The content is published under a Creative Commons Attribution Non-Commercial 4.0 License.
Reviewed Article:
Reconstructing the Pyrotechnological Development of the Harappans Using Ethnoarchaeological Parallels in The Region of Ghaggar, India
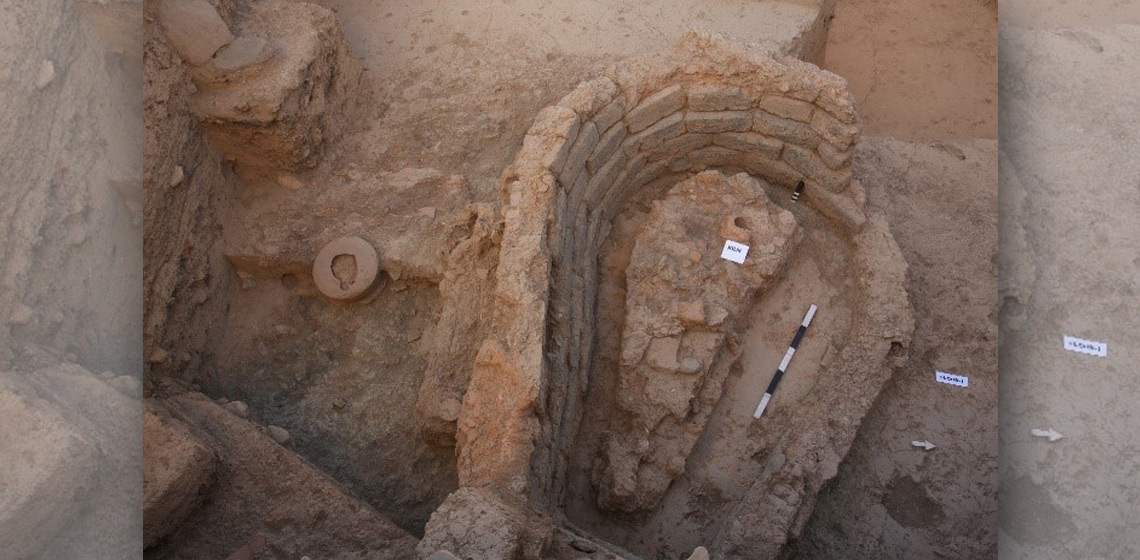
Indus Valley Civilization flourished in India and Pakistan owing to its technological advancements dating back to the 3rd millennium BC. The present paper aims to trace the emergence of pyrotechnology through documenting the industrial settlements that have been excavated in recent years, as well as locating the potential trading network for the craft items being produced at these small settlements on the outskirts of major Harappan cities such as Harappa, Mohenjo-daro and others. The paper focuses on the excavated Harappan sites with special reference to the site of Binjor - 4MSR in India's Ghaggar riverbed region. The reconstruction of kilns and furnaces based on the excavated remains was considered through the experimental study, such as wheel motion and the quantification of fuel consumption in the production of pottery, including terracotta figurines, bead and metal objects. During the research, the author has documented more than 50 furnaces, attempting to find parallels between Harappan heat treatment and modern potters and smiths located on ancient mounds. The ethnographic similarities between Harappans and the contemporary villagers who continue to inhabit the archaeological mound have been emphasised. The research also examines whether the technology utilised by the Harappans has changed or not, ranging from pottery manufacture to metal smelting, and what can be deduced from these experimental approaches to comprehend the technological prowess of their artisans.
Introduction
The pyrotechnological development of Harappans led to the development of technical expertise in producing craft items, helping to build strong hinterland and international trade networks among cities and contemporary civilizations such as Mesopotamia and Egypt. The emergence of Harappan craft centres in the Ghaggar region has provided us with substantial data through the excavation of Harappan sites such as Binjor - 4MSR (Manjul et al., 2017), and other adjacent sites in Rajasthan belonging to the Indus Valley Civilization. These sites aid in understanding the socioeconomic impact of small settlements that engaged in extensive craft manufacturing process.
