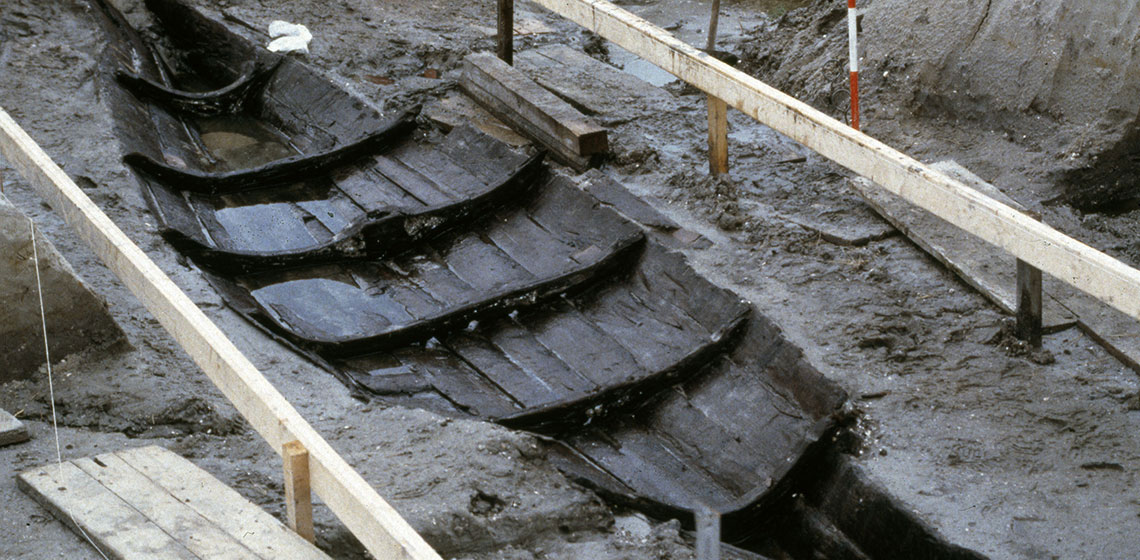
In 1993, the remains of a wooden boat were uncovered during drainage works north of the village of Gislinge, on the island of Sjælland in Denmark (Gøthche 1995). Now reclaimed agricultural land, the area had once been part of the shallow Lammefjord, itself connected to the Isefjord and the open sea. The boat was remarkably well preserved, and initial features such as the stepped stem and overlapping planking suggested that it may have been Viking Age in date (Gøthche 1995: 186). Later analysis proved the excavators’ first impressions were reasonably accurate; the find was dendrochronologically dated to ca. AD 1130, making it the first significant Danish find of a smaller vessel from the early Middle Ages.
The Gislinge Boat was a 7.7m long working boat, most likely used for fishing and the transport of people, livestock, and goods around the coastal settlements of the Lammefjord. We do not know exactly why it met its end on the bottom of the fjord but it had seen better days, and displayed signs of many years of hard service (Gøthche 1995:188). Several cracks in the hull had been patched using pieces of beech, yet despite the high level of wear and tear, the Gislinge Boat had once been a top quality vessel. Built entirely of oak, and with decorative profiles on many of its timbers, it was most likely a working boat in a larger fleet belonging to a local chieftain or land owner (See Figure 1).
The boat was reconstructed in full-scale at the Viking Ship Museum in Roskilde, in 1995 (This reconstruction was subsequently sold to the National Maritime Museum, Pusan, Republic of Korea.). Twenty years later, the decision was made to build a second reconstruction of the Gislinge Boat, using the same reconstruction model and working drawings that had been produced for the first version in 1995. This time, however, the project would have an added dimension, one that would seek to involve the public in the construction of the boat, while at the same time addressing the power and potential which the online world has in terms of communicating experimental archaeology.
Project background
With the Gislinge Boat, we wanted to explore to what extent the public could be involved with the experimental archaeological boatbuilding process. How could we get both visitors to the Museum and online followers as close to the boatbuilding process as possible? Even more ambitiously, would it be possible to get others building their own version of the Gislinge Boat? To that end, a cross-disciplinary project group was established, with representatives from the boatyard, the education and outreach department, and the exhibitions and communications teams, in the spring of 2015. The whole project was inspired by the open source concept: the idea that information and knowledge should be shared freely and openly, be as accessible as possible, and that this exchange of information should give rise to a dialogue between the Museum practitioners and the public.
