The content is published under a Creative Commons Attribution Non-Commercial 4.0 License.
Reviewed Article:
Scandinavian Arrowheads of the Viking Age, Their Manufacture and Distribution
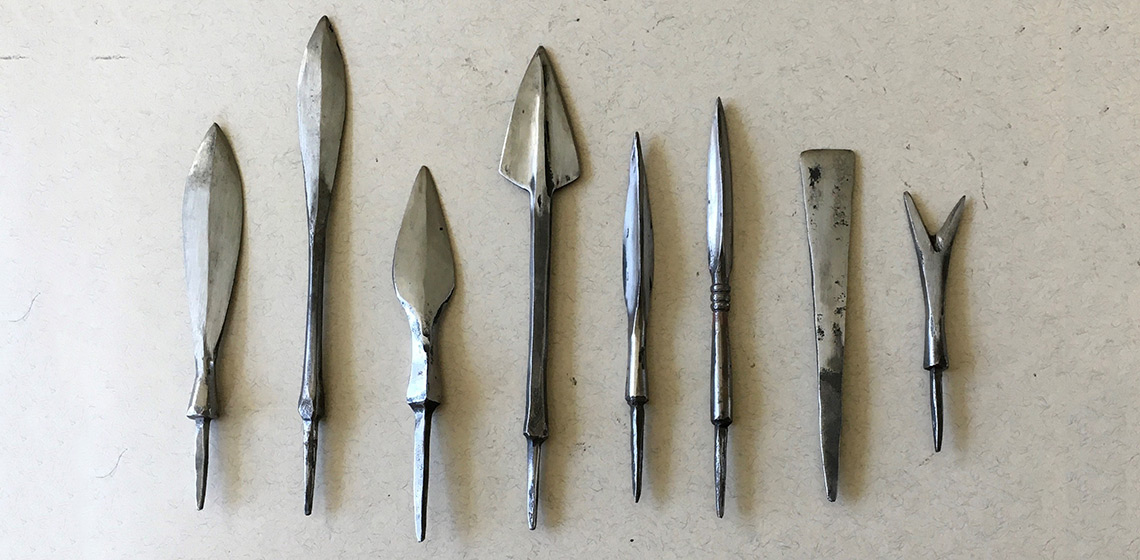
In recent years there has been a renewed interest in the arrowheads used in the Viking Age and their distribution. The 187 excavation of Viking graves in the Black Earth of Birka region of Sweden, re-examined in 2019 by Price (Price, et al., 2019) and the finding of arrows and arrowheads where glaciers have melted in Norway, prompted my research into the forging techniques of specific arrowheads from these finds, along with Viking arrowheads found in settlements in Ireland.
Introduction
In 1971 Erik Wegraeus (1973) wrote a paper on Swedish Viking period arrowheads covering their types, distribution, and functions. Wegraeus classified eight main arrowhead types in Sweden. A1, A2, B, C, D1, D2, E1 and E2, with the most popular being the A1, A2 and D1 heads (See Figure 1).
The A1 head is a general-purpose leaf shaped head for hunting and if necessary, war. The A2, D1, and D2 types are long, narrow bladed war heads of diamond or triangular section that would penetrate mail. The B type head is in general a wide-bladed triangular hunting head and the C type heads are long, multi-bladed heads with the blades set at right angles to each other. The E1 and E2 types are hunting heads. The E1 is a chisel head and can be round, square, or flat tanged. The E2 is a forked head with the fork being shallow or deep. A1 and E2 hunting heads have been found in Norway. These heads have been found where glaciers have melted in recent years due to global warming. It was traditional to hunt in the snow on these glacial areas and complete arrows that were lost in the snow are now being discovered in excellent condition.
Erik Wegraeus’ (1973) research was developed further by Peter Lindbom (1994) on arrowheads from the boat-graves in the county of Uppland in Sweden. During his research, Peter commissioned me to manufacture reproductions of the arrowheads from these boat graves, with reference to the D1 type war head with decorative rings on the shank of the arrowhead. This head proved quite a challenge to forge as it not only has the three rings on the shaft but is also a triangular section head. Triangular section heads were also forged in the Roman period and there is a good example of one in the British Museum. The British Museum head is a three bladed trilobed head that makes it even more complicated to forge. Larger versions of this type of head have been found in Norway and Ireland.
