Podcast:
Seen Through Glass
Next Episode
Previous Episode
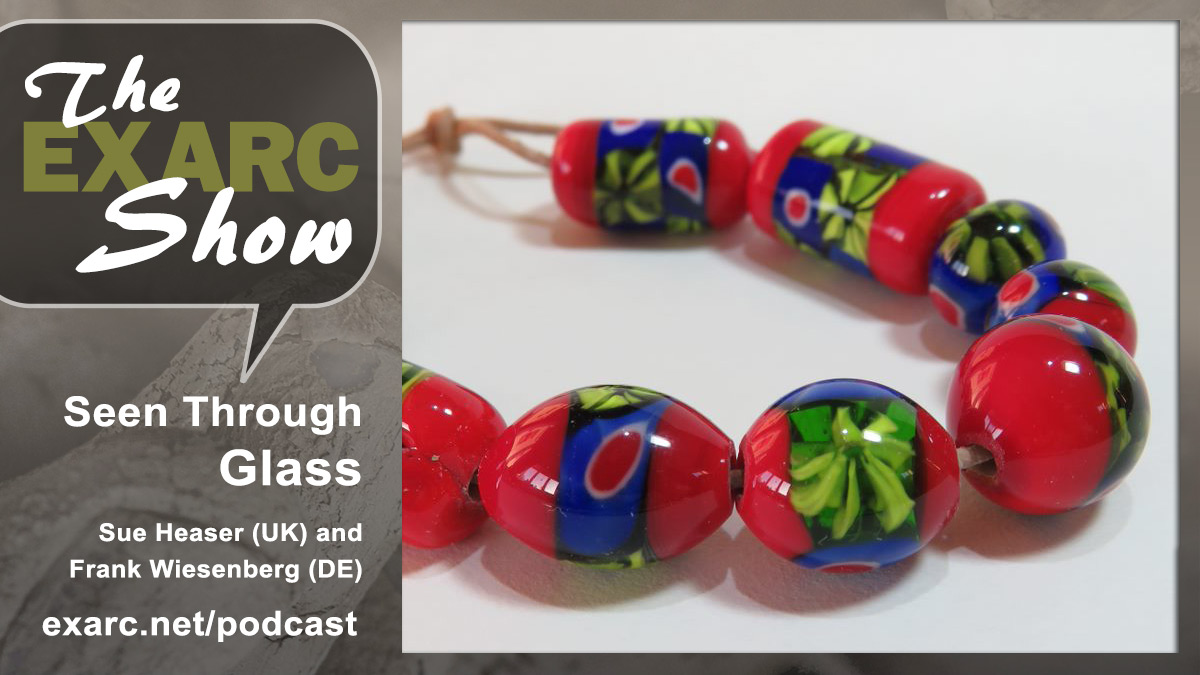
From drinking vessels to jewellery, glass is found in archaeological assemblages all over the world. Our guests Sue Heaser and Frank Wiesenberg join us on this month’s episode of Finally Friday to shed light on how experimental archaeology can help us ask new questions of this important material. Phoebe Baker is the host of this show.
EXARC Member: Sue Heaser (UK) Sue studied Archaeology at the University of Exeter and her early career was as a Finds Assistant for the Museum of London and then as an Archaeological Illustrator for what is now English Heritage. Her drawings of Anglo-Saxon finds in particular are published in many archaeological reports and publications. She studied jewellery making and many other traditional crafts in order to better illustrate artefacts and this led to a career writing many books on a wide variety of crafts... Read More |
EXARC Member: Frank Wiesenberg (DE) Starting in 1996 with Roman crafts living history demonstrations, I co-founded the project "Römischer Vicus", presenting several demonstrations of a dozen craftspeople on the website www.roemischer-vicus.de and attending Roman living history events in Germany, the Netherlands, Belgium, Austria and Switzerland... Read More |
Phoebe: Hello and welcome to #FinallyFriday. This chat session is run by EXARC, the society for archaeological open-air museums, experimental archaeology, ancient technology, and interpretation. My name is Phoebe Baker and today I am joined by two specialists from our EXARC community focusing on glass. Sue Heaser is an archaeologist, artist and author with specialisms in hot glass bead making. Her experience in both modern and archaeological jewellery making often gives a unique insight into how ancient materials were used and her current research focuses on reconstructing and understanding Anglo-Saxon and Roman British bead assemblages in the UK. More recently, this research has moved towards considering how glass’ physical properties can be affected during the glass working process. Frank Wiesenberg is a specialist in Roman glass furnace reconstruction and operation. These reconstructions are based on both literary and archaeological source material, as well as the practical knowledge informed by a background in mechanical engineering. He has experimented with both large and small furnaces and has set up replica workshops at a number of places, including the archaeological park Roman Villa Borg. Frank finished his master's degree in archaeology at the Roman Provinces in 2019 and is now currently the executive director of the RömerWelt museum near Bonn, Germany. So thank you, to both of you for joining us. I have a quick question to start you off. Why do you think it's important to look at glass? Sue, would you like to start?
