The content is published under a Creative Commons Attribution Non-Commercial 4.0 License.
Reviewed Article:
Shedding New Light on the Pure Copper Metallurgy of the Chalcolithic Southern Levant Through an Archaeological Experiment
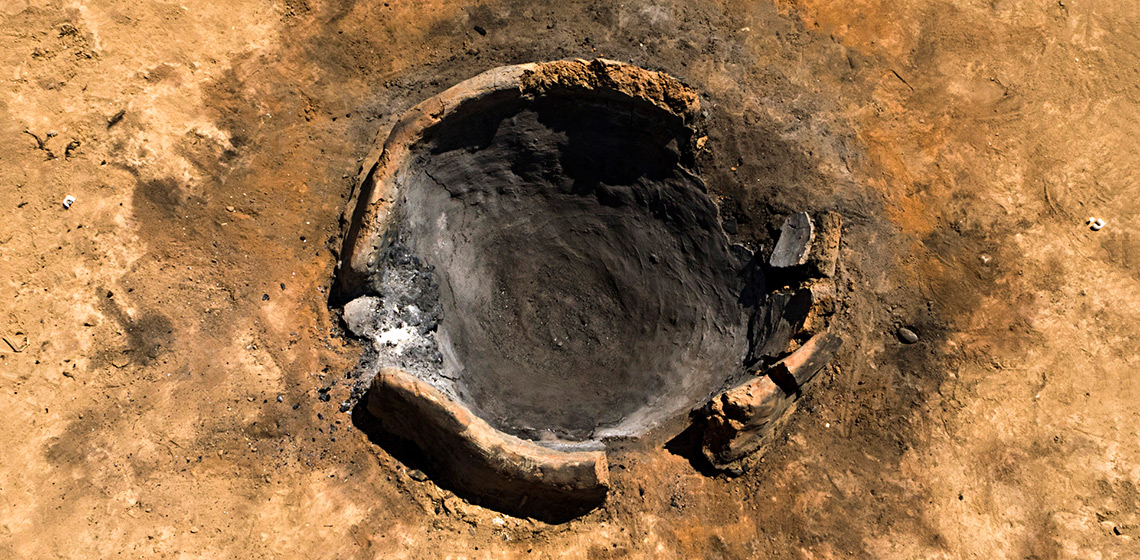
Two metallurgical traditions coexisted in the Chalcolithic Southern Levant: the lost wax casting of polymetallic alloys and the pure copper technology. Details of their operational sequences are still unknown. To date, no production sites of lost wax casting technology have been found. Only the main steps of the pure copper technology can be reconstructed from the archaeological record. Therefore, an archaeological experiment was carried out to shed new light on both technologies. Concerning the pure copper technology, the experiment focussed on the draught technique and high-temperature behaviour of the crucible and furnace clays. Based on archaeological evidence, a furnace and crucibles were reconstructed with local clays used by ancient metallurgists. Instead of the commonly hypothesised blowpipes, bellows were used to produce the draught. The furnace was successfully operated with bellows and reached temperatures high enough to melt copper. Furthermore, the clays’ behaviour varied considerably due to high heat exposure, but they are suitable if used appropriately. Our experiment establishes this draught technique as a viable alternative to the commonly assumed blowpipes as well as the suitability of local clays.
Introduction
The earliest metallurgy in the Southern Levant dates to the Ghassulian (4500 to 3800 BC). Among the most recognisable finds are the outstanding polymetallic lost wax cast objects of the Nahal - Mishmar hoard (Bar-Adon, 1980). A potential production site for such objects was recently suggested at Fazael in the Middle Jordan valley (Rosenberg, et al., 2020). Hitherto, the only preserved production remains are mould fragments on metal objects. The mineralogical composition of these mould fragments attests to a local production of the objects (Goren, 2008; 2014). No suitable deposits of polymetallic ores exist in the area. Therefore the metal was imported, most likely from Anatolia or the Southern Caucasus (Key, 1980; Tadmor, et al., 1995).
