The content is published under a Creative Commons Attribution Non-Commercial 4.0 License.
Reviewed Article:
The Making of Roman Metal Ink Pen Nibs
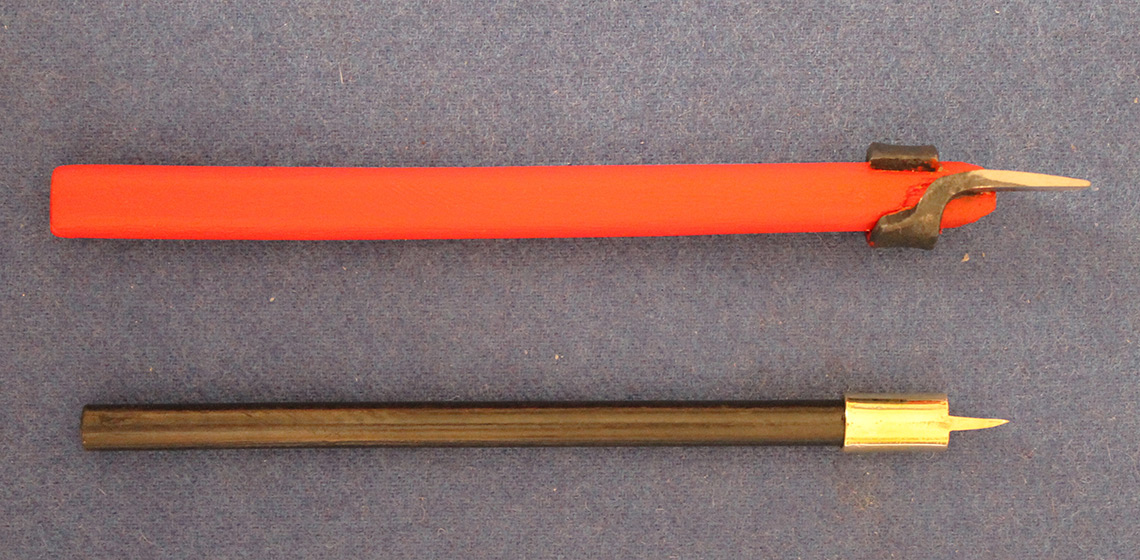
Roman ink pen nibs have been made from different materials such as bone, horn, reed, iron, and copper alloys. This article deals with experiments to reproduce Roman ink pen nibs made from copper alloy and iron.
Roman Bronze Ink Pen Nibs
Introduction
The main objective of this research was to establish the amount of time taken and the material lost to manufacture Roman pen nibs made for copper alloy and additionally iron. The original copper alloy ink pen nib being reconstructed for this set of experiments was published by Rees (1979, p.179c).
The original iron ink pen nib was published by Birley (1994).
Production parameters
These experiments adhere to a set of criteria that the author has always used when reproducing ancient artefacts:
- Only tools, materials, and equipment known to have existed during the Roman period have been used.
- The method used produces the minimum amount of waste material.
- The reproduction must be made in the minimum amount of time to ensure the finished product is fit for purpose.
Work force
These copper alloy nibs are delicate and were possibly made by a craftsman such as a jeweller, who specialised in fine metal work. The making of this type of copper alloy nib is skilled work; however, it does not mean it was carried out by a skilled metal worker. If more than a single nib was required, a likely scenario is that a skilled man taught unskilled labourers how to perform this task; small delicate hands are ideal for this sort of work so, it is possible that women and children were employed. These two groups are a ready supply of cheap labour.
Based on my 40 years’ experience of metal work, I would estimate that teaching the necessary skills could have been accomplished in perhaps, three, at most four, hours. After that time the pupil would have been able to work unassisted, but possibly supervised.
Production cost
The use of unskilled labour to perform a specific task significantly reduces the labour costs; however, labour always has a cost. If the labourers were slaves, then the cost is in kind because the slave must be maintained such as food, accommodation, and clothing. If it is in cash, then the cash payment for unskilled labour is significantly lower than that for a skilled work force.
Material
The nibs are made from copper alloy.1
Production sequence
Please see Figures 3 to 11 for the production
Making the first nib
In this set of experiments two possible manufacturing processes have been examined:
1. Using a scriber and a pair of compasses, the profile of each nib is marked out separately on a strip of copper alloy (See Figure 3).
