The content is published under a Creative Commons Attribution Non-Commercial 4.0 License.
Reviewed Article:
The Salme Ship Burials
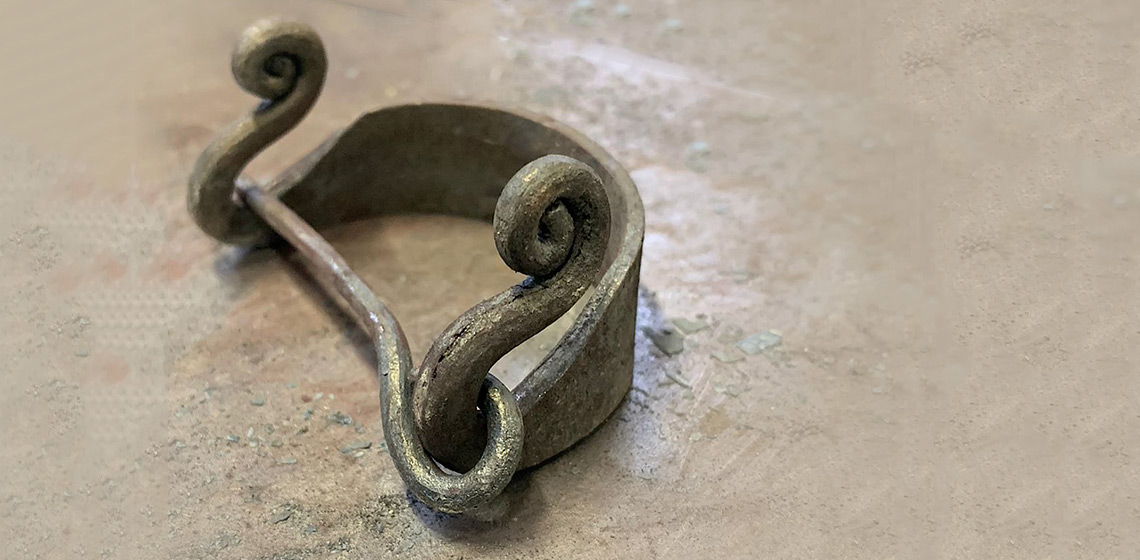
With the help of experimental reproduction of archaeological artefacts, it is possible to study how and from which materials that objects might have been made in the Iron Age. Reproductions are carried out with items such as weapons, accessories, jewellery, buildings, food, ceramics, tools, working methods, and many others. This reproduction aimed to determine the smithing methods of one iron fibula from the 12-piece collection in the Salme II Ship Burial on the island of Saaremaa, Estonia. Fibula no SM10602:325 from the distal end of the right femur of skeleton IV (F) was selected for the work (See Figures 1 and 2). Various fibulas were made in the Iron Age using various techniques, mainly from bronze alloys and precious metals. At the beginning of the Viking Age, iron fibulas were forged mainly from bloomery iron. These type 7th and 8th century fibulas have been found in archaeological excavations in Nordic countries, south-western Finland in Ostrobothnia, and Häme provinces (See Figure 4). One fibula was found in Latvia, but none in Estonia, before the archaeological excavations of the Salme ship burials.
The Salme Fibulas
The Salme archaeological finds include 12 iron fibulas. One fibula was found in the smaller ship and 11 in the larger one. In Sweden, fibulas are called bĂĄgfibula. Fibula no SM101601:215 of Salme I was found badly rusted and without a pin in mixed soil. Salme II's first fibula SM10602:147 was found in excavation square D2 and fibula SM10602:1657 in square C7, about three metres from the side of the ship, with band-shaped arches and hinges (See Figure 3).
Beside the distal end of the right femur of Skeleton IV (F) (Luik and Peets, 2023, pp.73 and 157) a fibula no SM10602:325 covered by a thick layer of rust was found. The reproduction of this fibula is the subject of this article. The width of the back of the fibula is 23 mm, the distance between the ends is 60 mm, the height from the pin to the back of the fibula is 29 mm, and the weight of the fibula is 27 g. The pin tapers towards the tip, and its diameter at the fastening loop is about 5 mm. Each end of the fibula is decorated with spirals. The corrosion layer on the back of the fibula shows (yellow arrows) the bases of rust bubbles. A light spiral stripe on the pin corrosion layer (blue arrows) may indicate it was forged from twisted pattern steel (See Figure 1).