The progression of technology relates to the control of fire: pyrotechnology. Until very recently, materials required the control of heat and the development of ever-increasing temperatures under regulated conditions. The first stage of pyrotechnology along this path was the mastery of fire. Use of fire was discovered in South Africa's Swatkrans Cave dating back 1.5 million years (Brain and Sillent, 1988). Cooked food and preserved flesh became feasible, as did the use of heat in working flint and hardening wooden tools, such as the yew spear from the Middle Palaeolithic site in Lehringen, Germany (Thieme, 2005). Terracotta figurines were produced sporadically in the Upper Palaeolithic periods at sites from the Pyrenees (Marshack, 1991). The most notable concentration occurs at the open-air site of DolnĂ VÄstonice-Pavlov (Svoboda, 2020) dating to approximately 30,000 years ago. They consist of small, well-modelled figurines of animals and humans which can be seen at the site of Binjor - 4MSR as well.
Humans became the masters of technology when they learned to control fire, but the real breakthrough was with the advent of metal technology, which was more complex and durable. The earliest civilization practicing metal technology in the Indian subcontinent was the Harappans. The technique of alloying was known to them along with the use of native copper.
Archaeological setting of the Harappan site of Binjor - 4MSR
Binjor village is located at 29 °12â872ââN:73°9â421ââ E & 159 m MSL (See Figure 1). The site is situated on the bank of the dried river Ghaggar (an affluent of an ancient Saraswati River) in the district of Shri Ganga Nagar, Rajasthan. The excavation of the site was carried out by the Institute of Archaeology, Delhi with the collaboration of Excavation Branch II, Purana Quila, New Delhi between 2014-2017, under the direction of Dr Sanjay Manjul, then Director of the Institute of Archaeology. Three seasonsâ excavations have yielded a substantial amount of information to reconstruct the past life ways. The habitation more than 1 hectare area, while the cultural material has been noted from 7 m (159-151.47 m MSL) above the natural soil. The top 0.8 m part of the mound has been disturbed due to various activities of the Indian Army and cultivation.
Binjor - 4MSR has revealed a single centre for terracotta and metal craft at Binjor. Three distinct cultural sequence were identified during the excavation. The C14 dating via accelerator mass spectrometry (AMS) dating was done on the samples from Binjor at two laboratories: Institute of Physics, Gliwice Radiocarbon Laboratory Gliwice Radiocarbon Laboratory, Poland, and Birbal Sahni Institute of Palaeosciences, Lucknow, India (Sharma et al., 2020).
Stage I - Pre/Early Harappan (2900â2600 BCE)
- Phase-I
- Phase-II
Pre/Early Harappan is characterized by the pottery, that is handmade on a slow wheel, comprising a red to dull red colour, with fine to medium fabric with typical monochrome, bichrome painting. A few polychrome sherds were found, similar to a pottery type from a pre-Harappan deposit at Kalibangan (Thapar, 1975). Phase II is marked by the presence of potsherds made on a fast-rotating wheel with bichrome painting. The surface is red to dull red in colour, on which the painting was done with black and white colour. The structural phases revealed a circular hearth with mud brick structure and remains of an enclosure wall built with sun dried bricks.
Stage II - Transitional Period (Early to Mature Harappan) (2600â2500 BCE)
The transitional period is marked with the continuation of bichrome pottery and the absence of polychrome pottery. Some new shapes, such as goblets, start to appear in this phase. The copper and semi-precious stones made their appearance, though in negligible numbers. The terracotta cakes in different shapes like mustika, idly, and triangular are found within the series of circular hearths. The structures associated with the mud floors had walls with five courses of mud bricks and are oriented in east-west.
Stage III - Mature Harappan (2500â1800 BCE)
- Phase-I
- Phase-II
This stage is marked by red ware and red slipped ware, made of well levigated clay and characterised by its typical painted design with black pigment. The paintings are done on carefully prepared red background. Number of postholes and hearths were encountered during the excavation suggesting the structures for the working-class population at the sites. The availability of a large number of ceramic assemblages, hearths, furnaces, weights, terracotta seals, beads, and bangles suggest that this stage reached the level of Mature Harappan.
The paper tried to document the living pottery traditions around the excavated area of the site. The site stands unique among all Harappan sites due to the high number of furnaces and kilns. The location of the site itself makes it an important area which could have served as a supplier for major cities such as Harappa (Vats, 1940), Mohenjo-daro (Mackay, 1934), Kalibangan (Lal et al., 2003), Rakhigarhi (Nath, 1998), and other adjacent Harappan sites. The present research, therefore, will try to reconstruct the craft specialisation with special emphasis on the documentation of local potters and artisans dealing with metal ornaments near the town still practicing the local techniques passed on by their ancestors.
