The content is published under a Creative Commons Attribution Non-Commercial 4.0 License.
Reviewed Article:
An Experimental Diachronic Exploration of Patination Methodology of Dark Patinated (Arsenical) Copper Alloys on Case Studies from the Eastern Mediterranean Bronze Age and Early Iron Age
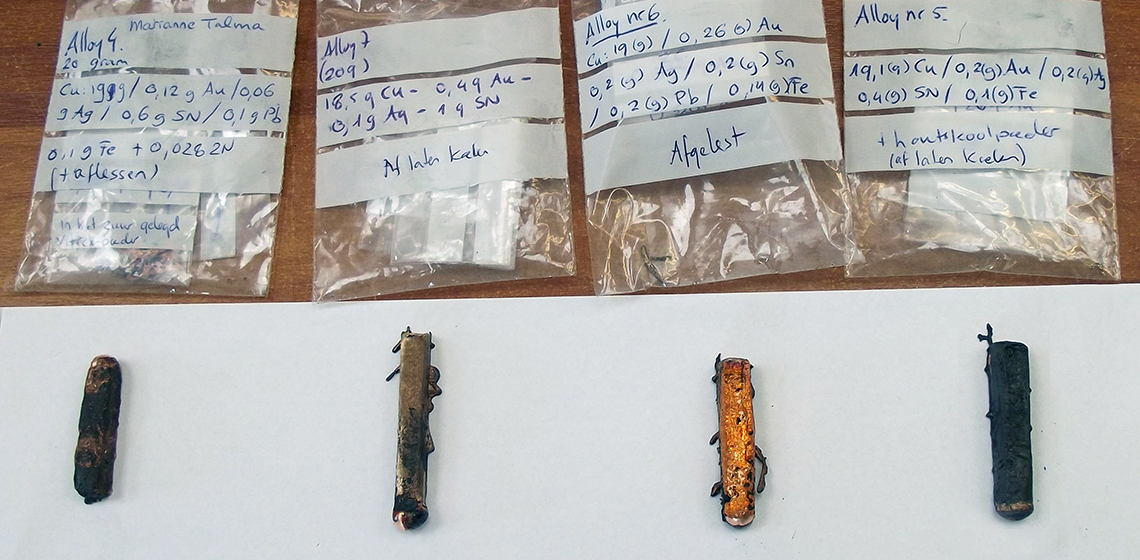
Artificially patinated copper alloys are found archaeologically in polychrome artefacts from the 19th century BC Egypt to historical and contemporary Japan. The unusual colour variations observed in these patinas, ranging from black to blue to purple, is due to a minor amount of gold (Au) and silver (Ag) in their copper matrix, whereas accompanying elements such as tin (Sn), iron (Fe), and arsenic (As) might influence workability, hue or shine.
Their patina consists of cuprite (Cu2O) however sometimes it may also contain tenorite (CuO). The process in which artificial patination was achieved in prehistory is unknown, however specialized knowledge exists for the production of the modern Japanese irogane alloys. As part of a master’s thesis project (Talma, 2015), the goal was to explore possible patination agents feasible for the Eastern Mediterranean Bronze Age, and to investigate observations put forward by Giumlia-Mair and Lehr (1998; 2003). Production of 4 arsenical copper alloys and material analysis (ICP-OES, SEM [ICP-OES: Inductively Coupled Plasma – Optical Emission Spectroscopy; SEM: Scanning Electron Microscope.]) was done in laboratories of Deutsches-Bergbau Museum in Bochum (Germany), while 4 arsenic free copper alloys were cast in a goldsmith’s workshop (Birgit Doesborg) in the Netherlands. A polymetallic eutectic was observed in the production of the alloys which raises questions with regard to other experimentally produced samples and production choices in antiquity. Common salt (NaCl) represents one possible patination ingredient to compare with the archaeological material, and corroborates earlier work by other authors. The author is greatly indebted to communication and help from experienced goldsmiths David Loepp (IT), Louis Hankart (NL) and Birgit Doesborg (NL).
Artificially dark patinated copper alloys appear in various times and regions and are commonly applied in prestigious polychrome metallic objects. Currently, the earliest finds known are from ca. 2000 BC in Egypt (See Fig. 1) and Palestine (See Fig. 2), followed by ca. 1500 BC in Greece and Cyprus (See Fig. 3 and 4) and again during the Roman period from ca. the late 4th century BC (See Fig. 5 and 6).
They also appear during the medieval Islamic world and at least from the (early) medieval period (9-14th century) in Asia (Burma, Tibet, China, Korea and Japan), the latter of which exists a long craft tradition extending up to recent times whose production is still a subject of research (See Fig. 7-10.). One source considers the possibility that surface manipulation on bronze was already practiced during the Shang dynasty in China, between 18th-11th century BC (Notis, 1988, p.315).
The process by which artificial patination on copper alloys was achieved in antiquity and prehistory is unknown and still investigated (e.g. Pacini, 2004; Campanella, et al., 2011). Some researchers propose that iridescence and (assumed) regenerative properties of the patina motivated manufacturing choices of dark patinated arsenical copper alloys (e.g. Giumlia-Mair and Lehr, 1998; 2003). The production of these patinated copper alloys was specialized knowledge and labour intensive, as can also be gleaned from the complexity of manufacture of objects where they were applied in. They were used as the base material inlaid with other metals or as inlays themselves in ritual statuary and (ceremonial) weaponry, in silver tableware and other fineries (found in tombs and other ritual contexts).
The focus of the author’s experiment in her Master’s thesis was to test possible patination agents feasible for the Bronze Age, the colour range of experimental alloys based on published compositional analysis of artefacts and to investigate whether arsenic is responsible for an iridescent effect on the patina.
The occurrence of similar alloys in various time periods and regions in the world with a seemingly similar prestige or value is intriguing. For the Eastern Mediterranean Bronze Age, a knowledge transfer is plausible (e.g. between Egypt, Syro-Palestine, Greece and Cyprus). However, with a larger diachronic and physical distance involved, multiple independent inventions should be considered, next to the possibility of a rediscovery or continual development.
The prehistoric alloys resemble more recent patinated copper alloys, such as a few of the Japanese irogane alloys (Hallam, in press.), the Chinese wu-tong, the Burmese mylar (van Bellegem, et al., 2007) and possibly a Roman period alloy that has been equated with corinthium aes despite the fact that authors in antiquity did not describe corinthium aes as black (Jacobsen and Weitzman, 1995 contra Giumlia-Mair and Craddock, 1993; Craddock and Giumlia-Mair, 1993).
A recent article also refers to possible Anglo-Saxon counterparts (Benzonelli, Freestone and Martinón-Torres, 2017, p.1034). These artificially patinated copper alloys appear to have been admired for their unusual range in colour from black to blue and purple in prehistory to a wider range of colours (at least) since Roman antiquity.
In particular, (historical) Japanese irogane alloys have achieved a great variety of colours (with several shades and complexity). Some of these copper alloys resemble the descriptions and appearance of the Tibetan dzñē-kṣim alloys (See Fig. 7) and related alloys of the Himalayas (see Fig. 8) taken from Buddhist texts (Dagyap, 1977, pp.51-57). The texts describe that when these copper alloys were treated with a special solution, the colours of the rainbow would appear on the surface, an effect also visible when the material was held up in sunlight. The earliest reference to the use of these alloys is linked to a contemporary of Sakyamuni Buddha who lived in the 6th or 5th century BC (Dagyap, 1977, p.52).
In the following paragraphs, diachronic examples will be briefly described to understand the procedures followed in the author’s experiments, but will hopefully also prove helpful to those interested in working on this topic.
The historical and recent Japanese alloys and patination method
William Gowland was one of the first Westerners to document traditional Japanese metalworking in the late 19th century, essentially employing a combination of (ethno)archaeology, material analysis and experimental archaeology (Gowland, 1915).
Up to the late 19th century, the Japanese alloy shakudo was made from a polymetallic ore (yamakin, mountain gold: a gold bearing quartz with accompanying elements) or from the artificial alloy niguromé (Hallam, in press.) The earliest reference to this dark patinated copper alloy applied in weaponry dates to the 12th century AD (Oguchi, 1983, p.125).
Shakudo is one of the dark patinated irogane copper alloys that was used for ritual statuary or as inlays in the fittings of Japanese swords (See Fig. 10) (Gowland, 1915; Notis, 1988; Hallam, in press). There are several recipes for creating shakudo, although usually it is a binary alloy of copper and gold (Uno, 1929, p.121; Ó Dubhghaill and Jones, 2009, p.290). It is also possible to use kuromido (an alloy of copper and up to 10% arsenic). However, artisans seemed to have deliberately chosen unrefined copper for producing the irogane alloys when they could have opted for pure copper in the Edo and Meiji periods (Hallam, in press).
Even with historical descriptions for the Japanese patination method, its complexity and sensitivity both require inside knowledge and trial-and-error to achieve successful results (the author is a novice with limited experience) (see Gowland, 1915, p.92; Hallam, in press).
