The content is published under a Creative Commons Attribution Non-Commercial 4.0 License.
Reviewed Article:
“Cuts Stones of all Sorts, In the Best Manner…”: Experiments in 18th Century lapidary work in America
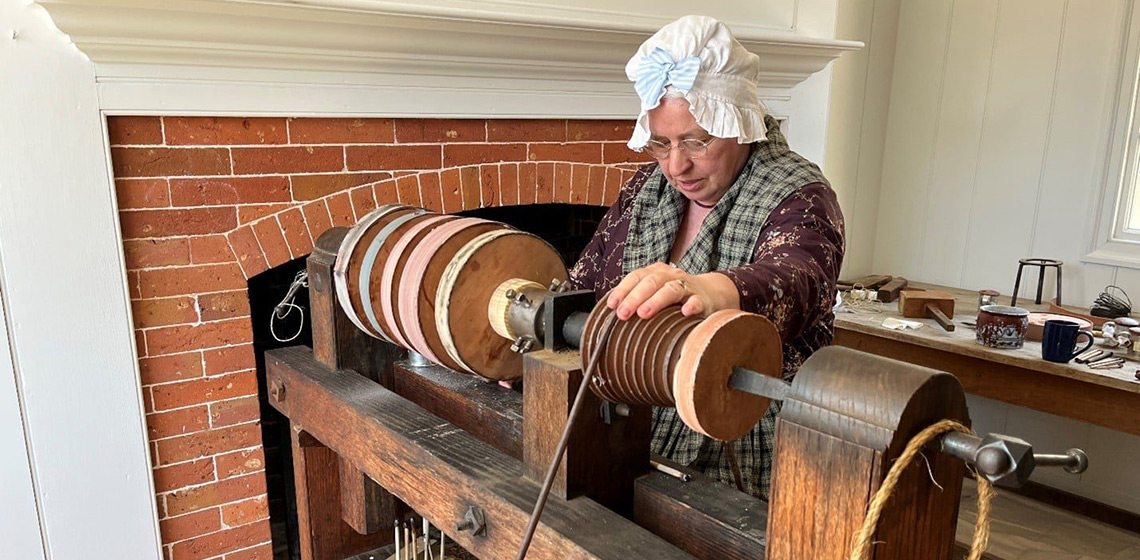
Unusual or rare gems have been valued for as long as there have been humans to appreciate them. The making of beads and ornaments provides some of the earliest examples of the manipulation of materials solely for aesthetic reasons. Throughout history, we have refined the processes and constructed dedicated machinery to further enhance the desirable qualities of certain stones. The gems themselves acquire legends and stories that enhance their value both as objects of beauty and wonder. Despite this rich history, few practical studies have been done on the history of gem cutting. Contemporary accounts have been written about the materials and equipment used for ancient and historical lapidary work, but few people working in experimental archaeology have undertaken to perform a program of experiments to undertake comparative analyses of lapidary work. The experiments carried out here explore the equipment used in the 18th Century as well as the various materials used for grinding gems and polishing them. And as in all field-based experimental archaeology, there is a strong experiential component.
This project was funded as a fellowship by Colonial Williamsburg in conjunction with EXARC. The author wishes to thank the staff of Colonial Williamsburg who support the exploration of craft industries and the recreation of lifeways during the 18th Century in Colonial America, and to EXARC for its overall support of experimental archaeology and for the promotion of this project.
Introduction
Colonial Williamsburg is unique among open-air museums. It encompasses 70 hectares (173 acres), where there are no barriers, except for motorised vehicles. Visitors can walk along the streets and visit shops, although an admission ticket is needed to enter workshops and interpretive centres. People working at Colonial Williamsburg are dressed in period costumes and are well versed in both history, the crafts they demonstrate, and in explaining them to the public. Colonial Williamsburg is an ideal environment for the exploration of 18th Century craft, history, and lifeways.
The city itself was founded in 1699 and became the capitol of the Virginia Colony. When the capitol moved to Richmond in 1780, Williamsburg’s development stalled, but continued with an economy supported by the presence of William and Mary College. As a result, many of its original buildings were preserved rather than having been torn down for newer developments. In 1926 the Reverend Doctor W.A.R. Goodwin approached John D. Rockefeller, Jr about preserving the remaining 18th Century buildings in the central part of the town. This led to the preservation of the entire historic site, and eventually to the reconstruction of buildings that had been destroyed, using archaeological and historical data (Williamsburg, VA 2022). Archaeological excavations continue, and the public is invited to see the ongoing work. The public is made aware of how the excavations contribute to greater knowledge of life in 18th Century Williamsburg, and how that knowledge has been used to recreate many of the buildings there.
Background and Political History of Lapidary in the American Colonies
By the 1700’s the American colonies were for the most part self-sufficient, however, they were dependent on imports for many luxury goods and staples that either could not be produced locally or were controlled by the British government through the Navigation Acts, the practice of mercantilism, and various treaties and taxes (Sawers, 1992). Merchants in the American colonies could import goods from Britain, but not from any other nation. All goods not originating in Great Britain had to be imported to Britain before they could be exported to the colonies. This meant that goods coming to the colonies were often doubly taxed, since the tax would be paid first upon import to Britain, and then again when exported to the colonies.