Sue: Well, glass is one of the most fascinating materials known to man, I would like to say. Obviously I'm biased because I find it so interesting myself, but glass has been part of the craft repertoire of the human being for thousands of years and it crops up all the way through archaeology or every excavation will produce a little glass most likely from all over the world. And so, because it's so universal and so many amazing things can be done with it, once we start studying all these details, I feel that it can start throwing a lot of light on how people worked, what they did, what they needed, what they created. Generally it's a fascinating and very broad subject.
Phoebe: Thank you. Frank, do you have anything to add?
Frank: For me two things concerning glass are very important. First vessel glass and glass windows were introduced in the period I'm focussing on, in the Roman Empire. So for me, for researching and also for teaching purposes hot Roman glass is the most fascinating material. And the other thing is, I've worked with several different materials, so starting with wood, bone, later using amber, bronze or even iron, glass is the most complex material concerning the knowledge of the material itself, its composition and also the infrastructure which is essential for glass working in order to make nice objects which can be used for museum’s educational programs for example.
Phoebe: Thank you Frank. To follow on from that, how frequent is glass usage in your particular periods and can we see any patterns in glass usage at the time?
Frank: In the Roman period glass was very, very frequently used. We see the first appearance of glass windows in bath houses and domestic buildings as well as in office buildings and even workshops. So this requires the manufacturing of glass all over the Roman Empire. This local production, which seems to pop up during the first century, also includes vessel glass production, which is much more than bead making, or making glass bangles. These crafts were carried out all over the Roman Empire. So it looks like during Roman times there also is a change in the use of the material glass, which is very interesting for me to take a closer to look at.
Sue: I was initially looking at quite a narrow period of time, which is really fifth and sixth centuries. It’s mostly from cemeteries that we get the glass found in Anglo-Saxon times. And as it's only within a couple of hundred years that I'm looking at there is a slight movement of glass usage, certainly in the bead side of things. I'm no specialist on vessels, but beads do change slightly, what you're discovering in the graves. But, again, yes, glass is frequently used. When you excavate an Anglo-Saxon cemetery, a very large proportion of the female graves do contain glass. I mean, obviously it varies between cemeteries but thousands and thousands of glass beads are cropping up. Vessels, which are absolutely beautiful, are less frequent. So I think many, many Anglo-Saxon women wore glass beads. So it was very important in their society. One wonderful thought is the glass colours in these colourful beads must've been absolutely stunning for them. The only other colour they would have had of that intensity would surely have been probably flowers. So I find that quite exciting that they were able to have this beautiful colour as part of their lives, because even dyeing clothes... the colours from natural dyes are much more muted than glass. So it must've been very exciting for an Anglo-Saxon woman to have had such brilliantly coloured pieces and the glass provided that in their society.
Phoebe: That's such a wonderful way to think about it. I've never really grasped how beautiful they must have been and how colourful they must've been. I've seen some natural dyes and they can be quite dull sometimes. Do you think experimental archaeology can tell us about archaeological glass in ways that more traditional approaches can’t?
Sue: Well, yes, I really think that experimental archaeology in glass is absolutely vital. It's no good to just study the ancient glass if you don't have some sort of understanding of glass techniques and I do feel that this is reflected in existing literature to a certain extent where people are writing reports when they really don't understand how glass works. And you do get a lot of error creeping in. There's one where almost all reports describe how any patterned bead has been marvered. And this is actually wrong because when you melt a bead that you have decorated with applied decoration of glass, you just need to keep turning it in the flame and the added decoration will sink smoothly with a shiny effect and completely flush with the surface. There is no need to use this very overused term called marvering. You don't need to push the decoration in. And this is something that a lot of people who are writing reports in the past have not understood. And that's a shame. It also means that if people study how glass actually works, you'll get better terminology, that will not be purely archaeological terminology. It will tie in with terminology of modern glass workers which is quite an important thing that we're all talking the same language. So I can see experimental archaeology in glassware - well, like most other things - it's going to be extremely important. And I feel that it should be done a lot more than it has been in the past. What does Frank think about that?