The author created a binary shakudo alloy (96% electrolytic copper, 4% gold) to be used as an alloy in a mokume gane plate during her goldsmithing studies in 2005 under the supervision of master goldsmith Louis Hankart (See Fig. 32). The shakudo patinated deep black after wearing the ring containing it for several days (due to natural chlorides and acids of the hands).1
Mokume gane (wood grain metal) is a decorative technique similar to damascening, where several plates of metals are fused together (traditionally through autogenous welding without the use of a solder). In the resulting plate figures are chiselled or drilled (never deeper than halfway) to create patterns while the plate is hammered out.
A recent experiment showed that rings made with combinations of copper alloys (like shakudo) and noble metals are in fact subject to galvanic corrosion, and will eventually deteriorate completely due to the interaction with skin products and water. There is less of a risk from application in other types of jewellery (Binnion, 2015).
Traditionally, the shakudo alloy was cast in a big bucket of water (70-90°C) and a thick cotton casting form framed on a metal wire (the name of the process is yudokobuki) – this is thought to limit the exposure to oxygen during casting and cooling, and to reduce the porosity in the resulting alloy (Uno, 1929, p.122, Table 2; Notis, 1988, p.317; Ó Dubhghaill and Jones, 2009, p.301).
The commercial patination solution (rokusho) was until recently a manufacturing secret that several authors and goldsmiths tried to figure out and elaborate upon by experiments (Untracht, 1982; Murakami, Niiyama and Kitada, 1988). What rokusho traditionally refers to is a special kind of verdigris (copper acetate) mixed with a carbonate such as crushed seashells, that in turn is an ingredient for the final patination solution (Niiro), to which sometimes alum is added (Ó Dubhghaill and Jones, 2009, p.289; David Loepp, pers. comm., 23 June 2015).2 Analysis of commercially produced rokusho (as an ingredient for Niiro) with X-Ray Diffraction (XRD) analysis detected calcium carbonate (CaCO3) and sodium chloride (NaCl), where the copper acetate (verdigris) was likely present in amorphous form and therefore not detectable by XRD (Ó Dubhghaill and Jones, 2009, pp.307, 320).
The traditional name for the final patination solution is Nikomi Chakusoku or Niiro.
The earliest archaeological evidence of the Niiro process dates to the 12th century, but some textual descriptions are known from the 8th century (Oguchi, 1983, p.125).
The Japanese patination process is a combination and succession of alkaline applications of a lye (Gowland, 1915, p.92), rasped Daikon (Japanese radish) and immersion of the copper alloys in mildly acidic to neutral solutions. Surface preparation and cleanliness is very important (preventing greasy fingerprints or tarnishing during the patination process). To prevent this tarnishing, the alkaline Daikon was applied immediately when the metal was taken from the patination liquid. The author rinsed them briefly in water before returning them in the solution, but it’s elsewhere described that samples are dipped in Daikon before immersion (Notis, 1988, p.317; Ó Dubhghaill and Jones, 2009, p.293).
An interesting experimental study was conducted by Ó Dubhghaill and Jones (2009), which also provides a concise yet informative background on the Japanese irogane alloys and the patination procedures.
A firm recommendation is the forthcoming book by master goldsmith Ford Hallam, who is regarded as a leading Western authority on traditional Japanese metallurgy.3
The Roman alloy, Corinthium Aes or Corinthian Bronze
Authors in antiquity (such as Cicero, Seneca, Vergil and Pliny) describe the great value that objects made from corinthium aes possessed, with a prestige that drove people to a far-reaching collector’s mania in the Roman empire from 146 BC onwards, although the earliest references to corinthium aes date to the late 4th century BC (Murphy – O’Connor, 2002, pp.202-206). Cicero was even proscribed and murdered later by Anthony who motivated his actions on account of Cicero’s unwillingness to part with some Corinthian objects in his collection (Pliny, Natural History 34.6, Loeb edition: p.131; Murphy – O’Connor, 2002, p.202).
The author was previously convinced that the term corinthium aes could be tied to the dark patinated copper alloy identified in Roman objects (Giumlia-Mair and Craddock, 1993), however if one reads the contemporary sources critically then none of them describes the material as black (Pliny, Natural History, 34.8; Jacobsen and Weitzman, 1995). The author apologizes for having perpetuated this paradigm (Talma, 2015), and would like to alert readers to alternative literature references. The Roman period alloys had played a minor role in the author’s thesis which focused on the prehistoric alloys in the Bronze Age.
According to Pliny, there were 4 patinated copper alloys that were regarded as valuable (Natural History 34.8 Latin section, Loeb translation, p.133):
“There are three kinds of this sort of bronze: a white variety, coming very near to silver in brilliance, in which the alloy of silver predominates; a second kind, in which the yellow quality of gold predominates; a third kind in which all the metals are blended in equal proportions. Besides these there is another mixture the formula for which cannot be given, though it is man’s handiwork; but the bronze valued in portrait statues and others for its peculiar colour, approaching the appearance of liver and consequently called by a Greek name ‘hepatizon’, meaning ‘liverish’ is a blend produced by luck; it is far behind the Corinthian blend, yet a long way in front of the bronze of Aegina and that of Delos which long held the first rank.”
Other scholars have compared several contemporary Latin, Greek, Hebrew and Syriac sources and conclude that the most prized variety of corinthium aes, such as the one described to have been used on the Gate of Nicanor in the Temple of Jerusalem had a golden colour – and that the dark patinated copper alloy might have been the before mentioned hepatizon that was deemed especially suitable for the production of statuettes (Jacobson and Weitzmann, 1995, pp.581-582). Rather than patination, perhaps surface enrichment through depletion gilding played a role in achieving the golden colour of corinthium aes by removing the cuprous oxide tenorite (CuO) through a pickling method (Jacobsen, 2000, p.62). The single possible example of a figurine made from corinthium aes (or hepatizon?) is a statuette (See Fig. 6) dating to the Hellenistic period prior to 146 B.C. that was stolen in 1990 from the Corinth Archaeological Museum (Mattusch, 1992, Plate 21).
The city of Corinth might not have been the major center of production of these alloys, but rather served as a port of trade. A flourishing and specialized bronze working industry was established in the neighbouring towns of Argos, Sikyon and Aegina (Pemberton, 1981, p.110). Some remains of metalworking workshops have also been excavated within the city of Corinth (e.g. Caley, 1941; Mattusch, 1991).
An interesting experimental study for the Hellenistic and Roman period employed several types of olive oil to create patinas containing copper sulphides, which were detected on some statues from this era (Campanella, et al., 2011).
The (pre)historic patinated copper alloys of the Eastern Mediterranean
Currently, the earliest applications of dark patinated copper alloys are found in ritual statuary and weaponry from the 19th century BC in Egypt (the El-Fayum crocodile, Fig. 1) and Palestine (the Khopesh sword of Balata-Sichem, Fig. 2) where they formed the main base material with inlays of electrum. Electrum is a naturally occurring gold alloy with 20-25% of silver.
According to some researchers, the Egyptian hieroglyph hm-ty km is associated with black copper whereas the word hsmn-km is associated with black bronze (See Fig. 12) (Cooney, 1966, p.43; Giumlia-Mair, 2012b, p.5). This is a possibility, but even more difficult to establish than the Roman period alloy corinthium aes for which there are contemporary descriptions.
Around 1500 BC dark patinated copper alloys are used as inlays in Mycenean daggers (See Fig. 3) and silver tableware from Cyprus (See Fig. 4) and Greece (Xenaki-Sakellariou and Chatziliou, 1989).
The question whether the daggers are laid in with niello or with a dark patinated alloy has been subject of debate (Thomas, 2011; Giumlia-Mair, 2012a). Material analysis favours the interpretation of the material as a dark patinated copper alloy (e.g. Demakopolou, et al., 1995; Cockrell, 2009, p.86) although the element detection limits of certain analytical methods such as XRF (X-Ray Fluorescence) can lead to a bias in interpretation as it does not readily detect sulphur (Thomas, 2005, p.426ff.; Cockrell, 2009; Thomas, 2011, p. 148ff). The detailed style of inlays in Mycenaean daggers have been referred to as ‘painting in metal’ (Xenaki-Sakellariou and Chatziliou, 1989).
Not much is known about the prehistoric patination process and until recently only one patination experiment was published (Giumlia-Mair and Lehr, 1998; 2003). These two publications describing this single experiment still left a number of open questions, and it was one of the goals of the author’s master thesis to test some of the observations of that study but also explore possible methodologies and agents that might be feasible for the Bronze Age (Talma, 2015). For this a diachronic approach was applied, arguing that a similar material will behave in similar ways (hence patination agents should induce similar effects). At the very least, the role of differing composition in relation to colour would be examined.
Shortly before, and during the period after the author’s Master thesis was finished (2015) other researchers experimented on this and related topics (cf. recent article by Jonathan Devogelaere on Roman period patination in EXARC Issue 2/2017).4
An interesting experimental study on ancient decorative techniques reproduced a dark patinated (arsenical) copper alloy blade with inlays of gold, that was based on a Mycenaean dagger (Pacini, 2004, 41-57). Hot immersion in an aqueous solution with copper sulphate created a deep black patina on the copper alloy, leaving the 18 kt gold inlay untarnished. The black patina was examined under SEM and consisted of the copper sulphides covellite, chalcocite and brochantite (Pacini, 2004, 47).