In 1642 King George II released a proclamation that allowed for the free import and export of “diamonds, pearls, rubies, emeralds, and all other jewels and precious stones”. The intent was to increase trade in gems, and especially to create an advantage for those who cut and polished gems in Britain. This meant that both rough and polished stones could be imported and exported without duty fees. This would be a boon to the trade for British gem cutters and later for jewellers in the colonies (George II, 1732).
The Stamp Act of 1765 was the first direct tax imposed on the American colonies by Great Britain and ratified by the British parliament under King George III. In short, every legal document and every piece of printed paper, including newspapers, that were produced in the American colonies had to have a stamp affixed that had to be paid exclusively in British currency. The proceeds from the tax were needed to pay for Britain’s war with France (1756–1763) and to support British troops stationed in the colonies. The Act triggered protests and a boycott of British goods. The Act was repealed the following year because of the pressure put upon the government by British merchants who relied on trade with the colonies. However, Parliament soon passed the Declaratory Act, which stated that the government had the right to tax the colonies as it saw fit (Bombay 2021). In a column in the Virginia Gazette dated from February 1769 a jeweller in Birmingham tells how several of his journeymen arrived in New York and now were requesting
“…many thousands of mocoa1 , paste, pebble, and crystal stones” and goes on to describe an economic decline in all areas of manufacture there due to the “stamp and other acts”
(Virginia Gazette, 1769).
Despite the difficulties, silversmithing and jewellery-making thrived in the colonies.
Personal Histories: Some of the Jewellers and Lapidarists in Colonial America
The primary source of information about lapidaries and jewellers is from contemporary newspaper advertisements and articles. Local and regional newspapers are also a source of information about the rise and fall in the popularity of certain styles and gemstones. In addition, the lives, and fortunes of jewellers and lapidarists can be followed by reading advertisements. While lapidary was not a common profession in the colonies, a jeweller could place an advertisement for someone working in that profession and reasonably expect a response (Bateman, 1774). Further research in archives could reveal more lapidaries, or jewellers who also cut stones.
In Colonial America, most jewellers did not rely solely on the sale of jewellery for their trade. Shop inventories included gold or silver snuff boxes decorated with mother of pearl, watches and clocks, buttons that frequently included stones or enamelling, ladies’ fans, keys, and seals, in addition to repairing jewellery, silverwork, and clocks.
James Craig was a well-known jeweller in Williamsburg. He arrived from London in 1742, and ten years later his advertisements in the Virginia Gazette include mentions of diamonds and amethysts, gems imported from Venice, and handling silverplate from estate sales. In 1765 he moved his shop from Francis Street to the east end of Duke of Gloucester Street, the commercial district of the main street of Williamsburg. The shop was later renamed The Golden Ball. In 1772 he was prosperous enough to take on an apprentice from Great Britain, who made and repaired watches and clocks. Later his advertisement listed pocket and pen knives, neat affordable jewellery, fine cutlery, pinchbeck buckles, scissors, and spectacles imported from London. In 1775 he advertised mourning rings and miniatures set in gold and silver. These were pieces of jewellery that were presented to significant mourners at funerals, often with the deceased’s name engraved or enamelled. Special pieces of mourning jewellery were sometimes set with tiny coffins carved from jet or small carved skulls. Locks of hair were encased below lenses of quartz or glass and set into pendants (Nehama and Bentley, 2012). James Craig’s combined shop and house has been reconstructed in Colonial Williamsburg with resident jewellers who work there and demonstrate the craft to visitors.
William Bateman was a lapidarist from London who also engraved stone seals. He was the third son of Hester Bateman, a famous silversmith of the time. He set up a shop in New York where he cut gems and seals, as well as engraving on stone, steel, silver, and copper (See Figure 1). A year later he left New York for another place in the colonies. Apparently, he indentured himself to Charles Oliver Bruff, and in 1775 a reward of eight dollars was offered for Bateman’s return. This is compared to rewards of three dollars that were often offered as rewards for most indentured servants. Bruff himself did lapidary work and advertised an extensive list of characters, both historical and mythical that he could engrave on seals. He also noted that he could “plait hair in the neatest manner” and could work hair into various designs such as birds, figures, and cyphers (monograms) (Bruff, 1775) These would have been set into mourning jewellery, or sentimental jewellery that would be given to a loved one.
Jewellery was also a means of personal identification and convertible wealth. Since most people could only afford a few pieces of jewellery they could be identified by the pieces of jewellery they wore. Escaped slaves, prisoners, and indentured servants were often identified in newspaper advertisements by their clothing, since many would have only one set of clothes, and any jewellery they might have (Heath, 1999). Jewellery could be both a way to identify a person while they were wearing it, but also if they were selling it.
Popular Gems in the American Colonies
In 1763 Edmund Milne of Pennsylvania advertised mocoa bracelets set round with garnets, pastes, Brazilian topazes, garnet and crystal earrings, coral necklaces, blue turkey (turquoise) bead necklaces, and carnelian seals (Ormsbee, 2009). Overall, a wide variety of stones were imported to the colonies for use in jewellery or to be cut for lapidary work.
