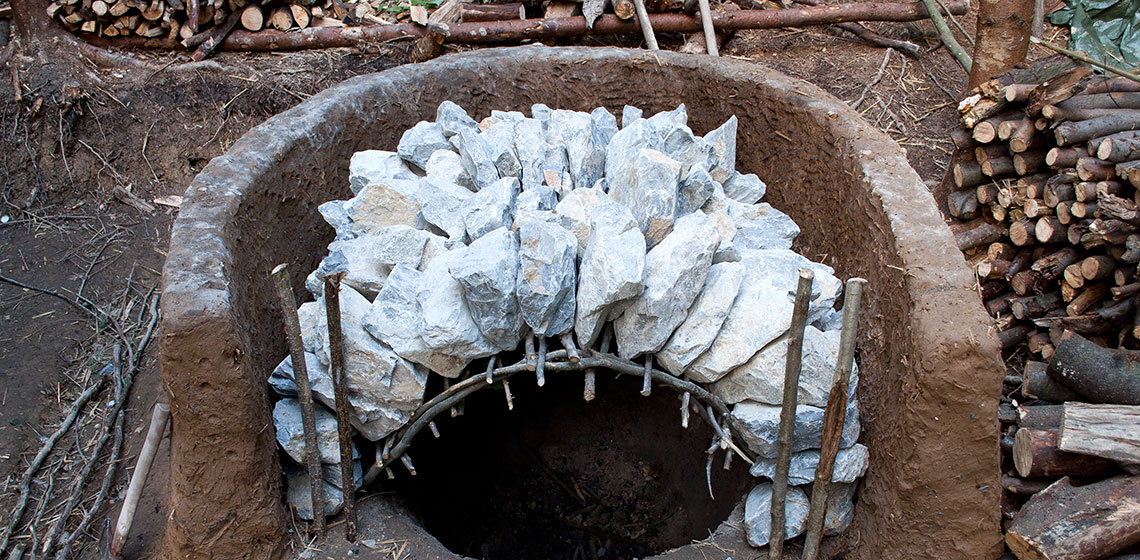
In 2006 the remains of two lime kilns from the Roman Empire period were discovered in Tuněchody near Chrudim in the Czech Republic. These finds became the object of a detailed multidisciplinary research project resulting in hypotheses on the use of the kilns. Based on these hypotheses experimental research was designed (Thér et al. 2010). The detailed results of these experiments will be published elsewhere. The aim of this article is to share the experience with basic technologies of lime burning that we can assume to have been used within the context of the Roman Empire period and that can be theoretically used in pyrotechnical structures from the Roman Empire period known in our region.
In Central Europe the technology for lime burning probably appeared in relation to cultural influences from the Roman Empire environment where lime was used mostly in building but also other purposes. Recently it was discovered that the production of lime in the barbarian territories during the Roman Empire period was much larger than earlier assumed (Uschmann 2006).
The process itself can be described by the following chemical reactions:
Lime burning produces quicklime/calcium oxide (CaO) and carbon dioxide (CO2) which escapes into the environment. This reaction takes places at temperatures above 700°C. Quicklime is highly reactive and in contact with water it changes into slaked lime/ calcium hydroxide (Ca(OH)2).
This reacts with CO2 in the air, which releases water creating solid slaked lime (Carbonisation) which is calcite CaCO3.
The find and the hypothesis
The feature that inspired the experimental kiln had an oval plan. It was 1.3 m long and 1 m wide, and it had a flat bottom slightly sloping towards the north. The maximum depth was 0.7 m, with a volume of 0.7 m3. Most of the infill consisted of two types of daub. The top was mostly filled with large blocks of this material. The surviving surfaces carried traces of smoothing by hand and were mostly flat. At the bottom there were daub fragments with numerous imprints of armature, the surface was covered with imprints of fists. At the complete bottom of the kiln there was a compact layer of a greyish-white ash mixed with a small amount of daub. The bottom was mildly burned to a depth of, at most, 2 cm, stronger on the south side. The burning of the sides strengthened towards the top and reached a depth of 10 – 14 cm, evenly along the whole circumference of the feature.
After ascertaining the function of the kiln with the help of petrographic analysis of the ash layer, it was necessary to decide what type of lime burning was in use. Based on the process of lime burning we can distinguish two basic methods: one-chamber and two-chamber burning. In a one-chamber burning the load of lime material was mixed with fuel and partially isolated from the outside environment. In the case of two-chamber lime burning the fuel is divided from the load most often by an arch created from the material that is being burnt above the hearth. Both methods are known from western Roman provinces (Dix 1982). The two-chamber method was experimentally tested based on evidence from Roman provinces (Sölter 1970, 1977) and from the barbarian territory (Uschmann 2006) and can be compared with replication of historical small-scale lime burning (Kos 2002). The one-chamber method was experimentally tested in the context of Pre-Pottery Neolithic in the Near East (Goren and Goring-Morris 2008).