Arrowhead forging methodology
When forging any historic arrowhead there are certain criteria to be considered. In general, they are as follows: -
- What was the material used to forge the head?
- What was the section of the material they would have used?
- How long it took the original smiths to forge the head?
- The dimensions of the original.
- The equipment used to forge the head.
The material used to forge arrowheads in the Norse period was mainly bloomery iron. This could be Phosphoric or non-Phosphoric iron. There are instances where medium carbon iron containing around 0.5% carbon was used on hunting heads to give hard cutting edges to the blade. This allowed it to be sharpened and keep its edge.
Phosphoric iron gives a harder surface to the blade and point than non-Phosphoric iron.
There is some debate as to what shape and section of material the smith would have started with. If the smiths were smelting their own iron then they would have started with the bloom of iron from the smelting furnace. The smith would then refine the bloom down into a billet and finally forge the billet into the correct section rod for making a particular arrowhead. From experiments carried out this process would result in a loss of at least 50% of the material weight of the bloom. The material section for forging the heads would have been square or flat depending on the type of head being forged. Round section bar would not have been used. When forging bars to the section required, the making of the bar into a round section is the final process. For arrow smithing this is an unnecessary use of time, fuel and effort.
If the smith received his iron from the smelters it would be in the form of a billet. The billet could be rectangular or square section tapering at both ends, or long rectangular section strips often referred to as “currency bars”. This billet would be forged down to the required section and size by the smith to make the arrowhead. Most of the narrow-bladed Viking heads that I have forge have been forged from 6 mm square section bar. Some of the broader bladed heads would be forged from rectangular section bar 12 mm by 3 mm section.
The dimensions of the original head to be replicated can be obtained in various ways in order of preference:
- Personally, taking the dimensions from the original.
- Working from an accurate archaeological drawing.
- Scaling up from a photograph of the original that has a scale in the photograph.
The basic tools of the smith have changed very little over the centuries that man has been working hot iron.
The basic tools are as follows: -
- The hearth to contain the fire and bellows to supply the air to keep the fire hot enough to heat up the iron.
- The anvil on which to hammer the hot iron into the required shape.
- The hammer for hammering the hot iron.
- Tongs to hold short lengths of bar that are too short to hold in the hand when heating and working the iron.
- Chisels and punches for cutting and marking the iron.
Tools of a more specialist nature would be made by the smith as and when he needed them. For the forging of the Birka head, special tools had to be made for forging the triangular section of the head and for forging the three rings on the shank of the head. The tools I made to form these particular sections of the head are well within the capabilities of the smiths of that period.
Norse arrowheads
The arrowheads of the Norse/Viking period were fitted to the shafts by tangs or sockets. Most of the early heads were of the tanged variety with the tang being approximately thirty millimetres long and round or square taper in section. This length of tang gives an optimum size for fitting heads into wooden shafts that must be drilled to take the tang. The end of the shaft was bound with silver or copper wire, thread, or sinew depending on the status of the person the arrows were being made for. The tang of the head was then driven into the end of the shaft. Done this way there is less chance of splitting the shaft and the binding is tightened as the tang is driven into the end of the shaft. The binding is then coated with resin or glue or wrapped in glued Birch bark to keep it secure. Some of the heads had a flat tang that required making a slot in the end of the shaft that would take the tang. The same method of fitting was used as described above. The tangs on the heads are quicker to forge than sockets and use less material. There is also less chance of the head snapping off the shaft than with socketed heads.
Socketed heads became more frequent in the later part of the period when there was a more plentiful supply of iron and bows became more powerful. Some of the early period sockets were forged as open sockets, as opposed to the closed sockets of the early and late medieval period. With the closed socket, the socket edges are overlapped to give more strength and prevent the socket opening when the arrow struck. It is also easier to square off the ends of the closed socket to give a better fit onto the shaft.
