The content is published under a Creative Commons Attribution Non-Commercial 4.0 License.
Reviewed Article:
Casting a Copper Age Axe Using a Replica of the Marl Mould Found in Baffoni Cave (AN)
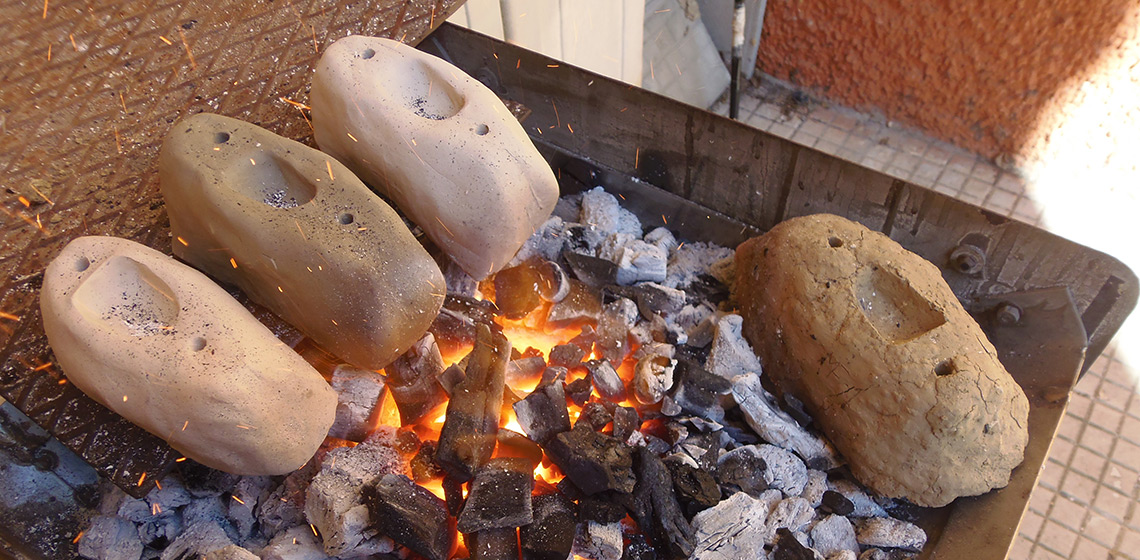
The Baffoni Cave is a cavern that lies in the Genga territory, in the province of Ancona, Italy. It is part of a complex of caves, the most famous of which are the Frasassi Caves. The whole territory is rich in archaeological features, with the most ancient specimen found within the Genga territory being a flint biface dating to the Lower Palaeolithic (Montanari and Pignocchi, 2022, p. 125). In 1952-1954, an archaeological expedition led by Dr Antonio Mario Radmilli searched the Baffoni Cave. Among the other specimens, three objects caught the attention of the scholar: a sandstone with signs of use, a bronze dagger and what initially appeared to be a clay mould for making unidentified metal objects.
These three artefacts suggested that some kind of metal working had most probably been carried out in the cave: Radmilli first described the mould as “a clay mould for casting… containing a piece of copper” (Radmilli, 1956, pp. 523-533), but no further analysis on them have been carried out until December 2020.1
At this time, Dr Gaia Pignocchi was reviewing Radmilli's excavation and these three specimens in particular. The author was experimenting with replicating bronze objects found in other Genga caves and Dr Pignocchi contacted him to ask his opinion on the Baffoni mould.
After an initial examination of the mould, the author found that it had been modelled by hand and that the central hollow was done by pressing a thumb on the wet clay (See Figure 1). A suspension hole survived and was showing traces of wear due to the sliding of a small rope, which suggested that the mould was either hung when not in use or designed to be carried from one place to another.
Considering this feature and assuming that the thumb itself could be a unit of measure, the author suggested that the mould could have been used by an itinerant metal worker to cast ingots, either from raw minerals or by recycling discarded, or broken, items.