Faking Stones
Before modern spectroscopy, gems were usually classified by colour and hardness. Thus, clear red stones were identified as either as a ruby or a garnet. Spinels are brilliantly coloured stones, and the red ones are often identified as rubies. While their specific gravities and refractive indexes are nearly identical, they are not as hard as a ruby (Sinkankas, 1962). The lapidarist would know the difference between a citrine (a yellow variety of quartz) and a topaz because they have different crystalline structures, and a topaz is much harder than a citrine. However, once a stone was cut, it would be difficult for the jeweller or the customer to tell the difference. The jeweller might notice that some stones were comparatively lighter or chipped more easily, but still might not be able to differentiate between an individual topaz and a citrine unless the jeweller had experience with handling both stones.
Nicols, in his book A Cabinet of Jewels (1652) describes various ways in which jewels can be counterfeited or enhanced with foils, dyes, and layering quartz with slices of more valuable stones. These stones, called doublets might have an amethyst adhered to a base of quartz, or even a sandwich with a thin piece of amethyst between a crown and base of quartz (triplets), making the finished gemstone appear to be more valuable than it is (Holtzapffel, 1894, p. 621). This practice is frequently used today with opals, where a quartz crown is used to protect the more delicate opal. However, there are also cases where a darker stone is glued beneath a thin slice of opal to make it appear to be a black opal, a more expensive stone. A composite stone would not deceive a jeweller, but once set would be difficult for a customer to discern.
Paste, or glass that was cut to resemble a gem was popular, but it was usually identified as such rather than being sold as a more valuable gem. While paste could be coloured to match various gems, the material is soft and brittle. It could easily be scratched or chipped, so it was often a practice to cut them as smaller stones where damage would not be as apparent.
A stone that is still popularly known as black onyx, is an agate that has been treated to turn it black. To do this, pieces of stone were heated in water mixed with either sugar or molasses and placed under pressure. Another treatment used sulphuric acid instead of the sugar solution (Holtzapffel, 1894, p.9). Similar treatments are used to produce blue agates (dyed with manganese oxide), green (copper oxide), or red (iron oxide). The colour of carnelian can be enhanced and deepened by putting the stone in an iron pot and slowly bringing it to a red heat. Stones could also be soaked in oil for two to three hours and then heated to darken the colour (Holtzapffel, 1894, p.619).
On the Nature of Lapidary Work
A note about nomenclature: When a lapidarist talks about cutting stones, it is the entire process that is being referred to. Rather than specifically slicing gem material with a saw, cutting gems includes the grinding, sanding, and polishing processes.
The hardness of stones is measured on the Mohs scale of hardness. The range begins with talc at 1 and finishes with diamond at 10. Simple tools can be used to scratch a stone to determine hardness. For example, a stone that could be scratched with a copper coin is 3.5 on the scale, while a steel knife is 5.5. Quartz is a 7, while topaz is an 8 on the scale. Citrine, which is a yellow form of quartz, can be differentiated from topaz since a piece of topaz will easily scratch a citrine, but a citrine will not be able to scratch a topaz. Rubies and Sapphires are rated at 9 on the scale and can be used to determine whether a softer stone, such as a spinel or a garnet has been used as a substitute.
Cleavage is also an important aspect of gem cutting. When a stone has a strong cleavage, it will break along the lines of the crystal structure. A sharp blow with a chisel will shear off a section of a solid stone, leaving a flat plane. Gems with an octagonal structure such as fluorite and diamonds can be easily cleaved into neat and precise double-pointed crystals with four facets each on the top and bottom. Cleavage leaves a smooth surface that often doesn’t require polishing and is a distinct advantage when creating a piece of jewellery with multiple small stones such as garnets. Other stones, however, have weak cleavages. Quartzes and cryptocrystalline quartzes such as flint, agates, and jaspers have a conchoidal fracture that is rounded and resembles a shallow clamshell shape. A shape that is familiar to anyone who has knapped flint.
Every stone is different, and it is up to the lapidary to be able to examine the stone to determine the best way to cut it with minimal loss of material. Subsurface flaws occur and so the lapidary must decide whether to continue cutting until the flaw is ground away, or if it is not worth the time and energy to continue. Sometimes the stone can be reshaped to eliminate a flaw, such as cutting the sides flatter to make an oval rather than the originally intended round stone.
The Difference between Faceting and Cutting Cabochons
Cabochons can be rounded or flat and in any shape. They usually have a flat back. Facetted stones are usually clear stones that have been cut with several flat sides. These sides are cut at angles that will maximise the reflected light, causing it to bounce and reflect off the interior facets of the stone. The interplay of the refraction can be seen through the table facet, the large flat facet on the top of the stone.
