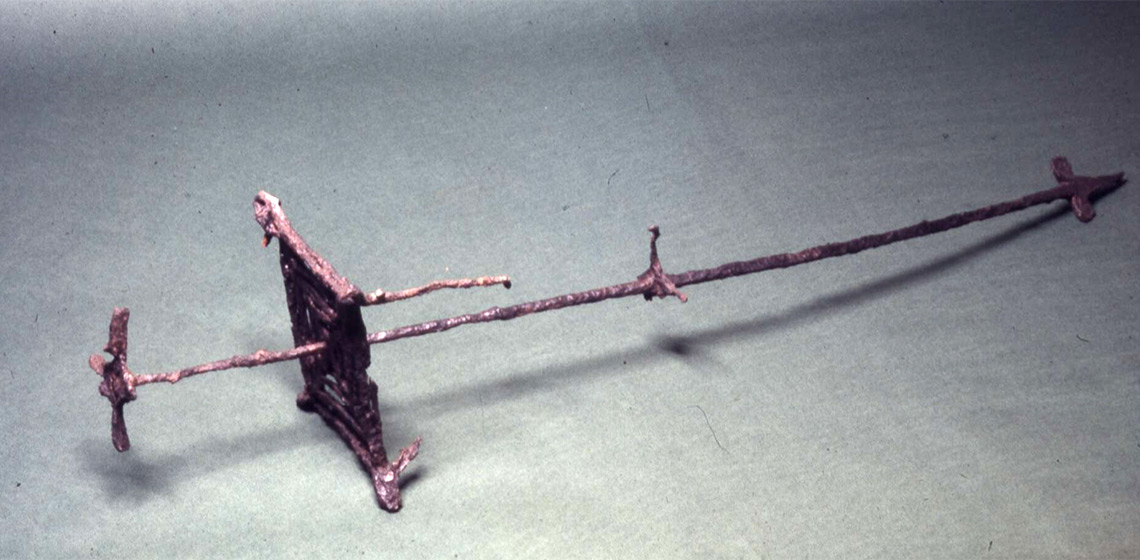
The Iron Stand from Sutton Hoo, Mound 1 was excavated in 1939. While a first tentative interpretation of its original appearance was made in 1952, this was updated in 1972 following a science-led investigation of the artefact. However, some features of the object were not included in the later representation. The examination of these additional features suggests that the basket element of the iron stand may have been welded to the shaft by the lowest ends of its retaining struts, as evidenced by the possible remains of a fireweld in that location.
The point A element, currently interpreted as the fallen base of the upper basket, may instead still be in its original position and represent the base of a second, lower basket element. This is evidenced by possible footing corrosion at points A and B, and a localised 45 degree twist in the shaft designed to retain the point A element.
Furthermore, evidence suggests that copper-alloy plating was used on the struts of the upper basket element for decorative effect. This plating was also used to retain an iron ring at the lower ends of each strut. These rings were of a sturdier construction than the welded scrolls present at the upper end of the struts and may have served a specific function.
Thus the stand may have had a markedly different appearance to that represented since 1972. The cumulative effect of this re-evaluation gives the artefact a more complex appearance than is currently understood.
The stand and its previous representations
The ‘iron stand’ was excavated in 1939, one of the many objects discovered in the Sutton Hoo, Mound 1 ship burial. To date, the stand is unique in the archaeological record but due to adverse burial conditions it is incomplete (See Figure 1). This makes its appearance and function difficult to discern. Due to this difficulty, while the first description of the object was published in 1940 (Phillips, 1940, pp. 6-27), further updated representations of its appearance were made in 1952 with the Herbert Batten reconstruction and again in 1972 with the Valerie Fenwick interpretation.
In order to locate more effectively the different components and areas of the object discussed in this work, please consult Figure 2.
The 1952 reconstruction was arrived at so that a physical interpretation of the stand’s appearance could be displayed alongside the original object, which had not been put on exhibition until then due to its fragility (Times, 1952). Two features of that reconstruction stand out: the first is that the stag element of the whetstone – a stone object excavated in proximity to the stand which features carved anthropomorphic faces and capped with copper-alloy finials - was erroneously surmised as having been mounted on the capital element of the stand. Secondly, the conclusion had been arrived at that the Point A element was likely the base of the upper basket element but still in its original location (Bruce-Mitford, 1947). As such, it showed the upper basket stretching down to it (See Figure 3).
During the 1970s, analysis removed the stag element and shortened the upper basket to meet the shaft at Point B, however the idea remained that the Point A element was the base of the upper basket. Because of this it was concluded that the Point A element was not in its original position but had fallen down the shaft and rotated through 120 degrees in so doing (Bruce-Mitford, 1978, p. 416). Thus the 1972 representation shows the Point A element firmly located at Point B (See Figure 4).
But various physical features of the stand were not incorporated into the 1972 representation, either due to their perceived ambiguity, because they were not noticed or due to misinterpretation. Based on information contained within both published and archived material, X-radiography and a working knowledge of the manufacture and degradation of forged ironwork, a new examination of those features may point towards the appearance of the stand being somewhat different from the current, 1972, representation (See Figure 5).
The struts of the upper basket element were possibly forge-welded at Point B and the Point A element may still be in its original location, acting as the base of a lower basket element
The possible presence of a forge-weld at Point B
Point B is located on the shaft of the stand immediately opposite the lower end of strut R, circa 200mm below the grille. A short swelling can be seen there, present on one face of the square shaft (See Figure 6). The swelling can be seen in X-radiography to be a solid feature rather than an oxide accretion and was described as such during the 1970s (Bruce-Mitford, 1978, p. 412) (See Figure 17). As it is wider than the body of the shaft, it is not likely to be a consequence of wastage. Its presence on the shaft was also noted by C.W Phillips soon after excavation (Phillips, 1940). While both Bruce-Mitford and Phillips hypothesised that the swelling may have been related to the retention of the upper basket element, those notions were not interpreted into their contemporary reconstructions of the object.
The current form of the swelling and the manner in which it has degraded are not propitious to it having been forged from solid bar. While a step could have been formed whilst still keeping the same shaft dimensions above and below it, more of such a step would have been expected to survive and the swelling would be expected to encompass the shaft rather than just occupying a single face (See Figure 7). Additionally, the swelling tapers upwards, meaning that the step created by its presence is located on the underside (See Figure 8). Had the swelling been designed as a retaining step, the step would be expected to be located above the taper (See Figure 9).
Instead, the swelling has the form of a type of forge-weld known as a branch-weld, whereby a ‘branch’ is added to a larger component. The forge-welding process is an additive one, whereby two elements are fused together to create a cross-section which extends to a slightly narrower extent than the combined thicknesses of the two or more elements being joined (the loss of some material thickness occurs due to oxidisation and stretching during the welding process).
Additionally, the nature of forge-welding requires the accurate shaping of the pieces to be welded. This is known as ‘scarfing’. The scarfing process involves the removal of shear-planes so that the added material will weld to the main bar rather than cutting through it (See Figure 10). In order to create a scarf, faces perpendicular to the weld are removed (See Figure 11). This is in line with the upward-facing taper of the Point B swelling (See Figure 12).
While it was argued above that more of a forged step would be expected to survive, the additive nature of forge-welding can contribute to weld failure. Forge-welding is a diffusion welding process conducted at temperatures below the melting point of the metals being welded (Simmons, 2009, p. 233). A forge-welded joint will have weaker corrosion resistance than a solid bar. This is due to silicone and iron oxides lining the internal join, partially impeding the welding process. Corrosion will travel along these seams, weakening the weld (Buchwald, 2005).