Frank: I do agree to your point of view, Sue. Actually, if you take a look at the history of glass archaeology, I think it was in 1908 when the German book ‘Das Glas im Altertume’ was published by Anton Kisa. His idea was to compile most knowledge on Roman glass making and on the vessel glass of that day to a nice handbook on Roman glass making. It was a very good approach at that time. It's more than a hundred years ago and many things mentioned there still have their archaeological value today. But a couple of ideas which were published at that time were just one possible way of explaining the things which were evident on Roman small finds. For example window glass: Kisa introduced the idea of cast window panes. The idea was to either have a dry wooden board, a dry wooden mould or a watered wooden mould - and the idea was to cast glass at a temperature of more than a thousand centigrades into this wooden mould. Well, what actually happens if you try to do something like this, either the dry wooden mould would start to burn or the water trapped inside the wet wooden mould would try to evaporate and you would get everything but a nice even window pane. So the idea sounded nice at that time - but more than a hundred years later, we should be at the stage to try to evaluate, to verify or falsify these theories. And this includes trying to reconstruct the glass recipes themselves and try to reconstruct the tools, if possible, and also try to reconstruct the infrastructure to seriously try out these things. But things got even a little worse in the late 1990s, when in German archaeological publications the ideas of ‘glass pottery’ were published. This meaning to try to use hot glass at a temperature of more than thousand centigrades - and pour it onto a rotating potter's wheel. Well that's not something which I would really recommend. So after all, this had to be tested and it has to be tested again and again, and again, to try to verify and to falsify these theories, which are already published. The regular archaeological excavations and even the analysis of small finds can’t really satisfactory answer these questions. So it has to be tried out using experimental archaeology.
Sue: Yes, I quite agree. And also if you're testing these things, I end up with a lot of waste glass from when I'm making beads and trying to restrict myself to the contemporary tools of that time. And the waste is something that when I show archaeologists what I'm doing, they pounce on my waste with such interest, because obviously this is what we are going to be looking for in excavations, but until you've actually seen what waste looks like, it could be quite easy to miss it or to misinterpret it. So that's another interesting angle, the waste products, as well as the tools you would be likely to use.
Frank: Well, if we're talking about archaeology, waste is always one of the best sources for information and this is exactly what happened at the workshop of Mark Taylor and David Hill, whose work I really do favour. They have started reconstructing Roman glass, Roman glass working techniques and even the furnaces, back in the late 1980s, and started a Roman furnace project in 2005 and 2006. These projects offered the opportunity to collect the waste products, to collect information on the furnaces, to collect the ashes and try to get them analyzed to build up some information which can be compiled and can be compared with the Roman evidence from excavations. And these were the sources which cannot be provided by any other discipline of archaeology, apart from experimental archaeology, in my opinion.
Sue: That must be absolutely fascinating to collect all... as I've been doing, I'm just collecting it in a tin, the waste glass, but if you've been reconstructing the furnaces that you do, I find that absolutely amazingly interesting. I'm cheating a bit. I am just using a very simple blowtorch of the type called a Hothead and it's just a single gas - it's not adding any oxygen - so I'm keeping it as simple as I possibly can, but I would very much..., oh, if we can get to the point where we can all travel again. I've been looking at your amazing furnaces and thinking it would be so fascinating to actually be creating objects with your replica furnaces, that would give you such insight into the techniques. I think this is, again, more experimental archaeology... is really absolutely championing this. I was just going to say I would be absolutely delighted to come and try because so far I have been purely using my gas torch because I wanted to do a lot of intense work. And I feared that if I started trying to reconstruct a small furnace in my garden… I'm not very far from West Stow museum and I've been talking to the lovely people there about creating a furnace, but it would be so much better to work with someone..., not reinvent the wheel and come to somewhere like the furnaces that you're working on, and then try out some of these very advanced techniques that I've been developing, trying to create, recreate Millefiori, which honestly is the hardest thing I have ever done in my entire life. Those ancient bead makers were amazing, but rather than me have to start from scratch and learn how to make kilns, it's so good if we could collaborate and I could use your expertise in order to further what I have been doing it would be extremely useful. And this is where collaboration comes in, isn't it? It's such an advantage to us when we can work together with people who have concentrated in particular areas.