Cutting Stones
To cut gems, the stones need to be adhered to a short stick that will enable the gem cutter to hold it more easily. The adherent is called dop wax, a substance like sealing wax that is melted and then picked up on the dop stick and pushed onto the back of the stone, which has also been heated. The same technique is used by modern lapidaries. In the spirit of experimentation, dop wax was made rather than bought. A mixture of flake shellac with small amounts of beeswax in a ratio of about 50:1 was melted in a small metal cup (See Figure 2).
Quartz based Gems
Quartz (Silicon dioxide) comes in a variety of colours, each with its own name. Amethyst, rose quartz, and citrine are all varieties of quartz that have been contaminated by trace amounts of iron (Sinkankas, 1962; Zeitner, 1996). Smokey quartz is a light brown and along with citrine, can pass for topaz. Quartzes have a hexagonal crystal that is apparent in clearer forms. Opaque varieties of quartz are usually massive, but the hexagonal crystal structure can still be seen under a microscope. Jaspers and agates, including carnelians and mocoa (moss agate) were the most used of the opaque forms of cryptocrystalline quartz in the American Colonies.
All these quartz varieties are cut and polished in the same way. Modern lapidaries use wheels impregnated with silicon carbide or diamond and then polish them with cerium oxide (Sinkankas, 1962). Before the discovery of cerium oxide, rottenstone (powdered limestone) also known as Tripoli was used, as well as tin oxide. Chambers (1728) describes the use of lead wheels charged with smalt (emery) and water to cut the stones and then polishing them with Tripoli.
Opal
Opal is also a quartz; however, it is more delicate and subject to thermal shock. Because of this, opals are now polished quickly on felt using cerium oxide (Sinkankas, 1962 p. 270-1). Holtzapffel recommends that it be cut similarly to alabaster rather than quartz, using a wooden wheel with flour emery for a preliminary polish and a leather wheel with putty powder, a mixture of tin and lead oxides (Holtzapffel, 1894, pp. 10,96). Chambers wrote that opals were cut and polished on a wooden wheel with Tripoli (Chambers, 1728).
Other types of Stones
Garnets (Carbuncles)
There are several varieties of garnets. The most popular are Almandine (Iron aluminium silicate), that range from a brownish red to a purple red, and Pyrope (Manganese aluminium silicate) which are predominantly dark red. They both have a hardness of 7-7.5 and a dodecahedral crystal structure. Pyrope garnets are also described as Bohemian garnets from the place where they were first found and are known for their intense red colour (Sinkankas, 1962, p.263; Zeitner, 1996). Garnets tend to be brittle, so care is taken to avoid chipping. In modern work, aluminium oxide or chrome oxide is used on wheels made of leather for polishing (Sinkankas, 1962 p.262). Holtzapffel recommends polishing cabochons using wooden wheels with Tripoli (Holtzapffel, 1894, p.58)
Emeralds are a green variety of beryl, aquamarine being the blue variety. They are usually flawed with either inclusions or small cracks. Sinkankas (1962) recommended sealing any holes by heating the stone and dipping it in warm shellac. After cutting and polishing the stone, the shellac is removed by boiling in alcohol. Emeralds are now polished on leather with either aluminium oxide or chrome oxide, or on felt with cerium oxide. Sinkankas notes that emeralds are slower to polish using cerium oxide (Sinkankas, 1962, pp.251-252).
Topaz is a hard stone, registering 8 on the Mohs scale of hardness. Modern lapidaries polish topazes on leather wheels with aluminium oxide (Sinkankas, 1962). In the 18th Century, topazes were polished on a copper wheel with Tripoli (Chambers, 1728).
Jet
In the past, several materials could have been identified as jet including coal, cannel coal, shale, or any other similar black mineral that was reasonably durable and could be polished. After cutting and polishing these materials, it is difficult to differentiate between them without the use of microscopy (Allason-Jones and Jones, 2001). True jet is defined as `being formed from drifted wood which has been secondarily impregnated with bitumen from its surrounding sedimentary environment' (Stach, 1982). All these materials can be carved with steel tools. Cabochons or flat pieces are ground with fine emery and finally on worn 200 abrasive sandpaper. Jet is usually polished on felt or leather wheels using cerium oxide, aluminium oxide, or tin oxide (Sinkankas 1962, p.266). Zeitner notes that when worked, jet has a greasy smell (Zeitner, 1996). Holtzapffel recommended working jet with a lead wheel and polishing with rottenstone and flannel in hand (Holtzapffel, 1894 pp. 10,31,70). When visiting the Jet Museum in Whitby, the author saw an original jet workshop where a variety of leather wheels were used, including walrus hide, and the use of crocus (iron oxide) as a polish.
Paste/Glass
Although not a natural gem, paste was popular since it could resemble more expensive gems at a fraction of the cost. The disadvantage was that paste is not as hard or as durable as most gems, so care needed to be taken when cutting and polishing the material. Modern lapidaries describe a process like cutting quartz, but the lapidary of the 18th Century would have used emery and polished with tin oxide on a soft felt or leather wheel (Sinkankas, 1962, p. 263), although Holtzapffel recommends using pumice (1894, p. 103). Paste gems were also improved in various ways. Colours were enhanced by using dyes or coloured inks, and stones could appear to be more brilliant by fitting a textured metallic foil between the back of the stone and the setting. (Nicols, 1652).