The case studies
Four archaeological case studies were selected based on published material analysis (for composition, see Table 1).
The first is an Egyptian ceremonial Khopesh scimitar sword dating to the second half of the 2nd millennium BC (the 12th dynasty, 1991-1778 BC) that was part of a hoard found in 1908 in Palestine (Balata-Sichem) and is currently in the collection of the Staatliches Museum Ägyptischer Kunst in Munich (Müller, 1987).
Within the bronze base of the sword is an inlay of dark patinated bronze that is decorated with electrum in elegant floral swirling patterns ending in a lotus (alloy 1 and 4, Fig. 2). A striking feature is the purity of the bronze and the polymetallic copper alloy used for the inlay of the dark patinated midrib indicating deliberate production choices (Giumlia-Mair and Riederer, 1998).
The second is the Egyptian Siamun sphinx with gold inlays dating from the Early Iron Age (978-959 BC), which is carrying a table of offerings and bears an inscription for King Siamun (See Fig. 11).
This ritual statuette would have a role during festive ceremonies gracing the deck of a barque shrine that served as a miniature temple (alloy 3 and 6, Delange, 2007, p.43; Mathis, et al., 2009, Table 1, p.64).
The third is a Mycenaean dagger in a private collection, with a midrib of a dark patinated copper alloy that bears additional inlays of electrum and gold in an elegant motif of dancing figures (See Fig. 3). Analysis of the dark patinated copper inlay in the midrib was the basis for alloy 7 (Ogden, 1993, p.42; Giumlia-Mair, 2013, p.100).
The fourth is an example of exceptional workmanship (see Fig. 4). The silver cup (ca. Ø 15 cm x 6 cm) found in a tomb in Enkomi (Cyprus) was decorated with at least 344 inlays of gold, 13 silver inlays and an unknown number of inlays of a dark patinated copper alloy (alloy 8) (Plenderleith, 1952, p.383). Not only would the silver base of the cup first have been hammered from a flat plate of silver in concentric circles to contract the material, afterwards this was likely sanded prior to creating the negative spaces and applying each succession of inlays.
The pattern (of bull’s heads, lotus flowers, ‘garlands’ and rosettes) at least visually appears fairly symmetrical, which is not easily achieved on a convex shape. Finally, a handle was attached through riveting to the cup.
The last case study is an alloy created in a previous experiment (Giumlia-Mair and Lehr, 2003, p.297, nr.27) in order to follow through and compare the findings of that study. Its composition correlates well with that of published material analysis on prehistoric objects. It was described as having a good ductility and displaying a light purple to blue iridescent colour after treatment in a patination solution (alloy 2 and 5).
Some presumptions that the author wanted to test were the proposed regenerative effect attributed to gold content (Uno, 1929, p.126) and iridescent effect of arsenic on the patina, both of which may have inspired conscious choices in prehistory or spoken to the imagination as a material with divine properties (Giumlia-Mair and Lehr, 1998; 2003; Giumlia-Mair, 2012).
The experiments
Four arsenical copper alloys were produced in the laboratories of Deutsches-Bergbau Museum (DBM) in Bochum (Germany), who also provided ICP-OES and SEM testing of the results.
Four additional non-arsenical copper alloys were cast in the workshop of Birgit Doesborg in Den Bosch, the Netherlands (See Fig. 20-22). Three Japanese patination solution recipes were tested in order to establish a baseline to explore the variation in colour from different compositions.
Afterwards, several agents and methods were tested that were deemed feasible for the Bronze Age.
A more detailed description of the experiments and analysis can be found in the author’s master thesis (Talma, 2015, pp.63 – 88, Appendix 164ff.).
For this article it will suffice to give a summary and discuss the main observations.
It is unclear whether the alloys created in the author’s experiment reflect those of other experimenters and the archaeological material (Cockrell, 2009). Through communication with other goldsmiths and what could be gleaned from the literature it became clear that a variety of methods leads to materials with diverse properties, which of course could reflect the variability of empirical methods employed by metalworkers in the past. But different production procedures should be considered when comparing experiments, so explicitness is important.
The method followed by the author (and Giumlia-Mair and Lehr, 2003, p.296) appears the most straightforward (melting all elements at once) but has no regard for eutectic systems.
A eutectic system refers to the different melting points of elements with varying atomic mass and lattice arrangement in the crystalline structure of alloys, which can only strike a balance (eutectic point) at specific temperatures to create a homogenous structure.
However, a heterogeneous crystalline structure is commonly reported for (experimental) shakudo and shibuichi alloys (e.g. Murakami, 1989, p. 660; Ó Dubhghaill and Jones, 2009, pp.302-303). 5
It was pointed out that a correct observance of binary and ternary phase diagrams (knowing which amount of metals to add at which temperature) would create more homogenous alloys with likely better workability, although for a polymetallic alloy containing arsenic this seems rather complex to figure out. It’s possible that prehistoric artisans were not concerned with perfect homogenous structures, but used their empirical experience to create materials with properties that suited their needs. 6
Casting
The casting forms were carved from natural charcoal soldering blocks that ensured a reductive atmosphere with good heat properties. The pure copper, fine gold, fine silver and other pure elements (save for antinomy) were acquired from a goldsmith’s wholesaler, the Aachener Foundry and the faculty of Material Engineering of the Ruhr University in Bochum (Germany).
The size of the graphite crucibles was calculated to be as small as possible (ca. Ø 30 x 40 mm high) to limit the presence of oxygen between the crucible and the intended ceramic lid.
In retrospect, a larger size would have proved more stable and easier to handle during casting.
The ceramic lid was too cumbersome for the small crucibles and was therefore not used.
The fine copper was cut in squares of ca. 4 x 4 mm (0.16”) and the grey arsenic (in small particle size, Fig. 13) was charged into the crucible nearly at the bottom, on a shallow bed of copper plates and then covered with the rest of the copper and other elements. A steel casting tong was bend slightly to create a better grip on the small graphite crucibles.
For the four non-arsenical copper alloys a regular ceramic crucible was used to cast the alloys in open flame. The arsenical copper alloys were heated in an electric oven set to 1100°C to 1170°C (2012 to 2138°F), with a nitrogen atmosphere (See Fig. 14-15).
Protective clothing (lab coat, closed shoes), gloves, respirators/breathing masks and a welding helmet (with darkened glass) were used to protect against toxic fumes, heat and brightness during casting (See Fig. 16).
Prolonged heating in the oven was not attempted as it was feared that the arsenic would vaporize from the alloy as well as some other elements. Consequently, none of the arsenical alloys were heated more than about an hour, and in the workshop the metals were cast simply under an open flame when liquidized.
Regarding the casting of the arsenical alloys (See Fig. 17-19), there was an unusual response to the inert nitrogen gas, which appeared to influence the viscosity of the alloys during the melt.
The use of carbon or green wood might be a much better solution, but should be controlled to make sure no air can react with the arsenic.
Adding charcoal and glass in the ingot before firing, and skimming them off the top when the metal is molten prior to casting also creates a cleaner alloy under a reductive atmosphere (Devogelaere, 2017).
ICP- OES and SEM analysis on the created alloys and their crystalline structure
The produced alloys were analysed with ICP-OES, where a discrepancy in relation to the ‘amount’ of silver was discovered due to a polymetallic eutectic where large silver crystals were bound with arsenic. This raises the question whether:
- the original (added) content of silver in archaeological objects was higher than is detected in material analysis (is there a similar heterogeneous structure in archaeological objects?)
- the alloys of experimenters reflect those recipes they sought to reproduce
The forging of samples resulted in typical striations where the direction of work could be observed under SEM (see SEM Data, 2015, p.74).
The arsenical samples were annealed under a reductive atmosphere, the non-arsenical copper alloys under an open flame.
The samples that were forged generally patinated faster, but there was no clear indication for a difference in colour (Giumlia-Mair and Lehr, 1998; 2001; Benzonelli, Freestone and Martinón-Torres, 2017, p.5).
The composition is shown in Table 1. Arsenical copper alloys: alloys nr. 1, 2, 3, 8; arsenic-free: alloys nr. 4, 5, 6, 7. The samples that are left unforged are designated with the code “number of alloy”a1, whereas the forged samples are “number of alloy”a2. Exception: 1b1 is a piece of alloy that was miscast (from alloy 1), and cast again separately (See Fig. 19, on the right).
The samples proved rather hard to cut, as if they had a high density. Perhaps also due to the size of the ingots, but comparatively the samples that were only cast were almost as tough as compared to those that had been forged, regardless of the variation in annealing. Some of the alloys had a relative good ductility (alloy 1, alloy 5, alloy 8) while the others were less workable. One also turned out to be hollow inside (alloy 2), so the ductility of this alloy could not be adequately tested. Alloy 5 is the arsenic free copy which had a relatively good ductility, conforming to the description by Giumlia-Mair and Lehr (2003, p.297).
The arsenical copper samples were cut on a diamond cutting saw, while the technician (Andreas Ludwig) applied water to prevent the dust from becoming aerosolized. The non-arsenical samples were cut with a jewellers saw.
The alloys yielded a total of 83 sample plates (See Fig. 25). Both types of samples were ground with carbide sanding paper from coarse to fine (See Fig. 26).
