The content is published under a Creative Commons Attribution Non-Commercial 4.0 License.
Reviewed Article:
An Experimental Approach to Ancient Egyptian Metalworking: The Mysteries of the Sesheshet
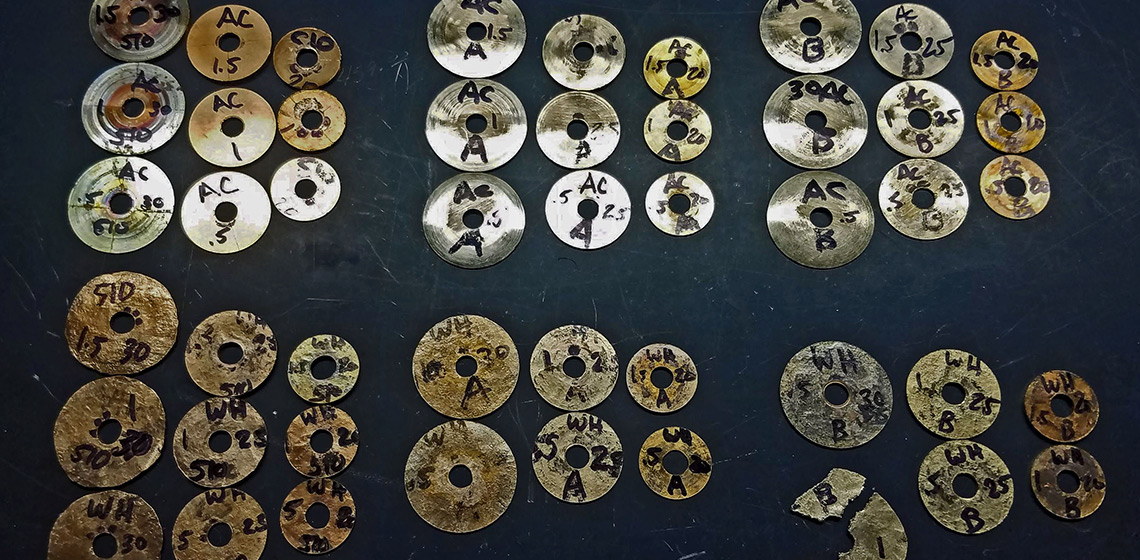
Our research represents a case study in ancient metalworking to illuminate the challenges, processes, and both human and material agency behind these objects. We focus on copper alloy Hathoric loop sistra since these musical instruments are steeped in ritual and mythological connections to metalworking. Our work represents the early stages of our ongoing investigations into the materiality of metal production in ancient Egypt. The ancient Egyptians never recorded any detailed description of craft production. While many scholars have suggested the use of lost wax casting in Egyptian metal working, we argue that this conclusion not only ignores significant technical obstacles, but overlooks the enigmatic complexities of craft production scenes in Egyptian art. We argue that these scenes are heavily imbued with religious connotations and therefore should not be read literally as some scholars have done in the past.
Introduction
In our research, we investigated the metallic properties ancient Egyptian copper-alloy loop sistra that first appear during that first half of the 12th Dynasty (ca. 1991-1843 BC) and reappear in the 18th Dynasty when they become decorated with the double face of the solar goddess Hathor (Soles and Giumlia-Mair, 2011, p.138).1 The two faces reflect the goddessâ dual nature as both destructive and benevolent (Pinch, 1982, p.140).2 In their most common form, sistra consist of a handle, capital, and loop (See Figure 1). The loop is pierced on either side for cross pins which support sounding metal disks. Sistra range in height anywhere from 4 cm tall amulets to 40 cm instruments intended for play.
Hymns to Hathor regularly imply the shaking of sistra accompanied by song and dance, highlighting the sacramental aspect of both producing and hearing the sound (Finnstad, 1999, p.113). Egyptian literature also alludes to soundâs transformative property, punctuating points where a character crosses a boundary in time, space, or experiences a change in his own identity (Manassa, 2011, pp.152-153).3 These changes are not unlike the seemingly âalchemicalâ transformation that copper undergoes on its journey to becoming a ritual object.