Scaling Back from Modern Equipment: The Experimental Lapidary Work at Colonial Williamsburg
Decisions about Building the Equipment
Many early illustrations depict lapidary tables with horizontal laps (wheels) operated by a hand crank. These also feature a jamb peg machine. These tables are designed for cutting faceted stones and feature a brace with holes drilled at specific angles. The dop stick is inserted into one of the holes of the jam peg, and the stone is lowered until it is in contact with the rotating lap which has been impregnated with either an abrasive or a polish. When one facet is cut, the stone is inserted into the next jamb peg hole to cut the next facet (Holztapffel, 1894, p. 604).
Gemstones have been cut on vertically mounted wheels that are operated similarly to a lathe since c 4000 BC (Untracht, 1985, pp.591-592). A metal rod, called an arbour, supports multiple wheels that are coated with different grades of abrasives. Due to the limitations of time and materials, it was decided to adapt a lathe that had been used for silversmithing and was currently in the gunsmithing shop. It was fitted with a square arbour that would prevent the wheels from slipping. Wooden wheels were made, and the abrasives were glued to the edge using emery and sandpaper made from linen tape. Polishes were applied directly to the wooden wheels or were applied to leather that was glued to the edge of the wheel. In addition, a polishing wheel was made from walrus leather. The walrus leather was obtained from a sheet that had been in the silversmith’s shop for over 50 years. The adapted lathe used to build the lapidary machine was larger than would have been used by an individual gem cutter, but the sizes of the wheels, as described below were consistent with lapidary workshops of the period.
Abrasives and Polishes
Holtzapffel (1894) describes the process for grinding and polishing carnelians as grinding the rough stone on a lead or pewter wheel with coarse emery and continuing with finer emery. The polishing is done on a lead wheel with “a plentiful amount of rottenstone and water”. Harder stones (e.g., rubies or sapphires) could be polished on a copper wheel (Holtzapffel 1894, p. 32). Chambers (1728) describes a similar process using emery (smalt) and Tripoli for a polish.
Iron oxide (crocus) (Holtzapffel, 1894, pp 96-99) is chemically the same as hematite; however, now it is seldom used because better polishes are available (Sinkankas, 1962 p. 72).
Putty powder (tin oxide) often included lead oxide (Holtzapffel, 1894, pp.103-104), Modern mixtures often include calcium or magnesium carbonate. It is also rarely used now because better polishes are available (Sinkankas, 1962, p. 72)
Rottenstone / Tripoli is a fine powdered porous rock with rounded particles that is still used as a mild abrasive for woodworking and metalworking. Holtzapffel also describes it as a variety of silex (Holtzapffel, 1894, pp. 5-6,105,119). Chemically it is silicon dioxide, pulverised weathered limestone mixed with silica containing the remains of silicated diatoms (Sinkankas, 1962, p. 72).
Sand (silex) is also used as an abrasive (Holtzapffel, 1894, pp. 108-109).
Lead oxide and lead grinding and polishing wheels were popular in the 18th Century, however, in the interests of health and safety no lead-based materials were used in the experiments.
Wheels were cut from hardwood by Brian Weldy, master of the Joinery Shop with square holes to fit a specially made arbour for the lathe. We discussed cutting down grindstones but would have had to cut square holes in the centre that would fit the arbour. Since the procedure would take longer, and that there was the risk of cracking the stones, it was decided to use wooden wheels with abrasives adhered to the edges.
The wheels were eight inches/20 cm in diameter and ranged from 1 ½ to 2 inches/3.8 to 5 cm wide. Four of the wheels were designated for grinding and sanding and two more for polishing. Commercial wet/dry sandpaper (220, 400, and 600 grit abrasives) were adhered using hide glue to the edge of two wooden wheels, and a replica sandpaper made of linen tape, hide glue, and 150 grit emery powder was glued to the edge of the fourth wooden wheel. A fifth wheel had belt leather glued to the edge of a wooden wheel for use with Tripoli and tin oxide (See Figure 3). In addition, two four-inch/10 cm diameter wheels of walrus hide were cut. One of the walrus hide wheels was mounted on the lathe and the other shown to visitors. The wheels were arranged with spacers with the coarsest on the left and progressing to the finest on the right, ending with a leather wheel that would be used with Tripoli (See Figure 3 and 4). The walrus hide wheel was placed by itself on the far left so as to avoid contamination. The arrangement of the wheels and the position of the lathe in the shop was chosen to allow the visitors to be able to see the lathe in action with as little obstruction as possible.