Some tiny metal spheres were visible, stuck in the mould’s surface (See Figure 2). The fragments of some of these were sent to Dr Marcello Cabibbo of the University of Engineering of Ancona for a metallographic analysis. The result showed very high copper content (maximum 92%) with a high percentage of zinc (8-12%) and smaller percentages of silver (0.5%) (Pignocchi, Cabibbo, Fiorentini and Montanari, 2022, pp. 33-38). This led Dr Pignocchi, Dr Fiorentini and Dr Cabibbo to assume that the mould was used to refine copper from a tennantite tetrahedrite mineral, such as Fahlerz. The latter is a copper antimony sulphide, composed of crystals and clusters resembling pyramids. Steel gray to black in color, it may also be iridescent with a colourful metallic film or with a slightly bronze color. In addition to the metallographic analysis, a fragment of the mould was sent to the geological laboratory of Dr Orestina Francioni for a lithic analysis that would help determine the exact litothype.
The result of this analysis was surprising - the mould was not made of clay but rather of marl, something that neither the author nor the other scholars involved in the research had ever heard of before, and of which they still are not aware of other comparisons. Additionally, the lithic analysis showed that the mould was heated at the quite low temperature of about 400°C, much lower than expected for a mould that has to sustain thermal shocks (Francioni, 2022).
The impact of this on further experiments will be discussed below.
First experiments on replicating the mould using soil and commercial clay
Before obtaining the results of the latter analysis, however, an experimental project was carried out. The objective was to recreate multiple clay moulds and pour molten copper in them to see which kind of metal objects could be obtained.
It was decided to make four moulds. One (MF-1) would be made using soil picked from a field, another (MF-2) using commercial red clay and two using commercial white clay (MF-3 and MF-4). Both the red and white clay were imported from Tuscany. All four would be modelled by hand when wet, and the hollows would be formed by pressing the thumb in the clay. The four moulds and hollows would be polished using fingers (See Figures 3 and 4).
Since there was nothing that could help determining either measurement or shape when the specimen was intact, it was decided to try to recreate the hollows as similarly as possible to what remains of the original one. This process was empirical, since the hollows were formed by pushing the thumb on the wet clay and then polishing its walls with a bone awl. As a result, despite the care put during this operation, the hollows’ dimensions varied from each other. Only one of them had the exact measures than the original one, that is a length of 4.6 cm, width of 3.2 cm wide and a depth of 1.65 cm.2 The suspension holes were made by piercing the clay with a pointed wooden stick, and polished using a hand-held flint blade knapped for the occasion (See Figure 5).
The moulds, and the replica of the Bronze Age clay crucible found at Moscosi di Cingoli (see below), were left to dry for 45 days (See Figure 6). They were fired using a manual forge and commercial charcoal, thus trying to replicate an open pit oven such as the ones attested in the Neolithic – Copper Age (Pignocchi, 1999, pp. 13-15) (See Figure 7).
During this experiment, mould MF-4 broke and mould MF-3 vitrified in a manner that prevented further use (See Figure 8). The firing of the remaining moulds and of the crucible were both successful. Using a laser thermoscope (model Axiomet AX-7540, set to record a maximum of 1.150 °C) the higher recorded temperature was 1.114 °C, and the average have been 465,31 °C for MF-1 and 755.5 °C for MF-2.
Replicating the bronze dagger and related experiments on sharpening it
A further experiment to replicate the bronze dagger found at Baffoni Cave was conducted. Two clay bricks were used as moulds with the negatives of the dagger being carved using a steel chisel (See Figure 9). Three castings were carried out, using an alloy of 90% copper + 10% zinc.3 The casting was done using an electric furnace model MF-3000 (See Video below). This resulted in three daggers, B-1, B-2 and B-3. Dagger B-1 was extracted from the mould and left untouched, B-2 was partially worked removing the excess of bronze and shaping the blade and edges with a whetstone, and B-3 went through the same process and more. It ended up as the finished product, polished with the same whetstone and then hafted (See Figure 10). It is worth noting that all three daggers were of the same weight – 99 g - immediately after casting and before being cold worked.
The sandstone found in the cave shows some traces of wear that made scholars identify it as a sharpener (Lucentini, 1997, p. 47, n. 11). A whetstone with grain similar to the specimen has then been chosen to test this hypothesis and used to polish and sharpen daggers B-2 and B-3. The wear traces between this whetstone and the specimen have then been compared. Using the whetstone against blades made of bronze left a subtle layer of golden metallic dust on its surface (See Figure 11), a data that might be useful in case of further analysis on the specimen. This presents a deep groove that seems to be the result of a prolonged rubbing of a blade against the stone. Such a feature has not been replicated during the experiment. This can be due to various factors, such as the different duration of use of each sharpener or different inclination of the blades on the stones.