Open source boatbuilding: new departures within maritime experimental archaeology
The Gislinge Boat Open Source Project was therefore designed as a combination of maritime craftsmanship, education and outreach activities, experimental archaeological research and digital communication, and was based upon four key elements:
- Make the working drawings for the construction of the Gislinge Boat freely available for download on the project website, allowing other boat builders the chance to build their own version of the boat
- Document and present as much of the construction process as possible online via the project website, Facebook, and Instagram, so that all those interested can follow and become engaged in the project
- Explore the ways in which we can 'involve' Museum guests in the construction process through new hands-on workshops based on the various processes involved in building a boat, creating a dialogue between the boat builders and our visitors
- Conduct a programme of experimental archaeological research both during and after the build
The project begins: building the boat
When building reconstructions of archaeological boat finds, an enormous amount of work must be undertaken before the boat builders can begin to swing an axe. The excavated remains must be recorded in detail and a scaled-down 3D reconstruction model of the find is produced in cardboard. Vessels rarely survive in their entirety, and the Gislinge Boat was no exception to this rule. Along with the t-shaped keel and the lower part of the after stem, the Gislinge Boat survived to a height of three strakes on the starboard (right-hand) side and to the fourth strake on the port (left-hand) side. Six frames also survived, including the mast-frame, with its hole for the foot of the mast, proving that the Gislinge Boat had been equipped with a sail. A loose stanchion as well as the presence of stanchion holes in several of the frames, also indicated that the boat had been fitted with cross beams, which would have strengthened the hull transversely while also doubling as thwarts for rowing (Gøthche 1995:187).
Therefore, while much of the boat had survived, the overall height of the hull was unknown, and the rudder, mast, yard, and all traces of sail and rigging were also missing. This is where the ship reconstructor must draw on other archaeological parallels, as well as their experience in reconstructing other archaeological ship-finds in order to fill in the gaps. When complete, the 3D model forms the basis for the boat builder's work in full scale, and it is at the model-making stage that all decisions concerning the boat's lines, shape, and form are made.
All boat and ship reconstructions built at the Viking Ship Museum boatyard are – as much as is possible – built using replica period tools. Axes dominate the boat builders' tool kit and the various axe types all serve different purposes: the heavy, thick-bladed axe from Skolegade in Århus is effective when felling trees, the bearded axes from Sæbø and Gjermundbu are best suited for shaping along specific lines and making finer adjustments, while the broad-bladed axes from Hedeby and Over Hornbæk are used to shape and smooth the face of planks and other longitudinal timbers. Knives, chisels, spoon-shaped augers, bow drills, clamps, adzes, planes, peening (riveting) hammers and profile scrapers complete the tool kit, and their use in late Viking Age/early medieval boatbuilding is attested archaeologically, either through recovery of tools during excavation or in the tool marks present on excavated ship and boat timbers (Finderup 2006).
As the boat had already been reconstructed previously, it was not the vessel as a whole that constituted the experimental archaeological aspect of the project. Rather, the boat builders outlined some specific areas of research that they wished to address, which through building another Gislinge Boat gave them the opportunity to explore:
- Production of iron rivets from bog ore: are rivets produced from bog ore more resistant to corrosion than other types of iron?
- Production of a hand-woven linen sail: how does linen perform as sailcloth?
During the spring of 2015, the project began exactly where the builders of the original Gislinge Boat started: in the forest. The boat builders searched the woods at Bøndeskovgård, Vallø and Jægerspris, looking for suitable materials for the boat. The original Gislinge Boat was built entirely of oak, so the boat builders selected a long, straight-growing oak to provide material for the planks, another straight-growing oak for the keel, a short, thick section of oak for the stems and several crooked timbers – branches and forked pieces, which have grown with a natural curve – for producing the frames. Other specifically shaped pieces of oak were chosen for the oar locks, rudder, and other fittings (See Figure 2).
Although the Gislinge Boat is technically medieval in date, it is still very much a part of the Viking Age boatbuilding tradition. While small saws have been found dating from the Viking and early Middle Ages, to date, no trace of saw marks has ever been identified on Scandinavian boat or ship timbers from those periods. Timbers must therefore be cleaved, either radially or tangentially depending on the type of wood in question, or hewn down to size (See Figure 3).