To be cut without damaging the stone, the wheels must be kept cool. Both in historic and modern contexts this is done with a drip system, or by having a shallow pan of water that would be filled to where the water would touch the bottom edge of the wheel. The wheels rotate counter clockwise so the water and swarf (the dislodged abrasive and ground particles of stone) would be thrown from the bottom and away from the person cutting the stones. Since the stones were small, and the lathe ran at a much slower speed than modern commercial lapidary machines, it was decided to have several small pots of water that were labelled to match each wheel and had a small rag tucked into the handle. The rag was dipped in water and wiped on the wheel as it turned. Labelling the pots and keeping their specific rag prevented abrasives from coarser wheels from contaminating the wheels with finer abrasives. Rather than cutting one stone at a time, the most efficient practice is to cut several stones at a single wheel, starting with the coarsest wheel. This is because the stones and the lathe have to be cleaned before progressing from the coarser wheel to the next wheel with a finer abrasive in order to avoid contamination from coarser grits.
Cutting the Gems
A selection of quartz, rose quartz, amethysts, garnets, opal, and carnelian were used in the experiments. These stones reflected a representative sample of the types of stones that were popular in the 18th Century American colonies (See Figure 5).
The stones were dopped and cutting commenced with the coarsest abrasive (150) to form the basic shape of the cabochon. The handmade sandpaper worked well, and lasted longer than the commercial paper, although it produced more swarf and was much messier. The other wheels that had the modern commercial wet/dry sandpaper were bare of any abrasives by the end of the day (approximately five hours of use). After cleaning, new sandpaper was glued to these wheels at the end of each day.
For the procedure, once the wheel was in motion, it was wet by wiping it with a damp cloth. The stone is introduced at an angle that will not gouge into the wheel. From that point the stone is constantly rotated, grinding down high spots, and avoiding the creation of any flat areas. The goal is to create a domed, symmetrical shape, either round or oval. All the coarse shaping is done on the first wheel, and when the basic shape is achieved the stone and work area are cleaned, and the gem is further refined on the next wheel.
Cutting the gems was noticeably slower than with modern electric lapidary machines which typically run from 1700-2000 rpm. Historical wheels have the limitation of the physical amount of energy that the lapidary is able to produce. Treadling at a high speed or for long periods is tiring. Treadling at 1-1 ½ rotations per second produced an rpm of about 240 for the lapidary wheels, which produced a steady rhythm for long sessions of cutting gems. In lapidary work, speed and pressure are not necessarily positive actions. If I pressed the stone against the wheel, I could feel more strain in my leg. This is a physical sensation that is not experienced when using modern machinery and was a constant reminder for me to not press the stone into the wheel so that the machine could work more efficiently. This sensation would have been felt by a lapidary using a foot pedalled or a hand powered machine.
In tracking the progress of a sample stone, Figure 6 shows a carnelian before grinding and after 30 minutes of shaping on the 150 abrasive emery wheels, and then 30 minutes on the 220-grit wheel. This was followed by 10 minutes on the third wheel with 400 grit, and five minutes on the final wheel with 600 grit abrasive. For the pre-polish the leather wheel was dampened, and then small amounts of Tripoli were dabbed on the wheel. Only a small amount of the powder was needed. The stone was prepolished for two minutes. The final polishing wheel was made of walrus hide with tin oxide for two minutes. When polishing the wheel is only slightly dampened, and only a small amount of polish is used. It is the only phase in which the stone is worked as dry as possible.
Wheel maintenance was a constant. At the end of each day more abrasive or new strips of sandpaper needed to be applied to the coarsest three wheels. Typically, the 220-grit wheel would be worn smooth after cutting five quartz stones on it. Since most of the heavy shaping is done on these wheels, it is natural for them to wear out the most quickly. The 600 abrasive wheels saw only light use, as it was needed only for sanding out any small imperfections before a pre-polish on the leather wheel.
Comparing the Experimentally Cut Stones to 18th Century Stones
A selection of jewellery with gemstones was made available from the DeWitt Wallace Collections of Colonial Williamsburg Foundation to compare the polish on historical stones to that of the stones being cut as part of the experimental programme. It was requested that the pieces were from historical collections rather than recovered archaeologically to avoid stones that could have been damaged by a more abrasive burial environment. Under magnification, the table facets of the rubies set in a brooch (1954-611), display fine parallel horizontal lines that can be seen underneath random scratches and damage caused by wear (See Figure 7). This can be compared to the stones cut during the experiment using a tin oxide polish (See Figures 8a and b), and a modern topaz polished cut by the author and polished with alumina oxide (See Figure 9). The lapidary must constantly check the stone under magnification for scratches and to see the degree of polish. If the stone is slightly softer, as in the case of a citrine compared to a topaz, then the lapidary must adjust the speed of the wheels and the amount of pressure applied to the stone in order not to cut too quickly or deeply. The fine abrasions seen in the stones cut with tin oxide and the historic stones are slightly coarser compared to the stone polished with alumina oxide, and as a result, they will seem slightly less lustrous than the modern stone when examined in hand.
Discussion
Fundamentally the lapidary craft has changed little since the 18th Century. Outside of electric power, the most significant changes were in the abrasives and polishes used. Smalt and emery were replaced by silicon carbide, and the discovery of aluminium oxide and cerium oxide in the middle of the 19th Century replaced iron oxide and Tripoli. Tin oxide is still used for some stones, however it along with iron oxide is soft (1-2 Mohs) compared to aluminium oxide and cerium oxide, which have a hardness of 9 and 7-8 respectively. These hard, well-refined polishing abrasives can polish much more quickly and efficiently. Levigated diamond powder mixed with oil was also used throughout this time and is still used today both as an abrasive and polish but the ability to finely sort diamond powder was more limited in the 18th Century than it is today.