Hathorâs connection not only with the instrument but also with its production process is considerable, but for the sake of brevity will only be briefly addressed here. Hathor at her root, is a solar goddess associated with the foreign regions and minerals including precious metals and what the ancient Egyptians called âtrue ,â often understood as âcopperâ (Harris 1961, 60-62; WB I, 436.1; Roberts, 2019, p.149),4 most of which was mined outside of Egypt and thus in Hathorâs territories. Her name itself is significant,
meaning âMansion of Horus,â a reference to a realm of the sky that appears in the Pyramid Texts in which the deceased king is rejuvenated, additionally characterizing her as a birth goddess (Leitz ,2002, pp.75-76). In later periods, Hathor is the Eye of Re, both the sun godâs daughter and mother (Pinch, 1982, p.137). It is this concept of the goddess giving birth,
[to birth] (WB II, 137.4), to the sun god which serves as the clearest allusion to the alchemical nature of the smelting process, and one which will serve as the binding thread of the following discussion. Worth noting is that
is also used to describe the procurement of metal ore, or mining (WB II, 138.11), highlighting not only the creative aspect of the goddess, but also the vitality of the minerals themselves, insofar as they are âbirthedâ from the earth (Daumas, 1983, pp.115-116).
Texts as early as the Middle Kingdom already emphasize copperâs solar connotations and allude to the materialâs radiant nature and connection with the sun (Lalouette, 1979, pp.338-339). For example, in the Middle Kingdom Coffin Text 17 (below), which reappears in the New Kingdom Book of the Dead when Hathor-headed sistra appear, the verb [to swim] (WB II, 236.10) is almost certainly a sound play as a homonym of the verb
[to smelt] (Grapow, 1917, pp.55-56; WB II, 236.6). Here, the sun god Reâs shining enigmatically evokes the act of smelting copper and highlights the âanimateâ nature of the material and the âanimatingâ nature of the process (Lalouette, 1979, pp.338-339). The text reads:
These text examples underscore the importance of understanding Egyptian art and language beyond a literal sense, implying that efficiency and manufacture of a finished product may not have been the primary objective in the manufacture of a ritual object. Instead, the production process itself may well have been steeped in ritual significance.
Manufacture & Design
The multi-component design of the loop sistrum would have necessitated more than one production methodology. The ancient Egyptians, however, did not leave us with explanations of these processes beyond vague tomb imagery and, as we argue, intermittent and enigmatic mythological allusions. In other words, there is a disconnect between what the scenes depict the craftsmen doing and what they are actually doing that has not been adequately addressed in the past.
The fine detailing of sistra handles and capitals suggests production via the lost wax casting process, long recognized in Egyptology, and practiced in Egypt by at least the Second Dynasty (ca. 2890 BC) if not earlier (Garland and Bannister, 1927, p.35). The earliest Egyptian evidence for beekeeping (See Figure 2) dates even earlier to the First Dynasty (ca. 3000 BC) (Kritsky, 2015, p.7). Furthermore, a much later hieratic text describes bees and their products as gifts from the creator god Re, who, as demonstrated above, plays a vital role in the production of bronze. The text reads:
âThe god Re wept and the tears from his eyes fell to the ground and turned into a bee. The bee made his honeycomb and busied himself with the flowers of every plant; so the wax was made and also honey out of the tears of Reâ
(Derchain 1965, fig. I.2; Kritsky, 2015, pp.1-2).
Not only does the above text again implicate Re in the bronze making process, but it also reveals that every stage of production has mythological connections that do not necessarily survive in the finished product. Although the lost wax process has long been recognized in the ancient world, archaeological evidence of ancient wax is somewhat rare, leading to speculation over the composition of the wax used in the process. Scholars generally agree that the primary constituent was filtered beeswax, which becomes more pliable as it is warmed but rapidly rigidifies as it cools (Noble, 1975, pp.368-369). Adding natural oils or resins, such as pistachio resin (AuenmĂŒller, Verly and Rademakers, 2019, p.144), to liquified beeswax can also prolong its malleability once it begins to cool, although evidence of additive use is rare.
While our experiment did not primarily focus on the wax used, we nonetheless attempted to work with four different wax compositions to test the viability of certain additives to make the sistrum handle for an investment mould. These compositions included beeswax mixed with turpentine, raw beeswax and pistachio oil, a modern lost wax formulation, and pure beeswax. We sourced our wax from a local apiary, raw and unfiltered. Of all our composition tests, the pure unfiltered beeswax proved most usable for our purposes. We were able to carve and smooth this unfiltered wax using only the heat from our hands. The wax did not leave behind excessive carving debris and it proved to be the most durable of the four combinations when cool.
Archaeological evidence for ceramic investment casting moulds, otherwise known as lost wax casting moulds, is limited in Egypt, although examples of such molds do exist (AuenmĂŒller, Verly and Rademakers, 2019, p.144).5 This limited evidence may be due to the mouldâs destruction after casting but may also indicate an additional or alternative casting method, such as sand casting (Hauptmann and Laschimke, 2016, pp.751-761), which leaves no trace of the original mould since sand moulds are destroyed to release the casting. These moulds use sand compacted around a pattern which is removed, leaving a void in its place to be filled with molten metal. Future research focusing on surface studies of cast metal objects could shed light on the type of mould used in the objectâs production as the surface of the object would retain the texture of the mould medium.