Casting copper in the moulds using an electric furnace: first comparative results
The two remaining moulds were used for 10 further castings, five per mould using the electric furnace. The results are of particular interest because the ingot’s average weights for MF-1 was 97.6 g (See Figure 12) while it was of 99.2 grams for MF-2 (See Figure 13). This reinforced the hypothesis previously stated by the author, that the Baffoni mould could have been used to obtain ingots. Since these resulted of a quite precise weight (around 100 g each) it was now possible to propose that they could have been easily used as a starting base for creating alloys. In fact, starting from such a precise weight means that no difficult calculations would be required to determine how much of another metal had to be added to the copper ingot in order to obtain the desired alloy. The weight of these ingots even made them suitable for casting bronze daggers such as the one found in the cave.4
Another result worth mentioning is how these castings affected the moulds and the surfaces of their hollows. MF-2’s hollow proved to be less durable than MF-1’s, breaking in multiple parts and resulting almost unusable after just five castings (See Figure 014). On the other hand, MF-1 reacted much better to the thermal shocks, with its hollow showing little signs of wearing, suggesting that it could be used for some more castings. (See Figure 15).
Related to the above is the change in the colours within the hollows. Since the internal walls darkened more and more as the castings took place, the colour of the original specimen was reached at the end of the experiment (See Figure 16). Lastly, during the pouring process, some boiling has been recorded (See Video below), with drops of molten metal spreading on the moulds’ surface (See Figure 17). Once cooled, these drops were very similar to the ones seen on the specimen. Radmilli had identified the specimen as a “…clay mould for casting… containing a fragment of copper” (Radmilli, 1956, p. 528, figs. 3-7), and these two facts confirmed his identification.
After the end of these experiments an article was published by G. Pignocchi, F. Cabibbo, A. Montanari and M. Fiorentini on the online journal of the University of Bologna5 , as previously mentioned.
Replicating the moulds with different kinds of marl
Dr Montanari determined the exact lithotype and found that the same marl can be found in a region of Umbria, the so-called Schlier blocks, located a short distance from the town of Gubbio. He gave the author some examples of this marl and some of another marl type from the village of Apiro, in the region of Marche. Dr Montanari deemed the latter different from the archaeological specimen because of differences in the internal structure. The marl found near Gubbio contains the same specimen of fossil foraminifera that can be found in the specimen, while the marl from Apiro lacked this feature.
The author decided to employ both marls to recreate as many moulds as possible, because different marls may have different reactions when processed. Since the most difficult part of the previous experiment had proven to be recreating the exact replica of the hollow, this time particular care was put in recreating the hollow of the original. Help came again from the University of Engineering of Ancona, which created a 3D model of the mould and the hollow itself (See Figure 18). This was used as a further support to recreate exact replicas of the hollow.
In addition to the 3D model, Dr Pignocchi pressed two pieces of modelling clay (brand DAS) on the original hollow and gave them to the author. A first tentative replica of the mould was made by crushing the marl from Apiro into dust with a stone hammer and mixing it with water (See Figures 19 and 20). Given that this was the very first attempt ever in working with marl, the author focused in understanding the material’s characteristics; for this reason, the hollow was created by simply pressing a thumb in the surface and smoothing it with a bone awl (See Figure 21), as was already done with clay moulds. This mould was named MF MA-1. A second mould was done with the same marl and the same methods except for the hollow, on which the author focused his attention this time. This mould was named MF MA-2. While it was drying one of the two DAS pieces was forced into its upper face, thus creating an exact replica of the original hollow (See Figure 22). The DAS piece was destroyed while it was pulled out, and this first mould was then left to dry after smoothing the hollow with a finger.
