The content is published under a Creative Commons Attribution Non-Commercial 4.0 License.
Reviewed Article:
Ancient Greek Weaving, Experimental Archeology on Greek Textiles and Household GDP
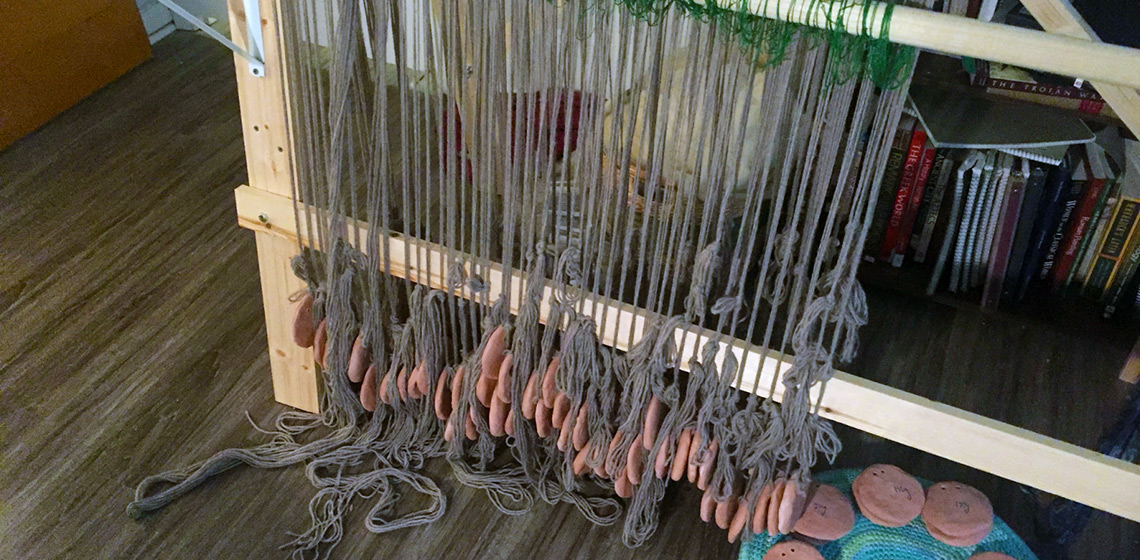
This paper outlines the experimental weaving project of an ancient Greek chlamys to investigate the weaving production capacity of a typical household and reconstruct women’s contribution to household GDP in ancient Greece. While some scholars have researched finer textiles and tech-niques based on visual evidence, very little is known about the skills and time needed to produce the most basic clothing form (the chlamys) produced in an ancient Greek domestic setting. The experiment, which involved the creation of a single heddle warp-weighted loom based on ar-chaeological and iconographic evidence, found that a team of three weavers could spin and weave this common use textile in roughly three to four weeks. Cutting extra-long warp threads made this process easier, as multiple garments can be made with one warp and then separated once they have been taken off the loom. Based on these results, it is possible to calculate the amount of money that an average household could earn in a calendar year. The author estimated that a family could sell enough textiles to make about 60-140 drachmae a year while keeping some textiles for their own use. Little is known about the exact demographics of who bought these textiles. However, there is some evidence for a market in the context of funerals as well as evidence for large, physical fiber craft markets in Athens. As an experimental archaeology pro-ject, this research sheds light on aspects of Greek household economics, the contribution of women’s household labor, and craft production skills within the domestic context.
Introduction
The project researches the process of creating an ancient Greek chlamys to investigate the production of an average household. The research will assess hands-on weaving and the study of this process from setting up the warp to completion. While research has been done on some individual aspects of weaving, there is little research concerning the whole process and the final product, and even scarcer research into everyday textiles (Canavan, 2015, p.123). This experiment can inform the study of the ancient world in the time required to make these garments, as well as the mathematics, skill, and physical toll required. The specific textile produced is a chlamys, a type common in the 5th c. BCE, although the garment itself was in use before and after this period. This knowledge can be used to better understand production and the amount of cloth that could be made in an average household, as well as what that cloth might be like (Canavan, 2015, p.123; Foxhall, 2016). The information from this project can give a better understanding of the daily life of women and the realities of textile production and trade, which are absent from our view of the Greek world.
Loom weights and Tools Used
The loom (histos) is not based on a single specific classical example, but, rather, conforms to examples proposed by other scholars as well as an understanding of the properties of single heddle warp-weighted looms (Mårtensson, Nosch, and Strand, 2009, p.374; Foxhall, 2016; Carroll, 1983; Gleba and Mannering, 2019, p.15). The loom used for this experiment is made out of modern materials, with dimensional lumber and metal arms in place of what would have been wooden pieces. While the materials are different, the function of the loom is not; although these modern materials could have some affect on the friction and process of weaving. This style of loom is a single heddle warp-weighted loom or a vertical loom using hanging ceramic weights to create tension (Carroll, 1983; Hooper, 1911). The loom can be taken down, folded, and reassembled even with a weave in mid-progress. An example of the loom used for this project and the heddles in use can be seen in Figure 1 and 2.