Work on the keel and stems began in mid-May and marked the start of a busy summer season at the boatyard. The outer circumference of the oak trunk for the keel was removed to create a square-sectioned blank, from which the T-shaped keel could be hewn. The fore and after stems were hewn out of another oak log, which had been cleaved to 1/8 sections. When the keel and stems were finished, they were raised on the stocks and the work of producing planks could begin.
The oak for the Gislinge Boat's planks was radially cleaved, a process that splits the wood along the length of its fibres, preserving a great degree of the wood's natural strength and flexibility (Nielsen 2011:66). All of the planks were cleaved from a single oak log, a process that began in the middle of June and continued until the middle of September. The technique of cleaving is a relatively simple one on paper, but it demands a high degree of understanding in terms of oak as a material and the way in which it behaves when worked. A line of wedges was driven into the root end of the 180 year-old oak log, and these were hammered into the oak, creating the first split into halves. As the wedges were worked further into the oak, larger wedges were then utilised. As the split progressed, wedges were also worked in from the long side of the log, forcing the fibres to divide. This process was then repeated, cleaving the oak further into quarters, eights and sixteenths.
The individual planks were then hewn and dressed to the correct dimensions. Once complete, they were ready to be bent on to the hull. Although the oak was fresh, it still needed a little extra encouragement in order to achieve the extreme sweeping curves of the Gislinge Boat's hull. Pairs of planks were heated over the embers of an open fire for ca. 25 minutes, and were rotated and coated with water every 30 seconds. The heat quickly converts the water to steam, which penetrates the fibres of the planks. This process warms the lignin -the natural glue within the fibres of the wood- making it pliable for a short window of time. Once sufficiently warm, the planks were clamped into position on the hull and allowed to set overnight, before being removed again for the final small adjustments prior to being riveted fast. This technique is the equivalent of the modern boatbuilder's steam chest, and one that has been refined over the course of several reconstruction projects. Prior to the fastening, caulking thread made of three-ply tarred wool was set into the land or overlap between the planks, helping to make the boat watertight (See Figure 4).
Like all clinker-built boats, the Gislinge Boat was built 'shell first': the garboards were attached to the keel and stems and the exterior of the hull was gradually built up, before the inner transverse timbers were inserted. Once the third strake had been attached, the boat builders could begin working on the frames. These transverse timbers are actually made up of several elements:
- Floor timbers: these sit in the bottom of the boat and form the base of the frame
- Futtocks: these sit on top of the upper edges of the floor timbers and extend the length of the frame upwards along the side of the hull
- Cross beams: on a small vessel like the Gislinge Boat, these double as thwarts for rowers. On the Gislinge Boat, they are formed with an integral knee in one end
- Knees: These angled timbers form the join at the opposite end of the cross beam
The frames were secured in place using treenails made from goat willow and pine, with wedges of oak. The treenails must be made in advance and allowed to dry, so they will expand and create a tight seal when the boat is first placed in the water (See Figure 5).
Once the floor timbers were in place, the final strakes, bulkheads, crossbeams and futtocks could be fitted. Each of these elements was produced from timber chosen specifically for that piece, as the wood had grown with the correct natural curve. Breasthooks are then inserted, followed by the row locks and additional thwarts.
As outlined above, some of these elements, and also other essential components such as the rudder, yard and mast, were missing from the original Gislinge Boat, so it was therefore necessary to reconstruct them on the basis of other similar archaeological boat finds. The small boats from the Gokstad find and some loose finds of boat timbers from the excavation of the medieval harbour of Bryggen in Norway provided comparative material, from which the boat builders could reconstruct the missing elements of the Gislinge Boat (Herteig and Christensen 1985: Nicolaysen 1882) (See Figure 6).
Traces of yellow ochre were found on the inner face of one of the planks of the original Gislinge Boat, so it was also decided to paint the upper two strakes on the hull's interior using yellow ochre pigment, while the rest of the boat was given a liberal coat of wood tar.
Rigging
With the hull complete, it was time to begin rigging the boat with the ropes the Museum's ropemaker had made during the previous months. In contrast to the later medieval period, there is little to no evidence for the use of hemp as rigging material during the 12th century (Magnus 2006:29). Instead, rope made of bast – the phloem or inner bark – from the lime tree (Tilia cordata) dominates the sample of surviving archaeological finds of rope from the Viking and early Middle Ages (Magnus 2006:30). Other materials that are also present in either the archaeological or historical records of the time include wool, hair (such as horsehair), tree roots (twisted to form withies), and skin (from walrus and seal) (Magnus 2006:29). The various materials all have different properties, making them better suited to either the standing or running rigging. Several different materials were therefore used in producing the Gislinge Boat's rig: sealskin, wool and lime bast were all employed, the strengths of each material dictating their position on the boat (See Figure 7).