Where a branch-weld is present, the expansion of corrosion at the crutch of the weld can simply shear the weld through pressure. This is due to iron oxide occupying 7 to 8 times the volume of the original iron (Harris, 1984, pp. 3791-3811). As such, the branch will subsequently shear at a point where the weld falls below a certain level of strength (See Figure 13). Due to this, it is more likely that a forge-weld would degrade in a manner resulting in a feature similar to the Point B swelling.
Furthermore, the scarfing process may leave a raised area at the toe of the weld. This is frequently the case where a scarf has not been sufficiently tapered or where the smith did not blend the weld (a weld will not be blended if doing so risks thinning the material being welded) (See Figure 14). Where a toe is present, it can become emphasized over time (See Figure 15). Such a raised toe appears to be present on the stand at point B (See Figure 16). This phenomenon is also visible on the base of the stand where the volutes have been welded to the spike (See Figure 57.b).
Further evidence suggestive of the swelling representing the remains of a forge-weld is to be seen: The presence of a splinter of iron extant on the side of the swelling is visible in X-radiography of the swelling. The splinter possibly represents the remains of the forge-weld adjacent to the main swelling but which has sheared closer to the toe of the weld (See Figure 17). This suggests that one weld was made to each face of the square shaft in that location (as shown in Figure 12.b).
In order to demonstrate all of the above propositions, an experiment was conducted. Four branches were scarfed and welded into position. With the notion being that the branch-welds were, in fact, the struts of the upper basket element, these were heated and formed perpendicular to the shaft once the welds were completed. This opened up the welds slightly where the fusion was at its weakest at the branch-main bar transition. This was incidental to the forming process and creates an area for corrosion to begin attacking the weld (See Figure 18).
The branches were then sheared by forcing them upwards so as to simulate corrosive expansion pressures between the weld and shaft of the stand. The welds sheared in different locations, based on the fusion of each weld, with the toes of all welds remaining. Where the welds sheared closest to the toe, slag inclusions and an oxidised surface were visible, indicating that corrosion could have eventually removed those welds almost completely (See Figure 19).
Where welds sheared lower than the adjacent weld, the predicted splinter of iron was present (See Figure 17.c). As a final test, the weld area was oxidised for comparison with the existing archaeology, producing a result similar to the Point B swelling (See Figure 20).
As such, it is the preferred explanation that the swelling represents a fire-weld at Point B. Given the presence of the remaining splinter of iron in contact with the side of the swelling, it is likely that further welds were made in that location and it is hypothesised that four welds could have been present. Given the location of Point B immediately adjacent to the lower end of strut R, the preferred explanation is that the struts of the upper basket element would have been welded in that location.
The presence of footing corrosion at Point A and immediately below Point B indicates the likely past presence of pass-through fittings in those locations
Both below the swelling at Point B (See Figures 6, 21) and just below the plate at Point A (See Figure 22), a belt of undercut corrosion is visible in X-radiography. This may represent a type of corrosion known as footing corrosion which is associated with horizontal pass-through fixings mounted on a vertical bar. A pass-through fitting in this context is where an iron bar is fitted through a hole in another iron bar (See Figure 23).
Footing corrosion is a form of galvanic corrosion caused by the creation of an anodic differential within a vertical length of iron. Where a section of the iron bar is encapsulated in either stone or further ironwork, the encapsulated section becomes isolated from electrolytes and thus becomes passivated. This passivation renders the section of iron immediately outside of the area of passivation anodic and thus more sensitive to electrolytes (See Figure 23).
In layman’s terms, if one area of an iron bar is isolated while one area is left open to the elements, a length of iron can become a battery. The flow of electrons between the isolated area and the exposed area will make the exposed area in contact with the isolated area corrode faster than if the whole bar had been left exposed.
The accumulation of dirt, moisture and organic materials around the vertical element (in this instance, the shaft of the stand) will contribute towards an accelerated degradation in that area, resulting in an undercut corrosion belt (English Heritage, 2012, pp.158,166). It is a readily observable form of degradation in historic exterior ironwork (See Figure 24).
As such, the footing corrosion present on the stand may be as a result of an extended period of static exterior use during the working life of the object combined with a low-maintenance regimen or may be due to an extended period of time spent in an upright position post-inhumation but prior to the collapse of the burial chamber (or a combination of both).
Due to its nature as a localised form of corrosion, footing corrosion will not occur where an object is buried in contact with the ground. This is due to a more randomised distribution of anodic elements (stones, particles, pools of moisture, etc.). Those conditions will instead form pitting (Liu, Dai and Chenga, 2020, pp. 3601-3614). Due to this, it is a requirement for footing corrosion to have formed before the iron stand was forced into a horizontal position.
Given these requirements for the presence of footing corrosion at Point B and Point A, it is likely that a tight-fitting horizontal pass-through element was present in both of those locations. This is because, while the current thinking is that the Point A element has been knocked down the shaft to its present position at Point A after previously being located at Point B and connected to the struts of the upper basket element (Bruce-Mitford, 1978, p. 416), had the Point A element had been knocked down the shaft by the collapse of the burial chamber then footing corrosion could not have occurred at Point A due to the stand being covered in spoil and the stand having fallen to a horizontal position. Because of this, it is more likely the case that two pass-through fixings were present on the shaft prior to the collapse of the burial chamber.
The shaft of the stand is deliberately twisted through 45 degrees at Point A, possibly in order to create a step for the Point A element to rest on
The various parts of the stand are mounted to the shaft in an alternating pattern, whereby each is placed at 45 degrees to the element above and/or below it. Thus, the grille is at 45 degrees to the capital element, the Point A element at 45 degrees to the grille and the volutes at 45 degrees to the Point A element. Given the consistency of the angles and the repeating nature of the pattern it is possible that this may be a decorative feature of the object (See Figure 26).
The difficulty in the manner by which this has been achieved is that for the volutes to match the pattern in its current form, a twist needs to have occurred in the shaft. This is because the volutes are welded to two opposing faces of the shaft and without a twist the volutes would be in line with the Point A element (C in Figure 26.a) instead of the grille (B in Figure 26.a). The same effect could more easily have been created by simply changing the order in which the fixing holes of the loose elements above the volutes alternate (See Figure 26.b).
An examination of the shaft shows that this twist possibly occurs at Point A. The actual area of twist itself is not visible, though its presence is observable in photography, which shows a 45-degree offset between the faces of the shaft above Point A from those below (See Figure 25).
The effect of this is that a step is formed on the shaft by the area of twist, as the corners of the shaft below Point A are brought to a position roughly central to the faces of the shaft above Point A. It is argued here that the twist was used to create a step at Point A for the Point A element to rest on, which it currently does. The reasons that the twist itself is not visible may be because it is located within the fixing hole of the Point A element or may be because the twist was forged out into a crisper step.
The angle of the volutes was noted during the 1970s but was explained as distortion to the object caused by the collapse of the burial chamber (Bruce-Mitford, 1978, p. 408). But while there is definite accidental bending to the shaft, there is no evidence of accidental twisting. Such accidental twisting would occur over the length of the shaft rather than being localised very precisely beneath or within the Point A element (See Figure 27). As such, it is possible that this is a deliberate design feature used to retain the Point A element in that location (See Figure 28).
Corrosion processes and their role in securing the Point A element to the shaft of the stand
The current notion is that the Point A element has fallen down the shaft of the stand and rotated through 120 degrees (Bruce-Mitford, 1978, p. 416). While it could be argued that the corrosive processes and subsequent degradation of the stand may have contributed to the slipping and rotation of the Point A element by loosening the fit of the Point A element, the nature of iron degradation, in fact, makes this less likely.