At the final stage all samples were polished on a rotating grinding device with diamond powder and water prior to the beginning of the patination experiments.
It was however discovered pretty early that it was necessary to use fine abrasives prior to each chemical bath to develop the patina (for this pumice and/or charcoal powder was used).
For the patination in solutions 8 teflon containers were perforated, of which 4 fitted in a pyrex glass of 800 ml (ca 27 oz). The pH level was measured several times at different temperatures, usually first at room temperature and then at the proposed temperature for the patination solution (See Fig. 28).
The patination experiments
Research strategy
The choice of patination methods and solutions is based on the following assumptions:
- The material properties of the agents are similar to those used in the Japanese process
- The materials were commonly available in (Eastern Mediterranean) Bronze Age society
- The patination time was likely limited to a maximum of a few weeks (in a cold solution), but probably (much) quicker (a hot-cold process)
For the patination process, seven possibilities are suggested:
- cold objects were submerged in cold solutions (below 50°C)
- a warm object was dipped in a cold solution
- a cold object was submerged in a warm solution
- a solution was first applied, and then the object was heated
- the objects were patinated using sweat (touching and holding in hands)
- the objects were patinated with vapour
- the objects were patinated with a dry (thermal) process
In the master thesis (Talma, 2015, pp.63-85), a division was made between cold experiments (below 50°C), hot experiments (near boiling solutions, quenching in cold solutions and dry thermal experiments). These follow the tables with pictures of the patination results from the experiments (See PDF ‘Alloys_and_patination_results_Table 1-10’).
In November 2017, three additional experiments were carried out to compare the crystalline structure of a binary shakudo alloy used in a mokume gane ring and patinated with the sweaty hands method (Exp. 23, Fig. 31). The same principle was tested again on a sample of alloy 5a1 (Exp.25) and finally the effect of seawater was tested on a sample from alloy 2a1 (Exp. 24).
Alloy 5 and alloy 2 are respectively the arsenic-free and arsenical copper alloys based on alloy nr. 27 of the experiment conducted by Giumlia-Mair and Lehr (2003, p.297) whose findings the author wanted to test. These results were later examined under SEM-EDS (see SEM data, 2017, and Table 10).
The following experiments correspond to the list of suggested possibilities above:
- Cold objects were submerged in cold solutions below 50°C (Table 3, 4, 5, 6, 8, 10)
- Rokusho EXP. 1 (1a1,1a2, 2a1, 3a1), EXP 4 (4a2, 5a1, 6a1, 7a1), EXP. 8 (4a1, 6a2, 7a1);
- Urine EXP. 3 and EXP.7 (3a2, 4a1, 7a1);
- Plum vinegar EXP. 10 (4a1), EXP.13 (1a1, 1a2, 2a1, 3a1); plum vinegar and verdigris (4a2, 6a2), EXP. 17
- Pomegranate + natronmix (with NaCl and EXP. 14 (5a1)
- Wine EXP.16 a (6a2); wine with natronmix EXP.16b (6a2), EXP. 20
- Grape sauce(5a2);
- Application with linen EXP.18 (2a1: tapwater and verdigris), (3a2: tapwater and alum);
- Tapwater EXP. 19a: (7a2); 19c: tapwater + pure natron; 19d: tapwater + natron mix (with NaCl and NaSO4).
- Seawater EXP. 24 (November 2017).
- A warm object was dipped in a cold solution (Table 5)
- Quenched red hot in rokusho EXP.11a(4a1); EXP.11b(6a1).
- A cold object was submerged in a warm solution (Table 3, 4, 5)
- Nikomi Chakusoku EXP.2 (1a1, 1a2), EXP. 5 (2a1, 2a2, 3a1, 3a2), EXP.6 (4a1, 4a2, 5a1, 6a1, 6a2), EXP.9 (1b2, 8a2, 7a1, 7a2), EXP. 12 (recycling EXP. 4)(4a2, 5a1, 6a1, 7a1),
- Niiro: EXP.22 (1a1, 3a1, 5a1, 7a1).
- A solution was first applied, and then heated. This was tested at least once on a sample but not used in the thesis. The colour was not uniform, nor were the quenched samples (the effect looked similar). It did not appear to be a viable method.
- The objects were patinated using sweat (Table 9, 10).
- Sweaty hands (as previously suggested for Chinese wu-tong) EXP. 15 (5a1, 5a2, 7a1, 7a2), EXP. 25 (November 2017, alloy 5a1).
- The objects were patinated with vapour (Table 7)
- Acidic vapour (vinegar) EXP. 20a (1a2), EXP. 20b (3a1)
- The objects were patinated with a dry (thermal) process (Table 9)
- Gas burner EXP. 11c (7a2),
- Black satin (oven) EXP. 21 (1a1, 8a2).
Summary of patination procedures (full process can be found in Talma, 2015, p.71ff.)
The first series of patination experiments employed Japanese procedures and patination recipes, to test the range of colours and get an impression of the patination behaviour. After that substances and agents that were (imagined) to be commonly available during the Bronze Age in the Eastern Mediterranean were tested. These ranged from fruit juices, sulphide-free wine, vinegar, alum, natron, salt to urine (as a natural ammonia source). The samples that had successfully darkened were analysed with SEM-EDX to observe the crystalline structure of the alloys as well as analyse the composition of the patina layer. The absence of the characteristic cuprite (Cu2O) or tenorite (CuO) in the patina of darkened samples was an exclusion criterion for a viable method. This was however a first exploration, and it’s possible that a combination with other elements can achieve a cuprite layer (Cu2O) or that different patina structures may indicate different (intentional) patination procedures.
The Japanese patination solution recipes
Patination solution 1: Rokusho (Untracht, 1982, p.671).
This was used in the authors experiment. It’s recommended to alternate with the composition in a different study that analyzed commercial rokusho (Ó Dubhghaill and Jones, 2009, p.309).
Copper acetate (verdigris) – Cu (C₂H3O₂)₂.CuO – 6 g
Calcium carbonate – CaCo3 – 2 g
Sodium hydroxide – NaOH – 2 g
Copper sulfate – CuSO4·5H2O – 2 g – this should be added when the liquid made from the other ingredients is ready for use (after a week).
Preparation: “Dissolve these chemicals in 150 ml of distilled water in a heat-resistant glass container, and allow these to sit untouched for one week or more. Siphon off the clear liquid result at the top, and add 1 liter of distilled water. Mix these and store the solution for future use. It will last according to how often it is used, and whether it becomes contaminated. When ready for use, add 2 grams of copper sulfate to this amount.” This solution is to be used at a temperature of 37,7°C.
Patination solution 2: Nikomi-Chakusoku (Murakami, Niiyama and Kitada, 1988, p.133).
Copper acetate (verdigris) – Cu (C₂H3O₂)₂.CuO – 1,9 g
Copper sulfate – CuSO4·5H2O – 1,2 g
Hydrated potassium aluminium sulfate (alum) – KAl(SO4)2·12 H2O
Water – H₂O – 1 liter
Preparation: In one liter of water mix 1.9 grams of verdigris (copper acetate), 1.2 grams of copper sulfate and 0.2 grams of alum and bring to a boil. Immerse the degreased copper alloys in them for a minimum of 30 minutes. The author was informed that Ryu Murakami actually used commercial rokusho rather than regular copper acetate (verdigris) in his experiments. This is likely due to a mistranslation to English as he explains his experiment more detailed in a Japanese journal (Murakami, 1989)7 . This may then have a markedly different effect during patination, and should be re-evaluated. In the Japanese article he advises to degrease the objects or samples to be patinated first with sodium bicarbonate and to use Daikon: instructions that were not included in the English article (Murakami, 1989, p.660). The author synthesized rokusho by mixing pure verdigris with calcium carbonate (CaCO3) in a ratio of ca. 3:1 and designated it as rokusho, the ingredient to the patination solution Niiro. Some salt (NaCl) was added to a plum vinegar that had been a ‘sweeter’ variety than traditional Ume-Su (resulting in a vinegar with a pH of 3.05 at room temperature (Talma, 2015, p.75).
Patination solution 3: The Niiro- solution (Ó Dubhghaill and Jones, 2009, p.294).
5 g rokusho
5 g copper sulfate (CuSO4·5H2O)
5 ml salty plum vinegar (ume-su)
1 liter of water
Preparation: The water should be boiled at least once to mix all ingredients, and then can be applied at any desired temperature. In the author’s experiments it was applied at ca. 90°C/194°F.
Additional materials
Pumice powder, charcoal powder, soft toothbrush, teflon containers, pyrex containers, a cooking plate (optionally if magnetized with stirring magnets), silver or gold wire or nylon thread (the author used copper wire but was afterwards informed that this can hamper the patination process if immersed in the solution), a brass tweezer, soda, grated daikon (Japanese radish) with the juice in a glass bowl (See Fig. 27; Fig. 29; Fig. 30). To be used in conjunction with the Niiro patination solution: lye and salty plum vinegar.
The Japanese patination solutions
The Japanese patination solutions were intended to serve as a baseline, to compare the range in patina colour on alloys of different compositions and the effect of recipes with different ingredients. The first two recipes were also used by Giumlia-Mair and Lehr (1998; 2003) so the results could be compared to their descriptions.