Sand casting is rarely mentioned in ancient Egyptian metal working scholarly discussions, but the technology was certainly available. The earliest sandcasting evidence to date comes from an early 2nd millennium coppersmithâs workshop at the site of Tell edh-Dhibaâi in Baghdad and not Egypt, but the crucibles found at the site are identical to those depicted in the Fifth Dynasty (ca. 2494-2345 BC) tomb of Mereruka at Saqqara (See Figure 3), suggesting possible interaction (Davey and Edwards, 2007, pp.146-148; Davey, 2012, pp.89-90) and perhaps a longer sand casting tradition than the archaeological record can account for due to post-use disintegration. We used the handle we carved in beeswax as a pattern for a cope and drag, or two part, sand mould, the upper half being the cope and the lower being the drag, and re-used this same handle as a pattern for an investment mold (See Figure 4). We used commercially available oil-bonded green sand in our two-part cope and drag moulds since it was not only cost effective but was also quite easy to pack into our wooden mould boxes and is reusable after a casting when burnt sand immediately surrounding the casting is removed.6
We selected a low-fire terracotta clay which can achieve full firing under 900°C in place of natural Egyptian earthenware, terracotta being typically classified under the wider category of earthenwares (Rice, 2015, p.5). Clay can be somewhat stiff and unlikely to capture all the fine details of the pattern, so we created a slurry of clay and water to coat the wax handle before encasing it fully in clay. Egyptian moulds may have had a sandier consistency and may not have required a slurry (AuenmĂŒller, Verly and Rademakers, 2019, p.144). The wax pattern of an investment mold melts out during firing, leaving a negative form (See Figure 5). Firing also helps dry the clay by converting any pore or surface water to vapor and is easily accomplished at low temperatures under 200°C (Rice, 2015, pp.102-103). Any water left in the clay when molten bronze is poured in will expand rapidly as gas and cause the mould to shatter.
Casting and Constructing the Sistrum
We used an antique, propane-powered, plumberâs lead melter as our furnace (See Figure 6), which we outfitted with refractory wool, creating an enclosed space akin to a pit furnace in which a crucible rests upon a bed of charcoal or other heat source. The crucible rests on supports which are directly above the furnaceâs flame. The crucible was a size #3 graphite crucible which could contain 4kg of material. We cast a total of about 10kg of our alloyed bronze over the course of the project and another 1kg of pure copper. Melts were stirred using wooden rods to aid in deoxidizing the material. Leftover material was cast into blank ingots for later use. A standard high-temperature thermocouple probe was inserted inside the furnace adjacent to the crucible and connected to a digital thermometer. The force of the propane simulated the airflow and heat that in ancient times would have been generated by blowpipes, bellows, or natural winds directed at a heat source (Craddock, 1995, p.159). We were able to achieve temperatures more than 1100°C, more than enough to melt copper whose melting point is around 1082°C. Equally high temperatures could have easily been achieved over a charcoal hearth with the aid of bellows or blowpipes (Scheel, 1989, p.23).
Fuel scarcity may in part be responsible for the continual depictions of multiple blow pipes and bellows in Egyptian art, as seen in the 18th Dynasty tomb of Rekhmire (See Figure 7). However, these methods also result in differential heating, evidence of which is found in the ubiquity of broken crucibles at ancient smelting sites (Davey and Edwards, 2007, p.152). Like the wax, the crucible was not the focus of this experiment, so we used a graphite crucible to maintain control over melting and pouring conditions.
Object | A | B | C |
Element % | (HNM 14398, from disks) | (2001.212) | (1949.106.A-C) |
Cu | 89-90 | 80,9 | 78,87 |
Sn | 4.9-5.1 | 5 | 0,83 |
Sb | Trace | 0,13 | 0,06 |
Pb | 0 | 5,8 | 0 |
As | Trace | 0,11 | 0,1 |
Fe | 0-1 | 0,45 | 0,15 |
Ag | 4,8 | 0,48 | 0,08 |
Zn | 0 | 6,95 | 19,9 |
Table 1. Observed Object Compositions. Documented chemistries of three sistra, object numbers listed. One object had only XRF data available which could not quantify the amounts of each element, so this object composition was not considered in the experiment.