Traces of surface corrosion would have been visible on the object within the first weeks of burial if the object held no protective surface coating. While corrosion will weaken ironwork and return it to its preferred state of iron-oxide with catastrophic consequences (the missing struts for example), the oxidisation process would also seize the Point A element in its original position. This is due to ferrous corrosion being expansive, occupying around 7 to 8 times the original volume of iron (Harris, 1984).
Where ironwork is unsupported this can result in distortion (See Figure 13) but where the corrosion is enclosed the oxide product will fill any void and wedge the two parts together. Had the Point A element been located at Point B prior to inhumation, it is likely that it would still be present in that location due to a likely tight original fit becoming even tighter due to corrosion.
An illustrative example of the phenomenon can be found from the Sutton Hoo, Mound 1 excavation in metallographic cross-sections taken from the socket of spearhead number 4. In that instance, expansive corrosion contained within the socket has formed a solid mass dense enough to have retained the cut marks from the sampling implement (Bruce-Mitford, 1978, p. 251). Had the corrosion been loose, it would have fallen away from the friction of the cutting tool.
Because of this, it is likely that the pass-through join of the Point A element would have been solidly wedged before the struts had either corroded through or become disconnected from the Point A element, particularly given the thickness of the struts vs the presumed close fit of the Point A element on the shaft. Thus it is unlikely that the Point A element would have had the opportunity to fall and rotate around the shaft prior to the collapse of the burial chamber. After the collapse, the stand lay horizontally, making the movement of the element more unlikely.
The argument for a lower basket element
It is therefore argued that the Point A element is still in its original location. This is based on the presence of footing corrosion above the Point A element, the presence of a deliberate step in the shaft upon which the Point A element rests and the expansive nature of corrosion which will have made the drop and rotation of the element unlikely.
Additionally, if the Point B swelling represents a forge-weld whereby the struts of the upper basket element were attached to the shaft in that location, then the Point A element becomes redundant as a base for the upper basket element at Point B. However, possible footing corrosion below the Point B swelling indicates that a horizontal pass-through element may have been extant in that location.
One explanation may be that the Point A element was, in fact, forge-welded to the shaft at Point B and that the upper basket element was fixed to a plate below the forge-weld (See Figure 29).
However, strut R appears to show compensation to bring it in line with the faces of the shaft (See Figure 30). Such compensation would not be necessary if the lower ends of the struts were affixed to a plate as they could sit at a 45-degree angle to the shaft in the same manner as the grille.
While it could be argued that the angular compensation visible in strut R could be due to distortion from the collapse of the burial chamber and/or subsequent ground movement, in this instance the simplest explanation is preferred: given the difficulties involved in fitting the upper basket element to the shaft with the lower basket element welded into place it seems more probable that the upper basket was forge-welded to the shaft and the lower basket slid upwards into position before the twist-step locked it into place with its upper plate resting against the bottom of the struts of the upper basket element.
It could also be argued that the Point B footing corrosion may be associated with a separate structure unrelated to either the upper basket element or the Point A element. But given the gap of circa 200 to 250mm between points A and B, it seems unlikely that two elements would be placed in this area given the similar, even spacing seen between the other elements of the stand (See Figure 2). An examination of the Point A element shows construction details which may offer an explanation.
The main body of the Point A element is formed from a sub-rectangular plate of iron on which two opposing corners have been drawn into struts. The remaining two corners are scarfed and have received their struts via forge-welding instead of them being drawn out (Bruce-Mitford, 1978, pp. 413-415) (See Figure 31).
Had the Point A element been designed so that the struts simply ended in hooks or similar, it is more probable that either all four of the struts would have been forge-welded, or all four of the struts would have been drawn from a single piece. This is because it is easier to make an item using the fewest number of different operations. Additionally, it is likely that the smiths who made the stand would have been producing iron bar-stock of dimensions appropriate to the task in hand by forging-down either blooms or larger merchant-bar, leading to an economy of gestures where possible.
This means that it would have been more efficient to either split the struts and form the Point A element OR form a square plate, draw a long strut section and cut it into four pieces which were then scarfed to the square plate than it would have been to draw out two struts before forging a separate length of strut and cutting it into two lengths which were then scarfed to the Point A element.
Because of the construction of the Point A element, the presence of footing corrosion at Point B and the distance between points A and B, it may be the case that a structure was present in that location, of which the Point A element represents fragmentary remains. The construction of the Point A element indicates that, if this were to be the case, then it is likely that the missing Point B pass-through element would have been a horizontal fitting identical to the lower plate but set perpendicular to it. In this manner, the two forge-welded struts on the lower plate would be the drawn-struts of the upper plate, while the drawn struts of the lower plate were forge-welded to the scarfed corners of the upper plate (See Figure 32).
It is to be noted that the weld shown in Figure 31.a is becoming detached. This is likely due to corrosion separating the welded faces. This effect is emphasised when a weld is of lower quality, performed at sub-optimal temperatures, which results in a cold-shut along which the corrosion can travel. Given the presence of good welds throughout the rest of the object (notably the grille) it is possible that the presence of a poor weld on the Point A element is the result of the weld being an awkward one.
The Point A element shows the remains of twist ornamentation on surviving strut sections. Given the use of a reverse-twist technique on the struts of the upper basket element and on the edges of the grille, the method has been assumed in the recreation of the lower basket element. However, this is a speculative notion and the lower basket twists may have simply followed the length of the struts (See Figure 33).
The struts of the upper basket element may have been plated with copper-alloy
Evidence for copper-alloy plating on strut R and rejection of the cross-contamination theory
When the stand was excavated, strut R of the upper basket element was covered in copper-alloy oxide to such an extent that the strut was thought to be an extraneous copper-alloy object attached to the grille by corrosion. Upon realisation that strut R was part of the stand, conservation efforts were made under the assumption that the copper-alloy oxide was a contaminant and mostly removed (Bruce-Mitford, 1978). However, the copper-alloy corrosion may possibly represent the use of braze-plating as a decorative surface treatment of the upper basket struts.
Some copper-alloy oxide still survives in places along strut R, visible from the lowest tip of the strut to just above the top scroll in the form of green Cu2O and yellow CuO (See Figure 34). Radiography of the lower-end of strut R reveals clearly defined areas of denser material still present which may represent surviving copper-alloy plating. In support of this, possible casting porosity, an indicator of brazing techniques (Turner-Walker, 2008, p. 57), can be observed at Point C (See Figure 35).
While cross-contamination of copper alloy corrosion through prolonged contact can occur, this is an unlikely explanation in the case of strut R. The layout of the mound 1 burial within the vicinity of the iron-stand shows no copper-alloy objects in proximity to the location of strut R, with the exception of the stag element from the stone sceptre/whetstone (See Figure 36).
However, if the copper-alloy oxide had come from contact with the stag element, the corrosion product should be localised to an area only slightly wider than the actual zone of contact between the two objects. Given the extent of the corrosion precisely along the length of the strut but not on the shaft or grille, this seems unlikely. It would also be assumed that the stag element would be in a more degraded condition had it provided such a volume of corrosion material.
Aside from the stag element, the nearest copper-alloy find was the large hanging bowl found in contact with the group of spearheads. However, this was not in the vicinity of the iron stand and its placement does not suggest that it was in contact with the object before or after the collapse of the burial chamber. The spearheads also show no sign of copper-alloy cross-contamination.
Had the presence of the copper-alloy corrosion come as a consequence of cross-contamination, the corrosion product would likely have been only loosely attached to the surface of the strut, taking the form of inclusions into the corrosion product of the strut itself. Instead, the copper-alloy corrosion product could not be easily removed and still shows green and yellow oxides post-conservation, more indicative of a bonded origin.
No evidence has been seen which would indicate that the Point A element was also plated in copper-alloy.