The solutions were heated in a pyrex glass with stirring magnets, with perforated Teflon containers suspended in the solution. The Teflon containers were attached with a copper wire to a metallic stand, but did not touch the solution (See Fig. 30). They were heated to different temperatures according to the instructions. The first solution was applied at body temperature (ca. 38°C /100°F), the others at near boiling solutions (ca. 90°C/ 194°F).
A soft, wet toothbrush was used to apply abrasives to prepare the surface of the sample plates, first pumice, then charcoal. The samples were covered with daikon the moment they were taken from the solution at regular intervals to observe the progress (ca. 10 minute intervals), then dipped in a bath of soda and immersed in the patination solution. To take the samples from the patination solution, the Teflon containers were pulled out of the patination solutions, and then the samples were taken out with a brass tweezer. The range of total patination time for warm immersion in Japanese patination solution was between 30 min-120 minutes, although for the majority the maximum time was 60 min.
The rokusho patination solution was the least effective of the ones tested, the first few experiments EXP. 1, 4 and 11 were quite unsuccessful, only the samples of Exp. 13 patinated slightly to a grey lilac colour. The patination solution had a bluegreen appearance. It was also applied in glass containers in a controlled environment with a fixed temperature of 35°C/ 95°F) for 5 days (EXP. 8). This did not have a positive effect. After one day samples exhibited a purple iridescent finish, which was unchanged on the second day. They were left there over the weekend and upon the 5th day the copper had come to the surface. The solution was also applied to linen cloth (EXP. 18), with new application 2-3 times per day.
The Nikomi Chakusoku patination solution had an opaque minty green appearance with residue clumped to the surface of patinated samples each time they were taken out of the solution, thus creating an irregularly distributed patina. Samples patinated from 10 minutes onwards and all samples had a predominantly lilac grey colour, some with a spotty iridescence (alloy 1a1 and 1a2, EXP.2, Table 1).
The Niiro patination solution was the most successful as it responded the fastest and created a more evenly distributed patina that was blueish black. A lye was synthesized from potassium carbonate (Table 2) and used to pre-boil the samples according to historical description (Gowland, 1915, p.92) apart from one control sample. After this, the samples of alloy 1a1, 3a1, 5a1 and 7a1 were dipped once in the salty plum vinegar, before being introduced in the Niiro patination solution at a temperature of ca. ca. 90°C/ 194°F (EXP.22).
Acidic patination agents
Amongst the acidic agents was human urine, freshly pressed pomegranate, organic wine (without sulphides), mushed grapes and plum vinegar. They were all tested at temperatures between ca. 35°C/ 95°F -35°C/ 95°F. Acidic vapour (plum vinegar) was filled in a desiccator and a sample of 1a2 and 3a1 tested. As could be reasonable expected verdigris (copper acetate) was formed, so this is not a viable method (unless one wished to make some).
Neutral patination agents
A sample was immersed in regular tapwater for 96 hours at room temperature, which resulted in a slight brown discolouration (EXP. 19a, Table 8).
Alkaline patination agents
A sample was immersed in tapwater with pure natron (EXP. 19c) and in tapwater with natronmix (with NaCl and NaSO4) for 72 hours (EXP19d, Table 8). The sample in pure natron patinated to a dark brown, whereas the sample in natronmix patinated to a dark blue black. In November 2017, a sample of alloy 2a1 was patinated by using seawater from the western shores of Kiel (Kiel-Schilksee, pH 8). It was applied two times per day with a cotton pad, over the course of 5 days. It patinated to a brown colour with a silver tinge.
Dry thermal patination
Both an oxidizing environment (EXP. 11c, 7a2) and a reductive environment (EXP.21, 1a1) were tested. For EXP. 11c a burner was used to heat the sample of 7a2 to 500°C /932°F), for (EXP. 21, 8a2) the electric oven was used with a nitrogen environment heated to 600°C /1112°F). It followed the method for regular bronze described as ‘Black Satin’ (Hughes and Rowe, 1994, p.92). The former (oxidising) turned into a dark blue grey, for the latter (reductive) the surface kept peeling off but patinated to a grey colour (likely due to the polymetallic composition).
Sweaty hands method
In the original experiment, 3 volunteers including the author held a sample of alloy 5a1, 5a2, 7a1 and 7a2 for about 2-3 hours in a hand whilst reading in the library. They patinated over the course of a few weeks to a dark brown to a greyisch black on the rough edges (EXP. 15, Table 9). The method was repeated in November 2017 on a sample of 5a1 for 12 hours, which achieved a similar result.
The author wanted to find out how fast the shakudo alloy (96% Cu, 4%) that was applied in a Mokume Gane ring, made in 2011, would patinate when the metal was made blank again. This darkened within the course of a day and was deep black within a week (EXP.23).
Interpretation of results of the patination experiments
The patina in most (pre)historic and recent patinated copper alloys is reported to consist of the copper oxide cuprite (Cu2O) sometimes with the presence of the copper oxide tenorite (CuO) (Notis, 1988, p.321; Giumlia-Mair, 2013, p.201).
The results of the experiments suggest that the patination agent is more important in creating the size of cuprite crystals and hence the dominantly observed colours (interference with the optical light spectrum), whereas a variation from 0.5-6% gold can influence the hue a bit (this was the range of composition in the recreated alloys).
It can be observed most clearly when comparing the similar method of patination, time duration, temperature but different (Japanese) patination recipes applied to samples of (arsenical) alloy 1a1 in experiment 2 and 22. They turned respectively a greyish lilac purple with a spotty iridescent surface (with large cuprite crystals) and a deep black (with small cuprite crystals) (see also SEM data, 2015, 85 (1a1, EXP.2); SEM Data, 2017 (EXP. 22, 1a1); Talma, 2015, p.186 (Exp. 2)).
This also corroborates the results from an earlier study where a variable colour palette was created by applying different patination agents, which included salts (Uno, 1929, p.123, Table 4).
The suggestion that crystals would be smaller when more elements are present was not apparent from the author’s results (contra Uno, 1929, p.147; Giumlia-Mair, 2013, p.102).
Recently, an article was published that suggest exactly the opposite to the author’s observation: alloy composition determines the colour more than the patination solution (Benzonelli, Freestone and Martinón-Torres, 2017, figures 5-7). However, the results above only refer to the alloys with a variable content of 0,5-6% gold (not without gold), and it remains curious that it was possible to achieve such contrastingly different colours on alloys of exactly the same composition and surface treatment with similar methods.
That suggests that some of the results described in the initial experimental exploration of Giumlia-Mair and Lehr (1998; 2003); Benzonelli, Freestone and Martinón-Torres (2017), and those presented in this article should be subjected to more rigorous and collaborative testing.
The dry thermal and quenching experiments did not seem to create uniform patinas, although a similar grey blue patina was achieved with a burner (Exp. 11c, Table 9) and with quenching in a patinaton solution in EXP. 11a, 11b (Table 5) as is described by Devogelaere (2017) for sample nr. 11 in his experiment.
For the samples that were tested with heat treatment in the oven (“Black Satin” in Hughes and Rowe, 1994, p.92) the layer was unstable and scaled off, even after several repetitions).
SEM analysis determined the layer to consist primarily of tenorite (CuO), which looks more rounded than cuprite (SEM data 2015, p.90.)
Seeing that the dry experiments appeared to create more tenorite (CuO) and the reported presence of cuprite (Cu2O) in the archaeological artefacts of the case studies, this carefully suggests a patination procedure similar to the one in traditional Japanese metallurgy, thus immersion in patination liquids (however the experiments are too limited to make confident generalizations).
The application of linen cloth soaked in an experimental solution of water and alum or verdigris to the surface of samples of alloy 2a1 and 3a2 (with reapplication every couple of hours) did not create a uniform patina (EXP.18), but this does not exclude the method of application itself.
The procedure was inspired by a description in a book on bronze patination techniques where originally cotton-wool was used (Hughes and Rowe, 1994, pp.41-42).
The results of the experiments proposed for the Chinese wu-tong (“sweaty hands”) method (e.g. Craddock and Giumlia-Mair, 1993, p.122ff.; Wayman and Craddock, 1993, p.129) and tested by Giumlia-Mair and Lehr (1998, 2003) did not create a cuprite layer in the author’s experiments although their patina adheres well (SEM data, 2017).
Similar non-crystalline structures were observed in a sample patinated with urine as a natural ammonia source (SEM Data, 2015, pp.58-73), with water and alum (SEM Data, 2015, pp.114-120) and with seawater (SEM Data, 2017).
By contrast, the presence of cuprite in the patina layers of wu-tong objects suggest that they have been patinated by similar processes and patination solutions as the Japanese process (David Loepp and Ford Hallam, pers. comm., 9th of January 2018).
Handling by sweaty hands might only have been a remedial process to ‘repatinate’ areas that have been damaged (Wayman and Craddock, 1993, p.133) and responsible for a ‘regeneration’ due to the natural chlorides and acids present in the hands. It would be interesting if this (a combination of both methods) could be detected.
If a difference can be observed in the patina structure of dark patinated archaeological copper artefacts, then this might either point to a different methodology or patination agent used or a contamination in burial context (Cockrell, 2009; Horn and von Holstein, 2017; Devogelaere, 2017).