(See Figures 2 and 3)
The Black Earth of Birka arrowheads
These particular arrowheads were peculiar to this area of Scandinavia in the 10th century. Many of the heads have been found in graves along with swords, seax, axe, bows and horse equipment.
The arrowhead that I re-produced came from a grave that contained a female warrior and all her equipment including a re-curve bow and a quiver full of arrows.
Forging the Birka arrowhead
The Birka arrowhead is classified as a D1 type but has three raised rings on the shank of the head. It is a triangular section head with grooves on each face. As a war head it is a complicated head to forge being triangular in section and having the rings forged and file finished on the shank of the head. This means that it takes at least 20 minutes to forge and ten minutes to finish each head. This is rather a long time to forge a war head as they were forged in large quantities. It would take around seven minutes to forge the standard warhead and three minutes to grind, harden and finish it (See Figure 4)
The three rings on the Birka head serve no practical purpose as far as the efficiency of the head is concerned so are purely a decorative feature. To forge the three rings a special top and bottom tool was made that would give the correct size and shape of the rings. With this tool the rings can be forged quickly in one heat but need some tidying up with a file afterwards.
The triangular section blade also needs special tooling to achieve the correct section and the grooves on each face. The section of material needed to forge this arrowhead heads is 6 mm square.
Stages of forging the head
The end of the bar is forged to a square point. The start of the rings is marked allowing for stretching of the material and the general shape of the blade is then forged in square section. This square section is then forged into a triangular section and the grooves forged into the three faces. The grooves can be forged using a special top and bottom tool or with a chisel having the head supported in a groove that is the correct angle and depth. The lower half of the shank is then forged to the correct taper and section and the ring section is rounded up prior to forging the rings in the top and bottom tool. The shoulder of the shank is then forged to the correct depth to allow the tang to be forged. The tang is of a round taper section approximately 25 mm long. This is the average length of tangs on most of the Norse arrowheads, as it would be time consuming to drill a deeper hole in the end of the wooden shaft to fit the tang of the head into. Many of the Norse period arrow heads had square section tangs as they are quicker to forge than round section ones. The tangs are left as forged with little or no filing up, but the shoulders are squared up with a file to give a good seating on the end of the shaft. The shaft would be drilled to the correct diameter and depth and the head fitted into the hole. The end of the shaft would then be tapered down to the shoulder diameter of the arrowhead. The Birka heads were bound onto the shaft with fine silver wire. This seems to indicate that arrows were made for a person of high status and, though of a typical war head style, were possibly not intended to be used in a battle situation, bearing in mind the skill, time and materials used to forge the heads and bind them to the shafts.
(See Figures 5, 6 and 7)
For Stages of forging the Birka arrow head see Figures 8-17
Arrowhead Types | Forging time | Finisidng time | Number of heats | Total time |
A1 Leaf or diamond shape tanged hunting head. | 15 minutes | 7 minutes | 8 | 22 minutes |
A2 Leaf or diamond shape long shank tanged hunting head | 18 minutes | 6 minutes | 10 | 24 minutes |
D1 Plain triangular section war head short shank | 16 minutes | 5 minutes | 14 | 21 minutes |
D2 Diamond shaped tanged long shank warhead | 7 minutes | 3 minutes | 8 | 10 minutes |
E1 Chisel ended tanged hunting head | 6 minutes | 3 minutes | 7 | 9 minutes |
E2 Flat forked ended tanged hunting head | 7 minutes | 3 minutes | 8 | 10 minutes |
3FLUTED Long wide three fluted tangedhead | 20 minutes | 6 minutes | 16 | 26 minutes |
BIRKA Tanged triangular grooved long shank war head with three raised rings on shank | 20 minutes | 10 minutes | 15 | 30 minutes |
Table 1. Forging times for Swedish/Norse arrowheads. All times are averages for the heads being forged. Based on work carried out in 2019. Author H.Cole
The amount of time taken to forge a head depends on the type of head being manufactured. This can vary from between five minutes to 45 minutes. The average time for forging a war bodkin or leaf shaped hunting head is seven minutes. Usually it is the large, barbed hunting heads that take the longest time to forge due to their complex construction. (See arrowhead forging chart). The finishing of the heads would have been done by grinding or filing to shape. The blade can easily be finished by grinding but the finishing of the three raised rings on the shank of the Birka heads is better done with a file. The heads were fitted onto the shafts in two ways either socketed or tanged. Some of the early Norse heads, around 600AD, were socketed but the sockets were not fully closed on most of them, compared to the medieval period when the sockets were fully closed and overlapped to stop them opening out on impact, due to the power of the bows that were being used at that time. The tanged head became the most popular method of fitting the heads in the Viking age and remained so until the early Medieval period when the closed socket became standard for arrowheads in Western Europe.