Discussion on parallels and historical precedents for copper-alloy plating of iron objects
The use of copper-alloy braze plating techniques on iron objects of the early medieval period is well represented in the archaeological record and has long been associated with objects such as bells, weights and padlocks (See Figure 37). However, its recognition on further early medieval archaeological ironwork as either weatherproofing or an ornamental technique is only recent.
As such, objects such as maille, stirrups, horse bits, etc. are emerging as having copper-alloy plating as a surface covering. In some instances, only partial plating was used in order to provide a visual contrast on the object (Corfield, 1993, pp. 276-282). While tinning techniques only date back to post-Roman contexts (Ottaway, 2016, p. 3), the plating of iron objects with copper-alloy can be traced back to the iron age.
A parallel to decorative copper-alloy plating on an object of intangible function can be found on the Fuldby staff from Denmark. This volva staff shows the remains of a copper-alloy plated coating on its basket element in a manner similar to that likely to have been visible on the struts of the upper basket element of the iron stand (See Figure 38). Several volva staffs have various ornamental copper-alloy fittings and it is possible that the use of plating techniques was a cheaper alternative to these. The presence of copper-alloy plating on the Fuldby staff and on the iron stand may not be coincidental and may have specific circumstances around the use of the technique, such as to increase the visual impact of an object used at a gathering or in a display area.
Such usage can be glimpsed in ‘Beowulf’, transcribed from 975 to 1025 but possibly originating in the eighth century (Chase, 1997, pp. 9-22), where the eponymous hero is presented with a gilded banner as a reward for the slaying of Grendel: ‘The flaming brand of Healfdene bestowed then upon Beowulf, as victory’s reward, a golden standard’ (Hall, 1914, l. 1020-1025). And when Wiglaf finds himself in the dragon’s lair and confronted with the creature’s hoard, placed upon it is another golden standard: ‘Hanging high above the hoard a standard (here: segen or signum) all of gold, greatest of marvels wrought by hand, woven by human skill’ (Hall, 1914, l. 2767-2771).
It is likely that the Beowulf epic uses hyperbolae as a means of placing the beauty of the dragon’s hoard above the treasures of the kings, warriors and warlords of the period. However, the embellishment concerns objects which would have been used in the contexts of socio-political and/or religious gatherings.
While gold gilding was well known to the Anglo-Saxons through the use of mercury gilding (Skinner and Ozgenc, 2004, p. 4), the technique does not appear to have been used on the Iron Stand. As gold does not oxidise it is likely that fragmentary traces would have remained present in the corrosion matrix.1
An interesting parallel to strut R comes from the excavation of the Voulokaliva tombs in Greece which revealed a series of iron phiales (libation bowls) dating from the 7th or 8th century B.C. Post-excavation, it was realised that the phiales were covered in copper-alloy oxide mixed in with the ferrous oxide from the phiales’ iron core. This was at first thought to be cross-contamination; however, it was soon realised that the copper-alloy corrosion covered the entirety of the objects and was, in fact, due to copper-alloy plating (Asderaki-Tzoumerkioti, Rehren and Malakasioti, 2009) (See Figure 39).
While much of that plating was fragmentary at the time of excavation due to corrosion, examination revealed some surviving areas of plating trapped beneath layers of mixed Fe and Copper-alloy corrosion. Metallographic analysis on the phiales shows a copper-alloy plating sub 100 microns thick, in line with the thicknesses measured on Roman subferratta coins which were copper-alloy plated iron (Strobl, Haubner and Pintz, 2012).
Discussion on processes leading to the loss of copper-alloy plating on strut R
Corrosion will be the main cause for the loss of plating on strut R. The conditions within the Sutton Hoo burial were favourable to copper-alloy oxidisation and due to the nature of strut R – copper-alloy plating over an iron base – the strut itself would have fared less well than the other iron or copper-alloy artefacts from the burial, due to bi-metallic corrosion. This is a possible explanation for the disappearance of the other three struts of the upper basket element, compared with the survival of the thin iron hoops of the yew bucket from the same burial.
Tests on soil and corrosion products (ferrous only) demonstrate that oxygen, chlorides, sodium and sulphates were present in the soil at Sutton Hoo and that the sandy subsoil had a pH of 4.5 (Barker, 1950, p. 348). While the chlorides were present in low quantities, the corrosion process, once begun, captures and concentrates them (Thickett, 2012, pp. 124-125). The degradation of all of the copper-alloy finds would require a Relative Humidity below 35%, oxygen and chlorides. Without the presence of all three of these factors, the decay of bronze, or bronze disease would not occur (Bishop and Pauley, 2018), replaced instead with the presence of a patina – a form of copper-alloy oxidisation which instead protects object by isolating its surface from the ambient atmosphere (Scotland, 2012).
The corrosion of copper-alloy begins with a red layer of cuprite forming on the surface of the copper-alloy. This cuprite is sensitive to attack from acidic ions such as chlorides, sulphides and carbonates, penetrating the grain boundaries of the metal and producing the more familiar green corrosion product. The corrosion expands to a greater volume than the previous metal and extrudes through the surface oxidisation. This is extremely destructive to the copper-alloy and results first in pitting, followed by eventual disintegration as the copper-alloy is consumed. The phenomenon is visible in micrography of the Sutton Hoo, Mound 1 bronze bowl (Craddock, 2009, pp. 349-350) and the assumption can be made that the same phenomenon was occurring on the copper-alloy plating of the upper basket struts.
The strut R plating will have faced additional corrosive forces due to the copper-alloy plating sitting on the ferrous body of strut R. The degradation of the copper-alloy plating would have resulted in severe pitting of the iron due to the gradual exposure of patches of iron. These exposed patches of iron suffer accelerated localised corrosion as they are rendered anodic due to partial exposure to the oxygen, moisture, chlorides, etc of the soil around them while the connected iron, still under the coating, becomes cathodic (ASM, 1987, pp. 242-247). The exposure of the iron to the environment would also have brought the advent of galvanic corrosion between the copper-alloy plating and the ferrous matrix of the strut as the pitting deepened and exposed a larger surface area to the elements.
Galvanic corrosion, or bimetallic corrosion, is an electrochemical reaction whereby two metals in contact via an electrolyte form a ‘battery’. The very small current generated precipitates the degradation of the lesser noble of the two metals (ASM, 1987, pp. 183-193). As iron corrodes in preference to copper-alloy, this would have led to the preferential corrosive degradation of the iron structure of strut R.
The pitting and undercutting of the structure of strut R would eventually lead to the shedding of the copper-alloy plating from the loosening surface of the iron through the expansion of ferrous oxide beneath the plating. This is due to iron oxides occupying around 7 times the volume of the original metal. Thus the expansive forces associated with this oxidisation are considerable and would have contributed to the loss of the copper-alloy plating (Harris, 1984, pp. 3791-3811).
While the Voulokaliva phiales benefitted from more propitious interment conditions (drier and less acidic), they have none the less severely degraded. This is possibly due to the interaction between the copper-alloy and iron. In some instances, almost total loss of both Fe and Copper-alloy can be observed, with both metals replaced by corrosion products (Asderaki-Tzoumerkioti, Rehren and Malakasioti, 2009).
In the case of the Phiales, the iron was around 2.5mm thick (Asderaki-Tzoumerkioti, Rehren and Malakasioti, 2009), limiting the potential volume of corrosion product. With the thickness of the struts of the upper basket element of the iron stand, there was additional iron available to the corrosion process in order for it to continue shedding the copper-alloy plating. This means that the plating, if it were of a similar thickness to that measured on the phiales, had little chance of surviving the burial conditions at Sutton Hoo.