While the various materials require different preparatory methods, the basic theory behind laying rope by hand remains the same: fibres, be they plant or animal, are twisted into chords, which are then laid together to make thicker lengths of rope. The rigging serves to stabilise the mast, to raise, lower, secure, and control the yard, as well as to trim and reef (reduce the surface area of) the sail.
Sail
Another element of the experimental archaeological research in relation to the Gislinge Boat was the manufacture by hand of a linen sail. To date, there has not been any definitive archaeological find of sailcloth from the Viking or early Middle Ages. The Museum has previously produced several hand-made wool sails, but had not yet attempted to make one from linen. Given the evidence for specialised processing of flax and production of linen during the Viking Age at Danish sites such as Næs, Skansø and Århus Søndervold, it was decided to produce a hand-woven linen sail, in order to explore the material's potential for use as sailcloth (Hansen and Høier 2001: Jensen 2004). The Museum's weaver would weave one of the five panels that would make up the 10m2 sail on a reconstructed warp-weighted loom, while the other four panels would be woven by hand on modern looms by weavers from the Institute for the Blind and Partially Sighted (IBOS), with whom the Museum had previously collaborated on the production of a sail for Eik Sande, the biggest Gokstad boat (See Figure 8).
While Anna's panel was completed at the Museum over the summer, problems sourcing adequate amounts of flax to complete the panels at IBOS meant a tough decision had to be made: should they wait for IBOS to complete the remaining panels and leave the boat without a sail for the rest of the sailing season, or should they order machine-woven linen sailcloth, so that test-sailing of the boat could begin in 2015? In the end, the decision was made to purchase modern sailcloth to make a pilot rig ready for the launch in October, allowing us to begin test-sailing straight away while also giving us the chance to fine-tune the design of the sail. The hand woven sailcloth would then be finished over the autumn and a fully handmade sail produced for the 2016 sailing season.
Rivets
In addition to wooden treenails, the Gislinge Boat is also held together using iron rivets. While the majority of iron produced in Denmark during the late Viking and early Middle Ages was produced from bog ore, this type of iron is rarely if ever used when building reconstructions (Bill 1994: Buchwald 2005). In keeping with the open source philosophy of the project, it was decided to conduct an on-site smelting trial, where the resulting iron would be forged into rivets and roves to be used on the boat (See Figure 9).
Iron smelter, Mads Jylov, and blacksmith, Jonas Bigler, ran a week-long workshop at the boatyard, where they conducted four controlled smelts using bog ore from Guldager. They produced a sample of 23 rivets and roves, which were placed at strategic points around the Gislinge Boat's hull, allowing us to explore how the iron reacts when under different levels of stress and both above and below the waterline.
Open source boatbuilding in practice: creation and communication
The Museum has a long history in the reconstruction of archaeological ship and boat finds and providing the working drawings to other groups involved in reconstruction projects. Normally, this is a service we would take a fee for. However, the open source philosophy we adopted with the Gislinge Boat Project meant that for the first time, a full set of working drawings would be made available for free download.
This international interest in building a reconstruction of a 12th century Danish boat has been fuelled by the digital communication of the boatbuilding process. A dedicated project website was developed, where the background to the find and the project itself was outlined. It also hosted a blog, with regular updates on the progress of the build, from the first days selecting timber in the forest to the launch of the boat six months later. Social media also played a large role in the open source element of the project: the ambition was to share the progress as and when it happened and the immediacy offered by platforms such as Facebook and Instagram allowed us to communicate the process in real time. Digital communication also gave us the chance to enter into a dialogue with the virtual Gislinge Boat community, who became actively engaged and involved in the reconstruction of the boat – a community which grew exponentially over the course of the project and which has demonstrated the great interest the general public has for experimental archaeology, both here in Denmark and abroad.
As of spring 2016, over 300 people from Argentina to Vietnam, Canada, Australia and everywhere else in between had downloaded a copy of the drawings with a view to beginning their own projects.
Activities during the build: involving the public in the boatbuilding process
The construction of the Gislinge Boat was also an educational and outreach project, designed to give the public the chance to try craftwork for themselves rather than just observing the practising crafts people. In this way, the activities connected to the build were also linked to the 'open source' philosophy: interested visitors – with the downloaded drawings to hand – could at any point get a practical introduction to Viking Age boatbuilding from the professional craftsman's perspective.