Frank: Yes definitely. And after the Corona era I hope it will be possible again. I was just sort of pushed into the topic of reconstructing Roman furnaces, those hot vessel glass workshops, and also small bead furnaces when trying to scale down things actually. For the bead furnaces, I wasn't convinced of the layout such as I have seen on different museum’s events or medieval markets. I wasn't convinced of medieval people or Romans using gas torches - even if they were disguised as cute little dragons. And also I wasn't convinced of the use of charcoal and bellows, because it's not the correct flame for glass working, in my opinion. So as I tried to scale down these layouts which I had already worked with, I found that using just a small shaft furnace with a collar to protect the burning fire from side winds provides an even, steady flame of 850 to 950 centigrades which would be perfectly suitable for bead making. It's a totally different thing compared to using a gas torch, because it's a very wide diameter flame. It's not very focused. So when you're comfortable with working with a gas torch, you might be the first time, at the first trial, a little bit uncomfortable with the flame of a wood-fired furnace, but in my opinion, most beads, and other things which are evident in the field of Roman and medieval beads, can be worked with these open flame furnaces.
Sue: Yes, this is incredibly relevant to what I have just been working on. In fact, in the last few days, I have been working on creating some spiral Millefiori canes, and some of the others that are more complicated, and I have been getting very frustrated with the width of the blow torch. It just doesn't give me the sort of area of heat that I need. And it's making me question as to whether people were actually using a furnace to create these Millefiori canes or if they were using a volcano type furnace with a wide aperture. And I just feel that the blowtorch is the worst thing to be using to recreate this and it's probably making it even more difficult than it is already because I can't make a big enough matrix that I can then pull into a cane because you make this mass of glass with the pattern inside with a diameter of about five centimeters. And the whole thing is probably about, ideally, 10 centimeters long. This is working quite small and then you get it to the right temperature and you pull the two ends apart. So they go thinner and thinner until you get these... and then you can chop it up into slices to decorate the beads. But if you can't keep that mass of 10 centimeters with a five centimeter diameter warm, which is very difficult to do in a blowtorch, you get a lot of cracking and problems. So the sort of furnaces that I have seen that you have been working on would be absolutely ideal to do this. It's actually harder to do it with the modern equipment. One would have to adapt though, because I would imagine that..., but you're getting the same temperature. My torch is around 900 centigrade, apparently, I haven't got the facility to measure it, but that's what I'm told. And I gather that you're getting that sort of temperatures around your furnaces, aren't you?
Frank: In fact I do. I think, since I recently got to the idea of also making mosaic canes, I think you might love the flame and heat of a wood-fired shaft furnace, Sue. Just a couple of weeks ago I did build two small bead furnaces at the Archaeological Park at Kempten in Bavaria in Germany. The slightly larger of them easily exceeded the temperature of a thousand centigrades. I thought, well, wouldn’t it be nice to try to melt some Roman glass fragments, some reconstructed Roman glass fragments, basically - some sherds - to fuse them together to a small rod and try to pull some canes for bead making? By the way, this is a question which I get frequently asked on events and demo’s: how do the Romans or how do medieval people make their raw glass? How is the glass supplied? How do they work? Do they also use canes? How are the canes pulled? I tried to demonstrate an easy solution to do this - just live - on this kind of furnace, and since this went very, very well I decided it could be just a small experiment: just compile some nice colours to mosaic glass and I pulled some long mosaic cane. I think I was starting with a diameter of close to five centimeters and a length of at least eight centimeters. I think it's been close to the dimensions you’re requesting, Sue.