Alongside the lost wax casting technology, copper ore from Faynan was smelted in sites located along the Nahal Beer Sheva (See Figure 1). The pure copper was cast in open moulds. Metallurgical debris from these production sites allows the reconstruction of a two-stage production sequence: smelting the ore in a simple pit furnace with low furnace walls to slag with entrapped copper prills and melting the mechanically extracted copper prills in a crucible (Ackerfeld, et al., 2020; Golden, Levy and Hauptmann, 2001; Hauptmann, 2007; Shugar, 2000); however, many details of this pure copper technology remain unclear.
Experimental archaeology can help to gain new insights into the two metallurgical traditions of the Chalcolithic Southern Levant. It allows the testing and improvement of the current reconstruction of the pure copper technology and, therefore, provides a deeper understanding of the metallurgical processes. Several experiments of the lost wax casting process have been carried out (Goren, 2014; Levy, et al., 2008; Shalev, 1999). Combined with technological studies of the artifacts (Goren, 2008; Tadmor, et al., 1995), their results provide general knowledge about the mould production and casting process. Previous experiments aiming to reconstruct the pure copper technology are known but remain unpublished.
The published experiments aimed to reproduce the technology or recreate the objects, sometimes with modern materials and furnaces. This severely inhibits a deeper understanding of the process beyond the knowledge already gained from the artefacts, archaeological context, ethnographical comparisons, and material sciences.
Aim of the Experiment
The archaeological experiment was designed to shed new light on some aspects concerning the metallurgy of the Chalcolithic Southern Levant. Regarding the lost wax casting technology, the aims of the experiment were to get a hands-on experience of the entire process and the production of analogues of the casting moulds. In a second step, analyses of the moulds were complemented by general technological considerations and the practical experience acquired in the experiment. Further, the preservability and identifiability of lost wax casting remains were investigated. This part of the project is ongoing and will be published at a later stage.
This study presents the results of the experiment related to pure copper technology. Two aspects were investigated: the draught technique and the high-temperature behaviour of the materials used for the metallurgical ceramics. Generally, blowpipes are assumed to create the draught in Chalcolithic metallurgy regardless of the lack of draught-related artefacts (Bourgarit, 2007). The same holds for the reconstructed process of the pure copper technology in the Chalcolithic Southern Levant (Golden, Levy and Hauptmann, 2001). A fragment from Abu Matar, assumed to be a tuyère fragment, was published by Shugar (2000), but the identification was questioned (Bourgarit, 2007). However, it was recently identified as a furnace wall fragment by Rose, Fabian and Goren (2021).
Furthermore, two additional fragments from the same site were identified as potential tuyère fragments, probably used with bellows (Rose, Fabian and Goren, 2021). Based on the reconstructed design and size of the furnace (Golden, Levy and Hauptmann, 2001; Shugar, 2000), the use of bellows is equally as likely as the use of blowpipes. From a practical perspective, positioning bellows in the opening of the furnace walls (See Figures 2a–c) reduces considerably the workforce and effort necessary to heat the furnace. The experiment tested whether such a set-up could heat the furnace to temperatures high enough to smelt copper.
The high-temperature properties of the local clays used for the crucibles and furnaces were not previously investigated in metallurgical contexts. However, their behaviour is a crucial parameter for the metallurgical process and can inform material-related constraints and technological choices. Comparing the observations and materials obtained from the experiment with archaeological material will help build new hypotheses about the ancient process.
For these reasons, the experiment relies heavily on conditions comparable to the past, especially concerning the furnace's raw materials and layout. Successfully melting the entire copper charge was not a primary concern. Placing it in the crucible sought to replicate the behaviour of the ancient crucible charge. Furthermore, it indicated whether comparable furnace conditions were achieved or not.
Materials and Preparation of Equipment
The archaeological record suggests that exclusively Negev loess was used to produce the metallurgical ceramics found in the Nahal Beer Sheva sites (Shugar, 2000). Recently, crucible fragments and lost wax cast objects were reported from Fazael (Rosenberg, et al., 2020). Although no direct evidence such as a furnace has been found yet, the crucible fragments mean that metallurgical activity at this site is highly likely. Accordingly, Negev loess and sediment from the Wadi Fazael were used as clay sources for the crucibles in the experiment. Further, the Negev loess was used for the tuyères and furnace lining. It is the local soil of the Beer Sheva region and consists of calcareous clay with silt-sized non-plastic components, predominantly quartz (for a detailed description, see the group "Loess-calcareous sand/quartzitic sand" in Goren, 1995). The strong red colour of the Fazael clay indicates a high iron content. Its non-plastic inclusions are predominantly silt-sized quartz and abundant calcareous fine sand.