Some days later a pair of subtle cracks were noticed departing from each side of mould MF MA-2 (See Figure 23). The risk of the mould splitting in two halves was high, so the decision was taken to pour lead in the hollow. Even if it was not perfectly dry, such decision was taken because only another DAS piece survived and it would have been too risky to use it for a second mould, given that the first DAS piece was destroyed. Pouring lead into the hollow of MF MA-2 would have produced a metal stamp that could be used in the future to make as many moulds as needed, each one with the exact replica of the original hollow. The lead was melted using a blowtorch and poured into the hollow in which an iron nail was kept suspended upright. This way, once the lead cooled, it could be pulled out easily using the iron nail as a handle (See Figure 24). This low-temperature casting did not damage mould MF MA-2, but the cracks later caused it to split in two halves.
The lead stamp which, when polished, looked similar to the second DAS stamp (See Figure 25), was then used to impress the hollow on six more moulds. Four of these were made using commercial fire-resistant clay imported from the region of Tuscany (these were named MF AR-1, MF AR-2, MF AR-3 and MF AR-4, shown in Figure 26), and two more were made with the Gubbio marl (these were named MF MAV-II and MF MAV-III, see Figs 27 and 28).
Considerable data were collected while working with marl. The marl from Apiro was formed of tiny greyish stones (similar to limestone) that were pulverized with a rock into fragments the size of table salt. The marl from Gubbio was naturally pulverised already, its consistency being the same as flour, and it was greenish in colour. In both cases two methods have been tried to add water. The first consisted in filling a 3 l cooking pot for one third of its depth and then putting 5 chunks of marl, total weight of 450 g in, letting them dissolve. The second was that the marls were put in another 3 l cooking pot and water was slowly added, mixing the paste by hand until it reached a ductile consistency, adding water or marl dust if deemed necessary.
The first method did not give any appreciable results as the quantity of water, approximately 1 l, proved to be too much. It was impossible to shape the resulting wet mud into a mould and two such experiments had to be aborted (See Figure 29). The second method was much more satisfying and led to the creation of the four marl moulds cited above. The seven intact moulds (that is, MF MA-1 with Apiro marl, MF AR-1, MF AR-2, MF AR-3 and MF AR-4 with commercial clay, MF MAV-II and MF MAV-III with Gubbio marl) were left to dry in a ventilated cellar in the shade, from August to January.
Meanwhile, during a moonless night in October, which traditionally is the best period for cutting wood6 , the branch of a cherry tree (Prunus avium) was cut using a flint biface. This is because its L-shape was deemed suitable to constitute the haft for the copper axe that was going to be produced with the marl moulds. The branch was debarked using an obsidian blade (See Figure 30) and then was stored for seasoning, hanged upside down in the same cellar where the moulds were drying. It should be noted, however, that the author is unaware of any evidence of P. Avium being used as a tool in European archaeological contexts earlier than the Bronze Age (Vv. Aa. 2015). This wood was chosen because it was readily available and quite strong, which made it suitable to be used as the haft of a tool.
While the moulds were drying, Mr. Daniele Giannotti, a friend of the author and also involved in ancient metallurgy7 , was contacted with the request to provide some charcoal for the research. He gave the author a total of 20 kg of hardwood coal (oak tree and chestnut tree) which is produced by charcoal burners in the inland of Pesaro’s province. This coal has been chosen over commercial coal because of the higher temperature it produces8 and the fact that is made using a traditional method locally called “ncotta”, which consists of piling wooden logs, covering them with earth and burn them without flames.
Melting copper in the marl mould using a historically accurate fire pit
The aim was to use this coal to melt copper. If the casting succeeded, the next step would be to cold work the resulting ingots, hammering them to see if it is possible to obtain copper axes of the Pila kind (Carancini, 2023, pp. 70-72, nn. 67-68, 69-70) like those preserved at the National Museum of Perugia.9 These have been studied by Dr Pignocchi and Dr Gian Luigi Carancini, who recently suggested that axes of the Pila or Patrica types are of a shape compatible with the Baffoni mould’s hollow (Carancini, 2023, pp. 70-72).