Measurements taken on Roman Sub-ferrata coins (Strobl, Haubner and Pintz, 2012) indicate a plating thickness of less than 75 microns and on the Greek Voulokaliva plated iron phiales of less than 100 microns. Visual comparison with plated bells, padlocks and weights of the early medieval period would tend to match this plating thickness. If it is assumed that the copper-alloy plating on strut R was of a similar thickness, then the plating had very little volume to lose before the copper-alloy was mostly transformed into corrosion product and ejected from strut R by the ferrous corrosion from below.
Historical plating processes
In order to create copper-alloy plating on iron, two techniques are to be found within the historical record. The first is to use a flux based on tartaric acid to braze copper-alloy directly onto the surface of the iron. The second is to wrap the object to be plated in clay with some quantities of copper-alloy before firing the package in a hearth or furnace once the clay shell has dried.
The evidence for the fluxing technique is literary and comes from Theophilus in his ‘On divers arts’. To produce the flux, argol (also known as cream of tartar, winestone or tartaric acid) is melted and ground down. A small quantity of salt and water is added. The black paste thus produced is smeared on the iron and allowed to dry. The copper-alloy is then placed on the dried paste and more paste is coated over the top and allowed to dry (Hawthorn, 1963, pp. 186-187). The whole can then be brazed on an open hearth or in a furnace.
The above recipe and techniques are also found in the Mappae Clavicula, written in the 12th century and partially based on some 7th-century texts (foregoing the addition of salt). It is to be noted that the original text used in the Mappae Clavicula uses Arabic words for certain materials, which may indicate an Eastern source as opposed to a Romano-Greek one (Carroll, 1981, p. 99).
A number of casual experiments were conducted following that recipe. The final result of this produced a copper-alloy coating (brass in this case) of less than 0.10mm thick. The flux itself removes fire scale (the layer of black oxides which forms on the surface of ferrous metals) from the iron which is to be plated, favouring the adhesion of the copper-alloy and allows the copper allow to flow thinly over the surface of the iron (See Figure 40). The technique favours the use of small quantities of powdered copper-alloy sprinkled regularly over the surface to be brazed. Larger quantities of copper-alloy such as strips do not spread well and tend to form large globules or run off the iron entirely (See Figure 41). The omission of salt from the recipe makes it harder to form a paste as the salt retains the water into the recipe.
The flux will only allow a small amount of copper-alloy to pass through it before it is rendered ineffective. Additionally, the technique prefers a flat and horizontal surface as both the flux and the copper-alloy tend to simply roll off the iron if it is rotated or held at an angle, which in itself would put it at a disadvantage when plating around a cylindrical object.
While Theophilus provides a workable recipe for a brazing flux, a greater body of evidence of use is available for package brazing. The technique involves wrapping copper-alloy wire, strips or fragments around or on an iron object before encasing it in clay. Once the object to be plated is wrapped in clay, it is left to air dry before the whole package is baked in a furnace long enough and at a high enough temperature for the copper-alloy to thoroughly melt (Gustafsson, 2005, p. 21).
The object would then have been withdrawn from the fire and rotated prior to and during the cooling process for long enough to obtain an even and regular coating around the object being thus plated.
The fired and discarded ceramic packages resulting from this process have been found across Europe at sites including Ireland (Clonfad), the U.K (York), Denmark (Hedeby) and Sweden (Birka, Helgo, etc), demonstrating a widespread use of the practice throughout Northern Europe (See Figure 42).
While the analysis of one site (Helgo) showed that the clays in this process were unrefined, untempered and of a silty nature (Soderberg, 2008, pp. 159-169), the practice probably varied across Europe dependent on available materials and local customs. The use of the clay packaging removes the need for a flux as it creates an anaerobic environment where no oxides can form. This works in the same manner as a flux but with the disadvantage that no acidic process is present, which will remove fire scale from the iron.
However, it does prevent the burning-off of any zinc, tin or lead contained in the copper-alloy as these are retained within the package. This means that the brazing process can be conducted at a higher temperature than normal, ensuring better bonding and a better spread of the plating. The ceramic packaging also acts as a mould which, as it is formed to the ironwork, ensures a thin and even coating of the copper-alloy plating and minimising globulation.
Sweden offers a wealth of ceramic packages disposed of after plating objects such as padlocks and weights. Excavations at the Garrison, Birka, Sweden, revealed a padlock factory. In all, around 5,600 ceramic fragments were discovered, some of which could be refitted together to form almost the entire casing. The ceramic was a result of the brazing and plating of the padlocks, with imprints showing decorative details such as twists still visible in the ceramic. The ceramic remains themselves had been heated almost to the point of vitrification and are a sign of the skill and familiarity with the clay brazing technique at the time (Gustafsson, 2005, p. 21).
It is to be noted that modern traditional cow-bell makers in Germany, Spain and Portugal still use this clay-wrap forge-brazing technique with only slightly different tools than would have been used in the Anglo-Saxon period. These plating techniques are performed without flux thanks to the clay wrapping which protects the copper-alloy in its liquid state from oxidisation.
Because the majority of the ceramic packages come from specialised workshops, they tend to demonstrate homogeneity in their contents, with the majority of objects plated being bells, padlocks and weights. Because the copper-alloy plating technique is one which requires practice, it is possible that such a specialist workshop was sub-contracted to create the copper-alloy plating on the struts.
The stand would likely have been completed and assembled by the time the copper-alloy plating took place. The reason for this is that the forge-welds involved with fitting the struts to the iron stand at Point B and to the grille would have damaged the plating, with forge-welding taking place at temperatures of around 1,400 °C for iron (Andrews, 1994, pp. 93-96) and the melting point of bronze, depending on the alloy, being 950 °C. Brass, depending on alloy, will melt at 900 to 940 °C. Because of this, forge-welding post-plating would have incurred the risk of the plating simply balling up and falling away, as well as preventing the welds from forming. Thus after completion of the forge-works, the struts would have been wrapped in copper-alloy and clay all at the same time and allowed to dry.
While the brazing process could have been carried out on an open hearth, this could only have been done one strut at a time due to the breadth of the upper basket element. However, brazing to an adequate degree is a lengthy process and firing the package at too low a temperature or for too short a period of time will only partially melt the copper-alloy and not achieve the desired coating. As such, it seems more likely that the entire upper basket element would have been baked in a furnace in order to achieve higher temperatures and a longer soak time.
Conclusion
The presence of copper-alloy corrosion on strut R is still observable on the artefact in its current condition, even post-conservation. While it has been interpreted as cross-contamination from copper-alloy objects excavated in proximity to the iron stand, this is an unlikely source given the extent of the corrosion and dearth of copper-alloy objects in contact with the strut. Instead, the struts of the upper basket element were possibly ornamentally plated with copper-alloy (See Figure 43). Radiography of the lower end of strut R appears to show some of this plating still present on the artefact. The skills and techniques necessary to produce this plating were present in the culture which created the stand, as demonstrated by the existence of numerous workshops producing plated bells, weights, etc and it is possible that the iron stand was plated using those same techniques.
Discussion on the presence of a possible brazed ring at Point C and the top scroll of strut R
At Point C of strut R, a small, anomalous projection is present, observable on the outside elbow of the strut in both X-Radiography and regular photography. The projection is fragmentary and may represent the remains of an iron ring brazed onto the strut (See Figure 44).
Post-excavation, it was thought that the projection might be a part of the copper-alloy stag element which had become incorporated into the corrosion product of strut R. This early conclusion was as a result of the layer of copper-alloy oxide which covered both strut R and the projection itself (some of this is still visible in Figure 44.b). However, it was realised during conservation that the projection was made of iron and a deliberate feature of the lower strut.
While Point C of strut R is represented as feature-less in both the 1952 and 1972 representations (See Figures 3, 45), the projection had, in fact, been re-examined during the 1970s and theorised to be a scroll designed to emulate the example featured at the top of strut R (Bruce-Mitford, 1978, p. 415) (See Figure 46).