In the past, works focusing on pyrotechnology of Harappans frequently failed to differentiate between the processes of melting and smelting, as well as the distinctions between kilns and furnaces. The research conducted by Miller (1993), as part of the Harappan Archaeology Research Project, has made significant contributions in clarifying these ambiguities, which extend beyond mere semantics and instead pertain to crucial metallurgical procedures. Kenoyer and Miller (1999) express a word of caution on the terminology employed, suggesting the use of the more inclusive term "kiln" instead of the more particular phrase "furnace," which is typically associated with metal processing.
The major indicators for metal processing at a site are defined by Kenoyer and Miller (1999) as including:
- Fragments of ores;
- Kilns, or fragments of kilns, attributed to metal processing.
- Metallurgical slag, from the reduction of ore to metal
- Tools used for metal processing such as crucible fragments with metal prills, moulds, anvil, stakes, hammer, chisels, etc., and
- Metal objects, including smelting and melting ingots, semi-finished and finished objects.
Nevertheless, these features defined by Kenoyer and Miller seem to match with the excavated site of Binjor since all the above-mentioned indicators are found at the site (see Figure 2). Based on the quantity and type of slag, the small amounts of copper metal slag found at Harappan sites seem to be more representative of melting rather than smelting (Miller, 1994b). The often-cited copper smelting slags from Ahar (Shinde, Raczek and Possehl, 2014) are from levels dated to the second millennium BC, after the end of the Harappan Phase. The absence of slag heaps and smelting debris may be due to the fact that most excavated sites, particularly of the Harappan Phase, are located some distance from the primary sources of metal ores (Kenoyer and Miller, 1999). But archaeologists working in Rajasthan have made a laudable effort to look for copper slag, which occurred at the site of Binjor - 4MSR, (Manjul et al., 2017). In addition, soil samples from the few furnaces were subjected to isotopic analysis, suggesting the presence of a considerable presence of lead (Pb), copper (Cu), and zinc (Zn), potentially representing substantial byproducts of the metallurgical processes at the site of Binjor (Sharma et al., 2020). Further, this site can help bridge the gap between locating the far-off industrial settlement and the urban Harappan settlement (See Figure 2).
Research Problem
The primary research question concerns the factors contributing to the higher prevalence of kilns, particularly in the Binjor region, as opposed to other Harappan sites. The likely explanation for the abundance of kilns at this site is the availability of ample resources, specifically raw materials such as copper ore and clay, in the surrounding area of Binjor. Numerous experts have posited thus far that the clustering of these kilns signifies that the location functioned as an industrial zone for the ancient Harappan civilization. The objective of this study is to undertake an investigation into the historical background of the Harappan civilization, specifically focusing on the inhabitants of the place under consideration. Another factor to consider is that, while the site has produced significant findings, these findings alone may not be sufficient for a comprehensive reconstruction of kilnâs function. Conducting experiments would be necessary to obtain a more detailed understanding of the site. The excavation of the site has spanned three seasons, during which more than a hundred furnaces and kilns - were discovered in a concentrated region, indicating a craft industry at work. This characteristic sets this particular site apart from other Harappan sites, rendering it distinctive in its own right. For example, the archaeological site of Harappa has revealed the presence of 16 kilns. Despite being a prominent city of the Harappans, it does not exhibit a significant concentration of industrial activities However, the lack of a good scientific approach has hindered the acquisition of conclusive results regarding the function of these furnaces and kilns (See Figure 3).
Archaeological Findings and Experimental Approach
The archaeological excavation of Trench S30W40 at Binjor - 4MSR has revealed the presence of a kiln with a distinctive pyriform or yoni shape, oriented towards the west (See Figure 4). The kiln was made using six brick courses, following the English bond pattern; Bricks are arranged in successive courses in an overlapping header (short side) and stretcher (long side) arrangement, following the brickwork bonding pattern. The kiln exhibits similarities to the experimental kiln built under the supervision of Professor Kenoyer at Maharaja Sayaji Rao University of Baroda, Vadaodara, Gujarat (see Figure 6). The excavated kiln was situated at MSL 154.25, with measurements of 2.08 m x 1.48 m x 0.50 m at the top and 1.49 m x 0.98 m x 0.50 m at the bottom (Length x Breadth x Height). The dimensions of the kiln indicate that it may not have been adequately designed for the purpose of heating pottery, as excavators have proposed that it could have been utilised for the smelting of ore. This is assumed because on the left side near the baulk, the presence of a stone anvil suggests that the fabrication of copper artefacts was done near the kiln. This hypothesis is supported by the discovery of slag and a small number of copper fragments, which have been subjected to scientific study.