On the 7th of January 2023 a small furnace was set up in the property of Mr. Marcello Meloni in Melano, close to the town of Fabriano (Ancona province). The forge consisted of a small pit dug in the terrain, a reliable system which has been described many times in previous works and which has proved to be so effective that it could reach iron’s melting point (1.538 °C) using oak and chestnut coal (Fiorentini, 2018, pp. 41-43, Fiorentini, 2020, pp. 70-73, Fiorentini, 2013, Fiorentini, 202110 The fire was powered by a single bag bellows, which is the same used in previous works (Fiorentini, 2013, Fiorentini, 2018, pp. 41-43, Fiorentini, 2020, pp. 70-73), and other tools included the aforementioned replica of the Moscosi di Cingoli’s crucible and wooden tongs shaped with an obsidian blade.11
While particular emphasis was put in minimising the use of modern tools, commercial tools or tools made by machinery, some backups were brought in case any of the traditional ones failed: a pair of steel tongs and a graphite crucible. A blowtorch, gas lighter and copper wire recycled from discarded electrical cables completed the equipment. The AXIOMET AX-7540 laser thermoscope would be used to collect data during the experiment.
In the afternoon the moulds were put on the edges of the furnace and the coal was lit with the blowtorch (See Figure 31). After about 45 minutes the thermoscope measured a maximum temperature of 1.027 °C in the fire pit. The Moscosi crucible was then filled with copper wire, put in the fire and covered with coal (See Figure 32). A few minutes later the flames were seen turning green, which meant the copper was beginning to melt. Once removed the coal covering the crucible, however, it was noted that half of it had melted and that it could not be used for pouring the metal in the mould (See Figure 33). This failed casting attempt has been named F1.
The graphite crucible was then put into the furnace and more copper wire was put into it. This allowed three successful castings (named F2, F3 and F4) in a very short time. Only one mould was used for these castings, and that was MF MAV-II (See Figures 34, 35 and 36). The resulting ingots weights as follows: F2, 37 g; F3, 18 g; F4, 41 g.
During all these castings the molten copper boiled, ejecting drops that would turn into metal spheres (prills) once cooled (See Video below). These can be seen on MF MAV-II and the nearby mould’s surfaces (See Figures 37 and 38), and have also been found and recovered from the terrain around the mould. This could be an important indication if another archaeological excavation takes place in the Baffoni Cave in the future. Finding such metal prills may help locate the furnace.
As a result of the boiling, F4 shows a hole that almost pierces through its full depth (See Figure 39). It is therefore unusable for the next hammering experiment. F3 has been made smaller on purpose by pouring less metal in the hollow (See Figure 40), because some of the axes in Perugia are very small, such as n. 68 which is only 2.8 cm long (Carancini, 2023, pp. 70-72). F2 is bigger and the metal has some voids that are due to the boiling and consequent formation of gas bubbles (See Figure 41). Still, it will be used for the next experiment.
With regard to how MF MAV-II reacted to the castings, the first thing to note is that it shows little to no signs of wear. No cracks or other significant damage can be seen in the hollow or on the surface. The mould was not properly fired, just pre-heated before pouring metal in it, with a maximum recorded temperature of 189,1° C on its surface at the moment of casting F2 (See Figure 42). It seems, therefore, that the marl from Gubbio is a very strong and reliable material to use for making moulds.
As said, prills like the ones on the specimen can be seen on the mould’s surface, and in the hollow. The hollow itself showed a change of colour and its surface has been darkened by the contact with the molten metal, showing dark-green marks that can be compared to those on the original.
Conclusions
The following conclusions summarise over two years of continuous experiments and multidisciplinary research on the subject, which proved to have quite unique features. These are therefore provisional conclusions and could be subject to changes as the research goes on.
When he first published the mould, Radmilli described it as “a clay mould for casting… containing a piece of copper” (Radmilli, 1956, pp. 523-533). The metallographic analysis carried out on the metal spheres stuck in the specimen confirmed that it was used in a context where copper ore was melted. In addition to this, all the experimental castings described in this work caused the hollows surfaces to change colour after being in contact with molten copper, precisely replicating the original. It is then safe to confirm Radmilli’s hypothesis, that the mould was used for casting metals, most probably from copper ore.
In addition to this, due to the specimen’s suspension hole, to the very nature of the ingots that can be obtained with the mould and to the fact that it was made using marl from a distant location, it can be assumed that it was the tool of an itinerant metal worker.
At the present stage of the archaeological research it can’t be defined if the casting took place inside the cave or not. This could be made clear if further excavations will reveal the presence of metal prills like the ones that have been produced during the experimental castings and that can be seen on either the specimen, the replica’s surfaces and on the ground where the casting was done.