How warrior IV (F) died is not known with absolute certainty, as the middle part of the skeleton and lower part of the skull were destroyed while excavating the cable trench. However, three impact strikes of a bladed weapon that penetrated the skull have been identified in the upper part of the skull (Peets et al., 2010, p.41; Almäe et al., 2023, pp.61 and 71). The skeleton was found in the first layer of the burial, against the starboard side of the ship on its right side, its head turned to the right and face down. Another fibula from the first layer, no SM10602:279, was found beside the forearm bone of Skeleton V (D) (See Figure 2).
Four more fibulas were found in the burial's middle layer: on Skeleton XI (K) no SM10602:407, Skeleton XIII (M) no SM10602:410, and two fibula fragments between Skeletons X (J) no SM10602:768 and XII (L) no SM10602:772. Fibula no SM10602:768 is decorated with two spirals at each end. Intact fibulas were also found beside Skeletons XXIII (W) no SM10602:848, XXXIII (Ĺ˝) no SM10602:895, and XXXII (Z) no SM10602:916. The number of fibulas suggests that about a third of the fallen warriors had an iron fibula on their grave goods (See Figure 3). Some of the deceased were perhaps covered with cloaks before the sand layers were added, which can explain the location of fibula no SM10602:325 beside the knee. All fibulas were quite badly rusted. They could have been affected by the heterogeneity of bloomery iron, the decay of organic matter, the humidity of beach sand, and especially the chloride ions of seawater salt.
The Nordic Fibulas and their Origin
By 2010, about 30 iron fibulas have been found in Finland, two in Ă…land, 32 in Sweden, five in Norway, four in Denmark, and one in Latvia (See Figure 4). It has been assumed that more similar iron fibulas were found, but they may not have been identified under a heavy layer of rust. Fibulas have been found in settlements, graves, cremation cemeteries, and mound burials, as well as the smithies (Moilanen, 2013, pp.55-64). In previous interpretations, the iron fibula was considered a "Finnish type", which would have spread from Finland through Ă…land to the rest of Scandinavia with the connections of the early Viking Age. In a more recent study, the origin and distribution of the fibulas were investigated using a finer sieve. According to the conclusions, the origin of the fibulas indicates a more western (Swedish), from where the fibulas spread to Finland during the first half of the Viking Age (Moilanen, 2013, pp.83-85).
It has also been assumed that the fibulas were made to differ slightly from each other, which would have somehow emphasised the characteristics of their owner or a certain group. Conversely, the blacksmith's craft has always included variations in the dimensions and models of similar objects. Iron fibula users are also suspected to have had some connection with persons specialised in iron production, i.e. blacksmiths or blacksmith families, e.g. because iron slag has been found in the same graves as fibulas (Moilanen, 2013, p.72). However, there is no metallurgical evidence that the slag was related to the "bloom" which was made into fibulas or that the slag came from fibula forging.
With the help of materials science research, separating iron slag according to the production process into smelting slag, forge slag, or decarburization slag would be possible. In the best-case scenario, the determination could even reveal the type of furnace used for smelting or other processes or even clarify the general picture of prehistoric iron production and the spread of related skills (e.g. Selirand 1989, pp.153-161; Jäppinen and Immonen, 2017, pp.19-30; Saage et al., 2017, pp.46-56; Magnusson, 2020, pp.11-63; Saage, 2020, pp.22-29 and pp.73-74; Jäppinen and Laakso, 2022, pp.11-21).
The Birth of Iron
From 2004 to 2007, over 30 iron smelting operations were carried out in the Struka and Ahvenkoski villages, in Finland. This article reviews the main features of one smelting in 2005, from which the resulting "bloom" was selected as the raw material for the fibula to be reproduced (Jäppinen, 2006, pp.3-17). The project started with finding bog ore, which considered the descriptions of the poem "The Kalevala", and the observations of local people. Ore was found nearby in three different places. A deposit of limonite pieces an approximate size of 25 mm x 50 mm - the size of a fair field - was found in the swamp in Pyhtää, which is now a forest. Two other ore deposits were found on the western branch of the River Kymijoki. One deposit is about 1.5 km northeast of the medieval village of Ahvenkoski, in a swamp between the rocks in Kukuljärvi (Z: 35 m above sea level), with an area of ​​about 3.5 ha.