The kiln was constructed using mud bricks that had later undergone vitrification because of prolonged exposure to high temperatures. Within the kiln, there were remnants of vitrified terracotta cakes in the shape of triangles and circles, usually referred to as idly shaped cakes, each featuring a small thumb impression at the centre. Charcoal was discovered in conjunction with an ashy deposit within the kiln. The dimensions of the bricks utilised in constructing the kiln wall are 32 cm x 16 cm x 8 cm. A total quantity of soil weighing 210 kg MSL was subjected to a flotation process, commencing with an initial weight collected from the MSL 154.78 and concluding at a final weight at the depth of 154.55 MSL. The adjacent quadrant to the kiln has provided a notable illustration of a dump that contains a substantial quantity of discarded broken potsherds, as well as a terracotta bull and other figurines. Furthermore, the discovery of a significant number of terracotta objects contradicts the presumed use of the kiln for ore smelting or terracotta production. The uncertainty surrounding this matter will be resolved once the laboratory analysis of the collected sample from the vitrified mud brick of the kiln wall yields authentic results - although the collection of slag was satisfactory from both the kiln and the waste dump.
In the vicinity of trench E30, a compact region measuring 10 m x 10 m had a diverse array of kilns, exhibiting various shapes and sizes. These kilns were discovered alongside earthen pots and jars which were observed to be in their original positions. What implications may be drawn from this? The varying levels of these kilns suggest the possibility of overlapping, indicating that they were utilised by individuals from different cultural periods at different points in time. The kilns revealed evidence of reuse, as indicated by the layer of plastered lining on the walls. This suggests that these kilns were a combination of many phases that coexisted over a certain period. As seen in Figure 5, the presence of two globular jars positioned in proximity to kilns serves to signify the intention of producing and fashioning items required for the annealing procedure, which involves submerging heated objects into water to An examination of trenches oriented towards the west has unveiled a circular kiln with an inside wall which has been coated with clay and has vitrified pottery fragments on the floor. This finding suggests a significant amount of burning took place in order to fire the pottery and other terracotta objects.
The experiment was conducted prior to the beginning of ongoing research, with the guidance of Professor Mark Kenoyer. We were able to gain insights on the pyrotechnology employed by the Harappans through the execution of these experiments. In our study, we exclusively employed traditional indigenous techniques in the absence of contemporary instruments, except for thermocouples which were utilised for measuring the temperature within the pottery kiln. The copper ores were roasted and broken down into pieces to collect the fragments. The collective fragments of copper were melted to prepare ingots. Whereas, an Updraft pottery kiln was constructed and utilised to replicate the pottery of the Harappans The recorded temperature of the kiln reached up to the temperature of 505° C (See Figure 6)
The fragmentary remains that are revealed during excavations provide limited assistance in understanding the historical context. This is mostly due to the necessity of dismantling the superstructure of the furnaces to retrieve the smelted metal located in the lowermost section of the furnaces. Additionally, the smelting process inherently leads to modifications in the size and shape of the furnace, often resulting in the destruction of crucial evidentiary components.
To gain such understanding, experiments in copper smelting, in addition to the pottery kiln, a furnace was created to reconstruct the Harappan smelting process. Ores were brought from the mines of Ambaji in Rajasthan and Oman to get a better understanding of the chemical properties of copper from both the sources (See Figure 7b).
A copper furnace was built with the unbaked mud bricks, leaving a narrow open mouth at the top to help draw in oxygen, enabling a higher temperature to smelt the ore see Figure 7a. The presence of a superstructure resembling the experimental copper furnace (See Figure 7a) suggests that a wide variety of furnaces may have been utilised for either smelting of ores or melting of copper at the site of Binjor. The excavation has yielded a variety of kilns and furnaces which are categorised based on their typological study such as circular, oval, circular pot based and circular shaped furnace with a shaft (See Figure 8).
The circular furnace is the most prevalent kind among all furnace designs. The use of an oval-shaped furnace, including a central mud brick structure serving as a shaft, is indicative of its likely application in metallurgical processes. The pot-based furnace has distinct characteristics. These furnaces are constructed by placing a circular clay pot in the ground, which is then coated with many layers of clay plaster. This suggests that the furnace was repeatedly used to produce various craft items, including steatite beads or metal objects. The circular shaped furnace with a shaft, characterised by its elongated structure and terracotta cake shaft, serves to retain heat efficiently during the fabrication of metal object.