The presence of metal working tools inside a cave sheds an intriguing light on the universal myth that places metal workers inside mountains (think about Ephestus in the Mediterranean culture or the Yakuts, for example) (Mircea Eliade 1962, pp. 81-84). Casting copper indoors have many technical advantages compared to casting outdoors. Inside a cave stable humidity and temperature help control the fire’s temperature, as does the absence of wind. The darkness itself improves noticing any change in the colours of the flames, therefore allowing the metal worker to understand when the casting point has been reached. If a metal worker was casting copper inside the Baffoni Cave, it is fascinating to suppose we are looking at the concrete evidence of the technical needs that were at the beginning of such myths.
The metallographic analysis carried out on the metal spheres stuck on the mould’s surface showed that the mineral might be a Fahlerz. This kind of copper ore can be found in Apuan Alps and in the Metalliferous Hills in Tuscany. A copper specimen of similar composition is an unidentified object found in the Copper Age village of Conelle di Arcevia, not far from Genga (Cazzella and Moscoloni 1999, pp. 205-208). Other copper specimens have been found at the nearby location of Pianacci di Genga, also dating to the period between the Neolithic and the Copper Age (Lollini n.d.).
It is currently difficult to link the Baffoni Cave mould to either the bronze dagger or the stone sharpener found in the cave, because we lack sufficient documentation from Radmilli’s excavation. It seems unlikely that the three objects belong to the same period because of the composition of the prills found on the mould and in its hollow.
Using an electrical furnace, moulds with hollows created by pushing a thumb in the clay and casting indoors it is possible to obtain ingots weighing slightly less than 100 grams. Casting copper with a more traditional plant made of a fire pit, bag bellows and charcoal produced ingots weighing a maximum of 41g. This difference can be explained by the fact that the hollow of MF MAV-II is the same replica of the original, having been made with the lead stamp.
The Baffoni mould is made of marl, which is currently a unicum in the author’s knowledge. Marl was never used before in his casting experiments, but it has proven to be a strong and reliable material, very easy to work and capable of sustaining thermal shocks with almost no damage, apparently out-performing clay and earthenware. The author suggests lithographic analysis should be carried out on moulds, crucibles or nozzles specimen in order to see if there are other examples made of marl.
It is safe to say that the mould found in the Baffoni Cave was used to make ingots, most probably starting from a copper mineral. These ingots could be used in various ways. Copper could be melted repeatedly until it was refined of extraneous metals (like zinc and silver), giving the metal worker ingots of almost pure copper that could then be used as a base for alloys or as currency. This process would be made easy by observing the changes in the ingot’s colour after each casting: the less extraneous metals in it, the darker red it would become.
These ingots may also have been used as semi-finished products that would then be hammered to obtain small axes similar to those found between Regions Umbria and Lazio, that are exhibited at the Museum of Perugia. The author will carry out such experiments on F2 and F3 in the future, to see if this hypothesis can be confirmed or will have to be discarded.
Lastly, the pit furnace served by bag bellows proved its effectiveness once more, suggesting that the remains of similar features should be looked for in any archaeological excavations that will take place in the Baffoni Cave in the future.
Dr. Luigi Gallo, Director of Museums of Region Marche, rejected the proposal of a conference on the subject in the Museum of Ancona, where the specimen is stored, motivating the refusal with the fact that the mould was not on display. Given the unique features of the Baffoni Cave’s marl mould and of the context where it was found, however, it is important to discuss the matter as much as possible. For this reason, I would like to thank EXARC for giving me the chance to illustrate the subject, the results obtained until now and the issues faced during the research. A special thanks goes to Moira Watson, Katerina Dvorakova, Dr. Giovanna Fregni and Dr. Rena Maguire, who reviewed the article and worked so much to make it readable and clear for the readers. The hope is that the mould and its context may get the attention they deserve.
- 1Since the present work is describing the author’s experimental contribute to this research, and that it is following a chronological order, it is important to underline that in 2021 and 2023 Dr. Montanari, Dr. Pignocchi and Dr. Carancini managed to propose a chronological and typological classification of the mould. This will be explained later.