If any heat treatment was carried out to the blade it would be done by heating the head up to a bright yellow heat and then quenching it in water. If this heating is done in a charcoal fire the iron absorbs some carbon into its surface sufficient to produce a hard surface or point when the head is quenched
Viking arowheads found in other countries
These two antler heads were found in an eleventh century farmhouse in Greenland excavated by C. L. Vebaek in 1958 (Vebaek, 1961). They are typical A1 diamond shape Norse heads of the period (See Figure 18).
The Irish connection
Many arrowheads have been found in the numerous Viking settlements in Ireland along with swords and spears from this period. Many of them were socketed needle bodkin types of various lengths and others were tanged, double bladed heads, with the blades set at right angles to each other. It is interesting to note that some of the spear heads with sockets were also double or even triple bladed.
(See Figures 19, 20 and 21)
Viking arrowheads found in Dublin
A large number of arrowheads have been excavated from sites in and around Dublin and have been recorded and drawn by Andrew Halpin (2008).
My research into Norse arrowheads has resulted in me forging archaeological reproductions of a number of these heads. All the leaf shaped heads from the Dublin sites conform in general to those of the same period found in Scandinavia as would be expected as the occupants came from that area.
The majority of the Norse heads were fitted to the shafts by inserting a tang into the end of the shaft and binding it in with thread or wire. Some of the heads had flat tangs that were fitted into a slot in the end of the shaft and then bound on in the same way as the square or round section tangs. From a practical point of view the tang is quicker to forge than a socket, especially the flat tang, and more important at that time, uses less material that a socket. A disadvantage of the tang is that it takes longer to fit onto the shaft than a socket and requires a drill to make the hole in the end of the shaft. When fitting a socketed head all you need is a sharp knife and some glue to fix the head onto the shaft. It is interesting that the needle bodkins have sockets though they are crudely forged compared to the sockets of medieval arrows.
When conducting research forging of artefacts, a record is kept of the making of the item in question. I was asked to forge some of the Dublin heads by Derek Gallagher who is conducting private research in this field. I recorded the forging process of one of the heads he required.
Forging record for the Dublin DWP69 arrowhead
The results are as follows for forging the leaf shaped head DWP69. This is the longer of the three heads.
- Material used: - Low carbon iron. 55 mm x 6 mm x 6 mm per head.
- Number of heats required: - 12.
- Forging time: - 14 minutes.
- Grinding and finishing time: - four minutes.
- Total average time per head 18 minutes.
For Forging the Dublin arrowhead see Figures 22-33
English Viking arrowheads
The most complete collection of Viking arrowheads found in England are from the Coppergate excavations in York. There are 25 arrowheads found on the site that fall into the Viking period with one other that could possibly belong to this period.
Many of the heads are tanged leaf shaped type A1. Four are socketed D1warheads and two are tanged A2 type hunting heads. A metallographic cross section of one of the heads shows it to be of sandwich construction with a medium carbon iron core between two pieces of low carbon iron. However, there is no evidence of any heat treatment being carried out on this head, but it has been cold worked to try and increase the hardness of the cutting edge.
The number of known Viking arrowheads found throughout the country are few and far between.
For Viking and Early English arrowheads of the period found in the Thames see Figures 34-37.