Cockrell examined several archaeological examples from the Hellenistic and Roman period and recommends to work from the objects rather than from texts as they may have been patinated through various methods (Cockrell, 2009, p.89).
Some indications as to whether a patination was intentional might be the combination of (patinated) metals of different colours or the combination of refined alloys next to polymetallic alloys such as in the Balata Sichem sword that suggests conscious production choices.
There were no indications of patinas regenerating themselves, also not in the two years since the initial experiments by the author.
The Japanese patination solutions tested usually around a pH of 4,5-6 (room temperature), but the procedure with a succession of alkaline applications in-between appeared to benefit the patination process in distribution of colour and speed of patination.
The best results appeared to be achieved with neutral to mildly acidic patination solutions, which correlate also with findings from Kitada, et al. (2002, pp.1059-1060). Fruit juices, wine, strongly acidic solutions and acidic vapour did not have positive results (as also partially demonstrated by Uno 1929), although the addition of vinegar to Japanese solutions to control the pH is described in some literature (Gowland, 1915, p.92).
Discussion
What may determine or contribute to the colour of the patina?
The patinas of the case studies from the Eastern Mediterranean Bronze Age and Early Iron Age are characterized by the presence of cuprite. Normally, cuprite is observed as red in colour but gold distributed in fine particles in the patina layers is thought to cause interference in the optical spectrum hence the colour is observed as darker (for example Uno, 1929, pp.125-126; Murakami, Niiyama and Kitada, 1988, pp.134-135; Kitada, 2005).
The results of the initial exploration of the author’s master thesis in 2015 suggests that the size, distribution and orientation of the cuprite determines the observed colour, where within the (tested) margin of 0.5 to 6% gold content the variation of composition can influence the hue, but appears to be of lesser importance than the patination agent/solution and method used to create the dominant colour (i.e. purple or black).
Different patinating agents seem to achieve variable sizes of crystals on samples from the same alloys and hence different observed colours (a contrasting interpretation is discussed in Benzonelli, Freestone and Martinón-Torres (2017) that favours a differing composition of alloy as determinant in the final colour). The effect of different abrasives and their relation to different patination colours is common knowledge amongst practitioners of the Japanese patination technique (Ó Dubhghaill and Jones, 2009, p.293; see also Benzonelli, Freestone and Martinón-Torres, 2017). In EXP. 2 and EXP. 22, the surface of the samples was prepared in the same way, immersed at similar temperatures and time duration.
Even the addition of a succession of a lye and vinegar applied to the surface (EXP.22) was accompanied by a control sample (alloy 1a1) that did not undergo these procedures and yet the patina on the samples was blueish black (EXP. 22, Table 5) versus a lilac purple colour (EXP. 2, Table 3, Table 4).
This observation only applies to a small margin variation and certainly merits more testing.
It’s plausible that different mixtures of chemical elements in patination liquids achieve different ‘electrical’ charges hence growth of corrosion (interaction with copper ions), thus creating patina (Ó Dubhghaill and Jones, 2009, p.294, quoting Hughes and Rowe, 1994, who suggested that Daikon might ‘activate’ the surface).
Reviewing the SEM data from 2015, there was some uncertainty whether gold particles were dispersed in all of the samples as it was detected as analysed points in a couple of samples and only a few raster images were created showing the distribution of elements on the surface.
Sometimes both silver and gold particles were dispersed in patinated samples (SEM Data, 2015, a sample without cuprite, pp.16-18) but also on the surface of unpatinated samples (SEM Data, 2015, pp.16-18).
Additional SEM analysis in November 2017 also did not detect gold and/or silver particles in each sample, but it did for example in the analysis of the thin patina surfaces of EXP. 23-25 and on samples from 2015, which may also be a signal from the underlying surface (SEM Data, 2017).
Benzonelli, Freestone and Martinón-Torres (2017, p.1041) noted an irregular distribution of gold particles in the cuprite patina layer of one sample).
The author is unsure why gold and silver particles seem to be distributed in some and not all samples patinated with Japanese patination procedures. This requires deeper study.
According to Kitada, this interference in the optical light spectrum is caused by electron clouds and cations in the cuprite crystals (Kitada, 2005, p.1069; Kitada and Kirino, 2005; Kitada, 2007).
This electrochemical effect in turn has a relationship with the pH Level of the patination liquids used (Kitada, et al., 2002, p.1360). According to Kitada, et al. (2002), their experimentation on copper suggest that when the Niiro proces is applied, both cuprite and tenorite are formed with fine gold particles distributed in the patina layer.
Hopefully more studies can corroborate these findings (perhaps a varying thickness of these layers causes the observed variation of blue to purple colours?). Another suggestion is that the cuprite (Cu2O) or tenorite (CuO) has locally formed, nearest to the gold (Au) inclusions (Prof. Dr. Lorenz Kienle, pers. comm., November 2017).
Does arsenic have an iridescent effect?
As for an iridescence effect of the arsenic this was not confidently refuted by the author’s experiments, although iridescence can also result from contamination during the patination process, restoration procedures and depositional milieu. In the Japanese patination tradition, iridescence is not a desired effect however taste is subjective.
The Tibetan alloys were described as achieving a patina with ‘colours of the rainbow on the surface’ (an effect also visible in sunlight), although a deeper study would be required to better understand this reference (Dagyap, 1977, p.51ff.)
Not all samples containing arsenic subjected to patination experiments resulted in iridescent patina, but all arsenical copper alloys exhibited unusual colours on the surface just after casting (perhaps already a light tarnish?).
The choice of arsenical ores might have been more motivated by factors like the workability (ductility, tensile strength) of the alloys (Northover, 1989; Lechtman, 1996) than an iridescent effect. Pacini (2004, 47) notes that his arsenical alloys had better fluidity during casting and that an iridescent surface formed during annealing.
Possible agents used in prehistoric patination processes
Of the tested patinated agents hypothesised to be available in prehistory, only the experiment with water and a natron mixture with sodium chloride (NaCl) and sodium sulfate (NaSO4) in a ratio as it was reported to occur in Wadi Natron (Lucas and Harris, 1962, p.267) resulted in a dark blue patinated layer with cuprite. The Mediterranean Sea is another possible source for chlorides and calcium carbonate. Sodium chloride (NaCl) presents a possible patination ingredient, but the burial context of objects can induce similar effects.
A study determined the presence of sodium chloride (NaCl) in rokusho for use in Niiro patination solutions (resulting in a blueish black colour on shakudo) (Ó Dubhghaill and Jones, 2009, p.322). Rokusho, a verdigris (copper acetate) mixed with a carbonate is a common ingredient in Japanese patination solutions, but it is unclear if it was used in prehistoric metallurgy and nor is this clear for alum (Lucas and Harris, 1962, pp.257-258). The Japanese patination solution recipes rokusho and Nikomi Chakusoku used in the authors experiment both contained copper sulfate (CuSO4) as well.
This gave a positive patination result (Pacini, 2004).
The experiment with seawater (Exp. 24, SEM Data, 2017) on the other hand, did not create cuprite but had a similar surface structure as those patinated by sweaty hands (Exp. 15, Exp. 25, SEM Data, 2017).
It is necessary to neutralize the salts afterwards, to prevent further corrosion, by rinsing them well under water, although this would need more testing to determine if this would suffice to prevent bronze rot. Perhaps that the alkaline liquids (Daikon and the lye) applied during the Japanese patination process (and eventual application of oil as the last step) serve to neutralize eventual salts and acids?
Conclusion
It is possible to achieve different colours of patina on samples of alloys of the same compositions using similar methods, time duration and temperatures but with different patination agents (responsible for creating different sizes of cuprite crystals). Published analysis of (pre)historical objects displaying artificial patinas ranging from black to blue and purple in colour, refer to the copper (II) oxide cuprite as its main constituent, sometimes with copper (I) oxide tenorite. The extant theories on what creates a different observance of colours of the cuprite (normally observed as red) in these patinas refer to a role of gold (Au) or silver(Ag) particles in the patina layer or alloy structure. Dispersal of gold (Au) or silver (Ag) particles was not detected in all samples. One important aspect to consider is a variability in the structure of experimental samples created by different authors using varying methodology, hence raising the question of comparability. This may also be true for prehistoric artisans employing different methods. A detailed description of production along with a growing reference collection hopefully will provide more insight in the future, and would benefit from collaboration with experienced practitioners of the complex Japanese patination techniques.
For achieving artificial patinas, acidic solutions and agents used by the author were by themselves detrimental or ineffective, neutral to alkaline (salts) agents created better results.
Samples patinated with urine (as a natural ammonia source), sweat or seawater created no cuprite, but their layers adhered well and proved difficult to remove. Similar structures might also occur due to contamination in burial context, for example due to the release of chlorides and acids during decomposition of bodies in graves (Horn and von Holstein, 2017).
Copper alloys with inlays of other metals or the presence of a very pure alloy next to a polymetallic alloy can be an indicator whether a contrast through artificial patination was intentional.
