dover Publications.
Hauptmann, A., Yalcin, Ü., 2000. Lime plaster, cement and the first pozzolanic reaction. Paléorient, 26(2), pp.61-68.
Hemelrijk, J.M., 1991. A closer look at the potter. In: T. Rasmussen and N. Spivey, eds. Looking at Greek vases. Cambridge: Cambridge University Press. pp.232-256.
Howard, H.C., 1995. Techniques of the Romanesque and Gothic wall paintings in the Holy Sepulchre Chapel, Winchester Cathedral. In: A. Wallert, E. Hermens and M. Peek, eds. Historical painting techniques, materials, and studio practice: preprints of a symposium held at the University of Leiden, the Netherlands, 26-29 June 1995. Marina Del Rey, CA: Getty Conservation Institute. pp.91-104.
Kirby, J., 1977. A spectrophotometric method for the identification of lake pigment dyestuffs. National Gallery Technical Bulletin, 1, pp.35-46.
Kirby, J., Spring, M. and Higgitt, C., 2005. The technology of red lake pigment manufacture: Study of the dyestuff substrate. National Gallery Technical Bulletin, 26, pp.71-87.
Kirby, J., Spring, M. and Higgitt, C., 2007. The technology of eighteenth- and nineteenth-Century red lake pigments. National Gallery Technical Bulletin, 28, pp.69-87.
Kyriakou, V.Th., 1997. Materials and methods for the water-protection of structures during antiquity. In: Ancient Greek Technology: Proceedings, 1st International Conference, Thessaloniki September 1997. Athens: ETVA Cultural Technical Institute; Thessaloniki: Techniko Mouseio Thessalonikis. pp.401-409. [Υλικά και μέθοδοι υγρό-προστασίας των κατασκευών κατά την αρχαιότητα. Αρχαία ελληνική τεχνολογία, 1ο διεθνές συνέδριο, Θεσσαλονίκη, 4 έως 7 Σεπτεμβρίου 1997, πρακτικά, Πολιτιστικό Τεχνολογικό Ίδρυμα ΕΤΒΑ, Αθήνα: Εταιρεία Μελέτης Αρχαίας Ελληνικής Τεχνολογίας -Τεχνικό Μουσείο Θεσσαλονίκης, σ. 401-409.]
Ling, R., 1991. Roman painting. Cambridge: Cambridge University Press.
Michoinová, D. and Rovnaníková, P., 2008. High-calcium lime mortar: The effects of traditional preparation and curing. APT Bulletin, 39(4), pp.23-29.
Nordmark, O., 1947. Fresco painting: Modern methods and techniques for painting in fresco and secco. New York: American Artists Group, Inc.
Papayanni, I., 2006. The longevity of old mortars. Applied Physics A: Materials Science & Processing, 83(4), pp.685-688.
Papayianni, I., Stefanidou, M. and Christodoulou, S., 2010. Influence of sand fines on the mechanical and physical properties of lime-based renders and plasters. In: J. Válek, C. Groot and J.J. Hughes, eds. 2nd Conference on Historic Mortars—HMC2010 and RILEM TC 203-RHM Final Workshop. Prague: RILEM. pp. 1135-1144.
Salavessa, E., Fernandes, L. and Duarte, A.M., 2012. Eco-plasters revive the plasterwork techniques of the past. In: ICOMOS 17th General Assembly Scientific Symposium proceedings: Part II, Session 3. 27 November-2 December 2011, Paris. pp.438-453. Available at: ICOMOS Open Archive: Eprints on Cultural Heritage < https://openarchive.icomos.org/id/eprint/1183/1/II-3-Article8_Salavessa… > [Accessed 12 November 2018].
Sciuti, S., Fronterotta, G., Vendittelli, M., Longoni, A. and Fiorini, C., 2001. A non-destructive analytical study of a recently discovered Roman wall painting. Studies in Conservation, 46(2), pp.132-140.
Seymour, P., 2003. The artist's handbook: A complete professional guide to materials and techniques. London: Arcturus Publishing.
Stefanidou, M. and Papayianni, I., 2005. The role of aggregates on the structure and properties of lime mortars. Cement and Concrete Composites, 27(9-10), pp.914-919.
Stefanidou, M., Papayianni, I. and Pachta, V., 2012. Evaluation of inclusions in mortars of different historical periods from Greek monuments. Archaeometry, 54(4), pp.737-751.
Stodulski, L., Farrell, E. and Newman, R., 1984. Identification of ancient Persian pigments from Persepolis and Pasargadae. Studies in Conservation, 29(3), pp.143-154.
Thompson, D.V., 1936. The materials and techniques of Medieval painting: with a foreword by Bernard Berenson. Reprint 1956. New York: Dover Publications.
Torgal, F. Pacheco, Gomes, J.P. Castro and Jalali, S., 2008. Some considerations about the durability of historic mortars. In: Laboratório Nacional de Engenharia Civil (LNEC), HMC08 Historical Mortars Conference: Characterization, diagnosis, conservation, repair and compatibility. Lisboa, Portugal, 24-26 September 2008. [CD-ROM] [s.l]: LNEC.
Vitruvius. The ten books on architecture. Translated by M.H. Morgan. Cambridge: Harvard University Press.
Vlavogilakis, A., 2020. Experimental archaeology and ancient Greek monumental painting. Fresco techniques and the case of the tomb of Persephone in the Great Tumulus of Vergina. PhD. University of the Aegean, Department of Mediterranean Studies, School of Humanities, Rhodes. [Πειραματική αρχαιολογία και αρχαία Ελληνική μνημειακή ζωγραφική. Τεχνικές νωπογραφίας και η περίπτωση του τάφου της Περσεφόνης στη Μεγάλη Τούμπα της Βεργίνας.]