London Museum arrowhead type | Description All heads are 3/8"socketed unless otherwise stated | Forging time | Grinding and finishing time | Heats | Total time | Material section (mm) |
Type 1 | Early medieval kite head diamond cross section. | 11 minutes | 4 minutes | 12 | 15 minutes | 12 x 3 |
Type 2 | Early medieval triangular head diamond cross section. | 12 minutes | 5 minutes | 14 | 17 minutes | 12 x 3 |
Type 3 | Early medieval triangular plain or barbed head. Long shanked | 15 minutes | 4 minutes | 15 | 19 minutes | 12 x 5 |
Type 5 | Conical head | 6 minutes | 3 minutes | 6 | 9 minutes | 8 x 8 |
Type 6 | Forked hunting head. | 10 minutes | 5 minutes | 12 | 15 minutes | 12 x 6 |
Type 7 | Diamond section needle war bodkin. | 7 minutes | 3 minutes | 9 | 10 minutes | 6 x 6 |
Type 9 | Diamond section war bodkin with shoulders to socket | 7 minutes | 4 minutes | 7 | 11 minutes | 8 x 8 |
Type 10 (short) | Diamond section war bodkin. | 6 minutes | 3 minutes | 7 | 9 minutes | 8 x 8 |
Type 10 (long) | Diamond section war bodkin | 7 minutes | 3 minutes | 7 | 10 minutes | 8 x 8 |
Type 10 (heavy) | Diamond section war bodkin | 9 minutes | 5 minutes | 9 | 14 minutes | 10 x 10 |
Type 12 | Triangular section shouldered war bodkin | 8 minutes | 4 minutes | 11 | 12 minutes | 8 x 8 |
Type 13 | Diamond section triangular barbed head long shank | 15 minutes | 5 minutes | 13 | 20 minutes | 15 x 3 |
Type 14 | Large curved broadhead with raised centre rib | 30 minutes | 8 minutes | 28 | 38 minutes | 20 x 6 |
Type 15 (Devizes) | Long barbed curved broadhead diamond section | 26 minutes | 7 minutes | 24 | 33 minutes | 15 x 5 |
Type 16 | Diamond section barbed war head. Welded barbs | 15 minutes | 7 minutes | 15 | 22 minutes | 8 x 8 socket 4 x 4 barbs |
Tudor | Conical head with integral cutting edges | 6 minutes | 3 minutes | 8 | 9 minutes | 8 x 8 |
Curved broadhead | Diamond section broadhead with barbs to end of socket | 21 minutes | 5 minutes | 17 | 26 minutes | 15 x 5 |
Straight broadhead | Diamond section broadhead with barbs to end of socket | 21 minutes | 5 minutes | 17 | 26 minutes | 15 x 5 |
Table 2. Medieval arrowhead data chart. All times are average for forging individual heads from start to finish. Author H.Cole
Acknowledgements
Peter Lindbom for his help and research paper on the Birka arrowheads.
National Museum of Ireland, Dublin for photographs of the Viking arrowheads.
Swedish History Museum, Stockholm for photographs of the Birka finds.
Keywords
Country
- Ireland
- Norway
Bibliography
Halpin, A., 2008. Weapons and warfare in Viking and Medieval Dublin. National Museum of Ireland Medieval Dublin Excavations 1962–81, Ser. B, vol. 9
Lindbom, P., 1994. Pilspetsar fran de Upplandska batgravfalten. CD-uppsats i arkeologi. Uppsala Universitet Ht 1993
Price, N., Hedenstierna-Jonson, C., Zachrisson, T., Kjellström, A., Storå, J., Krzewińska, M., Günther, T., Sobrado, V., Jakobsson, M. and Götherström, A., 2019. Viking warrior women? Reassessing Birka chamber grave Bj.581. Antiquity. Cambridge University Press, 93(367), pp. 181–198. doi: 10.15184/aqy.2018.258.
Vebaek, C.I., 1961. An Eleventh-Century Farmhouse in the Norse Colonies in Greenland. In: A. Small, ed. 1961. The Fourth Viking Congress. Edinburgh, pp.112-118.
Wegraeus, E., 1973. Pilspetsar under vikingatid. TOR XV, 1972-1973, pp. 191-208.