Ash and charcoal have been collected to conduct a scientific investigation in different laboratories to determine how these furnaces vary in temperature. Similar types of furnaces and kilns were reported from other sites in the Ghaggar region at the site of Baror (Sant, 2005), Tarkhanewala Dera (Trivedi, 2009). There are two separate types of kilns reported from Binjor, which continue to be utilised in various regions of India. The downdraft kiln, known for its simplicity in producing vessels, is particularly prevalent in rural India (See Figure 13). The Pyriform kilns are mostly updraft kilns at the site (See Figure 4), primarily used to produce deluxe ceramics such as classic Harappan ceramics: âSâ shaped jars, perforated jars and a dish on a stand with terracotta figurines.
Ethnoarchaeological Parallels
A survey spanning 50 km was undertaken during the field work to record the pottery traditions in the vicinity of the excavated site. During the survey, three settlements, namely Rai Singh Nagar, Anupgarh town, and the village of Binjor - 4MSR, were recorded. This ethnoarchaeological study tried to examine pottery, as well as other terracotta craft practices, including the domestic hearths (Chulha, Tandoor) along with documentation of blacksmiths and goldsmiths in Anupgarh. The initial aim was to document the copper smelting workshop near the village but due to the industrialization of large-scale metal industries the primitive method of smelting the copper ore seems to be a long gone phenomena. The steel industry has taken over and most of the smiths rely upon the meagre work of sharpening the agricultural tools hence the ancient practice of copper smelting could not be traced.
Pottery Traditions
The first meeting was with a local potter named Mr. Banwarilal and, under his guidance, experiments of pottery making were conducted. He has been engaged in this craft since the age of 14. Banwarilal acquired this knowledge from his father; however, it appears that Banwarilal is not succeeding in passing on his expertise to his young offspring. This is likely due to the fact that Banwarilal's business, which primarily consists of traditional pottery items, is experiencing significant limitations in the current period of more sophisticated and fashionable alternatives. Consequently, Banwarilal is facing considerable difficulties in achieving financial stability. Meanwhile, documentation of pottery making followed the step-by-step process of acquiring knowledge about his traditional method. The first step was the acquisition of raw materials. The clay is collected from a nearby field and thereafter soaked in water for one day allowing for the use of an elutriation method. This technique facilitates the separation of heavier particles, while the finer clay particles are retained for the purpose of crafting pots. After the clay has been prepared, it is kneaded and wedged to remove air bubbles and ensure uniform consistency. This process makes the clay more malleable and easier to work with. The levigating process of preparing clay was followed by making the vessel by hand and various tools to shape the clay into the desired form. This could be a pot, bowl, vase, or any other type of utilitarian terracotta objects, followed by the colouring of pots and other terracotta objects with yellow ochre and a white clay mineral bought from the surrounding market of Bikaner.
There are two types of wheels now in use. The potter residing in Raisingh Nagar, Banwarilal, continues to favour the use of a manually operated pottery wheel. In contrast, the 23-year-old potter, named Rakesh, employs an electric wheel in order to enhance production efficiency. Following the process of shaping, the pots are kept under shade or in a dark room, away from direct sunlight which turns pots "leather hard," wherein they retain a malleable consistency that allows for further shaping with the aid of a dabber.
Two types of pigment are used for the purpose of colouring the pot. The pigment that imparts a yellow ochre hue undergoes a transformation and turns red during exposure to high temperatures during the fire process (See Figure 9).
The firing stage of the pottery production process is arranging the husk beneath the unfired pots, which are positioned on a glass-shaped device with a perforation at the bottom, solely used during firing. Subsequently, broken potsherds are placed on top of the unfired ones to serve as a covering layer, and the entire structure is coated with clay plaster mixed with husk. This process results in the layout of two chambers, which are meant for the fuel. The firing process of pots involves the use of approximately five quintals (1 quintal = 100 kilograms) of burada (wood powder), two quintals of local tudi woods, and cow dung cake. After undergoing the firing process, vessels and other terracotta goods, such as skin rubbers, can be found in the market. The antiquity of skin rubber can be traced back to Harappan times in India.