Activities at the Museum are consciously focused on atmosphere, sensory experience, the Museum's own materiality, and what all this can mean in terms of what visitors can learn, and, the manner in which they do so. The idea is that today's guest is the co-creator of knowledge. They can read exhibition texts and observe the 1000 year old ships, but as an extension of this we try to work with addressing their senses and their own bodily experience of history.
The boatbuilding workshop formed the core of the education and outreach activities, and was located right beside the Gislinge Boat's stocks at the boatyard. Here, visitors could try the same techniques, tools and methods the boat builders used. The workshop was manned by a specially trained guide, who could advise the public as to how to use axes, planes and spoon augers.
Guests could try boatbuilding first-hand: to witness themselves how a plank can be worked so thin and still maintain its strength and flexibility. The boatbuilding workshop gave visitors the chance to 'step inside' the boat builder's workshop and learn the tricks of the trade. Our visitors experienced a sensation of being admitted into an exclusive world, which normally is not accessible for all.
During the construction, we focused sharply on the ancillary craft practices which were also necessary to build the Gislinge Boat: how iron is smelted from bog ore and forged into nails, how rope is made from lime bast, horsehair, wool and hide, and the processes involved in producing a sail from flax. Each of these topics was the focus of a themed week, where guests could get up close and personal with the processes.
As a new departure, the boat builders held guided tours of the boatyard, where the construction of the Gislinge Boat and the use of traditional tools became the 'artefacts' they talked about. Normally, when tours are given about boatbuilding, it is the museum's guides who hold them and who decide on what angle should be presented. As a rule, the angle from which the tour is presented is entirely different when it is the boat builders who get the chance to curate a tour. A craft is best understood by the craftsmen themselves, and it is often the most specific details that appeal to the audience, giving them the best experiences and the deepest insight.
Craft and Design: putting the Gislinge Boat on the educational agenda
The Museum's Education Department developed a course connected to the Crafts and Design syllabus – a subject which has been newly developed due to reform of the Danish school system. A special pilot programme was developed in collaboration with Absalon School in Roskilde and Boserupgaard Nature Centre.
The programme involved six workshops over six weeks and focused on the following areas:
- Design process: from a sketch to the finished product
- Selection of materials, tools, preliminary work, production and composition
- Exploring the construction of a ship and the significance of the interplay between sail, hull and rig
- Developing an understanding of the characteristics of the materials from wood to ship
- Insight into the Viking Age and its material culture
The first workshop involved an introduction to the project, and the pupils drew sketches of a ship in order to understand its construction. Afterwards, they took to the fjord in the Museum's traditional Nordic boats, learning how important the interplay between sail, hull, and rig is. On day two, the pupils went to the forest of Boserup. Here, they were introduced to how the Vikings built their ships with the use of crooked timber. During the last four workshops, the pupils worked as weavers, ropemakers, boat builders and blacksmiths. They worked with wool, lime bast, oak and iron, giving them an insight into Viking Age crafts, materials, and techniques.
The design process then continued back at the school, where the students were tasked with designing and building chairs inspired by the experiences they gained here at the Museum. Six of the finished chairs were then exhibited at the Museum, giving the students the opportunity to see the design process through to its logical conclusion.
The boat is launched – and the project continues…
The Gislinge Boat – or Gisle, as the boat was named – was launched on the 31st October 2015 and the event marked the end of the first phase of the project. The hectic pace of the weeks leading up to the launch was replaced by a calmer period of reflection as the process of test-sailing began. It takes time and skill to 'sail the boat in', a complex process where the interplay between each individual element of the boat and the impact they have on how the boat performs becomes apparent. Many adjustments must be made as the boat builders get to know the boat and how it performs, and this vital part of the experimental archaeological process will continue with the coming sailing season (See Figure 10).
The experimental archaeological testing of Gisle has taken a step further in 2016, as the boat builders have built yet another Gislinge Boat. During the winter, the Museum's ship reconstructor examined the post-excavation documentation of the original Gislinge Boat, and noticed several details which had previously been overlooked. The next reconstruction – Gislinge III – will therefore have a higher freeboard and a slightly wider forebody than the two previous Gislinge reconstructions. Building the boat again also offers the greatest research potential in terms of exploring the boat's sailing capabilities, as it allows for controlled and rigorous testing of the rig, sail, rudder and oars, as well as the specific techniques and materials the boat builders use during the construction of the hull itself.