The top scroll in question is an open scroll of thin material and most likely created by either setting down the end of the strut and folding it back on itself prior to welding (See Figure 47) or by faggot-welding an additional piece of material into position (See Figure 48). However, the Point C projection does not have the expected form for it to represent the remains of a scroll.
Firstly, radiography of Point C shows no join lines characteristic of forge-welding and the projection appears instead to have been brazed into position. Denser copper-alloy can be observed on x-radiography of the strut along with bubbles within the braze itself (See Figure 35). These bubbles, though not always present in a good brazed join, are a characteristic identifier of a brazed join or coating (Turner-Walker, 2008, p. 57). The projection was most likely brazed into position during the plating process.
Secondly, the Point C projection takes the form of a rough crescent attached at its centre to the strut and both tips of the crescent projecting outwards. This indicates that the shape of the Point C projection would more likely have been a loop or ring rather than a scroll. Had it been a scroll, then only one tip would project away from the strut (See Figure 49). The form of the crescent allows the size of a ring to be estimated at circa 15mm external diameter and 6mm internal diameter (See Figure 50). Given the small size, it is likely that the ring was punched and forged rather than formed and welded, though the latter would also be possible.
Forging a second scroll at Point C would have been a simple affair, but this was not done. The lack of similarities in form and construction methods between the Point C ring and the top scroll implies that the Point C ring may have had an intended purpose. Where the top scroll is open and made of thin material, the Point C ring is closed, which confers upon it greater structural rigidity and is suggestive of being designed to retain weight.
The top scroll itself is placed beneath the bull head of the grille of the upper basket element. This is similar in design style to the Capel Garmon firedogs, dating to the early iron age. Because of its association with a bull head it offers a design parallel to the bull-head/strut composition of the iron stand and implies that its presence may be stylistic (See Figure 51). Another example of a scroll associated with a bull head comes from Clogher, Ireland. This example has the scroll placed to the front of the bull head rather than to the rear and the scroll is of tighter construction.
While a forge-weld would have represented a stronger join, it would not have allowed the fitting of a closed ring at Point C with the same ease as brazing. It is therefore likely that the requirement for a ring in that location was in response to a particular need. A prosaic explanation may be that rings were required for the use of guy-ropes, used to ensure the balance of the stand via tethered cordage of plain bast, nettle, or hemp. However, it is equally possible that the rings were used for the suspension of ornamentation in the style of a Roman signum, as speculated by both Phillips and Bruce-Mitford (Bruce-Mitford, 1972, p. 21). Given the difference in construction from the top scrolls and its more solid construction, it is unlikely that the Point C loop was purely ornamental (See Figure 52).
Analysis and discussion on the base of the stand
The base of the stand consists of two forge-welded volutes placed on opposing faces of the shaft. Below these, the shaft tapers into a chisel point, currently 115mm long,2 the tip of which is in a degraded condition (See Figure 53). The spike currently represents 6.5% of the length of the iron stand but based on the angles of the taper may have been longer originally. It would likely have been planted into the ground with the help of the volutes, which were likely thicker than represented in the 1972 drawing.
The form of the volutes
While the 1972 depiction represents the volutes at the base of the stand as thin and open (See Figure 54), X-radiography of the area shows that they are instead thick, closed scrolls (See Figure 55). Based on the same images, it is visible that the spike was mostly formed before the volutes were welded to it, with final shaping occurring post-weld. The X-radiography shows some further interesting constructional details.
The volutes were added individually to the base. Each volute was partially scrolled at one end and scarfed at the other (See Figure 56). The volute on the right of the x-ray was possibly welded first, demonstrated by the longer weld line and thinner section of material (See Figure 57). This stretching occurred during the forge-welding of the second volute and demonstrates that both welds were separate operations rather than being done at the same time. Once the welding was completed, the volutes would have been scrolled to their final form. This is evidenced by the short open section at the upper end of each scroll which is a by-product of rolling a welded scroll and offers us an accurate measurement of how far the volutes were scrolled prior to welding (See Figure 58). The reason for not fully forming the volutes to their final size is to allow clearance to weld the base of the volutes to the shaft of the stand. The methodology used to attach the volutes is interesting due to it not being the easiest route.
An easier method would have been to start each volute on opposing ends of a single flat iron bar. The bar would then have been folded at the halfway Point Between the volutes into a V shape, fitted to the spike and welded (See Figure 59). This technique of attaching the volutes was outlined by Bruce-Mitford in his notes (Bruce-Mitford, 1975) and would have saved time during pre-positioning of the elements, made it easier to hold the volutes in place prior to welding, would only have required half of the welding passes and would have prevented inaccurate positioning. This method was used to create the top spike on the Prittlewell stand (See Figure 60).
The reasons for welding the volutes onto the spike separately are unclear but may be the preferred technique in order to avoid overheating both volutes while waiting for the spike to reach a welding heat. Indeed, when three pieces of metal are positioned together and heated simultaneously for forge-welding, the outer pieces will reach welding temperatures much faster than the middle piece unless all items are heated slowly, whereas two separate pieces will reach a welding heat at roughly similar times. It may also be the case that the spike was much longer than is currently understood and therefore it was not practical to use a long length of flat bar with a volute on each end.
A consequence of welding the volutes separately is that no opportunity was found to blend the weld of the right volute to be a closer match to the left volute. This is demonstrated by the right volute weld sitting prouder than the left (See Figure 57). However, dressing the right volute weld would have incurred further thinning of the left volute weld, which was already thinned and drawn by the welding of the right volute. This is due to the fact that while forging one side of a bar, the opposite side which rests on the anvil is being drawn out.
Additionally, the volute on the right-hand side of the X-ray appears to be lower than the one on the left (See Figure 61.a). Corrosion has contributed to the thinning of the outer faces of the scrollwork, but even with the corrosion being compensated for it can be seen that the right-hand scroll has been welded slightly lower than the left and that the volute itself was made slightly smaller in diameter by approximately 5mm. This would translate to around 15mm less length of scrolling material for the right-hand scroll (See Figure 61.b).
This discrepancy does not mean that the volutes were made with one shorter than the other. At the starting point, both volutes would have been exactly the same length. However, during the welding process it is likely that the right-hand volute was welded across a longer length than the left volute, effectively taking volute material and turning it into welded material. This is backed up by radiography of the area, where it can be seen that the weld begins lower on the right volute (See Figure 57).
Description of the spike
In 1972 it was estimated that the spike was longer by around 25 mm (Bruce-Mitford, 1978, p. 411). While a shortening of the spike is probable, it may be by more than the original estimate. This is implied by the slag layers within the spike, visible in X radiographs. While those fibres are generally difficult to discern across the shaft of the stand, corrosive processes have revealed them on the spike. This partly takes the form of roking – or the opening of the grain due to corrosive expansion, particularly beneath the right volute (See Figure 62).
These run roughly parallel to the sides of the taper, indicating that the taper can be roughly extended. Should the grain be truncated by the sides of the taper, this would be indicative that the taper is, in fact, due to corrosion rather than forging techniques. This is because the forging of the taper squeezes the grain to a similar form within the iron.
Based on this, the tapered spike may have been between 40mm (total length: 155mm) and 120mm (total length 235mm) longer than it is currently. As the flow of the grain is dictated by forging, had the spike been originally longer than 235mm then the grain would be seen to intersect the sides of the spike to a greater degree.
These estimations are based on extending the existing angles present in the taper of the spike and the assumption that a 2mm rounded edge existed at the end of the taper. While a figure of 2mm has been chosen for the termination of the taper, the actual figure is an unknown variable. Non-tool-related Chisel-tapers generally show this rounding of the end and a figure of 2mm would seem appropriate in this instance (See Figure 63).