(See Figures 10)
The downdraft kilns are a significant discovery at the archaeological site, as they showcase the remarkable layout and scale of the kiln, providing valuable insights into the workshop area of the site. The kiln utilised a downdraft system, wherein a significant quantity of fragmented potsherds was discovered predominantly at the lowermost section. The kiln revealed a circular configuration, comprising a lining of clay on a compacted mud floor. The excavation has yielded evidence of vitrified terracotta cakes, both circular and triangular shapes which are predominantely commen at harappan site suggesting the use for retaining the hot for a longer period. The dimensions of the kiln were measured to be 90 cm x 90 cm x 30 cm. The kiln alone indicates the maximum amount of material that could have been accommodated for producing at any given time. The downdraft kiln, traditionally characterised by its fuel consumption and mud plastering, differs from contemporary pottery firing methods employed by modern potters; it has been observed that the reported kilns from Binjor had thick plaster at the bottom whereas present day potters in nearby village do not plaster the base of the kilninstead it is left with the accumulated burnt ash over the years. There were multiple kilns that were exposed during excavation; however, all these kilns were found at different working levels of the mature Harappan phase. The resemblance between the excavated kiln (See Figure 12) and the modern kiln (See Figure 13) suggests the influence of ancient pottery making traditions among the modern population to this day
The shape of the pots has not altered since the Harappan period, indicating that the current people of northwest India have not changed their eating patterns. To some extent, the medium has changed from clay to metal. Apart from ceramics, Binjor was a flourishing centre for terracotta objects ranging from terracotta animal figurine to game pieces (See Figure 11 c)
The bead manufacturing kilns reported in Binjor are similar to the bead kiln (See Figure 14) reported from the site of Lothal in Gujarat (Rao, 1979) (See Figure 15). In situ steatite paste was found from multiple kilns. In addition, the site seemed to have traded shell and semi-precious stones from other resource centres.
Domestic Rural Hearths
The hearth is an archaeological feature that represents the remnants of a purposeful fire (Meyer, 2003). These are typically used to cook food but may have been used to heat-treat lithics, fire pottery, or for a variety of social reasons, such as keeping predators away, keeping warm, and providing an inviting gathering place. A hearth becomes a valuable element for an archaeological site because it provides insight into the dietary pattern, and aids in the archaeobotanical understanding of the people. This wide range of organic materials provides an opportunity for obtaining radiocarbon dates for the period. The site provides an insight into the Harappan rural settlements and, more precisely, into their craft workmanship. The presence of several kilns in a small area is the unique feature of the site. The site could have the potential to provide a huge amount of information for understanding the area with its regional-specific character and to clarify the obscure picture of early levels.
The Mesolithic sites of Damdama and Mahadaha have provided evidence of plastered oval and circular hearths. These plastering methods continue to be used by the local people of limited resources residing in the region. A total of 11 hearths, including a community hearth, have been documented at the Mesolithic site of Sarai Nahar Rai. Of these, eight hearths have been subjected to excavation. Four of these hearths are regular in shape, either circular or oblong, and they come in different sizes. A significant number of pit hearths have been discovered at another location within the Belan Valley, specifically the site of Chopani-Mando. The shape of these pits can be described as circular, oval, or oblong, with a width of 52 cm and a depth ranging from 15 cm to 40 cm. Additionally, certain pits have a confined base accompanied by a large opening. A portion of the objects are coated with damp clay. The pit hearths are comprised of clay lumps, ash, and small charred remains of animal bones. A discovery has been made at Mahadaha of a gaur skull adorned with horns, which was recovered from a pit hearth. Furthermore, during the chalcolithic levels at Koldihwa, a solitary-mouthed chulha has been discovered (Ansari, 2006).
The Harappan culture consisted of communities of artisans, traders, potters, and administrative figures similar to our modern society. Everyday objects have not altered such as the traditional pottery making, cooking methods and craft items. The traditional cooking methods of tandoor (See Figure 17 ab) and chulhas are employed by the people of Rajasthan and other northwestern parts of India to prepare Tandoori roti, a type of wheat bread, as well as other renowned Punjabi food such as Tandoori Chicken. The Harappan tandoor (oven) has been reported from the Harappan sites of Kalibangan (Lal et al., 2003) and Farmana (Shinde et al., 2008). Chulhas are commonly employed for the purpose of cooking curries and regular food every day.