2. Using a scriber, the profile of each nib is marked out on a strip of copper alloy using a template (See Figure 11).
Production time for marking out each nib separately
Figure Number | Operation | Time |
2 | Parent strip | |
3 | Marking out | 3 min 3 secs |
4 | Cut to shape with a chisel (ground as the cutting edge on a wood working chisel) | 3 mins 45 secs |
5 | Hammer point to work harden it | 48 secs |
6 | File point smooth and to a point | 1min 16 secs |
7 | Polish nib | 1 min |
Production time for nib | 10 min 19 secs |
Table 1. Production sequence for producing marked out nib.
Use of a template
Templates reduce the need for marking out each item separately. A template (See Figure 12) can be made using the first blank. The first nib was marked out, cut to size, then filed to the complete profile shape. This blank was then used as a template for marking out the rest of the batch. For this set of experiments, the author has considered the making of a batch of 10 nibs and handles. After the first nib was used as a template, the time to make out the first one was 21.3 secs, after four had been marked out, the time was reduced to 18.1 secs. It remained at this time for the rest of the batch. This is usual, when a new task is performed; the time taken to perform the task reduces until it plateaus, then it remains at that time.
Results
Marking out each nib separately the total production time 10 mins 32 secs. Use of a template reduces the production time to 7 mins 27 secs, a time saving of 3 mins 05 secs per nib.2
Conclusion
The advantage of the use of a template is obvious
Material loss
The original weight of the blank was 9 g and the weight of the finished nib was 5 g. The material loss was incurred when the pointed part of the nib was formed by removing the two side pieces as shown in Figure 4. The amount of material lost in further processes, such as filing and polishing, was too small to be measured on the weighing scales available, which measure down to the individual gram. This material, however, would not go to waste. Copper alloys are, and always have been, expensive materials and as such are recycled. They are usually melted down and then reused. It is also likely that floor sweepings were also melted down. When the metal is liquid, the unwanted detritus would float to the surface and would be skimmed off. The amount of material lost in the manufacture of copper alloy pen nibs is negligible (1g probably less).
Making the handle
See Figure 13
Production sequence of handle
A shaft of pine 60 cm long and 10 mm in diameter was produced (any type of wood can be used). From the time taken to make this length of round rod, it was calculated that the production time for each step was as follows:
- Production of an individual shaft = 49 secs;
- Cutting to length from parent rod = 6.3 secs,
- Smoothing the surface with a piece of sandstone = 34 secs;
- Applying black wax to surface and buffing with a soft rag = 1 min 20 secs
This lead to a total production time of 2 mins 50 secs. This means that the total production time for the nib and the shaft was 10 mins and 17 secs.3
See Figure 14
Use for writing
Several experiments were conducted with the point straight. None left any trace of ink on the page. After the nib was bent over (See Figure 8), the pen was used successfully. It can be seen in Rees (1979, p.179c) that the pointed tip of the nib is bent over. The scientific explanation as to why this happens would require a study of the surface finish on the nib, the viscosity of the ink, and its liquid flow dynamics, however, that work is beyond the scope of this paper.
See Figure 15 and 16
Discussion
In any manufacturing process there are always several methods that can be used to accomplish a finished product. This set of experiments was conducted to a set of criteria (see production parameters above). The tooling used for making this nib would be found in any metalworking shop, be it a blacksmith, or a jeweller.4
Experiments to reproduce Roman iron pen nibs
See Figure 17
Iron Nibs
No metallurgical analysis has been conducted on these nibs. There is a high probability, however, that these nibs were made from wrought iron.5 The making of this nib is skilled work; however, that does not mean it was carried out by a skilled metal worker.
The manufacture of iron pen nibs is forge work and would most likely have been carried out by a blacksmith or at least in a blacksmith’s forge. A likely scenario is that a skilled man taught an apprentice or even an unskilled labourer how to perform this task. Teaching could have been accomplished in perhaps, three, at most four, hours. After that time the pupil would have been able to work unassisted but possibly supervised.
Manufacturing Process
The Experiment
For this experiment, only tools and equipment known to have existed in the Roman period were used. The heat was from charcoal, blown with a pair of bellows. The hammer, anvil, and tongs were copies of Roman tools, made by the author. These tools have been used in many experiments since 1991 and have proven to be as efficient as modern tools. The development of blacksmiths tools had reached its terminal stage by the start of the Roman period.
Sequence of Production Operations
The Process
Please see Figures 18 to 24 for the process
Timings
The iron was heated to 750°C, appearing as a bright red colour. At this temperature, the iron is malleable and ductile. It took eight heats to complete the forging of the pen nib; this is because the metal is thin and does not hold heat. The iron remains at forging temperature for only 15 secs before reheating is necessary. The anvil and the hammer act as heat sinks, which reduces the amount of time the metal is at forging temperature.6 The material loss in this process was less than 1g.