- 2The hollow described belongs to mould MF-4. What remains of the specimen’s hollow measures 4,6 x 3,2 x 1,65 centimeters
- 3This percentage represents an average value deduced from some Bronze Age specimen found in Moscosi di Cingoli; cfr. Pignocchi G., Cabibbo M., Fiorentini M., Montanari A., “La matrice in terracotta e il pugnale in bronzo della Grotta dei Baffoni (Genga-AN): analisi, riproduzione e interpretazione”, IpoTesi di Preistoria, V. 14, pp. 15-44, 2022, pp. 31.
- 4Still, it seems unlikely that the dagger and the mould come from the same stratigraphic context. We suffer a lack of documentation about Radmilli’s excavations, which makes hard to understand the context of each specimen found in the cave. The most updated review on the excavation is Pignocchi et al., 2022.
- 5It is important to note that a dating has been proposed for the context in which the mould was found, that is 3640-3380 BC, corresponding to the Ancient Eneolithic.
- 6Pliny the Elder (Naturalis Historia 16, paragraphs 152-202) gives useful information about the best period for cutting wood, a tradition that continues today as reported by many forest inspectorates (e.g. Ispettorato forestale di Merano Konrad Greif) and Regions (e.g. Piemonte, Basilicata, etc…). This tradition is called “taglio di luna” (“moon cut”) and is based on the fact that either sap and chlorophyll are present to a lesser extent between September and January, and that the translocation of chlorophyll decreases with a waning moon. As a result, collecting wood during winter season and in nights without moon gives more chances to have less cracks in the wood and a safer recovery of the wood log
- 7Mr. Giannotti is specialized in iron smithing and produces replica of iron and steel specimen ranging from the Celtic context to the post-medieval era. He can be contacted via his website https://www.riproduzionistoriche.com/.
- 8As experimented in the author’s bachelor degree “Lavorare con il fuoco – La metallurgia fra aspetti tecnici e storici per un’interpretazione antropologica”, pp. 112-118.
- 9The Museum hosts a collection of small copper axes found between Regions of Umbria and Lazio. A further article by the author regarding the hammering experiment in order to replicate one of these axes will follow
- 10Such a feature has been described by the author on his bachelor degree too, pp. 81-112, pp. 118-124 and pp. 141-175.
- 11The crucible found in Moscosi di Cingoli belongs to a Late Bronze Age context; therefore, it seems to be more recent that the Baffoni Cave’s mould, which can be roughly dated to a period between the Copper Age and the Early Bronze Age. Still, no crucibles of that period have been found in Region Marche, so it has been decided to use the replica of Moscosi’s crucible, being one of the oldest and having no other options.
Country
- Italy
Appendix
Replicas of the bronze dagger: | |
B-1 | left untouched after the casting (weight 99 grams) |
B-2 | partially worked after the casting: the bronze in excess has been removed and both the blade and the edges have been shaped |
B-3 | the finished dagger, sharpened and hafted. |
Replicas of the mould (first attempts): | |
MF-1 | Made with simple soil. Cooking successful. Successfully used to cast 5 copper ingots (average weight 97,6 grams) |
MF-2 | Made with commercial red clay. Cooking successful. Used to cast 5 copper ingots (average weight 99,2 grams). Badly damaged afterwards. |
MF-3 | Made with commercial white clay. Cooking unsuccessful, had to be discarded. |
MF-4 | Made with commercial white clay. Cooking unsuccessful, had to be discarded. |
Replicas of the mould (second attempts): | |
MF MA-1 | First attempt with Apiro marl. Done to become acquainted with the material. Hollow done by hand. Uncooked. Unused. |
MF MA-2 | Second attempt with Apiro marl. Precise hollow done with DAS. Cracked while drying, it was used to obtain the lead stamp of the hollow. The mould later split in two halves. |
MF AR-1 | Made with commercial fire-resistant clay as a backup mould in case of emergency. Hollow done with the lead stamp. Not cooked. Unused. |
MF AR-2 | Made with commercial fire-resistant clay as a backup mould in case of emergency. Hollow done with the lead stamp. Not cooked. Unused. |
MF AR-3 | Made with commercial fire-resistant clay as a backup mould in case of emergency. Hollow done with the lead stamp. Not cooked. Unused. |
MF AR-4 | Made with commercial fire-resistant clay as a backup mould in case of emergency. Hollow done with the lead stamp. Not cooked. Unused. |
MF MAV-II | Made with Gubbio marl. Hollow done with the lead stamp. Not cooked. Used for 3 copper casting using the fire pit. Undamaged. |
MF MAV-III | Made with Gubbio marl as a backup mould in case of emergency. Hollow done with the lead stamp. Not cooked. Unused. |
Castings: | |
F1 | First tentative with the fire pit. Unsuccessful. |
F2 | Second tentative with the fire pit. Successful. Weights 37 gr. |
F3 | Third tentative with the fire pit. Successful. Weights 18 gr. |
F4 | Fourth tentative with the fire pit. Successful. Weights 41 gr. |
Table 1. Tables of the codes, used in the article, that relates to the replicas built
Bibliography
Carancini G. L. (edited by), 2023. Contributi relativi all’Eneolitico della penisola italiana. Perugia: Quaderni di Protostoria 5.