The loom weights (laiai) replicated various classical examples and were fired to the temperatures of pit firing, thus mimicking ancient firing techniques of loom weights and ensuring accurate replication (Foxhall et al., 2016; Meo, 2014; Mårtensson, Nosch, and Strand, 2009). The 77 weights used in this experiment are discoid loom weights, averaging about 180 grams in weight, and made by hand, using a lower quality blended clay like the local clays that would be used (Ulanowska, 2018, p.165). Since the loom weights were varied in size and weight, they each took a varied amount of threads, a process which has been noted by Karavidović and Ivančan (2018). All but three of these weights are very similar, the main type of weights are discoid, with two small holes near the top of the weight. The three weights that are different feature one or two large holes made by a human finger, although they are still within the weight range of the others. Since these are handmade, there is some variety in size, thickness, and weight, to replicate real weaving conditions, skills, and the range of weights rather than strict replicas (See Figures 3 and 4).
The tools used for weaving are handmade wooden and bone weaving tools, though they are not exact replicas as the evidence for the exact tools is too scarce to replicate. However, some parameters can be established in what tools to use as there were five main tools used in the ancient world and in this weaving experiment. The shuttle (penion) is a tool used to spool the weft and weave swiftly without constantly dealing with excess weft or new threads. Two shuttles were used, both wooden, a larger and smaller size to weave with multiple colors. A weaving knife or beater (spathe) is another essential tool; this is a carved stick that is used to tighten and compress the weave, as well as to separate warp threads that stick together. The weaving knife used is 31 centimeters long, four centimeters wide, and about 5-6 millimeters thick. The “blade” of the knife is flat and beveled in a v shape to form the edges. The tip also forms a v shape to mimic a double bladed knife and while there's no direct replica, there is an example of an Italian weaving knife that is from the period (Bazzanella, 2019, p.207). This does not mean that weaving knives are exclusive to Italy, as different beaters and knives were essential Greek tools, but some of the best-preserved tools are from Italian sites.
The next tool is a wool comb (kteis) which is essential both for weaving and carding (Gleba and Mannering, 2019, p.9). One of the better-preserved combs is from the same archaeological site as mentioned above, although the comb used in this experiment is a wider and more common hair comb of a similar thickness. Needles (rhaphis) are also essential to weaving, and physical examples are very rarely documented, so for this experiment, a set of bone and horn needles was chosen; as they are easy to produce and made from common materials (Spantadaki, 2016, p.93; Siennicka, Rahmstrof, and Ulanowska, 2018, p.2). The last major tool is the shear (kouris), which is irreplaceable for cutting threads. A standard shear design was chosen, as it shows little variation in functionality or design from the ancient world (Gleba and Mannering, 2019, p.7; Gleba, 2019, pp.234-5). The use of tools and the creation of the loom and weights are important, as they replicate the conditions of ancient weavings from the time it takes to use and set them up to their effects on the weave and the hand. A photo of all the tools used is provided below (See Figure 5).
Experimental Archeology and Questions
This undergraduate research project looks at the creation and production of textiles in ancient Greece, specifically using a single heddle warp-weighted loom and investigates the process of making a Greek chlamys, with the intent to create a finished woolen textile. Textiles were a daily part of life, as well as an important economic factor within the household domestic product and trade in general, the experiment can be used to determine the production value of an average household (Foxhall, 2016; Spantidaki, 2016, p.11; Canavan, 2015). Though this research focuses on the 6th, 5th, and 4th centuries BCE, since this is the period of the textile reproduced, archaeological evidence dating to before this time frame is often cited as the technology did not change in any substantive way. There are a few references to technologies used after the period under investigation when it seemed appropriate to include them. The archaeological evidence covers not only mainland Greece but also Magna Graecia and Turkey, as these areas have yielded significant archaeological finds.
While the author was not accustomed to this style of loom, there is some experience with different fibrecrafts and weaving them. With this lack of experience, the final products do not exemplify the skills of ancient weavers but rather the researcher’s intermediate technical skills and their experience with this style of loom.
Critical questions:
- How many hours does it take to make a basic utilitarian garment?
- What does this mean in terms of production for an average household?
- How physical is the work of weaving on a warp-weighted loom, what skills are required to work this style of loom?
- Would increasing the warp length to make two garments from one warping make the process quicker/easier?
- What is the final product, and how does it compare to the original depictions?