Sue: Right, interesting. So this is the similar size that we've ended up working at. I have been looking at videos of people making canes today. And they're working out of big furnaces and making... the masses then are enormous. They start off with a cane... well, the matrix for the cane is - I'm just holding my hands out here even though we're just on voice - and you've got 15 centimeters diameter and then probably 20 centimeters long, and then they will get a very long cane indeed. But for that you'd need a big glory hole to work inside. So I'm most intrigued that you've been doing the same thing working with your furnaces. And I'm also very interested to hear that you're finding that just wood, no bellows and no charcoal and that works well, you say…
Frank: Actually it works very, very well. And it's just a sort of a proposal. We don't have the archaeological evidence which really tells us anything about the upper structures of the furnaces if you take a closer look at some Roman or early Medieval workshops for bead making for example. For glass furnaces intended for vessel glass making it is a little bit different, because glass vessel furnaces need to be that large or that tall that some parts of the furnaces have to be embedded into the ground. So there are parts which have been dug into the ground, they have a decent chance to survive in archaeology. So we have a good layout plan for these types of furnaces, but even with the larger furnaces for glass making we don't have good valid information about the upper structures, because if these furnaces were built from daub, just prepared loam, even fired daub, it doesn't have a very good chance to survive our weather conditions when it’s freezing during winter time. And concerning the small workshops, I learned - when I did give a small lecture on my first couple of reconstructions of bead furnaces - a lecture which I gave at a small convention in Germany – well, I was just telling, we don't know anything about the bead furnace workshops apart from the small working waste, but I didn't know very much about the remains of the furnaces. In my opinion, that’s possible because the furnaces can be that small, so they were not dug into the ground. So there's basically no solid footprint left from these furnaces. But just the very first lecture which was given after mine, they displayed this bead workshop from the Zürich lake area and they were actually presenting just the right layout plan, which I was looking for, just a layout plan of roughly 60 by 40 centimeters, almost a teardrop shape, a pear shape. In fact, this is exactly the dimension of the furnaces I tend to work with for making beads.
Sue: Well, that's brilliant, isn’t it, how very satisfying, it sort of came out right. I have similar delights when I've been running around all the museums in Britain and one or two in Europe as well and photographing in great detail so many of these ancient beads and I try and work out how to make something. And I have had so many failures, you have to be so tough about this. You'll just have to pick yourself up and start again if it doesn't work. I was trying to work out how to make a very flattened, spiral bead and it took me ages. It seems so simple. And I thought that surely they make a flat bead and then they apply the spiral to it. And it just looked dreadful and I couldn't control it. And then I woke up in the middle of the night and thought I wonder..., and so I've got an idea. And so I made a round bead, applied the spiral, which is easy because you can just turn the mandrel with a bead on it and then I used my tongs to flatten it and it looked absolutely right. So I rushed to all my photographs of this particular type of bead and a bit like your delight with the furnace being right, there were the tong marks on the decoration to prove that the decoration had been added and then the bead had been shaped, which was the opposite to what I originally had imagined. And when you see the old tong marks still there in these 1500 year old beads and you realize you've got it right. And that's so exciting, isn't it? One little more puzzle [piece] fits in. It's really great.
Frank: Exactly the things I had to learn. Actually I'm not a bead maker, I don't consider myself to be a bead maker or even a glass maker, or a maker of glass vessels. The only thing I can do with this kind of hot material, the only capabilities I have is just to demonstrate that the furnaces are working. But I'm working on that issue and I'm trying to teach myself glass making and I also try to teach myself bead making. And it's very, very fascinating to use the infrastructure, if it works, to use the infrastructure, to teach yourself something which you've never known before. It is fascinating to take a closer look at the remains of the original furnaces and try to reconstruct them, first in your head and then try to get your fingers to follow the ideas in your head. And that's a problem, actually, what I'm struggling with most of the times. I have a certain idea, but I'm not capable to really carry it out - yet.
Sue: Yes, I've had many experiences like this and you just have to pick yourself up and keep going. In the last few days I've been working... trying to push myself into making more different types of cane and the trouble is, you've conquered one type and you think, well, therefore I must be getting better because I mean, my learning curve has been really steep and I keep struggling away, but having worked out one type of bead or one type of mosaic cane or something doesn't necessarily mean that you've now got the experience to try another one. Every new item you make it seems is another learning curve. I mean, obviously you generally become better at handling your tools and your heat source and so on. So I think it's amazing that you are actually using what looks very strongly likely to be what the ancient bead makers used in the way of their furnaces. Well, that makes it even more realistic. So I really do think that's an excellent way to go.
Frank: I hope that we have the most realistic approach with these projects. Basically, my idea is to keep it as simple as possible. In my opinion, this is what the Roman culture shows in many, many small things and small ideas. And also, I think I am a very lazy person. So if I can try to figure out a nice workable infrastructure which I can use with just a little bit of small branches of wood, just leftovers from other projects or whatever, just any type of wood which is lying around and being dried for long enough so that it does work and burn well - and if I can try to establish an infrastructure which can be used for bead making or even a little bit more, then it can't be that wrong - in my opinion. As I told you before I am quite lazy. I can operate the small furnaces by myself, even for vessel glass blowing. That’s ok. But I don't need to rely on anybody operating the bellows. I also had the experience of making charcoal to be involved in a big project over here in Germany, of making, let's say more than 10 tons of charcoal. That's a really interesting project which runs for close to 10 days. It's a very dirty project too, so I really like to restrict the use of charcoal to processes, which strictly rely on the charcoal as an energy source and to try to use a simpler source of energy for any other purposes. That's the approach I favour for most of the projects I do.