Cazzella A. and Moscoloni M., 1999. Conelle di Arcevia, un insediamento eneolitico nelle Marche. Lo scavo, la ceramica, i manufatti metallici, i resti organici. Rome: Gangemi editore.
Eliade M., 1962. The forge and the crucible, the origins and structure of alchemy. Chicago: University of Chicago Press.
Fiorentini M., 2013. A Picenian warrior who lived in the 8th Century b.C.: a hypothetical reconstruction. EXARC Journal, 2013(2). [online] Available at: < https://exarc.net/issue-2013-2/at/picenian-warrior-who-lived-eight-century-bc-hypothetical-reconstruction > [Accessed 10 July 2023].
Fiorentini M., 2018. I guerrieri Piceni. Rome: Edizioni Chillemi.
Fiorentini M., 2020. Armamenti e tattiche militari nella battaglia del Sentino. Sesto Fiorentino: All’Insegna del Giglio.
Fiorentini M., 2021. Novilara dei Piceni – Walk like a Picenian… EXARC Journal, 2021(4). [online] Available at: < https://exarc.net/issue-2021-4/mm/event-review-novilara-dei-piceni-walk-picenian > [Accessed 10 July 2023].
Francioni O., 2022. Analisi mineralogico-petrografica reperto proveniente dalla Grotta dei Baffoni – Frasassi (AN). Camerano: GeoPT Studio – Laboratorio.
Lollini D., n.d. Museo Archeologico Nazionale delle Marche. Sezione preistorica. Paleolitico-Neolitico. Falconara M.ma (AN).
Lucentini N., 1997. Le grotte della gola del Sentino In: Pacciarelli M. (ed.), Acque, grotte e dei. 3000 anni di culti preromani in Romagna, Marche e Abruzzo. Imola: Musei Civici. pp. 36-49.
Montanari A.and Pignocchi G., 2022. Frasassi – La piccolo grande storia delle grotte. [online] Available at: < www.speleomarche.it > [Accessed 1 July 2023]., FSM Federazione Speleologica Marchigiana.
Pignocchi G., 1999. La ceramica preistorica: tecniche, forme e decorazioni. Ancona: Laboratorio Ancona.
Pignocchi G., Cabibbo M., Fiorentini M. and Montanari A., 2022. La matrice in terracotta e il pugnale in bronzo della Grotta dei Baffoni (Genga-AN): analisi, riproduzione e interpretazione. [online] Available at: < https://ipotesidipreistoria.unibo.it/article/view/14325 > [accessed 10 July 2023]., University of Bologna: IpoTesi di Preistoria, V. 14, pp. 15-44.
Radmilli A. M., 1956. Gli scavi nella grotta dei Baffoni. Rome: BPI – Bullettino di Paletnologia Italiana, 65, Museo Nazionale Preistorico Etnografico “Luigi Pigorini”.
Vv. Aa., 2001. Eroi e regine – Piceni popolo d’Europa. Rome: Edizioni De Luca.
Vv. Aa., 2015. A Bronze Age battlefield? Weapons and Trauma in the Tollense Valley, north-eastern Germany. [online] Available at: < https://www.researchgate.net/publication/... > [accessed 24 May 2023]., Cambridge University Press.