Common salt (NaCl) was only an ingredient in a few of the patination solutions (EXP.22-Niiro, Table 5) and EXP. 19d - natron mix, Table 8) whose results exhibited small cuprite crystals in the patina layer (both solutions also containing NaSO4). Salt(s) might have been used as a patination ingredient for prehistory since rinsing with fresh water afterwards might be sufficient to prevent bronze disease (this requires more testing).
Thermal patination created patina layers that were characterized by tenorite, Cu0, whereas material analysis of Bronze Age artefacts usually indicate cuprite, Cu2O although some authors report both for the more recent Japanese hot immersion patination procedures (Kitada, et al., 2002). The claim of patina regeneration was not substantiated. Although the Roman period alloys were not a focal point in the experiments, the author wanted to refer readers to alternative literature sources that cast doubt on the identification of corinthium aes as a black patinated alloy.
Recommendations/Suggestions
- Follow the work of goldsmith Ford Hallam, who is currently putting all his expertise into a book on Japanese metalworking techniques.
- The bundling of expertise with more future collaboration between goldsmiths and material scientists and those working on similar topics.
- Publication and comparison of created reference collections with SEM imaging of archaeological artefacts describing the shape and size of crystals (also of other reproduced experiments) rather than just analysis results of composition (with ICP-OES, XRF or XRD). SEM images are published in for example Notis (1988), Kitada (2005), Ó Dubhghaill and Jones (2009), and Benzonelli, Freestone and Martinón-Torres (2017).
- Take the burial context into account when studying archaeological objects, as these can also explain the presence of chlorides (see Horn and von Holstein, 2017).
- Omitting arsenic as an ingredient does not seem to influence patination behavior negatively, but alloys may differ slightly in workability: they would still be a good analogy.
- Patination experiments with salts, verdigris (copper acetate), copper sulfate, carbonates, alum and combinations thereof. Hallam proposed starting much simpler with the application of oils, fats, water and mud or clays. Some wet clays can achieve a patination upon drying (due to chemical contents), and some fine clays can be used as abrasives. He also revealed that saltpetre mixed with water is a great oxidizer (Ford Hallam, pers. comm., 3 November 2017, 9 January 2018).
- Possibly also more thermal experiments by those who are already experienced in this methodology (see Hughes and Rowe, 1994).
- Use a silver or gold wire or nylon string as opposed to copper wire to submerge samples in patination solutions, as copper can emit an electrolyte that hampers patination.
The publications of Gowland (1915) and Uno (1929) were forwarded to EXARC to make them accessible. The author assumes full responsibility for all eventual errors or mistakes in this article. Some of the interpretations in this article contrast those expressed in the author’s MA thesis. The thesis will be uploaded to this link https://uni-kiel.academia.edu/MarianneTalma upon publication of this article.
Feel free to contact me for questions, comments or ideas for a productive collaboration (m.talma@ufg.uni-kiel.de, mariannetalma@gmail.com).
Acknowledgements
I‘m grateful to David Loepp, Ford Hallam and Gustav Wollentz for comments and proofreading of this article. I’m grateful to everyone who helped me in my masterthesis project, most especially Deutsches Bergbau-Museum (DBM) in Bochum and their employees (mentioned in detail on the poster for EXARC 2017), goldsmiths David Loepp, Louis Hankart, Birgit Doesborg and my former thesis supervisor (Jun.) Prof. Constance von Rüden, Dr. Arne Röttger and Claudia Brügge of the department ‘Werkstoffe’ (Material Engineering RUB) and Dr. Monica Wirth of the Aachen Foundry for supplying me with odd elements. For additional SEM analysis in 2017, I warmly thank Prof. Dr. Lorenz Kienle, Christin Szillus and Gero Neubüser (workgroup Synthesis and Real Structure) in the Technical Faculty (Materials Science) of Kiel University. I’d like to thank my reviewers of EXARC who helped improve my article in various stages of progression.
Finally, I wish to thank EXARC for providing the platform and means to release all my data, for transparency, and to help further research in this topic.
- 1This effect was known to Louis Hankart prior to 2005.
- 2The author only used a capital for the patination solution marketed under the name rokusho, to make a distinction with the special type of verdigris also traditionally known as rokusho that is an ingredient in the patination solution known as Niiro.
- 3See the kickstarter: https://www.kickstarter.com/projects/525883510/japanese-metalwork-technique-by-ford-hallam , the book is in the finishing stages (accessed 10th of January 2018).
- 4For example, Alessandro Pacini, Jonathan Devogelaere, Francois Mathis, Agnese Benzonelli and for related alloys of the Alpine region Daniel Berger. For work on arsenical copper e.g. Marianne Mödlinger, Frederik Rademakers.
- 5See Uno (1929), Kitada (2005), Kitada (2007), Ó Dubhghaill and Jones (2009, p.291). Paraphrasing David Loepp (pers. comm. 27-11-2017): “Homogenity is a complex matter and depends on the alloy. For example, in casting bronze it is very important to have a fairly cool mold otherwise the tin will separate from the copper. So a proficient artisan knows this from experience. When you heat most alloys to the proper temperature you will get a homogenous solution. At various percentages and temperatures, you will get different phases or intermetallic structures. An experienced artisan in the past may have known little of the science of metallurgy but knew how to adjust variables to favour certain qualities in alloys that he sought. It is in that that the artisan works, achieving certain qualities and effects through practice and observation passed down through generations. Some things are simply not important, such as the minor presence of oxides which apparently were favoured by the artisan in the past rather than shunned.”
- 6Pers. Comm. David Loepp 17th of October 2017.
- 7Pers. Comm. David Loepp who also forwarded the Japanese article, 8th of January 2018
Keywords
Country
- Cyprus
- Egypt
- Greece
- Israel
- Japan
- Palestine
- Turkey
Bibliography
Van BELLEGEM, M., FLETCHER, P., CRADDOCK, P., La NIECE, S. and BLURTON, R., 2007. The black bronzes of Burma. British Museum Technical Research Bulletin, 1, pp.55-63.
BENZONELLI, A., FREESTONE, I. C. and MARTINÓN-TORRES, M., 2017. A Better Shade of Black: Effects of Manufacturing Parameters on the Development of Ancient Black Bronzes. Archaeometry, [e-journal] 59(6), pp.1034-1049.
BINNION, J., 2015. Why you don’t want a copper and silver mokume gane ring. James Binnion Metal Arts, [blog] 6 July. Available at: <https://patternedart.wordpress.com/2015/07/06/why-you-dont-want-a-coppe…; [Accessed 26 November 2017].
CALEY, E. R., 1941. The Corroded Bronze of Corinth. Proceedings of the American Philosophical Society, 84(5), pp.689-761.
CAMPANELLA, L., De FILIPPO, B., FERRO, D., NATALI, S., GUISO, M. and BROTZU, A., 2011. Artificial patina in experimental archaeology. In: A. Macchia, E. Greco, B. A. Chiarandà, N. Barbabietola, eds. 2011. Yococu: contribute and role of youth in conservation of cultural heritage. Rome: Italian Association of Conservation Scientists. pp.281-295.
COCKRELL, B., 2009. Colourful Corrosion: Black Bronze and its Enigmatic Patina. Papers from the Institute of Archaeology, 19, pp.85-90.
COONEY, J., 1966. On the meaning of Hsmn-km. Zeitschrift für Ӓgyptische Sprache und Altertumskunde, 93, pp.43-47.
CRADDOCK, P. and GIUMLIA-MAIR, A., 1993. Hsmn km, Corinthian bronze, shakudo: black-patinated bronze in the ancient world. In: S. La Niece and P. Craddock, eds. 1993. Metal Plating and Patination: Cultural, Technical and Historical Developments. Oxford: Butterworth-Heinemann Ltd. pp.101-127.
DAGYAP, L. S., 1977. Tibetan Religious Art. Wiesbaden: Harrassowitz.
DELANGE, E., 2007. The Complexity of Alloys: New Discoveries About Certain “Bronzes” in the Louvre. In: M. Hill and D. Schorsch, eds. 2007. Gifts for the Gods: Images from Egyptian temples. New York: The Metropolitan Museum of Art. pp.39-49.
DEMAKAPOULOU, K., MANGOU, E., JONES, R. E. and PHOTOS-JONES, E., 1995. Mycenaean Black Inlaid Metalware in the National Archaeological Museum, Athens: A Technical Examination. Annual of the British School at Athens, 90, pp.137-153.
DEVOGELAERE, J., 2017. The Colour Palette of Antique Bronzes: An Experimental Archaeology Project. EXARC Journal, 2.
GIUMLIA-MAIR, A. R. and CRADDOCK, P. T., 1993. Corinthium aes, das schwarze Gold der Alchimisten. Antike Welt, 24, pp.2-62.
GIUMLIA-MAIR, A. and LEHR, M., 1998. ‘Patinating Black Bronzes: Texts and Tests’, Proceedings of the Fourth International Conference on the Beginning of the Use of Metals and Alloys (BUMA IV), Matsue, Japan, 25-27 May 1998. pp. 103- 108.
GIUMLIA-MAIR, A. and RIEDERER, J., 1998. Das tauschierte Krummschwert in der Ägyptischen Sammlung München. Berliner Beiträge zur Archäometrie, 15, pp.91-94.