Studies of ancient Egyptian sistra are nearly devoid of quantitative compositional data.7 From our study of 154 sistra, ranging in date from the Old Kingdom to the Late Period, only 86 were of copper-alloy, and of those 86 only four had data available on chemical composition and only three possessed numerical data (See Table 1). Of those four with known chemistry, only one could be dated to the Egyptian New Kingdom, and this sistrum was found outside of Egypt in Mochlos, Crete (Soles & Giumlia-Mair 2011). Due to the extremely limited amount of compositional data, we experimented with a standard bell-bronze (Heine, Loper and Rosenthal, 1967, pp.373-374). We also experimented with a modern 510 phosphor-bronze alloy as a control for both working and sound quality (See Table 2).
Composition | Standard; 510 Bronze | A | B | C |
Element % | High Silver | High Lead | High Zinc | |
Cu | 94,8 | 90 | 80 | 78 |
Sn | 5+ | 5 | 5 | 1 |
Sb | 0 | 0,1 | 0,13 | 0,25 |
Pb | 0,05 | 0 | 6 | 0 |
Fe | 0,1 | 0,1 | 0,5 | 0,15 |
Ag | 0 | 4,8 | 0,5 | 0,1 |
Zn | 0,03 | 0 | 7 | 20 |
Table 2. Adjusted Experiment Compositions. : Standard control compositions (phosphor and bell bronzes) and adjusted object compositions used during the experiment. Adjustments were made for ease of measurements during casting.
Casting
The sand-cast handle was a partial success; the mould halves separated slightly as the metal was poured in, causing a seam to form around the perimeter of the handle and smoothing facial details on one side. The lost wax cast handle was our most successful casting (See Figure 8). Once the mould cooled, we broke it open to release the casting- much like an egg, following the allegory of Reâs egg where Re is now fully formed. The casting retained all the fine details from the wax pattern with minor imperfections which we ground and sanded smooth. Finishing techniques were not the focus of the experiment, so in order to save time and retain control over the experiment we used metal files, coarse 60 grit sandpaper, and an electric angle grinder for sprue removal when necessary. Any surface detailing was done by hand using sandpaper. Most imperfections were left as-cast. The ancient Egyptians had available to them emery, along with hard stones to grind and polish, but it is not yet known what additional materials may have been used to achieve the high-quality polish and finish that is seen on so many objects (Garland and Bannister, 1927, p.71).
We experimented with both a cope and drag mould and an open sand to create the loop of the sistrum. We first attempted to cast the loop as a flat bar with holes for cross pins cast-in and work the bar into the shape of the loop. We used a beeswax pattern for the cope and drag mould with small wooden dowels inserted through it at the location of cross pin holes to retain the openings during casting. We removed the pattern from the mould before casting, leaving the dowels in place. The resulting casting from the open mould resulting in a significant amount of overflow which needed to be ground down. While usable, this piece required a fair amount of post-work which included drilling the pin holes which were not retained. In contrast, the cope and drag cast loop had minimal overflow. The surface retained some of the irregularities of the wax pattern, and the holes were successfully preserved by the wooden dowels.
Casting Disks & Pins
Sistra disks range in diameter from 20 mm to 30 mm and are between 1 mm and 2 mm thick. Casting them to near-net shape or a complete shape, which requires little to no post work, is difficult using the cope and drag method (See Figure 9) due to the disksâ thin width. Mould runners must be wide enough to promote metal flow, but the cavities for the disks are by nature too thin to promote sufficient flow. Ultimately, we find it unlikely that the ancient Egyptians cast these metal disks in a closed mould. Instead, we pressed a disk pattern into a flattened sand mould face and carved thin channels between the depressions to promote the flow of molten metal. We used the standard bell bronze composition (See Table 2) for this set of disks since these are the main sounding elements of the instrument. The disks were difficult to pour accurately, almost certainly due to the size, weight, and shape of our graphite crucible. The resulting castings were misshapen, uneven, and the surfaces were full of oxide build-up (See Figure 10). While our disks were mostly unusable, this method may still be plausible with additional controls for crucible shape.
We have already established the lack of chemical analysis of nearly all sistra, and of those that do have this data, it is seldom provided for individual components. We opted to make the sistra pins from pure copper since they require a great deal of ductility. These were to be cast in an open mould (See Figures 11 & 12) in which wooden dowels were inserted vertically into packed greensand. A funnel was shaped and packed around the dowels, and then the dowels were removed. Molten copper was poured directly from the crucible into the voids. However, the pure copper resulted in a porous casting which was unable to withstand cold working. Future attempts may prove successful as the process is refined Wire drawing is unknown in ancient Egypt, but wire could have been produced by cutting and working strips of metal sheet (Garland and Bannister, 1927, p.70). The pins used in the Mochlos Sistrum are made with a silver-copper-alloy like that of composition A in Table 1 (Soles and Giumlia-Mair, 2011, p.143). Based on our later experience working this alloy, we suspect that pins could have been successfully cast and worked to shape with annealing.