Figure Number | Operation | Time |
18 - 22 | Total forging time | 7 mins 43 secs |
23 | Total filing time | 3 mins 14 secs |
24 | Making the handle | 2 mins 16 secs |
Total production time | 13 mins 13 secs |
Table 2. Production sequence for producing and iron nib.
Aesthetic appeal
The pen shown in Figure 24 is fully functional but has little aesthetic appeal.
Figure 25 shows the same pen when the nib has been coated with black bees’ wax and the handle given a coat of red paint. After this embellishment it is much more aesthetically appealing.7 It took 5 mins 19 secs to add these embellishments, which brings the production time to 18 mins 32 secs.
Use for writing
The author used these pens along with those people mentioned later in this paper. We all had much the same experience in that after a few attempts to get used to these pens they wrote smoothly with no snagging. The paper was modern white card with the surface burnished with a bone folder. The ink was a reproduction of Roman ink (see Sim and Brown, 2014).
The frequency of re-dipping the pens was variable from person to person. For more details see (Sim, 2014).
Conclusion
The use of ink pens is well attested in the Roman period (Birley, 1994). Opinions vary as to the level of literacy in the Roman period, Echart puts it at 15%. The empire was so large and lasted for so long, however, that it is almost impossible to determine the level of literacy. A best guess is that it was between 10% to 15%. This means there is no secure information as to the number of ink pens that may have been manufactured. The low visibility of copper alloy pen nibs in the archaeological record may have many explanations; however, there are two major factors that need to be considered. Firstly, copper alloys are too valuable to discard, and are usually melted down and recycled. However, some may have just been lost and have returned to their original state, there is no way to be sure. Both copper alloy and iron nibs are simple and quick to make, therefore they would not be expensive items.
Secondly, their number and distribution has not been studied in depth, so it is impossible to put an accurate figure on how many were made and to what level they were distributed throughout the empire. A factor that also makes their number and use difficult to quantify is that they have been miss identified and recorded for some other purpose, such as ox goads.
Acknowledgments
I would like to thank Chris Legg and Margaret Lawrence for their help.
- 1
Roman brass was an alloy of Copper, zinc, and Tin, or in some cases Copper and Zinc. This is the common composition of Roman brass. The proportion of alloying elements in Roman brass are variable and there are no single standard set of proportions; however, the brass used in these experiments also so contains copper, tin and zinc.
- 2
If this process were divided into individual tasks, the time to produce each item could be reduced by as much as 25%; however, so far, it has not been possible to experiment with this idea.
- 3
If this process were divided into individual tasks, the time to produce each item could be reduced by as much as 25%; however, so far, it has not been possible to experiment with this idea.
- 4
If a production run of, say, 100 or more was required, then an investment of time and money in making a pair of press tool becomes a viable proposition. Given the high quality of Roman die sinking, as seen in the quality of coins, the making of such a pair of tool was easily accomplished. Such a pair of punch and die tools would reduce the production time of the blank to anywhere between 8 to 10 secs, depending on the operative.
- 5
The material this type of nib is made from is wrought iron. The metallurgical composition of many types of iron used in the United Kingdom during the Roman occupation varies in chemical composition. Some has a carbon content that put it in the category of steel, all be it low carbon steel. Other has almost no carbon and this material is what is called today, Wrought Iron. For this set of experiment Wrought Iron was the chosen material.
Nails I have examined shadowed many to be made from wrought iron, therefore that material was chosen because it was a common ferrous metal during the Roman period. - 6
This is light work and well within the physical ability of women and children. We only have to look at the work force in early 20th century Birmingham to see that children as young as four years old were employed in nail making, and in Sheffield children were employed in file making, amongst other manufacturing processes.
- 7
Roman brass was an alloy of Copper, zinc, and Tin, or in some cases Copper and Zinc. This is the common composition of Roman brass. The proportion of alloying elements in Roman brass are variable and there are no single standard set of proportions; however, the brass used in these experiments also so contains copper, tin and zinc.
Country
- United Kingdom
Bibliography
Birley, R., 1994. Roman Records from Vindolanda . Greenhead, Nothumberland:Roman Army Museum Publications.
Rees, S., E., 1979. Agricultural Implements in Prehistoric and Roman Britain, Part I. BAR British Series 69(1). Oxford: BAR Publishing.
Sim, D., 2014. Wood and Ink. Experiments in the Technology of Roman Writing.
UK: Vulcanus Publications.
Sim, D. and Brown, K., 2014. A Sticky Situation. The use of different gum in Roman ink from the Vindolanda Tablets. UK: Vulcanus Publications.