Negev loess for the crucibles and tuyères was collected close to the experiment’s site and crushed to < 1 mm after large impurities such as stones or straw were removed. The furnace lining was made from material excavated from the furnace pit after sorting out occasional pebbles. The wadi sediment from Fazael was elutriated to separate the calcareous sand from it. Subsequent sifting of the coarser fraction revealed elutriation splits very efficiently between grain sizes smaller and bigger than 125 µm. The dried fine fraction was crushed to < 1 mm to be used for the crucibles.
Chaff was produced by cutting grass from small animal bedding into suitable sizes (> 20 mm for the furnace lining and tuyères; > 5 mm for the crucibles) because the size and shape of the pores in the archaeological objects indicate the use of grass and not straw. Additionally, roughly chopped dry grass from the experiment site was used to temper the furnace lining. Non-vegetal temper is absent in the metallurgical ceramics of the Chalcolithic Southern Levant except for the lost wax casting moulds (Shugar, 2000; Goren, 2008).
Chaff and clay were mixed in a 1:1 volume ratio for the crucibles and tuyères. A similar ratio was aimed for when preparing the furnace walls and pit lining in the field. Water was added until the paste was not sticking to the fingers anymore. All objects were shaped by hand. Additionally, a stick was used to make the draught channel of the tuyères. Occasional drying cracks were repaired when the objects were leather-hard. Afterwards, the crucibles were thinly slipped to smooth the surface.
The shapes and dimensions of the crucibles follow those from Abu Matar in Shugar (2000, p. 97): about 12 cm diameter, 7 cm inner depth and a wall thickness of 0.9 to 1.2 cm. The bottom of the experimental crucibles became slightly thicker than the archaeological ones, but this should not significantly influence their performance because they are heated from the top. The archaeological material suggests a different shape for the crucibles from Fazael (Rosenberg, et al., 2020). Since their high fragmentation does not allow a complete reconstruction, the evidence from Abu Matar was preferred. The 1.5 to 2.0 cm diameter of the tuyères’ draught channels followed the reconstructed diameters of two recently identified tuyère fragments from Abu Matar (Rose, Fabian and Goren, 2021). Crucibles and tuyères were dried for several days, the last couple of days directly in the sun, to remove as much humidity as possible to avoid cracking when heated.
The dimension of the furnace and its walls follow the reconstruction of Golden, Levy and Hauptmann (2001): A round pit of 30 to 40 cm diameter and about 20 cm depth with about 10 cm high furnace walls that have an opening on one side (See Figures 2a–c). They reconstructed an unlined furnace pit based on the texture of the pit’s surface and slag adhering to it. In contrast to their reconstruction, some furnace fragments from Abu Matar seem to originate from furnace linings. Due to the surrounding soil and the clay paste consisting of Negev loess, a separate lining is unnecessary, and a smooth and regular pit surface can be easily achieved by smoothing the sediment. The sediment crumbles easily, however, so a separate lining was necessary to ensure proper removal of the pit surface after the experiment and allowing a close comparison with the archaeological remains in the lab. The pit lining of the experimental furnace was about 1 cm thick (See Figure 2b). It was left to dry overnight and did not have any drying cracks the following day.
Run | Tmax [°C] of the crucible | Duration [min] | Crucible paste | Metal mixture [wt. %] | Remarks |
1 | 1012 | 76 | Negev loess | Cu: 97.5 | Half of metal batch spilled into furnace |
Sb: 2.5 | |||||
2 | 950 | 65 | Negev loess | Cu: 95.0 | Crucible covered with lid |
Sb: 5.0 | |||||
3 | 1233 | 81 | Fazael clay | Cu: 89.5 | |
Sb: 10.0 | |||||
Pb: 0.5 | |||||
4 | 943 | 81 | Fazael clay | Cu: 90.0 | Two tuyères in 90° angle |
Sb: 10.0 |
Tab 1. Key data of the different runs. Please note that the temperature represents an estimate due to the difficulties in locating the focus pointer of the pyrometer (compilation: Thomas Rose).