The remains of the reconstructed feature of the pyrotechnical structure from Tuněchodyis similar to other finds from the period (Uschmann 2006) and corresponded to the two-chamber burning method because of its depth, the even burning of the surrounding terrain and the presence of large amount of evenly burnt daub. There were several construction hypotheses of the kiln design. The hypothesis that carried the least contradictions with the data was used as a model. According to this hypothesis the permanent sides of the kiln consisted of a daub coating a horseshoe shape offset from the sunken part in such a way that it created a bench to build the lime arch on. The front side stayed free, which made loading the kiln easy. Only after loading was this side closed with thick rod armature coated with daub. After the burning this side was dismantled.
Although the analysis suggested that two-chamber burning was more likely, the one-chamber burning was tested experimentally as well to allow for comparison of the effects of both situations with the found situation and gain clearer results.
One-chamber burning
The design of the one-chamber kiln was based on the requirements of this type. The sunken part was created according to the archaeological find. The above ground cylindrical cover of 70 cm height connected directly to the sunken part. The cover widens conically on the inside. At the circumference of the cover at its base there were four drawing eyes to allow for regulation during the burning (See Figure 1).
We used limestone from the Holštejn quarry in the Moravian Karst. It is grey to light grey bioclastic limestone with more than 96% of CaCO3. For the one-chamber burning it was crushed into fist-sized pieces. The fuel consisted of mixture of spruce and alder branches of about 8 cm diameter. When loading, the fuel was organised radially. The kiln was loaded alternately with layers of wood (See Figure 2) and limestone (See Figure 3) until it was completely full. The last layer functioned as insulation and consisted of large pieces of limestone (up to 40 cm in length). In the middle of the load a vertical shaft of about 30 cm diameter was left. The shaft was filled with spruce brushwood. About 600 kg of limestone and 150 kg of wood were used.
After igniting the brushwood, fuel was added for some time until the fire started properly (See Figure 4). The burning then went on without any further intervention. After about three hours the temperature of the top part of the load exceeded 800°C (See Figure 5A: T3 and T4).
The time of burning at this temperature was relatively short. The temperature in the lower parts never exceeded 800°C. The thermal maximum there was reached after about 15 hours of burning and for nearly 8 hours the temperature stayed above 600°C.
The burning was unsuccessful. The blocks of limestone were covered by about 1 mm thick layer of quicklime. The strongest layers were observed in the middle part of the load where an ideal combination of maximum temperatures and time of burning within this burning combined. The main problem seemed to be the lack of air within the lower parts of the kiln.
The primary aim of the next burning was therefore to adapt the loading of the kiln to allow for a better circulation of air throughout the whole load. The first layer of fuel was therefore stacked in a grate manner. Vertical rods were placed in the area of the drawing eyes (See Figure 6). These were pulled out after loading of the kiln, which left vertical channels leading from the lower fuel layer up to the surface of the load. All together we used 500 kg of limestone, 130 kg of gravel for insulation and 200 kg of wood. The temperatures in the centre of the load reached a maximum of about 950°C after 4 hours (See Figure 5B: T2 and T3).
In the lower part of the load lower temperatures of about 750°C were reached after 11 hours of burning (See Figure 5B: T2 and T3). The result was again only a partial change of the surface layer of stones into quicklime, but better than during the first burning. From the middle of the load it was possible, after separating, to take out a small amount of quicklime (2 kg).
Two-chamber burning
The kiln for the two-chamber burning was built according to the above described hypothesis (See Figure 7). A rod vault was built above the sunken part of the kiln arching over the narrower site of the hole (See Figure 8). The hazel rods creating the base of the vault were held by a layer of limestone stones stacked on the bench created by offsetting of the kiln sides from the hole. The ribbing thus created was later interwoven with thinner twigs. From the quarried material we selected flat and wedge shape stones of up to 50 cm long to build a stone vault on the rod armature arching over the whole hole.
At the front the vault stayed open (See Figure 9). There was eventually built a wall from combination of turf and armature covered with daub. A drawing eye (20 x 35 cm) was left open at the centre of the front side. A layer of limestone rubble with fragments up to 10 cm big was placed on the arch and the whole load was finished with a layer of fine fragments (up to approximately 4 cm). Altogether about 1000 kg of limestone were loaded into the kiln.