Polishing compounds have been the source of a mild controversy for generations. The process doesn’t appear as if it is a continuation of abrading with increasingly finer materials until the scratches are invisible to the human eye. Polishing seemed so special that in 1912 George Beilby, a chemist, published a paper about the mechanics of flow when polishing gems. His book, Aggregation and Flow of Solids (Beilby, 1912) posited that the chemical agents used for polishing, while under the pressure and heat of the polishing process, caused a thin layer on the surface of gems to partially liquify, flow, and then solidify to form a smooth surface. So popular was his theory that the polished surface of a gem was often referred to as the Beilby Layer. His theory held until the late 20th Century when researchers examined gems and concluded that polishing was indeed a series of increasingly finer scratches (Crowcroft, 1984; Engin, 2013).
Experiential Archaeology
An experienced lapidary relies on tactile information rather than constantly visually checking the stone. As the stone is rotated against the wheel, the lapidary can feel irregularities and adjust the angle or concentrate on a particular area until it feels symmetrical. The experience is described by Sennett (2008) as a feedback loop in which gesture and movement appear to be instinctual but are instead the ingrained physical responses based on previous experiences. In this way, the lapidary can gently slide the stone back and forth over a raised section until it is ground down to a smooth curve that continues across the stone.
A modern lapidary need only turn on the machine and adjust the speed before introducing the stone to the wheel. In this case when starting the lathe, the flywheel had to be brought into position so that when treadling commenced, the wheel would turn so that the swarf would be thrown away from the person cutting the stone. Once the lathe was going at the ideal speed, the wheel was moistened and then the stone was introduced to the wheel. Coordination was not difficult, but the amount of friction applied against the abrasive wheel did affect the ability to pedal at the same speed. In this way, I was given a signal that I needed to work more lightly and allow the water and abrasive to work more efficiently.
Public Interpretation
The mornings were spent in modern clothing doing experimental work, but the afternoons were spent in 18th Century costume and the shop was opened for the public to tour. I would explain the lapidary work and the process of cutting gems while treadling the machine. After they had seen the process, I then stopped to show examples of uncut stones and similar stones that had been finished. The most popular questions involved the mechanics of lapidary such as how the stone was held on to the stick and how the foot-pedalled lathe operated. Visitors also wondered if my left leg was stronger than my right leg since the lathe was treadled with only one foot.
Questions about where gemstones came from led to discussions about the Navigation Acts and Stamp Act, illustrating how craftwork in Colonial America was tied to larger political and social issues. When people asked about where I got the gems I was cutting, I explained that normally I would have hand-picked material at a gem and mineral show, but because of the COVID-19 pandemic, I had to rely on mail order. This led to a comparison of my situation to 18th Century lapidaries who would have to order material from overseas without seeing it prior to purchase, and often wait several months for it to arrive. Overall, the public was highly engaged and interested in a craft that they had not thought about previously.
Conclusion
While the physical coordination of treadling and cutting stones was not difficult, keeping the lathe running for hours was tiring. It was difficult to maintain speeds of more than about 250 rpm for extended periods of time. However, the advantage of the slower speed was that there were fewer opportunities for cutting a stone too far, or accidentally creating flat surfaces because the speed of the wheel is outstripping the pace at which the lapidary is rotating the stone against the wheel. A frequent mistake among beginning lapidaries is to run the machine at the highest speed to cut faster, but instead, it creates opportunities for making mistakes quickly.
In the 18th Century, jewellery would be seen under candle or lamplit conditions, often from a distance. The effect would be colourful and scintillating. Under these circumstances, it would be impossible to tell the difference between paste and genuine gemstones. Likewise, the polish would have been good enough to provide a lustre that would impress others seeing the jewellery at a social event. It is only when the jewellery would have been brought to a jeweller for appraisal or sale that the quality of the cut and the actual type of gem would come under scrutiny.
Overall, the experiments in recreating the lapidary equipment and the use of 18th Century polishes were successful, and the Fellowship provided the opportunity for both the support of the experimental work and for public outreach, enlightening an aspect of the history of a craft that deserves more study.
Acknowledgements
A project as large as this is the product of many hands and would not have been possible without the support of the staff and craftspeople of Colonial Williamsburg. Everyone at Colonial Williamsburg is extremely busy, filling days with the practical work of their trade in which they manufacture objects for use by other craftspeople in Colonial Williamsburg or for sale in some of the shops. In addition, they spend time demonstrating and interpreting their craft for the public. This often leaves very little free time, and I am grateful for all the people who took time out of their intense schedules to assist me on this project. Without their contribution of time and energy, it would not have been possible.