Clothing Choice, Functionality, and Common Use
A Greek chlamys is a cloak that is primarily associated with travelers and hunters and was widespread throughout the Greek world (Canavan, 2015, pp.118-127). The chlamys was chosen because it is a basic shape, requires only basic skills, and was a commonly used textile. Like many Greek textiles, it is rectangular in shape, and it is fitted to ones body with various pins and fibulae (Harlow and Nosch 2014, p. 22). These factors provide a good understanding of daily textiles, and they will make this easily replicable by weavers possessing a variety of skills. The dimensions are approximations based on images on red and black-figure pottery from the late Archaic/early Classical period around the 5th century B.C.E. (The Met, Funder, 1928; Atsma; Theoi Project). This is cross-referenced against a sheet that was fitted and pinned to the author to get the most accurate dimensions for his frame. The image that provided the key visual source appears on a krater in the Metropolitan Museum of Art depicting Persephone and Hermes (See Figure 6). The intended size is 76 cm x 178 cm, hanging just above the wearer’s knees and providing enough length to hang like the one on the krater at the Met (See Figure 7). While other images were consulted to get a good understanding of the chlamys, this image gives an exceptional view of the garment and a rare frontal depiction. The final products should fit similar to the depiction and include a stripe like the depiction as well. The experiment is a bit shorter than the image of Hermes in Figure 6, but both fit right above the knee, and the experiment’s edges were finished by creating fringes instead of sewing a hem.
The weave attempted is what is known as a tabby weave, that is, a weave with about the same amount of warp and weft. In this experiment the weft and warp are made out of the same yarn, except for the small weft stripe of red yarn at the beginning and ending of the weave. This stripe was the same width as the primary yarn. Stella Spantidaki has noted that these are the only identifiable weaves and one of the most common as well (Spantidaki, 2016, pp.55-56). The result of the experiment is a more warp-faced weave than weft-facing, although it is still a recognizable balanced tabby in certain sections. The edge itself is fringed on the first chlamys, as this seems to be a common enough finishing border, although sewing the ends in is also common (Spantidaki, 2016, p.55). Once finished, the chlamys required several washing and beating sessions to balance some of the weaves and make it a cohesive textile (Spantidaki, 2016, pp.91-92). The clamys was beaten with the spathe and struck over some railing repeatedly, then soaked in water briefly and dried. The process was repeated three times for this experiment, although the effect of creating the cohesive textile is more important than the number of repetitions These steps were taken to mimic classical weaving aesthetics and techniques and to ensure that the experiment was as close to ancient weaving as possible.
Yarn used, tension, style, size
It should be noted that the yarn used is machine produced and bought in a store: however, calculations have been made to determine how many hours it would take to spin the yarn (Mårtensson, Nosch, and Strand, 2009, p.393; Spantidaki, 2016, p.67). This yarn is 2-ply, which would be more improbable to see in the Greek world, but not impossible. The choice was mostly due to necessity and the ability to find large quantities; since 2-ply yarns did exist, this choice was a plausible substitution (Bazzanella, 2019, p.207; Gleba, 2019, p.223). The yarn used is pure wool, and the width of the yarn is based on the researcher’s understanding of functional textiles as well as economic considerations. The yarn is about 1mm wide, and while this is rather wide for clothing, there are textile fragments and iconography that demonstrate its use in Greek utilitarian textiles (Spantidaki and Moulherat, 2019, pp.188, 190-191). The colors used are based on natural wool colors as well as madder root dye, a red dye used throughout European history, and specifically noted in Greek sources (Martelli, 2014, pp.122-123, Canavan, 2015, p.115, Spantidaki, 2016, pp.63, 79, 87). These trends correspond to Iron Age Italy, where there is a color convention of darker cloaks with a border, like what is found in the red-figure depictions. The borders are often red, as noted by textile specialist Margarita Gleba in her monograph Italy: Iron Age: Textiles and Textile production in Europe (Gleba, 2019, p.224). This experiment is meant to mimic classical weaving, in part through aesthetic and style, so the common style of darker cloaks with a weft-faced stripe was used, implementing minimum but bold colors (See Figure 8). The use of traditional colors also corresponds to practical pricing, as any dyed good costs more, and an outer cloak would get the brunt of the elements. Using minimum dying for the outer cloak and nicer materials for a tunic would be the most practical way to use dyes without wasting money. These mimic the depictions of chlamys cloaks previously noted from the Theoi Project. The steps mentioned in the past few sections are in place to ensure that the weaving experience is as close as possible to classical weaving. The experiment was set up to focus on the weaving produced in an average house, where Lakonian purple or extra house slaves would be absent. This gives a much more accurate view of textiles used by an average person and creates the most accurate conditions to study the production of textiles.