Haras are typically used for the purpose of heating water, particularly for bathing. The aluminum or terracotta vessels are installed within these longstanding enclosures (Hara) (See Figure 18). Nevertheless, in the northern region of India, a wide variety of heating devices known as haras, which are specifically used to heat large quantities of milk at a low temperature, resulting in the distinct flavour of burnt whey, the sale of whey and milk contributes to their economic sustainability.
In the village, blacksmiths use small open furnaces that are operated by manually operated blowers to facilitate the flow of air. These blacksmiths use this setup to craft various small-scale agricultural tools and kitchenware (See Figure 19).
The goldsmiths in the town possess a comprehensive understanding of their craft, employing a combination of contemporary technology and traditional methods. Apart from copper, gold beads have been reported from the site of Binjor, providing the early development of metallurgical developments. Although it is difficult to draw firm conclusions, these artefacts suggest that the area has a long history of working with precious metals (See Figure 20). Although these modern goldsmiths are not using the indigenous primitive techniques instead, they take help of gas chambered furnace to melt the gold and silver which fastens the process of melting and casting the ornament. For fabrication of ornaments, they use automatic mild steel goldsmith wire and sheet rolling machine and variety of moulds to create pendants, earrings, and other ornaments.
In India, traditional goldsmiths have carried on many practices and earliest use of gold was reported from the early Harappan levels of Jalilpur (Mughal, 1974) and Kunal dating back to 4000 BCE (IAR, 1998-99, p.12). The gold jewellery is well known for its intricate designs in India, certain fundamental concepts have been maintained throughout the development of different techniques. Gold and silver have significant religious and cultural importance in India. It is often used as a synonym for success and wealth. This respect for gold has been passed down through the ages and it shows in the design and craftsmanship of traditional gold jewellery. The current regional traditions and beliefs are often reflected in the styles and designs of the time. In India, several families have made a living as goldsmiths by passing the trade down through the generations.
Conclusion
This paper contains the ethnoarchaeological study of Harappans which enabled the author to draw valid conclusions regarding the everyday life, technology, social structure, and cultural practices of the Harappan civilization. These revelations can aid in bridging the chronological divide and improve our comprehension of the Harappans.
It suggests that Harappans were skilled potters and metallurgists, working with copper, bronze and other noble metals such as gold and silver. They used furnaces and crucibles to smelt and cast metal objects. However, this paper could not draw valid conclusions in regards with the nature of each furnace and kiln whether one was solely indulged in metallurgy or terracotta craft production. Nevertheless, it is certain that site was an industrial settlement due to the presence hundreds of furnaces and kilns along with metal artefacts, ornaments, and figurines suggest a high level of proficiency in metalworking and terracotta. Pottery was a crucial part of their daily life. They created a wide range of objects including utilitarian items such as storage jars and cooking vessels, as well as decorative pieces. One of the remarkable aspects of Harappan pyrotechnology was the standardisation of pottery sizes and shapes. This standardisation is believed to have facilitated hinterland and international trade and commerce with contemporary civilization. Similar technological aspects can be seen in the pottery production to metallurgical advancement in modern day of potters and artisans residing near the excavated site and all across India.
Acknowledgements
I would like to express my gratitude to Dr. Sanjay Kumar Manjul for his invaluable contribution in providing pertinent data obtained from the excavation, which was conducted under his supervision. I am thankful to Dr. Narendra Parmar for his crucial help in making the map. I would like to express my sincere thanks to Prof. Jonathan Mark Kenoyer for imparting the understanding of experimental archeology during my masterâs program in Baroda. Additionally, I extend my appreciation to those individuals specially Mr. Daluram who offered assistance during my field work in Rajasthan.
Keywords
Country
- India
Bibliography
Ansari, S., 2006. An Ethnoarchaeological Study in The South-Central Ganga Valley. Past And Present: Ethnoarchaeology in India, p. 145.
Brain, C.K. and Sillent, A., 1988. Evidence from the Swartkrans cave for the earliest use of fire. Nature, 336(6198), pp. 464-466.
IAR: Indian Archaeology - A Review, 1998-99. Archaeological Survey of India: New Delhi, p.12.