Bag bellows were sewn from cow leather with a sewing awl and waxed polyester thread. Wooden rails were used to stabilise the inlet (see Figures 3a–b). Taking non-perfect tightness of the openings and the variation of different operators into account, about 10 l of air were delivered per stroke. Wooden pliers made from the same material were prepared to handle the crucibles. Copper filings, antimony shot, and lead granulate were mixed in set amounts (See Table 1) to simulate a range of polymetallic alloys used for lost wax casting in the Chalcolithic Southern Levant (arsenic was excluded for health reasons). Unfortunately, little is known about the fuel used for metallurgical operations in the region (for a case study from Faynan, see Engel and Frey, 1996). Due to its availability in a sparsely vegetated landscape, commercial citrus charcoal was employed, although it was not available in the Chalcolithic (Langgut, 2017). Temperatures were recorded with an infrared pyrometer BTMETER BT-1500 (accuracy for temperatures > 0°C: ± 2 % of measured temperature + 2°C, i.e. ± 22°C at 1000°C) and should be regarded as estimates as it was not always possible to see the focal points on the burning charcoal.
Melting Experiment
The experiment was carried out in late August 2020 at the Nahal Beer Sheva west of Tel Sheva. After the kindling of the fire, the furnace was slowly heated, and glowing charcoal accumulated until it reached the top of the furnace walls. When it reached 900°C, the bellows were used to increase the temperature to about 1200°C. The tuyère of the bellows was plugged into another tuyère, which then entered the furnace (See Figures 2b,c). After nearly two hours of pre-heating, the first of two runs with Negev loess crucibles began (See Table 1). Due to unfamiliarity in operating the pliers, about half of the metal batch was spilled onto the charcoal when the crucible was placed. It was positioned close to the opening of the furnace wall with its rim on the same height as the draught. In all runs, the crucible was covered with charcoal, and the bellows continuously operated to heat it. After 76 min, the crucible was taken out of the furnace. It was strongly affected by some spalling and occasional heat cracks. The currently visible extensive cracking and spalling, however, developed after the experiment (See Figure 4). The tuyère-facing side was considerably melted or vitrified. Similarly, the length of the tuyère was strongly reduced due to melting.
During the second run, the crucible was covered with a lid, with a small opening, of freshly prepared clay paste (See Figure 5) and placed at a slight angle to direct the air stream on the top of the crucible instead of on its side. It was covered with charcoal and heated for 65 min. After the run was finished, the crucible showed features similar to the crucible from run 1. Additionally, the lid and the tuyère had melted onto the crucible. However, the metal batch had not melted.
In the third and fourth run, crucibles made with Fazael clay were used. In both runs, the crucibles were placed in the centre of the furnace and heated for 81 min. During the third run, a small amount of metal melted. The tuyère melted and affixed itself to the crucible, contributing to the slag on the rim of the tuyère-facing crucible side and possibly acting as a flux for the Fazael clay. Outside this area, only the rim of the crucible was slightly vitrified (See Figure 6). For the last run, the furnace was modified to be operated with two bellows by creating a second opening in the furnace wall at a 90° angle to the initial one. Melted material from both tuyères flowed on the crucible and partly covered it (See Figure 7). Although the crucible showed a more substantial impact from the heat than the crucible in the previous run, parts of the rim opposite the tuyère did not melt. Some metal was melted, but its bright colour indicates that it was mainly antimony.
The tuyères of the third and fourth run lost considerable amounts of material due to melting and showed spalling similar to the crucibles in the first two runs. During run four, the melting of the tuyères was observed by an outward movement of the hot zones over time. None of the tuyères became blocked at any time. Cross-sections of the tuyères show that only their surfaces melted (See Figure 8).
On top of the difficulties in adequately arranging the crucibles and tuyères, the behaviour of the charcoal posed significant problems during the experiment. Compared to beech charcoal, used by one of the authors in a previous experiment, it burned very slowly and crumbled into large numbers of small pieces over time. This effectively blocked the airflow towards the crucible, keeping the hot zone immediately in front of the tuyère. At the same time, charcoal outside of the hot zone burned very hotly without additional draught.