The Weaving Experience and Costs
Time/materials for the first Chlamys: 6 hours to make loom weights (2 people), 8 for the firing but this was not an active firing process. |
Altogether, the first chlamys took 55-59 hours with the mistakes and experiments included. The loom weight firing is not included, because they are made once and then used multiple times like the loom. Without the experimental blunders, this would take about 49-53 hours. It can be assumed that a less experienced weaver would have made these mistakes, so they will be included as the author is a beginner to this loom. For every hour of warping or weaving (not including measuring the yarn, rolling the warp, reloading the shuttle, unwarping the textile, or retying the weights), it is generally calculated that it would take 10 hours of spinning, although some variation occurs (Spantidaki, 2016, p.11). With this calculation added, making this chlamys without the experiments would take 319-379 hours of labor. This textile work would be divided among a team of women, which, in an average house without many slaves, would be two or three women (Foxhall 2012, p.192-193, Kissell, 1918, p. 235). While this project was quite labor intensive, as a utilitarian cloak, it did not require the time nor skill that a chiton or tunic would. Undoubtedly, fine cloth such as those would take exponentially longer than this and require much more careful planning and a more diverse skill set.
The experience of weaving was demanding, but it was incredibly fulfilling to work on and finish. The second weaving experiment proceeded slightly faster, although there is a limit to how much the process can be hastened (See Figure 9). The author is not an expert in weaving, so the results reflect that, although this was a factor that was also present in the ancient world. As Linda Foxhall, a leading specialist in ancient Greek textiles, notes, “…The underlying premise that a girl in her early to mid-teens would have already learned some (but not all) of these critical skills [weaving on a loom] growing up at home.” (Foxhall, 2012, p.195). This means that girls would be exposed to weaving, spinning and other textile skills by their older female relatives, but it can be assumed that younger girls and teens might not be able to lead or work on weaving projects on their own. Linda Foxhall also mentions textile production in modern Mongolian and Berber cultures, where girls start to learn skills like spinning and roving in their early teen years and eventually working up towards more difficult skills like weaving (Foxhall, 2012, pp.195-196). Such skills with a loom require years of training and a level of physicality that children don’t yet have, no matter their class (Foxhall, 2012, pp.195, 197). In Xenaphon’s Oeconomicus Ischomachus talks about his wife and her weaving skills when she entered his house:
καὶ τί ἄν, ἔφη, ὦ Σώκρατες, αὐτὴν παρέλαβον, ἣ ἔτη μὲν οὔπω πεντεκαίδεκα γεγονυῖα ἦλθε πρὸς ἐμέ, τὸν δ᾽ ἔμπροσθεν χρόνον ἔζη ὑπὸ πολλῆς ἐπιμελείας ὅπως ὡς ἐλάχιστα μὲν ὄψοιτο, ἐλάχιστα δ᾽ ἀκούσοιτο, ἐλάχιστα δ᾽ ἔροιτο; [6] οὐ γὰρ ἀγαπητόν σοι δοκεῖ εἶναι, εἰ μόνον ἦλθεν ἐπισταμένη ἔρια παραλαβοῦσα ἱμάτιον ἀποδεῖξαι, καὶ ἑωρακυῖα ὡς ἔργα ταλάσια θεραπαίναις δίδοται; Xen. Oec. 7:5-6.
“And what knowledge could she have had, tell me, Oh Socrates; when I brought her in as my wife? She who hadn’t even been born 15 years when she came to me; before that time, she was living under diligent care in a way that she might see, hear, and ask as little as possible. For is this not expected to be enough, when she came, if she only knew how to turn wool into a cloak when she was given it, and she had only seen the task of spinning given out to her slaves.”
(Translation provided by the author)
This phrase provides a pertinent—if male-based—view into the skill set of a young woman during this period. Socrates has just asked if Ischomachus’ wife knew all the house duties and skills that a woman was supposed to. Though his wife is not necessarily a common girl, as he mentions her female slaves, girls of all classes were not assumed to have a lot of experience in weaving on a loom, due to the skill and difficulty of this medium. Girls were not expected to lead their own weaving projects before they were married, but newlyweds would soon become skilled in this process with the guidance of her mother in law and new relatives (Foxhall, 2012, p.196). If a girl married later in her life, or remarried, she would likely know how to weave, but the skill of weaving requires a level of physical maturity which often coincides with the young ages of brides in the Ancient Greek world (Foxhall, 2012, pp.195-196). The casual mentions of textile slaves (specifically spinners) in Xenophon 7:6 and 7:41 confirms the economic importance of weaving and the relative normalcy of buying slaves for this purpose. In general, weaving’s prominent place in this chapter (mentioned in 7:5-6, 21, 36, and 41) show’s women’s importance and their monetary value to a family and to a household. Such insights into ancient perceptions of weaving are rare in the textual sources and obviously written with a strong male bias. Nonetheless, it is clear that the economics of women’s work are of some importance.