In absence of usable cast pins, we substituted thick gauge copper wire to complete the project.
Once all the components were cast, they needed to be further worked and shaped. Bronze is a work-hardening material meaning that the more it is stuck, the harder it gets and the more likely it is to fracture. To counteract this natural property, we annealed, or reheated, the components to essentially âresetâ the microstructure of the material into its lowest-stressed state (See Figure 13). This process allows the material to be re-stressed during the next cycle of cold working without cracking.
Annealing
We have evidence that the Egyptians were aware of this property of bronze. One of the earliest known references to annealing in ancient Egypt comes from the Fifth Dynasty mastaba tomb of Wepemnofret at Giza (See Figure 14). Three sequential scenes and accompanying inscription, to be read from right to left, should by now appear familiar. The individuals on the far right are shown kneeling and forcing air into a pile of charcoal fuel. The text above these workers reads, âHurry, quickly put (it) at its baseâ (Weinstein, 1974, p.24). Molten metal has a very short pouring window before it solidifies and so the inscription is almost certainly an order to direct the blowpipes towards the base of the crucible to maintain the fire.
Left of the kneeling smelters, a man pours from a horn-shaped crucible, typical of the Old Kingdom style and consistent with those shown earlier in the tomb of Mereruka. The metal worker holds the crucible between two stones, pouring from the base of the crucible. The two men seated to the left are shown about to strike a rectangular object resting on a surface of either stone or wood with oval stones like those in the pouring scene. The caption behind the worker on the right tells the viewer that the rectangular object is âshining copperâ and the worker on the right says, âHeat this; it is dried upâ, âitâ being the copper. The worker on the left comments, âthere is no cracking if it is heated excellentlyâ (Weinstein, 1974, p.25). Considering our experiments, we understand that the worker is referencing the process of annealing and certainly the act the two are engaged in is drawing out the solidified copper, which we will see does indeed shine after quenching, meaning that these workers are, at the very minimum, reheating the copper for the second time and likely repeated the process several more times.
Working the Loop
We attempted both hot and cold forging on the open-mould-cast bronze bar, but it was too thick at roughly 11 mm and too narrow to be worked into a thin sheet metal loop. We attempted working a small section of this bar, but it cracked and fragmented with little input. We took the opportunity to use it as a test piece for bending with annealing, which we did using an acetylene torch with a neutral flame. The bar was heated to a dull red glow and immediately quenched in water. We annealed and then bent the bar by hand by leveraging it against opposing jaws of a vise, roughly 10-15° at a time, annealing between bends until about a 180° radius was achieved. The bar was not usable for the project; however, it did serve as an example of how annealing could be used to continuously shape a work-hardening bronze. The cope and drag mould-cast loop was highly porous, some large pores visible on the surface and many more riddling the interior, indicating that our mould was not sufficiently vented. We annealed this bar in the same manner as described previously and began to work it out with a steel headed blacksmithâs hammer and cast iron anvil, alternating rounds of annealing and working. The bar was thinned in each round from the centre towards the ends. We were unable to thin the bar sufficiently since it would have become too wide and/or potentially too damaged by working. We worked it from 8 mm to about 5-6 mm thick. Had the bar been originally cast thinner, it could have been much more workable for this experiment and thus more valuable in suggesting possible manufacturing techniques.
The holes for the pins were cast-in, the wooden dowels mostly carbonized during casting and were easily removed. We used a readily available steel punch to open and widen the holes since our tool needed to be harder than the material to be worked and annealed the bar again, focusing mainly around the centre where bending would occur. Like the first loop attempt, bends were no greater than 10° and were alternated with rounds of annealing. Unfortunately, the bar broke during bending, but we took advantage of this moment to use brazing to simulate a plausible Egyptian repair method in which molten metal is poured over and into an area of a break and allowed to harden, perhaps surrounded by clay to avoid overflow (Garland and Bannister, 1927, pp.62-63; p.75). We were able to reattach the broken halves, using a modern brazing flux paste to encourage the flow of molten material into the joint (See Figure 15). Any oily or waxy agent like tallow or rendered animal fat could have served as a fluxing agent.