Kenoyer, J.M. and Miller, H.M.L., 1999. Metal technologies of the Indus valley traditions in Pakistan and western India. In: V.C. Pigott, ed. The Emergence and Development of Metallurgy. Philladelphia University Museum
Kenoyer, J.M. and Miller, H.M.L., 1999. Metal Technologies of the Indus Valley. The Archaeometallurgy of the Asian Old World, 16, p.107
Lal, B.B., Joshi, J.P., Thapar, B.K. and Bala, M., 2003. Excavations at Kalibangan â The Early Harappans (1961-1969). New Delhi: Archaeological Survey of India, pp. 101-105
Manjul, S.K., Manjul, A., Chattopadhyay, P.K., Pal, D.C. and Baidya, A.S., 2017. Metal Craft of Harappan Culture: A Case Study at Binjor. BUMA IX Proceeding.
Mackay , E.J.H., 1934. Further Excavations at Mohenjo-Daro. Journal of the Royal Society of Arts, 82(4233), pp.206-224.
Marshack , A., 1991. The female image: a âtime-factoredâsymbol. A study in style and aspects of image use in the Upper Palaeolithic. Proceedings of the Prehistoric Society, Vol. 57, No. 1, pp. 17-31. Cambridge University Press.
Meyer, J.C., 2003. Understanding hearth function: an approach from Harappa. Asian Perspectives, pp. 287-303.
Miller, H.L., 1993. Metal processing at Harappa and Mohenjo-daro: Information from non-metal remains. In Annales Academiae Scientiarum Fennicae. Series B (Vol. 273, pp. 497-510).
Miller. H. M. L., 1995. Locating Ancient Manufacturing Areas: High-temperaturing Debris from Surface Surveys at Harappa, Pakistan. In: A. Parpola and P. Koskikallio, ed. South Asian Archaeology, 1995. Suomalainen Tiedeakatemia, Helsinki, Finland, pp. 939-845.
Mughal, M.R., 1974. New evidence of the Early Harappan culture from Jalilpur, Pakistan. Archaeology, 27(2), pp.106-113.
Nath, A., 1998. Rakhigarhi: A Harappan metropolis in the Saraswati-Drishadvati divide. Puratattva, 28, pp.39-45.
Rao, S. R., 1979 . Lothal: A Harappan Port Town (1955-62). New Delhi: Archaeological Survey of India.
Sant U., T.J. Baidya, N.G. Nikoshey, N.K. Sinha, S. Nayan, J.K. Tiwari and A. Arif 2005. Baror: A New Harappan Site in Ghaggar Valley - A Preliminary Report. Puratattva 35:50-59.
Sharma, S., Agnihotri, R., Pokharia, A.K., Phartiyal, B., Bajpai, S., Pande, P.C., Manjul, S.K., Manzul, A., Maharana, C. and Ojha, S., 2020. Environmental magnetic, Geochemical and Sulfur isotopic imprints of an Indus archaeological site 4MSR from western India (Rajasthan): Implications to the Indus industrial (metallurgical) activities. Quaternary International, 550, pp.74-84.
Shinde, V., Toshiki Osada, Akinori Uesugi and Manmohan Kumar., 2008 . A Report on Excavations at Farmana 2007-08. In: Toshiki Osada and Akinori Uesugi, ed. Occaisional Paper: Linguistics, Archaeology and the Human Past. Kyoto: Research Institute for Humanity and Nature.
Shinde, V., Osada, T., Sharma, M.M., Uesugi, A., Uno, T., Maemoku, H., Shirvalkar, P., Deshpande, S.S., Kulkarni, A., Sarkar, A. and Reddy, A., 2008. Exploration in the Ghaggar Basin and excavations at Girawad, Farmana (Rohtak District) and Mitathal (Bhiwani District), Haryana, India. Occasional Paper, 3, pp.77-158.
Shinde , V., Raczek, T.P. and Possehl, G.L., 2014 . Excavations at Gilund: The Artefacts and Other Studies (Vol. 138). University of Pennsylvania Press.
Svoboda, J.A., 2020. DolnĂ VÄstoniceâPavlov: Explaining Paleolithic Settlements in Central Europe. Texas A&M University Press.
Thapar, B K. 1975. Kalibangan: A Harappan Metropolis Beyond the Indus Valley. Expedition 17 (2): pp.19â32.
Thieme , H., 2005. The lower Palaeolithic art of hunting: the case of Schöningen 13 II-4, lower Saxony, Germany. Hominid Individual in Context, pp. 115-132. Routledge.
Trivedi, P.K., 2009. Excavations at Tarkhanewala-Dera and Chak 86 (2003-2004). Archaeological Survey of India No.99.
Vats, M.S., 1940 . Excavations at Harappa (Vol. 2). Manager of Publications, Delhi.