One aspect of weaving that must be noted is the creation of long textiles on the warp-weighted loom. The ability to roll the warp is essential to weaving on almost every loom, but the process on the warp-weighted loom is not fully documented. The author did not have to untie the warp weights, as he tied the excess in large knots right above the warp weights and simply untied to release, making this process incredibly efficient and helpful. When this occurs, the tension is taken off of the textile, and the woven warp can be wound around the cloth beam, exposing the next section of warp threads to weave. Using a round cloth beam, as depicted in classical artwork, leads to the warp sliding and the warp weights crashing onto the floor as soon as tension is reapplied (Spantidaki, 2016, pp.52-53). It took the author several attempts to figure this out and several more experiments before a solution to this issue came about. Since the information on warp-weighted mechanics is sparse, a look into another form of ancient weaving was taken to obtain relevant information. Backstrap weaving is a form of weaving where the warp is tied around one’s body and then readjusted when the weaver reaches the end of their workable warp. As the textile is tied to your body, there is a constant need to reroll the warp, so backstrap weaving has developed an easy solution for rerolling (Spantidaki, 2016, pp.52-53; Siennicka, Rahmstrof, Ulanowska, 2018, pp.3-4). Backstrap weaving adds an extra cloth beam and then traps the warp in between them, ensuring that the warp will not slide when it is readjusted (Waddington 2009). To stop the cloth beams from moving around, they were lashed onto the loom with cordage, and then the process was repeated when the warp needed to be moved. This method was extremely effective and allowed the author to reroll his first warp four times without issue (Fig. 10). The lack of representation on period artwork could be since the second cloth beam is not terribly noticeable, and the cordage is already seen in some places (Spantidaki, 2016, p.50). While there could have been another way for ancient Greek weavers to achieve this, until further evidence is shown, this method seems historically plausible, and it follows the general way that these looms work.
On a more physical note, the art of weaving on a warp-weighted loom requires a strong dominant arm and some endurance (Foxhall, 2012, p.197). After a few hours of continual weaving, my hands, wrists, and arms often hurt from beating the warp tight, while my muscles were sore after a full day of weaving. This could obviously be mitigated by having multiple people who could switch duties, as well as through general conditioning, but it is important to note that this fiber-art is physically demanding (Foxhall, 2016; Foxhall, 2012, p.195). Using a warp-weighted loom still requires a second person, at the very least, to roll up the warp. Overall, a team of three weavers, as suggested by Foxhall, would make this process much faster, but the hours and skills required do not change (Foxhall, 2016, Foxhall, 2012, p.195; Gleba, 2019, p.237). As the author repeats this experience, more data will be compiled to give the most accurate view of ancient Greek weaving.
Time/materials for the Second and Third Chlamys: 19 balls of natural yarn (each about 200 yards), plus a few dozen yards of red weft threads. |
The second experiment mimicked the first in almost every way, from the dimensions to the use of the red stripes. The times are listed above, with the two chlamydes grouped together since they were on the same warp and in a continual manner. The most notable difference is the slight acceleration of pace in weaving and measuring the threads. The time it takes to weave is extensive, and the author was not planning on seeing this drastically reduced. The weave had two functions, to ensure that the findings of the first experiment are repeatable and consistent and to experiment with the idea of rolling the cloth beam to make multiple full-length textiles from one warp set up. In the first project, the cloth beam was rolled 4 times to get the full length but ensuring that the process would work for two weaves is important. This experiment saw a reduction in the production time by over 20 hours, as using the warp for two pieces means that the measuring and warping time does not have to be done for each textile. For this second project, the 8-foot-long warps of the first experiment were doubled to 16 feet. The final product was of a better quality and contained fewer errors.
Textile Production and Sale
The lives of ancient Greek women are woefully under-documented, and that is particularly true when it comes to evaluating their labor within a monetary context. Textile prices are generally absent from the ancient textual sources. Still, there is some pertinent evidence found in the sumptuary laws limiting funerary costs and the maximum amounts that a family could spend. These funerary edicts mention blankets, similar in dimension and material to that of a chlamys, so the amounts of these blankets will be used to price the chlamys, which allows us to extrapolate prices. An edict from Delphi during the Classical Period allowed for the purchase of one blanket and one cushion, totaling no more than 35 drachmae. This is quite low compared to other similar laws where the expected cost of a single garment is close to 50 drachmae and would suggest that the Delphic blanket is a plainer weave closer to the one created in this experiment (Spantidaki, 2016, p.6). Unless further evidence is gathered, for the purpose of this paper, the cost will be split roughly down the middle, with the blanket costing 20 drachmae, as it would be more material than a cushion. One cannot assume that women were paid the same as men, and the textile trade was often done under the table, but these numbers give a great starting point into understanding the economics of textile production (Foxhall, 2016). The number of textiles that could be produced within a calendar year could fully flesh out this analysis and provide a theoretical amount of money that women could earn through weaving. While speculative, it may be possible to generate some predictions about the number of textiles that an average family could produce. However, this does not imply that every family produced textiles in these numbers or that this involved the three-woman dynamic previously mentioned.