Sound Studies
Separate from the disks mentioned earlier, additional disks (See Figure 16) were made for purposes of audio-spectral analysis to observe any sound pitch and frequency differences in different copper alloys due to alloying elements, hardness, and size. This study used compositions A, B, C and the phosphor bronze standard listed in Table 2. These alloys are three out of 84 bronze or copper alloy sistra that we studied, and of these three, only one, composition A, was obtained from sistra disks (Soles and Giumlia-Mair, 2011, p.138). Experiment control was emphasized for these disks since we only wanted to examine sound quality rather than methods of manufacturing. The alloys were cast into cylindrical blanks in graphite moulds and machined on a lathe into disks of various size and thickness to account for tonal difference due to shape (See Table 3). We could not machine disks for composition C due to equipment failures. Cold working was performed using a hammer and anvil to harden select disks of each alloy following a proportional reduction in thickness and increase in diameter of each disk to ensure uniformity. Disks were suspended by monofilament wire, struck with a hardened steel striker, and recorded using a microphone. Despite a large sample set, we only examined the set of 25mm disks due to time constraints.
Outside Diameter | Thickness |
20mm | 0.5mm |
25mm | 1mm |
30mm | 1.5mm |
2mm |
Table 3. Disk Sizing. Size and thickness range of disks that were created for sound testing. Disk measurements are rarely provided in studies of sistra, so a range of each value was chosen.
Sound effects
The results, shown in Figure 17, show changes due to both chemical composition and material hardness. Material chemistry had the largest effect on sound. The standard phosphor bronze and silver bronze (A) produced a continuous, audible high pitch while the leaded bronze (B) was dull and muted, suggesting this alloy is less likely to be used in sounding elements. The phosphor bronze standard had the highest peak magnitude of the alloys until it was work hardened. We found that work hardening increased frequency and magnitude of the A samples by 20% and 12.6%, respectively, compared to the as-cast samples. The leaded (B) samples, likely due to the high lead content, did not work evenly and suffered from stress cracking. Pitch increased only slightly in the B samples. In the phosphor bronze standard, these numbers decreased despite an increase in hardness. More investigations are needed to inform this outcome, but the results remain clear: hardness affects sound. It is therefore likely that ancient smiths could have opted for a specific tone in their instruments by manipulating their materials; however, to truly confirm this suspicion, technical analysis of known sistra is required.
Other Implications
Metallography of select samples from compositions A, B, and the phosphor bronze was done. We observed evidence of banding in the work hardened samples. Study of known sistra disks that exhibit banded microstructures would indicate that the disks were likely work hardened as an intentional step in the manufacture of these instruments.
Conclusions
Perhaps metal workingâs intimate engagement with the divine is what caused the Egyptians to shroud it in secrecy, accessible only through cryptographic texts and imagery. Or perhaps the restricted knowledge has its roots in copperâs connection with the power to transform. Or a combination of the two, but this clear control of craft specialization has the unique effect of steeping the material and the process in a cosmic, enigmatic secret. In part due to this mystery, the sistrumâs affective power resides just as much in the process of production as in the final, physical object and its ability to produce sound and function in a ritual context.
Yet, the knowledge was also available, albeit highly coded, and easily understood by those who worked intimately with the material and with the sun god himself. More inclusive and wide-ranging studies of sistra could reveal more ways in which the smiths manipulated their materials to achieve a desired effect while also becoming entwined in the process itself. We should see copper working as an animating process. It is the agency of fire which acts upon the raw material in its crucible, and which nurtures the foetal Re in Hathorâs womb. When this metal is controlled and when it, like the raging goddess herself, is pacified we see what can best be summarized as a divine transmutation of nature.
This experiment ultimately suggests that more than one method was necessary in the production of an ancient Egyptian sistrum. Our later work also indicates that changes to alloy and mechanical properties could impact the sound made by sistra. The processes require practice and understanding of the materials, which may account for some of our failures, although in some cases, such as in casting the disks, the results indicate that the process we selected was unlikely to have been applied in ancient times. Later work also clarified the workability of cast disks; some compositions worked easier than others. We noted that the alloys that worked well also performed best musically, while the alloy that broke during cold working performed poorly musically. The sound a sistrum makes may be intentionally changed by adjusting the alloy. The silver bronze alloy followed a chemical composition of sounding disks from a sistrum while the leaded alloy was based on a chemical composition from a handle only, suggesting that different parts could be made with different alloys as necessary. We noted many difficulties working with the cross pins. The steps to manufacture these remains somewhat unexplained given their slender appearance and finely worked ends, so future experiments should be done to provide answers.