GIUMLIA-MAIR, A. and LEHR, M., 2003. Experimental reproduction of artificially patinated alloys, identified in ancient Egyptian, Palestinian, Mycenaean and Roman objects. In: P. Bellintani and L. Moser, eds., 2003. Archeologie sperimentali: Metodologie ed esperienze fra verifica, riproduzione, comunicazione e simulazione. Atti del Convegno, Comano Terme – Fiavè: 13 - 15 settembre 2001. Trento: Provincia Autonoma di Trento, Servizio Beni Culturali, Ufficio Beni Archeologici. pp.291-310.
GIUMLIA-MAIR, A., 2012a. The Enkomi cup: niello vs kuwano. In: V. Kassianidou and G. Papasavvas, eds. 2012. Eastern Mediterranean Metallurgy and Metalwork in the Second Millennium B.C. A conference in honour of James D. Muhly. Nicosia, 10-11th October 2009. Oxford and Oakville: Oxbow Books. pp.107-116.
GIUMLIA-MAIR, A., 2012b. I materiali della Coppa di Enkomi (Cipro), ovvero, non è tutto niello quel che è nero. In: M. Denoyelle, S. Descamps-Lequime, B. Mille and S. Verger, eds. 2012. Bronzes grecs et romains, recherches récentes. Hommage à Claude Rolley. INHA Actes de colloques, [online] Available at: < http://journals.openedition.org/inha/3245 > [Accessed 10 January 2018].
GIUMLIA-MAIR, A., 2013. Development of artificial black patina on Mycenaean metal finds. Surface Engineering, 29(2), pp.98-106.
GOWLAND, W., 1915. Metals and Metalworking in Old Japan. London: The Transactions of the Japan Society of London.
HALLAM, F., (in press) Japanese Metalwork Technique. Velp: Mommersteeg Vormgeving.
HUGHES, R. and ROWE, M., 1994. The Colouring, Bronzing and Patination of Metals. A Manual for Fine Metalworkers, Sculptors and Sesigners. 3rd ed. London: Thames & Hudson.
HORN, C. and Von HOLSTEIN, I. C. C., 2017. Dents in our confidence: The interaction of damage and material properties in interpreting use-wear on copper-alloy weaponry. Journal of Archaeological Science, 81, pp.90-100.
JACOBSEN, D.M., 2000. Corinthian Bronze and the gold of the alchemists. Gold Bulletin, 33 (2), pp. 60-66.
JACOBSEN, D.M. and WEITZMANN, M.P., 1995. Black bronze and the ‘Corinthian alloy’. Classical Quarterly, 45 (02), pp. 580-583.
KITADA, M., KIRINO, F., TSURU, T., SUGIMOTO, K. and MATSUHIMA, T., 2002. Electrochemical Characteristics of Niiro-colored Cupper Colored by Japanese Traditional Craft-technique. Journal of the Japan Institute of Metals and Materials, 66(12), pp.1356-1361.
KITADA, M., 2005. Microstructures and Physical Properties of Colored Layer of Cu-4 mass% Au Alloy (Shakudou) Fabricated by Japanese Traditional Technique. Journal of Japan Institute of Metals and Materials, 69(12), pp.1069-1076.
KITADA, M. and KIRINO, F., 2005. Traditional Coloring Technique for Metals with Color Scheme. Hyomen Kagaku, 26(4), pp.226-230.
KITADA, M., 2007. Microstructures and Optical Properties of Colored Layer of Cu- 20 mass% Ag Alloy (Shibuichi) Prepared by Traditional Japanese Technique. Journal of the Japan Institute of Metals and Materials, 71(2), pp.295-303.
LECHTMAN, H., 1996. Arsenic Bronze: Dirty or Chosen Alloy? A view from the Americas. Journal of Field Archaeology, 23(4), pp.477-514.
LUCAS, A. and HARRIS, J. R., 1962. Ancient Egyptian Materials and Industries. 4th ed. London: Edward Arnold Publishers Ltd.
MATHIS, F., DELANGE, E., ROBCIS, D. and AUCOUTURIER, M., 2009. HMTY-KM (black-copper) and the Egyptian bronzes’ collection of the Musée du Louvre. Journal of Cultural Heritage, 10(1), pp.63-72.
MATTUSCH, C. C., 1991. Corinthian Metalworking: The Gymnasium Bronze Foundry. Hesperia: The Journal of the American School of Classical Studies at Athens, 60(3), pp.383-395.
MATTUSCH, C. C., 1992. A Bronze Warrior from Corinth. Hesperia: The Journal of the American School of Classical Studies at Athens, 61(1), pp.79-84.
MURAKAMI, R., NIIYAMA, S. and KITADA, M., 1988. Characterization of the black surface layer on a copper alloy coloured by traditional Japanese surface treatment. Studies in Conservation, [e-journal] 33(1), pp.133-136.
MURAKAMI, R., 1989. Surface Coloring of Metal Cultural Artifacts. Journal of the Japan Society of Colour Material, [e-journal] 62(11), pp.658-665.
MURPHY-O’CONNOR, J., 2002. St.Paul’s Corinth: Texts and Archaeology. 3rd ed. Collegeville, MN: The Liturgical Press.
MÜLLER, H. W., 1987. Der Waffenfund von Balâṭa-Sichem und Die Sichelschwerter. Munich: Verlag der Bayerischen Akademie der Wissenschaften.
NORTHOVER, J. P., 1989. Properties and use of Arsenic-Copper Alloys. In: A. Hauptmann, E. Pernicka and G.A. Wagner, eds. 1989. Old world archaeometallurgy: proceedings of the International Symposium “Old World Archaeometallurgy”, Heidelberg 1987. Bochum: Deutsches Bergbau-Museum. pp.111-118.
NOTIS, M. R., 1988. The Japanese alloy shakudo: its history and its patination. In: R. Maddin, ed. 1988. Proceedings of the First International Conference on the The Beginning of the Use of Metals and Alloys (BUMA I), Zhengzhou, China, 21-26 October 1986. Cambridge, MA: MIT Press. pp.315-327.
Ó DUBHGHAILL, C. and JONES, A. H., 2009. Japanese irogane alloys and patination - a study of production and application. In E. Bell, ed. 2009. Santa Fe Symposium on Jewelry Manufacturing Technology 2009: proceedings of the twenty-third Santa Fe Symposium in Albuquerque, New Mexico. Albuquerque, NM: Met-Chem Research. pp.289-324.
OGDEN, J., 1993. Aesthetic and technical considerations regarding the colour and texture of ancient goldwork. In: S. La Niece and P. Craddock, eds. 1993. Metal Plating and Patination: Cultural, Technical and Historical Developments. Oxford: Butterworth-Heinemann Ltd. pp.39-49.
OGUCHI, H., 1983. Japanese Shakudo: its history, properties and production from gold-containing alloys. Gold Bulletin, 16(4), pp.125-132.
PACINI, A., 2004. Studi ed esperimenti su preziosi policromi antichi. Montepulciano: Madonna delle Querce.
PEMBERTON, E., 1981. The attribution of Corinthian bronzes. Hesperia: The Journal of the American School of Classical Studies at Athens 50, pp. 101-111.
PLINY (the Elder). Natural History (books 33-35). Loeb classical library 394 (translation by H. Rackham). Cambridge: Harvard University Press.
PLENDERLEITH, H. J., 1952. Technical Report. In C. F. A. Schaeffer, ed. 1952. Enkomi- Alasia: nouvelles missions en Chypre 1946-1950. Paris: Librairie C. Klincksieck. pp.381-389.
TALMA, M., 2015. The application of black-patinated alloys in the Eastern Mediterranean: technology and technology transfer. MA. Ruhr-Universität Bochum.
TALMA, M., 2017. It’s complicated: an experimental approach towards understanding dark patinated copper alloys from the Eastern Mediterranean Bronze Age. 10th Experimental Archaeology Conference (EAC10) of the International Organisation of Archaeological Open-Air Museums and Experimental Archaeology (EXARC). Leiden, the Netherlands, 20-22 April 2017.
THOMAS, N. R., 2005. The Mycenaean pictorial daggers: patina and inlay. Surface Engineering, 21(5-6), pp.424-430.
THOMAS, N. R., 2011. Recognizing Niello: three Aegean daggers. In: A. Vianello, ed. 2011. Exotica in the Prehistoric Mediterranean. Oxford: Oxbow Books. pp.146-161.
UNO, D., 1929. Künstliche Korrosion von japanischen Speziallegierungen. Korrosion und Metallschutz unter Einbeziehung des allgemeinen Metallschutzes, 5(6), pp. 121-130, 147-156.
UNTRACHT, O., 1982. Jewelry: Concepts and Technology. New York: Doubleday.
WAYMAN, M. and. CRADDOCK, P. Wutong, a neglected Chinese decorative technology. In: S. La Niece and P. Craddock, eds. 1993. Metal Plating and Patination: Cultural, Technical and Historical Developments. Oxford: Butterworth-Heinemann Ltd. pp.127-133.
XENAKI-SAKELLARIOU, A. and CHATZILLIOU, C., 1989. Peinture en metal à l’ époque Mycénienne: incrustration damasquinage niellure. Athens: Ekdotike Athenon.