Weaving a chlamys is a considerable time investment, and even with a group of three women, this would take several weeks. It is unknown how much time a group of women would spend weaving each day; the forty-hour workweek of the modern era does not apply to the daily lives of women during the Archaic and Classical periods. Nevertheless, if one is to treat the production of textiles as a cottage industry, a minimum average of 5 hours of work per person is assumed for this paper. This number allows for plenty of time to focus on other jobs that women were responsible for and the activities that were a part of daily life while giving textile production its proper place as an important contribution to household economics (Foxhall 2016). Using the average work mentioned above, and if this weaving continues 7 days a week, a single chlamys such as this can go from a pile of wool to a fully finished cloak in 3-4 weeks. If the team of weavers produced two chlamys from a single warp, then roughly 20 hours of work would be removed, pushing this closer to 3 weeks. This was one of the questions answered in the experiment, and it gives a better understanding of how this weaving can be streamlined (Spantidaki, 2016, p.52). Weaving with a warp of such length requires additional materials and so possibly the extra upfront cost of this means that the method should not be assumed to be the standard. It is also possible that ancient Greek weavers measured long enough threads on one warp for more than two textiles, but more experimental archeology needs to be done to see the quality and results of this. The author believes that the week of leeway is important, as this is not a wage job, and one cannot assume the uniformity of production that our modern world requires.
Given these numbers and the rate of production, a team of three weavers could realistically spin and weave between 13 and 17 chlamydes a year. Most families would need to create other textiles for daily wear, but until more research is done it is uncertain how much more time finer textiles would take to produce. Due to the limited scope of this experiment chlamydes are the only textile that can be calculated. Using a warp long enough for two cloaks would put this number firmly closer to 17 cloaks a year, although this method might not have been exclusively used. This is a significant amount of textiles to produce on such a loom, and 13-17 chlamydes (or a comparable amount of other clothing such as chitons) would be more than a typical family needs. This strongly suggests that women could create enough textiles both to sell and to clothe themselves and their families. Even if a family took the equivalent of 10 cloaks produced a year, either in chlamys and blankets or in finer tunics, there would be 3-7 chlamydes to sell (Spantidaki, 2016, 11). This excess textile would be worth a significant amount of money, based on the price calculated above 60-140 drachmae a year. While this many textiles may not have always been produced, and regional economics would determine different prices, this baseline provides an important perspective on women’s potential contribution to the domestic GDP. If families would only sell these extra textiles, this still constitutes about 9-28 weeks’ worth of labor and, thus a significant amount of money for a family. The amount of extra textiles that could be made in one year, and the amount of money for which they could be sold, significantly alters prior notions of family economics. Women’s contributions to family wealth were significant, and this cottage industry represents an important force in the daily lives of ancient Greeks.
The most speculative aspect of this research is a very simple question-- who would buy these textiles if many households wove their own? This is difficult to answer as textile sales were often overlooked, but there is some evidence for large textile markets in Athens (Spantidaki, 2016, p.11). This demonstrates that there was a market for fibercrafts, even if it doesn’t reveal the buyers or other details. The widespread enforcement of funerary laws limiting the amount families could spend on textiles is also relevant here as it indirectly reveals that a significant motivator in buying textiles for funerary usage would have been convenient. People would not always have weeks to wait for a textile to be made in-house. In funerals, one would have to prepare the body immediately, and in cases like this, buying a pre-made shroud is far more practical (Spantidaki, 2016, p.6). There were also metics (foreigners) and bachelors to account for, i.e., people who might not have family nearby to weave their clothes. This is speculative in the absence of affirmative evidence, yet these assumptions can give a better understanding of how the textiles would be circulated throughout the population.
Other variables that make calculating a strict price for these textiles still remain. Textiles require raw material, in this case wool, and if the family bought the yarn, that would cut into the profit margins (Spantidaki, 2016, p.11). If the family owns sheep, then those sheep require care and land, although we can assume most citizen families would own land. If a household were to buy pre-spun yarn, the process would be shortened rather significantly. Assuming all the yarn was bought already spun, an average family could produce a chlamys per week, although this would cut into the profits of the final product significantly. Even with these variables unknown, it is abundantly clear that these textiles could have contributed to a portion of the families’ wealth and that women’s contributions to the standard of living were potentially quite substantial.
Improvements for Future Research
As mentioned previously, continual training on this loom is paramount to producing successful and beautiful textiles. There is a large learning curve to developing this skill, and continued study will both make an improved product as well as a decrease production time. While the first textile contains several mistakes, the second seems to be of better quality. Nevertheless, the author is proud of both, and they are very warm.