At the ditch at which the water drained out of the swamp (Z: 15-20 metres above sea-level), the iron had been precipitated into a peat layer several metres thick. Precipitation of ore probably pre-dates the Mesolithic Stone Age and continues to the present day. The ore's iron content was measured as Fe 36.4%. During roasting, the organic matter burned off, and about 20 litres of iron soil shrank into 10 litres of red hematite ore, with an estimated iron content of about Fe 60%-70% by weight (Jäppinen, 2006, p.31). Iron smelting occurred through the senses without scientific measurements. We followed the lessons received from the old Finnish master blacksmith Yrjö Puronvarsi in the spring of 2004, which he had learned from his own father in the 1950s.
Smelting was done in a metre-high cylindrical test furnace cast from aluminium silicate with an inner diameter of 30 cm. The tuyere was on the side of the furnace about 25 cm from the bottom of the furnace. The diameter of the tuyere inside the furnace was 35 mm. Air was blown into the furnace with bellows, and the diameter of the bellows nozzle was 10 mm (cf. Peets, 2003, pp.127-130 and 151). Bellows produced blowing air of about 700 l/min, and weights controlled the operation of the upper chamber.
All of Struka's experiments succeeded and produced either carbonless iron C <0.1%, wrought iron C 0.1%-0.3%, or carbon steel C 0.3%-1%. In one case, high-carbon steel was created C >1.3%, but the cause for carbon diffusion into the molten iron remained unclear. Preheating the furnace took four hours; the actual smelting process took about 3.5 hours. The fuel used was charcoal that Blacksmith Juha Korpela created from spruce stumps (Miehikkälä smithy, Finland). After smelting, the glowing iron bloom was carefully lifted from furnace and compacted first with an oak hammer and then with workshop hammers (See Figure 6).
After cooling, the condensed bloom was reheated in a forge and chopped with a chisel into blanks suitable for forceps and pliers. One blank was further heated again to a white heat (approx. 1250-1300 C°) (See Figure 7), and then forge welded into a symmetrical square bar, causing most of the slag inclusions to splash around. In forge welding, the blanks were protected with quartz sand. This work phase has a connection with the 0.2-2.0 mm sized slag balls found around the Iron Age and medieval forges, which have been found, e.g. around the Haasianiemi and Loviisa Viirankoski smithies (Jäppinen, 2020, p.49).
The Fibula Reproduction
Master Blacksmith Tiia Lahti in Strömfors Ironworks smithy carried out the fibula reproduction to determine what possible method and working steps blacksmiths used in the 8th century when forging fibula. Another goal was to achieve approximate dimensional and shape accuracy compared to the Salme fibula. Lahti started the work by first using industrial steel for two prototypes to evaluate, in advance, the dimensioning of the blank to study the behaviour of the iron and the threading and hammering of the skewers and spirals at different temperatures.
After the prototypes were completed, work continued using "Ahvenkoski bloomery iron". Initially, the slab was stretched closer to the dimensions of the billet, while one forge welding seam of about 10 mm that had torn in the primary forging was sealed. Next, the spiral blanks were forged out (drawn) over an anvil horn, which were hammered and rounded into spirals to the required size (See Figures 8,-10). Lahti gradually approached the dimensions of the blank of Salme's fibula without measurements to the extent that the dimensions could be determined from the photographs:
"I wanted to work in the so-called "by eyes and hands", avoided exact measurements, trusting in my already accumulated professional skills and the fact that hardly any blacksmith has ever had time to measure his work every now and then. The homemade iron was nice to forge, and without any major problems". (Master Blacksmith Tiia Lahti, 25 March 2024).
Before turning the spirals and bending the body into the shape of a curved handle, the back of the fibula was hammered thinner in the middle so that the length of the finished arch became 65 mm, and the thickness of the ridge of the back was reduced to about two millimetres. At the point of attachment of the pin and the pin housing, the diameter of the pin remained 4.5 millimetres (See cover photo). In this way, the fibula became remarkably elegant instead of the general impression of being uniformly thick (See cover photo).
According to the master blacksmith, self-made Ahvenkoski's bloomery iron was surprisingly easy to forge. Bloomery iron is often very heterogeneous and sometimes contains countless slag inclusions. It is because the amount of remaking slag and heterogeneity of the material is influenced by the environment including the hand worked steps, and seasonality of production. In the current reproduction, the carbon content in the measured areas was only C 0.1%-0.3%, and no martensite could develop, so the fibula did not, for example, harden in the air (See Figure 11). Small transverse cracks tore in the uppermost layer during bending, and a new, approximately 10 mm tear near the edge of the pin attachment end appeared.