A more accurate estimation of the length of the spike can be made if account is taken for the roking of the iron beneath the right volute. As the roking of the iron has opened the fibres of the spike, it will have caused a small amount of distortion at the lower end. Compensating for the width of the opening and ignoring the distortion, a figure of 80mm of loss of material is arrived at (total length 195mm or 11.5% length of the shaft).
An average of the maximum, minimum and compensated lengths also gives a figure of 80mm of additional material and this is likely close to the actual material loss +/- 10mm. A length of 195mm would give the spike a similar dimension to other features of the stand (capital element to grille, grille to Point A, Point A to Point B), which are circa 200mm to 230mm deep along the shaft. However, these are estimations and it may be the case that the spike is still within 5 mm of its original length and that it had a sudden termination of its taper; but a 7mm broad point seems unlikely for an object which needs to be driven into the ground.
Compared to the 1972 interpretation, the spike was likely broader at the shoulders, more heavily constructed and longer by circa 80mm (See Figure 64). Indeed, the 1972 interpretation barely depicts it tapering at all beneath the volutes and almost maintaining the same dimensions as the shaft above the volutes (See Figure 55). The upper breadth of the spike and the shallow taper of roughly 6 degrees would confer some structural rigidity to the spike and mitigate the tip from simply bending if it happened to hit a hard object in the ground, such as a rock.
The shaft/base transition
From 35mm beneath the datum point to 15 mm above the datum point, the shaft between the volutes is relatively flat and broad, with a slight bulging beneath the right volute. The slight bulging is due to the right volute being welded second to the left volute, whereby the material has been worked less.
The broadness in the shaft is likely the result of the taper in the shaft which extends from 15mm to 70mm above the datum point having previously extended to the area now 35mm beneath the datum point prior to the volutes being welded into place. The welding of the volutes then flattened this area so the taper towards the shaft now starts at the upper base of the volutes. This is a logical manner to weld the volutes without reducing the base of the spike-taper, which would otherwise have been circa 5mm narrower.
Discussion on the use of the spike
In 1972 it was suggested that given the short length of the spike, the stand was possibly not designed to stand upright on its own and may instead have been displayed or paraded and carried ‘in the manner of regimental colours’ in a leather holster or frog (Bruce-Mitford, 1972, p. 21). However, if the spike had been designed to fit into a leather strap, it is more likely to have been forged as a round section rather than a tapering rectangular section so as to prevent wear to the frog, strap and corners of the spike through weight and motion. Instead, a cylindrical base would cause little wear to the frog, would not risk cutting through the leather and would not risk becoming wedged as would a rectangular taper.
Instead, it is more likely that the spike was used to locate the iron stand in the ground, particularly if the suggested longer length of the spike is accepted. The geometry and design of the spike suggest that it was used in an exterior setting rather than an interior one. If intended to be used in an interior setting featuring a stone, wooden or beaten earth floor, then the base would possibly be expected to have been made with legs, in the same manner as the Prittlewell stand (See Figure 65).
While the 1952 interpretation was deemed too heavy to support its own weight on the short spike, the 1972 representation was considerably lighter and thought to have been able to hold its own weight (Bruce-Mitford, 1972, p. 21). Indeed, physical reproductions of the 1972 interpretation are capable, in good ground, of holding themselves upright with ease.
Although the representation of the iron stand outlined in this work has added two main additional features to the object: The lower basket element and copper-alloy plating, the spike itself has been elongated by around 80mm, conferring stability to the object. The insertion of the spike into the ground could have been aided by the volutes used as treads in the manner of a spade.
Indeed, the thickness of the volutes and their design as closed scrolls is likely a deliberate feature, as this confers a large amount of rigidity to them and prevents them from bending out of form when pressure is applied. This makes the volutes propitious for use as shoulders for footing the spike into the ground. The thickness of the scrolls serves the additional purpose of reinforcing the spike itself and thickening out its shoulders as the welding process combines the thickness of the scroll material that has been left on the substance of the spike rather than forging it back down to the thickness of the shaft, which could quite easily have been done.
A brief commentary on the shaft of the stand
The shaft in the 1972 interpretation is represented as tapering gently and consistently from above the volutes to the capital element (See Figure 4). It is described as such by Bruce-Mitford with the additional feature of it being slightly rectangular above the volutes (Bruce-Mitford, 1978, pp. 406-408). However, the idea of the shaft being a continuous taper appears to be incorrect.
While the shaft is broader at the base, where it is 20mm wide (in-line with the volutes) by 16mm thick, it becomes approximately 16mm square around 30mm above the volutes and remains so up to the grille.
Based on the measurement of the oxide ‘shell’ surrounding the shaft shortly after its discovery, which is circa 35mm across, a calculation of 18mm original thickness can be arrived at based on an expansion rate of 7:1 of the corrosion. However, this only provides a rough estimate, as corrosion shell thickness was surmised from pre-conservation photographs of the object.
At Point A, the shaft is twisted through 45 degrees within or slightly below the Point A element. No width corrections appear to have been made to the shaft above the Point A twist and as such the shaft would have appeared slightly larger from certain angles above Point A, but larger below Point A from others (See Figure 28).
The impression of a taper in the shaft stems from the degradation between Point A and the grille (See Figure 66). There, the ironwork has corroded to a greater degree than below Point A. While this is possibly a consequence of the copper-alloy plating from the struts causing a galvanic reaction with the shaft above and below the presumed fitting point of the struts at Point A, there is a possibility that the shaft may have been painted between Point A and the grille.
This possibility is considered because the corners of the shaft appear to have deteriorated more than the faces. As corrosion of square bar typically (though not always) maintains a roughly square section, it may be that the corners were more affected either because they were not painted or the paint had worn off them. With the faces of the shaft passivated by a coating, the galvanic reaction to the copper-alloy plating of the struts would have been focused on those areas. However, this is hypothetical as no other evidence for a coating has been seen (as such, the concept is not introduced into the drawing of the object).
Above the grille, the shaft is slightly set-down, reducing the cross-section to circa 9mm in order that the lands of the twisted section observed between the grille and the capital element do not surpass the width of the square section below. This was likely done in order to allow the grille to fit closely to the shaft while still being able to pass over the twisted section, which would otherwise be wider than the square sections of the shaft.
Conclusions on the differences between the 1972 interpretation and proposed new interpretation
Between its discovery in 1939 and the scientific investigation of the 1970s, the appearance of the iron stand from Sutton Hoo was much debated. Whereas parts of the artefact such as the capital element, the grille and the shaft remain recognisable, the decorative elements located below the grille are more difficult to interpret due to deterioration. Scientific investigation solidified some notions pertaining to the appearance of the stand and enabled the conclusions leading to the 1972 interpretation. However, some evidence was not included in that final representation due to its perceived ambiguity. A new examination of those features suggests that the artefact may have had a different appearance to the one embodied in the current representation.
The main differences between the current representation and the proposed new design are to be found between points A and B of the shaft. This is mainly due to the 1972 representation using the conclusion, carried over from the 1952 interpretation that the Point A element was the original base of the upper basket element. While the Point A element is currently too low to have fulfilled this function, the explanation arrived at during the 1970s was that it had fallen down the shaft and rotated 120 degrees.
However, the presence of a possible forge-welded connection of the struts to the shaft at Point B makes the presence of the Point A element redundant in that location and signifies that it is possibly still in its original location. This conclusion is supported by the possible presence of footing corrosion above the Point A element, which indicates that the latter was likely present in its current location prior to the collapse of the burial chamber. Additionally, the shaft appears to be twisted through 45 degrees at Point A in order to provide a step on which the Point A element rests. This 45-degree twist also serves to extend the design principle of alternately facing elements along the shaft, whereby the grille is orientated at 45 degrees to the capital element, the lower basket element at 45 degrees to the grille and the volutes at 45 degrees to the lower basket element.