Learning how to tablet weave and how to incorporate those weavings into the warping phase will create a more even warp and will assist in future experiments (Ulanowska, 2018, p.170). Now the author cannot tablet weave, so both textiles were produced without the benefit of starting with this type of weaving. The next steps are to continue developing my skills as a weaver and creating more ancient Greek textiles to understand this area of study better.
Conclusions
The process of setting up a loom is a difficult endeavor but one which had a strong economic impact on ancient Greek society. While many of the details concerning the actual prices and trade are still uncertain, this experimental project and research contribute both to our knowledge about the quantity of textiles that an average ancient Greek family could produce and to our knowledge about the process of making a textile and what it requires to embody those skills through technical expertise. This project confirms earlier claims that textile production could have made major contributions to a family's economy (Foxhall, 2016). Further research must be done to repeat these results and to branch out into different textiles to get a clearer picture of Archaic and Classical weaving.
Acknowledgements
Many people made this project possible, both friends and family, and it cannot be understated how their contributions were. A note of appreciation to the UNCA Ceramics Department for allowing me the use of a kiln and giving invaluable counsel in the best types of clay, methods of firing, and construction of the loom weights. As mentioned, the entire loom had to be moved mid-project, so special thanks should be given to my parents for allowing their upper hallway to be taken over by weaving and for putting it with the late-night sounds of clanging weights and dropped shuttles. Another special thanks should be given to my father, Richard Palmer, for moving the loom back and forth from Asheville to Mooresville and for helping build the loom in the first place.
Outside of moving the loom, my parents and uncle have been the cornerstones of my research. The author wishes to thank Sandra Palmer, Richard Palmer, and Shane Brightly for always believing and supporting me. Dov Wiener was irreplaceable in editing this paper, and their friendship buoyed me throughout this experiment. The author wishes to thank Dr. Laurel Taylor for her guidance, patience, and enthusiasm; without her advice, this project wouldn’t have been written.
To everyone unnamed who helped the author in this project, thank you.
Keywords
Country
- Greece
Bibliography
Atsma, A. J., K14.9 PERSEPHONE & HERMES. Metropolitan Museum of Art. Theoi Project, Available at: < https://www.theoi.com/Gallery/K14.9.html > [Accessed 14 July 2021]
Atsma, A. J., K11.4 HERMES PSYCHOSTASIA & MEMNON. British Museum, London. Theoi Project, Available at: < https://www.theoi.com/Gallery/K11.14.html > [Accessed 14 July 2021]
Atsma, A., J.K11.2 HERMES & INFANT DIONYSUS. Gregorian Etruscan Museum, Vatican CityTheoi Project, Available at: < https://www.theoi.com/Gallery/K11.2.html > [Accessed 14 July 2021]
Atsma, A. J., P23.2 PERSEUS, ATHENA & THE HEAD OF MEDUSA. Museum of Fine Arts, Boston. Theoi Project, Available at: < https://www.theoi.com/Gallery/P23.2.html > [Accessed 14 July 2021]
Atsma, A. J,. K11.7 HERMES. Gregorian Etruscan Museum, Vatican City. Theoi Project, Available at: < https://www.theoi.com/Gallery/K11.7.html > [Accessed 14 July 2021]
Atsma, A. J., K6.1B THE DEATH OF ACTAEON. Museum of Fine Arts, Boston. Theoi Project, Available at: < https://www.theoi.com/Gallery/K6.1B.html > [Accessed 14 July 2021]
Bazzanella, M., 2019. Italy Neolithic and Bronze Age: Textiles and Textile production in Europe. In: M. Gleba and U. Mannering (eds.), Textiles and Textile Production in Europe From Prehistory to AD 400. Oxford: Oxbow Books, pp.203-214.