The fuel consisted mostly of spruce in various sizes from brushwood to logs of 20 cm diameter. The quality of wood was not ideal as most of the wood was gathered from the surrounding woods during the burning. It was not green wood, but in many cases the wood was not sufficiently dry or it was partially rotted. About 300 kg of fuel were used.
Before ignition the hearth was filled with fuel. The operational temperatures at the surface of the limestone vault were reached within two hours of burning (See Figure 5C: T1 and T2). The rest of burning the operational temperature gradually reached the edge of the load (See Figure 5C: T3 and T4) (See Figure 10).
The fuel was added for 17.5 hours. The burning was very effective thanks to the fact that the hearth was sunken. The single pieces of wood were, after they were added, leaning against the layer of embers on the bottom and against the edge of the drawing eye on the other side. Most of the wood surface was therefore exposed to oxygen flowing into the kiln during burning. Thanks to that it was possible to use low quality fuel without causing a decrease of the operational temperature.
When taking the vault apart, we found that the top layer of limestone was not burnt enough (See Figure 11). The total weight of not-burnt or only partially burnt limestone was 500 kg. The rest of infill consisted of lime (See Figure 12). On the bottom there was a 21 – 23 cm thick layer of ash and embers.
The burning of the walls of the sunken part of the kiln deepened from the bottom towards the bench up to 20 cm. The thickest burn layer was represented by a dark grey to black layer with carbonised organic components that was behind and orange burnt layer of maximum depth of 4 cm.
Discussion
The experiments with lime burning suggest that the lime kiln found at Tuněchody seems better accustomed to two-chamber burning. There were no complications with this type of burning. It also showed to be undemanding concerning the quality of fuel, which is an important fact if we consider the high consumption. The yield was unsatisfactory. We presume this was caused by the amount of limestone load. The open outer area of the load causes heat to escape and prevents a sufficient burning of the upper parts of the load. It is therefore possible to presume that with a larger load we would get approximately the same amount of unburnt limestone while the amount of lime would increase. As it follows from the suggested design of the kiln the height of the sides can be seen as minimal as it was based on the amount of daub gained directly from the infill of the sunken feature, therefore the capacity of the kiln could have been higher.
The one-chamber burning has much higher demands of the quality of fuel and also on the preparation of the material. The lime-burners may have possibly collected the needed limestone from scree or gravel or used fine-grained carbonate sediments like for example lake chalk. The access of oxygen to lower parts of the load creates a problem, demanding a high quality of fuel. For this type of burning wide shallow holes or surface shafts are more suitable.
Nevertheless the fact that the two-chamber burning in the given kiln seems to be distinctively more effective cannot be taken as a proof that this method was used. From this point of view the thermal alteration of sides of the sunken part and the creation of its infill is more interesting. These features, compared directly to the archaeological situation, correspond more likely with the two-chamber method. It primarily concerns the potential to cause deep and even alteration of sides by burning and the creation of a thick ash layer on the bottom of the hearth during standard use.
Bibliography
DIX, B., "The manufacture of lime and its uses in the western Roman provinces", Oxford Journal of Archaeology, vol. 1, pp. 331–346, 1982.
GOREN, Y., and A. N. GORING-MORRIS, "Early pyrotechnology in the Near East: experimental lime-plaster production at the Pre-Pottery Neolithic B site of Kfar HaHoresh, Israel", Geoarchaeology, vol. 23, pp. 779–798, 2008.
KOS, P., "Experimentální výpal vápna v peci ze 16. století u Mokré", Archeologia Technica, vol. 13, pp. 9-17, 2002.
SÖLTER, W., Römische Kalkbrenner im Rheinland, Kunst und Altertum am Rhein, Rheinland-Verlag, Düsseldorf, 1970.
SÖLTER, W., "Antike und moderne Technologie. Der neueste Kalkofen und der Iversheimer Ofentyp", Berichte aus der Arbeit des Museums, vol. 2, Bonn, Das Rheinische Landmuseum Bonn, pp. 17–19, 1977.
THÉR, R., E. DROBERJAR, M. GREGOR, L. LISÁ, P. KOČÁR, and R. KOČÁROVÁ, "Vápenické pece z doby římské v lokalitě Tuněchody (okr. Chrudim)", Archeologické Rozhledy, vol. 62, Praha, pp. 326–347, 2010.
USCHMANN, K U., "Kalkbrennöfen der Eisen- und römischen Kaiserzeit zwischen Weser und Weichsel. Befunde – Analysen – Experimente", Berliner Archäologische Forschungen (BAF), no. 3, Rahden, Westfalen, 2006.