Excavation of the Furnace
Two days after the experiment, the charcoal was removed and the furnace cleaned. Larger heat cracks occasionally occurred on the rim of the furnace wall. The regions close to the initial tuyère opening were vitrified on the inside, and sporadic spalling was visible on the outside (See Figure 9). Cross-sections of the furnace wall and the pit lining were grey or black due to unburned carbon from the chaff in regions initially covered with charcoal. On the outside, in direct contact with air, it had the typical intensive red colour of burnt clay. The chaff in the lining of the furnace pit bottom remained unburnt. Outside of the furnace, burnt and blackened soil clearly indicated the activity zones of the furnace, mainly to which area charcoal was moved when interacting with the crucible (See Figure 10).
Three amorphous metal lumps with enclosed charcoal pieces were discovered in the furnace a few centimetres under the surface of the charcoal (See Figure 11). Their yellowish surface indicates the nearly complete absence of copper oxides. Metal was only lost into the furnace during the first run, and the shape of the lumps suggests that it did melt entirely during the experiment.
Interpretation and Discussion
The experiments have shown that the calcareous Negev loess and the ferruginous Fazael clay behave very differently at high temperatures. Only the rim of the Fazael clay crucibles was partially vitrified, while tuyères and crucibles made from Negev loess lost significant parts of their material due to melting. Vitrification of the Negev loess seems to be more localised, but it cannot be ruled out that this is due to differences in the position of tuyères and crucibles.
Despite the differences, both clays are suitable for the smelting and melting of copper even if the Negev loess melts at significantly lower temperatures. On the crucibles, flowing textures only appeared on the tuyère-facing sides (See Figures 5,6), and vitrification was restricted to the surface (See Figure 8). This indicates excellent heat-insulating properties of the Negev loess. The material on the surface consumes the majority of the heat, and only when it is removed by melting, the material underneath is affected whilst maintaining the overall structural stability of the object. As a result, Negev loess can be effectively used if the hot zone is concentrated on the opening of the crucible and the outside of the crucible is kept cool enough to prevent melting. This was not the case in the experiment, however, because the intense heat of the charcoal heated the entire tuyère and the outside of the crucible. With a proper hot zone, it is to be expected that the cooler air from the bellows might act as an adequate coolant for the tuyère and prevent it from significantly melting.
These results are similar to features observed on archaeological artefacts, such as the preserved crucible rims from the 1990s excavation of Abu Matar. Independent of adhering copper stains and slag on the inside of the crucible fragments, some were without vitrification on the outside, some were (heavily) vitrified, sometimes even with bloated rims. Vitrification in the archaeological material is restricted to a few centimetres below the rim, but the features are very similar to the experimental results (See Figure 12). This indicates that our technique resembles the ancient one, thus strongly pointing towards a unidirectional draught.
The extensive cracks and spalling of the Negev loess crucibles in the clay during cooling were probably caused by the rehydration of the calcium carbonates (cf. Shoval, et al., 1993). This feature is absent on the preserved archaeological crucible fragments, further indicating a highly localised hot zone on the top of the crucible in the ancient process and significantly lower temperatures on the outside of the crucible.
Furthermore, the high-temperature behaviour of the Negev loess might explain why tuyères are rarely found. After the experiment, the unvitrified parts were very brittle and could be easily trampled to crumbs. Additionally, some parts of the tuyère were neither heated to very high temperatures nor did they show any other signs of metallurgical activity. Consequently, tuyère fragments might be best preserved when they melt, but at the same time, they might have lost any indicative shape due to complete liquefaction. The melted Negev loess, however, had a characteristic deep black colour and glossy surface, nearly identical to the slagged tuyère fragment reported by Rose, Fabian and Goren (2021). Both colour and surface differ distinctively from the green-stained slag pieces. Thus, they might help differentiate between melted ceramics and other metallurgical remains in future studies on the metallurgy of the Chalcolithic Northern Negev.