I wish to thank Brian Weldy for adapting the lathe and making the wheels, in addition to taking time to learn about the lapidary craft to reproduce everything that was needed. I am also grateful to Janea Whitacre for the loan of the costume, Janine Skerry, Tina Gessler, and Patricia Silence for their assistance in examining gems at DeWitt Wallace Collections and Conservation, and to Carl Childs of the Rockefeller Library for providing access to the library and research documents. Also, thanks to Rebecca Starkins Godzik and Janea Whitacre for outfitting me in 18th Century clothing.
Thanks to George Cloyed and the staff of the Rockefeller Library, Christina A. H. Strum, and Karen Clancy for the loan of equipment and information about jewellers of Williamsburg, to Ted Boscana Director of Trades who made his staff available, and especially to Dr Peter Inker and Wendy Sumerlin who coordinated the project and made sure that everything ran as smoothly as possible.
- 1Moss agate, a clear or white agate with green dendritic inclusions that resembles moss.
Keywords
Country
- USA
Bibliography
Allason-Jones, L. and Jones, J.M., 2001. Identification Of `Jet' Artefacts By Reflected Light Microscopy. European Journal of Archaeology, 4(2), pp. 233-251.
Bateman, W., 1774. New York Gazette and Weekly Mercury, Nov 7, 1774.
Beilby, G.T., 1912. Aggregation and Flow of Solids, London: Macmillian and Co.
Bombay, S., 2021. On This Day: The Stamp Act plants seeds of the Revolution. Constitution Daily, Constitution Center. Available at: < https://constitutioncenter.org/blog/on-this-day-the-stamp-act-plants-seeds-of-the-revolution > [Accessed 13 May 2022]
Bruff, C.O., 1775. New York Gazette and Weekly Mercury. Feb 6, 1775.
Chambers, E., 1728. Cyclopædia : or, an universal dictionary of arts and sciences; Containing The Definitions of the Terms, And Accounts of The Things signify'd thereby, In the several Arts, Both Liberal and Mechanical, And the several Sciences, Human and Divine: The Figures, Kinds, Properties, Productions, Preparations, and Uses, of Things Natural and Artificial; The Rise, Progress, and State of Things Ecclesiastical, Civil, Military, and Commercial: With the several Systems, Sects, Opinions, &c. among Philosophers, Divines, Mathematicians, Physicians, Antiquaries, Criticks, &c. The Whole intended as a Course of Antient and Modern Learning. London: James & John Knapton; John Darby; and others.
Crowcroft, P.J., 1984. Demise of the Beilby-Bowden Theory of Polishing. Lapidary Journal May 1984.
Engin, I.C., 2013. Theories on Rock Cutting, Grinding and Polishing Mechanisms. In: H. Pihtili, ed., Tribology in Engineering. IntechOpen: London.
Fales, M.G., 1995. Jewelry in America 1600-1900. Woodbridge, Suffolk England: Antique Collectors’ Club.
George II, 1732. An Act for the Free Importation and Exportation of Diamonds, Pearls, Rubies, Emeralds, and all other Jewels and precious stones. John Baskett: London.
Heath, B.J., 1999. Buttons, Beads, and Buckles: Contextualizing Adornment Within the Bounds of Slavery. In: M. Franklin and G. Fesler, eds., Historical Archaeology, Identity Formation, and the Interpretation of Ethnicity. Colonial Williamsburg Foundation Library Research Report Series – 0385. Williamsburg: Colonial Williamsburg Foundation Library.
Holtzapffel, C., 1894. Turning and mechanical manipulation vol III: Abrasives and Other Processes Not Accomplished with Cutting Tools Mendham, New Jersey: Astragal Press
Nehama, S. and Bentley, A.E., 2012. In Death Lamented: The tradition of Anglo-American mourning jewelry. Boston: Massachusetts Historical Society.
Nicols, T., 1652. Arcula Gemmae or The Cabinet of Jewels. Cambridge: Thomas Buck University of Cambridge.
Ormsbee, T.H., 2009. Flashback: Colonial Americans and Their Jewelry. Collectors Weekly Available at: < https://www.collectorsweekly.com/articles/colonial-americans-and-their-jewelry/ > [Accessed 13 May 2022].
Sawers, L., 1992. The Navigation Acts Revisited. The Economic History Review, New Series, 45(2) (May, 1992), pp. 262-284.
Sennett, R., 2008. The Craftsman, London, Penguin Books.
Sinkankas, J., 1962. Gem Cutting: A Lapidary’s Manual. Second Ed. New York: Van Nostrand.
Stach, E., 1982. Stach's Textbook of Coal Petrology. Berlin and Stuttgart: Borntraeger.
Untracht, O,. 1985. Jewelry Concepts and Technology. London: Robert Hale.
Virginia Gazette Feb 24, 1769 No. 146. Accessible through the Colonial Williamsburg Rockefeller Library Collections Pages < https://research.colonialwilliamsburg.org/DigitalLibrary/va-gazettes/ > [Accessed 13 May 2022]
Williamsburg, Va., 2022. A Brief History of Williamsburg. Available at: < https://www.williamsburgva.gov/488/History > [Accessed 13 May 2022].
Zeitner, J.C., 1996. Gem and Lapidary Materials for Cutters, Collectors and Jewelers. Tuscon: Geocsience Press.