Additional footing corrosion beneath the Point B possible forge-weld indicates the likelihood that a second pass-through element was located in that area. As the Point A element was not necessary at Point B due to the forge-weld, the conclusion is arrived at that the upper pierced element and the Point A element were linked, forming a lower basket element.
As such, the two plates may have been connected by twisted struts, based on the surviving ends of the original struts present on the Point A element. Given the use of reverse twists on the struts of the upper basket element as well as on the shaft between the grille and the capital element of the stand, it would seem plausible that the lower basket element featured such a design.
Furthermore, the struts of the upper basket element were possibly plated with copper-alloy; a conclusion arrived at based on the extensive copper-alloy corrosion, which reportedly covered strut R at the time of excavation and is still partially visible on the artefact. X-radiography shows traces of the plating still remaining, including porosity bubbles. The purpose of the braze plating would likely have been ornamental. The plating was achievable through package brazing, a widespread copper-alloy plating technique of the period.
At the Point C bend of strut R, also missing from the 1972 interpretation: an iron ring, brazed into position at the same time as the plating was applied. The iron ring has been deliberately created and added in a more structurally rigid manner than the upper scroll of strut R. This is despite it being relatively easy to create an identical scroll at Point C. However, its exact function is indeterminate and may be related to the suspension of ornamentation or to retain guy-ropes used to steady the stand when the latter was deployed on hard or sandy terrain.
On good ground, however, guy ropes would not have been necessary due to the construction of the foot. The volutes of the foot were created as thick, closed scrolls rather than the thin, elegant ones represented in the 1972 interpretation. These would have been propitious for use as treads, used to help sink the spike into the ground. The spike itself may have been around 80mm longer than is currently represented; a conclusion arrived at based on the extension of the angles visible in the spike.
The addition of these design features to the representation of the iron stand makes for an object with a different, more elaborate appearance. The iron stand from Sutton Hoo, Mound 1 is a culturally important object not only for the United Kingdom and Northern Europe but also to the rest of the world and this paper is written in the hope of opening a debate which will further the understanding of the artefact and the skills and techniques used to create it (Figures 67, 68, 69).
- 1Skeumorphic techniques were used during the Anglo-Saxon period to simulate materials with cheaper alternatives, such as the use of red glass or amber to simulate garnet or the use of tinning to simulate polished iron or silver (Barker, 2013). A deliberate technique of the Anglo-Saxons was to use copper-alloys in order to simulate the appearance of gold (Mortimer, Pollard and Scull, 1986). By varying the alloying elements to the copper, creating different brasses and bronzes, etc., a gold-like effect could be created.
- 2The 115mm length of the spike is taken from below the lowest curve of the volutes. The top end of this measurement will be the datum point for all other measurements in this description.
Bibliography
Andrews, J., 1994. New edge of the Anvil: a ressource book for blacksmiths. s.l.:shipjack press.
Asderaki-Tzoumerkioti, E., Rehren, T. and Malakasioti, Z., 2009. Bronze-plated iron bowls from Early Iron Age Central Greece.. s.l., ISA 2006: 36th International Symposium on Archaeometry 2006.
ASM, 1987. Metals handbook, vol: 13: Corrosion. 9th ed. s.l.:ASM international handbook committee.
Barker, H., 1950. Unusual phosphatic material in the Sutton Hoo ship burial. Nature, Volume 166, p. 348.
Barker, J., 2013. The colour and composition of early Anglo-Saxon copper alloy jewellery, s.l.: unpublished PhD thesis, University of Durham.
Bishop, N. and Pauley, B., 2018. Analysis of bronze disease treatments by scanning electron microscopy , s.l.: University of Northern Iowa.
Bruce-Mitford, R., 1947. The Sutton Hoo Ship Burial: A provisional guide. London: The British Museum Publications Ltd.
Bruce-Mitford, R., 1972. The Sutton Hoo Ship Burial, a handbook. 2nd ed. London: The British Museum Publications Ltd.
Bruce-Mitford, R., 1975. Fig.1, unpublished notes, London: The British Museum, dept. of Britain, Europe and Prehistory.
Bruce-Mitford, R., 1978. The Sutton Hoo Ship Burial, Vol. 2: Arms, armour and regalia. London: The British Museum Publications Ltd..
Buchwald, V. F., 2005. Iron and Steel in Ancient Times.. Copenhagen: Kongelige Danske Videnskabernes Selskab.
Carroll, D.-L., 1981. Antique Metal-Joining Formulas in the Mappae Clavicula. Proceedings of the American Philosophical Society, 125(2), pp. 91-103.
Chase, C., 1997. The dating of Beowulf. Toronto: University of Toronto press.
Corfield, M., 1993. Copper Plating on Iron, Metal Plating and Patination: Cultural, technical and historical developments. s.l.:Butterworth-Heineman.
Craddock, P., 2009. Scientific investigations of copies, fakes and forgeries. s.l.:Butterworth-Heinemann.
English Heritage, 2012. Practical Building Conservation - Metals. s.l.:Ashgate Publishing.
Gustafsson, N. B., 2005. On Norse Padlocks - Production and use: Examples from the Birka Garrison. Journal of Nordic Archaeological Science, Volume 15, pp. 19-24.
Hall, C., 1914. Beowulf, a metrical translation into modern English. Cambridge: Cambridge University Press.
Harris, J., 1984. Oxidation induced deformation and fracture. Advances in fracture research. Oxford: Pergammon Press.
Hawthorn, J. G., 1963. Theophilus, On divers arts. s.l.:Dover Books.
Liu, H., Dai, Y. and Chenga, F., 2020. Corrosion of underground pipelines in clay soil with varied soil layer thicknesses and aerations. Arabian Journal of Chemistry, 13(2), pp. 3601-3614.
Mortimer, C., Pollard, A. and Scull, C., 1986. XRF analyses of some Anglo-Saxon copper alloy finds from Watchfield, Oxfordshire. Journal of the Historical Metallurfy Society, 20(1), pp. 36-42.
Ottaway, P., 2016. The products of the blacksmith in mid-late Anglo-Saxon England, part 1, s.l.: unpublished.
Phillips, C., 1940. The Sutton Hoo Ship-Burial. I. The Excavation. Antiquity.
Scotland, H. E., 2012. The repair and maintenance of war memorials, s.l.: Historic Environment Scotland.
Simmons, C. a. M. D., 2009. Manual of Engineering Drawing: Technical Product Specification and documentation to British and International Standards. s.l.:Elsevier.
Skinner, L. and Ozgenc, M., 2004. Analysis of Early Anglo-Saxon, non-ferrous metal artefacts and surface coatings on objects from Blacknall Field, Pewsey, Wiltshire, Centre for Archaeology report 72/2004, s.l.: English Heritage.
Soderberg, A., 2008. Metallurgical clay packages, excavations at Helgo XVII, s.l.: The Royal Swedish Academy of Letters, History and Antiquities.
Strobl, S., Haubner, R. and Pintz, U., 2012. Buntmetallbeschichtungen auf Römischen Eisenmünzen – Subferrata.. Prakt. Met. Sonderband, Volume 44, pp. 295-300.
Thickett, D., 2012. Post excavation changes and Preventive Conservation of archaeological iron, PhD Thesis, University of London. London: English Heritage.
Times, T., 1952. The Times, 16th January, p. 2.
Turner-Walker, G., 2008. A Practical guide to the care and conservation of metals, vol.1. Taichung: Wang Show-Lai.