Cracking may have been born from the primary forging just after the iron was smelted and when probably forging the billet at too low a temperature. About 5 mm from the end of the spiral on the side of the pin house, a fracture was revealed, which extended to the middle of the material. The use of an Olympus MG/ Moticam1080 HDMI microscope revealed a few more transverse hairline cracks in the forge-welded layer of the back of the fibula. They could have arisen from slag inclusions left at the interface of the ferrite phases.
Final Words
The reproduction aimed not to imitate the Salme II iron fibula, to forge it as a gift, or to make it into a museum display case but only to understand the life cycle of the fibula - from the iron soil to the finished object. No major problems appeared, and we learned one possible method that an 8th century blacksmith may have used when forging fibula. The fibula did not differ from the original in a visually significant way except for the width of the pin and the back of the fibula. The pin of the original fibula is half as thick as the base - about 5 mm. The spiral light stripe in the original fibula pin corrosion layer can also indicate that twisted pattern steel may have been used for its raw material (See Figure 1, blue arrows). The back of the fibula was also 7 mm narrower than the original. These dimensioning details were revealed afterwards from more detailed photographs.
The 12 iron fibulas from the Salme I and Salme II ship burials are probably one of the largest collections found in two simultaneous ship funerals from around the middle of the 8th century. With the Salme fibula collection, the total number of iron fibulas in Sweden will rise to 44. About a third of the Salme deceased had an iron fibula in their grave goods (See Figure 3). Researchers have asked whether the users of the fibulas represented a certain family or whether their close circle included blacksmiths (Moilanen, 2015 and 2013). Warriors were at least part of the clientele of blacksmiths, as they were responsible for ordering everyday objects or bladed weapons. However, it is difficult to say whether the fibulas come from an ordinary smithy or a smithy specializing in weapons, where swords, seax, shields, axes, and other supplies were made.
Acknowledgements
I thank Master Blacksmith Tiia Lahti for cooperating and forging the Salme iron fibula from the bloomery iron smelted by the author himself. I thank also to Prof. Visa Immonen Norway and to the researchers in Estonia - Marge Konsa, Reet Maldre, JĂĽri Peets, and Ragnar Saage - for commenting on the manuscript, and for the drawings, photos, and information on the Salme research.
Keywords
Country
- Estonia
Bibliography
Allmäe, R., 2023. Human Skeletal Remains from the Salme II Ship. In: L. Lõugas and H. Luik, ed. 2023. The Salme Ship Burials. Two Eight-Century Mass Graves on Saaremaa Island, Estonia. Tallinn: Tallinn University.
Hedenstierna-Jonson, C., 2020. Entering the Viking Age through the Baltic. In: Kitzler Åhfeld, C. Hedenstierna-Jonson, P. Widerström, and B. Raffield, eds., Relations and Runes: The Baltic Islands and Their Interactions During the Late Iron Age and Early Middle Ages. Visby: Riksantikvarieämbetet. pp. 11-22.
Hedenstierna-Jonson, C., 2006. THE BIRKA WARRIOR - The material culture of a martial society. PhD Thesis. Stockholm University.
Jäppinen, J. and Laakso, J., 2022. Pintaa syvemmältä: Puukonterien mikrorakenteiden tarkastelua. Hiisi 2/2022. Available at < https://www.academia.edu/86370407/Pintaa_syvemm%C3%A4lt%C3%A4_Puukonterien_mikrorakenteiden_tarkastelua > [Accessed 12 November 2024]
Jäppinen, J. ed., 2014. Pajan hämärästä: Sepän kulttuurihistoriaa. Saksa: BoD.
Jäppinen, J. ed., 20 >06. Kymijokisuiston rautakuona. Kokeellisia tutkimuksia No 1. Tutkimusraportti. Fennica.
Jäppinen, J. and Immonen, V., Loviisan Viirankosken vyökoukku ja sen ennallistus. Muinaistutkija 2017:4. pp. 19-30.
Jäppinen, J. ed.. 2020. Rautakymi: Talonpoikia, seppiä, lohiylimyksiä. Saksa: BoD
Konsa, M., Allmäe, R., Maldre, L. and Vassiljevm J., 2009. Rescue excavations of a Vendel Era boat-grave in Salme, Saaremaa. Archaeological Fieldwork in Estonia. pp.53-64.