Sue: Yes, that absolutely makes sense. And another question I'd like to ask you, please, Frank is, when you're making beads with one of your furnaces, I presume one of the smaller furnaces, how much wood do you actually need? I'm just trying to imagine a bead maker, say, working on his own or her own. To do a day's bead making, how many sort of kilos of wood would you need? Would it require a lot of resources?
Frank: Oh, definitely not. I would say it depends on the length of time to work, on the time span and also on the layout and size of the bead furnace, but normally it's a small wheelbarrow of wood which we tend to refill twice or three times a day. So I believe it's less than 50 kilograms of wood, much less as I recall.
Sue: That's really good news to me because what I'm imagining is from all my study of the beads in Britain for instance - because I very much feel that the Anglo-Saxons, they came immediately after the Roman period in Britain and so the techniques would have overlapped, would have just carried on much the same, but the idea... I'm finding that in the evidence of the beads that are found, it seems to me that there was certainly one small unit or maybe only one individual who made a significant number of a very distinctive type of bead. They're very beautiful. They're red, they've got a twisted cable decoration on them and I call them my twisted yellow-green beads, or twyig beads. And I feel that this must... may very well have been one person, or a family unit maybe. And so what you're saying about a furnace is they could have gone, moved around the country. They could have perhaps built a furnace in a few days and settle down and made their own beads and not actually needed huge resources of wood and then moved on. The furnaces would all wash away in the rain, so no evidence...
Phoebe: So thank you both for that really interesting discussion. It was a pleasure to listen to. As a final question: what are your plans for the future and how can the EXARC community help to make a difference in regards to the points that you discussed today? Sue, would you like to go first?
Sue: Well, I find I mustn't plan too far ahead because I keep making new discoveries all the time and that sends me off in a zigzag all the time, another branch. My most recent interest though, is I have found that I've started working with different types of glass, just some old beach glass I had picked up underneath a medieval castle and I found a huge difference in the handle of this glass compared to the modern glass, the coloured glass that I'm using to make beads, which comes from Venice. It's the Murano glass and matches the ancient glass as closely as possible, the soda lime. And so I'm now very, very interested in trying to try making beads with some ancient glass and I've just applied to the Museum of London, because this is obviously destructive and I'm really in hope that either they will say yes, or else I can find some other organization that maybe... what I'm really after is the coloured glass and it seems very likely that tessera, as it was used at Riba... all the brightly beautiful colours from mosaics, whether it was the bead maker's glass as well or is very similar. And they certainly..., the museums, strangely enough they won't let me melt beads. It's very, very sad, but understandable. I'm not allowed to start melting all these artefacts, but some sites, certainly in Europe, have produced vast quantities of coloured tesserae and if it could only be possible to get permission to try making beads from them it would give me a much better feeling as to the ancient glass that was used by the ancient bead makers. And if I could use one of Frank's replica furnaces at the same time, then I think I would have total joy. So that's where I'm hoping to go.
Frank: Sounds like a very nice plan to do, I’m looking forward to this, Sue! I have just finished a teaching project at the Glasfachschule Rheinbach, which comprised of more than a week of Roman glass making on a small Roman style furnace. And I'm heading for a weekend of bead making at the Archaeological Park Roman Villa Borg - there are also a lot of plans for next year because next year will be the International Year of Glass. There are a lot of promising projects, which also could include reconstructing a small glass workshop for glassblowing at the Archaeological Park in Kempten, Bavaria. And also if it's possible, if I can find a place and get the funding, we'll try to reconstruct a small workshop for hot glass making at the museum I’m conducting right now, the RömerWelt museum at Rheinbrohl in Germany. Actually I think these are enough plans because I try to keep in contact with most of the places where there are some furnaces and I try to work at these places and try to get more people involved with the topic of hot glass. And also I like to invite all the EXARC members to get more knowledge about hot Roman style glass, try to visit a project, and maybe even try to reconstruct a small furnace by themselves. If I can do it, almost everybody can!
Phoebe: They sound like really interesting plans from both of you. And thanks again for joining us.