Acknowledgements
The research into the sound qualities of different alloys was funded as part of author Benjamin Doddyâs Hauber Research Fellowship at Loyola University Maryland in summer 2021 and conducted with support of Loyola Materials Engineering faculty mentors Dr. Robert Pond, who supported research, metallography, and hardness studies, Dr. Yanko Kranov, who provided the machining and supported experimental design and material sourcing, Dr. Suzanne Keilson, who supported audio-spectral analysis and access to audio analysis programming, and prepared the spectral analysis plots in Figure 17. Emily Chambers, an assistant research engineer at Johns Hopkins University, provided microscope access and documented the micrographs for the project. Figures 3 & 14 were prepared by author Chelsea Kaufman, a PhD candidate in Egyptian Art and Archaeology at Johns Hopkins University.
- 1The earliest textual references to this goddess appear in the fourth dynasty on the façade of Khafreâs valley temple and priestesses of Hathor are attested to by the reign of Menkaure. During this time, Hathor also takes on her identity as âmistress of the sycamore in all her places.â (Robyn A. Gillam, âPriestesses of Hathor: Their Function, Decline and Disappearance,â Journal of the American Research Centre in Egypt 32 (1995): 215. http://www.jstor.org/stable/40000840.)
- 2The title âShe who exalts with her two facesâ Hknt m Hr snw=s snw which appears in the Pyramid Texts is a likely reference to Hathor (Sethe, Die Altaegyptischen Pyramidentexte, Band I, Spruch 234).
- 3As in the story of Sinuhe, âson of the Sycamore (Hathor)â s3 náž„.t, where he is welcomed into the pharaohâs court with a hymnic performance by the royal women personating Hathor, shaking sistra, and wearing menat necklaces (Manassa 2011, 152-153; Lichtheim 1976, 232) a literary allusion to being welcomed onto the solar barque after death with the pharaoh himself acting the part of Re (Gillam 1995, 217). Sound in Egyptian literature also signals divine presence and intervention as in the Shipwrecked Sailor where the sound of the approaching serpent is described as a âthunderingâ (Lichtheim 1976, 212). In both stories, the sound appears out of place and as such disrupts oneâs sense of space and indeed these sounds occur at moments of change in the stories.
- 4Bj3 is sometimes also translated as âironâ or âferrous metal.â The dual identification may stem from the co-occurrence of iron and copper in ores, especially those sources from the Sinai. Of the two, copper was the more popular throughout Egyptian history. For a more thorough discussion, see Harris âLexicographical Studies,â 60-62.
- 5For a Late Period example of an in-tact lost-wax mould, see AuenmĂŒller, Verly & Rademakers âBronze Casting Artefacts from the Qubbet el-Hawa â Moulds, Materials, and Experimental Methods,â 144.
- 6For a detailed description of the use of oil-bonded sand in cope and drag moulds, see Heine, Loper, & Rosenthal, Principles of Metal Casting, pp. 26-29.
- 7For some compositional references, see: Garland (1927); Soles and Giumlia-Mair (2011).
Country
- Egypt
Bibliography
Rattle, Sistrum - 54-33-5 a, , Penn Museum, Philadelphia.
Sistrum Handle with the Head of Hathor 2001.212 b, , Harvard Art Museums.
Sistrum of the Chantress Tapenu c, The Metropolitan Museum of Art, New York.
Sistrum, 1949.106.A-C d, , Harvard Art Museums, Boston.
AuenmĂŒller, J., Verly, G. and Rademakers, F. 2019 Bronze Casting Artefacts from the Qubbet el-Hawa - Moulds, Materials, and Experimental Methodsâ, in G. Verly, F.W. Rademakers and F. TĂ©reygeol, eds. Studies in Experimental Archaeometallurgy: Methodological Approaches from Non-Ferrous Metallurgies. Editions Mergoil.
Craddock, P.T. 2000 From Hearth to Furnace: Evidences for the earliest metal smelting technologies in the Eastern MediterraneanPaleÌorient, vol. 26, no. 2, pp.151-165.
Daumas, F. 1983). L'alchimie a-t-elle une origine Ăgyptienne, in G. Grimm, H. Heinen and E. Winter, eds. Das Römisch-Byzantinische Ăgypten: Akten des Internationalen Symposium 26-30 September 1978 in Trier. Mainz am Rhein: P. von Zabern, pp.109-118.
Davey, C. J. 2012 Old Kingdom Metallurgy in Memphite Tomb ImagesAncient Memphis: "enduring is the perfection". Proceedings of the international conference held at Macquarie University, Sydney 14-15.8.2008, pp.85-107.
Davey, C. J. and Edwards, W. I. 2007 Crucibles from the Bronze Age of Egypt, Proceedings of the Royal Society of Victoria, 120(1), pp.148-156.
Davies, N. d. G., 1943. The tomb of Rekh-mi-RÄ at Thebes. New York: Metropolitan Museum of Art.