Larsson, G., ed., 2007. Ship and Society. Maritime Ideology in Late Iron Age Sweden. Department of Archaeology and Ancient History. Uppsala: Uppsala Universitet.
Luik, H. and Peets, J., 2023. Artefacts from the Salme II Ship. In: L. Lõugas, and H. Luik, eds., The Salme Ship Burials. Two Eight-Century Mass Graves on Saaremaa Island, Estonia. Fieldwork and Catalogue. Archaeological Research Collection, Tallin: Tallinn University. pp-34-37.
Lõugas, L. and Luik, H., eds., 2023. The Salme Ship Burials. Two Eight-Century Mass Graves on Saaremaa Island, Estonia. Fieldwork and catalogue. (Archaeological Research Collection, Tallin: Tallin University.
Magnusson, G., 2020. The Iron Industry of Viking times. Key to the modernization of the Nordic countries. Jernkontorets Berghistoriska Skriftserie 51. Stockholm: Jernkontoret.
Maldre, L.,2011. Salme I Paadi Arheozooloogiline materjal. Kaheaastaraamat 2009-2010 Saaremaa Muuseum. Kuressaare. pp. 30-47.
Moilanen, U., 2013. Merovingiajan (n. 550-800 jKr.) rautaiset sankasoljet Archaeology of Personhood -teorian valossa. Pro gradu -tutkielma. University of Turku.
Moilanen, U., 2015. Hauta-antimena sankasolki - Kuka käytti rautaisia solkia nuoremmalla rautakaudella? Kalmistopiiri 9. Available at < https://kalmistopiiri.fi/2015/05/09/hauta-antimena-sankasolki-kuka-kaytti-rautaisia-solkia-nuoremmalla-rautakaudella/> [Accessed 12 November 2024]
Mäss, V., 2008. Salme laevaleiu ehitustehnoloogiline interpretatsioon. Estonian Maritime Museum.
Peets, J., Allmäe, R., Maldre, L., Saage, R., Tomek, T. and Lõugas, L., 2012. Research Results of the Salme Ship Burials in 2011-2012. Archaeological Fieldwork in Estonia.
Peets, J., Allmäe, R. and Maldre, L., eds. 2010. Archaeological investigations of Pre-Viking Age burial boat in Salme village at Saaremaa. Archaeological fieldwork in Estonia. Tallin: Tallin University.
Peets, J., 2003. The Power of Iron. PhD Thesis. Tallinn Ajaloo Instituut.
Pleiner, R., 2006. Iron in Archaeology - Early European Blacksmiths. Prague: ArcheologickĂ˝ Ăşstav AV CĚŚR.
Pleiner, R., 2000. Iron in Archaeology - The European bloomery smelters. Prague: Archeologicky Ustav AV CĚŚR.
Price, D. T., Peets, J., Allmäe, R., Maldre, L., Price, N., 2020. Human Remains, context, and place of origin for the Salme, Estonia, boat burials. Journal of Anthropological Archaeology 58, pp. 1-13.
Price, D. T., Peets, J., Allmäe, R., Maldre, L., Oras, E., 2016. Isotopic provenancing of the Salme ship burials in pre-Viking Age Estonia. Antiquity 90(352), pp. 1022-1037.
Ragnar S., Jüri P., Priit K., Priidu P. and Mart V., 2017. Metallographic Investigation of Iron Blooms and Bars from the Smithy Site of Käku, Estonia: Fennoscandia archaeologica XXXIV, pp.46-58.
Saage, R., 2020. Metalworking Sites in Estonia during the 7th-17th Centuries. PhD Thesis. University of Tartu.
Saage, R., Peets, J., Kulu, P., Peetsalu, P. and & Viljus, M., 2017. Metallographic Investigation of Iron Blooms and Bars from the Smithy Site of Käku, Estonia. SARKS: Fennoscandia archaeologica XXXIV. pp.46-58.
Selirand, J., 1989. Viron rautakausi. Pohjois-Suomen historiallinen yhdistys. Oulu.
Zachrisson, T., 2020. Viking Age society, its realms and the importance of iron. Reflections on the historical background and emerging networks. In: C. Karlsson and G. Magnusson, eds., Iron and the Transformation of Society: Reflexion of Viking Age Metallurgy. Stockholm: Jernkontoret, pp.89-140.