Canavan, R., 2015. Weaving Threads: Clothing in Colossae. In: A. H. Cadwallader, Fragments of Colossae, ATF (Australia) Ltd. pp. 111–133. < https://doi.org/10.2307/j.ctt19b9mrx.10 >
Carroll, D. L., 1983. Warping the Greek Loom: A Second Method. American Journal of Archaeology, 87(1), pp. 96–99. < https://doi.org/10.2307/504672 >
Foxhall, L., Quercia, A., Silvestrelli, F., and Edlund-Berry, I. E. M., 2016. Loom Weights. In: F. Silvestrelli and I. E. M. Edlund-Berry (eds.), The Chora of Metaponto 6: A Greek Settlement at Sant'Angelo Vecchio, Austin: University of Texas Press, pp. 455–468. Available at: < www.jstor.org/stable/10.7560/309476.37 > [Accessed 23 September 2020]
Foxhall, L., 2012. Family Time: Temporality, Gender and Materiality in Ancient Greece. In: J. Marincola, L. Llewellyn-Jones, & C. Maciver (eds.), Greek Notions of the Past in the Archaic and Classical Eras: History without Historians Edinburgh: Edinburgh University Press, pp. 183–206. Available at: < www.jstor.org/stable/10.3366/j.ctt3fgsc9.16 > [Accessed 23 September 2020]
Foxhall, L., 2016. Webs of Knowledge: Untangling Textile Production in Ancient Greece. [video online] Available at: < https://www.youtube.com/watch?v=3AAIljnCe-Y > [Accessed 14 July 2021]
Fletcher Fund, 1928. Terracotta bell-krater, Attributed to the Persephone Painter. 1928. Metropolitan Museum of Art, CC0, via Wikimedia Commons. Available at: < https://commons.wikimedia.org/wiki/File:Terracotta_bell-krater_(bowl_fo… > [Accessed 14 July 2021]
Gleba, M., 2019. Italy: Iron Age. In: M. Gleba and U. Mannering (eds.), Textiles and Textile Production in Europe From Prehistory to AD 400. Oxford: Oxbow Books, pp.215-241.
Gleba, M. and Mannering U., 2019. Introduction:Textile Preservation, Analysis, and Technology. In: M. Gleba and U. Mannering (eds.), Textiles and Textile Production in Europe From Prehistory to AD 400. Oxford: Oxbow Books, pp.1-26.
Harlow, M. and Nosch, M.-L., 2014. Weaving the Threads: methodologies in textile and dress research for the Greek and Roman world – the state of the art and the case for cross-disciplinarity. In: M. Harlow and M.-L. Nosch (eds.), Greek and Roman Textiles and Dress: An Interdisciplinary Anthology. Oxford: Oxbow Books, pp.1–33. < https://doi.org/10.2307/j.ctvh1dh8b >
Hooper, L., 1911. The Technique of Greek and Roman Weaving. The Burlington Magazine for Connoisseurs, 18(95), pp.276–284. Available at:<http://www.jstor.org/stable/858660> [Accessed 23 September 2020]
Karavidović, T. and Ivančan. T. S., 2018. Understanding the Archaeological Record: Reconstructing a Warp-Weighted Loom. EXARC Journal, 2018(2). Available at: < https://exarc.net/ark:/88735/10351 > [Accessed 23 September 2020]
Kissell, M. L., 1918. Ancient Greek Yarn-Making. The Metropolitan Museum of Art Bulletin, 13(11), pp.235–237. < https://doi.org/10.2307/3253904 >
Martelli, M., 2014. Alchemical Textiles: colourful garments, recipes and dyeing techniques in Graeco-Roman Egypt. In: M. Harlow & M.-L. Nosch (eds.), Greek and Roman Textiles and Dress: An Interdisciplinary Anthology, pp. 111–12). Oxford: Oxbow Books. < https://doi.org/10.2307/j.ctvh1dh8b.10 >
Mårtensson , L., Nosch, M.-L. and Strand, E., 2009. Shape of Things: Understanding a Loom Weight. Oxford Journal of Archaeology, 28(4), pp.373 - 398. < https://doi.org/10.1111/j.1468-0092.2009.00334.x >
Meo, F., 2014. New Archaeological Data for the Understanding of Weaving in Herakleia, Southern Basilicata, Italy. In: M. Harlow and M.-L. Nosch (eds.), Greek and Roman Textiles and Dress: An Interdisciplinary Anthology, pp. 236–259. Oxford: Oxbow Books. < https://doi.org/10.2307/j.ctvh1dh8b.15 >
Siennicka, M., Rahmstrof, L. and Ulanowska, A., 2018. Introduction. In : M. Siennicka, L. Rahmstrof, A. Ulanowska (eds.), First Textiles The Beginnings of Textile Manufacture in Europe and the Mediterranean, Oxford: Oxbow Books, pp. 1-16.
Spantidaki, S., 2016. Textile Production in Classical Athens. Oxford: Oxbow Books.
Spantidaki, Y. and Moulherat, C. 2019. Greece. In: M. Gleba and U. Mannering (eds.), Textiles and Textile Production in Europe From Prehistory to AD 400. Oxford: Oxbow Books, pp.185-202.
Ulanowska, A., 2018. Experimenting with Loom weights. More Observations on the Functionality of Early Bronze Age Textile Tools.in: M. Siennicka, L. Rahmstrof and A. Ulanowska (eds). First Textiles: The Beginnings of Textile Manufacture in Europe and the Mediterranean, Oxford: Oxbow Books, pp. 163-174.
Waddington, L., 2009. Backstrap Baiscs. WeaveZine: an online magazine for handweavers, Warp Thread Media LLC, 16 September 2009, Available at: < http://www.weavezine.com/content/backstrap-basics.html > [Accessed 23 September 2020]