Derchain, P. 1965 Le Papyrus Salt 825 (B.M. 0051), rituel pour la conservation de la vie en Ăgypte. Bruxelles: Palais des AcadĂ©mies.
Duell, P. 1938The Mastaba of Mereruka. Chicago: Univ. of Chicago Press.
Erman, A. and Grapow, H. 1961Wörterbuch der aegyptischen Sprache, 3 unverÀnderter Neudruck. Berlin: Akademie-Verlag.
Finnestad, R.B. 1999 Enjoying the Pleasures of Sensation, in E. Teeter, and J.A. Larson, eds., Gold of Praise: Studies on Ancient Egypt in Honor of Edward F. Wente. Chicago: The University of Chicago, pp.111-119.
Garland, H. and Bannister, C. O. 1927Ancient Egyptian Metallurgy. London: Griffin.
Gillam, R.A. 1995 Priestesses of Hathor: Their Function, Decline and Disappearance Journal of the American Research Center in Egypt, vol. 32, pp.211-237.
Grapow, H. 1917Religiöse Urkunden. Leipzig: J.C. Hinrichs.
Harris, J. R. 1961Lexicographical Studies in Ancient Egyptian Minerals. Berlin: Akademie Verlag.
Hassan, S., JÄmiÊ»at FuÊŒÄd al-Awwal and Egypt1932Excavations at GĂźza. Oxford: University Press by J. Johnson.
Hauptmann, A., Laschimke, R. and Burger, M. 2016. On the Making of Copper Oxhide Ingots: evidence from metallography and casting experiments Archaeological and Anthropological Sciences, vol. 8, no. 4, pp.751-761.
Heine, R. W., Loper, C. R. and Rosenthal, P. C. 1967Principles of Metal Casting, 2. ed., New York: McGraw Hill.
Kritsky, G. 2015 The Tears of Re: Beekeeping in Ancient Egypt. Oxford: Oxford University Press, Incorporated, New York.
Lalouette, C. 1979 Le firmament de cuivre. Contribution à l'étude du mot bi3.Bulletin de l'Institut Français d'Archéologie Orientale Le Caire, vol. 79, pp.333-353.
Leitz, C. 2002a Lexikon der Àgyptischen Götter und Götterbezeichnungen. Leuven: Peeters.
Leitz, C. 2002bLexikon der Àgyptischen Götter und Götterbezeichnungen. Band V. Leuven: Peeters.
Lichtheim, M. 1976Ancient Egyptian Literature. Berkeley: University of California Press.
Lucas, A. and Harris, J. R. 1962Ancient Egyptian Materials and Industries, 4th ed., rev. and enlarged edition. London: Arnold.
Manassa, C. 2011 Soundscapes in Ancient Egyptian Literature and Religion in E. Meyer-Dietrich, edLaut und Leise: Der Gebrauch von Stimme und Klang in historischen Kulturen. Bielefeld: Transcript Verlag, pp.147-172.
Noble, J. V. 1975. The Wax of the Lost Wax Proces. American Journal of Archaeology, vol. 79, no. 4 pp.368-369.
Ogden, J. 2000. Metals in P.T. Nicholson and I. Shaw, eds. Ancient Egyptian Materials and Technology. Cambridge: Cambridge University Press, pp.148-176.
Pinch, G. 1982 Offerings to HathorFolklore (London), vol. 93, no. 2, pp.138-150.
Rice, P.M. 2015Pottery Analysis, 2. ed. Edition. Chicago: University of Chicago Press.
Roberts, A.M. 2019 Hathorâs Alchemy: The Ancient Roots of the Hermetic Art. East Sussex: North Gate.
Rosmorduc, S., 2014. JSesh Documentation. [online] Available at < http://jseshdoc.qenherkhopeshef.org > [Accessed 24 November 2022]
Scheel, B. 1989 Egyptian Metalworking and Tools, 1. publ. edition, Aylesbury: Shire Publications.
Sethe, K. 1908Die Altaegyptischen Pyramidentexte Pyramidentexte nach den Papierabdrucken und Photographien des Berliner Museums. Leipzig: J.C. Hinrichs'sche Buchhandlung.
Soles, J. S. and Giumlia-Mair, A. 2011. The Mochlos Sistrum and Its Origins in: P.P. Betancourt and S.C. Ferrence, eds. Metallurgy: Understanding How, Learning Why: Studies in Honor of James D. Muhly. Philadelphia: INSTAP Academic Press, pp.133-148.
Weinstein, J. 1974 A Fifth Dynasty Reference to AnnealingJournal of the American Research Center in Egypt, vol. 11, pp.23-25.