Although only melting operations were performed, the completely melted metallic copper (See Figure 11) indicates that the furnace achieved temperatures high enough for smelting of the oxide copper ores used in the Chalcolithic Southern Levant (Hauptmann, 2007) with bellows instead of the commonly assumed blowpipes. During Chalcolithic smelting, the ore never fully liquefied long enough to separate metallic copper and slag, thus suggesting similar or even lower temperatures than those achieved in the experiment. At the same time, the vast abundance of, for example, cuprite in the Chalcolithic slag indicates mildly reducing conditions (Shugar, 2000; Hauptmann, 2007). No oxide layer had formed around our copper lumps, therefore, pointing towards stronger reducing conditions in the experiment. They might be caused by the charcoal, whose small pieces effectively hindered the flow of oxygen into deeper parts of the furnace. This does not necessarily mean that such reducing conditions were achieved also in the ancient process because citrus charcoal was not available in the Chalcolithic as previously mentioned.
In a broader scope, the very different high-temperature behaviour of Negev loess and Fazael clay hint at a probable technological explanation for the separation of at least two metallurgical centres: pure copper technology and open mould casting in the Northern Negev (Ackerfeld, et al., 2020; Golden, Levy and Hauptmann, 2001; Shugar, 2000) and lost wax casting with polymetallic alloys in the Middle Jordan valley (Rosenberg, et al., 2020). Due to its comparatively low melting temperature, the Negev loess is unsuitable for lost wax casting moulds because their walls are much thicker than crucibles. Detailed castings, like some of the Nahal Mishmar Hoard objects, require pre-heating of the mould to keep the metal liquid long enough to let it flow into all details. Pre-heating the Negev loess would probably pose the danger of the mould’s interior surface starting to melt. Moreover, it seems highly likely that the cast metal melt would have reacted with the mould to some extent and melted its interior surface. This, in turn, would have obscured the shape of the object, especially the detailed ornamentation.
In contrast, Fazael clay has a considerably higher melting temperature, and its more extensive vitrification might indicate that, at the same time, the heat transfer capabilities are superior to the Negev loess. Both aspects reduce the risk of melting in contact with the molten metal and allow pre-heating of the moulds to higher temperatures.
Conclusions
Due to the limited archaeological record, essential details of the operational sequences of smelting, melting and casting in the Chalcolithic Southern Levant (4500 to 3800 BC) are still unknown. An archaeological experiment was conducted to gain further knowledge of the technologies. This study focuses on the results of the pure copper technology. In the area, it was almost exclusively employed to cast in open moulds, differentiating it from the lost wax technology which casts polymetallic ores. The experiment successfully tested whether bellows would be a plausible alternative to the usually assumed use of blowpipes. Furthermore, data concerning the high-temperature behaviour of the clays used in the process was acquired.
Negev loess has a considerably lower melting point than the local clay of the Wadi Fazael but is, nevertheless, well suited for metallurgical processes. Employing this clay in metallurgical operations requires a very well localised hot zone on top of the crucible, which is in good agreement with the archaeological material. The experimental results further confirmed a significant colour difference between molten ceramic material and other metallurgical materials. This might help to identify such remains in the field, especially by excavators untrained in prehistoric metallurgy. Further, these differences might indicate that the incipient separation between lost wax casting in the Middle Jordan valley and pure copper technology in the Nahal Beer Sheva region could be related to the suitability of the local clay for these processes.
The experiment proved that the furnace could be successfully operated with a bellows to temperatures high enough to smelt the oxide copper ores used in the Chalcolithic. Hence, bellows must be regarded as a viable alternative to blowpipes, but further experiments are necessary to investigate this aspect. Specifically designed smelting experiments can help to produce modern-day analogues of the furnace walls with either draught technique. Compared with the archaeological material, they can help to reconstruct aspects of the metallurgical process not directly accessible by the archaeological record.
Acknowledgements
This project has received funding from the European Union’s Horizon 2020 research and innovation programme under the Marie Skłodowska-Curie grant agreement No 766311. The experiments would have been not possible without the substantial efforts of Yarden Pagelson, Cécile Fossé, Manuel J. H. Peters, and Cohava Peterman-Lipschutz. The anonymous reviewers made valuable comments, which improved the article considerably.
Keywords
Country
- Israel
- Jordan
- Palestine
Bibliography
Ackerfeld, D., Abadi-Reiss, Y., Yagel, O., Harlavan, Y., Abulafia, T., Yegorov, D. and Ben-Yosef, E. 2020. Firing up the furnace. New insights on metallurgical practices in the Chalcolithic Southern Levant from a recently discovered copper-smelting workshop at Horvat Beter (Israel). Journal of Archaeological Science: Reports, 33, 102578.