The same open source approach will also be applied to the construction of Gislinge III, giving those who have downloaded the drawings and begun working on their own version of the Gislinge Boat the chance to gain an even deeper understanding of the boatbuilding process. The combination of maritime experimental archaeology and digital communication may have been a new departure for the Museum at the beginning of the project, but its success means it is a methodology that we hope to develop further over the coming years (See Figure 11).
Glossary of boatbuilding terms (after Crumlin Pedersen and Olsen 2002)
Breasthook: Transverse, horizontal timber in the bow, in line with the sheerstrake
Bulkhead: Transverse partition dividing the interior of the hull into separate spaces
Cross beam: Transverse timber forming part of the frame construction
Floor timber: Central frame element that crosses the keel in the lower part of the hull, forming the ‘ribs’ of the boat
Frame: A transverse timber or group of connecting timbers against the inner surface of the planking, providing substantial strength and stiffness to the hull
Futtock: A timber that serves to extend the floor timbers upwards against the inside of the planking
Garboard: The first strake, against each side of the keel
Keel: The central, longitudinal bottom element, forming the ‘spine’ of the boat
Knee: L-shaped timber in which the grain follows (at least approximately) the sweep of the timber, typically used to reinforce the angular joint between two other timbers, such as floor timbers and cross beams
Row lock: Curved timber attached to the sheerstrake. The curved projection is used to secure the oar when rowing
Rudder: The steering element of the boat, in this case a side rudder
Sheerstrake: The uppermost strake of the planking
Stanchion: Small upright sitting in the floor timber and providing support to the cross beam
Stem: Centreline timber at either end of the hull of a double-ended vessel (the fore and after stem), to which the hooding ends of the planking are attached
Strake: A run of planks from bow to stern
Thwart: Transverse bench used when rowing
Treenail: Wooden fastening, secured with a wooden wedge
Yard: The horizontal timber from which the sail is hung
Bibliography
BILL, J. (1994). Iron Nails in Iron Age and Medieval Shipbuilding. In Westerdahl, C. (ed) Crossroads in Ancient Shipbuilding: Proceedings of the Sixth International Symposium on Boat and Ship Archaeology, Roskilde 1991. Oxbow Books: Oxford, pp. 55-63.
BUCHWALD, V.F. (2005). Iron and steel in ancient times. Historisk-filosofiske Skrifter 29. The Danish Royal Academy of Sciences and Letters: Copenhagen.
CRUMLIN PEDERSEN, O. and OLSEN, O. (2002). The Skuldelev Ships I: Topography, Archaeology, History, Conservation and Display. The Viking Ship Museum in Roskilde: Roskilde.
FINDERUP, T. (2006). History written in tool marks. In Blue, L., Englert, A. and Hocker, F. (eds) Connected by the Sea: Proceedings of the Tenth International Symposium on Boat and Ship Archaeology, Roskilde 2003. Oxbow Books: Oxford, pp. 21-26.
GØTHCHE, M. (1995). Båden fra Gislinge. National Museets Arbejdsmark 1995. Foreningen Nationalmuseets Venner: Copenhagen.
JENSEN, P.M. (2004). Arkæobotanisk undersøgelse af formodet hørarbejdningsgrube. Højberg: Moesgård Museum.
HANSEN, K.M. and HØIER, H. (2001). Næs – en vikingestidsbebyggelse med hørproduktion. Kuml 2000, pp. 59-89.
HERTEIG, A.E. and CHRISTENSEN, A. E. (1985). The Bryggen Papers. Main Series. Vol. I. Universitetsforlaget: Oslo.
MAGNUS, O. (2006). Reconstruction of rope for the copy of Skuldelev 2: Rope in the Viking Age. In Blue, L., Englert, A. and Hocker, F. (eds) Connected by the Sea: Proceedings of the Tenth International Symposium on Boat and Ship Archaeology, Roskilde 2003. Oxbow Books: Oxford, 27-34.
NICOLAYSEN, N. (1882). Langskibet fra Gokstad ved Sandefjord. Cammermeyer: Kristiania.
NIELSEN, S. (2011). The Sea Stallion from Glendalough: Reconstructing a Viking-Age Longship. In Staubermann, K. (ed) Reconstructions: Recreating Science and Technology of the Past. National Museum of Scotland: Edinburgh, pp. 59-82