Bar-Adon, P. ed. 1980. The Cave of the Treasure. The Israel Exploration Society: Jerusalem.
Bourgarit, D. 2007. Chalcolithic copper smelting. In: La Niece, S., Hook, D.R. and Craddock, P.T. eds. Metals and mines: Studies in archaeometallurgy; selected papers from the conference Metallurgy: A Touchstone of Cross-cultural Interaction, held at the British Museum, 28 - 30 April 2005 to celebrate the career of Paul Craddock during his 40 years in the British Museum. Archetype: London, pp.3–14.
Engel, T. and Frey, W. 1996. Fuel resources for copper smelting in antiquity in selected woodlands in the Edom highlands to the Wadi Arabah/Jordan. Flora, 191(1), pp.29–39.
Golden, J.M., Levy, T.E. and Hauptmann, A. 2001. Recent Discoveries Concerning Chalcolithic Metallurgy at Shiqmim, Israel. Journal of Archaeological Science, 28(9), pp.951–963.
Goren, Y. 1995. Shrines and Ceramics in Chalcolithic Israel. The view through the Petrographic Microscope. Archaeometry, 37(2), pp.287–305.
Goren, Y. 2008., The location of specialized copper production by the lost wax technique in the Chalcolithic southern Levant. Geoarchaeology, 23(3), pp.374–397.
Goren, Y. 2014. Gods, Caves, and Scholars. Chalcolithic Cult and Metallurgy in the Judean Desert. Near Eastern Archaeology, 77(4), pp.260–266.
Hauptmann, A. 2007. The archaeometallurgy of copper: Evidence from Faynan, Jordan, Springer: Berlin.
Key, C.A. 1980. The Trace-element Composition of the Copper and Copper Alloys Artifacts of the Naḥal Mishmar Hoard. In: Bar-Adon, P. ed. The Cave of the Treasure, The Israel Exploration Society: Jerusalem, pp.238–243.
Langgut, D. 2017. The Citrus Route Revealed. From Southeast Asia into the Mediterranean. HortScience, 52(6), pp.814–822.
Levy, T.E., Levy, A.M., Sthapathy, D.R., Sthapathy, D.S. and Sthapathy, D.S. 2008. Masters of fire: Hereditary bronze casters of South India, Veröffentlichungen aus dem Deutschen Bergbau-Museum Bochum, 162, Deutsches Bergbau-Museum: Bochum.
Rose, T., Fabian, P. and Goren, Y. 2021. New insights into the Chalcolithic Metallurgy of the Southern Levant. Revisiting the evidence of Abu Matar. Metalla, Sonderheft 11, pp.12–14.
Rosenberg, D., Buchman, E., Shalev, S. and Bar, S. 2020. A Large Copper Artefacts Assemblage of Fazael, Jordan Valley. new evidence of Late Chalcolithic copper metallurgy in the southern Levant. Documenta Praehistorica, 47, pp.246–261.
Shalev, S. 1999. Recasting the Nahal Mishmar hoard. Experimental archaeology and metallurgy”. In: Hauptmann, A. ed. The beginnings of metallurgy, Proceedings of the International Conference ‘The Beginnings of Metallurgy’, Bochum 1995, Deutsches Bergbau-Museum: Bochum, pp.295–299.
Shoval, S., Gaft, M., Beck, P. and Kirsh, Y. 1993. Thermal behaviour of limestone and monocrystalline calcite tempers during firing and their use in ancient vessels. Journal of Thermal Analysis, 40(1), pp.263–273.
Shugar, A.N. 2000. Archaeometallurgical Investigation of the Chalcolithic Site of Abu Matar, Israel. A Re-assessment of Technology and its Implications for the Ghassulian Culture. PhD thesis, Institute of Archaeology, University of London: London.
Tadmor, M., Kedem, D., Begemann, F., Hauptmann, A., Pernicka, E. and Schmitt-Strecker, S. 1995. The Naḥal Mishmar Hoard from the Judean Desert. Technology, Composition, and Provenance. ‘Atiqot, 27, pp.95–148.